挤压成型技术
混凝土挤压成型技术及应用

混凝土挤压成型技术及应用一、前言混凝土挤压成型技术是一种新型的混凝土施工技术,其应用范围广泛,可以用于建筑、桥梁、隧道、地铁、水利工程等领域。
本文将从混凝土挤压成型技术的基本原理、施工流程、应用案例等方面进行详细介绍。
二、混凝土挤压成型技术的基本原理混凝土挤压成型技术是利用专用设备在模具内将混凝土挤压成型的一种施工技术。
其基本原理是将混凝土从模具的一端注入,然后利用挤压机从另一端将混凝土挤压至模具的另一端,形成所需的形状。
三、混凝土挤压成型技术的施工流程1.准备工作:检查设备是否正常运转,准备好所需的混凝土、模具、钢筋等材料。
2.模具安装:将模具安装在挤压机上,并根据需要进行调整。
3.钢筋布置:在模具内布置好所需的钢筋。
4.混凝土注入:将混凝土从模具的一端注入。
5.挤压成型:启动挤压机,从另一端将混凝土挤压至模具的另一端,形成所需的形状。
6.养护:待混凝土凝固后,拆卸模具,并进行养护。
四、混凝土挤压成型技术的应用案例1.建筑领域:混凝土挤压成型技术可以用于建筑领域的各种构件制作,如梁、柱、板、墙等。
相比传统的混凝土施工技术,挤压成型技术可以大幅度提高施工效率,同时还能够保证成型件的质量和精度。
2.桥梁领域:混凝土挤压成型技术可以用于桥梁领域的各种构件制作,如桥墩、桥台、梁等。
相比传统的混凝土施工技术,挤压成型技术可以大幅度提高施工效率,同时还能够保证成型件的质量和精度。
3.隧道领域:混凝土挤压成型技术可以用于隧道领域的各种构件制作,如衬砌、拱顶等。
相比传统的混凝土施工技术,挤压成型技术可以大幅度提高施工效率,同时还能够保证成型件的质量和精度。
4.水利工程领域:混凝土挤压成型技术可以用于水利工程领域的各种构件制作,如堤坝、水闸、渠道等。
相比传统的混凝土施工技术,挤压成型技术可以大幅度提高施工效率,同时还能够保证成型件的质量和精度。
五、混凝土挤压成型技术的优势与不足1.优势:(1)施工效率高:相比传统的混凝土施工技术,挤压成型技术可以大幅度提高施工效率。
金属锻造挤压成型技术
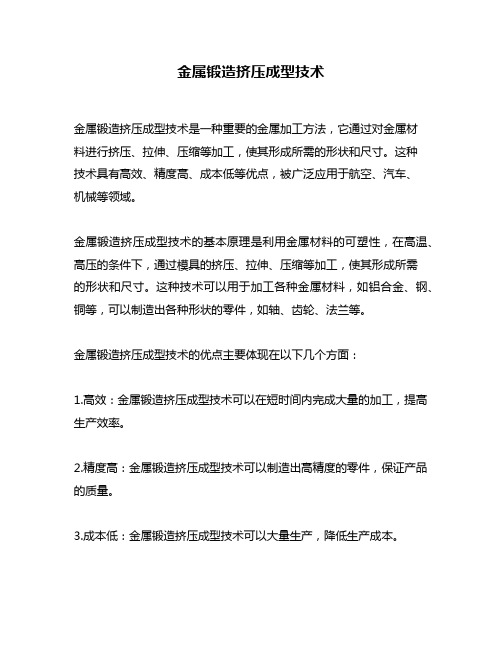
金属锻造挤压成型技术金属锻造挤压成型技术是一种重要的金属加工方法,它通过对金属材料进行挤压、拉伸、压缩等加工,使其形成所需的形状和尺寸。
这种技术具有高效、精度高、成本低等优点,被广泛应用于航空、汽车、机械等领域。
金属锻造挤压成型技术的基本原理是利用金属材料的可塑性,在高温、高压的条件下,通过模具的挤压、拉伸、压缩等加工,使其形成所需的形状和尺寸。
这种技术可以用于加工各种金属材料,如铝合金、钢、铜等,可以制造出各种形状的零件,如轴、齿轮、法兰等。
金属锻造挤压成型技术的优点主要体现在以下几个方面:1.高效:金属锻造挤压成型技术可以在短时间内完成大量的加工,提高生产效率。
2.精度高:金属锻造挤压成型技术可以制造出高精度的零件,保证产品的质量。
3.成本低:金属锻造挤压成型技术可以大量生产,降低生产成本。
4.材料利用率高:金属锻造挤压成型技术可以将金属材料的利用率提高到90%以上,减少浪费。
金属锻造挤压成型技术的应用范围非常广泛,主要包括以下几个方面:1.航空领域:金属锻造挤压成型技术可以制造出各种形状的航空零件,如发动机叶片、涡轮盘等。
2.汽车领域:金属锻造挤压成型技术可以制造出汽车发动机、变速器等零件。
3.机械领域:金属锻造挤压成型技术可以制造出各种机械零件,如轴、齿轮、法兰等。
4.电子领域:金属锻造挤压成型技术可以制造出各种电子零件,如散热器、机箱等。
总之,金属锻造挤压成型技术是一种非常重要的金属加工方法,具有高效、精度高、成本低等优点,被广泛应用于航空、汽车、机械等领域。
随着科技的不断发展,金属锻造挤压成型技术也将不断创新和发展,为各个领域的发展提供更好的支持。
挤压成型的基本原理
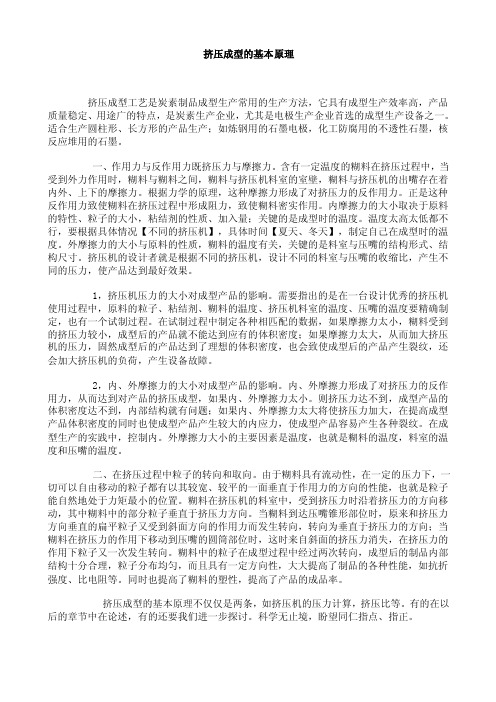
挤压成型的基本原理挤压成型工艺是炭素制品成型生产常用的生产方法,它具有成型生产效率高,产品质量稳定、用途广的特点,是炭素生产企业,尤其是电极生产企业首选的成型生产设备之一。
适合生产圆柱形、长方形的产品生产;如炼钢用的石墨电极,化工防腐用的不透性石墨,核反应堆用的石墨。
一、作用力与反作用力既挤压力与摩擦力。
含有一定温度的糊料在挤压过程中,当受到外力作用时,糊料与糊料之间,糊料与挤压机料室的室壁,糊料与挤压机的出嘴存在着内外、上下的摩擦力。
根据力学的原理,这种摩擦力形成了对挤压力的反作用力。
正是这种反作用力致使糊料在挤压过程中形成阻力,致使糊料密实作用。
内摩擦力的大小取决于原料的特性、粒子的大小,粘结剂的性质、加入量;关键的是成型时的温度。
温度太高太低都不行,要根据具体情况【不同的挤压机】,具体时间【夏天、冬天】,制定自己在成型时的温度。
外摩擦力的大小与原料的性质,糊料的温度有关,关键的是料室与压嘴的结构形式、结构尺寸。
挤压机的设计者就是根据不同的挤压机,设计不同的料室与压嘴的收缩比,产生不同的压力,使产品达到最好效果。
1,挤压机压力的大小对成型产品的影响。
需要指出的是在一台设计优秀的挤压机使用过程中,原料的粒子、粘结剂、糊料的温度、挤压机料室的温度、压嘴的温度要精确制定,也有一个试制过程。
在试制过程中制定各种相匹配的数据,如果摩擦力太小,糊料受到的挤压力较小,成型后的产品就不能达到应有的体积密度;如果摩擦力太大,从而加大挤压机的压力,固然成型后的产品达到了理想的体积密度,也会致使成型后的产品产生裂纹,还会加大挤压机的负荷,产生设备故障。
2,内、外摩擦力的大小对成型产品的影响。
内、外摩擦力形成了对挤压力的反作用力,从而达到对产品的挤压成型,如果内、外摩擦力太小。
则挤压力达不到,成型产品的体积密度达不到,内部结构就有问题;如果内、外摩擦力太大将使挤压力加大,在提高成型产品体积密度的同时也使成型产品产生较大的内应力,使成型产品容易产生各种裂纹。
挤压成型工艺技术

挤压成型工艺技术挤压成型工艺技术是一种常用的金属加工方法,广泛应用于制造行业。
挤压成型是将金属坯料经过一定的压力挤压成具有所需形状和尺寸的产品的一种成型方法。
挤压成型工艺技术的基本原理是通过将金属坯料置于挤压机的工作室中,然后施加一定的压力使金属坯料通过模具的缝隙挤压出来,最终形成所需形状和尺寸的成品。
挤压成型工艺技术的关键是模具设计和成型参数的控制。
模具设计需要考虑到产品的形状、尺寸和结构,以及金属的流动性和可挤压性。
成型参数的控制包括挤压力、挤压速度、温度和润滑条件等。
合理的模具设计和成型参数的控制可以保证产品质量和生产效率。
挤压成型工艺技术有许多优点。
首先,挤压成型可以实现连续生产,提高生产效率。
其次,挤压成型可以制造复杂形状的产品,例如管材、型材和复杂截面的零件等。
此外,挤压成型可以提高材料的利用率,因为挤压成型可以将金属坯料从较大横截面挤压成较小横截面,减少材料浪费。
挤压成型工艺技术的应用范围非常广泛。
在汽车制造行业,挤压成型常用于制造汽车车身和车架等零部件。
在建筑行业,挤压成型常用于制造铝型材和钢管等建筑材料。
在电子和电器行业,挤压成型常用于制造散热器和散热片等散热材料。
然而,挤压成型工艺技术也有一些局限性。
首先,挤压成型只适用于某些金属材料,例如铝、铜和钢等。
对于某些高硬度和高熔点的金属,挤压成型难以实现。
其次,挤压成型有一定的限制,不能制造过大和过长的产品。
此外,挤压成型过程中可能会出现材料变形和挤出问题,需要通过优化模具设计和成型参数来解决。
总之,挤压成型工艺技术是一种重要的金属加工方法,具有广泛的应用前景。
通过合理的模具设计和成型参数的控制,挤压成型可以实现高效、精确和连续的生产,满足各行业对产品形状和尺寸的要求。
随着材料科学和加工技术的不断发展,挤压成型工艺技术的性能和应用也将不断提高和拓展。
金属锻造挤压成型技术

金属锻造挤压成型技术金属锻造挤压成型技术是一种重要的金属加工方法,广泛应用于航空航天、汽车制造、机械工程等领域。
它通过对金属材料施加压力,使其在高温下发生塑性变形,从而得到所需的形状和尺寸。
本文将详细介绍金属锻造挤压成型技术的原理、应用和优势。
一、原理金属锻造挤压成型技术基于金属材料的塑性变形性质。
在加热至合适温度后,金属材料的结晶粒会发生变形,从而改变其原有的形状和尺寸。
通过在金属材料两侧施加压力,使其发生挤压变形,从而得到所需的形状。
挤压过程中,金属材料会经历压缩、延伸和弯曲等变形,最终形成所需的产品。
二、应用金属锻造挤压成型技术在工业生产中有着广泛的应用。
首先,在航空航天领域,金属锻造挤压可用于制造飞机发动机叶片、涡轮叶片等关键零部件。
这些零部件需要具备高强度和高耐热性能,而挤压成型能够满足这些要求。
其次,在汽车制造领域,金属锻造挤压可用于制造汽车车身结构、车轮毂等零部件。
挤压成型具有高效率和高精度的特点,能够提高汽车的安全性和稳定性。
此外,金属锻造挤压还广泛应用于机械工程、电子设备制造等领域。
三、优势金属锻造挤压成型技术具有以下几个优势。
首先,它可以提高材料的密度和强度。
在挤压过程中,金属材料会发生塑性流动,使得晶粒更加致密,从而提高了材料的密度和强度。
其次,它可以实现复杂形状的制造。
通过调整挤压过程的参数,可以制造出各种复杂的形状和结构,满足不同产品的需求。
再次,它可以节约材料和能源。
相比于传统的切削加工方法,挤压成型可以减少材料的浪费和能源的消耗,有利于环境保护和资源节约。
最后,它可以提高生产效率和产品质量。
挤压成型具有高效率和高精度的特点,能够实现批量生产,提高生产效率,同时保证产品的一致性和稳定性。
金属锻造挤压成型技术是一种重要的金属加工方法,具有广泛的应用前景和优势。
在未来的发展中,我们可以进一步改进挤压设备和工艺,提高挤压成型的效率和质量,推动金属加工技术的发展,为各行各业的发展提供支持。
金属锻造挤压成型技术
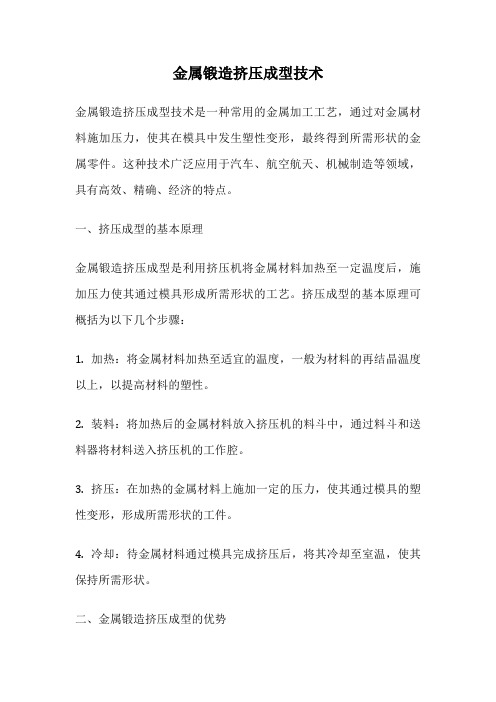
金属锻造挤压成型技术金属锻造挤压成型技术是一种常用的金属加工工艺,通过对金属材料施加压力,使其在模具中发生塑性变形,最终得到所需形状的金属零件。
这种技术广泛应用于汽车、航空航天、机械制造等领域,具有高效、精确、经济的特点。
一、挤压成型的基本原理金属锻造挤压成型是利用挤压机将金属材料加热至一定温度后,施加压力使其通过模具形成所需形状的工艺。
挤压成型的基本原理可概括为以下几个步骤:1. 加热:将金属材料加热至适宜的温度,一般为材料的再结晶温度以上,以提高材料的塑性。
2. 装料:将加热后的金属材料放入挤压机的料斗中,通过料斗和送料器将材料送入挤压机的工作腔。
3. 挤压:在加热的金属材料上施加一定的压力,使其通过模具的塑性变形,形成所需形状的工件。
4. 冷却:待金属材料通过模具完成挤压后,将其冷却至室温,使其保持所需形状。
二、金属锻造挤压成型的优势1. 节约材料:挤压成型可以有效利用金属材料,减少材料的浪费。
2. 提高产品质量:挤压成型可以使金属材料的晶粒细化,提高材料的强度和硬度。
3. 提高生产效率:挤压成型速度快,可大幅提高生产效率。
4. 适应性强:挤压成型适用于各种金属材料,包括铝、铜、钢等。
5. 成本低:挤压成型工艺简单,设备投资和生产成本相对较低。
三、金属锻造挤压成型的应用领域金属锻造挤压成型技术被广泛应用于各个领域,特别是在汽车、航空航天和机械制造等行业具有重要地位。
以下是几个典型的应用领域:1. 汽车制造:挤压成型可以用于制造汽车车身、车门、车架等零部件,具有优良的强度和刚性。
2. 航空航天:挤压成型可用于制造航空航天器的翼、舵面等零件,具有轻量化、高强度的特点。
3. 机械制造:挤压成型可用于制造各种机械零件,如齿轮、轴承座等,具有高精度和高强度。
四、金属锻造挤压成型技术的发展趋势随着科技的不断进步,金属锻造挤压成型技术也在不断发展。
未来,金属锻造挤压成型技术可能呈现以下几个趋势:1. 精密化:随着对产品精度要求的提高,金属锻造挤压成型技术将朝着更高的精密化方向发展。
挤压工艺技术交底
挤压工艺技术交底挤压工艺技术交底一、挤压工艺技术的定义和概述挤压工艺技术是一种利用挤压机将金属或非金属材料加热至一定温度后,通过挤压头对其进行挤压成型的加工技术。
挤压工艺技术广泛应用于铝合金、铜合金、钢材等金属材料的加工,也可用于塑料、橡胶等非金属材料的加工。
二、挤压工艺技术的基本原理和流程1. 原材料准备:根据产品要求,选择适合的金属材料或非金属材料,并进行前处理,如锯切、砂光等。
2. 加热预处理:将原材料加热至适当温度,提高材料的塑性和可挤压性。
3. 挤压成型:将加热的材料放置在挤压机的挤压头下,通过挤压头的运动,施加较大的压力将材料挤压成型。
4. 温度控制:在挤压过程中,通过控制加热温度、冷却速度等参数,控制产品的质量和性能。
5. 后续处理:将挤压成型的产品进行修整、焊接、除氧化层等处理,提高产品的完整性和美观度。
三、挤压工艺技术的工艺参数和设备要求1. 挤压机:挤压机是挤压工艺技术的核心设备,主要包括机架、挤压头、压力系统和控制系统等组成部分。
2. 挤压头:挤压头是挤压机的关键部件,其结构和形状决定了产品的外观和尺寸精度。
3. 温度控制系统:温度控制系统能够对挤压过程中的加热和冷却进行精确控制,保证产品质量和性能。
4. 模具:根据产品的要求,设计和制造适应性的模具,用于挤压成型过程中的形状和尺寸控制。
四、挤压工艺技术的应用领域和优势挤压工艺技术被广泛应用于汽车、航空航天、建筑、电子、电器等行业,其优势主要有:1. 产品精度高:挤压工艺技术能够实现高精度的产品加工和成型,满足不同行业对产品精度的要求。
2. 成本低:挤压工艺技术在大批量生产中具有较高的效率和较低的成本,降低了产品制造成本。
3. 节约材料:挤压工艺技术能够最大限度地利用原材料,减少浪费和环境污染。
4. 增加产品强度:挤压过程中,材料的晶粒重新排列,使产品具有较高的强度和耐磨性。
综上所述,挤压工艺技术是一种高效、精确、经济的加工技术,具有广泛的应用前景。
螺旋挤压生产棒状成型物技术
螺旋挤压生产棒状成型物技术螺旋挤压生产棒状成型物技术是一种常见的生产工艺,它通过将熔融状态的原料料坯通过螺旋挤出机进行连续挤压成型,最终得到棒状产品。
这种技术广泛应用于塑料、橡胶、金属和陶瓷等领域。
本文将对螺旋挤压生产棒状成型物技术进行详细介绍。
螺旋挤压生产棒状成型物的原理是通过螺旋挤出机将熔融态的料坯推进至模具中,经过模具的挤出口,进一步挤压成型。
螺旋挤出机通常由进料机构、加热区、挤出机筒和模具挤出口组成。
进料机构将原料料坯送入加热区,使其达到熔融状态。
然后,熔融原料经过加热区的加热作用进入到挤出机筒中。
在筒内,螺旋将料坯向前推进并加热,同时通过压力将熔融料坯挤压入模具中,形成棒状物。
最后,挤压出来的棒状物经过冷却和固化处理,形成最终的产品。
螺旋挤压生产棒状成型物技术具有以下几个优点。
首先,该技术可以实现连续生产,提高生产效率。
相对于传统的批量生产工艺,螺旋挤压技术可以连续进行,大大节省了时间和人力成本。
其次,该技术适用于多种材料,如塑料、橡胶、金属和陶瓷等。
因此,不同领域的制造业都可以应用该技术进行生产。
此外,螺旋挤压生产棒状成型物技术还具有成本低、质量稳定等特点。
在实际应用中,螺旋挤压生产棒状成型物技术有多种不同的方法。
其中一种常见的方法是单螺旋挤压法。
单螺旋挤压法通过一根螺旋将熔融原料从筒中挤入模具中,形成棒状物。
这种方法适用于较粘性的物料,例如塑料等。
另一种方法是双螺旋挤压法。
双螺旋挤压法利用上、下两根螺旋将原料从两侧挤入模具中,形成棒状物。
这种方法适用于较流动性的物料,例如金属等。
在螺旋挤压生产棒状成型物技术中,需要注意一些关键因素,以保证产品质量和生产效率。
首先,原料的选择非常重要。
不同的材料具有不同的熔融温度、流动性和黏度等参数,需要根据具体要求选择适合的材料。
其次,挤出机的参数设置也很关键。
挤出机的进给速度、转速、压力等参数需要根据不同材料和产品要求进行调整。
此外,模具的设计和制造也对产品质量有重要影响。
挤压成型工艺基本介绍
挤压成型工艺基本介绍
挤压成型是金属加工中的一种常见的成型工艺,它通过挤压机或其他挤压设备,将金
属坯料在特殊模具中挤压成所需的呈现形状。
它可以有效地生产出特殊结构的具有复杂外
形的各种工件。
挤压成型是金属高效加工的重要技术之一。
挤压成型工艺主要分为热挤压成型和冷挤压成型两种。
热挤压指的是在挤压成型之前,先将金属材料经过适当热处理,增加其可塑性,然后在型腔内进行挤压成型。
冷挤压是指
在没有热处理的情况下进行挤压成型工艺,模具由强度较大的P20模具钢制成,这种工艺
可以生产出具有良好的表面粗糙度和精度的工件。
这种工艺还可以使金属铸态焊接,防止
金属材料松脱,对于生产体积较小的技术含量比较高的工件具有更大的优势。
挤压成型技术可以节能,延长工件使用寿命,由于挤压过程发挥金属本身的强度,因
此具有较强的抗冲击性,工件表面几乎无边角、变形较小等特点,并且具有较高的表面精度。
挤压成型是金属材料加工中最有效率的方法之一,较大程度上改进了产品结构设计,
可以减少制造成本和生产时间,大大提高了工件的产量。
挤压成型有一定的要求,例如需要考虑的模具的尺寸、圆度和耐磨程度,以及能够承
受挤压力的硬度、强度和热韧性。
同时,还需要考虑材料的可塑性、流动性、延展性、稳
定性和抗拉伸强度。
施工时,还要充分考虑金属进行挤压的温度、挤压时间、塑形角度和
模具的尺寸设计等影响挤压成型的因素。
材料成型工艺学挤压与拉拔新技术
4 连续挤压
有连续挤压和连续铸挤两种。 连续挤压(Conform) 20世纪70年代提出。
是挤压技术的一 次革命,可连续生 产,生产率、成品 率高;主要缺点是 生产的品种和规格 受到限制(适于合 金强度低、尺寸规 格小、形状简单的 场合)。
连续挤压复合
铝包钢线:1956年日立电 缆公司研制成功。生产方法 有:
1 比较空拉、固定短芯头拉拔、游动芯 头拉拔的特点
2 拉制品的残余应力、危害及消除措施
3 实现带滑动连续拉拔的条件
4 拉拔的历史与发展趋势
有无润滑和润滑两种方式。
无润滑:主要由于生产长制品, 一般要求 合金在挤压温度下有具有好的焊接性能, 且限于对焊合面的质量和性能要求不高的 制品。
润滑:目的是消除压余、提高成品率 ( 10~15%)、缩短非挤压间隙时间。
注:润滑挤压时一般采用凹形垫片以平衡 金属流动、防止缩尾、使接合界面成近似 平面(减少切头切尾损失)。
将液、固相共存的均匀混合的 非枝晶坯料由挤压筒内挤出成形 的加工方法。
特点:1)变形抗力低,可实 现大变形;2)可获得晶粒细小、 组织性能均匀的制品;3)有利 于低塑性、高强度、复合材料等 难变形材料的成形。
半固态坯料制备方法:在凝固过程中进行强烈的机械搅 拌、电磁搅拌、单辊剪切/冷却、倾斜板铸造、近液相线铸 造等,将枝晶破碎进而获得液相和细小等轴晶组成的半固 态坯料。利用半固态坯料直接成形的方法称为流变成形; 将坯料加热到半固态进行成形的方法称为触变成形。
包覆轧制:轧包后仅能表 明精整,不能拉拔,因此性 能较低;
热浸镀法:镀层厚度不均 且较脆,不宜再加工;
粉末挤压烧结法:将铝粉 挤压包覆在钢芯上,经烧结 再加工。技术成熟(美国), 我国尚未掌握。
- 1、下载文档前请自行甄别文档内容的完整性,平台不提供额外的编辑、内容补充、找答案等附加服务。
- 2、"仅部分预览"的文档,不可在线预览部分如存在完整性等问题,可反馈申请退款(可完整预览的文档不适用该条件!)。
- 3、如文档侵犯您的权益,请联系客服反馈,我们会尽快为您处理(人工客服工作时间:9:00-18:30)。
挤压成型技术
主要内容•挤压成型基础知识
•铝型材挤压
1定义
挤压成型(Press Forming)是对放在模具模腔(或挤压筒)内的的金属坯料施加强大的压力,迫使金属坯料产生定向塑性变形,从挤压模的模孔中挤出而获得所需断面形状、尺寸并具有一定力学性能的零件或半成品的塑性加工方法。
金属挤压示意图
2.挤压分类方法
2.1按金属塑变流动方向可以分为:
正挤压:挤压时,金属流动方向与凸模运动方向相同
反挤压:挤压时,金属流动方向与凸模运动方向相反
复合挤压:挤压时,坯料一部分金属流动方向与凸模运动方向相同,另一部分则相反
径向挤压:挤压时,金属流动方向与凸模运动方向成90°
2.2按金属坯料的温度分类:
模具材料表面处理及
润滑零件质量影响因素
冷挤压高强度,高硬度,
高韧性,高耐磨
性,耐热性
表面磷化处理,
氟化石蜡油、肥
皂油和二硫化钼
混合液润滑处理
1.设备的刚性
2.温度升高
3.模具弹性变形
温挤压有足够的硬度,
强度,韧性,抗
磨损,耐疲劳润滑剂具有一定
热稳定和绝热性
1.温度
2.润滑
3.模具弹性变形
热挤压高温抗变形能力,
高温耐磨性,抗
热疲劳能力,抗
回火能力,良好
加工性
润滑剂应具有耐
压、耐热、不分
解变质性能,无
腐蚀作用
1.温度变化
2.
挤压件断面形状
3.润滑条件
4.氧
化
3.挤压条件
1)使金属处于三向压应力状态;
2)建立足够的应力值,使金属能够产生塑性变形;
3)有能使金属流出的孔或间隙,提供一个阻力最小的方向。
4工艺特点:
•挤压时金属坯料处于三向压应力状态下变形,因此可提高金属坯料的塑性,有利于扩大金属材料的塑性加工范围。
•可挤压出各种形状复杂、深孔、薄壁和异型截面的零件,且零件尺寸精度高,表面质量好,尤其是冷挤压成形。
•零件内部的纤维组织基本沿零件外形分布且连续,有利于提高零件的力学性能。
•生产率较高,只需更换模具就能在同一台设备上生产形状,尺寸规格和品种不同的产品。
•节约原材料,挤压属于少(无)切削加工,大大节约了原材料。
5.影响挤压力大小的因素
1)变形抗力(金属的屈服限)越大,所需挤压力越高,高温时,变形抗力降低,挤压力随之降低。
2)加工率的影响。
加工率越大,所需挤压力越大。
3)锭坯长度的影响
长度越长,挤压过程越长,挤压终了时温度变化大,变形抗力变大。
正挤压时,要克服锭坯与挤压筒壁的摩擦力,故挤压力增加,反挤压时,挤压力与锭坯长无关。
4)挤压速度的影响。
5)摩擦条件的影响
挤压筒内表面的状态、润滑条件影响锭坯与筒壁间的摩擦状况,从而会影响挤压力大小。
6)挤压筒温度的影响
挤压筒预热适当们可以降低锭坯的冷却速率,减小挤压力。
7)挤压温度的影响
金属在挤压时必须考虑适宜的挤压温度。
6.挤压时金属的流动
I为定径区 II为变形区 III区位未变形区IV为死区
7.挤压件常见缺陷•表面折叠
•表面折缝
•缩孔
•裂纹
8.挤压新工艺
1)静液挤压
采用高压液体代替了通常的挤压轴的直接作用,将锭坯从模具中基础形成制品的加工方法。
静液挤压不仅适用于脆性金属,也适用于铜、铝等塑性良好的金属,冷的和预热的锭坯都可以挤压。
具有良好的润滑条件和均匀的金属流动性,特别适合于形状复杂、尺寸精度及表面质量要求高的异型管材的成形。
与传统挤压方法的区别是:作用在挤压筒上的径向压力与轴向压力相同,对挤压筒提出更高的设计要求。
2)等温挤压 3)连续挤压 4)轧挤法
9.挤压生产流程
1)铝合金挤压车间生产流程锭坯加热
挤压切断毛坯
车皮镗孔
取样切头二次挤压
矫直淬火
退火矫直
取样人工时效
包装入库检查验收检查验收检查验收检查验收
包装入库
包装入库包装入库
铝型材挤压技术
1.铝型材挤压技术的发展现状
•工艺装备向大型化,现代化,精密化和生产自动化方向发展。
•大型优质圆,扁挤压筒与特种模具技术取得突破性进展。
•挤压工艺不断改进和完善。
•铝挤压材的产品结构有了很大的改进。
铝型材挤压模具
产品:
发展趋势:
•节能减排
•减少外部摩擦,提高变形效率•提高精度
•防止产生缺陷,利用缺陷•提高回收率和成品率
•提高工模具品质和使用寿命•减少工序
•降低劳动强度
金属挤压机的类型选择机械压力机液压机
行程次数行程次数高,生产率高,无
法调节行程次数一定范围内任意调节行程次数
行程长度行程长度长,可任意调节
压力大小根据行程位置不同可改变压
力整个行程中可得到相同的压力,保持最高压力
过载保护装置可靠性不高有安全阀作为过载保护装置,
安全可靠
维修与保养相对较低易漏损,需经常更换密封装
置,维修费用高
谢谢!。