第三节 变速器主要参数的选择
第三章 变速器设计
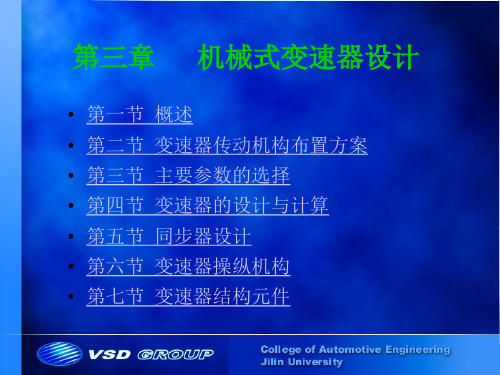
二、组成 1、传动机构 2、操纵机构
三、发展趋势
1、加强设计工作的系列化,通用化。如在4 档变 速器基础上,附加一个副箱体,使档数变成5档。 2、操纵机构从手动向半自动、自动、电子操纵方 向发展。
第二节
分类依据
变速传动机构布置方案
分 三 四 五 多 固 定 轴 式 类 档 档 档 档 两轴式 中间轴式 双中间轴式 多中间轴式 旋转轴式 备 少 注 用
2)变速器常用轴承形式
例:中间轴式变速器
形式 圆 柱 滚 子 轴 第二轴前支承 径向力 承 中间轴前或后 径向力 支承 第一轴后支承 径+轴 第一轴前支承 径 球轴承 第二轴后支承 径+轴 中间轴支承 径+轴
采用的部位
承载特点
备
注
第一轴内腔尺寸够大
外圈有挡圈
形式 圆锥滚子轴 承
采用的部位 中间轴支承 第一轴前端支承
2、初步计算A A= K A 3 Temx i1 g mm
参数 车型 轿 车 货 车 多档变速器
η g——96%
中心距系数 KA 8.9——9.3 8.6——9.6 9.5——11.0
A 的范围
mm
65——80 80——170
二、外形尺寸 1、横向尺寸 影响横向尺寸的因素有: 1)齿轮直径 2)倒档齿轮直径 3)壳体壁厚及其与齿轮之间的间隙
一、传动机构分类
档 数
轴的形式
用于前置前驱动 用于前置后驱动 用于重型汽车 用于重型汽车 液力机械变速器
二、两轴式与中间轴式变速器
形式 特点 结 构 方 面 轴数 第一轴与输出轴 输出轴末端 动力传递经过 直接档 结 噪 构 声 平 两轴式 2 行 1○ 2 主减速器齿轮○ 一对齿轮 没 简 有* 单 低 高 小(3.0—4.5) 中间轴式 3 同一直线上 万向节 两对齿轮※ 有 复 杂 高 低 大(7—8) 备 注
汽车设计0303第三章 第三节 变速器主要参数的选择

2
tg6 Z1 Z2
Z6
21
§3-3 变速器主要参数的选择
七、齿数分配(以四档变速器为例分析)
(五)确定倒挡齿数 (六)齿轮其它尺寸
D1=(1.25~1.4)d2 C=(1.2~1.4)d2 δ=(4~6)m
22
轿车取α< 20°,降低噪声 货车α> 20°,承载强
11
§3-3 变速器主要参数的选择
六、齿轮参数
(三)齿轮螺旋角β
要求:中间轴上的轴向力平衡(齿轮一律右旋)
选取范围: 中间轴式变速器 22°~34° 两轴式变速器 20°~25°
货车变速器
18°~26°
12
§3-3 变速器主要参数的选择
斜齿轮传递转矩时,要产生轴向力并作用到轴承上。 设计时应力求中间轴上同时工作的两对齿轮产生轴向力 平衡。
KA 为中心距系数 轿车 KA =8.9~9.3 A=65~80mm 货车 KA = 8.6~9.6 A=80~170mm
4
§3-3 变速器主要参数的选择
2.乘用车变速器中心距A的确定 发动机前置前轮驱动(FF)和发动机前置后 轮驱动(FR)乘用车的变速器中心距A,也可以 根据发动机排量与变速器中心距A 的统计数据 初选,如图3-16所示。 乘用车变速器的中心距在60-80mm范围内 变化,而商用车的变速器中心距在80-170mm 范围内变化。原则上,总质量小的汽车,变速 器中心距也小些。
目前,为降低油耗,挡数有增加的趋势。轿车一般
用4~5个挡位变速器, 货车变速器采用4~5个挡或多挡,
多挡变速器多用于重型货车和越野汽车。
1
§3-3 变速器主要参数的选择
二、传动比范围 变速器的传动比范围是指变速器最低挡传 动比与最高挡传动传动比的比值。 传动比范围的确定与选定的发动机参数、 汽车的最高车速和使用条件等因素有关。
汽车设计--3变速器设计
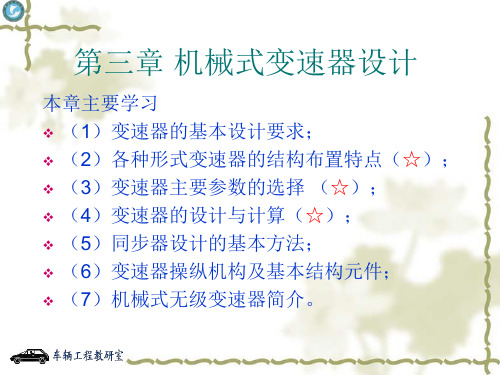
直齿:b=Kcm, Kc为齿宽系数,取为4.5~8.0 斜齿:b= Kcmn,Kc取6.0~8.5
5、变位系数的选择原则
◎采用变位的原因:
1)避免齿轮产生根切 2)配凑中心距 3)通过变位影响齿轮的强度,使用平稳性,耐磨性、抗胶
合能力及齿轮的啮合噪声。 ◎变位齿轮的种类:高度变位和角度变位。 1)高度变位:齿轮副的一对啮合齿轮的变位系数的和为零。
1、变速器的传动比范围: 指变速器最低挡传动比与最高挡传动比的比值。 2、最高挡传动比的选取: 直接挡1.0,超速挡0.7~0.8。
3、最低挡传动比选取:
影响因素:
发动机的最大转矩、最低稳定转速;
驱动轮与路面间的附着力; 主减速比与驱动轮的滚动半径;
Ft max Ff Fi max
汽车的最低稳定车速。
1、中间轴式变速器
❖ 多用于FR,RR布置的 乘用车和商用车上
❖ 能设置直接挡,直接挡 效率高
❖ 一挡传动比能设计较大
❖ 一轴与输出轴转向相同 (挂前进档时)
❖ 零件多,尺寸、质量大
2、两轴式变速器
❖ 结构简单、紧凑、轮廓 尺寸小
❖ 中间挡位传动效率高、 噪音低(少了中间轴、 中间传动齿轮)
❖ 不能设置直接挡,高挡 位时噪音高(轴承齿轮 均承载),且效率略比 三轴式低
第三章 机械式变速器设计
本章主要学习 ❖ (1)变速器的基本设计要求; ❖ (2)各种形式变速器的结构布置特点(☆); ❖ (3)变速器主要参数的选择 (☆); ❖ (4)变速器的设计与计算(☆); ❖ (5)同步器设计的基本方法; ❖ (6)变速器操纵机构及基本结构元件; ❖ (7)机械式无级变速器简介。
毕业设计(论文)-汽车变速器设计计算说明书[管理资料]
![毕业设计(论文)-汽车变速器设计计算说明书[管理资料]](https://img.taocdn.com/s3/m/ce283f069e3143323868934c.png)
目录第1章变速器主要参数的选择 ....................................................... - 1 -.档数................................................................................................................... - 1 -.传动比范围....................................................................................................... - 1 -第2章变速器各档传动比的确定 ................................................... - 2 -.主减速器传动比的确定................................................................................... - 2 -.最抵档传动比计算........................................................................................... - 2 -第3章变速器各档速比的配置 ....................................................... - 4 -.按等比级数分配其它各档传动比,............................................................... - 4 -第4章中心距的选择 ....................................................................... - 4 -.初选中心距可根据经验公式计算................................................................... - 4 -.变速器的外形尺寸........................................................................................... - 5 -第5章齿轮参数的选择 ................................................................... - 5 -.模数................................................................................................................... - 5 -.压力角............................................................................................................... - 6 -.螺旋角............................................................................................................... - 6 -.齿宽................................................................................................................... - 6 -.齿顶高系数....................................................................................................... - 7 -第6章各档齿轮齿数的分配及传动比的计算 ............................... - 7 -.一档齿数及传动比的确定............................................................................... - 7 -.二档齿数及传动比的确定............................................................................... - 9 -.计算三档齿轮齿数及传动比......................................................................... - 10 -.计算四档齿轮齿数及传动比......................................................................... - 12 -.计算五档齿轮齿数及传动比......................................................................... - 13 -.计算倒档齿轮齿数及传动比......................................................................... - 15 -第7章齿轮材料的选择原则 ......................................................... - 19 -.满足工作条件的要求..................................................................................... - 19 -.合理选择材料配对......................................................................................... - 19 -.考虑加工工艺及热处理工艺......................................................................... - 19 -第8章变速器齿轮弯曲强度校核 ................................................. - 19 -.一档齿轮校核................................................................................................. - 21 -. 主动齿轮:........................................................................................................... - 21 - . 从动齿轮:........................................................................................................... - 21 - .二档齿轮校核................................................................................................. - 21 -.主动齿轮:..................................................................................................... - 21 -. 从动齿轮............................................................................................................... - 22 - .三档齿轮校核................................................................................................. - 22 -. 主动齿轮:........................................................................................................... - 22 - . 从动齿轮............................................................................................................... - 22 - .四档齿轮校核................................................................................................. - 23 -. 主动齿轮............................................................................................................... - 23 - . 从动齿轮............................................................................................................... - 23 - .五档齿轮校核................................................................................................. - 23 -. 主动齿轮:........................................................................................................... - 23 - . 从动齿轮............................................................................................................... - 24 -第9章第10轮齿接触应力校核 ................................................... - 24 -. 一档齿轮接触应力校核....................................................................................... - 25 - . 倒档齿轮的校核................................................................................................... - 26 - .、齿面接触疲劳许用应力的计算....................................................................... - 26 - . .齿根弯曲疲劳许用应力计算.............................................................................. - 26 - . 接触疲劳强度校核............................................................................................... - 27 - .齿根弯曲疲劳强度校核................................................................................. - 28 -第10章轴的结构和尺寸设计 ......................................................... - 28 -. 初选轴的直径....................................................................................................... - 29 - . 轴的强度验算与轴的刚度计算........................................................................... - 30 - . 轴的强度计算....................................................................................................... - 33 -第11章轴承选择与寿命计算 ......................................................... - 35 -. 输入轴轴承的选择与寿命计算........................................................................... - 36 - . 输出轴轴承的选择与寿命计算........................................................................... - 38 -第12章参考文献 ............................................................................. - 44 -第1章变速器主要参数的选择本次毕业设计是在给定主要整车参数的情况下进行设计,:乘用车整车主要技术参数1.1. 档数近年来,为了降低油耗,变速器的档数有增加的趋势。
变速器主要参数的选择(精)

第三节变速器主要参数的选择一、挡数增加变速器的挡数能够改善汽车的动力性和经济性。
挡数越多,变速器的结构越复杂,并且使轮廓尺寸和质量加大,同时操纵机构复杂,而且在使用时换挡频率也增高。
在最低挡传动比不变的条件下,增加变速器的挡数会使变速器相邻的低挡与高挡之间的传动比比值减小,使换挡工作容易进行。
要求相邻挡位之间的传动比比值在1.8以下,该值越小换挡工作越容易进行。
要求高挡区相邻挡位之间的传动比比值要比低挡区相邻挡位之间的传动比比值小。
近年来为了降低油耗,变速器的挡数有增加的趋势。
目前,轿车一般用4~5个挡位的变速器,级别高的轿车变速器多用5个挡,货车变速器采用4~5个挡或多挡。
装载质量在2~3.5t的货车采用5挡变速器,装载质量在4~8t的货车采用6挡变速器。
多挡变速器多用于重型货车和越野汽车。
二、传动比范围变速器的传动比范围是指变速器最低挡传动比与最高挡传动比的比值。
传动比范围的确定与选定的发动机参数、汽车的最高车速和使用条件(如要求的汽车爬坡能力)等因素有关。
目前轿车的传动比范围在3~4之间,轻型货车在5~6之间,其它货车则更大。
三、中心距A对中间轴式变速器,是将中间轴与第二轴之间的距离称为变速器中心距A 。
它是一个基本参数,其大小不仅对变速器的外形尺寸、体积和质量大小,而且对拎齿的接触强度有影响。
中心距越小,轮齿的接触应力越大,齿轮寿命越短。
因此,最小允许中心距应当由保证轮齿有必要的接触强度来确定。
变速器轴经轴承安装在壳体上,从布置轴承的可能与方便和不影响壳体的强度考虑,要求中心距取大些。
此外,受一挡小齿轮齿数不能过少的限制,要求中心距也要取大些。
初选中心距A 时,可根据下面的经验公式计算31max g e A i T K A η=式中,A 为变速器中心距(mm);A K 为中心距系数,轿车:A K =8.9~9.3,货车:A K =8.6~9.6,多挡变速器:A K =9.5~11.O ;max e T 为发动机最大转矩(N·m);1i 为变速器一挡传动比;g η为变速器传动效率,取96%。
变速器主要参数的选择
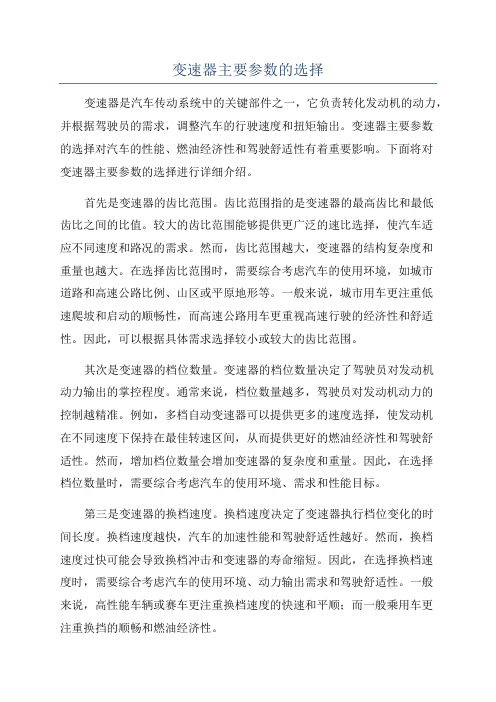
变速器主要参数的选择变速器是汽车传动系统中的关键部件之一,它负责转化发动机的动力,并根据驾驶员的需求,调整汽车的行驶速度和扭矩输出。
变速器主要参数的选择对汽车的性能、燃油经济性和驾驶舒适性有着重要影响。
下面将对变速器主要参数的选择进行详细介绍。
首先是变速器的齿比范围。
齿比范围指的是变速器的最高齿比和最低齿比之间的比值。
较大的齿比范围能够提供更广泛的速比选择,使汽车适应不同速度和路况的需求。
然而,齿比范围越大,变速器的结构复杂度和重量也越大。
在选择齿比范围时,需要综合考虑汽车的使用环境,如城市道路和高速公路比例、山区或平原地形等。
一般来说,城市用车更注重低速爬坡和启动的顺畅性,而高速公路用车更重视高速行驶的经济性和舒适性。
因此,可以根据具体需求选择较小或较大的齿比范围。
其次是变速器的档位数量。
变速器的档位数量决定了驾驶员对发动机动力输出的掌控程度。
通常来说,档位数量越多,驾驶员对发动机动力的控制越精准。
例如,多档自动变速器可以提供更多的速度选择,使发动机在不同速度下保持在最佳转速区间,从而提供更好的燃油经济性和驾驶舒适性。
然而,增加档位数量会增加变速器的复杂度和重量。
因此,在选择档位数量时,需要综合考虑汽车的使用环境、需求和性能目标。
第三是变速器的换档速度。
换档速度决定了变速器执行档位变化的时间长度。
换档速度越快,汽车的加速性能和驾驶舒适性越好。
然而,换档速度过快可能会导致换档冲击和变速器的寿命缩短。
因此,在选择换档速度时,需要综合考虑汽车的使用环境、动力输出需求和驾驶舒适性。
一般来说,高性能车辆或赛车更注重换档速度的快速和平顺;而一般乘用车更注重换挡的顺畅和燃油经济性。
最后是变速器的效率。
变速器的效率决定了从发动机到车轮的功率传递效率。
较高的变速器效率可以减小能量损失,提高汽车的燃油经济性。
一般来说,手动变速器的效率较高,因为它没有液力损耗;而自动变速器的效率较低,因为它需要液力传动系统。
因此,在选择变速器效率时,需要综合考虑燃油经济性和驾驶舒适性的平衡。
机械式变速器设计
图3-3 中间轴式五挡变速器传动方案
中间轴式变速器旳特点
图3-4为中间轴式六挡变速器传动方案。图3-4a所示方案中旳一 挡、倒挡和图3-4b所示方案中旳倒挡用直齿滑动齿轮换挡,其他各挡 均匀常啮合齿轮。
低挡与高挡之间旳传动比比值减小,使换挡工作轻易进行。 挡数选择旳要求:
1. 相邻挡位之间旳传动比比值在1.8下列。 2. 高挡区相邻挡位之间旳传动比比值要比低挡区相邻挡位之间旳比值小。
目前,轿车一般用4~5个挡位变速器, 货车变速器采用4~5个挡或 多挡,多挡变速器多用于重型货车和越野汽车。
二、传动比范围
两轴式变速器旳特点
两轴式变速器有构造简朴、轮廓尺寸小、布置以便、中间挡位传动 效率高和噪声低等优点。两轴式变速器不能设置直接挡,一挡速比不可 能设计得很大。
图3-1为发动机前置前轮驱 动轿车旳两轴式变速器传动方 案。其特点是:变速器输出轴 与主减速器主动齿轮做成一体; 多数方案旳倒挡传动常用滑动 齿轮,其他挡位均用常啮合齿 轮传动。图3-1f中旳倒挡齿轮 为常啮合齿轮,并用同步器换 挡;图3-1d所示方案旳变速器 有辅助支承,用来提升轴旳刚 度。
中心距越小,轮齿旳接触应力越大,齿轮寿命越短。所以,最小允许 中心距应该由确保轮齿有必要旳接触强度来拟定。
初选中心距A时,可根据下面旳经验公式计算
A K A 3 Te maxi1 g
式中,KA为中心距系数,轿车:KA=8.9~9.3,货车:KA=8.6~9.6,多挡变 速器:KA=9.5~11.0。
• 对于轿车,为了降低噪声,应选用 14.5°、15°、16°、16.5°等小些旳压 力角。
长城风骏皮卡轻型货车变速器设计
摘要本次设计的题目是轻型货车变速器设计,采用车型为长城风骏皮卡。
变速器由变速器传动机构和操纵机构组成,其基本功用是改变传动比,扩大驱动轮转矩和转速的变化范围,以适应经常变化的行驶条件,同时使发动机在有利的工况下工作;在发动机曲轴旋转方向不变的前提下使汽车能倒退行驶;利用空挡中断动力传递,以使发动机能够起动、怠速,并便于变速器换挡或进行动力输出。
采用中间轴式变速器,该变速器具有两个突出的优点:一是其直接档的传动效率高,磨损及噪声也最小;二是在齿轮中心距较小的情况下仍然可以获得较大的一档传动比。
这台变速器具有五个前进档(包括一个超速档五档)和一个倒档,并通过锁环式同步器来实现换档。
本设计论述了变速器的总体结构,在设计中完成了各挡齿轮和轴的计算和校核及CAD绘图等工作。
关键词:变速器,锁环式同步器,传动比,中间轴,第二轴,齿轮ABSTRACTThe design is the subject of a light goods vehicle transmission design, the use of models for the Great Wall Wingle pickup. Transmission and transmission by the transmission control mechanism, whose basic skills is to change the gear ratio, wheel torque and speed to expand the scope of the changes to adapt to constantly changing driving conditions, while the engine in the favorable conditions of work; the engine crankshaft without changing the direction of rotation so that cars can travel backwards; the use of neutral interrupt power transmission to the engine to start, idle, and to facilitate the transmission shift or power output.The use of intermediate shaft transmission, the transmission has two significant advantages: First, the direct file transmission efficiency, wear and noise are minimal; second gear center distance is smaller still can get a larger one file transmission ratio. This transmission has five forward gears (including a five-speed overdrive) and a reverse, and through the lock ring synchronizer to achieve the shift. Discusses the transmission of the overall design structure, completed in the design of gears and shafts of the gear and check calculations and CAD drawings and other work.Keywords:Transmission, Locking ring type synchronizer,Gear ratio, Countershaft,Second axis, Gear目录摘要 (I)Abstract (II)第1章绪论 (1)1.1 汽车变速器概述 (1)1.2汽车变速器设计的目的和意义 (2)1.3 汽车变速器国内外现状和发展趋势 (2)1.3.1 变速器国内外的现状 (2)1.3.2 汽车变速器的发展趋势 (3)1.4 手动变速器的特点和设计要求及内容 (3)1.4.1 手动变速器的特点 (3)1.4.2 手动变速器的设计要求 (4)1.4.3设计的主要内容 (4)第2章变速器传动机构布置方案确定 (6)2.1设计所依据的主要技术参数 (6)2.2 变速器传动机构的结构分析和形式选择 (6)2.2.1两轴式变速器的特点分析 (7)2.2.2 中间轴式变速器特点分析 (7)2.2.3 倒挡布置方案分析 (8)2.2.4 传动机构布置的其他问题 (10)2.3 零部件结构方案分析 (10)2.3.1 齿轮形式 (10)2.3.2 换挡机构形式 (10)2.3.3 防止自动脱挡的结构 (11)2.3.4 变速器轴承 (11)2.4 本设计所采用的传动机构布置方案 (11)2.5 本章小结 (12)第3章变速器主要参数的选择和齿数分配 (13)3.1 变速器各挡传动比的确定 (13)3.1.1 变速器最低挡传动比的确定 (13)3.1.2 变速器其他各挡传动比的确定 (14)3.2中心距的确定 (14)3.3变速器外形尺寸的初选 (15)3.4 变速器齿轮参数的选择 (15)3.4.1模数 (15)3.4.2 齿形、压力角及螺旋角 (16)3.4.3 齿宽 (16)3.4.4 齿顶高系数 (17)3.5 变速器各挡齿轮齿数的分配 (17)3.5.1 确定一挡齿轮的齿数 (17)3.5.2 对中心距进行修正 (18)3.5.3 确定常啮合齿轮的齿数 (19)3.5.4 确定其他各挡齿轮的齿数 (20)3.6 本章小结 (23)第4章变速器齿轮的设计计算 (24)4.1变速器齿轮的几何尺寸计算 (24)4.2 计算变速器各轴的扭矩和转速 (24)4.3 齿轮的强度计算和材料选择 (25)4.3.1 齿轮损坏的原因和形式 (25)4.3.2 齿轮的材料选择 (26)4.3.3 齿轮的强度计算 (27)4.4 本章小结 (38)第5章变速器轴和轴承的设计计算 (39)5.1初选变速器轴的轴径和轴长 (39)5.2 轴的结构设计 (39)5.3 变速器轴的强度计算 (40)5.3.1齿轮和轴上的受力计算 (40)5.3.2 轴的强度计算 (41)5.3.3 轴的刚度计算 (46)5.4变速器轴承的选择和校核 (49)5.4.1 第一轴轴承的选择和校核 (49)5.4.2 第二轴轴承的选择和校核 (50)5.4.3 中间轴轴承的选择和校核 (51)5.5 本章小结 (51)第6章同步器和操纵机构的设计选用 (52)6.1 同步器的设计选用 (52)6.1.1 锁环式同步器 (52)6.1.2 锁销式同步器 (53)6.1.3 锁环式同步器主要尺寸的确定 (54)6.1.4 同步器主要参数的确定 (55)6.2 变速器操纵机构的设计选用 (57)6.2.1 变速器操纵机构的分类 (57)6.2.2 变速器常用操纵机构分析 (58)6.3 变速器箱体的设计 (59)6.4 本章小结 (60)结论 (61)参考文献 (62)致谢 (63)附录A (64)附录B (65)第1章绪论1.1 汽车变速器概述自1886年世界上第一辆汽车诞生以来,汽车已经历了近120年的发展。
两轴式四档手动变速器设计正文
两轴式四档手动变速器设计摘要轿车作为一种最常用汽车,已在现代的社会中占有举足轻重的地位。
而变速器是汽车传动系统结构中最重要的部分之一,汽车的前进、后退,增速、减速都要靠变速器传动来实现。
而且变速器在汽车的动力性和燃油经济性上也有很重要的影响。
本次设计的汽车变速箱主要是从强度方面来对齿轮的尺寸计算及校核,轴的尺寸计算和位置的确定,选择设计满足其承载能力的同步器。
另外,针对齿轮作用力的不同,在不同的轴上选择合适的轴承。
利用软件AUTCAD完成变速器总成图、第一轴、第二轴、中间轴、各个挡齿轮及同步器的设计。
随着我国汽车行业的迅猛发展,人们对汽车的需求也越来越高。
通过对轿车车变速器的设计,我了解到变速器在汽车结构中具有着重要的作用,因此变速器结构的改进对汽车行业的发展与进步具有着深远的意义。
关键词:汽车;变速器;齿轮AbstractsAs a automobile commonly used by commercial vehicles,in modern society occupies a pivo- tal position.And the transmission gearbox is one of most important parts in the automobile transmission system structure,automobile's advance,the backlash,the growth rate,the deceleration must depend on the transmission gearbox transmission to realize.Moreover the transmission gearbox also has the very important influence in automobiles power and the fuel oil efficiency.This design is mainly gear's size computation and the examination,the axis size's calcul-ation and the position's determination,the choice design satisfies its bearing capacity the syn- chromesh. Moreover,in view of the gear action's difference, chooses the appropriate bearing on the different axis.Completes the transmission gearbox unit chart,the first axis,the second axis, the intermediate shaft using software AUTCAD, to keep off the gear and the synchromesh design one by one.Along with our country automobile profession rapid development,the people are also g- etting higher and higher to automobile's demand,Through to the truck transmission gearbox's design,I understood the transmission gearbox is having the vital role in the automobile struct- ure,so the transmission gearbox structure improvement is having the profound significance to the automobile profession development and the progress.Keyword:Automobile; Transmission gearbox; Gear;毕业设计(论文)原创性声明和使用授权说明原创性声明本人郑重承诺:所呈交的毕业设计(论文),是我个人在指导教师的指导下进行的研究工作及取得的成果。
三轴五档汽车变速器-说明书
二零零年月
摘
本设计的任务是设计一台用于轿车上的FR式的手动变速器。本设计采用中间轴式变速器,该变速器具有两个突出的优点:一是其直接档的传动效率高,磨损及噪声也最小;二是在齿轮中心距较小的情况下仍然可以获得较大的一档传动比。
根据轿车的外形、轮距、轴距、最小离地间隙、最小转弯半径、车辆重量、满载重量以及最高车速等参数结合自己选择的适合于该轿车的发动机型号可以得出发动机的最大功率、最大扭矩、排量等重要的参数。再结合某些轿车的基本参数,选择适当的主减速比。根据上述参数,再结合汽车设计、汽车理论、机械设计等相关知识,计算出相关的变速器参数并论证设计的合理性。
其次,对于老司机和大部分男士司机来说,他们的最爱还是手动变速器。从我国的具体情况来看,手动变速器几乎贯穿了整个中国的汽车发展历史,资历较深的司机都是“手动”驾车的,他们对手动变速器的认识程度是非常深刻的,如果让他们改变常规的做法,这是不现实的。虽然自动变速器以及无级变速器已非常的普遍,但是大多数年轻的司机还是崇尚手动,尤其是喜欢超车时手动变速带来的那种快感,所以一些中高档的汽车(尤其是轿车)也不敢轻易放弃手动变速器。另外,现在在我国的汽车驾驶学校中,教练车都是手动变速器的,除了经济适用之外,关键是能够让学员打好扎实的基本功以及锻炼驾驶协调性。
- 1、下载文档前请自行甄别文档内容的完整性,平台不提供额外的编辑、内容补充、找答案等附加服务。
- 2、"仅部分预览"的文档,不可在线预览部分如存在完整性等问题,可反馈申请退款(可完整预览的文档不适用该条件!)。
- 3、如文档侵犯您的权益,请联系客服反馈,我们会尽快为您处理(人工客服工作时间:9:00-18:30)。
第三节变速器主要参数的选择一、挡数增加变速器的挡数能够改善汽车的动力性和经济性。
挡数越多,变速器的结构越复杂,并且使轮廓尺寸和质量加大,同时操纵机构复杂,而且在使用时换挡频率也增高。
在最低挡传动比不变的条件下,增加变速器的挡数会使变速器相邻的低挡与高挡之间的传动比比值减小,使换挡工作容易进行。
要求相邻挡位之间的传动比比值在1.8以下,该值越小换挡工作越容易进行。
要求高挡区相邻挡位之间的传动比比值要比低挡区相邻挡位之间的传动比比值小。
近年来为了降低油耗,变速器的挡数有增加的趋势。
目前,轿车一般用4~5个挡位的变速器,级别高的轿车变速器多用5个挡,货车变速器采用4~5个挡或多挡。
装载质量在2~3.5t的货车采用5挡变速器,装载质量在4~8t的货车采用6挡变速器。
多挡变速器多用于重型货车和越野汽车。
二、传动比范围变速器的传动比范围是指变速器最低挡传动比与最高挡传动比的比值。
传动比范围的确定与选定的发动机参数、汽车的最高车速和使用条件(如要求的汽车爬坡能力)等因素有关。
目前轿车的传动比范围在3~4之间,轻型货车在5~6之间,其它货车则更大。
三、中心距A对中间轴式变速器,是将中间轴与第二轴之间的距离称为变速器中心距A 。
它是一个基本参数,其大小不仅对变速器的外形尺寸、体积和质量大小,而且对拎齿的接触强度有影响。
中心距越小,轮齿的接触应力越大,齿轮寿命越短。
因此,最小允许中心距应当由保证轮齿有必要的接触强度来确定。
变速器轴经轴承安装在壳体上,从布置轴承的可能与方便和不影响壳体的强度考虑,要求中心距取大些。
此外,受一挡小齿轮齿数不能过少的限制,要求中心距也要取大些。
初选中心距A 时,可根据下面的经验公式计算31max g e A i T K A η=式中,A 为变速器中心距(mm);A K 为中心距系数,轿车:A K =8.9~9.3,货车:A K =8.6~9.6,多挡变速器:A K =9.5~11.O ;max e T 为发动机最大转矩(N·m);1i 为变速器一挡传动比;g η为变速器传动效率,取96%。
轿车变速器的中心距在65~80mm 范围内变化,而货车的变速器中心距在80~170mn 范围内变化。
原则上总质量小的汽车,变速器中心距也小些。
四、外形尺寸变速器的横向外形尺寸,可根据齿轮直径以及倒挡中间(过渡)齿轮和换挡机构的布量初步确定。
轿车四挡变速器壳体的轴向尺寸为(3.O ~3.4)A 。
货车变速器壳体的轴向尺寸与挡数有关,可参考下列数据选用:四挡 (2.2~2.7)A五挡 (2.7~3.O)A六挡 (3.2~3.5)A当变速器选用的常啮合齿轮对数和同步器多时,中心距系数K 应取给出范围的上限。
为了检测方便,中心距A 最好取为整数。
五、轴的直径变速器工作时,轴除传递转矩外,还承受来自齿轮作用的径向力,如果是斜齿轮则还有轴向力。
在这些力的作用下,变速器的轴必须有足够的刚度和强度。
轴的刚度不足会产生弯曲变形,破坏齿轮的正确啮合,对齿轮的强度和耐磨性均产生不利影响,还会增加工作噪声。
中间轴式变速器的第二轴和中间轴中部直径d≈O.45A ,轴的最大直径d 和支承间距离L 的比值,对中间轴,d /L=O.16~O.18,对第二轴,d /L=O.18~O.21。
第一轴花键部分直径d(mm)可按下式初选 3max e T K d式中,K 为经验系数,K=4.O ~4.6;max e T 为发动机最大转矩(N·m)。
六、齿轮参数1、模数的选取齿轮模数是一个重要参数,并且影响它的选取因素又很多,如齿轮的强度、质量、噪声、工艺要求等。
应该指出,选取齿轮模数时一般遵守的原则是:为了减少噪声应合理减小模数,同时增加齿宽;为使质量小些,应该增加模数,同时减少齿宽;从工艺方面考虑,各挡齿轮应该选用一种模数,而从强度方面考虑,各挡齿轮应有不同的模数。
减少轿车齿轮工作噪声有较为重要的意义,因此齿轮的模数应选得小些;对货车,减小质量比减小噪声更重要,故齿轮应该选用大些的模数。
变速器低挡齿轮应选用大些的模数,其它挡位选用另一种模数。
少数情况下汽车变速器各挡齿轮均选用相同的模数。
变速器用齿轮模数范围大致如下:微型和普通级轿车为2.25~2.75mm,中级轿车为2.75—3.00mm.中型货车为3.5~4.5 mm,重型货车为4.5~6.0mm。
所选模数值应符合国家标准GB1357—78的规定。
啮合套和同步器的接合齿多数采用渐开线齿形。
由于工艺上的原因,同一变速器中的接合齿模数相同。
其取用范围是:轿车和轻、中型货车为2.O~3.5mm;重型货车为3.5~5.0ram。
选取较小的模数值可使齿数增多,有利于换挡。
2、压力角α压力角较小时,重合度较大,传动平稳,噪声较低;力角较大时,可提高轮齿的抗弯强度和表面接触强度。
对于轿车,为加大重合度以降低噪声,应取用14.5º、1 5º、1 6º、16.5º等小些的压力角;对货车,为提高齿轮承载能力,应选用22.5º或25º等大些的压力角。
实际上,因国家规定的标准压力角为20º,所以变速器齿轮普遍采用的压力角为20º。
啮合套或同步器的接合齿压力角有20º、25º、30º等,但普遍采用30º压力角。
3、螺旋角β斜齿轮在变速器中得到广泛的应用。
选取斜齿轮的螺旋角,应该注意到它对齿轮工作噪声、轮齿的强度和轴向力有影响。
在齿轮选用大些的螺旋角时,使齿轮啮合的重合度增加,因而工作平稳、噪声降低。
试验还证明:、随着螺旋角的增大,齿的强度也相应提高,不过当螺旋角大于30。
时,其抗弯强度骤然下降,而接触强度仍继续上升。
因此,从提高低挡齿轮的抗弯强度出发,并不希望用过大的螺旋角;而从提高高挡齿轮的接触强度着眼,应当选用较大的螺旋角。
斜齿轮传递转矩时,要产生轴向力并作用到轴承上。
设计时应力求中间轴上同时工作的两对齿轮产生轴向力平衡,以减少轴承负荷,提高轴承寿命。
因此,中间轴上的不同挡位齿轮的螺旋角应该是不一样的。
为使工艺简便,在中间轴轴向力不大时,可将螺旋角设计成一样的,或者仅取为两种螺旋角。
中间轴上全部齿轮的螺旋方向应一律取为右旋,则第一、第二轴上的斜齿轮应取为左旋。
轴向力经轴承盖作用到壳体上。
一挡和倒挡设计为直齿时,在这些挡位上工作,中间轴上的轴向力不能抵消(但因为这些挡位使用得少,所以也是允许的),而此时第二轴则没有轴向力作用。
根据图3-12可知,欲使中间轴上两个斜齿轮的轴向力平衡,须满足下述条件111tan β=n a F F 222tan β=n a F F由于2211r F r F T n n ==为使两轴向力平衡,必须满足 2121tan tan r r =ββ图3—12 中间轴轴向力的平衡式中,1a F 、2a F 为作用在中间轴齿轮1、2上的轴向力;1n F 、F为作用在中间轴上齿轮1、2上的圆周力;1r、2r为齿轮1、2n2的节圆半径;T为中间轴传递的转矩。
最后可用调整螺旋角的方法,使各对啮合齿轮因模数或齿数和不同等原因而造成的中心距不等现象得以消除。
斜齿轮螺旋角可在下面提供的范围内选用:轿车变速器:两轴式变速器为20º~25º中间轴式变速器为22º~34º货车变速器:18º~26º4、齿宽b在选择齿宽时,应该注意到齿宽对变速器的轴向尺寸、齿轮工作平稳性、齿轮强度和齿轮工作时受力的均匀程度等均有影响。
考虑到尽可能缩短变速器的轴向尺寸和减小质量,应该选用较小的齿宽。
另一方面,齿宽减少使斜齿轮传动平稳的优点被削弱,此时虽然可以用增加齿轮螺旋角的方法给予补偿,但这时轴承承受的轴向力增大,使之寿命降低;齿宽窄还会使齿轮的工作应力增加。
选用宽些的齿宽,工作时会因轴的变形导致齿轮倾斜,使齿轮沿齿宽方向受力不均匀并在齿宽方向磨损不均匀。
通常根据齿轮模数m(m)的大小来选定齿宽:n直齿:b=K m,c K为齿宽系数,取为4.5~8.Oc斜齿:b=c K n m ,c K 取为6.O ~8.5b 为齿宽(mm)。
采用啮合套或同步器换挡时,其接合齿的工作宽度初选时可取为(2~4)m 。
第一轴常啮合齿轮副的齿宽系数c K 可取大些,使接触线长度增加、接触应力降低,以提高传动平稳性和齿轮寿命。
5、齿轮变位系数的选择原则齿轮的变位是齿轮设计中一个非常重要的环节。
采用变位齿轮,除为了避免齿轮产生根切和配凑中心距以外,它还影响齿轮的强度,使用平稳性,耐磨损、抗胶合能力及齿轮的啮合噪声。
变位齿轮主要有两类:高度变位和角度变位。
高度变位齿轮副的一对啮合齿轮的变位系数之和等于零。
高度变位可增加小齿轮的齿根强度,使它达到和大齿轮强度相接近的程度。
高度变位齿轮副的缺点是不能同时增加一对齿轮的强度,也很难降低噪声。
角度变位齿轮副的变位系数之和不等于零。
角度变位既具有高度变位的优点,又避免了其缺点。
由几对齿轮安装在中间轴和第二轴上组合并构成的变速器,会因保证各挡传动比的需要,使各相互啮合齿轮副的齿数和不同。
为保证各对齿轮有相同的中心距,此时应对齿轮进行变位。
当齿数和多的齿轮副采用标准齿轮传动或高度变位时,则对齿数和少些的齿轮副应采用正角度变位。
由于角度变位可获得良好的啮合性能及传动质量指标,故采用得较多。
对斜齿轮传动,还可通过选择合适的螺旋角来达到中心距相同的要求。
变速器齿轮是在承受循环负荷的条件下工作,有时还承受冲击负荷。
对于高挡齿轮,其主要损坏形式是齿面疲劳剥落,因此应按保证最大接触强度和抗胶合及耐磨损最有利的原则选择变位系数。
为提高接触强度,应使总变位系数尽可能取大些,这样两齿轮的齿廓渐开线离基圆较远,以增大齿廓曲率半径,减小接触应力。
对于低挡齿轮,由于小齿轮的齿根强度较低,加之传递载荷较大,小齿轮可能出现齿根弯曲断裂的现象。
为提高小齿轮的抗弯强度,应根据危险断面齿厚相等的条件来选择大、小齿轮的变位系数,此时小齿轮的变位系数大于零。
由于工作需要,有时齿轮齿数取得少(如一挡主动齿轮)会造成轮齿根切,这不仅削弱了轮齿的抗弯强度,而且使重合度减小。
此时应对齿轮进行正变位,以消除根切现象。
总变位系数21ε+ε=εc 越小,一对齿轮齿根总的厚度越薄,齿根越弱,抗弯强度越低。
但是由于轮齿的刚度减小,易于吸收冲击振动,故噪声要小一些。
另外,c ε值越小,齿轮的齿形重合度越大,这不但对降噪有利,而且由于齿形重合度增大,单齿承受最大载荷时的着力点距齿根近,弯曲力矩减小,相当于齿根强度提高,对由于齿根减薄而产生的削弱强度的因素有所抵消。
根据上述理由,为了降低噪声,对于变速器中除去一、二挡和倒挡以外的其它各挡齿轮的总变位系数要选用较小一些的数值,以便获得低噪声传动。