cnc钻攻中心钻孔编程【技巧】
加工中心钻深孔的编程方法

加工中心钻深孔的编程方法加工中心是一种能够进行多种加工操作的机床,它能够进行钻孔、铣削、切割等各种加工操作。
在加工中心钻深孔时,需要进行编程来控制加工过程。
下面将介绍一下加工中心钻深孔的编程方法。
手工编程是指操作员根据工艺要求和深孔钻的尺寸要求,手动输入程序进行编程。
手工编程需要操作员具备一定的加工经验和编程技术,在加工过程中需要根据具体要求进行调整和修正。
CAD/CAM编程是指通过计算机辅助设计(CAD)和计算机辅助制造(CAM)软件来进行深孔钻的编程。
操作人员首先使用CAD软件进行3D模型的设计,然后通过CAM软件进行加工路径的生成和刀具路径的优化,最后生成机床的加工程序。
CAD/CAM编程可以提高编程的精度和效率,减少操作员的工作量。
在编写加工中心钻深孔的程序时,需要注意以下几点:1.首先,确定深孔钻的参数,包括钻孔的直径、深度、切削速度、进给速度等。
这些参数需要根据具体的工件材料和加工要求来进行选择。
2.确定刀具的选择和安装方式。
深孔钻一般使用长钻杆和内冷却器,可以有效降低切削温度,提高加工质量。
3.编写切削路径。
切削路径应该保证刀具在钻削过程中的稳定性和最优切削条件。
一般来说,采用螺旋切削路径可以提高切削效率和加工质量。
4.设置冷却液的供给。
加工深孔钻时,需要通过内冷却液来降低钻头的温度,从而提高加工质量。
在编程过程中需要设置冷却液的供给时间和流量。
5.考虑加工中心的刀库和刀具切换。
在进行复杂零件的加工时,可能需要多次换刀。
在编写程序时要考虑到刀具的切换和切换点的选择,以避免刀具碰撞或者加工误差。
总结来说,编写加工中心钻深孔的程序需要根据具体的工艺要求和机床的特点来进行选择。
手工编程和CAD/CAM编程是两种常用的方法,都需要考虑到刀具选择、切削路径、冷却液的供给等因素。
通过合理的编程,可以提高加工效率和产品质量。
加工中心钻深孔的编程方法

加工中心钻深孔的编程方法首先,加工中心钻深孔的编程需要采用G代码进行控制,因此需要编写相应的G代码程序。
编程主要分为几个步骤。
第一步是确定钻孔顺序。
在编程的过程中,需要确定钻孔的顺序,即先钻哪些孔,后钻哪些孔。
这取决于工件的几何形状和孔的位置。
通常,可以按照从外到内、从上到下的方式确定钻孔顺序,以便保证加工的稳定性和高效性。
第二步是确定切削参数。
在编程之前,需要事先确定切削参数,包括切削速度、进给速度和切削深度等。
这些参数的选择需要根据工件材料和加工要求来确定。
切削参数的选择直接影响着钻孔的质量和加工效率。
第三步是确定坐标系。
在编程之前,需要确定加工中心的坐标系,以便编写相应的G代码程序。
加工中心的坐标系通常是以工件的一些参考面或参考点为基准建立的。
编程时,需要将钻孔的坐标位置进行转换,使其与加工中心的坐标系一致。
第四步是编写G代码程序。
编写G代码程序是将加工过程指令转换为机床能够理解和执行的代码。
编写G代码程序时,需要按照加工顺序和切削参数依次编写相应的G代码指令。
一般情况下,每一个钻孔都对应着一段G代码程序,包括进给指令、刀具选取指令等。
在编程过程中1.确保钻孔参数正确。
切勿将错误的参数输入到程序中,否则会影响钻孔的质量和加工效果。
2.合理选择进给方式。
对于较深的孔,进给方式选用螺纹进给能够提高加工效率和孔的质量。
3.考虑切削液的使用。
在加工过程中,可以适当使用切削液,以降低切削温度、延长工具寿命和提高加工质量。
总之,加工中心钻深孔的编程方法主要包括确定钻孔顺序、确定切削参数、确定坐标系和编写G代码程序。
编程的准确性和合理性直接影响着钻孔的质量和加工效率。
因此,对于加工中心钻深孔的编程,需要严谨认真地进行,确保编程参数和程序的准确性和合理性。
加工中心钻孔编程实例

加工中心钻孔编程实例一、前言加工中心钻孔编程是数控加工中的重要部分,其精度和效率直接影响到产品的质量和生产效率。
本文将结合实例,详细介绍加工中心钻孔编程的步骤和注意事项,以便读者更好地理解和应用。
二、编程前准备1.选择合适的刀具:根据钻孔直径、深度、材料等因素选取合适的刀具。
2.确定坐标系:加工中心有多种坐标系,如绝对坐标系、相对坐标系等。
在编程前需要确定使用哪种坐标系。
3.测量工件:测量工件尺寸和位置,以便正确设置初始点和结束点。
三、编程步骤1.设置初始点:在程序开头设置起始点,一般为工件表面上方一定距离处。
可以使用G90指令将机床坐标系设为绝对坐标系,在G代码开头使用G00指令快速移动到起始点。
2.设定进给速度:使用F指令设定进给速度,一般根据材料硬度等因素进行调整。
例如:F2000表示进给速度为2000mm/min。
3.设定钻孔深度:使用G81指令设定钻孔深度,例如:G81 X50 Y50 Z-20 R2 F2000表示在X50 Y50处开始钻孔,深度为20mm,进给速度为2000mm/min,R2表示快速进刀距离。
4.设定结束点:使用G80指令设定结束点,例如:G80 X50 Y50 Z5表示在X50 Y50处结束钻孔,Z5表示离工件表面5mm处。
5.重复钻孔:使用M98指令进行循环操作,例如:M98 P100 L10表示执行程序号为100的子程序10次。
6.结束程序:使用M30指令结束程序。
四、注意事项1.刀具选择要合适。
2.坐标系要正确设置,并根据需要进行转换。
3.测量工件尺寸和位置要准确。
4.进给速度要根据材料硬度等因素进行调整。
5.钻孔深度要控制好,避免过深或不足。
6.循环次数要根据实际需要进行设置。
7.编程前应先进行模拟验证,确保程序正确无误后再进行加工操作。
加工中心钻深孔的编程方法

加工中心钻深孔的编程方法加工中心是一种多功能的数控机床,能够进行多种加工操作,包括钻孔。
钻深孔是指钻孔深度较大的孔径。
进行钻深孔加工的编程方法需要考虑到以下几个方面。
首先,需要确定孔径和孔深。
在进行编程之前,需要明确要加工的钻孔的孔径和孔深。
这是编程的基础,也是后续计算加工参数和路径的依据。
其次,需要计算切削参数。
切削参数包括主轴转速、进给速度和切削进给量等。
主轴转速的选择需要考虑材料的硬度和刀具的耐用性。
进给速度的选择需要考虑加工的效率和表面质量。
切削进给量的选择需要考虑刀具和工件的强度和刚性等因素。
然后,需要选择合适的刀具。
钻深孔加工需要选择合适的直柄钻头或深孔钻头。
钻头的选择需要考虑到孔径和孔深,以及材料的硬度和加工精度等因素。
较大的孔径和较深的孔深通常需要较长的钻头和更大的冷却液流量。
接着,需要编写加工程序。
钻深孔加工的编程方法通常有两种:点位编程和插补编程。
点位编程是指根据孔径和孔深,计算每个点的坐标并依次钻孔。
插补编程是指根据加工路径和切削参数,通过插补运动产生连续的切削轨迹。
点位编程适用于简单的孔径和孔深,而插补编程适用于复杂的孔形和大批量的钻深孔加工。
最后,需要进行程序验证和优化。
在进行实际加工之前,需要通过模拟和仿真等方法对加工程序进行验证。
在验证过程中,需要检查加工轨迹、切削参数和表面质量等方面是否满足要求。
如果存在问题,需要及时进行调整和优化。
总之,钻深孔的编程方法需要综合考虑孔径和孔深、切削参数、刀具选择、加工程序编写和程序验证等因素。
只有在充分理解和合理运用这些方法的基础上,才能有效地进行钻深孔加工。
加工中心钻孔程序的编制

加工中心的典型程序编制来源:数控产品网添加:2008-08-12 阅读:276次[ 内容简介 ]钻孔程序的编制1.钻孔程序的编制如图1,沿任意一条直线钻等距的孔。
若使用配备FANUC-6M系统的立式加工中心,则加工程序如下:图1 沿直线钻等距孔O1000N10 G92 X400.0 Y300.0 Z320.0 建立加工坐标系N20 M06 T00 换上中心钻N30 G90 G00 X0 Y0 X、Y向定位N40 Z0 Z向定位N50 M03 S500 F30 主轴启动N60 G81 G99 R-4.0 Z-10.0 钻深为5mm的中心孔N70 G91 G00 X20.0 Y10.0 L03 重复3次钻3中心孔N80 M05 主轴旋转停止N90 G28 Z0 经加工原点回机床原点N100 M06 T01 换钻孔刀,返回加工点NIl0 M03 G90 G00 G44 H01 G81 G99 R-5.0 Z-30.0 钻第一个孔,加刀具补偿N120 G91 X-20.0 Y-10.0 L03 重复钻3次孔N130 M05 G28 G49 Z320.0 撤消刀具长度补偿回Z轴N140 M01 参考点N150 M99 P20 返回到N20程序段程序的特点:1)使用G92建立加工坐标系,坐标系的偏置量在程序中进行设置,修改调整更方便。
2)有两次自动换刀,并使用刀具长度补偿,体现加工中心自动加工的功能。
机床起动后主轴上装的是F 10钻头刀具,刀库的零号刀位上应安装有中心钻。
因整个程序只用两把刀,刀库不用转动,原地换刀就可以了。
3)使用中心钻(N60程序段)预钻定位孔,使孔定位准确。
4)使用相对值指令(N70,N120)给出了孔的位置,使固定循环功能重复使用,直到把孔全部钻完。
L03为重复次数。
5)使用了M01(N140)程序暂停。
注意:使用M01时操作面板上的程序暂停开关应放到接通位置,这样在程序执行到M01时面板上的指示灯燃亮,告诉操作者程序处于任选停止,可以装卸零件,待处理工作结束时按循环起动按钮,程序接着执行。
CNC加工中的数控编程方法与技巧
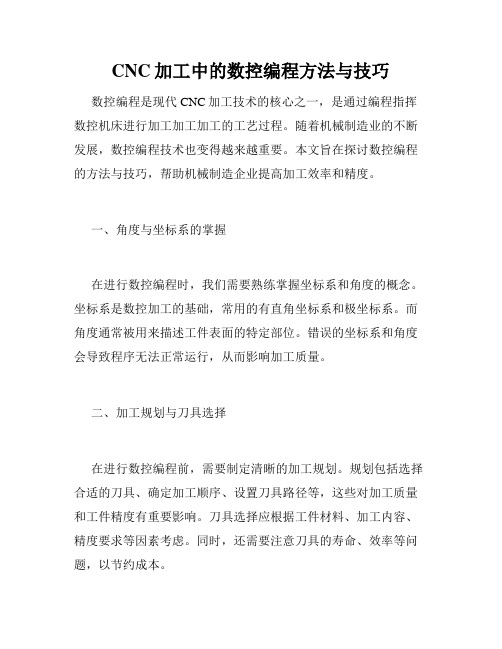
CNC加工中的数控编程方法与技巧数控编程是现代CNC加工技术的核心之一,是通过编程指挥数控机床进行加工加工加工的工艺过程。
随着机械制造业的不断发展,数控编程技术也变得越来越重要。
本文旨在探讨数控编程的方法与技巧,帮助机械制造企业提高加工效率和精度。
一、角度与坐标系的掌握在进行数控编程时,我们需要熟练掌握坐标系和角度的概念。
坐标系是数控加工的基础,常用的有直角坐标系和极坐标系。
而角度通常被用来描述工件表面的特定部位。
错误的坐标系和角度会导致程序无法正常运行,从而影响加工质量。
二、加工规划与刀具选择在进行数控编程前,需要制定清晰的加工规划。
规划包括选择合适的刀具、确定加工顺序、设置刀具路径等,这些对加工质量和工件精度有重要影响。
刀具选择应根据工件材料、加工内容、精度要求等因素考虑。
同时,还需要注意刀具的寿命、效率等问题,以节约成本。
三、编程语言的选择与使用目前常用的数控编程语言有G代码和M代码。
G代码一般用于定义加工轨迹和刀具路径,而M代码则用于指示机床的功能和特定操作。
正确使用编程语言可有效提高程序运行的效率和精度。
四、边缘刀路算法的运用边缘刀路算法是指在数控加工中使用稳健的算法来定义切削轮廓。
这种算法可以使得工件表面的光洁度更高、光滑度更好。
边缘刀路算法适用于不同形状的工件,对于需要进行光洁度检测的工件尤其重要。
五、进给率和转速的控制进给率和转速是影响加工效率和精度的两个重要因素。
进给率过高会导致刀具磨损过快,精度下降,而进给率过低则会使得加工周期长、效率低下。
转速过高则会损耗刀具。
因此,合理控制进给率和转速非常重要。
六、切削力的控制切削力是数控加工过程中必须考虑的关键因素之一。
高强度材料的加工通常需要更高的切削力,为了避免切削过度,需要使用切削力控制系统。
控制切削力可以有效提高加工效率和精度,同时还可以降低能源消耗。
总之,数控编程技术是机械制造工业的发展趋势,正确的数控编程方法和技巧可以提高加工效率、降低成本、提高工件精度。
CNC机床加工中的加工中心的编程与操作技巧

CNC机床加工中的加工中心的编程与操作技巧CNC机床是现代制造业中一种非常重要的设备,它使用计算机数控技术,能够高效、精确地进行加工。
而在CNC机床中,加工中心更是一种非常常见且功能强大的设备,具备多轴控制、多刀具切削能力,能够实现复杂零部件的高速、高精度加工。
在加工中心的编程与操作中,掌握一些技巧是非常重要的。
本文将介绍一些CNC机床加工中心的编程与操作技巧,希望对读者有所帮助。
一、了解加工中心的基本结构与工作原理在编程与操作加工中心之前,首先需要对加工中心的基本结构与工作原理有所了解。
加工中心主要由机床主体、控制系统、夹具系统、刀具系统等组成。
了解加工中心的基本构造,对于编程与操作会有很大的帮助。
二、熟悉加工中心编程语言加工中心的编程语言通常采用G代码,需要熟悉G代码的基本语法与功能。
例如,G01表示直线插补,G02表示圆弧插补,G04表示暂停,等等。
了解G代码的基本指令,能够正确编写程序,提高加工效率。
三、合理设置刀具补偿在编程过程中,需要合理设置刀具补偿。
刀具补偿可以根据具体的切削条件来进行设置,不同的刀具补偿参数会影响加工精度和表面质量。
熟悉刀具补偿的设置,能够使加工效果更好。
四、注意加工过程中的切削参数在进行加工中心的编程与操作时,需要注意切削参数的选择。
切削参数包括切削速度、进给速度、切削深度等。
合理设置切削参数,能够提高加工效率,同时保证加工质量。
五、注意加工中心的安全操作在进行加工中心的编程与操作时,需要注意安全操作。
操作人员应该熟悉机床的安全操作规程,佩戴相关的个人防护装备,并严格按照操作规程进行操作。
保证人员的安全是非常重要的。
六、加工中心编程与操作中的常见问题及解决方法在加工中心的编程与操作中,常会遇到一些问题,例如机床刀具的选择、工件夹紧方式的选择、切削参数的合理设置等。
针对这些常见问题,需要有相应的解决方法。
在实际操作中,运用正确的方法能够解决问题,并提高加工效率。
本文介绍了一些CNC机床加工中心的编程与操作技巧。
加工中心的孔加工编程及技巧
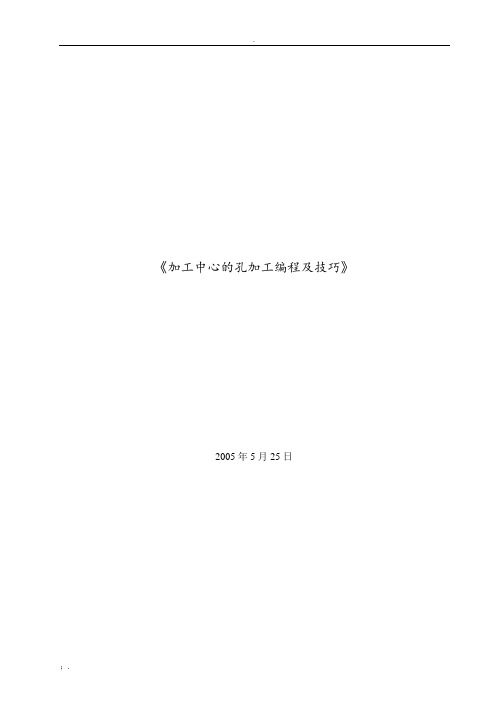
.《加工中心的孔加工编程及技巧》2005年5月25日加工中心的孔加工编程及技巧摘要:孔加工在数控加工中一直占有重要的地位,如何在加工过程中按照合理的工艺编制出正确的加工程序是非常关键的因素。
关键词:孔加工固定循环子程序极坐标一、引言孔加工在数控加工中一直占有重要的地位。
在合理的加工工艺编制好以后如何编制出正确的程序将直接影响到工件是否加工合格。
复杂的孔加工将用到数控系统中的许多功能。
诸如:孔加工固定循环、子程序、极坐标、坐标旋转等。
因此,如何将这些指令灵活应用在加工的程序中将直接关系到程序的合理性。
二、应用实例下面就以一个定位连接板(图1)作为实例,介绍该类程序的编制及技巧。
1、技术要求:1)零件材料:灰铸铁HT2002)加工部位:加粗部分(φ110,2-φ70H7),8-M12深15,18-φ13深20。
3)加工说明:φ70H7预孔为铸造,余量5mm。
基准面A、B、C、D前工序已完成。
夹具形式不用考虑,φ110孔用铣削方式。
4)数控机床:立式加工中心VMC800;数控系统:FANUC 0iM5)按数控工序卡片编制加工中心程序。
6)程序编制方法:固定循环、子程序、坐标系旋转、极坐标指令等图1 定位连接板2、加工工艺夹具3、加工程序主程序O0001;第0001号程序,加工主程序G90G00G55X80.0Y80.0;建立工件坐标系,并运动到φ70H7孔的中心位置N10T02M6;调用02号刀具(粗镗φ69.7)G43H02Z100.0;刀具长度正补偿,并运动到安全高度M03S380;主轴正转M08;打开冷却液G98G86Z-45.0R3.0F95;调用粗加工固定循环加工φ70H7孔至φ69.7X280.0 Y180.0;在X280.0Y180.0位置继续加工G80;取消固定循环N20T03M6;调用03号刀具(φ40立铣刀铣φ110孔)G00X280.0Y180.0;快速定位到φ110孔的中心位置G43H03Z100.0;刀具长度正补偿,并运动到安全高度M3S420;主轴正转G01Z-14.6F2000;下刀至第一次的深度位置(粗加工)M98P0501;调用0501号子程序G01Z-14.8F2000 S560;下刀至第二次的深度位置(半精加工)M98P0501;调用0501号子程序M01;检查尺寸14.8。
- 1、下载文档前请自行甄别文档内容的完整性,平台不提供额外的编辑、内容补充、找答案等附加服务。
- 2、"仅部分预览"的文档,不可在线预览部分如存在完整性等问题,可反馈申请退款(可完整预览的文档不适用该条件!)。
- 3、如文档侵犯您的权益,请联系客服反馈,我们会尽快为您处理(人工客服工作时间:9:00-18:30)。
图1 孔加工固定循环的动作
加工中心编程中,经常用到的孔加工固定循环功能指令主要有G81~G89九个,如表1所示。
可以实现钻孔、镗孔、攻螺纹等加工。
孔加工固定循环指令由以下6个动作组成,如图1所示。
1)X和Y轴定位;
2)快速运行到R点;
3)孔加工;
4)在孔底的动作,包括暂停、主轴反转等;
5)返回到R点;
6)快速退回到初始点。
CNC加工中心孔加工固定循环程序段的一般格式为
G90/G91 G98/G99 G81~G89 X_ Y_ Z_ R_ Q_ P_ F_ L_;
式中 G90/G91——绝对坐标编程和增量坐标编程指令;
G98/G99——返回点平面指令,G98为返回到初始平面,G99为返回到R平面,参见图2;
G80~G89——孔加工指令,详细图解如2所示;
X、Y——孔位置坐标;
Z——孔底坐标,按G90编程时,编入绝对坐标值,按G91编程时,编入增量坐标值;
R——按G90编程时,编入绝对坐标值,按G91<
给大家举例说明,一块厚10MM的45号钢板上钻两个5.5的孔。
—、
%
o0001(程序号)M6 T1(选择1号刀)
Go G90 G54 X7.Y-5.M3 S1200(快速定位到个孔上方,主轴正转)G43H1Z50.M8(建立刀具长度补偿,打开冷却液)
G98 G817-2.R2.F60.(点孔固定循环格式)
X33.(点第二个孔)
G80(取消固定循环)M5(主轴停止)
G91G28 Z0.M9(切削液关,Z轴返回机床参考点)G28 Y0.(Y轴返回机床参考点)
M01(选择性停止)
M6 T2(钻孔)
G0 G90 G54 X7.Y-5.M3 S1000G43 H2 Z50.M8
G98 G83Z-13.R2.Q2.F60.X33.
G80M5
G91 G28 Z0.M9G28 Y0.
M30(程序结束)%
在厚为10MM的圆料上钻孔3-M4贯穿均布,这个可以使用极坐标钻孔指令(G16),选择三把刀@10的点钻,D3.3的钻头,M4的丝锥。
坐标原点是大圆圆心,这个需要说明的是X为这三个M4圆心所在圆的半径值,V为度数,符合坐标系逆时针为正,顺时针为负。
—、%o0001
M6 T1(点孔)
G0 G90 G54G16X34.5 Y180.M3 S1200 (以极坐标方式快速移动到较左边的孔上方,主轴正
转)G43H1 Z50.M8
G98 G81Z-2.R2.F60.
G91 Y120.K2.(相对坐标旋转两次,每次120度点孔)G0 G80 G90G15(取消相对坐标,固定循环,极坐标)M5
G91 G28 Z0.M9G28 Yo.
M01
M6 T2(钻底孔)
G0 G90G54G16 X34.5 Y180.M3 S1200G43 H2 Z50.M8
G98 G83Z-13.R2.Q2.F60.G91 Y120.K2.
G0 G80 G90 G15M5
G91 G28 Z0.M9G28 Y0.
M01
M6T3(攻丝)
G0 G90 G54G16 X34.5 Y180.M3 S100G43 H3 Z50.M8 G98 G84Z-13.R2.F70G91 Y120.K2.
G0 G80 G90 G15M5
G91 G28Z0.M9G28 YO.M30%。