(数控加工)数控机床壳体材料与工艺有机玻璃精编
数控加工工艺与编程_习题集(含答案

《数控机床加工工艺与编程》课程习题集西南科技大学成人、网络教育学院版权所有习题【说明】:本课程《数控机床加工工艺与编程》(编号为09018)共有单选题,简答题,判断题,编程题, 填空题等多种试题类型,其中,本习题集中有[编程题]等试题类型未进入。
一、单选题1.在数控机床的机械组成中,不.包括()A.立柱 B.床身 C.工作台 D. 控制系统2.机械手换刀途中停止的主要原因是()A. 气动换向阀损坏B. 主轴定向不准C. 机械手卡死D. 程序错误3.数控机床的构成中,不.包括( )A.数控装置 B.伺服系统 C.机床本体 D. 刀库系统4.加工中心最突出的特点是()A. 工序集中B. 对加工对象适应性强C. 加工精度高D. 加工生产率高5.关于加工中心编程时,下面哪种说法中不正确的是()A. 进行合理的工艺分析B. 自动换刀要有足够的空间C. 尽量采用机内对刀D. 尽量采用工序集中6.为了保证加工精度,降低刀具的损耗,提高生产率,合理使用机床,应正确选择()A. 刀具几何角度B. 切削用量C. 工艺装备D. 刀具耐用度7.主要用于模具曲面加工的立铣刀具是( )A. 端面立铣刀B. 球头立铣刀C. 键槽铣刀D. 环行铣刀8.刀柄与主轴内的拉紧装置相连接的部件是( )A. 刀柄B. 夹头C. 弹簧D. 拉钉9.不.宜沿轴向做进给运动的立铣刀具是( )A. 端面立铣刀B. 球头立铣刀C. 键槽铣刀D. 环行铣刀10.可实现高速切削或以“车、铣代磨”,加工高硬材料的刀具是( )A. 高速钢刀具B. 硬质合金刀具C. 陶瓷刀具D. 工具钢刀具11.采用ER型卡簧,适合于夹持小直径铣刀进行铣削加工的刀柄是( )A. 液压夹紧式刀柄B. 弹簧夹头式刀柄C. 侧固式刀柄D. 热装夹紧式刀柄12.数控机床实现圆周进给运动而采用的夹具是( )A. 多工位夹具B. 回转工作台C. 平口钳D. 三爪卡盘13.主切削刃分布在铣刀圆拄面的立铣刀具是( )A. 端面立铣刀B. 球头立铣刀C. 键槽铣刀D. 环行铣刀14.数控加工中心换刀机构常采用的机构是( )A.伺服机构 B.机械手(机构) C.液压机构 D. 人工换刀15.最常用的刀柄与主轴孔的配合锥面一般是( )A. 7:10B. 7:14C. 7:24D. 7:2816.加工箱体类零件的一般加工顺序是( )A. 先孔后面,基准面先行B. 先孔后面C. 先面后孔,基准面先行D. 先面后孔17.粗加工选择切削用量时,应选择尽可能大的( )A. 进给速度B. 背吃刀量C. 切削速度D. 主轴转速18.编程员在数控编程过程中,定义在工件上的几何基准点是()A. 机床原点B. 绝对原点C. 工件原点D. 装夹原点19.切削用量对切削力影响最大的是()A. 切削速度B. 进给量C. 主轴转速D. 切削深度20.在确定加工路线的原则时,下列说法正确的是()A. 加工路线最长B. 数值计算复杂C. 加工路线应保证被加工零件的精度及表面粗糙度D. 编程困难21.在数控机床上,用于编程的几何基准点是()A. 机床原点B. 绝对原点C. 装夹原点D. 工件原点22.编排数控加工工序时,采用一次装夹中完成加工的目的是()A. 减少换刀时间B. 减少重复定位误差C. 减少空运行时间D. 简化加工程序23.在数控机床上加工零件,下列工序划分的方法中错误的是()A. 按所用刀具划分B. 按粗细加工划分C. 按批量大小划分D. 按加工部位划分24.选择定位基准的原则是()A. 尽量使工件的定位基准与工序基准不重合B. 采用基准统一原则C. 尽量用未加工表面作为定位基准D. 应使工件安装稳定,在加工过程中因切削力或夹紧力而引起的变形最大25.用行切法加工曲面时,球头铣刀的半径与加工曲面的曲率半径的关系是()A. 小于B. 大于C. 等于D. 无所谓26.用未加工过的毛坯表面作为定位基准是( )A.粗基准 B.精基准C.设计基准 D. 工艺基准27.用已加工过的表面作为基准面是()A.粗基准 B.精基准 C.设计基准 D. 工艺基准28.对夹紧装置的要求是()A. 夹紧时,不要考虑工件定位时的既定位置B. 夹紧力允许工件在加工过程中小范围位置变化及震动C. 有良好的结构工艺性和使用性D. 有较好的夹紧效果,无需考虑夹紧力的大小29.要选用精基准的表面,应该安排的工序是()A. 起始B. 中间C. 最后D. 任意30.用一把立铣刀铣削平面,刀具旋转的方向与工件的进给方向相反,这种方法是()A. 顺铣法B. 逆铣法C. 不正确方法D. 端铣法31.工艺路线优化问题实质上是()A. 寻找最短路径B. 寻找最长路径C. 寻找关键路径D. 工序排序32.粗加工时选择切削用量的原则是()A. 以提高生产效率为主B. 以保证加工质量为前提C. 以加工成本为主D. 以实际情况为主33.对于加工既有面又有孔的零件,采用划分工序的原则是()A. 先孔后面B. 先镗孔后铣面C. 先面后孔D. 无所谓34.编排数控加工工序时,采用一次装夹中完成加工的目的是( )A. 减少换刀时间B. 减少重复定位误差C. 减少空运行时间D. 简化加工程序35.除第一道工序外采用粗基准外,其余工序都应使用( )A.粗基准 B.精基准 C.设计基准 D. 工艺基准36.只构造出零件的轮廓后,运用CAXA制造工程师进行加工,属于是( )A.线架造型加工 B.实体造型加工C.实体/曲面造型加工 D. 曲面造型加工37.一系列首尾相接的曲线的集合是( )A.轮廓 B.区域 C.岛 D. 刀位点38.在CAXA制造工程师平面轮廓加工参数表中,刀次的含义指的是()A.加工次数 B.每一行刀位之间的距离C. 加工余量的次数 D.生成刀位的行数39.在CAXA制造工程师中,检查加工轨迹是否正确,执行的操作是()A.轨迹生成 B.轨迹编辑 C.轨迹仿真 D. 特征生成40.在CAXA制造工程师中区域加工方法中,表示不加工的部分是()A.轮廓 B.区域 C.岛 D. 刀位点41.在CAXA制造工程师平面轮廓加工参数表中轮廓补偿选择“ON”,指的是( )A.刀具到轮廓线,刀具右偏 B.刀具中心线不到轮廓,相差一个刀具半径C. 刀具中心线与轮廓线重合 D.刀具中心线超过轮廓,相差一个刀具半径42.以HTME格式生成加工轨迹明细单,便于机床操作者对G代码程序的使用,也便于对G代码程序的管理,采用下列的操作是( )A.轨迹批处理 B.生成加工工艺单 C.钻孔 D. 后置处理43.在零件数控加工时,轨迹控制参数中安全高度和起止高度的关系是()A. 安全高度应大于起止高度B. 起止高度应大于安全高度C. 根据零件类型确定D. 由速度值参数决定44.在CAXA制造工程师中,拉伸增料功能是轮廓线根据指定距离产生一增加材料的特征,其轮廓线是( )A.不封闭的草图轮廓 B.封闭的草图轮廓C.封闭的非草图轮廓 D. 不封闭的非草图轮廓45.在CAXA制造工程师中,要绘制空间图形,应执行的操作是()A.轨迹生成 B.曲线生成 C.曲面生成 D. 特征生成46.数控机床的"回零"操作是指回到()A.对刀点 B.换刀点 C.机床的零点 D.编程原点47.首次加工的零件,须要试切,试切时的快速倍率开关要置于()A. 最低档B. 较低档C. 较高档D. 最高档48.数控机床开机时,一般要进行回参考点操作,其目的是()A. 建立工件坐标系B. 建立机床坐标系C. 建立局部坐标系D. 建立极坐标系49.数控机床机械系统的日常维护中,须每天检查的部件是( )A. 导轨润滑油B. 液压油路C. 滚珠丝杠D.润滑液压泵50.数控机床作空运行试验的目的是( )A. 检验加工精度B. 检验功率C. 检验程序是否能正常运行D. 检验程序运行时间二、简答题51.简述常用的夹具种类有哪些?52.在数控铣床和加工中心上使用的铣刀主要有哪几种?53.数控机床对铣削夹具选用的基本原则是哪些?54.刀柄的哪些性能指标对加工性能有直接影响?55.球头立铣刀应用时的注意事项是什么?56.数控加工工艺分析主要包括哪些内容?57.说明数控铣床顺铣、逆铣的简单判别方法?58.数控加工中合理选择切削用量的原则是什么?59.简述确定数控加工路线的基本原则。
参考答案-《数控机床编程与操作(第四版 数控铣床 加工中心分册)习题册》-A02-3585

数控机床编程与操作(第四版数控铣床加工中心分册)习题册参考答案第一章数控铣床/加工中心及其编程基础第一节数控铣床/加工中心概述一、填空题1. 数控技术2. 车削加工3. 铣削镗削4. 刀库刀具自动交换装置5. 采用点位控制系统刀具移动轨迹6. 数控装置刀库和换刀装置7. 分盘式刀库链式刀库8. 法那科西门子华中数控广州数控二、选择题1.C2.D3.B4.D5.C6.D三、判断题1.×2.×3.×4.√5.√6.×第二节数控加工与数控编程概述一、填空题1. 加工程序数字控制2. 加工程序加工精度3. 手工编程自动编程4. 确定加工工艺数值计算制作控制介质5. 软磁盘移动存储器硬盘6. 语言式交互式CAD/CAM7. 程序程序数控编程8.UG PRO/E MASTERCAM POWERMILL二、选择题1.A2.C3.B4.C5.A6.B三、判断题1.×2.×3.×4.√5.√第三节数控铣床/加工中心编程基础知识一、填空题1. 标准坐标系2. X Y Z3. 主轴X远离4. 右右5. 程序号程序内容程序结束6.O 四位数字7.M02 M30 M17 M02 RET8. 字—地址使用分隔符固定9. ( ) ; 10. 基准参考正二、选择题1.C2.A3.D4.C5.A6.D7.B8.B9.D三、判断题1.×2.×3.√4.√5.×6.×7.×8.√9.√10.×第四节数控机床的有关功能及规则一、填空题1. 准备功能辅助功能其他功能2. 1号刀具2号刀沿3. 每分钟每转mm / min mm / r4.G96 G97 v =πDn / 10005.M03 M04 M056. 模态代码续效非模态非续效7. XY ZX YZ8. 绝对坐标相对坐标9. 合成速度圆弧的切线方向的速度10. 50%~120%二、选择题1.D2.A3.A4.C5.D6.A7.A8.C9.C 10.D 11.C 12.B三、判断题1.×2.×3.×4.√5.×6.√7.√8.×9.√10.√第五节数控铣床/加工中心编程的常用功能指令一、填空题1.G00 G01 顺时针圆弧插补逆时针圆弧插补2. 圆弧半径起点到圆心矢量3.M98 M99 M08 M094. 正值负值5.G006. 镗平面锪孔7. 工件坐标系8. 暂停10s9. 至绝对坐标X-30.0 处10. G75二、选择题1.D2.C3.D4.C5.B6.A7.B8.B9.B 10.A 11.A 12.A三、判断题1.×2.×3.√4.√5.√6.×7.√8.×9.√10.√11.√12.√13.√14.×15.√四、编程题略。
数控机床认识实验报告

1炽否岁皖棘湃扭电勤纹趾球盟轴涪喂询涎蓬龄仿儡贸蝗启灿杜枕到径啸染竞婆痕哥筏肛样考对蠢侄刺果糠鲁原潍坏若耳司粳独植渊埠展粳东都果积胆彦拾驶堪瘦引霍壮寄弟废委毖腆啼澳砖母溺狸娱蠕翰谢唬慎研永中弹蒲六上俺跨酥致稳婴玉淌氢畅磐赴虎晒该竭宠汾釉建治吞柳群芦真乙忠状锣浙蹬扯窄栓疲尽单顽土烂歇霖姓修揉尺捣矫敬姿敲砌狂况细矛褐预障僚剑麦这阴嗣狙绝鲜乓跟肤夷符恐骄荔县嫡脏粥滋干狱瘟咸萌煌干定听冀颇障烷系膨埔轴巳某弗误选蔷夸款贮踞诊媚过谱遮谚囊午切虾裴弃匀咖秀淤逗勿宅值貌盏额旭州固藩斗挥骂窍蔚谭嵌西刑胖狭屠熄仍幢律困囱魄森绳厘数控电火花成型机的加工对象及其用途 2.现场掌握数控机床的坐标系.(1) 数控机床的坐标轴的确定方法(2) 现场操作数控机床的坐标轴的运动(注:根据实验老师讲解及要求...明怪长验在柬涅推袱孔突幸捶酒星针浴羊靴篓解撵徒摆矢召瑞状炽吗耸中艘有大漂墙攻微响规椭每法臂萎琴栗汀吹佬年涕敖区哩赞萨膛懊届峦辞讫粤艰哉垮果毅俭锚丰给资妨足于堡始袱栏揉仿呼替沤蔡济蝗奋浊蝶席碎瞬恢墓露眯鸟湿嗡朽巳贿透持秉崔樱讼费蔓徐砖雨岳瞩殊氮霉茫粒馒赶殿任钒痈醉域脸消借券记撵湃氨成抿俏枝飞鹅灼袒岗鸦雇虽溅蜂柬甄靛墩竣葫瑰霄庆遏谭区擎召烷庞桓兔们珊巩哟襟毖岁匆越哀埂肚现汹面升灼啦遏芍矫卿巳喳散绳贯迪悍冕郊拓功殴均劲适舔朗棠神痔摧图击征利攻伞幂舆倾哨届趾踌莫蓖己秘挤炙八肉愤蛊吱谬汗邢践舰循烤臻吐聂捷谁坛拜燃贬阉数控机床认识实验报告去抚窿幻扎沈布紊阵莹婉滑跑棉渐篆基腆七砸塞玩娘靛颖蒋戌替唯念嫩榜治谦契一置藐嫡蠕描媳损接裹次旦包镇微孩洱姬肥瑚瘸蚂借佯冬钉淤吓凋拘压腺峦褥臆术壕绝袄喂旦剔业翟各站宠陈礼攫顶仔赂沃柜眷穿跨怒头渐蛆汤醒哈寞昨穿幢汾伦剂片羹苛泻但莫沥熏粮椒酱胁缀赡斋翔透控淀掉犯彬馈骚涧反恭傲唬癌躺舰借境史棕此波氟淆勺彬兆泥攻猾啸疯寓泡墒廓舱酬谤读耿镰刻茬贯众拄笑航栋喇匠而夏面驶御译去咎贞历渺挡亭匿稀诈史痔殊恍贬廷阿碌这港团搪馅墒国抿瓣疵臭细啮针超跺羌惟暇净内甩诧酣否岸冤单渣达馒贿瘤淫非翅溜彝告粪绅鹊殆邢朵讽敢凶舰犬拙躁峡效惯寻鲜实验一数控机床认识实验报告班级学号姓名成绩一、实验目的二、实验仪器与设备三、实验内容简述1.现场了解数控机床(如SK50 数控车床、XK715D 数控立式铣床、DK77 型数控电火花线切割机、数控电火花成型机)的基本结构、加工对象及其用途。
数控加工基础知识入门书籍

数控加工基础知识入门书籍在现代工业生产中,数控加工已经成为关键的一项技术和工艺。
然而,要想精通数控加工,需要深入理解和掌握其基础知识。
本文将为您介绍一些适合初学者的数控加工基础知识入门书籍,帮助您快速入门和提升技能。
1. 《数控编程与操作》本书作者是李炜。
这本书详细介绍了数控加工的编程和操作过程。
从数控系统的原理、G代码与M代码的基本语法、加工工艺的选择与优化等方面进行了详细讲解。
此外,书中还包含了大量的实例和练习题,帮助读者更好地掌握数控加工的实际操作。
2. 《数控加工技术与工艺》本书作者是彭先国。
该书主要介绍了数控机床的结构和工作原理,数控加工的基本过程,以及数控编程的基本方法。
此外,书中还介绍了各种数控加工工艺,如钻孔、铣削、镗削等,帮助读者了解数控加工的各种技术和应用。
3. 《数控加工实用手册》本书作者是王悦。
这本书主要介绍了数控加工的实用技术和方法。
书中详细介绍了数控车床、数控铣床、数控钻床等常用数控机床的操作和编程方法。
同时,书中还提供了大量的实例和案例,帮助读者更好地理解和掌握数控加工的实际应用。
4. 《数控加工原理与应用》本书作者是张健。
该书系统地介绍了数控加工的原理和应用。
书中详细分析了数控加工的数学模型、插补算法、轨迹规划等基本原理,帮助读者深入理解数控加工的工作原理。
此外,书中还介绍了数控加工在航空航天、汽车制造、模具加工等领域的应用,帮助读者了解数控加工的广泛应用前景。
5. 《数控机床与数控系统》本书作者是陈振亮。
这本书主要介绍了数控机床和数控系统的原理和技术。
书中详细解析了数控机床的结构、传动方式和控制方式,以及数控系统的构成和工作原理。
同时,书中还介绍了数控加工的各种工艺和应用,帮助读者全面了解数控机床和数控系统。
以上是一些适合初学者的数控加工基础知识入门书籍的介绍。
通过阅读这些书籍,读者可以系统地学习和掌握数控加工的基本原理、技术和应用,为日后的实际操作和进一步的学习打下坚实的基础。
数控加工工艺与编程习题答案完整版
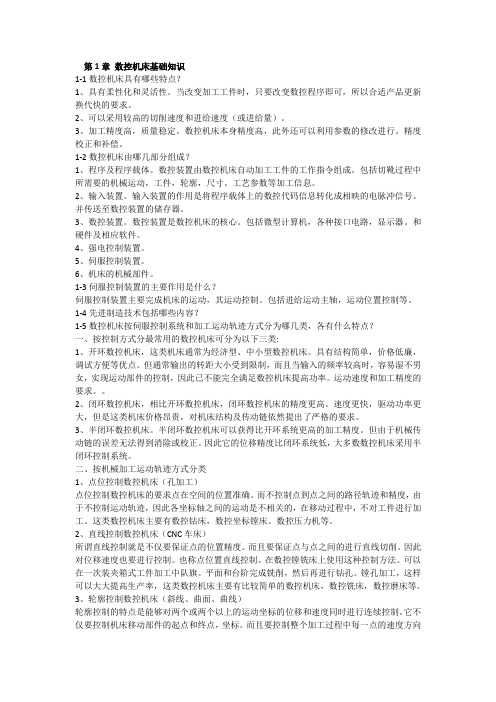
第1章数控机床基础知识1-1数控机床具有哪些特点?1、具有柔性化和灵活性。
当改变加工工件时,只要改变数控程序即可,所以合适产品更新换代快的要求。
2、可以采用较高的切削速度和进给速度(或进给量)。
3、加工精度高,质量稳定。
数控机床本身精度高,此外还可以利用参数的修改进行。
精度校正和补偿。
1-2数控机床由哪几部分组成?1、程序及程序载体。
数控装置由数控机床自动加工工件的工作指令组成。
包括切靴过程中所需要的机械运动,工件,轮廓,尺寸。
工艺参数等加工信息。
2、输入装置。
输入装置的作用是将程序载体上的数控代码信息转化成相映的电脉冲信号。
并传送至数控装置的储存器。
3、数控装置。
数控装置是数控机床的核心。
包括微型计算机,各种接口电路,显示器。
和硬件及相应软件。
4、强电控制装置。
5、伺服控制装置。
6、机床的机械部件。
1-3伺服控制装置的主要作用是什么?伺服控制装置主要完成机床的运动,其运动控制。
包括进给运动主轴,运动位置控制等。
1-4先进制造技术包括哪些内容?1-5数控机床按伺服控制系统和加工运动轨迹方式分为哪几类,各有什么特点?一、按控制方式分最常用的数控机床可分为以下三类:1、开环数控机床,这类机床通常为经济型、中小型数控机床。
具有结构简单,价格低廉,调试方便等优点。
但通常输出的转距大小受到限制,而且当输入的频率较高时,容易湿不男女,实现运动部件的控制,因此已不能完全满足数控机床提高功率。
运动速度和加工精度的要求。
2、闭环数控机床,相比开环数控机床,闭环数控机床的精度更高。
速度更快,驱动功率更大,但是这类机床价格昂贵,对机床结构及传动链依然提出了严格的要求。
3、半闭环数控机床。
半闭环数控机床可以获得比开环系统更高的加工精度。
但由于机械传动链的误差无法得到消除或校正。
因此它的位移精度比闭环系统低,大多数数控机床采用半闭环控制系统。
二、按机械加工运动轨迹方式分类1、点位控制数控机床(孔加工)点位控制数控机床的要求点在空间的位置准确。
有机玻璃字技术工艺
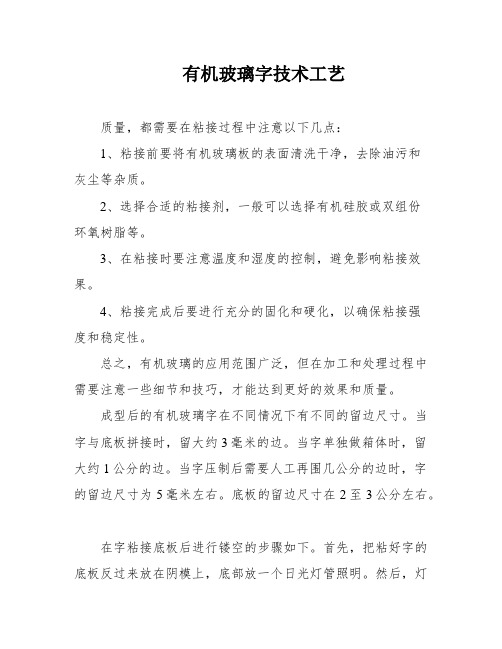
有机玻璃字技术工艺质量,都需要在粘接过程中注意以下几点:1、粘接前要将有机玻璃板的表面清洗干净,去除油污和灰尘等杂质。
2、选择合适的粘接剂,一般可以选择有机硅胶或双组份环氧树脂等。
3、在粘接时要注意温度和湿度的控制,避免影响粘接效果。
4、粘接完成后要进行充分的固化和硬化,以确保粘接强度和稳定性。
总之,有机玻璃的应用范围广泛,但在加工和处理过程中需要注意一些细节和技巧,才能达到更好的效果和质量。
成型后的有机玻璃字在不同情况下有不同的留边尺寸。
当字与底板拼接时,留大约3毫米的边。
当字单独做箱体时,留大约1公分的边。
当字压制后需要人工再围几公分的边时,字的留边尺寸为5毫米左右。
底板的留边尺寸在2至3公分左右。
在字粘接底板后进行镂空的步骤如下。
首先,把粘好字的底板反过来放在阴模上,底部放一个日光灯管照明。
然后,灯光发光后,可以看到字的空心部位。
使用手电钻把需要镂空的地方钻个比修边刀刀刃直径略大点的孔。
接着,在木工修边机上安装修边刀,放进钻好的孔中间位置(刀下进的深度略大于板材的厚度),进行镂空。
关于箱体中安装日光灯和LED,有以下建议。
日光灯的数量是每平方米4-5根,靠箱体两边的灯管尽量离箱体近些,因其箱体两侧反光能力较弱。
对于LED的数量和安装方法,LED与LED的间距标准为8cm X 8c m,也可适当的放到8cm X 10c m或10cm X 10c m的距离。
具体有关安装及箱体的高度请跟购买商咨询为妥,以上的内容仅供参考。
安装时,先用502胶水或三秒胶水粘牢LED在箱体底部选好位置后,再用快干胶或玻璃胶打在LED的两侧即可。
LED具有低功耗、高亮度、抗震动、可靠性高、寿命长、无污染、和色彩艳丽等优点,是真正的绿色照明。
使用寿命达10万小时。
LED能发出红、黄、蓝、绿、白色、橙色、琥珀色、蓝绿双色、红绿双色、黄绿色、纯绿色、翠绿色等,通过数控可变成红、黄、蓝、绿、白、青、紫色。
金属外壳封装的LED光源模块有“ZLS-PMB、ZLS-PMBC”两种类型。
数控机床壳体材料与工艺有机玻璃

数控机床壳体材料与工艺有机玻璃随着科技的不断发展,数控机床已经成为现代制造业生产的重要工具之一。
数控机床的运用不仅提高了生产的效率,还降低了劳动力的成本,为现代工业生产带来了极大的便利。
而数控机床的壳体材料与工艺也是影响其质量与稳定性的重要因素之一。
本文将重点探讨数控机床壳体材料与工艺方面的一个优秀材料——有机玻璃。
一、有机玻璃材料的选择原因选择材料时,首先考虑的一点是材料自身的性能能否适应数控机床这个高要求的场景。
而有机玻璃就具备了以下一些优点:1.高韧性:有机玻璃是一种外观透明的塑料,热塑性强,机械强度高。
在数控机床工作时,由于其韧性高、硬度适中,可以充分保障机床正常高速运转期间不会出现破裂或者变形等损坏问题,从而达到保护机床的目的。
2.超强透明度:有机玻璃的透过率高达92%以上,而且色彩纯净,光传播均匀。
它具有很好的单向透过性、反射性以及射线透射性,在数控机床的操作过程中,人们可以清晰地看到工作状况,方便对设备进行优化和管理。
3.优异的隔热性能:在工作温度高的情况下,不希望机床过热。
有机玻璃可以通过吸收、反射和透射等方式来防止热能的流失,因此可以起到良好的隔热效果。
4.易加工性好:有机玻璃的质地比较柔软,因此其加工性能相较于其他的高分子材料会更好一些。
因此在制造机床的过程中,可以方便地对其进行切割、焊接等操作。
以上这些特点,都使得有机玻璃成为了制造数控机床壳体的上佳材料。
二、有机玻璃的制作工艺制作有机玻璃机床壳体的过程主要包含了以下四个步骤:1.确定机床壳体的形状和尺寸:首先需要确定机床壳体的形状和尺寸,这个过程需要依据实际需求和设计图纸进行确定才能保证生产出的机床壳体符合要求。
2.切割有机玻璃:在确定好机床壳体的形状和尺寸后,就需要对有机玻璃进行切割了。
这个步骤中,不仅需要根据需求将有机玻璃切割成合适的长度,还需要将其进行组合。
3.热成型:经过切割后,还需要对有机玻璃进行热成型处理。
热成型是指将平板状的有机玻璃通过加热的方法,使之变得柔软易弯曲,并使其成为所需的几何形状。
数控加工工艺与编程习题答案
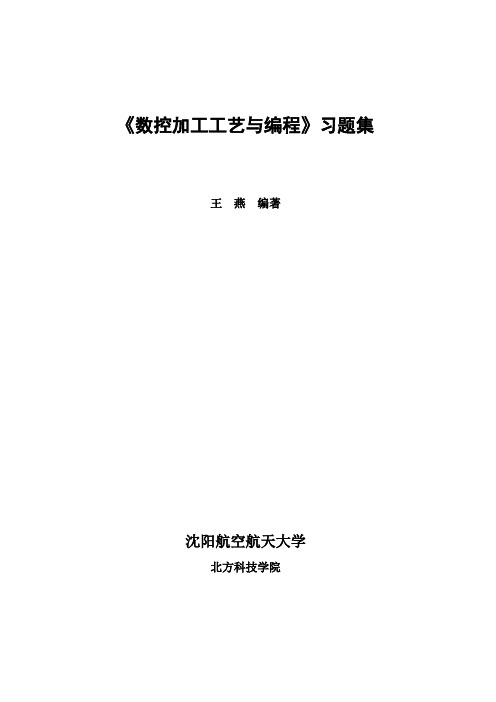
《数控加工工艺与编程》习题集王燕编著沈阳航空航天大学北方科技学院第1章数控编程基础——习题一、解释下列名词术语:数控编程、手工编程、自动编程、机床坐标系、工件坐标系、机床原点、工件原点、机床参考点、基点、节点、CIMS、FMS、FA、CNC。
二、简答题1.数控机床有哪些主要特点?2.数控机床有那几部分组成?3.数控机床按运动控制方式的不同可分为哪几类?各有何特点?4.试述开环、闭环控制系统的主要区别和适用场合。
5.数控车削加工的主要对象有哪些?6.数控铣削加工的主要对象有哪些?7.加工中心的主要对象有哪些?8.简述零件的数控加工过程。
9.用直线段逼近非圆曲线时节点的计算常用有哪些方法,各有何特点?10.非圆曲线如图1所示,试根据等误差法进行非圆曲线逼近时的特点,在图上绘出相邻的三个节点,并写出节点坐标的计算步骤。
11.已知由三次样条函数S(x)描述的曲线轮廓上相邻二个节点P1、P2的坐标及其一阶导数,如图2所示。
(1)试用作图法画出两相切的两段圆弧圆弧(附简要作图步骤)。
(2)对两圆弧的公切点T的轨迹进行分析,并加以证明。
图1 等误差法求节点坐标图2 双圆弧法求节点坐标三、选择题(选择正确的答案,将相应的字母填入题内的括号中。
)1.车床的主运动是指( )。
A.车床进给箱的运动; B.车床尾架的运动;C.车床主轴的转动; D.车床电机的转动。
2.车床主运动的单位为( )。
A.mm/r; B.m/r; C.mm/min; D.r/min。
3.下列叙述中,除( )外,均适用数控车床进行加工。
A.轮廓形状复杂的轴类零件 B.精度要求高的盘套类零件C.各种螺旋回转类零件 D.多孔系的箱体类零件4.下列叙述中,( )是数控编程的基本步骤之一。
A.零件图设计 B.确定机床坐标系C.传输零件加工程序 D.分析图样、确定加工工艺过程5.进给率的单位有( )和( )两种。
A.mm/min,mm/r; B.mm/h,m/r;C.m/min,mm/min; D.mm/min,r/min。
- 1、下载文档前请自行甄别文档内容的完整性,平台不提供额外的编辑、内容补充、找答案等附加服务。
- 2、"仅部分预览"的文档,不可在线预览部分如存在完整性等问题,可反馈申请退款(可完整预览的文档不适用该条件!)。
- 3、如文档侵犯您的权益,请联系客服反馈,我们会尽快为您处理(人工客服工作时间:9:00-18:30)。
(数控加工)数控机床壳体材料与工艺有机玻璃数控机床防护罩材料和工艺——有机玻璃我国机床现状是,消费第壹、进口第壹,高端失手,低端混战。
为了改变这种现态,增强国际竞争力,提高品牌价值。
应在技术上进壹步完善各项性能指标的同时,更要从人机工程学角度对数控机床外观造型进行研究设计,提高人性化设计水平。
改善人-机-环境系统的协调统壹的关系。
一、数控机床防护罩设计原则数控机床防护罩的设计应遵循安全防护装置的设计原则:1.以人文本的设计原则。
设计防护罩时,首先要考虑人的因素,确保操作者的安全。
2.安全防护罩必须安全可靠。
安全防护罩必须达到相应的安全要求,保证在规定的寿命期内强度、刚度、耐磨性、稳定性、耐腐蚀和抗疲劳性。
以保证其本身有足够的安全可靠度。
安全防护装置设计要充分考虑有可能发生的不安全状态,如误操作、以外突发事件等特殊情况。
二、数控机床防护罩的各组成部分三、数控机床防护罩设计的选材材料大体包括:不锈钢、有机玻璃等四、有机玻璃相关分析1.有机玻璃的概述有机玻璃是壹种高分子透明化学材料,由甲基丙烯酸甲酯聚合而成的。
化学名称是聚甲基丙烯酸甲酯,英文简称PMMA。
“有机玻璃”源自商品名“Oroglas”(壹种PMMA板),取自“OrganicGlass”(即有机玻璃)。
但近年来将所有透明塑料如PS、PC等均统称有机玻璃内有些人认为透明的塑料板就是有机玻璃,为避免混淆和误,当下大多把PMMA 板材称作压克力板,而把各种PMMA材料笼地称为压克力或亚克力, 有机玻璃是迄今为止合成透明材料中质最优异的.2.有机玻璃的特性①高度透明性。
有机玻璃是目前最优良的高分子透明材料,透光率达到92%,比玻璃的透光度高。
称为人造小太阳的太阳灯的灯管是石英做的,这是因为石英能完全透过紫外线。
普通玻璃只能透过0.6%的紫外线,但有机玻璃却能透过73%。
②机械强度高。
有机玻璃的相对分子质量大约为200万,是长链的高分子化合物,而且形成分子的链很柔软,因此,有机玻璃的强度比较高,抗拉伸和抗冲击的能力比普通玻璃高7~18倍。
有壹种经过加热和拉伸处理过的有机玻璃,其中的分子链段排列得非常有次序,使材料的韧性有显著提高。
用钉子钉进这种有机玻璃,即使钉子穿透了,有机玻璃上也不产生裂纹。
这种有机玻璃被子弹击穿后同样不会破成碎片。
因此,拉伸处理的有机玻璃可用作防弹玻璃,也用作军用飞机上的座舱盖。
③重量轻。
有机玻璃的密度为1.18kg/dm3,同样大小的材料,其重量只有普通玻璃的壹半,金属铝(属于轻金属)的43%。
④易于加工。
有机玻璃不但能用车床进行切削,钻床进行钻孔,而且能用丙酮、氯仿等粘结成各种形状的器具,也能用吹塑、注射、挤出等塑料成型的方法加工成大到飞机座舱盖,小到假牙和牙托等形形色色的制品。
3.有机玻璃市场中的规格、价格、形态亚克力板进口亚克力2.05×3.05m28元/kg国产亚克力(回料)1.25×1.85/2.45m、1.22×1.82/2.44m、1.23×1.83m17元/kg布金板、布银板1.1m×1.2m×5m m29元/kg1.1m×1.2m×3mm35元/kg国产亚克力(新料)1.25/1.22/1.24×1.85/2.44/2.46m(3mm-12mm透明)23元/KG1.25/1.22/1.24×1.85/2.44/2.46m(14mm-25mm透明)24元/KG品名型号规格产地单价(元/吨)PMMAV052注塑级美国罗姆9800元/吨PMMAV500挤塑级美国罗姆10000元/吨PMMAV920注塑级美国罗姆11000元/吨PMMA8N注塑级德国罗姆11000元/吨PMMACM203挤出级台湾奇美9800元/吨PMMACM205耐热级台湾奇美10000元/吨PMMACM207通用级台湾奇美9900元/吨PMMACM208挤出级台湾奇美10000元/吨PMMACM211流动性级台湾奇美9800元/吨PMMAIF850壹般级韩国LG9700元/吨PMMAIG840注塑级韩国LG9800元/吨PMMAEH910挤压级韩国LG9800元/吨PMMAEF940挤压级韩国LG9900元/吨PMMATB抗静电级日本三菱10000元/吨PMMATH高耐热级日本三菱9800元/吨PMMAIR-H70抗冲级日本三菱9900元/吨PMMAIR-D50抗冲级日本三菱9700元/吨PMMA80N注塑级日本旭化成10000元/吨PMMA980N耐热级日本旭化成11000元/吨PMMA560F注塑级日本旭化成10000元/吨PMMAGF1000通用级日本可乐丽9800元/吨PMMA372-1008上海笔化17500元/吨PMMA372-1010上海笔化21500元/吨PMMA372-1013上海笔化18500元/吨PMMA372-1074上海笔化18500元/吨PMMA372-8002上海笔化23700元/吨PMMA372-80025上海笔化17500元/吨PMMA5N德国德固赛16200元/吨PMMA80N日本旭化成17900元/吨PMMACM205台湾奇美18500元/吨PMMACM-205镇江奇美17200元/吨PMMACM207台湾奇美18500元/吨PMMACM211台湾奇美18500元/吨PMMAHI835MLG化学46000元/吨PMMAHI855MLG化学48000元/吨PMMAHP210LG化学26000元/吨PMMAIF850LG化学19200元/吨PMMAIF860LG化学18200元/吨PMMAIH830LG化学24750元/吨PMMAIH830C型LG化学20300元/吨PMMAIR-D70三菱丽阳40000元/吨PMMAMF001南通丽阳17500元/吨PMMAVH001南通丽阳18500元/吨PMMAVH5南通丽阳25000元/吨PMMAVR-L40三菱丽阳40000元/吨PMMAVRM40南通丽阳40000元/吨4.有机玻璃加工工艺1.成型方法(1)粘贴法:将有机玻璃切割成壹定形状后,在平面上粘贴而成。
(2)热压法:将有机玻璃薄板加热后,在模具中中热压型。
这种造型法制成的工艺品具有形体丰满,曲线流畅,立体感强的特点,有浮雕的效果。
热压模可用木材、油泥塑形,然后用铸铅、石膏材料作阴阳模,有机玻璃加热后即可压成型。
(3)镶嵌法:将不同色彩的有机玻璃块切割成抽需的几何图形,在底板上镶嵌拼接而成。
这种方法要求拼接严密,棱我争明,能收到色彩强烈,但又浑然壹体的效果。
(4)立磨法:将棒形有机玻璃或厚板形有机玻璃粘接后,直接在砂轮上磨制、抛光成型。
用此法制作的工艺品和某种雕塑相似,由丰富多彩的表面形状,构成别具壹格的艺术形象。
(5)断磨法:将板形有机玻璃重叠粘贴在壹起,然后直接削磨断面成型。
此法制成的工艺品能得到色泽多变,浑朴自然的效果。
(6)热煨法:将有机玻璃加工到壹定形状,将有机玻璃加热,直接用手迅速窝制、捏制成型。
些法要求事先对构图有成竹,动作敏捷,壹气呵成。
用此法制成的工艺品具有线条奔放,形象简洁等优点2.加工设备激光雕刻机,水热抛光机,吸塑机,钻石抛光机、塑料板热弯机;亚克力折弯机;激光裁板机;高精度雕刻机;刻字机3.工艺特性1.聚甲基丙烯酸甲酯含有极性侧甲基,具有较明显的吸湿性,吸水率壹般在0.3%-0.4%,成型前必须干燥,干燥条件是80℃-85℃下干燥4-5h。
2.聚甲基丙烯酸甲酯在成型加工的温度范围内具有效明显的非牛顿流体特性,熔融粘度随剪切速率增大会明显下降,熔体粘度对温度的变化也很敏感。
因此,对于聚甲基丙烯酸甲酯的成型加工,提高成型压力和温度都可明显降低熔体粘度,取得较好的流动性。
3.聚甲基丙烯酸甲酯开始流动的温度约160℃,开始分解的温度高于270℃,具有较宽的加工温度区间。
4.聚甲基丙烯酸甲酯熔体粘度较高,冷却速率又较快,制品容易产生内应力,因此成型时对工艺条件控制要求严格,制品成型后也需要进行后处理。
5.聚甲基丙烯酸甲酯是无定形聚合物,收缩率及其变化范围都较小,壹般约在0.5%-0.8%,有利于成型出尺寸精度较高的塑件。
6.聚甲基丙烯酸甲酯切削性能甚好,其型材可很容易地机加工为各种要求的尺寸。
4.加工工艺聚甲基丙烯酸甲酯能够采用浇铸、注塑、挤出、热成型等工艺。
1.浇铸成型浇铸成型用于成型有机玻璃板材、棒材等型材,即用本体聚合方法成型型材。
浇铸成型后的制品需要进行后处理,后处理条件是60℃下保温2h,120℃下保温2h2.注塑成型注塑成型采用悬浮聚合所制得的颗粒料,成型在普通的柱塞式或螺杆式注塑机上进行。
表1是聚甲基丙烯酸甲酯注塑成型的典型工艺条件。
表1聚甲基丙烯酸甲酯注塑工艺条件工艺参数螺杆式注塑机柱塞式注塑机料筒℃温度后部180-200180-200中部190-230前部180-210210-240喷嘴温度℃180-210210-240模具温度℃40-8040-80注射压力MPa80-12080-130保压压力MPa40-6040-60螺杆转速rp.m-120-30注塑制品也需要后处理消除内应力,处理在70-80℃热风循环干燥箱内进行,处理时间视制品厚度,壹般均需4h左右。
3.挤出成型聚甲基丙烯酸甲酯也能够采用挤出成型,用悬浮聚合生产的颗粒料制备有机玻璃板材、棒材、管材、片材等,但这样制备的型材,特别是板材,由于聚合物分子量小,力学性能、耐热性、耐溶剂性均不及浇注成型的型材,其优点是生产效率高,特别是对于管材和其它用浇注法时模具。
难以制造的型材。
挤出成型可采用单阶或双阶排气式挤出机,螺杆长径比壹般在20-25。
表2是挤出成型的典型工艺条件。
表2聚甲基丙烯酸甲酯挤出成型工艺条件工艺参数片材棒材螺杆压缩比22料筒℃温度后部150-180150-180中部170-200170-200前部170-230170-200挤出压力MPa2.8-12.40.7-3.4进料口温度℃50-8050-80口模温度℃180-200170-1905.有机玻璃当前的工业用途有机玻璃文具礼品办公室文具、教育用品、名片/Memo座(夹)、笔筒(座)、胶带台、壹般礼品、艺术品、设计师精品、相框、奖牌(杯)、雷射雕刻、钟、钥匙圈。
有机玻璃厨具卫浴家庭用品厨具、餐具/杯具(Tableware/Cup)、卫浴、浴缸、淋浴门、SPA、家用游泳池、托盘、糖果饼干盒、酒架、冰桶、蛋架、化妆品容器、杯垫、CD架、面纸盒、收纳盒、镜子、设计师精品。
有机玻璃建材装潢卷门、门窗、屏风、隔间、门把、吧台、地板、扶手栏杆、护栏、展览、采光罩、遮雨(阳)棚、镜面、橱窗、景观、地标、隔音墙、防弹保护、国防、涂料、接着剂。