卧式钻镗组合机床的液压系统设计
卧式钻镗组合机床的液压系统设计

卧式钻镗组合机床的液压系统设计
首先,需要确定机床所需的液压系统工作压力。
卧式钻、镗组合机床的工作压力通常为10-25MPa。
根据工作压力确定油泵的流量和型号,流量需满足机床加工的需要。
其次,需选择合适的液压元件。
根据机床的加工需求,选择相应的液压元件。
液压缸用于实现主轴、工作台、主轴箱等运动部件的运动,而液压马达则用于切削液的输送。
接下来,需考虑液压系统的控制方式。
对于卧式钻、镗组合机床,可使用手动控制、脚踏开关控制或电脑数控控制。
手动控制简单可靠,适用于简单的加工任务;脚踏开关控制可以实现机床的步进、停止和反转等功能;而电脑数控控制则提供了更高的自动化水平和加工精度。
最后,需考虑液压系统的安全性和可靠性。
在液压系统设计时,需要考虑系统的安全保护装置,如过载保护、泄漏检测、温度保护等,以及系统的故障诊断和报警功能。
在设计完液压系统后,还需进行系统的试运行和调试。
首先,检查液压油的质量和流量是否正常;其次,逐一检查液压元件的工作情况,确保系统各部件正常运行;最后,进行系统的负载试运行和调试,确保系统能够满足加工需求。
总之,卧式钻、镗组合机床的液压系统设计需要考虑工作压力、液压元件的选择、控制方式、系统的安全性和可靠性等因素。
通过合理的设计和调试,能够提高机床的加工效率和精度,提高机床的使用寿命。
液压课程设计卧式钻镗组合机床液压系统

设计一台卧式钻、镗组合机床液压系统1、液压系统用途(包括工作环境与工作条件)及主要参数:1)工作循环:“快进—工进—死挡铁停留—快退—原位停止”。
组合机床动力滑台工作循环2)工作参数轴向切削力12000N,移动部件总重10000N,工作循环为:“快进——工进——死挡铁停留——决退——原位停止”。
行程长度为0、4m,工进行程为0、1,快进与快退速度为0、1m/s,工过速度范围为0、0003~0、005,采用平导轨,启动时间为0、2s。
要求动力部件可以手动调整,快进转工进平稳、可靠。
2、执行元件类型:液压油缸设计内容1、拟订液压系统原理图;2、选择系统所选用的液压元件及辅件;3、验算液压系统性能;4、编写计算说明书。
目录序言: (5)1 设计的技术要求与设计参数 (6)2 工况分析 (6)2、1确定执行元件 (6)2、2分析系统工况 (6)2、3负载循环图与速度循环图的绘制 (8)2、4确定系统主要参数2、4、1初选液压缸工作压力 (9)2、4、2确定液压缸主要尺寸 (9)2、4、3计算最大流量需求 (11)2、5拟定液压系统原理图2、5、1速度控制回路的选择 (12)2、5、2换向与速度换接回路的选择 (12)2、5、3油源的选择与能耗控制 (13)2、5、4压力控制回路的选择 (14)2、6液压元件的选择2、6、1确定液压泵与电机规格 (16)2、6、2阀类元件与辅助元件的选择 (17)2、6、3油管的选择 (19)2、6、4油箱的设计 (20)2、7液压系统性能的验算2、7、1回路压力损失验算 (22)2、7、2油液温升验算 (22)序言作为一种高效率的专用机床,组合机床在大批、大量机械加工生产中应用广泛。
本次课程设计将以组合机床动力滑台液压系统设计为例,介绍该组合机床液压系统的设计方法与设计步骤,其中包括组合机床动力滑台液压系统的工况分析、主要参数确定、液压系统原理图的拟定、液压元件的选择以及系统性能验算等。
卧式钻镗组合机床液压系统设计

课程设计说明书题目:液压与气动技术——卧式钻镗组合机床液压系统设计姓名:郑义强学号: 1 5 0 6 2 4 0 1 3 0系别:机电工程与自动化学院专业:机械设计与制造班级:15机械1指导教师:陈佳彬黎明职业大学2017年6月27日目录1.设计任务 (1)1.1设计要求 (1)1.2设计参数 (1)1.3主要内容 (1)2.工况分析 (2)2.1负载图及速度图 (2)2.1.1负载分析 (2)2.1.2负载图、速度图 (3)2.2工况分析图 (4)3.方案确定 (5)3.1选择液压回路。
(5)3.1.1调速回路及油源形式 (5)3.1.2快速回路及速度换接回路 (5)3.1.3换向回路 (6)3.1.4行程终点的控制方式 (6)4.计算和选择液压元件 (6)4.1确定液压泵的规格和电机功率 (6)4.1.1压泵工作压力的计算 (6)4.2液压阀的选择 (7)4.3确定管道尺 (8)4.3.1压油管道 (8)4.3.3回油管道 (9)4.4确定邮箱容量 (9)5.组成液压系统图 (9)6.液压系统主要性能的估算 (10)6.1液压缸的速度 (10)6.2系统的效率 (11)6.2.1回路中的压力损失 (12)6.2.2液压泵的工作压力 (13)6.2.3顺序阀的调整压力 (13)6.3液压回路和液压系统的效率 (14)1.设计任务设计一台卧式钻、镗组合机床液压系统。
该机床用于加工铸铁箱形零件的孔系,运动部件总重G=10000N,液压缸机械效率为0.9,加工时最大切削力为12000N,工作循环为:“快进——工进——死挡铁停留——快退——原位停止”。
快进行程长度为0.4m,工进行程为0.1 m。
快进和快退速度为0.1m/s,工进速度范围为3×104-~5×10m/s3-,采用平导轨,启动时间为0.2s。
要求动力部件可以手动调整,快进转工进平稳、可靠。
1.1 设计要求设计一台卧式钻、镗组合机床液压系统。
液压课程设计卧式钻镗组合机床液压系统

设计一台卧式钻、镗组合机床液压系统1、液压系统用途(包括工作环境与工作条件)及主要参数:1)工作循环:“快进—工进—死挡铁停留—快退—原位停止”、组合机床动力滑台工作循环2)工作参数轴向切削力12000N,移动部件总重10000N,工作循环为:“快进——工进-—死挡铁停留-—决退——原位停止”、行程长度为0.4m,工进行程为0.1,快进与快退速度为0。
1m/s,工过速度范围为0。
0003~0.005,采用平导轨,启动时间为0、2s。
要求动力部件可以手动调整,快进转工进平稳、可靠。
2.执行元件类型:液压油缸设计内容1。
拟订液压系统原理图;2.选择系统所选用得液压元件及辅件;3。
验算液压系统性能;4。
编写计算说明书。
目录序言: (5)1 设计得技术要求与设计参数ﻩ 62 工况分析 (6)2、1确定执行元件ﻩ 62.2分析系统工况 (6)2。
3负载循环图与速度循环图得绘制ﻩ82、4确定系统主要参数2。
4、1初选液压缸工作压力ﻩ92、4。
2确定液压缸主要尺寸ﻩ92。
4.3计算最大流量需求 (11)2、5拟定液压系统原理图2.5。
1速度控制回路得选择 (12)2.5。
2换向与速度换接回路得选择 (12)2.5.3油源得选择与能耗控制ﻩ132.5、4压力控制回路得选择................................... 142。
6液压元件得选择2。
6。
1确定液压泵与电机规格................................. 162.6、2阀类元件与辅助元件得选择 (17)2、6。
3油管得选择ﻩ192。
6。
4油箱得设计ﻩ202。
7液压系统性能得验算2.7。
1回路压力损失验算 (22)2.7。
2油液温升验算ﻩ2 2序言ﻩ作为一种高效率得专用机床,组合机床在大批、大量机械加工生产中应用广泛、本次课程设计将以组合机床动力滑台液压系统设计为例,介绍该组合机床液压系统得设计方法与设计步骤,其中包括组合机床动力滑台液压系统得工况分析、主要参数确定、液压系统原理图得拟定、液压元件得选择以及系统性能验算等。
卧式钻镗组合机床液压系统设计
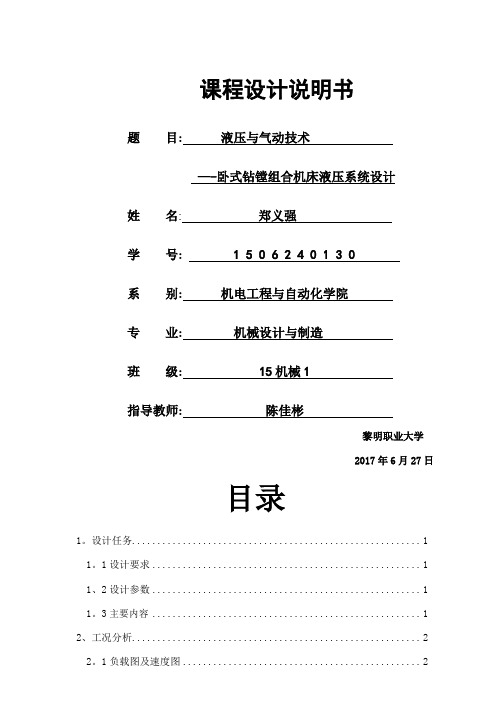
课程设计说明书题目:液压与气动技术—-卧式钻镗组合机床液压系统设计姓名:郑义强学号: 1 5 0 6 2 4 0 1 3 0系别:机电工程与自动化学院专业:机械设计与制造班级: 15机械1指导教师:陈佳彬黎明职业大学2017年6月27日目录1。
设计任务 (1)1。
1设计要求 (1)1、2设计参数 (1)1。
3主要内容 (1)2、工况分析 (2)2。
1负载图及速度图 (2)2、1。
1负载分析 (2)2、1、2负载图、速度图 (3)2。
2工况分析图 (4)3、方案确定 (5)3、1选择液压回路。
(5)3、1、1调速回路及油源形式 (5)3。
1、2快速回路及速度换接回路 (5)3。
1、3换向回路 (6)3、1、4行程终点得控制方式 (6)4。
计算与选择液压元件 (6)4。
1确定液压泵得规格与电机功率 (6)4。
1。
1压泵工作压力得计算 (6)4。
2液压阀得选择 (7)4、3确定管道尺 (8)4、3、1压油管道 (8)4。
3、3回油管道 (9)4、4确定邮箱容量 (9)5。
组成液压系统图 (9)6、液压系统主要性能得估算 (10)6、1液压缸得速度 (10)6、2系统得效率 (11)6。
2、1回路中得压力损失 (12)6。
2、2液压泵得工作压力 (13)6。
2、3顺序阀得调整压力 (13)6。
3液压回路与液压系统得效率 (14)1、设计任务设计一台卧式钻、镗组合机床液压系统。
该机床用于加工铸铁箱形零件得孔系,运动部件总重G=10000N,液压缸机械效率为0。
9,加工时最大切削力为12000N,工作循环为:“快进——工进-—死挡铁停留——快退—-原位停止”。
快进行程长度为0、4m,工进行程为0。
1 m。
快进与快退速度为0。
1m/s,工进速度范围为3×10~5×10m/s,采用平导轨,启动时间为0、2s。
要求动力部件可以手动调整,快进转工进平稳、可靠。
1。
1 设计要求设计一台卧式钻、镗组合机床液压系统。
卧式钻镗组合机床的液压动力液压系统课程设计解读

卧式钻镗组合机床的液压动力液压系统课程设计
设计的目的和要求:
1工作循环:“快进—工进—死挡铁停留—快退—原位停止” 。
2工作参数轴向切削力 12000N ,移动部件总重 10000N ,快进行程 200mm,快进与快退速度 4.2m/min ,工进行程 30mm,工进速度 0.05m /min ,加、减速时间为 0.2s ,静摩擦系数 0.2,动摩擦系数 0.1,动力滑台可在中途停止。
要求动力部件可以手动调整,快进转工进平稳、可靠。
一、工况分析,确定液压缸推力
1.1 负载分析:
切削推力: tF=12000N
静摩擦力 : aF=afG=0.2×10000=2000N 动摩擦力 : dF=dfG=0.1×10000=1000N 启动惯性力: mF=t
vm
=
t
vgG =357.14N
1.2 液压缸的推力 (液压缸效率 9.0 启动推力:启F= aF/η= 222
2.22N 加速推力:加F=(dF+mF /η=1507.93N 快进推力:快F= dF/η=1111.11N 工进推力:工 F=(tF+ dF /η=14444.44N
反向启动过程作用力与 F 启、 F 加、 F 快大小相同,方向相反。
卧式钻镗两用组合机床的液压系统设计文档

卧式钻镗两用组合机床的液压系统设计文档一、引言液压系统是卧式钻镗两用组合机床中的重要部分,主要用于实现机床在加工过程中的各种动作控制。
本文档旨在设计一套稳定可靠的液压系统,以满足卧式钻镗两用组合机床的加工需求。
二、系统结构1.液压泵站:液压泵站是液压系统的动力源,主要由液压泵、电机和控制阀组成。
液压泵负责将液压油从油箱中抽取并压力传输至液压马达或液压缸,电机用于驱动液压泵的运转,控制阀用于调节油压和流量。
2.液压油箱:液压油箱用于存放液压油,并通过滤油器来保证油液的清洁。
油箱内还设置有油位显示器、温度传感器等装置,以便监测液压系统的工作状态。
3.液压马达:液压马达是卧式钻镗两用组合机床中驱动主轴转动的关键元件。
液压马达的转速和扭矩可以通过调节液压系统中的油压和流量来实现。
4.液压缸:液压缸主要用于实现机床在加工过程中的直线运动,例如镗削过程中的进给和退刀等操作。
液压缸的活塞直径和行程应根据机床的加工需求来确定,同时需要有充足的力量来保证加工负载。
5.控制阀组:控制阀组由数个液控阀组成,用于控制液压系统中油液的流向和压力。
应根据机床的运动要求来选择合适的控制阀,以满足机床的工作需求。
三、设计要点1.液压系统的压力和流量应根据机床的加工要求来确定,以保证机床能够稳定运行并满足加工负载。
2.液压系统应具备过热保护功能,通过设置合适的油温传感器和过热报警装置,可以在油温过高时及时发出警报并停止液压泵的工作,以防止系统损坏。
3.液压系统中应安装滤油器,以保证油液的清洁,避免杂质进入液压元件造成损坏。
4.液压系统中的液压油应定期更换,并注意油液的粘度和温度,在不同的季节和环境条件下进行调整,以保证系统的良好工作。
5.液压系统应配备完善的安全保护装置,例如安全阀、溢流阀和接触器等,以确保系统在异常情况下能够及时切断液压油的供给,并保护机床和操作人员的安全。
四、总结本文档对卧式钻镗两用组合机床的液压系统进行了设计,并提出了相关要点。
卧式钻,镗组合机床的动力滑台液压系统设计
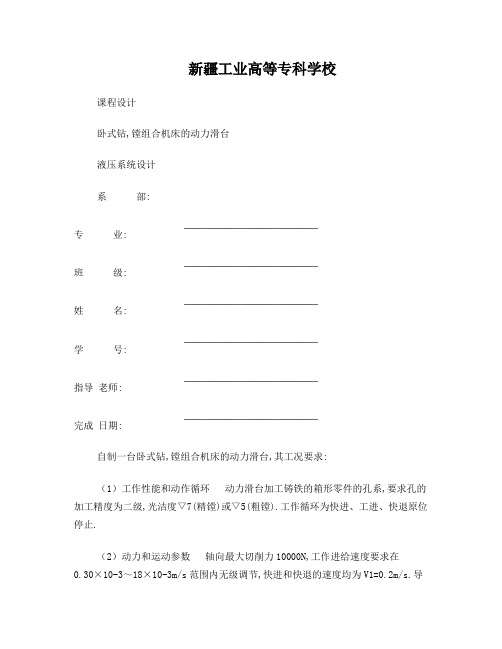
新疆工业高等专科学校课程设计卧式钻,镗组合机床的动力滑台液压系统设计系部:专业:班级:姓名:学号:指导老师:完成日期:自制一台卧式钻,镗组合机床的动力滑台,其工况要求:(1)工作性能和动作循环动力滑台加工铸铁的箱形零件的孔系,要求孔的加工精度为二级,光洁度▽7(精镗)或▽5(粗镗).工作循环为快进、工进、快退原位停止.(2)动力和运动参数轴向最大切削力10000N,工作进给速度要求在0.30×10-3~18×10-3m/s范围内无级调节,快进和快退的速度均为V1=0.2m/s.导轨型式为平导轨,静、动摩擦系数:f8=0.2、fd=0.2.往返运动的加速、减速时间为0.3s,快进行程L1为0.2m,工进行程L2为0.2m.(3)自动化程度采用液压与电气配合,实现工作自动循环.根据上述工况要求和动力滑台的结构安排,应采用液压缸为执行元件,有液压缸筒与滑台固结完成工作循环,活塞杆固定在床身上.由于要求快进与快退的速度相等,为减少液压泵的供油量,决定采用差动型液压缸,取液压缸前、后腔的有效工作面积比为2:1,活塞杆较粗,结构上可允许油管通过,进、出油管穿过活塞杆,直接使用硬管与液压装置或液压泵连接.这样就避免了由于较长软管的弹性变形引起动力滑台在转换中产生“前冲”“后坐”现象.使液压缸无杆腔为高压工作腔,这样能得到较大的输出动力,并可得到较低的稳定工作速度,以便满足精加工的要求.按本章前几节设计步骤,分步计算如下:一、计算外负载动力滑台受力情况如图9-12所1.切削阻力为已知Ft=12010N导轨摩擦阻力2.导轨摩擦阻力由动力滑台颠复力矩产生的,本题忽略颠复力矩的影响. 图 9-12动力滑台受力分析简图静摩擦阻力Fts=fsFg=0.2×12010N=24020N动摩擦阻力Ffd=fdFg=0.1×12010=12010N3.惯性阻力(1)动力滑台快速时惯性阻力Fm动力滑台启动加速、反响启动加速和快退减速制动的加速度相等,△V=0.2m/s,△t=0.3s,故惯性阻力为(2.动力滑台工进时惯性阻力F′m动力滑台由工进转换到制动是减速,取=15×10-3m/s ,=0.3s,故惯性阻力为4.重力由于动力滑台为卧式放置,所以负载不考虑重力.关于液压缸内部密封装置摩擦阻力Fs的影响,计入液压缸的机械效率中.根据以上分析,计算各工况负载列表9-10.本机床动力滑台所受负载迹为液压缸所受负载.表9-10 液压缸在各动作阶段的负载注: 取液压缸机械效率?m=0.9.二,绘制负载图和速度图根据已给的快进,快退,工进的行程和速度,配合表9—10中相应负载的数值,可绘制液压港的F—l与υ—l图,或近似计算快进、工进、快退的时间如下:快进工进V×10-3图9—13液压缸负载图和速度图(a)F—t图(b)υ—t图工进所需最长时间t2max为工进所需最短时间t2min为快退配合表9—10中相应负载的数值,可绘制F—t、υ—t图,见图9—13所示。
- 1、下载文档前请自行甄别文档内容的完整性,平台不提供额外的编辑、内容补充、找答案等附加服务。
- 2、"仅部分预览"的文档,不可在线预览部分如存在完整性等问题,可反馈申请退款(可完整预览的文档不适用该条件!)。
- 3、如文档侵犯您的权益,请联系客服反馈,我们会尽快为您处理(人工客服工作时间:9:00-18:30)。
课程设计说明书课程名称:液压与气压传动题目名称:卧式钻、镗组合机床的液压系统设计班级:姓名:学号:指导老师:评定成绩:教室评语:指导老师签名:20 年月日机电工程学院课程设计任务书目录第一章绪论 (4)1.1 开发背景及系统特点 (4)第二章液压系统的工况分析 (4)第三章负载图和速度图的绘制 (5)第四章液压缸主要参数的确定 (6)第五章液压系统的拟定 (8)5.1 液压回路的选择 (8)5.2 液压回路的综合 (11)第六章液压元件的选择 (11)6.1 液压泵 (11)6.2 阀类元件及辅助元件 (13)6.3 油管和油箱 (13)第七章液压系统性能的验算 (14)7.1 验算系统压力损失并确定压力阀的调整值 (14)7.2 油液温升验算 (16)第八章设计总结 (17)参考文献 (17)卧式钻、镗组合机床的液压系统设计说明书第一章 绪论 1.1 开发背景及系统特点本次课程设计将以组合机床动力滑台液压系统设计为例,介绍该组合机床液压系统的设计方法和设计步骤,其中包括组合机床动力滑台液压系统的工况分析、主要参数确定、液压系统原理图的拟定、液压元件的选择以及系统性能验算等。
组合机床是以通用部件为基础,配以按工件特定外形和加工工艺设计的专用部件和夹具而组成的半自动或自动专用机床。
组合机床一般采用多轴、多刀、多工序、多面或多工位同时加工的方式,生产效率比通用机床高几倍至几十倍。
组合机床兼有低成本和高效率的优点,在大批、大量生产中得到广泛应用,并可用以组成自动生产线。
组合机床通常采用多轴、多刀、多面、多工位同时加工的方式,能完成钻、扩、铰、镗孔、攻丝、车、铣、磨削及其他精加工工序,生产效率比通用机床高几倍至几十倍。
液压系统由于具有结构简单、动作灵活、操作方便、调速范围大、可无级连读调节等优点,在组合机床中得到了广泛应用。
第二章液压系统的工况分析一、工作负载工作负载是在工作过程中由于机器特定的工作情况而产生的负载,即W F =12000N 二、惯性负载最大惯性负载取决于移动部件的质量和最大加速度。
已知加、减速时间为0.2s ,工作台最大移动速度,即快进、快退速度为0.1m/s ,因此惯性负载为:N t v g G t v mF m 2.5102.08.91.010000=⨯⨯=∆∆•=∆∆=三、阻力负载阻力负载主要是工作台的机械摩擦阻力,分为静摩擦阻力和动摩擦阻力两部分。
静摩擦阻力 N F f F N s fs 2000100002.0=⨯== 动摩擦阻力 N F f F N d fd 1000100001.0=⨯==根据上述负载力计算结果,可得出液压缸在各个工况下所受到的负载力和液压缸所需推力情况,如下表所示:注:1、液压缸的机械效率为0.92、不考虑动力滑台上的颠覆力矩的作用。
液压缸各运动阶段负载表第三章 负载图和速度图的绘制按上面计算的数值以及已知条件进行绘制,即可绘制出负载和速度图,如下所示:速度图负载图第四章液压缸主要参数的确定由《液压传动》表11-2和表11-3可知,组合机床液压系统在最大负载约为14444.4N是宜取P=4MPa。
快退时回油腔中也是有背压的,这时选取背压值12P =0.6MPa 。
取液压缸无杆腔有效面积等于有杆腔有效面积的2倍11221112/(/2)m F A p A p A p A p η=-=-故有 23621110012.41028.044.144442m P P F A m -⨯=⨯⎪⎭⎫ ⎝⎛-=⎪⎭⎫ ⎝⎛-÷⎪⎪⎭⎫ ⎝⎛=η 快进速度V 快=0.1m/s ,工进速度V 工进=0.005m/s,相差很大,应进行差动换接,取k= A 2/ A 1=0.5,则:mm F D 83.75)kp - (p 421==π工d = 0.707D=0.707×75.83=53.62mm ,根据GB/T2348—2001对液压缸缸筒内径尺寸和液压缸活塞杆外径尺寸的规定,圆整后取液压缸缸筒直径为D=80mm ,活塞杆直径为d=60mm 。
中低压液压系统,由其切削加工性能确定液压缸筒壁厚,按薄壁圆筒计算壁厚: 额定工作压力: P n =7MPa<16MPa 试验压力为:P y =1.5P n =1.5×7=10.5MPa许用应力取:[]2/11000mm N =σ ([]n b /σσ= 取安全系数n=5)[]mm D p y 382=≥σδ此时液压缸两腔的实际有效面积分别为:23211003.54/m D A -⨯==π 232221020.24/)(m d D A -⨯=-=π按最低工进速度验算液压缸尺寸,查产品样本,调速阀最小稳定流量q=0.05L/min 因工进速度为0.00265m/s 为最小速度,则有1A ≥q/v=50000/15.92mm =31452mm因为1A =50242mm ≥31452mm ,满足最低速度的要求。
初步确定液压缸流量为:快进:11vA Q ==30L/min22vA Q ==15L/min21Q Q Q p -==15L/min工进:12A v Q =工=0.8L/min根据上述液压缸直径及流量计算结果,进一步计算液压缸在各个工作阶段中的压力、流量和功率值,如下表所示:第五章 液压系统图的拟定5.1液压回路的选择首先要选择调速回路。
这台机床液压系统的功率小,滑台运动速度低,工作负载变化小,故采用节流调速的开式回路是合适的,为了增加运动的平稳性,防止钻孔时工件突然前冲,系统采用调速阀的进油节流调速回路,并在回油路中加背压阀。
从工况图中可以清楚地看到,在这个液压系统的工作循环中,液压缸要求油源交替地提供低压大流量和高压小流量的油源。
最大流量和最小流量之比约为11,而快进快退的时间1t 和工进所需的时间2t 分别为:sv l v l t 7)1.04.0()1.03.0()/()/(33111=÷+÷=+=s v l t 2005.01.0/222=÷==即是2t /1t =3。
因此从提高系统效率、节省能量的角度上来说,采用单个定量泵作为油源显然是不合适的,而宜选用大、小两个液压泵自动并联供油的油源方案。
如下图所示:双泵供油油源其次是选择快速运动和换向回路。
系统中采用节流调速回路后,不管采用什么油源形式都必须有单独的油路直接通向液压缸的两腔,以实现快速运动。
本系统中,单杆液压缸要作差动连接,所以它的快进快退换向回路,如下图所示:换向回路再次是选择速度缓解回路,工况图可以看出,当动力头部件从快进转为工进时滑台速度变化较大,可选用行程阀来控制快进转工进的速度换接,以减少液压冲击,图如下所示:速度换接回路夹紧回路的选择,用三位四通电磁阀来控制夹紧、松开换向动作时,为了避免工作时突然失电而松开,应采用失电夹紧方式。
考虑到夹紧时间可调节和当进油路压力瞬时下降时仍能保持夹紧力,所以单向阀保压。
在该回路中还装有减压阀,用来调节夹紧力的大小和保持夹紧力的稳定,图示如下所示:5.2液压回路的综合液压回路的综合和整理第六章 液压元件的选择6.1液压泵工进阶段液压缸工作压力最大,取进油总压力损失Σp ∆=0.5MPa,压力继电器可靠动作需要压力差0.5MPa,则液压泵最高工作压力Pp=1p +Σp ∆+0.5MPa=4.8MPa因此泵的额定压力Pr ≥1.25×4800000Pa=6MPa工进时所需要流量最小是0.8L/min,设溢流阀最小流量为2.5L/min,则小流量泵的流量1p q ≥(1.1*0.32+2.5)L/min=2.85L/min快进快退时液压缸所需的最大流量为15.4L/min,则泵总流量qp=1.1*15.4L/min=16.9L/min 。
即大流量泵的流量2p q ≥qp-1p q =(16.9-2.85)L/min=14L/min根据上面计算的压力和流量,查产品样本,选用双联叶片泵,该泵额定压力6.3MPa ,额定转速960r/min二、电动机的驱动功率系统为双泵共有系统,其中小泵的流量1p q =(0.04/60)3m /s=0.0006673m /s大泵的流量2q =(0.012/60)3m /s=0.00023m /s差动快进,快退时的两个泵同时向系统供油;工进时,小泵向系统供油,大泵卸载。
快进时,小泵的出口压力损失0.45MPa ,大泵出口损失0.15MPa 。
小泵出口压力1p p =1.26MPa(总功率η=0.5) 大泵出口压力2p p =1.41MPa (总功率η=0.5) 电动机功率1p =1p p 1q /η+2p p 2q /η=0.73Kw工进时调速阀所需要最小压力差0.5MPa 。
压力继电器可靠需要动力差0.5MPa 。
因此工进时小泵的出口压力1p p =1p +0.5+0.5=4.8Pa. 大泵的卸载压力取2p p =0.2Pa 小泵的总功率η=0.565 大泵总功率η=0.3电动机功率2p =1p p 1q /η+2p p 2q /η=0.7Kw 快退时小泵出口压力1p p =1.65MPa(总功率η=0.5) 大泵出口压力2p p =1.8MPa(总功率η=0.5) 电动机功率3p =1p p 1q /η+2p p 2q /η=0.9Kw快退时所需的功率最大。
根据查样本选用Y90L-6异步电动机,电动机功率1.1Kw 。
额定转速910r/min6.2阀类元件及辅助元件液压系统原理图中包括调速阀、换向阀、单项阀等阀类元件以及滤油器、空气滤清器等辅助元件。
阀类元件的选择6.3油管和油箱各元件间连接管道的规格按元件接口处尺寸决定,液压缸进、出油管则按输入、输出的最大流量计算。
由于液压泵的具体选定之后液压缸在各阶段的进、出流量已与原定数值不同,所以要重新计算如表所示液压缸的进、出流量和运动速度当油液在压力管中流速取3m/min 时,可算得与液压缸无杆腔和有杆腔相连的油管内径分别为:mm v q d 59.166********.382236=⨯⨯⨯⨯⨯==ππmm v q d 44.126010310888.212236=⨯⨯⨯⨯⨯==ππ 这两根有关按GB/T2351-2005选用外径16φmm 、内经13φmm 的无缝钢管。
油箱容积按公式计算,当去K 为6时,求得其容积为V=6×40=240L ,按GB2876-81规定,取最靠近的标准值V=250L 。
第七章 液压系统性能的验算7.1 验算系统压力损失并确定压力阀的调整值一、工进工进时管路的流量仅为0.8L/min,因此流速很小,所以沿程压力损失和局部损失都非常小,可以忽略不计。
这时进油路上仅考虑调速阀的损失0.5MPa ,回油路上只有背压阀损失,小流量泵的调整压力:Pp= +0.5+0.5=4.8MPa 二、快退时的压力损失及大流量泵卸载压力的调整快退时进油管和回油管长度为1.8m ,有油管直径d=0.015m ,通过的流量为进油路 =16L/min ,回油路 =32L/min 。