石墨制作工艺
石墨造粒工艺

石墨造粒工艺石墨造粒工艺是一种将石墨材料加工成颗粒状的工艺过程。
石墨是一种特殊的非金属材料,具有良好的导电性、导热性和耐高温性能,因此在许多领域有着广泛的应用。
石墨造粒工艺可以改善石墨材料的使用性能和加工工艺,并扩大其应用范围。
石墨造粒工艺的目的是将石墨材料加工成具有一定形状和尺寸的颗粒。
首先,需要选择合适的石墨原料。
石墨可以分为天然石墨和人工石墨两种类型,根据不同的需求选择合适的石墨原料。
然后,将石墨材料进行破碎和研磨,使其变成一定粒度的石墨粉末。
研磨过程中需要注意控制研磨时间和研磨介质的选择,以保证石墨粉末的质量和粒度分布。
接下来,通过造粒机将石墨粉末进行造粒。
造粒机主要有压力造粒机和挤压造粒机两种类型。
压力造粒机通过一定的压力将石墨粉末压制成颗粒状,该方法适用于较细的石墨粉末。
挤压造粒机则利用挤压力将石墨粉末挤压成颗粒状,该方法适用于较粗的石墨粉末。
在造粒过程中,需要控制造粒机的参数,如压力、温度和速度,以获得理想的造粒效果。
完成造粒后,还需要进行干燥和筛分处理。
干燥过程可以去除石墨颗粒中的水分,提高石墨颗粒的质量。
筛分过程可以分离出不同粒度的石墨颗粒,以满足不同应用的需求。
干燥和筛分的参数需要根据具体情况进行调整,以获得理想的处理效果。
石墨造粒工艺的优点在于可以改善石墨材料的使用性能和加工工艺。
通过造粒,可以提高石墨材料的流动性和均匀性,便于在生产过程中的加工和使用。
此外,石墨颗粒还可以通过配方设计和表面处理等方法进行功能改性,以满足不同行业和领域的需求。
石墨颗粒的应用范围广泛,包括电池、涂料、橡胶、塑料、涂料、摩擦材料等领域。
石墨造粒工艺是一种重要的石墨加工方法,可以改善石墨材料的使用性能和加工工艺。
通过选择合适的石墨原料、破碎研磨、造粒、干燥和筛分等工艺步骤,可以获得具有一定形状和尺寸的石墨颗粒。
石墨颗粒的应用范围广泛,可以满足不同行业和领域的需求,具有很高的经济和社会价值。
石墨造粒工艺的发展将进一步推动石墨材料的应用和推广,为相关行业的发展做出积极贡献。
石墨焙烧工艺和石墨化

石墨焙烧工艺和石墨化引言石墨是一种重要的非金属制品,广泛用于电池、涂料、化工、冶金等领域。
而石墨焙烧工艺和石墨化则是石墨生产过程中至关重要的步骤。
本文将全面探讨石墨焙烧工艺和石墨化的原理、工艺流程、影响因素以及应用。
I. 石墨焙烧工艺的原理1.1 石墨焙烧的概念石墨焙烧是指通过高温处理氧化石墨,将其还原为石墨的过程。
焙烧温度通常在2500℃以上,采用惰性气体氛围,如氩气或氮气,避免氧化石墨再次发生燃烧反应。
焙烧工艺可以有效提高石墨晶体的完整性和结晶度。
1.2 石墨焙烧的原理石墨焙烧的原理可以从石墨晶体结构和化学反应两个方面来解释。
首先,石墨晶体结构由六个碳原子构成的六边形结构堆积而成。
在高温下,焙烧过程中晶格结构的热振动将使石墨晶体扩张,从而促进杂质离子的扩散和逸出。
其次,焙烧过程中,氧化石墨与还原气氛中的气体发生反应,氧原子离开石墨分子,生成气体的氧化物。
II. 石墨焙烧工艺流程2.1 原料准备石墨焙烧工艺的第一步是原料的准备。
通常使用天然石墨或人工合成石墨作为原料,将其破碎、粉碎、筛分,以获得均匀颗粒分布的石墨粉末。
2.2 石墨焙烧设备石墨焙烧设备通常采用电阻炉或感应炉,其具备高温、恒温、密闭和惰性气氛等特点。
炉体内部通常使用耐火材料进行衬底,以抵御高温和化学腐蚀。
2.3 焙烧工艺参数焙烧工艺参数对焙烧效果至关重要。
主要包括焙烧温度、保温时间、惰性气氛和压力控制等。
其中,焙烧温度是最关键的参数,不仅影响石墨晶体的晶化程度,还会直接影响石墨焙烧的产率和能耗。
2.4 石墨焙烧过程石墨焙烧过程一般分为预热、焙烧和冷却三个阶段。
首先,在预热阶段,将石墨样品加热到预定温度,以去除其中的挥发性杂质。
然后,在焙烧阶段,将温度进一步提高,在惰性气氛中进行石墨焙烧生成还原石墨。
最后,在冷却阶段,将石墨样品从高温环境中取出,并进行自然冷却或强制冷却。
III. 石墨化的原理和方法3.1 石墨化的概念石墨化是指将非晶态碳材料转化为石墨的过程。
石墨化工艺流程

石墨化工艺流程石墨化工艺流程是一种将天然石墨转化为高纯度石墨的工艺流程。
石墨是一种具有特殊结构和性质的矿物,具有良好的导电、导热、耐高温、耐腐蚀等特性,因此在电子、航空、军工等领域有着广泛的应用。
然而,天然石墨中含有杂质较多,需要经过石墨化工艺流程进行提纯,才能得到高纯度的石墨。
石墨化工艺流程主要包括石墨矿石的选矿、石墨的粉碎、浮选、化学处理、高温热解等步骤。
首先是石墨矿石的选矿。
石墨矿石中含有大量的杂质,如石英、黄铁矿、方铅矿等,需要进行选矿处理。
选矿的目的是通过物理或化学方法将石墨和杂质分离,得到高品质的石墨矿石。
常用的选矿方法有重选、浮选、磁选等。
接下来是石墨的粉碎。
经过选矿处理后的石墨矿石需要进行粉碎,以便于后续的浮选和化学处理。
石墨的粉碎通常采用球磨机、研磨机等设备进行。
然后是浮选。
浮选是石墨化工艺流程中最关键的一步,也是提纯石墨的主要方法。
浮选的原理是利用石墨和杂质在水中的不同亲水性,通过添加药剂使石墨和杂质分别吸附在气泡上,从而实现石墨和杂质的分离。
常用的浮选药剂有黄药、黑药、绿药等。
接着是化学处理。
经过浮选后的石墨仍然含有一定的杂质,需要进行化学处理。
化学处理的目的是去除石墨表面的氧化物和有机物等杂质,提高石墨的纯度。
常用的化学处理方法有酸洗、氧化、还原等。
最后是高温热解。
经过化学处理后的石墨需要进行高温热解,以去除残留的杂质和提高石墨的结晶度。
高温热解的温度通常在2500℃以上,需要采用高温炉进行。
石墨经过高温热解后,其结晶度和纯度都得到了显著提高,可以用于制备高纯度石墨材料。
石墨化工艺流程是一种将天然石墨转化为高纯度石墨的工艺流程,包括石墨矿石的选矿、石墨的粉碎、浮选、化学处理、高温热解等步骤。
通过这些步骤的处理,可以得到高品质的石墨材料,为电子、航空、军工等领域的发展提供了重要的支持。
石墨浮选工艺流程

石墨浮选工艺流程
一、简介
石墨浮选工艺是指利用化学药剂将石墨与杂质分离的过程。
该工艺广泛应用于石墨的提取和加工过程中,能够有效地提高石墨的品质和产量。
二、前期准备
1. 原料准备:选择优质的石墨原料,并进行初步的筛选和清洗。
2. 设备准备:准备好需要使用的设备,包括颚式破碎机、圆锥式破碎机、球磨机等。
3. 环境准备:确保生产环境卫生干净,无尘无杂质。
三、粗选阶段
1. 破碎:将原料经过颚式破碎机和圆锥式破碎机进行初步粉碎。
2. 磨细:将初步粉碎后的原料送入球磨机进行进一步细化。
3. 除杂:利用筛分器对细粉进行筛分,去除其中的杂质。
四、中选阶段
1. 调节药剂:根据不同类型的原料选择合适的药剂,并进行调配。
2. 混合搅拌:将调配好的药剂与细粉进行混合搅拌,使其充分接触。
3. 浮选分离:将混合好的物料送入浮选机中,利用化学药剂的作用使
石墨和杂质分离。
五、精选阶段
1. 磨细:将浮选后的石墨进行再次磨细。
2. 除杂:利用筛分器对磨细后的石墨进行筛分,去除其中的杂质。
3. 烘干:将除杂后的石墨送入烘干机中进行脱水和干燥处理。
六、尾料处理
1. 回收药剂:将浮选机中使用过的药剂进行回收和再利用。
2. 处理废水:对于浮选过程中产生的废水进行处理,达到环保标准。
七、总结
通过以上流程可以看出,石墨浮选工艺是一项复杂而又关键性极强的工艺。
只有在严格控制每一个环节并保证设备运转正常的情况下,才能够生产出高品质、高产量的石墨产品。
石墨粉生产工艺流程

石墨粉生产工艺流程
石墨粉的生产工艺流程如下:
1. 原料准备:选用高品质的天然石墨矿石作为原料,经过矿石的破碎、研磨、筛分等工序,得到适合生产石墨粉的原料。
2. 石墨粉磨碎:将原料石墨矿石放入石墨粉磨碎机中,通过机械力对矿石进行粉碎,使其达到所需的粒径大小。
3. 分选:将磨碎后的石墨粉通过筛分设备进行分选,分离出不同粒径的石墨粉,以满足不同要求的应用领域。
4. 石墨粉烘干:将分选后的石墨粉放入烘干设备中,通过热风或排除水分的方法,将石墨粉中的水分蒸发或排除,使其达到所需的含水率。
5. 石墨粉表面处理:通过与表面活性剂等物质的混合,对石墨粉进行表面处理,以改善石墨粉的分散性、润湿性和流动性等性能。
6. 石墨粉包装:将经过处理和烘干的石墨粉装入包装袋中,根据不同需求进行分装和标记。
以上为一般石墨粉的生产工艺流程,不同厂家和产品在实际生产过程中可能会有一些差异。
石墨生产工艺介绍

石墨生产工艺介绍石墨,又称为石墨材料,是一种具有良好导电、导热和润滑性能的材料,广泛应用于电子、冶金、化工等领域。
石墨的生产工艺分为自然生石墨和人工合成石墨两种。
自然生石墨的生产工艺主要分为开采、研磨和加工三个步骤。
首先,需要选取含有较高石墨矿物质的岩石,通常选取石英岩或者云母岩。
然后,通过开采方法将石墨矿石从矿脉中提取出来,常用的开采方法有露天开采和井下开采。
露天开采适用于矿脉露头较大的情况,通过爆破和拆卸等手段将矿石提取出来;井下开采适用于矿脉露头较小或者埋深较大的情况,需要通过井下隧道或者井筒将矿石运出地下。
提取出的石墨矿石经过研磨处理,主要目的是将石墨矿石的杂质去除,获得纯净的石墨粉末。
通常采用湿法研磨的方法,将石墨矿石与水混合并添加一定的研磨介质,通过摩擦和冲击的作用将矿石粉破碎为粉末。
研磨过程中需要控制研磨时间和研磨介质的大小,以获取合适的石墨粒度。
最后,经过研磨处理后的石墨粉末可以进行加工,常见的加工方法包括压制、烧结和石墨化处理。
压制是将石墨粉末放入模具中,在高温高压的条件下进行压制,使石墨粉末紧密结合成坚硬的石墨块状。
烧结是将压制成型的石墨块放入烧结炉中,在高温下进行烧结,使石墨块的颗粒间相互融合,形成致密的结构。
石墨化处理是在高温高压的环境中,通过化学反应或者物理变化将石墨块进行改性处理,以提高其性能。
人工合成石墨的生产工艺主要有化学气相沉积法和高温焙烧法两种。
化学气相沉积法是利用气相化学反应使石墨材料在衬底上沉积形成,可以控制石墨材料的形貌和结构。
高温焙烧法是将石墨材料的前驱体经过高温热处理,使其发生结构变化,形成石墨结构。
总之,石墨的生产工艺主要分为自然生石墨和人工合成石墨两种。
自然生石墨主要通过开采、研磨和加工三个步骤,而人工合成石墨主要通过化学气相沉积法和高温焙烧法进行。
随着技术的不断进步,石墨的生产工艺也在不断发展和改进,以满足不同领域对石墨材料性能和品质的要求。
石墨化工艺流程
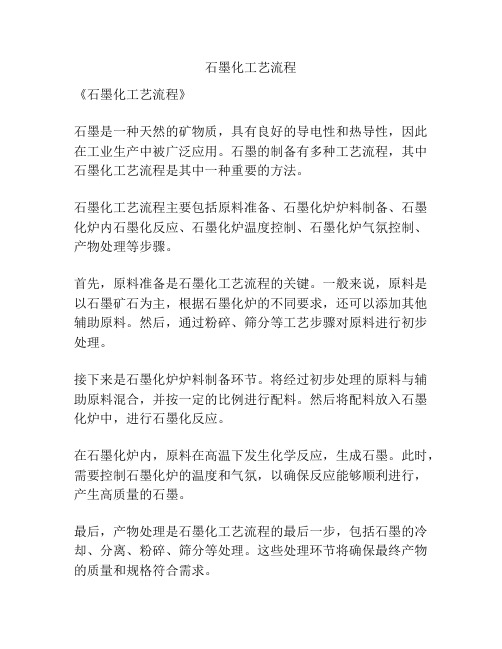
石墨化工艺流程
《石墨化工艺流程》
石墨是一种天然的矿物质,具有良好的导电性和热导性,因此在工业生产中被广泛应用。
石墨的制备有多种工艺流程,其中石墨化工艺流程是其中一种重要的方法。
石墨化工艺流程主要包括原料准备、石墨化炉炉料制备、石墨化炉内石墨化反应、石墨化炉温度控制、石墨化炉气氛控制、产物处理等步骤。
首先,原料准备是石墨化工艺流程的关键。
一般来说,原料是以石墨矿石为主,根据石墨化炉的不同要求,还可以添加其他辅助原料。
然后,通过粉碎、筛分等工艺步骤对原料进行初步处理。
接下来是石墨化炉炉料制备环节。
将经过初步处理的原料与辅助原料混合,并按一定的比例进行配料。
然后将配料放入石墨化炉中,进行石墨化反应。
在石墨化炉内,原料在高温下发生化学反应,生成石墨。
此时,需要控制石墨化炉的温度和气氛,以确保反应能够顺利进行,产生高质量的石墨。
最后,产物处理是石墨化工艺流程的最后一步,包括石墨的冷却、分离、粉碎、筛分等处理。
这些处理环节将确保最终产物的质量和规格符合需求。
总的来说,石墨化工艺流程是一项复杂的生产工艺,需要对原料、炉料、炉温、气氛等多个因素进行精密控制,才能够获得高质量的石墨产品。
随着科技的不断发展,石墨化工艺流程也在不断优化和改进,以满足日益增长的市场需求。
纯化石墨粉生产工艺

纯化石墨粉生产工艺一、概述纯化石墨粉是一种高纯度的石墨产品,其主要用途是作为电极材料、高温材料和涂料等领域。
本文将介绍纯化石墨粉的生产工艺。
二、原材料准备1. 石墨矿:选用高品质的天然石墨矿作为原料,其含碳量大于90%。
2. 化学试剂:氢氧化钠、硫酸、盐酸等。
3. 水:用于稀释试剂和冲洗设备。
三、制备过程1. 粉碎:将原材料的天然石墨矿进行粉碎,可采用球磨机或者振荡式球磨机等设备进行处理,以保证粒度均匀。
2. 酸洗:将粉碎后的原材料进行酸洗,可采用浓硫酸或盐酸进行处理,以去除其中的杂质和氧化物。
需要注意的是,在操作过程中要注意安全防护措施,并对废酸进行合理处理。
3. 碱洗:将经过酸洗处理后的原材料进行碱洗,可采用氢氧化钠溶液进行处理,以去除其中的酸性物质和残留的杂质。
需要注意的是,在操作过程中要控制碱液浓度和温度,以避免产生不必要的化学反应。
4. 过滤:将碱洗后的原材料进行过滤,以去除其中的固体颗粒和杂质。
可采用压滤机或者离心机等设备进行处理。
5. 干燥:将经过过滤处理后的原材料进行干燥,可采用烘箱或者真空干燥箱等设备进行处理,以保证其水分含量低于1%。
6. 筛分:将经过干燥处理后的原材料进行筛分,可采用振动筛或者离心筛等设备进行处理,以保证其粒度均匀。
7. 热解:将筛分后的原材料进行高温热解处理,可采用电阻式高温炉或者感应加热器等设备进行处理。
在操作过程中需要控制温度、时间和气氛组成等参数,以保证产物纯度和晶体结构。
8. 冷却:将经过高温热解处理后的产物进行冷却处理,可采用自然冷却或者水冷等方式进行处理。
9. 磨制:将经过冷却处理后的产物进行磨制,可采用球磨机或者超细粉碎机等设备进行处理,以保证其粒度均匀和细度达到要求。
四、产品质量控制1. 碳含量:纯化石墨粉的碳含量应大于99.9%。
2. 氮含量:纯化石墨粉的氮含量应小于50ppm。
3. 水分含量:纯化石墨粉的水分含量应小于1%。
4. 粒度分布:纯化石墨粉的粒度分布应符合要求,一般为D50=10-20μm。
- 1、下载文档前请自行甄别文档内容的完整性,平台不提供额外的编辑、内容补充、找答案等附加服务。
- 2、"仅部分预览"的文档,不可在线预览部分如存在完整性等问题,可反馈申请退款(可完整预览的文档不适用该条件!)。
- 3、如文档侵犯您的权益,请联系客服反馈,我们会尽快为您处理(人工客服工作时间:9:00-18:30)。
石墨制作工艺
This model paper was revised by the Standardization Office on December 10, 2020
石墨制造工艺简介
一般而言,碳素是用焙烘炉在1000℃到1300℃温度下,将焦碳与粘附沥青混合后予以焦化而生产的,然后将碳素用电热炉在2500℃至3000℃温度下予以石墨化,将无形质碳素体加工成晶性石墨的结构,因此就称为石墨。
在将碳素材料予以石墨化前,还经浸沥青和再次焙烘,这可以增进其电气和机械性能。
当将石墨材料用于某些特别用途时,常常予以纯化或用陶瓷加以涂层,一般来讲,根据石墨的生成方法,可将其划分为三种类型:各向同性石墨(采用等静模压发),挤压成形石墨和模压成型石墨。