DFM可制造性设计
制造DFM(可制造性设计)培训最强资料

第一讲 DFM(可制造性设计)一、概述:1.1最优化设计DFX随着越来越多的公司引入可制造性设计(DFM)方法来提高利润和产量,最优化设计(DFX)的概念逐渐变得引人瞩目起来。
成功实施DFX,可以确保产品的生产和检测质量,保证高度的可制造性和可测试性,因而DFX可以说是电子组装中的一个关键性因素。
缺乏有竞争力的DFX文化和方法可能导致设计失败。
虽然DFX已被各种各样地定义,但总的来说包括以下几种:DFM:Design for Manufacturing,可制造性设计;DFT/DFD: Design for Test/Design for Diagnosibility可测试/可分析设计;DFA:Design for Assembly,可装配设计;DFE:Design for Environment,环保型设计DFF:Design for Fabrication of the PCB,PCB可制造性设计;DFS:Design for Sourcing,可周转性设计;DFR:Design for Reliability,可靠性设计;DFX:Design for "X",包括以上所有。
SMT行业正渐渐地、实实在在地接受DFX的概念。
要让公司的各部门,特别是分布在全球各地的公司各部门,普遍接受DFX理念,虽然是一件困难的任务,不过随着新型传媒(如Web)的发展和公司决策阶段的不断重视,DFX 的实施会在企业内部及行业内逐步延伸和深化。
表面贴装顾问委员会(SMC)在七八年前就提出了DFX概念,以鼓励可制造性(DFM)、可测试性和可靠性等的设计。
从那以后,SMC不断推广DFX概念并鼓励应用DFX。
在1996年的表面贴装国际会议上,DFX是其中一个主要议题;同年SMC 出版了一个包含6个DFX白皮书的文件(其副本可从IPC–连接电子工业协会获得)。
该文件名SMC-WP-004,包括以下论文:《成功的设计》,作者为Hiatt & Associates公司的Dale Hiatt;《装配设计》,作者是Tessera公司的Vern Solberg;《构造设计》,作者是德州仪器公司的Foster Gray;《测试设计》,作者是Teradyne公司的Paul Spitz ;《可靠性设计》,作者是Engelmaier & Associates公司的Werner Engelmaier和乔治亚技术学院的Laura Turbini;以及IPC的Christopher Rhodes所写的《环境设计》。
dfm报告是什么意思

dfm报告是什么意思DFM报告是什么意思。
DFM,即Design for Manufacturability,中文意思为“可制造性设计”。
DFM报告是在产品设计阶段,为了提高产品的制造效率和降低制造成本而进行的一项重要工作。
DFM报告的目的是通过对产品设计的全面评估,找出可能存在的制造难点和问题,并提出相应的改进建议,以确保产品的顺利制造和生产。
DFM报告通常由制造工程师或专业的DFM团队来编制,他们会根据产品的具体设计图纸和技术要求,对产品进行全面的分析和评估。
在DFM报告中,通常会包括以下几个方面的内容:1. 材料选择,对产品所选用的材料进行评估,包括材料的可获得性、成本、加工性能等方面的考量。
如果产品设计中存在材料选择上的问题,DFM报告会提出更合适的材料建议。
2. 结构设计,对产品的结构设计进行评估,包括零部件的连接方式、结构强度、稳定性等方面的分析。
如果产品结构存在问题,DFM报告会提出相应的改进建议。
3. 制造工艺,对产品的制造工艺进行评估,包括加工工艺、装配工艺等方面的分析。
DFM报告会提出如何优化制造工艺,以提高生产效率和降低成本。
4. 可靠性设计,对产品的可靠性进行评估,包括产品的寿命、耐久性、抗疲劳性等方面的分析。
DFM报告会提出如何改善产品的可靠性设计建议。
5. 成本分析,对产品的制造成本进行评估,包括材料成本、加工成本、人工成本等方面的分析。
DFM报告会提出如何降低制造成本的建议。
通过DFM报告的编制和实施,可以有效地减少产品设计中的制造难点和问题,提高产品的制造效率和质量,降低制造成本,从而提高企业的竞争力和市场占有率。
总之,DFM报告是在产品设计阶段进行的一项重要工作,它的目的是通过全面的评估和分析,找出产品设计中可能存在的制造难点和问题,并提出相应的改进建议,以确保产品的顺利制造和生产。
通过DFM报告的实施,可以有效地提高产品的制造效率和质量,降低制造成本,为企业的发展提供有力支持。
DFM设计可制造性规范
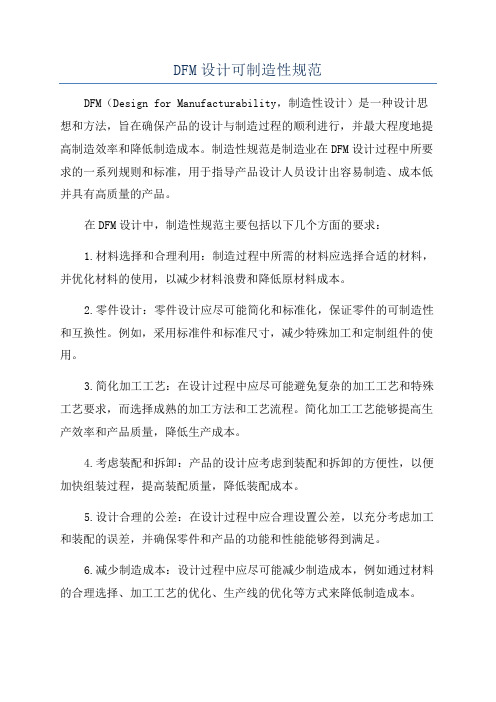
DFM设计可制造性规范DFM(Design for Manufacturability,制造性设计)是一种设计思想和方法,旨在确保产品的设计与制造过程的顺利进行,并最大程度地提高制造效率和降低制造成本。
制造性规范是制造业在DFM设计过程中所要求的一系列规则和标准,用于指导产品设计人员设计出容易制造、成本低并具有高质量的产品。
在DFM设计中,制造性规范主要包括以下几个方面的要求:1.材料选择和合理利用:制造过程中所需的材料应选择合适的材料,并优化材料的使用,以减少材料浪费和降低原材料成本。
2.零件设计:零件设计应尽可能简化和标准化,保证零件的可制造性和互换性。
例如,采用标准件和标准尺寸,减少特殊加工和定制组件的使用。
3.简化加工工艺:在设计过程中应尽可能避免复杂的加工工艺和特殊工艺要求,而选择成熟的加工方法和工艺流程。
简化加工工艺能够提高生产效率和产品质量,降低生产成本。
4.考虑装配和拆卸:产品的设计应考虑到装配和拆卸的方便性,以便加快组装过程,提高装配质量,降低装配成本。
5.设计合理的公差:在设计过程中应合理设置公差,以充分考虑加工和装配的误差,并确保零件和产品的功能和性能能够得到满足。
6.减少制造成本:设计过程中应尽可能减少制造成本,例如通过材料的合理选择、加工工艺的优化、生产线的优化等方式来降低制造成本。
7.考虑生命周期环境:产品设计应考虑产品的整个生命周期环境,包括运输、使用和维护过程中的各种环境因素,以确保产品能够在不同环境下正常运行和维护。
通过遵循制造性规范,设计人员可以更好地理解制造过程和要求,并在产品设计的早期考虑到制造相关因素,从而提高产品的制造效率和质量,降低制造成本。
同时,制造性规范还可以促进设计人员和制造人员之间的沟通和合作,加强产品设计与制造之间的衔接,减少设计变更和重工的发生,提高整个生产过程的效率。
总而言之,DFM设计可制造性规范是一种促进制造业发展的重要方法和思想,通过遵循制造性规范,设计人员能够设计出更易于制造和更具竞争力的产品,从而提高企业的竞争力和市场占有率。
可制造性设计(DFM)
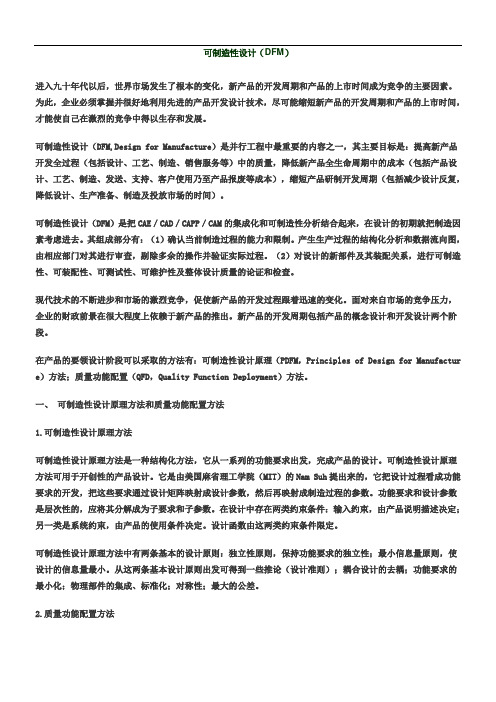
可制造性设计(DFM)进入九十年代以后,世界市场发生了根本的变化,新产品的开发周期和产品的上市时间成为竞争的主要因素。
为此,企业必须掌握并很好地利用先进的产品开发设计技术,尽可能缩短新产品的开发周期和产品的上市时间,才能使自己在激烈的竞争中得以生存和发展。
可制造性设计(DFM,Design for Manufacture)是并行工程中最重要的内容之一,其主要目标是:提高新产品开发全过程(包括设计、工艺、制造、销售服务等)中的质量,降低新产品全生命周期中的成本(包括产品设计、工艺、制造、发送、支持、客户使用乃至产品报废等成本),缩短产品研制开发周期(包括减少设计反复,降低设计、生产准备、制造及投放市场的时间)。
可制造性设计(DFM)是把CAE/CAD/CAPP/CAM的集成化和可制造性分析结合起来,在设计的初期就把制造因素考虑进去。
其组成部分有:(1)确认当前制造过程的能力和限制。
产生生产过程的结构化分析和数据流向图,由相应部门对其进行审查,剔除多余的操作并验证实际过程。
(2)对设计的新部件及其装配关系,进行可制造性、可装配性、可测试性、可维护性及整体设计质量的论证和检查。
现代技术的不断进步和市场的激烈竞争,促使新产品的开发过程跟着迅速的变化。
面对来自市场的竞争压力,企业的财政前景在很大程度上依赖于新产品的推出。
新产品的开发周期包括产品的概念设计和开发设计两个阶段。
在产品的要领设计阶段可以采取的方法有:可制造性设计原理(PDFM,Principles of Design for Manufactur e)方法;质量功能配置(QFD,Quality Function Deployment)方法。
一、可制造性设计原理方法和质量功能配置方法1.可制造性设计原理方法可制造性设计原理方法是一种结构化方法,它从一系列的功能要求出发,完成产品的设计。
可制造性设计原理方法可用于开创性的产品设计。
它是由美国麻省理工学院(MIT)的Nam Suh提出来的,它把设计过程看成功能要求的开发,把这些要求通过设计矩阵映射成设计参数,然后再映射成制造过程的参数。
产品dfm报告是什么意思

产品dfm报告是什么意思什么是DFMDFM是Design for Manufacturability(可制造性设计)的缩写,是一种将产品设计、工程和制造领域的原则和方法相结合的设计过程。
DFM的目标是通过优化产品的设计,使得产品在制造、装配和维护过程中更容易和更经济地生产。
DFM考虑了材料的选取、工艺的选择、零件的设计、装配的方案等诸多因素,以最大程度地提高制造效率、降低成本、增强产品质量。
什么是产品DFM报告产品DFM报告是对产品设计可制造性的评估和分析的文档,旨在为设计师、工程师和制造商提供指导和建议,帮助他们改进产品设计,以便更好地满足制造要求和标准。
产品DFM报告通常由专业的DFM团队或工程师编制,涵盖了产品设计、材料、工艺、质量和成本等方面的考虑。
产品DFM报告的内容产品DFM报告通常包括以下内容:1. 产品设计评估产品设计评估是产品DFM报告中的重要部分。
它涉及对产品设计图纸、样品或虚拟模型的分析,以评估其制造可行性和可优化性。
产品设计评估主要考虑以下因素:- 零件的形状和结构:评估零件的形状、尺寸和结构是否符合制造工艺的要求,是否能够在加工过程中保持稳定性和精度。
- 零件材料的选择:评估零件材料的可用性、成本和适用性,以及其对产品性能和质量的影响。
- 零件的装配方式:评估零件的装配方式和顺序,以确保装配过程的顺利进行和高效性。
2. 材料选择和工艺优化产品DFM报告还涉及材料选择和工艺优化的建议。
这部分主要考虑以下内容:- 材料的选择:根据产品的需求和制造要求,评估不同材料的可行性,并提出合适的材料选择建议。
- 工艺的选择:评估不同工艺的优劣,选择最适合产品要求和制造成本的工艺,并提供工艺优化的建议。
- 加工和装配方法:提供加工和装配方法的建议,以确保零件和组件能够在制造过程中顺利加工和装配。
3. 质量控制和测试方案产品DFM报告还包括质量控制和测试方案的建议。
这部分内容主要考虑以下方面:- 质量控制方法:提供质量控制方法和措施的建议,以确保产品在制造过程中达到预定质量标准。
DFM产品可制造性设计规范

文件制修订记录1.0目的为了让设计者更好的了解如何在材料,工艺和设备影响印刷电路设计,提供设计和布局的印刷电路组件的概念,给设计者一个基本的设计建议和NPI工程师一个基本指导。
2.0适用范围:适用于指导PCB产品的生产过程中所需的要求。
3.0术语:3.1 DFM:产品可制造性设计(Design for manufacturability)。
用来确定生产线的规划,使其设备满足公司产品、工艺和品质要求。
3.2 PCB:Printed Circuit Board印刷线路板;3.3 FPC:Flexible Printed Circuit 简称,柔性印刷线路板;3.4 layout: 布局设计。
4.0职责:4.1项目BU负责与客户沟通,向公司内部传达客户信息;4.2 NPI小组的PIE/ME负责制作DFM报告,NPI组长负责主导召开新产品评估会议和DFM报告的审核,工程部经理负责批准;4.3新产品导入小组(NPI)负责评估新产品的可制造性。
5.0程序:5.1项目BU负责在新合同评审时,在客户有要求或者NPI小组评估需要时召集公司NPI专家评审小组成员对新产品进行可制造性评审,由NPI PIE/ME负责根据会议的结果在两个工作日内完成“可制造性评估(DFM)报告”;5.2 NPI PIE/ME将制作完成的DFM报告提交给NPI主管审核,审核OK之后,提交工程部经理批准;5.3工程部经理批准后DFM报告NPI主管转发给项目经理提交给客户或直接提供客户对应的工程人员;5.4 PIE/ME确认DFM报告中客户的评价与改善方案,以便作出相应的对策。
6.0可制造性设计规范DFM 1、PCB/FPC layout1.1印制线路要点:虽然布置layout是运用的软件,但是要考虑线路的形状尽可能的简单以此缩减制作成本,直角形状的板子比其它不规则的形状的成本低且更容易处理。
设计内部的拐角必须考虑板子的外形,避免暴露在外面。
浅谈DFM(半导体晶片可制造性设计)现况
Metal 1, AlCuP-EpiP-Wafer N-Well P-WellPMD p +p +n +n +WMetal 1Contact P-well N-well Polycide gate and local interconnectionV ssV ddNMOS PMOSV inV out STICMOS inverter layout Mask 1, N-well Mask 2, P-wellMask 3, shallow trench isolation Mask 4, 7, 9, N-Vt, LDD, S/D Mask 5, 8, 10, P-Vt, LDD, S/D Mask 6, gate/local interconnection Mask 11, contact Mask 12, metal 1Layout and Masks of CMOS Inverter曝光後製作出來的圖形已經變形得無法接受當波長小於孔徑繞射會嚴重影響成像,目前曝光所使用的光波長為193nm ,而我們所要顯影的線寬卻是65nm 或更小Why DFM?CMP (Chemical Mechanical Polishing)鑽石植佈技術化學蝕刻與機械磨削兩者相互作用下,將晶片上凸出的沈積層,加以去除密度不同的區域,研磨的速率不同,若密度不均則會增加後續製程上的困難增加金屬層的密度均勻度有助於改善製程中平坦化的良率Critical Area Analysis z A defect shorting conductor lines causing a fault.wireDefect of size r Critical area for defect of size rshort Particle causes openParticle causes shortMicrolithography微影製程z將圖形顯影於矽晶圓Optical Proximity Correction (OPC)z Optical proximity correction (OPC) is a photolithography enha ncement techniques commonly used to compensate the mask p attern for image errors due to diffraction or process effectsHammer headjogserifExtension Typical OPC typeCorner roundingz simulation-based lithography OPC verification tool to ensure effective OPC before mask makingEEtaiwan: 台積電(TSMC)推出設計參考流程7.0版。
dfm制造可行性分析报告
dfm制造可行性分析报告一、概述在产品设计和制造过程中,DFM(Design for Manufacturability,可制造性设计)是一项重要的方法和原则,旨在最大限度地优化产品的制造性能、降低制造成本,并确保产品质量。
本报告将对DFM制造可行性进行全面分析,以评估产品制造的可行性,并提出相应的优化建议,保障产品的生产效率和质量。
二、DFM分析1. 产品设计与制造工艺的匹配在产品设计阶段,需要充分考虑到产品的制造工艺,与工艺流程相匹配。
通过工艺分析,我们可以评估产品设计是否合理,是否能够在现有的制造条件下高效生产。
2. 材料选择与可加工性材料的选择对于产品制造过程中的成本和质量具有重要影响。
我们需要评估材料的可加工性,包括加工难度、成本和稳定性等因素,以确保材料与制造工艺的匹配性。
3. 零部件设计分析零部件的设计对产品的制造性能和质量同样至关重要。
我们需要分析零部件的设计是否合理,是否能够满足生产工艺的要求,并提出相应的改进建议。
4. 工艺流程分析通过对工艺流程的分析,我们可以评估产品的制造难度、性能稳定性等因素,从而对生产过程进行优化。
在此过程中,我们需要关注生产效率、设备利用率和人力成本等关键指标,并提供相应的改进措施。
5. 设备和工装评估评估生产设备和工装的适用性和可靠性,以确保其能够满足产品制造的需求。
同时,我们需要关注设备的维护和保养,以保证其长期稳定运行。
三、优化建议1. 设计优化在产品设计阶段,我们建议将制造工艺要求纳入考虑,并与设计团队进行密切沟通。
通过优化设计方案,减少零部件数量和复杂性,提高产品的可制造性。
2. 材料优化在材料选择上,我们建议选用易加工、成本适中且质量稳定的材料。
同时,优化材料库存管理,减少资源浪费和库存压力。
3. 工艺流程优化通过精简工艺流程,优化制造顺序和工艺参数的设定,可以提高生产效率和产品质量。
同时,引入自动化设备和机器人技术,提升制造过程的稳定性和一致性。
dfm标准
dfm标准
DFM(Design for Manufacturing)即面向制造的设计,是一种在制造行业中的重要标准和依据,旨在通过优化产品设计和制造流程来降低生产成本、提高质量和效率。
它确保了产品设计与制造之间的协调和无缝衔接。
DFM标准涉及到多个方面,包括产品的可制造性、PCB(印刷电路板)的设计和材料选择等。
以下是一些常见的DFM标准:
1.产品可制造性:产品设计应考虑到制造的可行性和成本效益,以确保产品能够
在现有的生产设备和工艺条件下顺利制造出来。
2.PCB设计:PCB的设计应符合一定的规范和标准,包括基材的选择(如环氧玻
璃布覆铜板)、铜箔的厚度(如双层板成品表面铜箔厚度≥35μm)等。
此外,PCB
的结构、尺寸和公差等也需要符合设计要求,以确保其可制造性和可靠性。
3.材料选择:在选择材料时,应考虑到其可加工性、成本、环保性等因素,以确
保所选材料能够满足产品的制造要求。
此外,DFM标准还强调在产品开发设计时起就考虑到可制造性和可测试性,使设计和制造之间紧密结合。
通过遵循DFM标准,企业可以降低生产成本、提高生产效率、减少生产缺陷,从而获得更好的经济效益和市场竞争力。
请注意,具体的DFM标准可能因不同的行业、企业和产品而有所差异。
因此,在实际应用中,需要根据具体情况制定相应的DFM标准和规范。
模具设计DFM模板
• DFM简介 • 模具设计前期准备 • 模具结构设计 • DFM评审与优化 • DFM模板应用案例
01
DFM简介
DFM定义
DFM是Design for Manufacturability的缩写,中文称为“可制造性设计”。它 是一种设计方法论,旨在确保产品设计在制造过程中具有高效、低成本和高质量 的特点。
感谢观看
DFM强调在设计阶段充分考虑制造过程中的需求和限制,通过优化设计来降低制 造成本、提高生产效率并减少产品缺陷。
DFM的目的和重要性
目的
DFM的目标是在产品设计阶段就发现和解决可能影响制造的 问题,从而提高产品的可制造性,降低生产成本,缩短产品 上市时间。
重要性
随着市场竞争的加剧,产品的质量和上市时间成为企业成功 的关键因素。DFM能够帮助企业在设计阶段就预测和解决制 造问题,提高产品质量和生产效率,降低生产成本,从而增 强企业的市场竞争力。
DFM的流程和内容
流程
DFM的流程包括评估设计方案、确定制造需求、制定制造规范、进行可制造性 评审、优化设计方案等步骤。
内容
DFM的内容包括产品结构的合理性、制造工艺的可行性、生产效率、制造成本 等方面。在DFM过程中,需要综合考虑材料、工艺、设备、人力资源等各方面 的因素,确保设计方案符合制造需求和规范。
02
模具设计前期准备
产品分析
产品结构分析
对产品进行详细的结构分析,包 括产品的形状、尺寸、精度要求 等,以便确定模具设计的难点和
重点。
材料性能分析
了解产品的材料性能,如材料的硬 度、韧性、热处理状态等,以便选 择合适的模具材料和热处理工艺。
工艺性分析
评估产品在生产过程中的可加工性, 如切削性能、焊接性能等,以便在 模具设计中考虑到生产工艺的需求。
- 1、下载文档前请自行甄别文档内容的完整性,平台不提供额外的编辑、内容补充、找答案等附加服务。
- 2、"仅部分预览"的文档,不可在线预览部分如存在完整性等问题,可反馈申请退款(可完整预览的文档不适用该条件!)。
- 3、如文档侵犯您的权益,请联系客服反馈,我们会尽快为您处理(人工客服工作时间:9:00-18:30)。
2
DFM誕生背景
• 电子产品不论是电视机, 计算机, 手提电话或其它产品, 基本上是由产品设计, 量产制造, 然后上市行销. 但长久以来产品设计与量产制造之间始终存在着需 多沟通不良的情形, 也因此造成许多不必要的争执与人力, 物力或成本上的损 失 • 传统上, 产品在设计部门设计完成后, 便交付生产线试产及量产, 但是在生产线 上我们常可听到工程师的抱怨" PCB设计不佳, 造成SMD或传统零件组装困难 或组装后高不良点数", 相反的在产品设计或其它部门我们也常听到"产品制造 品质太差"的检讨声.在讨论问题的时后也常常会有"产品制造品质不良应该由 生产线 负责的主张, 但生产线也会提出"产品在设计本来就不易生产"的反应, 因此到底 该如何有效整合, 这不只牵涉到设计与制造单位, 同时也影响整体的 利益. • 实际上在许多的产品生产与设计的争执中, 经过沟通讨论后大部分都是可以取 得共识并解决问题, 主要差别是在于"沟通的时机与方法", 虽然产业界许多厂 商已了解此问题的存在, 同时也推动许多如所谓"同步工程", "共同开发"…等, 多种方法以设法改善此一问题, 但仍然存在着许多"灰色地带"待解决, 传统上 许多产品开发设计到量产的模式, 生产线是在准备试产时才收到产品相关信息, 但是 即便是生产线此时发现设计瑕疵不易生产, 但如果改善牵涉到PCB LAYOUY 的大幅修改, 可能也无法被接受, 因为PCB 重新LAYOUT 耗时过长将 严重 影响产品整体进度 .
4
DFM誕生背景
• 要追究这些问题的原因, 实际上也不能归咎任何一方, 产品设计与制造单位平 日忙碌于各自专业范围内的工作, 也不一定会有机会能接触到专业以外的事务, 要改善这些问题实际上并不困难, 只要将生产线参与产品设计的时程提早, 从 零件选择, 零件 LIBRARY 的建立, 到 PCB COMPONENT PLACEMENT 的规划初 期, 就加入生产线相关工程人员的讨论与建议, 虽然不一定能完全预防产品制 造问题的发生, 但至少对严重瑕疵可有所防范, 加上后续试产后实质的检讨, 后 续即便是设计上需要局部修正, 也不致“牵一发而动全身”, 甚至产品设计人 员也可以因生产线设备或技术之提升, 而能协助解决许多产品设计上的困扰, 举例而言, 许多零件供应厂商所发出之SMD零件焊盘设计标准, 并不一定完全 实用, 某些情况下稍作修改后能使PCB LAYOUT 更加容易, 但必须由生产线 提 出相关技术资料, 如在选择某些BGA零件焊盘尺寸时, 如果能将焊盘尺寸 稍作 修改, BGA 焊盘间走线, 就可由原先1条增加为2条, 而省下PCB 空间 及LAYOUT 困难度, 但此举必须配合生产线机器及制程控制能力, 因此需要 生产线提供相 关信息.并讨论可行性 • 随着时代的进步与市场的需求, 许多电子产品设计势必更加小型化, 也因此 将 造成PCB上可使用面积更加拥挤且零件密度更高, PCB的表面可用空间可谓 "寸 土寸金", 如笔记本型计算机或其它携带式产品, 产品从设计到制造的困难度将 越来越高, 在产品规划或设计之初, 就能先行沟通并提早做好应变措施, 产品设 计与制造间积极而有效之沟通并建立一定模式, 相信不只有利于设计及制造单 位, 也同时能改善整体之效益.
可制造性设计
---Design For Manufacturability
Prepared by:
1
பைடு நூலகம்
目錄
• DFM誕生背景 • DFM 设计概念 • DFM的基本理念 • SMT产品设计评审和印制电路板DFM审核 • DFT 测试点Layout 原则
• • • • • 附錄1﹕并行工程为什么能提高产品设计开发能力 附錄2﹕腾博公司推出---DFM软件 附錄3﹕腾博公司推出---DFT软件 附錄4﹕PCB之DFM检验 附錄5﹕DFM通用指導原則
7
DFM设计概念
• 目前在工业界里,几乎没有人不谈‘品质’管理的。先进管理观念强调,品 质不是制造出来,而应该是设计出来的。这观念有其重要的地方,是使用户 从以往较被动的关注点(生产线上)移到较主动的关注点(设计上)。但说 法不够完善。严格和具体来说,品质既不是生产来的,也不是单靠设计来的, 而应该是配合来的。好的品质是通过良好的设计(配合工艺和生产能力的设 计),优良的工艺调制,和生产线上的工艺管制而获得的。而这三者又是需 要有良好的品质管理理念、知识、系统和制度来确保的。 • 要确保产品高而稳定的品质、高生产效率和低生产成本、以及准确的交货时 间,我们的生产线必须要有一套‘坚固工艺’(Robust Process)。而坚固工 艺是必须通过设计、工艺能力、和设备性能之间的完好配合才能实现的。所 谓坚固工艺,是指其对外界各种影响它表现的因素的灵敏度很低。也就是说, 对这些因素的大变化,其整体效果还是稳定不变或只限于合格范围内的变动。 • 在我们计划引进一条生产线时,我们必须确保此生产线能处理我们所要制造 的产品范围。但当我们有了生产线后,我们则应该尽力使我们的产品设计, 能适用于此生产线上制造。
6
DFM设计概念
• 为什么现今的管理对设计师在这方面的表现特别重视呢?主要是因为设计是 整个产品寿命的第一站。以效益学的观点来说,问题越是能够尽早解决,其 成本效益也就越高,问题对公司造成的损失也就越低。在电子生产管理上, 曾有学者做出这样的预测,即在每一个主要工序上,其后工序的解决成本费 用为前一道工序的10倍以上。例如设计问题如果在试制时才给予更正,其所 需费用将会较在设计时解决高出超过10倍,而如果这设计问题没有在试制时 解决,当它流到再下一个主要工序(批量生产)时,其解决费用就可能高达 100倍以上。此外,对于设计造成的问题,即使我们厂内拥有最好的设备和工 艺知识,也未必能够很完善的解决。所以基于以上的原因,把设计工作做好 是很重要的管理项目。所谓把设计做好,这里指的是包括产品功能、性能、 可制造性和质量各方面。 • SMT是一门复杂的科技。因此目前的设计师也面对许多方面知识的压力。身 为一个SMT产品设计师,必须对很多方面如元件封装、散热处理、组装能力、 工艺原材料、元件和组装寿命等等数十种科目具备一定的知识。许多这方面 的问题都是以往的插件技术中不必加以考虑和照顾的,但如今却成了必备的 知识。所以当今的设计师,他们应该具备的知识面,已不能像以往处理电子 产品设计时的范围一样。而现在谈到的DFM技术,也正是当今SMT设计师必 备的知识之一。
3
DFM誕生背景
• 许多所谓“沟通”的方法通常是, 当生产线抱怨产品设计不佳不易生产时, 由生产线订 定一份类似所谓“产品制造设计准则”, 交由产品设计单位执行, 但却又常因为许多所 谓“准则”内容不符合产品设计基本需求, 或因生产单位不了解产品设计过程, 因此许 多所谓“标准”设计单位根本无法采用, 或因造成设计单位之 困扰而被拒绝使用又未经 当面讨论, 所谓“沟通”又回到原点, 然后生产线与设计单位各自想办法, 各自解决问题, 实际上真正要解决问题不只是定标准, 或听哪 个单位的议建而已, 而是共同参与互了解 各自的需求与困难后, 取得共识并共同解决问题. • 一项产品虽然是从设计而后到量产上市, 但产品'设计'与'量产'间常因需求 不同, 甚至会 有互相矛盾的标准, 举例而言, 现代许多产品趋向所谓'轻", "薄', '短', "小', 因此在产品设 计上会缩小PCB, 增加零件密度, 及使用小型零件, 但 对制造而言, PCB缩小, 零件密度增 加, 及小型零件, 都可能因此增加零件及产品组装甚至维修困难, 另外大部分的产品设计 人员可能并不了解, 生产线上所谓 "阴影效应","墓碑效应", "森林效应", "闸流效应'…等特 性, 与锡炉焊接与回焊 焊接应该用不同的焊盘形式及尺寸, 而生产线人员可能也不了解 设计上所谓"COMPONENTS LIBRARY" , "EMI", VIA 孔径标准…等各种设计上电气规格 与需求等. • PCB在生产线上过锡炉后, 产生许多空焊, 短路等不良焊点, 需要许多人工 做修补, 其原 因可能只是因为产品设计人员, 不了解PCB 及零件过锡炉时要考虑方向, 有些短路可能 只要设计上稍做调整, 就可彻底解决, 另外对生产线而言, 可能并不了解, 虽然以制造的 标准可能某些零件并须选择在PCB上某些特定区域, 但是在产品原始设计上就已受限于 外形或其它因素, 而无法满足所需, 此类问题不只发生在业界, 甚至许多国外俱有数10 年 知名的厂商也同样存在.
8
DFM设计概念
• ‘坚固的工艺’是相对的,所以一套设计规范也是有其针对性的。它在某一 生产环境下(设备、管理、材料、工艺能力、品质标准)也许是‘坚固’的, 但在另一个环境下却可能变得不‘坚固’。因此,设计的好与不好,也是有 它的特定性。用户必须了解和牢记这一点。 • 产品寿命,是另一设计上应该注重的地方。由于产品在服务期内会受到各种 不同的环境压力(如热变化、机械振动等等),产品的设计必须确保在这方 面能经得起使用环境中会遇上的各种压力。另一个要照顾到的是制造方面, 可制造性和寿命有什么关系?一个设计得非常难组装的产品,其对服务寿命 的威胁一般也较大,而制造工艺上的小变化常常也会缩短其服务寿命。比如 一个热处理做得不好的设计,其制造过程中所受到的焊接热冲击会较大,因 温差较大使焊点的可靠性也不容易得到保证。这就影响了此产品的寿命。
• 影响寿命的因素很多,可分为主因素和次因素两大类。主因素如元件引脚种类、元件 的尺寸大小、元件和基本材料的匹配等等,这些对寿命的影响较明显严重。次因素虽 然单独的影响不是很明显严重,但几种次因素的作用加起来,其整体作用也可以是相 当可观的。这方面的例子如焊点的形状、成品的保护涂层(conformal coating)、基板的 外形比等等。在影响产品寿命的种种因素之中,热处理的考虑应该算是SMT应用中最 重要的一部分。因为在SMT应用上,许多和寿命有关的问题都是和热处理有关。它同 时也是影响可制造性的重要因素,所以在热问题的考虑上,用户应该同时兼顾到制造 工艺上和产品寿命上的问题。另外一个对热处理关注的原因,是绝大多数使用在电子 产品上的材料,他们的性能都会随温度(即关系到热处理)而发生变化的,轻则性能 不稳定,重则可能失效(暂时性)或甚至被损坏(永久性)。 • 我们了解到设计规范对我们的产品寿命(即质量)、成本和交货期都有影响,那我们 该采用什么设计规范或标准呢?我们可以发现,公开市场上有不少类似IPC等机构推荐 的设计标准。他们之间都有差别,加上各大电子厂也都有自己本身的一套规范,标准 可谓五花八门。他们之中那一个较好呢?为什么大电子厂不采用如IPC这类世界有声望 机构推荐呢?而我们是否可以采用呢?首先我们必须了解和认同的一点,是 SMT工艺 是一门复杂的科技学问,在SMT应用工作中,常出现一个问题现象是由无数因素联合 形成的这一现象。而有效的解决这些问题,有赖于我们对整体的配合能力。这是所谓 的技术整合。由于因素众多,也随时间在改变,所以要找到两家完全一样的工厂的机 会是很微小的。既然设计规范在优化的情况下是必须配合工艺和设备能力等方面的, 也就是说设计标准都有其适用范围,越是要优化其适用范围就越小。所以如果要很好 的使用设计来解决问题,一套适用于本身的规范标准是必须按本身特有的条件而开发 的。