数控加工中心在线检测的基本原理
加工中心触发式测头在线检测的实现

本文以实现加工中心零件测量自动化为目的 , 通过在加工中心上配备测头装置 , 实现在线 测量。实现了测量自动化 , 通过微机交互界 面操作 , 实现测量程序自动生成。测量结果 计算在程序中进行修正 , 进行复杂的综合误 差补偿运算由原来不可能而成为可能。
系统结构、工作原理及工作过程 在线检测系统组成 一个完整的加工中心在线检测系统一般由以 下几个部分组成:
系统工作原理 对于柔性制造系统 ( FMS ) 等各种现代先进制造技术体系来说 , 加工中心在线检测系统是必不可少的组成部分。要实现计算机辅助 加工中心在线检测 , 首先应在计算机辅助编程系统上自动生成检测 主程序 , 将检测主程序由 RS - 232 串行通讯接口传输给加工 中心 , 通过程序控制 , 测头将按程序规定的路径向测量点运动 , 当测球接触工件时发出触发信号 , 通过测头与数控系统的专用接口 将触发信号传到转换器 , 并将触发信号转换后传给机床的控制系统 , 该点的坐标被记录下来。信号接收后 , 机床停止运动 , 测量点的 坐标通过 RS- 232 串行通讯接口传回计算机 ,这时按程序控 制进行下一个测量动作。在计算机软件控制系统的控制下 , 可对系 统测量结果进行计算进行补偿及修正等数据处理工作。
测量数据提取 在 FANUC 16i 中测量数据的提取方法为(以内孔类 零件为例) : POPEN DPRNT [CfnumKL#107[34]LLy1LLz 2]
DPRNT [CfnumLL#108[34]LLy1LL z 2] DPRNT [CfnumLLx1LL#120[34]LL z 2] DPRNT [CfnumLLx1LL#121[34]LL z 2] PCLOS
导轨直线度检测的方法及工具

导轨直线度检测的方法及工具1. 通过使用激光对导轨进行扫描,可以得到高精度的直线度检测数据。
2. 利用光学显微镜和数字影像处理技术,可以实现对导轨的直线度检测。
3. 使用激光干涉仪器对导轨进行测试,可以获得直线度的精确度信息。
4. 利用高精度的电子测量仪器,可以进行导轨直线度的快速检测。
5. 基于摄像头成像技术设计的导轨直线度检测仪,可以满足不同工件的直线度要求。
6. 使用应变片传感器结合数据采集系统,可以对导轨的直线度进行高精度测量。
7. 利用高精度的连接轴进行导轨的直线度测试,可以获得真实可靠的检测数据。
8. 采用数控机械加工中心进行导轨的直线度检测,可以实现高效率和高精度的检测。
9. 利用光栅尺或线性位移传感器进行导轨直线度的在线监测,可以提升生产线的稳定性。
10. 基于图像处理技术设计的导轨直线度检测软件,可以实现自动化的检测和分析。
11. 通过激光投影仪对导轨进行检测,可以实现对直线度的高精度测量。
12. 利用激光干涉仪和激光测距仪结合进行导轨的直线度检测,可以提高测试的准确性。
13. 基于感应原理的导轨直线度检测装置,可以实现对导轨直线度的非接触式检测。
14. 利用振动传感器和数据采集系统,可以实现对导轨直线度的动态检测。
15. 基于机器视觉技术开发的导轨直线度检测系统,能够实时获取导轨的直线度数据并进行分析。
16. 利用光电编码器对导轨进行直线度测量,可以得到高分辨率的检测结果。
17. 采用多点测量法对导轨直线度进行检测,可以有效避免测量误差的影响。
18. 利用电子水准仪结合自动化测量系统,可以实现对导轨直线度的全方位检测。
19. 基于三坐标测量机设计的导轨直线度检测夹具,可以提高检测的稳定性和准确性。
20. 利用微型惯性导航系统对导轨进行直线度检测,可以实现高速运动状态下的测量。
21. 基于电容式传感器开发的导轨直线度检测设备,可以实现高灵敏度的检测。
22. 利用激光测量仪进行导轨直线度的取样检测,可以有效降低人为误差。
五轴数控机床在线测量分析方法研究

开发研究«湖北农机化»2020年第1期作者简介:王立鹏(1987G),男,汉族,本科,研究方向:计量检测.五轴数控机床在线测量分析方法研究王立鹏(齐齐哈尔二机床(集团)有限责任公司,黑龙江齐齐哈尔161005)㊀㊀摘要:五轴数控机床广泛地应用于航空航天行业当中,主要的是负责对于飞机上的机身结构㊁模具以及涡轮叶片等具有复杂曲面的元件进行加工,因为这些原件具有较为复杂的几何形状,同时外表凹凸不平.这就要对这些元件进行加工过程当中,对其外形进行切削.而通过五轴数控机床能够达到这一目的,不仅仅能够具备更高的切削效率,加工出符合要求的曲面元件,还能够进一步地降低工作人员的工作量以及工作难度.关键词:五轴数控机床;在线测量;方法1五轴数控机床在线检测系统的组成五轴数控机床所配备的在线检测系统可以分为2台,第一种是直接地通过调用测量宏程序库,而不使用计算机进行辅助而完成整个工件的测量;而第二种则是需要自己开发出测量程序库,并且利用计算机对于运行程序进行编制,并且还应当由反应中心及时地生成检测程序,之后将该程序传到数控系统当中而起到测量作用.以上2种检测系统分类的主要依据点主要的是看其是否与计算机系统连接.而在数控机床加工中心在线检测系统当中,融入计算机系统也能够补充测头系统的不足之处,从而能够利用计算机的综合能力,提高检测的进度以及可操作性,从而做好各项检测工作.2对其检测方法进行探究2.1定位测头以及测量距离为了能够在五轴数控机床使用过程当中使用触发式测头对于工件进行测量,就需要设置一些中间的定位点.防止在测量过程当中,工件发生碰撞而影响其后续的质量.同时还需要设置有快速的定位点,防止因为测头在机床使用过程当中移动距离过大,从而能够使得测头能够快速地进行前进,从而进一步提高机床的测量效率.而为了能够规划出更短的测量路径,则需要定义已接触距离㊁搜索距离㊁回退距离等3个距离而达到这一目的.2.2规划检测路径在五轴数控机床应用过程当中,使用触发式测头进行检测过程当中,可以根据被测表面在检测点之间的接触以及相关的参数,而选择出最短的检测路径.而通过这种方法进行测量,能够进一步补偿测头半径,同时使用这种方法也能够使得侧头直接地接触被测物体的表面,不出现打滑现象.同时在规划检测路径时,还需要进一步确定选题单元以及相关的关系,同时还需要选择最适合的测量工艺.而在进行测量工艺的选择时,还要考虑到多个影响因素,包括安装以及测量机面㊁使得零件定位于数控机床之上,之后还需要进一步规划测量工具㊁判断测量过程当中需要测量哪些参数㊁判断参数是直接测量还是间接测量,同时还需要进一步确定测点的位置,之后还需要进行防碰撞检验,防止数控机床以及测头还有其余的附件发生碰撞.2.3检测具有曲面特征的工件使用五轴数控机床对曲面进行在线检测,就需要确定最为合适的测量点,并且还需要对于曲面工件的误差进行分析.而这一项分析工作具有十分复杂的操作步骤,为了进一步保证测量结果的准确性,就需要正确的选择测量点,因为在在线测量的前期,为了更好地对曲面车间内工件进行检测,则需要使用网格的方法选择出最为合适的测量点,根据所需要测量曲面的曲面形状以及曲率大小而生成测量点,之后使用之字形的检测路径进一步地提高在线检测的检测效果,同时在生成最短的路径.同时还需要根据测量点的分布,依次地将测量点进行连接.同时在测量过程当中务必要保证每一个测量点只检测一次,从安全的角度出发,还需要进一步检查所生成的最终检测路径,防止在检测的过程当中测量的工件以及测头系统发生碰撞,从而影响到最终的检测效果.同时如果测量点以及检测工件在运动时出现碰撞现象,导致测头受力过大可能会危害到测头本身,就立刻停止测头系统的应用,并且进行报警,防止测头受到严重损害,而影响到数控机床的精密度以及完整度.在对曲面工件进行测量的过程当中,使用触发式的侧头进行测量,并且将测量过程当中曲面的下陷区域规定为测量点,计算曲面上测量点所与之对应的曲率半径,判断曲率半径以及测头半径之间的大小关系,如果前者小于后者则可以将其视为劣质测量点,直接地将其剔除,之后再次进入检测路径当中之后,再选择先前的测量点进行第二次测量.3结束语本文主要研究了五轴数控机床在线测量路程当中系统的基本组成,以及在测量过程当中具体应用的检测方法.通过对于测头进行定位,并且进一步判断测量距离,寻找测量点,同时在检测具有曲面特性的工件,比如说航空航天中机身结构以及模具等的过程中,对工件的表面外形进行了雕刻,从而方便之后的设计以及加工工作,筛选出不符合要求的工件,从而进一步减轻工作者的工作量,并且使工件加工过程具备更高的切削效率,为航空航天行业发展做出突出贡献.参考文献:[1]曹著明,孙红梅,史海军.某五轴数控加工中心在线检测关键技术研究[J ].机械设计与制造,2017(11):149G152.[2]司朝阳.五轴机床R T C P 同步检测系统的误差分析与补偿研究[D ].成都:电子科技大学,2018.[3]曹旭妍.微型五轴数控机床的设计与研究[J ].煤矿机械,2017(11):16G18.(收稿日期:2019G09G26)。
数控机床及加工中心概论

• 2. 1 数控机床及加工中心的定义 • 2. 2 数控机床及加工中心的发展历程 • 2. 3 数控机床及加工中心的组成和工作原理 • 2. 4 数控机床的分类 • 2. 5 加工中心的分类 • 2. 6 数控机床及加工中心的用途
返回
2. 1 数控机床及加工中心的定义
一个回转运动坐标, 工件一次装夹后完成四个侧面的加工, 特别适于加 工箱体类工件。如图2-3 所示的大型卧式加工中心配置有交换工作台, 可使工件的装卸、调整时间与切削加工时间重合。 • 2. 5. 1. 2 立式加工中心
下一页 返回
2. 5 加工中心的分类
• 立式加工中心主轴的轴线为垂直设置, 一般具有三个直线运动坐标, 也 可以在工作台上安装一个水平轴(第四轴) 的数控回转台, 如图2-4 所 示, 用于加工螺旋线类的工件。立式加工中心适于加工盘类、套类和 板类工件。
• 精密级加工中心, 定位精度介于2~10μm 的加工中心(以5μm 较多)。
• 2. 5. 5 按自动换刀装置分类
• 2. 5. 5. 1 转塔头加工中心 • 转塔头加工中心有立式和卧式两种, 用转塔的转位来换主轴头, 以实现
自动换刀。主轴数一般为6~12 个, 换刀时间短, 主轴转塔头定位精度 要求较高。钻削加工中心多采用转塔头式自动换刀装置。
上一页
返回
2. 4 数控机床的分类
• 2. 4. 1 按工艺用途分类
• 2. 4. 1. 1 普通数控机床 • 普通数控机床主要包括数控车床、数控铣床、数控镗床、数控钻床、
数控刨床和数控磨床等。 • 普通数控机床按切削工艺的分类见表2-2。 • 2. 4. 1. 2 加工中心 • 在普通数控机床上加装刀库和自动换刀装置, 构成一种带自动换刀系
嘉兴职业技术学院《数控编程与加工》期末考试试卷C

嘉兴职业技术学院《数控编程与加工》期末考试试卷C一、填空题:(本题共10小题,每小题2分,满分20分)1.机床采用的标准坐标系是坐标系。
2.车床中G04指令一般用于场合。
3.坐标轴一般是 ,与工件安装面平行,且垂直Z 坐标轴。
4.数控机床的图形模拟显示及空运转,只能检验的正确性,不能查出被加工零件的。
5.机床上,为提高工件的加工精度,应尽量选择工件的作为对刀点。
6.数控机床坐标系分为坐标系和坐标系。
7.M00后,若重新按,则继续执行加工程序。
8.夹具就是安装在机床上,用以装夹工件或引导刀具,使工件和刀具具 有。
9.“假想刀尖A ”对零件表面加工会产生加工误差;对零件表面加工不会产生加工误差。
10.T0202含义为;T0200含义为。
二、选择题:(本题共20小题,每小题1.5分,满分30分。
每小题给出的四个选项中,只有一个符合题目要求,请将所选项前的字母填入括号内)分院: 班级: 姓名: 学号:1.选择数控加工定位基准的原则之一是()。
(A)宜选用粗糙的面作定位基准(B)应尽量避免与设计基准相重合(C)在一次装夹中,应完成尽可能多的加工内容(D)与工件坐标系的原点不一定要有确定的几何关系⒉在G41或G42指令的程序段中不能用()指令。
(A)G00或G01;(B)G02或G03;(C)G01或G02;(D)G01或G03。
3.加工平面任意直线应采用()。
(A)点位控制数控机床(B)点位直线控制数控机床(C)轮廓控制数控机床(D)直线控制数控机床4.逐点比较法插补第二象限一条直线时,当P点在直线下侧( F<0 )时,应向( )方向发生一脉冲。
(A)+X (B)-X (C)+Y (D)-Y5.适宜加工形状特别复杂(如曲面叶轮)精度要求较高的零件的数控机床是()类机床。
(A)两坐标轴(B)三坐标轴(C)多坐标轴(D)2.5坐标轴6.G02 X20 Y20 R-10 F100;所加工的一般是()。
CIMS环境下在线检测及信号处理技术的研究

在线循环检测系统分为前 向通道和后向通道 。前向通道是被测对象与系统相互联系的信号输人通道, 在该通道中主要是与传感器有关 的信号调节 、变换 电路 , 也称为传感器接口通道 ,触发式测头 、 光栅及其
机与数控机床 ) 的控制软件。实现 了多任务并行处理 , 并保证了现场实时性的要求 ;实现了数控机床的分
级变速进给运动及主轴转速的分级调整 ,在此功能的基础上,实现了在线 自动检测功能。
2 检测信号滤 波器 的设计
设被测信号序列
=Y +, +V ( ) 1
式中 :Y 为期望的信号序列 ;盯 为均值为零的高斯 自噪声序列 ; 为脉冲噪声序列 。
维普资讯
第 2 卷第 4 3 期
20 0 7年 7月
齐 齐 哈 尔 大 学 学 报
J ral f qh r ie st oun ia v r i o Qi Un y
Vo .3 N . 1 , o4 2
J l,0 7 uy2 0
Cl 环境 下在 线检 测及信号处理技术 的研究 MS
第 4期
CM 环境下 在线检测及信号处理技术的研究 IS
・ 1 2.
在测量过程 中,如何减小随机误差是提高测量精度的一个重要组成部分 ,而高斯 白噪声和脉冲型噪声 的干扰则是产生随机误差的根源。为减小高斯噪声对测量精度的影响 ,可建立基于稳态模型的最佳滤波器 模型。然而 ,实际信号往往是非稳态的,而且可能是由多种不同成分组成的 ,在这种情况下 , 若仍然用稳 态模 型来描述它 ,是困难的。同时 ,由于信号不同成分之间的界限往往是模糊的,基于信号的特征分组最 佳滤波也是困难的。 为解决信号的正确估计问题 ,这里构造一种基于模糊集合论的滤波方法 ,称之为模糊滤波 ,与中值滤
第四章 加工过程的智能监测与控制
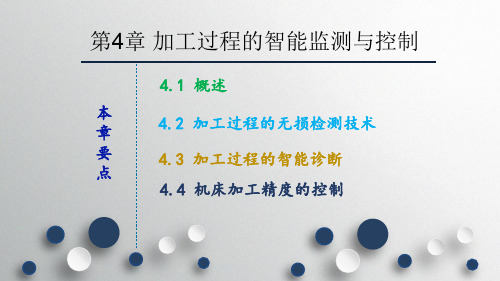
图像匹配:图像分割后,对多幅图片进 行同名点匹配,从匹配结果中可以获得同一 目标在多幅图片上的视差,最后计算出该目 标的实际坐标。
左侧CCD
右侧CCD
4.1.2 智能监测与控制的内容
NC
传感器与检
程 序
加工中心
测系统
参数调 整、误 差补偿
预先建好的系 统控制模型
切削振动、变 形、温度、刀具 磨损、零件表面 质量、设备运行
状态...
监测、控制与 故障诊断
车间管理 MES系统
图 4-1 加工过程监测与控制实现流程
(1)加工过程仿真与优化:针对 不同零件的加工工艺、切削参数、进给 速度等加工过程中影响零件加工质量的各种参数,通过基于加工过程模型的 仿真,进行参数的预测和优化选取,生成优化的加工过程控制指令。
(2)过程监控与误差补偿:利用各种传感器、远程监控与故障诊断技术, 对加工过程中的振动、切削温度、刀具磨损、加工变形以及设备的运行状 态与健康状况进行监测;根据预先建立的系统控制模型,实时调整加工参 数,并对加工过程中产生的误差 进行实时补偿。
(3)通讯等其他辅助智能:将实时信息传递给远程监控与故障诊断系统, 以及车间管理MES系统。
4.1.3加工过程的智能监测与控制发展趋势 加工过程的智能监控技术的发展将主要包括: (1)加工过程监控更适合于精密加工和自适应控制的要求; (2)由单一信号的监控向多传感器、多信号监控的发展, 充分利用多传感器的功能来消除外界干扰,避免漏报误报 情况; (3)智能技术与加工过程监控结合更加紧密;充分利用智 能技术的优点,突出监控的智能性和柔性;提高监控系统 的可靠性和实用性。
数控机床位置检测的研究
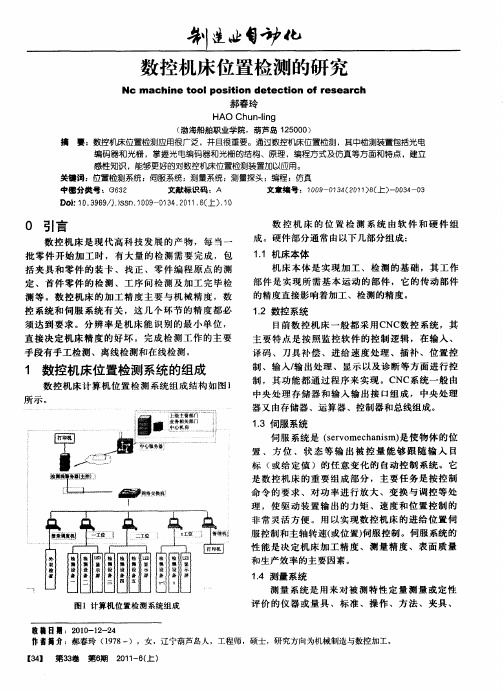
勺 化
数控机床位置检测的研究
N C m achi ne ooIpos ton d ecton o ese ch t ii et i fr ar
郝春 玲
HAO u . n Ch n 1 g i
( 渤海船舶职业学院 ,葫芦岛 1 5 0 ) 20 0
摘
j 管机 f理
服 控制 和主轴 转速( 或位 置) 伺服控 制 。伺 服 系统 的 性 能 是决 定机 床加 工 精 度 、测 量 精 度 、表 面质 量
和 生产效 率的主 要因素 。
…
圈圈 离圈 围圈
图 1 计 算机 位置 检 测 系统 组 成 第6 期 2 1- ( ) 01 6上
1 测 量系统 . 4 测 量 系统 是 用 来对 被 测 特性 定 量 测 量 或定 性
评 价 的仪 器 或 量具 、标 准 、操 作 、方 法 、 夹具 、
收 麓 日用 :2 1-1- 4 00 2 2 作者简介 :郝春玲 (9 8一),女 ,辽 宁葫芦 岛人,工程师 ,硕士,研究方向为机械制造与数控加工 。 17 【4 第 3 卷 3】 3
直 接 决 定机 床 精 度 的 好坏 。完 成 检 测工 作 的 主要 手段 有手工 检测 、离线 检测 和在线检 测 。
主 要特 点 是 按照 监 控软 件 的 控制 逻 辑 ,在 输 入 、
译码 、刀具 补 偿 、进 给 速 度处 理 、 插补 、 位置 控
制 、输入/ 出处 理 、显 示 以及诊 断 等方面 进 行控 输 制 ,其功 能 都通 过 程 序 来实 现 。C NC系统 一般 由 中央 处理 存 储 器 和输 入 输 出接 口组成 , 中央 处 理 器 又 由存储 器 、运 算器 、控 制器和 总线组成 。