快速反应程序
QRQC快速反应质量控制程序
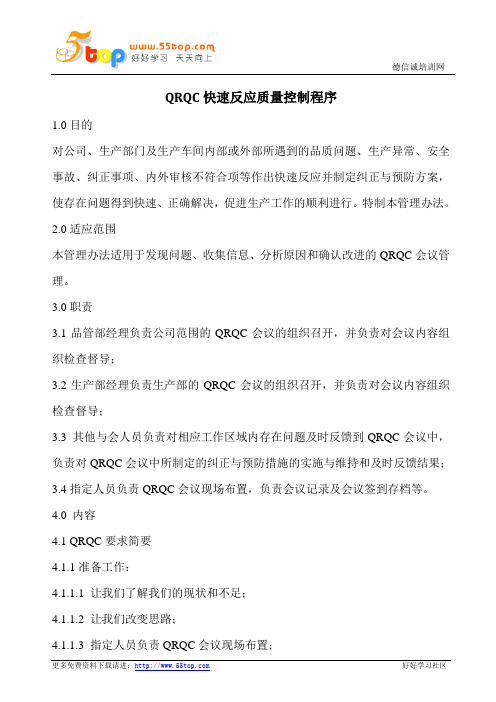
QRQC快速反应质量控制程序1.0目的对公司、生产部门及生产车间内部或外部所遇到的品质问题、生产异常、安全事故、纠正事项、内外审核不符合项等作出快速反应并制定纠正与预防方案,使存在问题得到快速、正确解决,促进生产工作的顺利进行。
特制本管理办法。
2.0适应范围本管理办法适用于发现问题、收集信息、分析原因和确认改进的QRQC会议管理。
3.0职责3.1品管部经理负责公司范围的QRQC会议的组织召开,并负责对会议内容组织检查督导;3.2生产部经理负责生产部的QRQC会议的组织召开,并负责对会议内容组织检查督导;3.3 其他与会人员负责对相应工作区域内存在问题及时反馈到QRQC会议中,负责对QRQC会议中所制定的纠正与预防措施的实施与维持和及时反馈结果;3.4指定人员负责QRQC会议现场布置,负责会议记录及会议签到存档等。
4.0 内容4.1 QRQC要求简要4.1.1准备工作:4.1.1.1 让我们了解我们的现状和不足;4.1.1.2 让我们改变思路;4.1.1.3 指定人员负责QRQC会议现场布置;4.1.1.4 指定人员负责收集当天需要审查的问题;4.1.1.5 将当天问题提前书写在QRQC现场记录板上;4.1.1.6会议前先在《会议培训签到表》上签到。
4.1.2会议时间:4.1.2.1公司QRQC会议,原则上每周五晚上19:00(特殊情况另行安排,以临时通知为准);4.1.2.2生产部QRQC会议,根据实际情况而定(凡发生重大品质事故时,必须及时召开)。
4.1.3会议地点:4.1.3.1公司QRQC会议:办公楼二楼会议室;4.1.3.2生产部QRQC会议:生产部作业现场。
4.1.4参加人员:4.1.4.1公司QRQC会议:副总经理、人事行政部经理、技术部经理、品管部经理、生产部经理、车间主管、班组长、质检员、工程师、技术员、代理或指定人员;必要时,通知营销部与采购部派人参加。
4.1.4.2生产部QRQC会议:生产经理、车间主管,班组长、质检员、工程师、技术员。
快速反应程序:解决质量问题的反应模式

(Example)
OPERATION:
STEP NO.
Standardized Operations Worksheet And Layout标准化操作工作表和布局
WORK ELEMENT
FROM:___________________________
QUANTITY PER SHIFT:______________
TO: _____________________________
SHIFT:________
ELEMENT TIME
HAND WORK MACHINE WALK
STANDARD INPROCESS STOCK
Q
QUALITY
CHECK
CUSTOMER CYCLE TIME:________________
•用目视管理方法建立统一的识别程序
• (Example) 用明亮色彩作为首选的识别方法
✓ ✓✓✓-
红色=废品 黄色=可疑品 绿色=合格品
废品
可疑品或待处 理品
标签内容
标签内容
IN THIS SECTION IN THIS SECTION
IS AT LOCAL
IS AT LOCAL
DISCRETION
DISCRETION
PLT001
红标签表示废品。
PLT002
黄色标签表示可疑产品或待 处理的材料,需要返工的材 料或需要进一步检查的材料
半成品或合格 品
标签内容 IN THIS SECTION
IS AT LOCAL DISCRETION
PLT003
绿色或其他颜色的标签表示产品是可 接受的 (红色和黄色除外). .
TOTAL
快速反应流程

修改码:B/0 1 目的建立快速反应流程,确保所有重大外部/内部问题尽快得到各职能部门的关注和沟通并快速反应,从而系统的分析解决问题,避免再发。
2 适用范围本流程适用于本公司及子(分)公司内生产、技术、质量、安全、采购、物流等相关部门进行快速反应解决问题。
3 定义3.1快速反应系统:--- 标准化的应对重大的内/外部质量问题的反应流程----通过例会加强沟通交流和知识分享----用可视化的方法展现重要问题3.2快速反应会议:生产例会,是一个沟通会议,不是问题解决会议。
3.3经验教训系统:主要指建立获取信息的流程,对所有操作流程的持续改进提供支持,利用成功经验,防止错误重复出现;经验教训适用于所有的岗位,因此组织中相关人员需参加。
3.4 高频客诉追踪:对于一年内再发或者高频客诉抱怨(12个月内多余24起)的,成立专项小组对应,快速记录清单使用红色色标标注。
(公司内部目标值:同类型缺陷相关原因产生的不良件数<2件每月)4 职责4.1 质量部:负责收集24小时内发生的重大问题,主导召开快速反应会议,并跟踪确认。
负责组织对发生问题(内外部问题、安全、交付)的产生与流出原因进行分析。
4.2 生产部:负责对发生问题(内外部问题、安全、交付)的产生与流出因分析及对策实施,负责解决模具、夹治具及生产条件问题,参与对已发生问题根本原因进行分析。
4.3物流部:负责汇报影响生产计划达成和交付问题的报警、跟踪确认。
4.4设备科:负责汇报因设备问题导致客户抱怨、内部重大不良或影响生产等问题,并负责改善确认。
4.5采购部:负责汇报由于采购件的短缺、批量质量问题导致影响交付问题的报警、跟踪确认。
4.6行政企划部:负责汇报安全、工伤问题,及原因调查整改确认。
修改码:B/0 5 程序5.1 快速反应5.1.1 会议前的准备活动为准备快速反应会议,质量部必须找出过去24小时发生的重大质量事故。
收集问题的要素包括问题描述,问题来源,发生日期,频次,原因分析,长短期措施及断点,措施验证结果,责任人。
快速反应会议管理程序
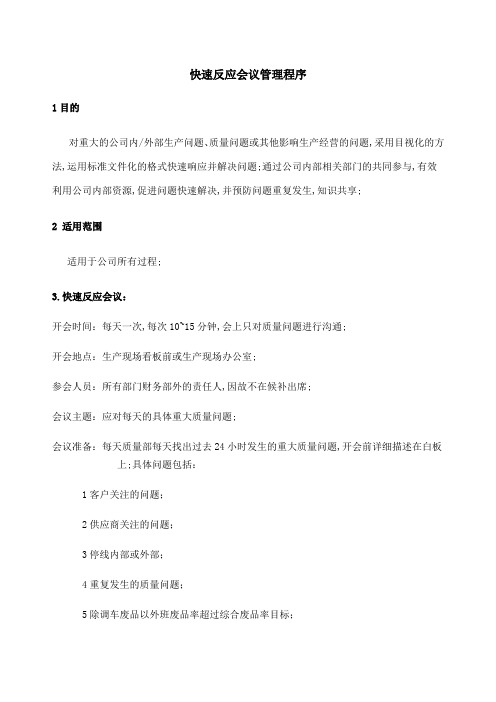
快速反应会议管理程序1目的对重大的公司内/外部生产问题、质量问题或其他影响生产经营的问题,采用目视化的方法,运用标准文件化的格式快速响应并解决问题;通过公司内部相关部门的共同参与,有效利用公司内部资源,促进问题快速解决,并预防问题重复发生,知识共享;2 适用范围适用于公司所有过程;3.快速反应会议:开会时间:每天一次,每次10~15分钟,会上只对质量问题进行沟通;开会地点:生产现场看板前或生产现场办公室;参会人员:所有部门财务部外的责任人,因故不在候补出席;会议主题:应对每天的具体重大质量问题;会议准备:每天质量部每天找出过去24小时发生的重大质量问题,开会前详细描述在白板上;具体问题包括:1客户关注的问题;2供应商关注的问题;3停线内部或外部;4重复发生的质量问题;5除调车废品以外班废品率超过综合废品率目标;6验证岗位中发现的问题;7分层审核中发现的问题;8其它内部质量问题;会议内容:1会议主席协调各方意见,确定新问题的责任人和关闭日期;2旧问题负责人提交相关报告,报告具体进度,紧抓问题退出标准,由与会人员确认关闭;3会议主席根据当天情况,标明具体问题和日Q图的状态;会后工作:问题负责人运用8D等方法、相关工具解决问题,总结形成报告;其他定期工作:快速反应跟踪表应记录所有产生的问题;每月汇总公布问题发生数趋势图;4职责公司生产部长:负责组织和主持快速反应会议,跨部门指定解决问题的责任人;质量部:是快速反应会议的归口管理部门,负责收集和反馈公司内/外部问题,并跟踪问题解决进展;其他部门:负责参加并积极响应快速反应会议;问题责任人:负责按照规定的时间完成问题解决并符合推出标准;协调跨部门问题解决小组在会议外完成相应审核;更新快速反应看板上退出标准及状态栏;向快速反应会议报告问题各阶段的进展;5工作程序6相关文件7相关表单编制/日期:审核人:审核/日期:批准/日期:。
快速反应规定

有限公司快速反应规定编号:QC/HL-3-101-37版本号: A修改次数: 2受控状态:分发号:实施日期:2008年08月08日批准日期会签日期审核日期编制日期1. 目的:通过每日例会加强沟通和管理;使用标准化的反应流程来应对重大的内/外部质量问题;采用目视管理的方法展示重要的信息;保证所有的问题都得到彻底的解决;提供系统的问题解决方法,降低质量问题再次发生的次数;提高质量水平,提高顾客满意度。
2. 范围:对重大的问题(生产、质量、设备、安全等问题)进行快速反应,重大问题如下:2.1 顾客关注的问题(顾客投诉、顾客退货、顾客电话等);2.2 供应商关注的问题;2.3 入库、发货抽检,产品审核时发现的质量问题;过程分层审核发现的质量问题;2.4 生产停线的问题(主要针对单一生产设备、检测设备,如:涂装线、压衬套机等设备停线且又没有其他补救措施来继续维持正常生产的情况;以及导致工厂不能继续生产该产品2小时以上,或导致该产品不能计划完成订单或需要延期交付为界定标准);2.5 一次下线合格率数据(比目标下降5%以下);2.6 新品开发验证过程出现失败导致送样延后问题;2.7 出现重大以上设备责任事故问题;(具体界定标准参考公司《设备奖罚制度》)2.8 出现重大以上工伤安全事故问题;(具体界定标准参考公司《工伤安全制度》);2.9 验证岗位发现的问题;2.10 产生产品遏制的问题;3. 职责:3.1 制造部每天召开快速反应会,制造部经理为快速反应会议主持人;3.2 质检科负责收集过去24小时内发生及收到的重大质量问题,并在快速反应会议前将问题写在快速反应看板上;3.3 产品开发科负责收集与汇报重大新品验证问题;设备科负责收集与汇报重大设备责任事故问题;工伤安全事故发生单位负责收集与汇报重大安全事故问题;计划科负责收集与汇报生产停线问题;3.4 原则上问题负责人(或问题出现\发现工序主管)为每个问题的总负责人,确保能按时完成所有退出标准所要求的项目,将问题解决,并在每次指定的汇报时间,向管理层汇报问题解决的状态。
QSB快速反应流程

QSB快速反应流程快速反应流程(QSB,Quick Service Bulletin)是一种用于迅速处理问题和将解决方案迅速传达给相关人员的流程。
它旨在确保问题能够得到及时解决,以最小程度地对组织的正常运营造成干扰。
以下是一个包含超过1200字的QSB的标准流程:第一步:问题识别(Identification)快速反应流程的第一步是识别问题。
这可以通过多种方式进行,例如通过客户反馈、内部质量监控和检查、日常操作的异常情况等等。
一旦问题被发现,相关人员应该立即报告给负责的团队或部门。
第二步:问题分析(Analysis)第三步:解决方案开发(Solution Development)一旦问题的根本原因得到确认,团队需要制定相应的解决方案。
这通常涉及到制定一系列具体的步骤和行动计划,以修复问题并防止类似问题的再次发生。
解决方案应该是可操作和具体的,以便相关人员能够迅速理解并采取相应行动。
第四步:解决方案验证(Solution Validation)在制定解决方案之后,团队需要进行验证,以确保问题解决方案的有效性。
这可能包括验证方案的实施、测试解决方案的可行性,并确保它真正解决了问题。
如果验证过程中发现问题或需要进行进一步的调整,团队将返回前面的步骤进行修正。
第五步:解决方案发布(Solution Release)在解决方案被验证通过之后,团队需要将其传达给相关人员。
这可能包含编制发布公告、更新相关文件或培训相关人员。
目标是确保解决方案被传达给那些需要知道并实施它的人员。
第六步:问题解决(Problem Resolution)解决方案发布之后,团队需要跟踪问题是否得到解决。
这可以通过定期的监控和检查来实现。
如果发现问题仍未解决或出现新的问题,团队需要立即采取行动进行纠正。
第七步:总结和反馈(Summary and Feedback)在问题解决之后,团队应该进行总结和反馈。
这包括评估问题解决的效果、提取教训和经验,并在需要的情况下更新标准操作程序和其他相关文件。
QSB+快速反应流程
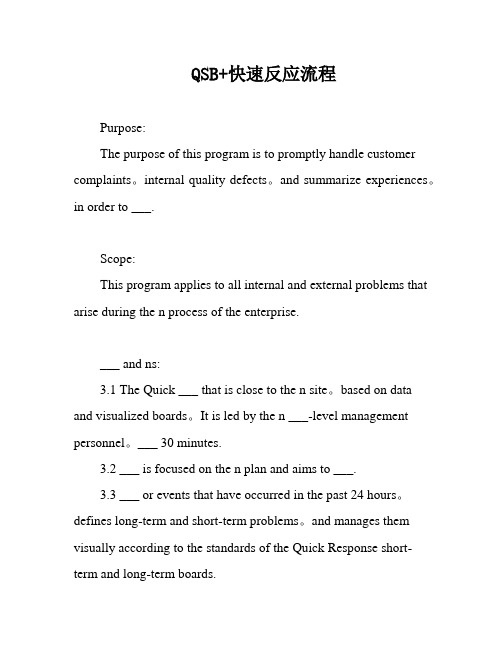
QSB+快速反应流程Purpose:The purpose of this program is to promptly handle customer complaints。
internal quality defects。
and summarize experiences。
in order to ___.Scope:This program applies to all internal and external problems that arise during the n process of the enterprise.___ and ns:3.1 The Quick ___ that is close to the n site。
based on data and visualized boards。
It is led by the n ___-level management personnel。
___ 30 minutes.3.2 ___ is focused on the n plan and aims to ___.3.3 ___ or events that have occurred in the past 24 hours。
defines long-term and short-term problems。
and manages them visually according to the standards of the Quick Response short-term and long-term boards.3.4 ___ sharing。
___-making。
and ___ of the meeting is based on the effective n of problems and the n of experience (horizontal n。
美军应急装备采办的做法和启示

军现代战争在战争形态、作战样式、武器装备等方面都发生了很大的变化,信息化装备越来越多,装备的技术含量越来越高,装备、物资消耗越来越快,传统机械化战争时代所采用的战时采办程序已不能适应现代高技术战争的战场需要,迫切需要一种快速应急反应程序来实现战场军事装备的快速补给。
美军结合近几场战争的实践,在应急装备采办的组织机构、法规制度、采办程序和合同管理等方面,积累了大量经验,建立起一套应急装备采办程序,较好地满足了战争的需要。
1.美军应急装备采办程序应急装备采办程序是指国家在应对紧急状况的准备阶段或是紧急状态期间(包括战争、突发自然灾害以及其他紧急状况)进行装备采办活动或采办事项办理的先后顺序。
应急装备采办由于其“应急”特点,美军在应急装备采办的组织机构、法规制度、采办程序和合同管理等方面,积累了大量经验,建立起一套应急装备采办程序,较好地满足了战争的需要。
本文结合美军应急装备采办程序的主要内容、实施途径等方面谈几点对我军装备采办的启示。
美军应急装备采办的做法和启示■ 贺 鸣因此主要适用于金额相对较低的二、三类武器装备,而金额较高的一类(如航母、坦克、飞机等),通常采用常规的装备采办程序。
目前美军应急装备采办主要采用以下三种采办程序。
1.1快速反应程序快速反应程序(RRP)是海湾战争开始之前,由美空军提出的,主要针对战场上的紧急装备需求,通过减少管理层次、简化采办程序,加速成熟技术转化为作战能力。
该采办程序的实施分为三个阶段:第一阶段由作战部门提出装备需求,编写作战任务需求书提交空军参谋长批准;第二阶段由“快速反应评估委员会”、空军装备司令部以及“快速反应程序委员会”等机构对项目进行评审,并起草项目管理指令;第三个阶段为项目执行官发布项目管理指令,开始实施采办计划。
一般来讲,快速反应程序从提交《作战任务需求书》到发布计划管理指令不到16天,整个采办周期一般不超过半年。
项目经费由空军各司令部根据项目紧急程度从国会已经划拨的采办经费中提取。
- 1、下载文档前请自行甄别文档内容的完整性,平台不提供额外的编辑、内容补充、找答案等附加服务。
- 2、"仅部分预览"的文档,不可在线预览部分如存在完整性等问题,可反馈申请退款(可完整预览的文档不适用该条件!)。
- 3、如文档侵犯您的权益,请联系客服反馈,我们会尽快为您处理(人工客服工作时间:9:00-18:30)。
1 目的
使用标准化的反应流程来应对重大的内/外部质量问题,使所有的问题都得到彻底的解决,降低质量问题再次发生的次数。
提高处理质量问题的效率,保证生产顺利进行和产品的准时交付
2 术语
2.1 快速反应:通过每日例会加强沟通和管理,采用目视管理方法展示重要信息,使应对重大的内、外部质量问题的反应标准化。
2.2 问题解决:一个系统化的用来识别、分析和消除现状和现行标准或期望之间的差距,并预防根本原因再次发生的过程。
2.3 经验总结:利用成功经验,防止问题重复出现。
3 职责:
3.1 生产副总负责快速反应会议,每天召开快速反应会,并担任快速反应会议主持人。
如因故不在应提前指定候补代理人主持。
3.2 质量部负责汇总过去24小时内发生及收到的重大质量问题,并在快速反应会议前将问题写在快速反应看板上;每天更新《快速反应跟踪板》和《日质量Q图》。
3.3 制造部负责收集与汇报生产停线问题;
3.4 研发部负责收集与汇报重大新品和工艺验证问题;
3.5 设备部负责收集与汇报重大设备责任事故问题;
3.6 工伤安全事故发生部门负责收集与汇报重大安全事故问题;
3.7 问题责任人负责采用8D等方法、运用相应质量工具解决问题。
原则上问题责任人(或问题出现/发现工序主管)为每个问题的总负责人,确保能按时完成所有退出标准所要求的项目,将问题解决,并在每次指定的汇报时间,向领导层汇报问题解决的状态。
收集问题解决的所有资料,并提交到质量部存档。
3.8各负责部门负责总结其相应经验教训活动。
4 工作内容
4.1 快速反应会议
4.1.1 开会时间:必须每工作日进行一次,时间为每天早上8:00~8:30,每次15~30分钟,会上只对质量问题进行沟通。
4.1.2开会地点:生产现场看板前或生产现场办公室。
4.1.3参会人员:所有部门(财务部除外)的第一责任人,因故不在由候补代理人出席。
参加会议人员应在《日质量会议签到表》上签到。
4.1.4会议主题:应对每天具体的重要质量问题。
4.1.5会议准备:
每天下班前,各部门负责人或候补代理人将本部门当天的重要质量问题提交质量部(书面或邮件)。
开会前质量部将过去24小时发生的重要质量问题详细描述在白板上。
具体问题包括:
a) 顾客关注的问题;
b) 供应商/外包方关注的问题;
c) 停线(内部或外部);
d) 重复发生的质量问题;
e) 废品率超过综合废品率目标的问题;
f) 检验/验证岗位中发现的问题;
g) 分层审核中发现的问题;
h) 其它内部质量问题。
4.1.6会议内容:
a) 会议主持人协调各方意见,确定新问题的责任人和关闭日期。
b) 老问题责任人提交相关报告,报告具体进度,紧抓问题退出标准,由与会人员确认
关闭。
c) 会议主持人根据当天情况,标明具体问题和日Q图的状态。
4.1.7 快速反应看板上板界限:
4.1.7.1 外部问题:
a) 客户抱怨:包括开PRR抱怨和口头抱怨、邮件抱怨;
b) 供应商/外包方的问题:来料质量不合格:生锈、错装、缺(多)肉、变形、丢漏工
序、尺寸超差、开焊、表面有坑包;
c) 批量事故:来料10件以上产品质量不合格情况;
d) 发货缺件:来料缺5件以上事故;
e) 发货滞后:未按物流要求发货、到货情况等
4.1.7.2 内部问题
a) 因产品质量问题造成停线10-15分钟以上的情况;
b) 一天内一种产品连续出现3次同类不良问题的情况(注:只限于外观、击穿缺陷);
c) 所有产品只要发生尺寸超差、虚焊、丢漏工序必须上板;
d) 产品批量返工/返修问题。
e) 其他变化点问题。
4.1.8 快速反应看板下板界限:
a) 每次制定上板问题措施,规定24小时内提供断点,长期断点为7天,验证关闭时间
为30天。
b) 长期无法关闭的问题,下板跟踪,且必须每天早会进行回顾,待问题解决后在记录
表中关闭。
4.2会后工作:
4.2.1 制造部经理对每一项重要质量问题指定一个负责人,由负责人召集相关的人员成立一个问题解决小组。
4.2.2 问题解决时,每个问题都必须有一个问题解决报告《PPSR快速反应问题报告单》,遵循《8D流程指导书》,使用3×5Why记录根本原因查找过程。
4.2.3 问题负责人对问题制定退出标准,并确定下次汇报的日期。
4.2.4 负责人汇报时回顾报告的内容,以汇报问题的整体结构状况,并保持既定的会议时间安排不被打乱。
问题负责人汇报跟踪进度,并提交相关的文件资料(含《PPSR快速反应问题报告单》),会议上对此进行审核。
4.2.5 问题负责人汇报必须包括问题解决报告中以下阶段:
a) 问题描述,遏制阶段
b) 原因分析阶段
c) 纠正措施和纠正预防措施
d) 验证阶段
4.2.6 遏制后合格产品的发运必须填写《遏制产品发运记录表》
4.2.7质量部其他定期工作:
a) 采用《快速反应跟踪汇总表》记录所有产生的问题。
b) 每月汇总公布问题发生数趋势图。
c) 将有关的更新的文件及时发给相关部门及人员。
4.3经验总结
4.3.1经验教训适用于所有的岗位,公司每个人都应参与经验教训总结的过程。
通过下列内容相关的活动展开经验总结(括号内为负责部门):
a) 每月的质量Q图(质量部)
b) 分层审核(制造部)
c) 防错装置验证(研发部)
d) 内部质量问题(质量部)
e) 检验/验证岗位(质量部)
f) APQP 程序执行(研发部)
g) 持续改进小组活动(质量部)
h) (顾客抱怨, 风险降低)问题解决和报告(质量部、研发部)
i) 管理评审(质量部)
j) 合理化建议项目(综合办)
4.3.2以上活动的负责部门应建立一个经验教训档案,每月更新公布经验教训清单。
由综合办负责对各部门经验教训清单每月进行归档在内部网中公布。
5 相关文件
●管理评审程序
●纠正措施控制程序
●8D流程指导书
发行对象:
总经理、副总经理、人力资源部、技术部、质量部、生产部、销售部、采购部、设备部、财务部
编制审核批准
日期日期日期。