中厚板生产课程设计指导书..
30×2100×6000(Q215) 中厚板生产规程设计
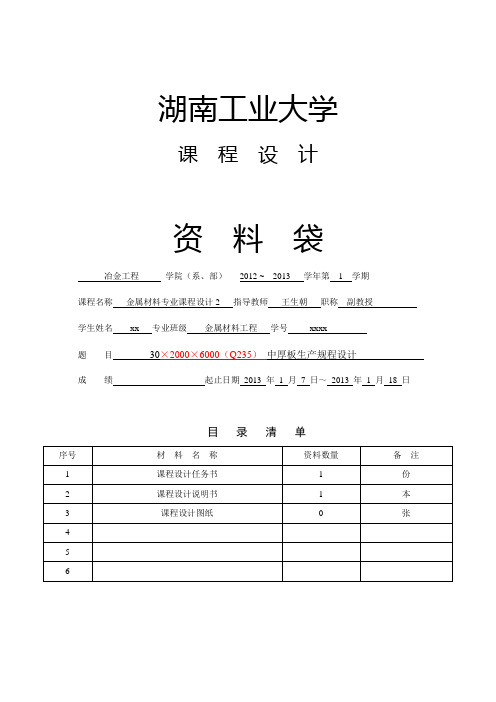
湖南工业大学课程设计资料袋冶金工程学院(系、部)2012 ~ 2013 学年第 1 学期课程名称金属材料专业课程设计2 指导教师王生朝职称副教授学生姓名xx 专业班级金属材料工程学号xxxx题目30×2000×6000(Q235)中厚板生产规程设计成绩起止日期2013 年1 月7 日~2013 年1 月18 日目录清单金属材料专业课程设计2设计说明书30×2000×6000(Q235)中厚板生产规程设计起止日期:2013 年 1 月7 日至2013 年 1 月18 日学生姓名xxx班级金属材料093班学号xxxx成绩指导教师(签字)冶金工程学院2013年1月17 日湖南工业大学课程设计任务书2012 —2013 学年第 1 学期冶金工程学院学院金属材料工程专业金属材料093 班级课程名称:金属材料专业课程设计2设计题目:30×2000×6000(Q235)中厚板生产规程设计完成期限:自2013 年 1 月7 日至2013 年 1 月17 日共两周指导教师(签字):王生朝2013年 1 月7 日系主任(签字):王生朝2013年1 月7 日冶金工程学院课程设计指导教师评阅表冶金工程学院课程设计答辩及最终成绩评定表说明:采用百分制计分,最终评定成绩=答辩评分(20%)+指导教师评分(80%),根据综合分值给出相应等级。
目录1 制定生产工艺 (1)1.1制定生产工艺 (1)1.2制定工艺制度 (1)2 制定压下规程 (1)2.1原料设计 (1)2.1.1原料的质量 (1)2.1.2原料的尺寸 (2)2.2轧制规程的设计 (2)2.2.1坯料的选择 (2)2.2.2道次压下量分配的影响因素 (2)2.2.3道次压下量的分配规律 (3)2.3轧制速度制度 (5)2.3.1轧辊的咬入和抛出转速及轧辊加速度的确定 (5)2.3.2最大轧制转速及最大轧制速度的确定 (5)2.3.3纯轧时间及间隙时间的确定 (6)2.4温度制度的确定 (8)2.5变形制度的确定 (9)2.5.1变形程度的计算 (9)2.5.2平均变形速度 (10)2.5.3变形抗力的计算 (10)2.6轧制力能参数计算 (13)2.6.1轧制压力的计算 (13)2.6.2计算各道传动力矩 (14)典型产品生产规程设计1 制定生产工艺1.1制定生产工艺选择坯料→原料清理→加热→除磷→横轧两道次(使宽度接近成品宽度)→转90°纵轧到底→矫直→冷却→表面检查→切边→定尺→表面尺寸形状检查→力学性能检测→标记→入库→发货。
中厚板设计

1 产品方案与坯料的选择1.1 产品方案的主要内容产品方案是设计任务书的主要内容之一,是进行车间设计时制定产品生产工艺过程中,确定轧机组成和选择各项设备的主要依据。
制定产品方案的主要原则:(1)满足国民经济发展对轧制产品的需求,特别是根据市场信息解决某些短缺产品的供应和优先保证国民经济重要部门对与钢材的需要。
(2)考虑各类产品的平衡,尤其是地区之间产品的平衡。
要正确处理长远与当前,局部和整体的关系。
做到供应适合,品种平衡。
产销对路,布局合理,要防止不顾轧机特点,不顾车间具体工艺设备条件一哄而上,一哄而下的倾向。
(3)考虑轧机生产能力的充分利用和建厂地区的合理分工。
有条件的要争取轧机的专业化和产品系列化的发展,以利于提高轧机生产技术水平。
(4)考虑建厂地区资源及环境条件,物资和材料等道路运输情况,逐步完善和配套起我国自己的独立的轧钢生产体系。
(5)要逐步解决产品品种和规格老化问题要适应当前对外开放,对内搞活新的经济形式的需要,要根据车间工业设备的情况,力争做到产品结构和产品标准的现代化,有条件的考虑生产一些出口产品,走向国际市场。
产品方案的主要内容包括:(1)车间生产的钢种和生产的规模;(2)各类产品的品种和规格(3)种类产品的数量和其在总量中所占的比例。
各种产品的品种和规格及种类产品的数量和其在总量中所占的比例如表所示表1-1中厚板产品方案(典型产品:1.2金属平衡表成品率的倒数即为金属的消耗系数。
它表示轧制一吨成品需要多少吨原料。
所以成品的数量乘以1金属消耗系数就是金属的需要量。
即:原料需要量=金属消耗系数×成品数量为分析轧钢生产中金属的损失,寻找降低损失的途径。
须编制金属平衡表按本次设计要求。
本设计只列出典型产品的金属平衡表。
单位(万t)表1-2金属平衡表1.3坯料的技术条件1.3.1中厚板的坯料选用中厚板生产采用的原料有扁锭、初扎坯、连铸坯、三种。
中厚板生产压下规程设计
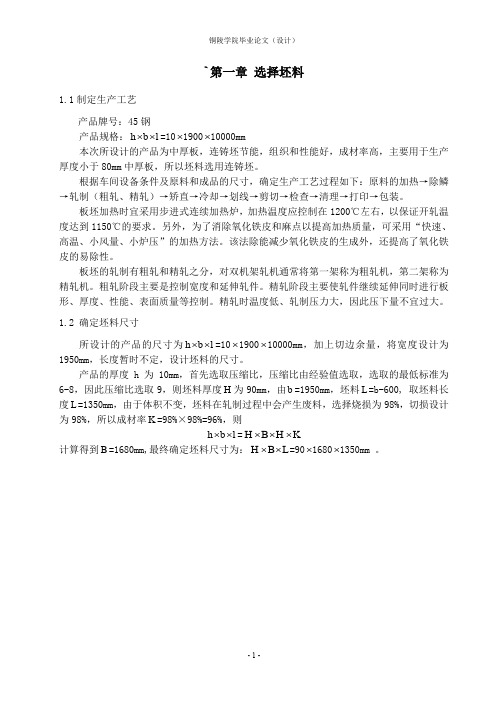
`第一章选择坯料1.1制定生产工艺产品牌号:45钢产品规格:l⨯=10⨯1900⨯10000mmbh⨯本次所设计的产品为中厚板,连铸坯节能,组织和性能好,成材率高,主要用于生产厚度小于80mm中厚板,所以坯料选用连铸坯。
根据车间设备条件及原料和成品的尺寸,确定生产工艺过程如下:原料的加热→除鳞→轧制(粗轧、精轧)→矫直→冷却→划线→剪切→检查→清理→打印→包装。
板坯加热时宜采用步进式连续加热炉,加热温度应控制在1200℃左右,以保证开轧温度达到1150℃的要求。
另外,为了消除氧化铁皮和麻点以提高加热质量,可采用“快速、高温、小风量、小炉压”的加热方法。
该法除能减少氧化铁皮的生成外,还提高了氧化铁皮的易除性。
板坯的轧制有粗轧和精轧之分,对双机架轧机通常将第一架称为粗轧机,第二架称为精轧机。
粗轧阶段主要是控制宽度和延伸轧件。
精轧阶段主要使轧件继续延伸同时进行板形、厚度、性能、表面质量等控制。
精轧时温度低、轧制压力大,因此压下量不宜过大。
1.2 确定坯料尺寸所设计的产品的尺寸为l⨯=10⨯1900⨯10000mm,加上切边余量,将宽度设计为bh⨯1950mm,长度暂时不定,设计坯料的尺寸。
产品的厚度h为10mm,首先选取压缩比,压缩比由经验值选取,选取的最低标准为6-8,因此压缩比选取9,则坯料厚度H为90mm,由b=1950mm,坯料L=b-600, 取坯料长度L=1350mm,由于体积不变,坯料在轧制过程中会产生废料,选择烧损为98%,切损设计为98%,所以成材率K=98%×98%=96%,则h⨯⨯=KblH⨯⨯⨯HB计算得到B=1680mm,最终确定坯料尺寸为:L⨯=90⨯1680⨯1350mm 。
H⨯B第二章变形量分配2.1 确定轧制方法先经过二辊轧机纵轧一道,在不考虑切边的情况下,使板坯长度等于成品宽度,然后转90°横轧到所需规格。
2.2 确定道次压下量坯料尺寸:LBH⨯⨯ =90⨯1680⨯1350mm,则总的压下量为90-10=80mm。
中厚板课程设计-16Mng中厚板轧制规程的编制

大学课程设计说明书设计题目:16Mng中厚板轧制规程的编制学院:专业班级:学生姓名:指导教师:成绩:2014 年月日1.前言.......................................................................................... 错误!未定义书签。
1.1中厚板产品品种 (3)1.2中厚板用途 (4)1.3 16Mng的特性及用途 (4)2.中厚板生产工艺流程简介 (5)2.1中厚板生产工艺 (5)2.2原料的加热 (6)2.3 除鳞 (6)2.4粗轧 (7)2.5精轧 (7)2.6精整与热处理 (7)3.压下规程设计 (7)3.1选择坯料 (8)3.2坯料尺寸的确定 (9)3.3确定轧制方法 (9)3.4确定轧制道次、压下量及压下率 (10)3.4.1校核咬入能力 (10)3.4.2压下量的分配和压下率 (10)3.5速度制度 (11)3.6温度制度 (13)3.7轧制力计算 (14)3.7.1平均单位压力 (14)3.7.2总轧制力的计算 (15)3.8计算传动力矩 (16)3.8.1轧制力矩的计算 (16)3.8.2附加摩擦力矩的计算 (17)3.8.3 空转力矩的计算 (17)3.8.4动力矩的计算 (18)4.辊型设计计算 (18)4.1辊凸度计算 (19)4.2轧辊的弹性弯曲变形 (19)4.3轧辊的磨损 (21)4.4辊型设计 (21)5 设备校核 (22)5.1 咬入条件的校核 (22)5.2 轧辊强度校核 (23)5.2.1工作辊强度校核 (24)5.2.2 支承辊强度校核 (25)5.2.3 工作辊与支承辊间的接触应力 (27)5.3主电机过载和过热校核 (28)5.3.1 轧机主电机过载校核 (28)5.3.2轧机主电机的发热校核 (29)6.结束语 (30)参考文献 (30)1.前言中厚板带材是机械制造﹑桥梁建设造船和石油化工的容器及管道制造等重要的原材料。
中厚板生产压下规程课程设计(DOC)

《塑性成型工艺(轧制)》课程设计说明书课题名称12×1800×10000mm轧制规程设计指导教师张金标. 专业小组10材控第3设计小组.小组成员x x x 101012101xx x x 101012101xx x x 101012101xx x x 101012101xx x x 101012101xx x x 101012101x2013年06月05日《塑性成型工艺(轧制)》课程设计任务书10级材料成型与控制工程专业设计小组:第 3 小组成员:x x x x x x x x xx x x x x x x设计课题:中厚板轧制规程设计指导教师:张金标一、设计产品设计小组学生学号产品牌号产品规格/mm1 24,1,2,3,4,5 Q235 10×2000×90002 6,7,8,9,10,11 45 10×1900×100003 12,13,14,15,16,17 12CrNi3A 12×1800×100004 18,19,20,21,22,24 4Cr13 13×1700×90005 25,26,27,28,29,30 Q235 12×2100×120006 31,32,33,34,35,36 45 8×1800×130007 37,38,39,40,41,42 12CrNi3A 14×2000×90008 43,44,45,46,47,48 4Cr13 12×2000×80009 49,50,51,52,53,55 Q235 9×2050×1200010 56,57,58,59,60,62 45 10×2300×1200011 63,64,65,66,67,68 12CrNi3A 13×1900×1200012 69,70,146,147,148,149,150 4Cr13 15×2100×9000二、设计条件机组:双机架串列式可逆机组(二辊可逆轧机粗轧,四辊可逆轧机精轧)。
课程设计中厚板计算

课程设计中厚板计算一、课程目标知识目标:1. 让学生掌握厚板计算的基本理论和方法,理解厚板的受力特点及计算原理;2. 使学生了解厚板在实际工程中的应用,并能结合实际案例进行分析;3. 引导学生运用所学知识,解决厚板计算中的实际问题。
技能目标:1. 培养学生运用力学原理进行厚板计算的能力,提高学生的计算准确性和效率;2. 培养学生运用专业软件或手工绘图进行厚板结构分析的能力;3. 培养学生团队协作、沟通交流的能力,提高学生在实际工程项目中的问题解决能力。
情感态度价值观目标:1. 培养学生对力学学科的热爱,激发学生学习兴趣,增强学生的自信心;2. 引导学生树立正确的工程观念,认识到厚板计算在工程中的重要性;3. 培养学生严谨、细致的学习态度,提高学生的责任感和使命感。
本课程针对高中年级学生,课程性质为专业选修课。
在教学过程中,充分考虑学生的认知水平、兴趣和特长,结合教材内容,设计具有实践性和挑战性的教学活动。
通过本课程的学习,使学生能够在掌握厚板计算基本原理的基础上,运用所学知识解决实际问题,提高学生的专业素养和实践能力。
同时,注重培养学生的团队协作和沟通能力,提升学生在实际工程中的应用能力。
课程目标的设定旨在使学生在知识、技能和情感态度价值观方面取得全面发展。
二、教学内容1. 厚板的基本概念及分类:介绍厚板的概念、分类及在实际工程中的应用,使学生了解厚板的结构特点及计算意义。
(对应教材第2章)2. 厚板受力分析:讲解厚板受力的基本原理,引导学生掌握厚板受力分析方法,包括弯矩、剪力及扭矩的计算。
(对应教材第3章)3. 厚板计算方法:详细介绍厚板的计算方法,包括弹性理论和塑性理论,使学生能够根据不同情况选择合适的计算方法。
(对应教材第4章)4. 厚板稳定性分析:探讨厚板稳定性问题,讲解稳定性计算方法,提高学生在实际工程中对厚板稳定性的认识。
(对应教材第5章)5. 实际案例分析:分析典型厚板工程案例,使学生将理论知识与实际工程相结合,提高问题解决能力。
毕业设计(论文)-16MnR_中厚板轧制规程制定
攀枝花学院学生课程设计(论文)题目:16MnR中厚板轧制规程制定学生姓名:学号:200911101052所在院(系):材料工程学院专业:材料成型及控制工程班级: 2011级压力加工班指导教师:肖玄职称:讲师2014年10 月13 日攀枝花学院教务处制攀枝花学院本科学生课程设计任务书目录1 绪论 (5)2中厚板生产工艺 (6)2.2中厚板生产工艺流程的制订 (7)2.3 中厚板生产工艺流程 (7)2.3.1坯料 (7)2.3.1.1坯料的选择 (7)2.3.1.2 铸坯的材质 (8)2.3.1.3 铸坯检查与清理 (8)2.3.2坯料加热 (8)2.3.2.1 加热炉选择 (8)2.3.2.2加热温度 (9)2.3.2.3 加热速度 (9)2.3.2.4 加热时间 (9)2.3.2.5保温时间 (9)2.3.2.6 燃料选择 (10)2.3.3 轧制 (10)2.3.3.1 除鳞 (10)2.3.3.2 粗轧 (10)2.3.3.3 精轧 (11)2.3.4 中厚板轧后冷却 (11)2.3.4.1 冷却方式 (11)2.3.4.2 冷床 (12)2.3.5 精整及热处理 (13)2.3.5.1 热处理 (13)2.3.5.2 矫直 (13)2.3.5.3 翻板、表面检查及修磨 (13)2.3.5.4 划线与剪切 (13)2.3.5.5 钢板的标志与包装 (14)2.3.5.6 钢板的质量检验 (14)3 总结 (15)参考文献 (16)1 绪论中厚板是指厚度4.5-25.0mm的钢板,主要用于制造石油、化工气体分离和气体储运的压力容器和其它类似设备,一般工作压力在常压到320kg/cm2甚至到630kg/cm2,温度在 -20-450°C范围内工作,要求容器钢板除具有一定强度和良好塑性和韧性外,还必须有较好冷弯和焊接性能,如:Q245R 、Q345R、14Cr1MoR、15CrMoR等。
中厚板的生产
条件:原料宽度B < 成品宽度b
(3) 精轧Biblioteka 控制钢板厚度主要任务
板形控制 表面质量和性能
2)全横轧法
概念:横轧即是钢板延伸方向与原料纵轴方向垂直的轧制 ,全横轧法是将板坯进行横轧直至轧成成品的方法。 条件:板坯长度L≧成品宽度b,原料宽度B<成品宽度b 初轧板坯作原料. 优点:改善钢板的各向异性,显著改善钢板的横向性能。
缺点:受到钢坯长度、规格、数量的限制,调整钢板宽度
的灵活性小。
3)角轧—纵轧法(角轧法)
中厚板生产
一、中厚板的概念 二、中厚板的用途 三、中厚板的工艺生产流程
定义:中厚板是指厚度4.5-25.0mm的钢板,厚度25.0100.0mm的称为厚板,厚度超过100.0mm的为特厚板。 中厚板主要用途:建筑工程、机械制造、容器制造、造船、桥 梁等。 中厚板用途:广泛用来制造各种容器、炉壳、炉板、桥梁及 汽车静钢钢板、低合金钢钢板、桥梁用钢板、造般钢板、锅炉 钢板、压力容器钢板、花纹钢板、汽车大梁钢板。、拖拉机某 些零件及焊接构件。
2.3中厚板生产工艺流程及车间平面布置
一、一般中厚板生产流程
2.4中厚板的生产工艺
一、原料准备
1.原料种类
2.4.3轧制
除磷--粗轧--精轧
或
成型轧制--展宽轧 制--伸长轧制
(1)除鳞
①除鳞目的:除去表面的氧化铁皮以获得有
良的表面质量。 ②除鳞原理:利用高压水的强烈冲击作用,
去除表面的氧化铁皮。
(2)
粗轧(展宽轧制)
粗轧阶段的主要任务:将板坯或扁锭展宽到所需
要的宽度并进行大压缩延伸。
角轧—纵轧法 展宽的方法 综合轧制法 全纵轧法
全横轧制法
轧制方法 (1) 全纵轧法 概念:钢板的延伸方向与原料纵轴方向相一致的轧制方法。 条件:原料宽度B≥成品宽度b,不用展宽而直接纵轧成成品。 优点:操作简单,产量高。 缺点:钢板横向性能低(尤其是冲击韧性,单方向的延伸使偏析 和夹杂等呈明显条带状分布,钢板组织和性能严重各向异性。
中厚板生产压下规程课程设计概论
《塑性成型工艺(轧制)》中厚板轧制设计说明书课题名称12×1800×10000mm轧制规程设计指导教师. 专业小组.2015年06月18日目录第一章制定生产工艺及工艺制度 ........................................................... - 3 -一、制定生产工艺及工艺制度 ............................................................................... - 3 -二、坯料选择 ........................................................................................................... - 3 -三、中厚板压下量 ................................................................................................... - 3 -第二章设计变形工具................................................................................ - 5 -一、设计二辊 ........................................................................................................... - 5 -二、设计四辊 ........................................................................................................... - 5 -第三章计算力能参数................................................................................ - 7 -一、选择速度图 ....................................................................................................... - 7 -二、设计轧制速度(n1、n2、n3、a、b)....................................................... - 7 -三、速度图 ............................................................................................................... - 7 -四、计算各道次时间 ............................................................................................... - 7 -五、计算各道次轧制温度 ....................................................................................... - 8 -六、计算各道次变形抗力 ....................................................................................... - 9 -七、选用Sims公式计算各道次轧制力 ................................................................. - 9 -第四章轧辊强度校核............................................................................... - 11 -一、二辊轧机强度校核 ......................................................................................... - 11 -二、四辊轧机强度校核 ......................................................................................... - 12 -第五章主电机容量校核.......................................................................... - 14 -一、绘制力矩图 ..................................................................................................... - 14 -二、计算各机架电机最大输出力矩及等效力矩 ................................................. - 15 -三、校核各机架主电机容量 ................................................................................. - 16 -参考文献.................................................................................................... - 23 -第一章制定生产工艺及工艺制度一、制定生产工艺及工艺制度1.制定生产工艺选择坯料→原料清理→加热→除鳞→纵轧一道(使长度接近成品宽度)→转90°横轧到底→矫直→冷却→表面检查→切边→定尺→表面尺寸形状检查→力学性能试验→标记→入库。
中厚板生产课程设计指导书
目录1 产品标准和技术要求1.1.1钢材的尺寸、外形及允许偏差钢板和钢带的尺寸、外形及允许偏差见国标GBT/709-2006《热轧钢板和钢带的尺寸、外形、重量及允许偏差》(国标可从网上下载,下同)。
1.1.2技术要求合金牌号和化学成分可查国标,如碳素结构钢可查GB/T700-2006,低合金结构钢可查GB/T1591,优质碳素结构钢 GB/T 699-1999等另外,技术要求可查找GB 3524-2005《碳素结构钢和低合金结构钢热轧钢带》,GB/T4237-2007《不锈钢热轧钢板和钢带》,GB/T8749-2008《优质碳素结构热轧钢带》等。
(1)钢的牌号、化学成分和力学性能见表1-6。
2 生产工艺流程及主要设备参数2.1生产工艺流程根据车间设备条件及原料和成品的尺寸,生产工艺过程一般如下:原料的加热→除鳞→轧制(粗轧、精轧)→矫直→冷却→划线→剪切→检查→清理→打印→包装。
板坯的轧制有粗轧和精轧之分,但粗轧与精轧之间无明显的划分界限。
在单机架轧机上一般前期道次为粗轧,后期道次为精轧;对双机架轧机通常将第一架称为粗轧机,第二架称为精轧机。
粗轧阶段主要是控制宽度和延伸轧件。
精轧阶段主要使轧件继续延伸同时进行板形、厚度、性能、表面质量等控制。
精轧时温度低、轧制压力大,因此压下量不宜过大。
中厚板轧后精整主要包括矫直、冷却、划线、剪切、检查及清理缺陷,必要时还要进行热处理及酸洗等,这些工序多布置在精整作业线上,由辊道及移送机纵横运送钢板进行作业,且机械化自动化水平较高。
2.2 主要生产工艺(1)加热板坯加热目的:中厚板加热目的是提高钢的塑性,降低变形抗力,利于轧制;生成表面氧化铁皮,去除表面缺陷;加热到足够高的温度,使轧制过程在奥氏体化温度区域内完成;在可能的下并可以溶解在后阶段析出的氮化物和碳化物。
一般厚板加热炉的型式有两种:连续式和半连续式。
比较而言,连续式加热炉的产量高、热效率高,装入,抽出方便间歇式加热炉产量一般在10~20t/h,热效率也低。
- 1、下载文档前请自行甄别文档内容的完整性,平台不提供额外的编辑、内容补充、找答案等附加服务。
- 2、"仅部分预览"的文档,不可在线预览部分如存在完整性等问题,可反馈申请退款(可完整预览的文档不适用该条件!)。
- 3、如文档侵犯您的权益,请联系客服反馈,我们会尽快为您处理(人工客服工作时间:9:00-18:30)。
目录1 产品标准和技术要求1.1.1钢材的尺寸、外形及允许偏差钢板和钢带的尺寸、外形及允许偏差见国标GBT/709-2006《热轧钢板和钢带的尺寸、外形、重量及允许偏差》(国标可从网上下载,下同)。
1.1.2技术要求合金牌号和化学成分可查国标,如碳素结构钢可查GB/T700-2006,低合金结构钢可查GB/T1591,优质碳素结构钢 GB/T 699-1999等另外,技术要求可查找GB 3524-2005《碳素结构钢和低合金结构钢热轧钢带》,GB/T4237-2007《不锈钢热轧钢板和钢带》,GB/T8749-2008《优质碳素结构热轧钢带》等。
(1)钢的牌号、化学成分和力学性能见表1-6。
2 生产工艺流程及主要设备参数2.1生产工艺流程根据车间设备条件及原料和成品的尺寸,生产工艺过程一般如下:原料的加热→除鳞→轧制(粗轧、精轧)→矫直→冷却→划线→剪切→检查→清理→打印→包装。
板坯的轧制有粗轧和精轧之分,但粗轧与精轧之间无明显的划分界限。
在单机架轧机上一般前期道次为粗轧,后期道次为精轧;对双机架轧机通常将第一架称为粗轧机,第二架称为精轧机。
粗轧阶段主要是控制宽度和延伸轧件。
精轧阶段主要使轧件继续延伸同时进行板形、厚度、性能、表面质量等控制。
精轧时温度低、轧制压力大,因此压下量不宜过大。
中厚板轧后精整主要包括矫直、冷却、划线、剪切、检查及清理缺陷,必要时还要进行热处理及酸洗等,这些工序多布置在精整作业线上,由辊道及移送机纵横运送钢板进行作业,且机械化自动化水平较高。
2.2 主要生产工艺(1)加热板坯加热目的:中厚板加热目的是提高钢的塑性,降低变形抗力,利于轧制;生成表面氧化铁皮,去除表面缺陷;加热到足够高的温度,使轧制过程在奥氏体化温度区域内完成;在可能的下并可以溶解在后阶段析出的氮化物和碳化物。
一般厚板加热炉的型式有两种:连续式和半连续式。
比较而言,连续式加热炉的产量高、热效率高,装入,抽出方便间歇式加热炉产量一般在10~20t/h,热效率也低。
这里采用的加热炉为步进梁式加热炉。
中厚板加热工艺的特点:由于厚板的产品种类较多,板坯的规格变化大,所以加热温度的变化范围较广,一般在950~1250°C左右,这与热连轧的情况不完全一样,由于生产的批量小,炉内板坯的温度变化频繁,这样就造成加热炉的热负荷变化较大,加热温度的控制要求较高。
(2)轧制中厚板轧制过程包括除鳞、粗轧、精轧三个阶段。
随控制轧制技术的应用,为满足控制轧制时的温度条件,在粗轧过程中或粗轧后还有一个控制钢板温度的阶段。
轧制过程主要包括以下几个阶段:1)除鳞:钢板表面质量是钢板重要的质量指标之一,加热时高温下生成的氧化铁皮若在轧制前不及时清理或清理不净,在轧后的钢板表面上,因氧化铁皮被压入钢板表面,会出现“麻点”等缺陷,因此轧前除鳞是保证获得优良表面的关键工序。
目前广泛采用的方法是使用高压水除鳞和轧机前后的高压喷头进行除鳞。
2)粗轧:中厚板轧制粗轧阶段的任务是将板坯或扁锭轧制到所需的宽度、控制平面形状和进行大压缩延伸。
粗轧阶段首先调整板坯或扁锭尺寸,以保证轧制最终产品尺寸的宽度满足要求。
根据坯料尺寸和延伸方向的不同,“调整宽度”的轧制方法可分为:全纵轧法、全横轧法、横轧-纵轧法、角轧-纵轧法。
全纵轧法:当板坯宽度达到毛板宽度要求时采用。
它的优点是产量高,但钢板组织和性能存在严重的各向异性,横向性能特别是冲击韧性太低。
横轧-纵轧法:当板坯宽度小于毛板宽度而长度又大于毛板宽度时采用。
其优点是板坯宽度与钢板宽度可灵活配合,钢板的横向性能有所提高(因横向延伸不大),各向异性有所改善;缺点是轧机产量低。
纵轧-横轧法:当板坯长度小于毛板宽度时采用。
由于两个方向都得到变形且横向延伸大,钢板的性能较高。
角轧-纵轧法:当轧机强度及咬入能力较弱(如三辊劳特轧机)时或板坯较窄时采用。
全横轧法――当板坯长度达到毛板宽度要求时采用。
轧制过程中金属在轧向和横向上流动是不均匀的,造成在轧制一道或数道后,钢板的平面形状不是一个精确的矩形,甚至与矩形形状偏离较大,如在轧向上形成鱼尾形或舌头形,横向形成桶形等。
进入精轧后无法修正,使轧后最终产品的平面形状复杂,必须切掉头、尾、边部才能得到所需的矩形,增加了金属消耗。
3)精轧:精轧阶段的主要任务是延伸和质量控制。
在精轧机上为了减少板宽方向各点纵向延伸不均,以获得良好的板型,一些中厚板轧机的精轧机上装备有工作辊或支承辊液压弯辊系统,通过控制轧辊凸度,提高板宽方向上的均匀性。
精轧机在厚度控制方面大多采取厚度自动控制系统。
(3)精整与热处理中厚板厂产品质量最终处理和控制的环节。
精整工序主要包括矫直、冷却、划线、剪切、检查、缺陷清理、包装入库等根据钢材技术条件要求有的还需要热处理和酸洗。
中厚板厂通常在作业线上设置热矫直机,多使用带支撑辊的四重式矫直机,为了补充热矫直机的不足,还离线设置拉力矫直机或压力矫直机等冷矫设备。
板厚在25mm以下时侧边使用圆盘剪,头尾使用锄头剪或摇摆剪。
50mm 以上的钢板多采用在线连续气割的方式。
中厚板的热处理最常用的是退火、正火、正火加回火、淬火加回火处理。
2. 3主要设备参数2.3.1 粗轧机组四辊可逆式粗轧机产品数据(供参考):板坯厚度180mm, 220mm, 260mm, 300mm板坯宽度1200~2300mm板坯长度双排装料2200~3600mm单排装料4800~7500mm板坯重量双排装料最大16.8t单排装料最大35t钢板厚度6~50mm钢板宽度(轧制)1500-3650mm钢板长度(轧制)最大74米轧机参数:形式四辊可逆式轧机名义轧制力<74000kN轧机模数(供参考)7900kN/mm轧辊尺寸工作辊直径1050/950×3500mm支承辊直径2100/1900×3400m机架窗口高度大约9000mm2.3.2 精轧机组四辊可逆式精轧机主要技术参数:轧机参数:形式四辊可逆式轧机名义轧制力74000kN轧机模数(供参考)79000kN/mm轧辊尺寸工作辊直径1050/950×3500mm支承辊直径2100/1900×3400mm 机架窗口高度大约9000mm3 典型产品工艺设计3.1 原料的设计中厚板轧机所用原料的尺寸,即原料厚度、宽度、长度,直接影响着轧机的生产率,坯料的成材率以及钢板的力学性能。
中厚板坯料选用考虑以下3个方面:(1)保证成品钢板的尺寸和性能满足使用要求。
(2)能够充分发挥炼钢车间和厚板车间的工艺条件和设备能力。
(3)所生产的钢板成本最低。
3.1.1 原料质量按成品钢板的质量和计划成材率计算出原料的质量。
计划成材率指的是在设计原料尺寸时的成材率,可以按下面的公式计算。
=()()()()rp twlt t w w l l l s +∆+∆++计划成材率式中:t —成品板厚度 W —成品板宽度 L —成品板长度t t +∆—轧制平均厚度 w w +∆—轧制平均宽度rp l —试样长度S —烧损△t —宽度余量 △w —厚度余量 3.1.2 原料尺寸由计算出的原料质量和连铸坯或初轧坯,钢锭的规格范围,考虑到压缩比,横轧时轧机送钢的最小长度,轧机允许最大轧制长度,加热炉允许装入长度等因素,决定原料的厚度、宽度和长度。
3.2 轧制规程的设计中厚板的轧制规程主要包括压下制度、速度制度、温度制度、辊型制度。
轧制规程的设计就是根据钢板的急速要求、原料条件、温度和生产设备的实际情况,运用数学公式或图表进行人工计算或计算机计算,来确定各道次的实际压下量、空载辊缝、轧制速度等参数,并在轧制的过程中加以修正和应变处理,达到充分发挥设备能力、提高产量、保证质量、操作方便、设备安全的目的。
通常中厚板轧制规程设计的方法和步骤:(1)在咬入能力允许的条件下按经验分配各道次压下量,确定各道次压下量分配率及各道次能耗负荷分配比。
(2)制定速度制度,计算轧制时间并确定逐道次轧制温度。
(3)计算轧制力、轧制力距及总传动力矩。
(4)检验轧辊等部件的强度和电机力矩。
(5)进行必要的修正和应变处理。
3.2.1 坯料的选择中厚板的原料的主题是连铸坯,其厚度虽然不受初轧机轧辊的最大开口度的限制,但为了确保成品钢板的综合性能,连铸坯与成品钢板间的最小压缩比也要保持在6:1以上。
连铸坯的宽度受到连铸机结晶器宽度的限制。
3.2.2 道次压下量分配的影响因素道次压下量分配轧制总道次数应根据从坯料到成品钢板厚度上的压下量和平均压下量,参照类似的轧制规程来确定,对于单机架、总道次数应为奇数,对于双机架应为偶数,并且要考虑两架轧机的轧制节奏要大致平衡。
道次压下量的分配要考虑咬入条件:成形轧制阶段由于板坯的厚度大、温度高、轧制速度低、道次压下量大,所以咬入条件可能成为限制压下量因素。
每道次的压下量应该小于由最大咬入角所确定的最大压下量。
(1cos )(1mas mas h D a D ∆=-=-式中:D ——轧辊直径,mm f ——摩擦系数。
平辊热轧碳钢中厚板时,当轧制温度在700℃以上时,轧制速度在5m/s 以下时的摩擦系数f 值可由下式计算:钢质轧辊: f=1.05-0.0005T-0.056v 冷硬铸铁轧辊:f=0.94-0.0005T-0.056v 式中: T ——轧制温度,℃; v ——轧制线速度,m/s ;二辊和四辊可逆式中厚板轧机的轧制厚度可调,因此可以采用低速咬入,所以实际的最大咬入角可以达到22°到25°。
在这类轧机中厚板,咬入条件将不是限制压下量的主要因素,在实际生产中,热轧钢板时,咬入角一般为15°到22°,低速咬入可取为20°。
除考虑咬入外,还需考虑轧辊及辊颈的强度条件,主电机的能力限制,钢板性能质量的制约。
3.2.3道次压下量分配的分配规律二辊和四辊可逆式中厚板轧机的轧制厚度可调,因此可以采用低速咬入,所以实际的最大咬入角可以达到22°到25°。
因此,这类轧机在采用连铸坯或初轧坯作为原料时,除鳞道次之后可以采用大压下量轧制,中间道次为了充分利用钢坯温度高,变形抗力低的优势,采用较大的压下量。
然后随着钢坯温度降低,压下量逐渐变小,最后1-2道次为了保证板形和温度精度也要采用较小的压下量,甚至最后一道采用平轧道次。
在双机架上轧制中厚板,压下量的分配还要考虑一到两个机架间的轧制节奏匹配和轧机负荷的平衡,通常情况下粗轧机要承担总变形量的75%以上。
总压下量:100%H hHε∑-=⨯粗轧压下量:一般在总压下量的75%以上,取85%。
则:85%εε∑=⨯出口 所以:h 100%H Hε-⨯=出口出口 可得:h 出口数值。
总之,对于单机架,总道次数应为奇数,对于双机架应为偶数,并且要考虑两架轧机的轧制节奏要大致平衡。