集成电路工艺制程1
集成电路工艺制程介绍1
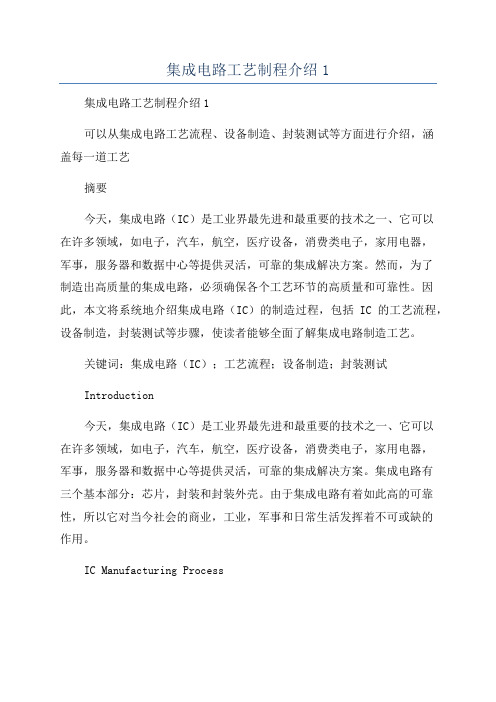
集成电路工艺制程介绍1
集成电路工艺制程介绍1
可以从集成电路工艺流程、设备制造、封装测试等方面进行介绍,涵
盖每一道工艺
摘要
今天,集成电路(IC)是工业界最先进和最重要的技术之一、它可以
在许多领域,如电子,汽车,航空,医疗设备,消费类电子,家用电器,
军事,服务器和数据中心等提供灵活,可靠的集成解决方案。
然而,为了
制造出高质量的集成电路,必须确保各个工艺环节的高质量和可靠性。
因此,本文将系统地介绍集成电路(IC)的制造过程,包括IC的工艺流程,设备制造,封装测试等步骤,使读者能够全面了解集成电路制造工艺。
关键词:集成电路(IC);工艺流程;设备制造;封装测试
Introduction
今天,集成电路(IC)是工业界最先进和最重要的技术之一、它可以
在许多领域,如电子,汽车,航空,医疗设备,消费类电子,家用电器,
军事,服务器和数据中心等提供灵活,可靠的集成解决方案。
集成电路有
三个基本部分:芯片,封装和封装外壳。
由于集成电路有着如此高的可靠性,所以它对当今社会的商业,工业,军事和日常生活发挥着不可或缺的
作用。
IC Manufacturing Process。
集成电路基本制造工艺
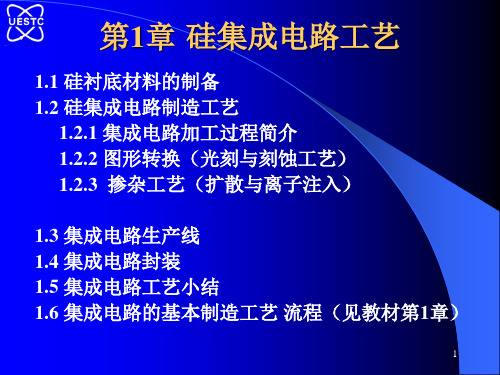
– Na、K、Fe、Cu、Au 等元素 – 扩散系数要比替位式扩散大6~7个数量级 – (绝对不许用手摸硅片—防止Na+沾污。)30
Sc
Sc
xJ
xJ
立体图
柱面
平面 球面
横向扩展宽度=0.8xj
剖面图
杂质横向扩散示意图
31
离子注入
离子注入是另一种掺杂技术,离子 注入掺杂也分为两个步骤:离子注入和 退火再分布。离子注入是通过高能离子 束轰击硅片表面,在掺杂窗口处,杂质 离子被注入硅本体,在其他部位,杂质 离子被硅表面的保护层屏蔽,完成选择 掺杂的过程。进入硅中的杂质离子在一 定的位置形成一定的分布。通常,离子 注入的深度(平均射程)较浅且浓度较大, 必须重新使它们再分布。掺杂深度由注 入杂质离子的能量和质量决定,掺杂浓 度由注入杂质离子的数目(剂量)决定。
27
1.2.3 掺杂工艺(扩散与离子注入)
通过掺杂可以在硅衬底上形成不同类型的半导体区
域,构成各种器件结构。掺杂工艺的基本思想就是通过 某种技术措施,将一定浓度的Ⅲ价元素,如硼,或Ⅴ价 元素,如磷、砷等掺入半导体衬底。
D
G
S
G
D
S
Al
SiO2
N
N
P-si
28
掺杂:将需要的杂质掺入特定的 半导体区域中,以达到改变半导 体电学性质,形成PN结、电阻、 欧姆接触
湿法刻蚀:利用液态化学试剂或溶液通过化 学反应进行刻蚀的方法。
干法刻蚀:主要指利用低压放电产生的等离子 体中的离子或游离基(处于激发态的分子、原子 及各种原子基团等)与材料发生化学反应或通过 轰击等物理作用而达到刻蚀的目的。
26
集成电路工艺流程
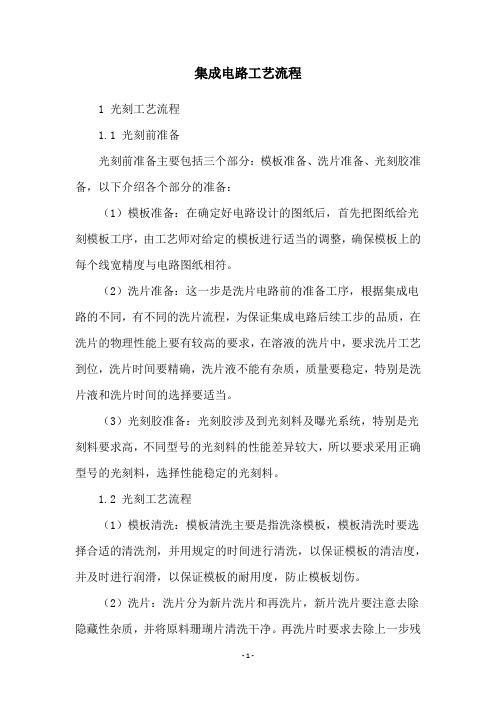
集成电路工艺流程1 光刻工艺流程1.1 光刻前准备光刻前准备主要包括三个部分:模板准备、洗片准备、光刻胶准备,以下介绍各个部分的准备:(1)模板准备:在确定好电路设计的图纸后,首先把图纸给光刻模板工序,由工艺师对给定的模板进行适当的调整,确保模板上的每个线宽精度与电路图纸相符。
(2)洗片准备:这一步是洗片电路前的准备工序,根据集成电路的不同,有不同的洗片流程,为保证集成电路后续工步的品质,在洗片的物理性能上要有较高的要求,在溶液的洗片中,要求洗片工艺到位,洗片时间要精确,洗片液不能有杂质,质量要稳定,特别是洗片液和洗片时间的选择要适当。
(3)光刻胶准备:光刻胶涉及到光刻料及曝光系统,特别是光刻料要求高,不同型号的光刻料的性能差异较大,所以要求采用正确型号的光刻料,选择性能稳定的光刻料。
1.2 光刻工艺流程(1)模板清洗:模板清洗主要是指洗涤模板,模板清洗时要选择合适的清洗剂,并用规定的时间进行清洗,以保证模板的清洁度,并及时进行润滑,以保证模板的耐用度,防止模板划伤。
(2)洗片:洗片分为新片洗片和再洗片,新片洗片要注意去除隐藏性杂质,并将原料珊瑚片清洗干净。
再洗片时要求去除上一步残留的杂质和外界污染物,保证集成电路元件的耐用性,再洗片也可以用来清洗模板。
(3)蒸汽消毒:蒸汽消毒要求使用洁净蒸汽,以防止杂质和微生物污染,确保集成电路的质量。
(4)光刻制程:光刻制程要求在图案和图形绘制操作之前,要经过模板检测,以保证模板的质量,其次要核对图纸和模板,并进行曝光时间设定,最后要进行曝光机操作,以及检查曝光图案的质量,确保曝光结果的完美。
(5)洗涤:洗涤是指精确洗涤光刻后的集成电路图案,可以去除曝光过程中残留的光刻胶,确保电路图案的光洁度和精细度。
此外,还可以使用高级的洗涤工艺,如超声波洗涤、活性弱酸洗涤、高纯水洗涤等,以满足特殊的应用要求。
集成电路制造工艺流程
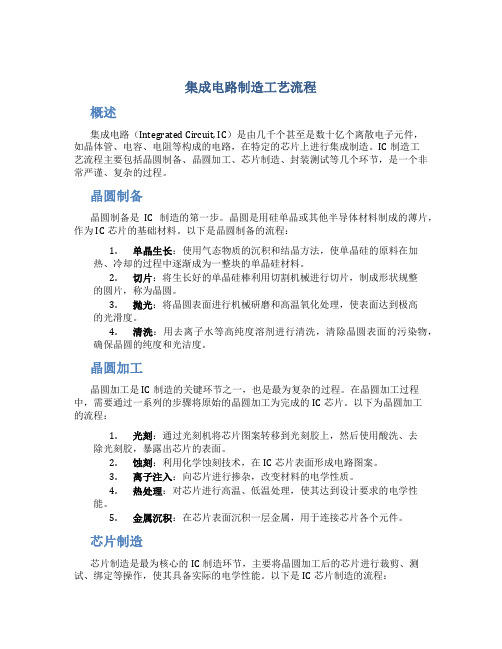
集成电路制造工艺流程概述集成电路(Integrated Circuit, IC)是由几千个甚至是数十亿个离散电子元件,如晶体管、电容、电阻等构成的电路,在特定的芯片上进行集成制造。
IC制造工艺流程主要包括晶圆制备、晶圆加工、芯片制造、封装测试等几个环节,是一个非常严谨、复杂的过程。
晶圆制备晶圆制备是IC制造的第一步。
晶圆是用硅单晶或其他半导体材料制成的薄片,作为IC芯片的基础材料。
以下是晶圆制备的流程:1.单晶生长:使用气态物质的沉积和结晶方法,使单晶硅的原料在加热、冷却的过程中逐渐成为一整块的单晶硅材料。
2.切片:将生长好的单晶硅棒利用切割机械进行切片,制成形状规整的圆片,称为晶圆。
3.抛光:将晶圆表面进行机械研磨和高温氧化处理,使表面达到极高的光滑度。
4.清洗:用去离子水等高纯度溶剂进行清洗,清除晶圆表面的污染物,确保晶圆的纯度和光洁度。
晶圆加工晶圆加工是IC制造的关键环节之一,也是最为复杂的过程。
在晶圆加工过程中,需要通过一系列的步骤将原始的晶圆加工为完成的IC芯片。
以下为晶圆加工的流程:1.光刻:通过光刻机将芯片图案转移到光刻胶上,然后使用酸洗、去除光刻胶,暴露出芯片的表面。
2.蚀刻:利用化学蚀刻技术,在IC芯片表面形成电路图案。
3.离子注入:向芯片进行掺杂,改变材料的电学性质。
4.热处理:对芯片进行高温、低温处理,使其达到设计要求的电学性能。
5.金属沉积:在芯片表面沉积一层金属,用于连接芯片各个元件。
芯片制造芯片制造是最为核心的IC制造环节,主要将晶圆加工后的芯片进行裁剪、测试、绑定等操作,使其具备实际的电学性能。
以下是IC芯片制造的流程:1.芯片测试:对芯片的性能进行测试,找出不合格的芯片并予以淘汰。
2.芯片切割:将晶圆上的芯片根据需求进行切割。
3.接线:在芯片表面安装金线,用于连接各个器件。
4.包装:将芯片放入封装盒中,并与引线焊接,形成成品IC芯片。
封装测试封装测试是IC制造的最后一步。
集成电路生产工艺流程(一)

集成电路生产工艺流程(一)集成电路生产工艺概述集成电路生产工艺是指将所有电子元件集成在单一芯片上的生产过程。
它被广泛应用于电子设备制造业,如计算机、手机、电视等。
制造流程1.设计–集成电路设计师设计电路–使用EDA软件进行仿真与验证2.掩膜制造–制造掩膜–通过光刻技术将图案转移到硅片上3.投影光刻–使用掩膜将图案投影在硅片上–制造电路的输送4.融合–在高温下将掩膜和硅片融合–形成晶体管5.化学处理–使用化学液体进行蚀刻–将不需要的硅层去除6.金属化–在硅片表面蒸镀金属–形成线路和电极7.包装测试–切割硅片–用陶瓷或塑料封装芯片–测试芯片性能制造技术1.CMOS–基础工艺–低功耗和低噪音2.BJT–晶体管工艺–高频率和高速率3.BCD–模拟与数字工艺结合–适用于汽车、医疗和航空等领域4.MEMS–微电子机械系统–功能丰富的微型机械装置制造挑战1.芯片尺寸缩小–越来越小的芯片尺寸–需要更精密的光刻技术和更高的抗干扰能力2.成本控制–竞争日益激烈–芯片制造成本需要持续降低3.故障排除–单个芯片上有上亿个晶体管–如何排查其中的问题是一个挑战结论集成电路生产工艺是一个非常复杂的过程,需要各个流程相互合作,使用最新的技术和设备。
随着时间的推移,它将继续进化和改进,以满足越来越高的市场需求和更严格的质量控制。
制造趋势1.三维IC制造技术–将多个芯片堆叠在一起,以提高芯片效率和成本效益2.全球晶圆制造技术–分布式制造技术可帮助降低成本–全球晶圆制造可促进产业链的全球化3.自动化技术–机器学习和人工智能将推动制造工艺的自动化–减少人为干扰和错误应用领域1.通信–集成电路的高速率和低功耗等特点十分适合通信应用2.计算机–处理器、内存、存储等都需要集成电路–集成电路的不断进步也推动了计算机性能的提升3.汽车–外部环境复杂,需要集成电路来实现各种功能–集成电路技术适合于汽车电子系统的小型化和高度集成化4.医疗–集成电路技术在医疗成像、生物传感器和仿生器件等方面有广泛应用–提升了医疗设备的精度和可靠性结语随着各种工业领域的发展和需要,集成电路生产工艺将继续前进和改进。
集成电路工艺制程1PPT课件

集成电路生产的3个阶段
✓图显示集成电路从晶 圆的 (a)拉晶; (b)制造; (c)切割; (d)封装; 完成的简易流程; ✓图(e)为单一晶粒的 集成电路放大图标
集成电路生产的3个阶段
硅晶片(wafer)的制造
集成电路的制作
集成电路的封装(Package)
习惯以线路制造的最小线宽、晶片直径及DRAM(动态随机存储 器)所储存的容量来评断集成电路的发展状况。
物理气相沉积
电致迁移(Electro migration)
解决:加入适量Cu, 0.5%~4% 为了预防“尖峰”、“电移”,使用含Si与Cu的AL合金做 导线。
阻障C层u缺(点Ba:rr不ie易r L形ay成er挥)发—物Ti,N 不及易Ti蚀W刻。 如图所示,可避免铝—硅界面的尖峰
现象,提升附著能力。
1)增大距离; 2)包好衬底; 或采用Epi substrate, SOL等。
总结:随着IC集成度提高,出现“短沟效应”,引发了“热电子 效应”。采用LDD结构无法解决集成度提高衍生出的能量耗损及 散热问题,因此出现低能耗高集成度的CMOS,而且现已成为 VLSI主要结构,但成本提高,出现双载流子现象所衍生出的latchup问题。
半导体元件的制程
沉积理论
薄膜的沉积,是一连串涉及吸附原子的吸附、吸附原子 在表面的扩散及在适当的位置下聚结,以渐渐形成薄膜 并成长的过程。
半导体元件的制程
分类及详述
物理气相沉积(Physical Vapor Deposition)——PVD
○ 蒸 镀(Evaporation) 利用被蒸镀物在高温(近熔点)时,具备饱和蒸汽压,来沉积薄膜 的过程。 ○ 溅 镀(Sputtering) 利用离子对溅镀物体电极(Electrode)的轰击(Bombardment)使 气相中具有被镀物的粒子(如原子),再来沉积薄膜。
集成电路制造工艺流程

集成电路制造工艺流程引言:集成电路(IC)作为现代电子技术的核心,被广泛应用于计算机、通信、消费电子等领域。
集成电路制造工艺是将原始材料经过一系列加工步骤,将电路图案和其他组件集成到单片硅芯片上的过程。
本文将详细介绍集成电路制造的工艺流程。
一、晶圆制备1.材料准备:通常采用硅作为晶圆基底材料。
硅材料需经过多次高温处理来去除杂质。
2.切割:将硅原料切割成圆片形状,厚度约为0.4毫米。
3.晶圆清洗:通过化学和物理方法清洗硅片表面。
二、晶圆表面处理1.清洗:使用化学物质去除晶圆表面的有机和无机污染物。
2.二氧化硅沉积:在晶圆表面形成一层绝缘层,以保护电路。
3.光刻:通过对光敏材料进行曝光、显影和刻蚀等步骤,将电路图案转移到晶圆表面。
三、激活剂注入1.清洗:清洗晶圆表面以去除光刻过程产生的残留物。
2.掺杂:使用离子注入设备将所需的杂质注入晶圆表面,以改变材料的导电性。
四、金属化1.金属沉积:在晶圆上沉积一层金属,通常是铝或铜,以用作导电线。
2.蚀刻:使用化学溶液去除多余的金属,只保留所需的电路。
3.封装:将晶圆裁剪成多个小片,然后分别进行封装,以提供保护和连接接口。
五、测试1.功能测试:确保电路功能正常。
2.可靠性测试:对电路进行长时间运行测试,以验证其性能和可靠性。
3.封装测试:测试封装后的芯片性能是否正常。
六、成品测试和封装1.最终测试:对芯片进行全面测试,以确保其达到预期的性能指标。
2.封装:在芯片表面添加保护层,并提供引脚用于连接到其他电子设备。
结论:本文详细介绍了集成电路制造的工艺流程,包括晶圆制备、晶圆表面处理、激活剂注入、金属化、测试和封装等环节。
每一步都是为了保证集成电路的性能和可靠性。
随着科技的不断发展,集成电路制造工艺也在不断创新,以提高集成电路的性能和功能。
集成电路制造工艺流程

*
磷穿透扩散:减小串联电阻 离子注入:精确控制参杂浓度和结深
B
P-Sub
N+埋层
SiO2
光刻胶
P+
P+
P+
P
P
N+
P-Sub
1.2.2 N阱硅栅CMOS工艺主要流程 2. 氧化、光刻N-阱(nwell)
*
1.2.2 N阱硅栅CMOS工艺主要流程 3. N-阱注入,N-阱推进,退火,清洁表面
P-Sub
N阱
*
1.2.2 N阱硅栅CMOS工艺主要流程 4.长薄氧、长氮化硅、光刻场区(active反版)
N阱
P-Sub
*
集成电路(Integrated Circuit) 制造工艺是集成电路实现的手段,也是集成电路设计的基础。
单击添加副标题
第一章 集成电路制造工艺流程
*
无生产线集成电路设计技术
引言
随着集成电路发展的过程,其发展的总趋势是革新工艺、提高集成度和速度。 设计工作由有生产线集成电路设计到无生产线集成电路设计的发展过程。 无生产线(Fabless)集成电路设计公司。如美国有200多家、台湾有100多家这样的设计公司。
*
P-Sub
1.2.2 N阱硅栅CMOS工艺主要流程 13. 钝化层淀积,平整化,光刻钝化窗孔(pad)
*
N阱
有源区
多晶
Pplus
Nplus
接触孔
金属1
通孔
金属2
PAD
1.2.3 N阱硅栅CMOS工艺 光刻掩膜版汇总简图
*
2. 减缓表面台阶
3. 减小表面漏电流
P-Sub
N-阱
- 1、下载文档前请自行甄别文档内容的完整性,平台不提供额外的编辑、内容补充、找答案等附加服务。
- 2、"仅部分预览"的文档,不可在线预览部分如存在完整性等问题,可反馈申请退款(可完整预览的文档不适用该条件!)。
- 3、如文档侵犯您的权益,请联系客服反馈,我们会尽快为您处理(人工客服工作时间:9:00-18:30)。
微影(Photolithography)
微影需备的器材有:光源---光罩---光阻---显影液(Developer), NaOH、KOH中和。 微影制程:①光阻覆盖(Coating);②曝光;③显影。 ○ 光阻:主要由树脂(Resin),感光剂(Sensitizer)及溶剂 (Solvent)混合而成 负光阻——光阻遇光后产生链结(Cross linking),使结构加强而 不溶于显影液; 正光阻——光阻遇光后产生解离,形成一种溶于显影液的结构。 好的光阻应具备: 附著性(Adhesion) 抗蚀刻性(Etch Resistance) 解析度(Resolution)
刻蚀(Etch)
○ Polycide的蚀刻 ○ 铝合金蚀刻 铝-硅-铜合金。铜蚀刻困难,限制了它的使用。 ○ 钨回蚀:钨插塞—VIA 如图所示:TiN或TiW提高附著能力。
图:多重金属 化制程中常见 的“钨插塞” 的制作流程
N井CMOS
CMOS
----Complementary Metal Oxide Semiconductor
三种主要的CMOS设计结构
:
双井CMOS
CMOS的缺点 :Latch-up
寄生双载子晶体管在CMOS内的 发生情形
衍生的正回馈 回路
金属Al与Si接触的表面 发生“尖峰”现象
物理气相沉积 电致迁移(Electro migration)
溅镀沉积的铝,经适当的退 火( Anneal )之后,通常以 多晶形式存在,当铝传导电 流时,由于电场的影响,铝 原 子 将 沿 着 晶 粒 界 面 (Grain Boundary)而移动, 这一现象称为电致迁移. Al线因电致迁移而产生断路
LDD(Lightly Doped Drain)—轻掺杂漏极
半导体元件的制程
集成电路生产的3个阶段
图显示集成电路从晶 圆的 (a)拉晶; (b)制造;
(c)切割;
(d)封装; 完成的简易流程; 图(e)为单一晶粒的 集成电路放大图标
集成电路生产的3个阶段
硅晶片(wafer)的制造
集成电路的制作
集成电路的封装(Package)
习惯以线路制造的最小线宽、晶片直径及DRAM(动态随机存储 器)所储存的容量来评断集成电路的发展状况。
机械性质—薄膜间的机械应力
退火(Annealing)
•原理:
利用热能(Thermal Energy),将物体内 产生内应力的一些缺陷加以消除。所施加的能 量将增加晶格原子及缺陷在物体内的振动及扩 散,使得原子的排列得以重整。
集成电路工艺制程介绍
Table of Content
集成电路生产的3个阶段
机械性质
退火(Annealing) 双极型晶体管(Bipolar Junction Transistor-BJT) 短沟道效应—集成的结果 热电子效应(Hot Electron Effect )
典型采用LDD设计的晶体管的截面外观
FOX—Field Oxide,场氧化层,隔离器件
CMOS
Incoming Data Format ----Complementary Metal Oxide Semiconductor
三种主要的CMOS设计结构 :
P井CMOS
刻蚀(Etch)
分类:
○ 湿蚀刻:等向性蚀刻 ○ 干蚀刻: ①非等向性(垂直方向>>横向蚀刻速率) ②选择性(Selectivity)——蚀刻速率比 ③蚀刻速率---产量 ④均匀性--- 品质完善,Yield增高
刻蚀(Etch)
溅击蚀刻 + 极佳的非等向性,但选择性较差 ; 等离子蚀刻(Plasma Etching) + 选择性较佳,但非等向性差; 反应性离子蚀刻(Reactive Ion Etch)RIE + 选择性、非等向性俱佳(选择性:2:1~40:1;非等向 性:80º 以上); + 通过选用不同的气体或含量等离子体来获得对不 同薄膜的刻蚀速率; + 基本上氟原子及氯原子都可以和各种过渡金属形 成具挥发性的化合物。
微影(Photolithography)
○ 光罩:6英寸 晶片,每片约 需40~60次左 右曝光(依赖 chip大小)
微影
○ 曝光技术:×5倍的 mask。 显示两种微影的曝光技术: (a)接触式 (b)投影式 (c)为以10倍的光罩进 行重复且步进的投影式 曝光的概念图。
经掺杂的多晶硅及硅化钨所组成的多晶硅化金属(Polycide)是 VLSI中最主要gate导电层。 ○ W——钨插塞(Tungsten Plug),极佳的阶梯覆盖能力。
图:钨插塞在多重 金属化制程上的应 用及其结构
半导体元件的制程
微影(Photolithography)
通常以一个制程所需要经过光罩(mask)数量来 表示这个制程的难易。
半导体元件的制程
沉积理论
薄膜的沉积,是一连串涉及吸附原子的吸附、吸附原子 在表面的扩散及在适当的位置下聚结,以渐渐形成薄膜 并成长的过程。
半导体元件的制程
分类及详述
物理气相沉积(Physical Vapor Deposition)——PVD
○ 蒸 镀(Evaporation) 利用被蒸镀物在高温(近熔点)时,具备饱和蒸汽压,来沉积薄膜 的过程。 ○ 溅 镀(Sputtering) 利用离子对溅镀物体电极(Electrode)的轰击(Bombardment)使 气相中具有被镀物的粒子(如原子),再来沉积薄膜。
半导体元件的制程
蚀刻(Etch)
微影只是将光罩图案转移到光阻上,接下来利用这层光 阻为罩幕(mask),以便对光阻下的薄膜或Si片进行选 择性蚀刻或离子注入。蚀刻即是利用化学反应或物理作 用,把光阻上的图案转移到薄膜上。 元件制作:薄膜沉积---微影---蚀刻
薄膜经:
(a)等向性蚀刻及 (b)非等向性蚀刻 后的簿膜横截面轮 廓
化学气相沉积
主要介电材料:SiO2、Si3N4、PSG及BPSG---热流。
图:沉积薄膜在沉积后(a)及(b)经过热流(Flow)后, 其外观上的差异 2. 导体:WSix、TiSi2、Ti、W、Poly(多晶硅) 3. 半导体:Si、epi片
化学气相沉积
○ Si3N4 最主要的应用,是做为SiO2层的蚀刻幕罩(mask),且不易被氧 和H2O所渗透的优点,这层幕罩还可以作为场氧化层(FOX)制作 时防止有源区(Active Area)受氧化,这就是有名的LOCOS制程。 ○ Poly、WSix
短沟道效应—集成的结果
如图所示:
因源极和漏极的 缺乏层区域所导 致的沟道长度变 化的情形。
热电子效应—Hot Electron Effect
LDD(Lightly Doped Drain)
LDD缺点:
* 使得NMOS制作变得复杂;
* 源漏串联电阻增加,速度 降低; * 耗电增加。 采用LDD设计的NMOS晶体管的外观
CMOS的缺点 :Latch-up
* 引发电流 (Triggering Current) IH,当I> IH时,产生Latch-up, CMOS电路的功能将暂时或永久性丧失。
* 防止Latch-up方法:
1)增大距离; 2)包好衬底; 或采用Epi substrate, SOL等。 总结:随着IC集成度提高,出现“短沟效应”,引发了“热电子 效应”。采用LDD结构无法解决集成度提高衍生出的能量耗损及 散热问题,因此出现低能耗高集成度的CMOS,而且现已成为 VLSI主要结构,但成本提高,出现双载流子现象所衍生出的latchup问题。
物理气相沉积
Salicide制程
金属钛(或白金)极易与Si交互扩散而形成一种电阻很低的化合
物TiSi2,因此,钛与Si的界面可以形成一个很好的欧姆接触。
自行对准金属硅化物(Self-Aligned Silicide)制程
如图: “自行对 准金属硅 化物”制 程的主要 流程
化学气相沉积(Chemical Vapor Deposition)——CVD
反应气体发生化学反应,并且生成物沉积在晶片表面—— 薄膜沉积 技术。
物理气相沉积
铝合金溅镀
铝合金铝、硅、ቤተ መጻሕፍቲ ባይዱ合金。 硅对AL有一定的固态溶 解度(Solid Solubility), 在400℃时,硅扩散进入铝, 且铝也会回填硅因扩散所留 下的空隙,形成如图所示的 尖峰(Spike),解决之道 为主动掺杂Si,使含量在1%。
微影
光源——解析度、聚焦深度与光源的波长有关
* 紫外线:4360Aº * 深紫外线:2480 Aº ,寻找 波长更短的光源 * X光(不易聚焦且专用光 罩不易制作) * 电子束曝光时间长,影响 量产。解析度 R≤0.35、 0.25、0.18μ,聚焦深度 DOF≥ 光阻厚度 因为光阻的厚度,曝光机所提供的解析度应该至少能含盖图里的a、 b两点。我们常以DOF、来表示曝光机所能提供的这个深度。
双极型晶体管
----(Bipolar Junction Transistor--BJT)
美国贝尔实验室(Bell Lab)发明,近代最重要半导体元 件之一,获Nobel物理学奖; 如图:一个在芯片上的NPN双载子
晶体管的截面结构;
MOS晶体管:是VLSI里最重要的一种基本的晶体管, 已取代了BJT。