操作型计算和特殊精馏
第三章 精馏

*
(3-8)
当操作压强不高时,气相仍遵循道尔顿分 压定律,式(3-7)可改写为
pyA x A y A x B y A ( 1 x A ) pyB x B y B x A ( 1 y A )x A
x y 1 ( 1) x
(5-12)
(3 - 11)
例3-2 由表3-3数据,求算苯-甲苯的相对 挥发度、平均相对挥发度及气液两相平衡 组成。
精馏是气液两相间的传质过程,传质是 以两相达到平衡为极限的。在分析和解 决精馏操作中所涉及的问题时,常以溶 液的气液相平衡关系为基础。
§3.1 双组分溶液的气液相平衡
3.1.1理想溶液 : 溶液中不同组分的分子间 作用力和相同分子的分子间作用力完全相 等的溶液.即 AA BB AB
图3-4 具有正偏差的非理想溶液的p-x相图
正偏差很大的体系
(a)T-x(y) 图
(b)
x-y图
图3-5 乙醇-水体系的气液相平衡组成图
负偏差很大的体系
(a)T-x(y) 图
(b)
x - y图
图4-6 硝酸-水体系的气液平衡组成图
4.1.3 相对挥发度
气液平衡关系除用相图表示之外还可用相对挥 发度来表示。 纯液体的挥发度通常指液体在一定温度下的饱 和蒸汽压 由于双组分溶液中一组分的蒸气压受另一组分 存在的影响,故溶液中各组分的蒸汽压比纯组 分的低,溶液中的挥发度可用它在蒸汽气中的 分压 pi 和与其成平衡的液相中的摩尔分数 xi 来表示。
表3-5 由平均相对挥发度计算所得苯-甲苯气液相平衡组成
T
xA yA
0
C
80.1 1.00 1.00
11 特殊精馏

1
第1页
特殊精馏
一般的蒸馏或精馏操作是以液体混合物 中各组分的相对挥发度差异为依据的。组 分间挥发度差别愈大愈容易分离。 但对某些液体混合物,组分间的相对挥发 度接近于1或形成恒沸物,以至于不宜或 不能用一般精馏方法进行分离。则需采用 特殊精馏方法。
第2页
特殊精馏
特殊精馏方法有膜蒸馏、催化精馏、吸附 精馏、恒沸精馏、萃取精馏、盐效应精馏 等。 对恒沸精馏、萃取精馏、盐效应精馏都是 在被分离溶液中加入第三组分以加大原溶 液中各组分间相对挥发度。
第14页
流程收敛
• 介绍概念
✓模块收敛(convergence blocks) ✓撕裂流股(tear streams) ✓流程顺序(flowsheet sequences)
第15页
流程收敛
评估流程的收敛性,需确定
• 计算顺序 • 撕裂流股 • 求解的迭代次数 • 收敛容差 • 收敛的计算方法
关于流程收敛性的所有信息都会写入控制面板(Control Pan nel)
第16页
流程收敛---收敛模块
• 每个设计规定和撕裂流都有一个相关联的收敛模块 • 收敛模块确定撕裂流估算初值或设计规定中控制变
量值在逐次迭代过程中的更新方法。 • Aspen Plus定义的收敛模块的名字以字符“$.”开
头
• 用户定义的收敛模块的名字一定不要用字符“$.”开头 。
• 要确定由Aspen Plus定义的收敛模块,请看Control Panel(控制面板)信息中的“Flowsheet Analysis (流程分析)” 部分。
第24页
特殊精馏—多效精馏
• 例题:
甲醇分离塔,要将60wt%甲醇水溶液提纯。分别用单塔 和双效塔进行分离,并比较当两种产品一致时的能量 利用情况。已知条件: 进料温度为20C,压力为101.325kPa,流率为100kg/h 。单塔的压力为101.325kPa,理论板数为22, 进料板 位置为11, 塔顶产品流率为63kg/h,摩尔回流比为0. 65.
特殊精馏方法介绍

(2-162) ln 12 p1s (1 2 x1 ) ln( s ) Ts A12 p2 (2-161)
讨论溶剂S对 1, 2 的影响:
第三项: x ( A A ) 反映了溶剂S对组分1,2不同作用效果.
s 1S 2S
使 1, 2 / s 1 A1s 0
3)当三元系中有二对二元最低恒沸物,而另一对是二元最 高恒沸物时,压力曲面上就可能出现“谷”;温度曲面 上 就可能出现“脊”; 当三元系中有二对二元最高恒沸物,而另一对是二元最 低恒沸物时,温度曲面上就可能出现“沟”;压力曲面 上 就可能出现“脊”;
2.恒沸点的预测
12
恒沸点时: 12 1 ki ˆV i P
sn x s
结合(2-164)和(2-167) 精:
xs S D sn (1 sn ) L 1 xs
(2-168)
S
RDxs (1 sn )
D sn x s
(1 x s )
1 (1 sn ) x s
(2-169)
提:
xs
其中:
S (1 sn ) L
xs [A 1s A s2 2x1(A s1 A 1s ) xs (A 2s A s2 ) C(x2 x1)]
若 r~X 曲线近似对称,即 Ai,j=Aj,i , C=0
A1, 2 A2,1 A12
A12 A1, 2 A2,1 2
S A1, S AS ,1 A1
V i
0
ˆ P
0
1, 2
V 0 ˆ K1 2 1 f1 V ˆ f0 K2 1 2 2
一般萃取精馏操作压力不高,所以
第三章 多组分精馏和特殊精馏(化工分离过程)
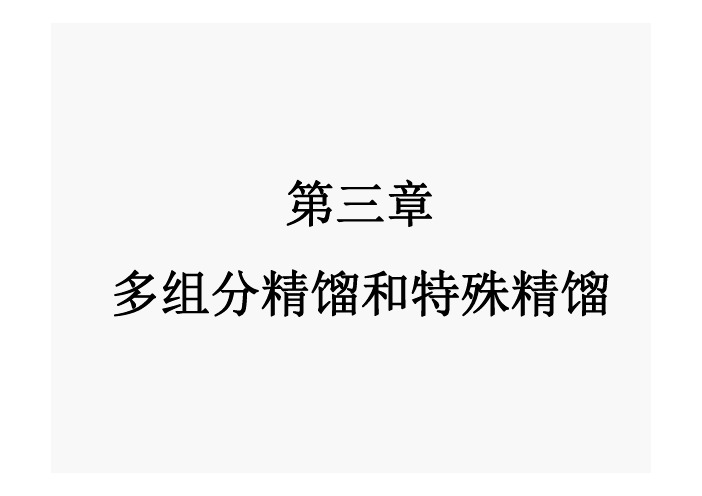
3.1.3 最少理论板数(Nm)和组分分配
全回流对应最少理论板数,但全回流下无产品采出, 因此正常生产中不会采用全回流。 什么时候采用全回流呢?
1、开车时,先全回流,待操作稳定后出料。 2、在实验室设备中,研究传质影响因素。 3、工程设计中,必须知道最少板数。
最少理论板数的计算
Fenske(芬斯克)方程推导前提: 1、塔顶采用全凝器,(若采用分凝器,则分凝器为第1块塔板) 2、所有板都是理论板。
一、关键组分(Key Components)
Na=串级数(2)+分配器(1)+侧线采出
F
(0)+传热单元(2) = 5
已被指定的可调变量: (1)进料位置;(2)回流比; (3)全凝器饱和液体回流或冷凝 器的传热面积或馏出液温度。
余下的2个可调设 计变量往往用来指 定组分在馏出液和 釜液中的浓度。
两组分精馏 指定馏出液中一个组分的浓度,就确定了馏 出液的全部组成;指定釜液中一个组分的浓 度,也就确定了釜液的全部组成。
下面通过实例分别对二组分精馏和多组分精馏过 程分析进行比较。
二组分精馏实例:苯-甲苯
图3-1 二组分精馏流率、温度、浓度分布
三组分精馏实例:苯(LK)-甲苯(HK)-异丙苯
图3-2 三组分精馏流量分布 图3-3 三组分精馏温度分布
四组分精馏实例:苯-甲苯(LK)-二甲苯(HK)-异丙苯
图3-6 四组分精馏液相组成分布
⎜⎜⎝⎛
yA yB
⎟⎟⎠⎞ 2
= ⎜⎜⎝⎛
xA xB
⎟⎟⎠⎞1
代入(3-2)式:
⎜⎜⎝⎛
yA yB
⎟⎟⎠⎞1
= α1 ⎜⎜⎝⎛
xA xB
⎟⎟⎠⎞1
=
⎜⎜⎝⎛
多组分精馏和特殊精馏

核算式
对HNK:C3,iC4,nC4进行核算: C3:d0.6448,xD0.017 C4:xD0
\ 清晰分割假设对 C 3不成立,须调整
5.调整
以前面结果为初值,进行试差
设 d 0 .6 4 4 8 , 其 它 不 变 , 重 复 1 4 步
计 算 , 至 前 后 二 次 结 果 相 近 为 止 。
3. 核实清晰分割的合理性
对
于LNK
,
核
实w
,看
i
是
否xi
,W
0
核实式: fi di wi;
fd ( w )i ( w )i 1
\ wi fi 1 (wd )i
将
(d ) wi
i
h
N
m(d )代 wh
入
上
式
有:
wi
1i
fi h N m(wd )h
核算式
对 于 甲 烷 , w 9 .6 1 0 5 0 ; x W 1 .5 1 0 6
结果:第二次dC3 0.635 与第一次相近
例3-3 苯(B)-甲苯(T)-二甲苯(X)-异丙苯 (C)的混合物送入精馏塔分离,进料组成(摩尔 分数)为:zB=0.2,zT=0.3, zX=0.1, zC=0.4。相对 挥发度数据:αB=2.25,αT=1.00,αX=0.33,αC= 0.21。分离要求:馏出液中异丙苯不大于0.15%;釜 液中甲苯不大于0.3%(摩尔)。计算最少理论板和 全回流下的物料分配。
1.000 0.025 0.901 0.0167 1.000 - 1.325 0.901 1.325
故
Rm 1.306
返回
3.1.3 最少理论板数和组分分配
1、最少理论板数 全 回 流 R 时 操N , 作 N m
特殊精馏的原理

特殊精馏的原理特殊精馏是一种分离混合物中不同组分的方法,它利用了组分的物理性质在蒸发和冷凝过程中的差异。
特殊精馏在化学工业中具有广泛的应用,例如提取纯净的化学品,去除杂质,以及分离可变组分的溶剂,等等。
特殊精馏的原理主要基于液体的沸点和蒸汽压之间的关系。
不同组分的沸点不同,因此在加热过程中,组分的蒸汽压也会有所不同。
通过适当的控制温度和压力,可以使特定的组分蒸发并在冷凝器中重新变为液体。
这种过程可以重复进行,从而实现对混合物中不同组分的分离。
特殊精馏有许多不同的类型,以下是其中一些常见的特殊精馏方法:1. 水蒸气蒸馏:水蒸气蒸馏是一种常用的特殊精馏方法,特别适用于那些沸点较高的溶剂。
在水蒸气蒸馏中,混合物首先与水接触,然后加热。
水蒸气将溶剂带至冷凝器中,并在那里冷凝为液体,从而实现了与其他组分的分离。
2. 气相色谱法:气相色谱法通过将混合物分子逐一地通过柱状填充物层来分离组分。
填充物通常是一种不溶于混合物的固体,可以选择根据组分沸点和亲和性来设计填充物。
通过控制载气的流速和温度,可以使不同的组分在柱中以不同的速度通过,从而实现分离。
3. 分馏塔:分馏塔是一种常用的特殊精馏设备,特别适用于分离混合物中沸点相差较小的组分。
分馏塔通常由许多平面或圆柱体的平口塔板组成,这些塔板上有孔,材料可以通过这些孔进入下一个塔板。
在分馏塔内,混合物从底部进入,然后通过不同的塔板,然后在最顶部冷凝为纯净的液体。
不同组分的分离是通过不同的沸点和蒸汽压来实现的。
特殊精馏的原理主要涉及到沸点和蒸汽压的关系,以及控制温度和压力的重要性。
通过调整这些变量,可以根据组分之间的差异实现分离。
特殊精馏方法的选择取决于混合物中的组分种类、沸点范围和分离要求。
在实际应用中,还可能需要结合多种特殊精馏方法,以达到更高的分离效果。
总的来说,特殊精馏是一种非常有效的分离混合物中不同组分的方法,它利用了组分的物理性质差异。
通过适当的控制温度、压力和其他条件,可以实现对混合物中不同组分的分离。
化工原理 精馏 图例

全塔物料衡算--确定产品流量,浓度与进 料流量和浓度之间关系. 精馏段物料衡算—确定精馏段相邻两块 塔板之间的物料组成关系.实为精馏操作 线方程. 提馏段物料衡算—确定提馏段相邻两块 塔板之间的物料组成关系.实为提馏操作 线方程.
例题
每小时将15000kg含苯40%(质量,下同) 和甲苯60%的溶液,在连续精馏塔中进行 分离,要求釜残液中含苯不高于2%,塔 顶馏出液中苯的回收率为97.1%。试求馏 出液和釜残液的流量和组成,以摩尔流 量和摩尔分率表示。
捷算法确定理论塔板层数
平衡蒸馏
流程如下页图:单级而连续操作,溶液预热达较 高温度后,通过减压阀减压,送入蒸馏釜中被部 分气化,两相平衡后分离得产品. 只能实现部分分离. 计算项:
⑴物料衡算—得操作线方程; ⑵溶液预热温度确定; ⑶溶液平衡温度和产品浓度的确定.
平衡蒸馏例题
对某两组分理想溶液进行常压闪蒸,已 知xF为0.5(原料液中易挥发组分的摩尔 分率),若要求汽化率为60%,试求闪蒸 后平衡的气液相组成及温度。
精馏操作线方程例题3
在一连续操作的精馏塔中,分离正戊烷正己烷。进料温度为20℃,进料组成为 0.4,馏出液组成为0.95,塔釜组成为 0.95,釜液组成为0.05,上述组成均为 正己烷的摩尔分率。精馏段每层塔板下 降液体的流量为馏出液流量的1.6倍(摩 尔比),试写出提馏操作线方程
精馏操作线方程例题4
气液平衡方程(去除 下标):
x y 1 ( 1) x
相图说明
相图t-x-y:两线三区五状态.
相图x-y:实质是气液平衡方程的曲线表 达.
强调—本章所有浓度,溶液量表示全部用 摩尔分率和摩尔量.
武汉理工大学 化工原理实验 特殊精馏
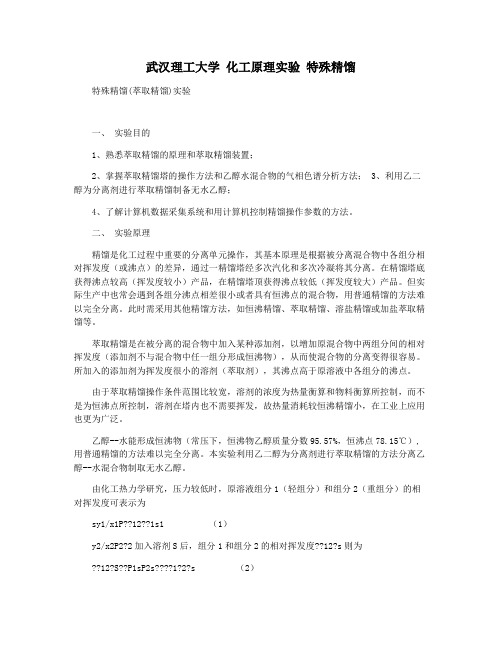
武汉理工大学化工原理实验特殊精馏特殊精馏(萃取精馏)实验一、实验目的1、熟悉萃取精馏的原理和萃取精馏装置;2、掌握萃取精馏塔的操作方法和乙醇水混合物的气相色谱分析方法;3、利用乙二醇为分离剂进行萃取精馏制备无水乙醇;4、了解计算机数据采集系统和用计算机控制精馏操作参数的方法。
二、实验原理精馏是化工过程中重要的分离单元操作,其基本原理是根据被分离混合物中各组分相对挥发度(或沸点)的差异,通过一精馏塔经多次汽化和多次冷凝将其分离。
在精馏塔底获得沸点较高(挥发度较小)产品,在精馏塔顶获得沸点较低(挥发度较大)产品。
但实际生产中也常会遇到各组分沸点相差很小或者具有恒沸点的混合物,用普通精馏的方法难以完全分离。
此时需采用其他精馏方法,如恒沸精馏、萃取精馏、溶盐精馏或加盐萃取精馏等。
萃取精馏是在被分离的混合物中加入某种添加剂,以增加原混合物中两组分间的相对挥发度(添加剂不与混合物中任一组分形成恒沸物),从而使混合物的分离变得很容易。
所加入的添加剂为挥发度很小的溶剂(萃取剂),其沸点高于原溶液中各组分的沸点。
由于萃取精馏操作条件范围比较宽,溶剂的浓度为热量衡算和物料衡算所控制,而不是为恒沸点所控制,溶剂在塔内也不需要挥发,故热量消耗较恒沸精馏小,在工业上应用也更为广泛。
乙醇--水能形成恒沸物(常压下,恒沸物乙醇质量分数95.57%,恒沸点78.15℃),用普通精馏的方法难以完全分离。
本实验利用乙二醇为分离剂进行萃取精馏的方法分离乙醇--水混合物制取无水乙醇。
由化工热力学研究,压力较低时,原溶液组分1(轻组分)和组分2(重组分)的相对挥发度可表示为sy1/x1P??12??1s1 (1)y2/x2P2?2加入溶剂S后,组分1和组分2的相对挥发度??12?s则为??12?S??P1sP2s????1?2?s (2)TSsP2s?�C―加入溶剂S后,三元混合物泡点下,组分1和组分2的饱式中?P1TS和蒸汽压之比;??1?2?s―加入溶剂S后,组分1和组分2的活度系数之比。
- 1、下载文档前请自行甄别文档内容的完整性,平台不提供额外的编辑、内容补充、找答案等附加服务。
- 2、"仅部分预览"的文档,不可在线预览部分如存在完整性等问题,可反馈申请退款(可完整预览的文档不适用该条件!)。
- 3、如文档侵犯您的权益,请联系客服反馈,我们会尽快为您处理(人工客服工作时间:9:00-18:30)。
9.5双组分精馏的设计型计算9.5.1理论板数的计算 9.5.2 回流比的选择9.5.3双组分精馏过程的其他类型(1)直接蒸汽加热若待分离的混合液为水溶液,且水是难挥发组分,釜液接近于纯水,这时可采用如上图所示的直接加热方式,把加热水蒸汽直接通入塔釜,以省掉造价昂贵的再沸器。
与间接蒸汽加热精馏塔相比,直接蒸汽加热时精馏操作线、q 线均相同,但是由于塔釜中通入蒸汽直接加热,提馏段物料衡算及全塔物料衡算关系变了。
① 全塔物料衡算总物料衡算 W D S F +=+ 易挥发组分衡算 W Wx Dx S Fx +=⨯+D F 0 式中 S ——直接加热蒸汽流率,kmol/h ; W ——直接蒸汽加热时釜液流率, kmol/h ; W x ——直接蒸汽加热时釜液组成,摩尔分率。
其它符号意义与间接蒸汽加热相同。
② 提馏段操作线方程直接蒸汽加热时也应满足恒摩尔流假设,故有S V =,W L =。
根据物料衡算可导出提馏段操作线方程为W W m x S W x S W x V L x V L y -=-=+1如图所示,直接蒸汽加热时提馏段操作线通过横轴上的点(0,W x )及q 线与精馏段操作线的交点(q q y x ,)两点,因此也可用两点求直线的方法求提馏段操作线方程:*W*W00x x y x x y q q --=--用上式求直接蒸汽加热时提馏段操作线方程比较方便,问题归结为两操作线交点坐标(q q y x ,)如何求。
因为q 线及精馏段操作线均与间接蒸汽加热时相同,所以仍可用前述方法求q x 、q y 值。
若用式求,则需根据F q D R F q V V S )1()1()1(--+=--==,qF L L W +='=*等关系导出可利用题给已知条件的形式才能求解。
(2)多股进料两种成分相同但浓度不同的料液可在同一塔内进行分离,两股料液应分别在适当位置加入塔内。
整个精馏塔可分成三段,每段均可按图中所示符号用物料衡算推出其操作线方程。
① 操作线方程Ⅰ段 11D+++=R x x R RyⅡ段 V x F Dx x V L y F ''-+''''=11D 式中 1111F q RD F q L L +=+=''1111)1()1()1(F q D R F q V V --+=--=''特别,当1F 为泡点进料)1(1=q ,则Ⅱ段操作线可写成1/1/11F D 1+-+++=R DF x x x R D F R yⅢ段 W x WL W x WL L y -'--''=式中 2211211122F q F q RD F q F q L F q L L ++=++=+''='D F F W -+=21无论何种进料热状况,操作线斜率必有(Ⅲ) (Ⅱ) (Ⅰ)。
② 全塔物料衡算总物料衡算 W D F F +=+21 易挥发组份衡算 WD 2F 21F 1Wx Dx x F x F +=+联立以上两式可得WD W 1F WD W 2F 121x x x x x x x x F F F D --+--=回收率 2F 121F D 12F 21F 1D)/()/(x F F x x F D x F x F Dx+=+=η③ q 线方程q 线方程数与进料股数相同,两股进料q 线方程有两个,即1111F 11---=q x x q q y ,1122F 22---=q x x q q y④最小回流比m in R回流比R 减小,三条操作线均向平衡线靠拢。
当R 减小至某个值时,挟点可能出现在Ⅰ-Ⅱ两段操作线的交点1e 处,也可能出现在Ⅱ-Ⅲ两段操作线的交点2e 处。
对非理想性很强的物系,挟点也可能出现在某个中间位置,先出现挟点时的回流比为最小回流比。
(3)侧线出料如下图所示,此时操作线数目314=-=,因而整个精馏塔可分成三段,每段均可按图中所示符号用物料衡算推出其操作线方程。
以下仅讨论侧线抽出的产品2D x 为泡点液体的情况。
操作线方程Ⅰ段 11D+++=R x x R RyⅡ段 1)/(1/2D 121D 12++++-=R x D D x x R D D R y (泡点采出)以上两式中R 定义为1/D L R =。
Ⅲ段 W x WL W x WL L y -'--''=式中 qF D RD qF D L qF L L +-=+-=+''='21221D D F W --=有侧线出料时操作线斜率通常Ⅱ、Ⅰ,在最小回流比m in R 时,挟点一般出现在q 线与平衡线交点处。
9.6 双组分精馏的操作型计算9.6.1 精馏过程的操作型计算(1)操作型计算的命题:此类计算的任务是在设备(精馏段板数及全塔理论板数)已定的条件下,由指定的操作条件预计精馏操作的结果。
计算所用的方程与设计时相同,此时的已知量为:全塔总板数N 及加料板位置(第m 块板);相平衡曲线或相对挥发度;原料组成F x 与热状态q ,回流比R ;并规定塔顶馏出液的采出率FD 。
待求的未知量为:精馏操作的最终结果——产品组成w D ,x x 及逐板的组成分布。
操作型计算的特点:① 由于众多变量之间的非线形关系,使操作型计算一般均须通过试差(迭代),即先假设一个塔顶(或塔底)组成,再用物料衡算及逐板计算予以校核的方法来解决。
② 加料板位置(或其它操作条件)一般不满足最优化条件。
下面以两种情况为例,讨论此类问题的计算方法。
回流比增加对精馏结果的影响设某塔的精馏段有)1(-m 块理论板,提馏段为)1(+-m N 块板,在回流比R '操作时获得塔顶组成D x '与釜液组成wx '(参见图9-43a )。
现将回流比加大至R ,精馏段液气比增加,操作线斜率变大;提馏段气液比加大,操作线斜率变小。
当操作达到稳定时馏出液组成D x 必有所提高,釜液组成w x 必将降低,如图(9-43b )所示。
定量计算方法是:先设定某一w x 值,可按物料衡算式求出FD F Dx x x D )1(w F --=然后,自组成为D x 起交替使用精馏段操作线方程111+++=+R x x R R y D n n 及相平衡方程nnn y y x )1(--∂=α进行m 次逐板计算,算出第1至m 板的气、液组成。
直至算出离开加料板液体的组成m x 。
跨过加料板以后,须改用提馏段操作线方程w 1)1()1(1)1()1(x D F q R D F x D F q R DF qR y n n --+----++=+及相平衡方程进行m N -次逐板计算,算出最后一块理论板的液体组成N x 。
将此N x 值与所假设的w x 值比较,两者基本接近则计算有效,够则重新试差。
必须注意,在馏出液流率FD 规定的条件下,藉增加回流比R 一提高D x 的方法并非总是有效:a .D x 的提高受精馏段塔板数即精馏塔分离能力的限制。
对一定板数,即使回流比增至无穷大(全回流)时,D x 也有确定的最高极限值;在实际操作的回流比下不可能超过此极限值。
b .D x 的提高受全塔物料衡算的限制。
加大回流比可提高D x ,但其极限值为DFx x D F=。
对一定塔板数,即使采用全回流,Dx 也只能某中程度趋近于此极限值。
如DFx x D F=的数值大于1,则D x 的极限值为1。
此外,加大操作回流比意味着加大蒸发量与冷凝量。
这些数值还将受到塔釜及冷凝器的传热面的限制。
(2)进料组成变动的影响一个操作中的精馏塔,若进料组成F x 下降至Fx ',则在同一回流比R 及塔板数下塔顶馏出液组成D x 将下降为D x ',提馏段塔釜组成也将由w x 降至w x '。
进料组成变动后的精馏结果D x '、wx '可用前述试差方法确定。
图9-44表示进料组成变动后操作线位置的改变。
此时欲要维持原馏出液组成D x 不变,一般可加大回流或减少采出量FD。
值得注意,以上两种情况的操作型计算中,加料板位置不一定是最优的。
图9-43b 说明了这一问题。
9.6.2 精馏塔的温度分布和灵敏板(1)精馏塔的温度分布溶液的泡点与总压及组成有关。
精馏塔内各块塔板上物料的组成及总压并不相同,因而 塔顶至于塔底形成某种温度分布。
在加压或常压精馏中,各板的总压差别不大,形成全塔温度分布的主要原因是各板组成不同。
图9-45a 表示各板组成与温度的对应关系,于是可求出各板的温度并将它标绘在图9-45b 中,即得全塔温度分布曲线。
减压精馏中,蒸汽每经过一块塔板有一定压降,如果塔板数较多,塔顶与塔底压强的差别与塔顶绝对压强相比,其数值相当可观,总压降可能是塔顶压强的几倍。
因此,各板组成与总压的差别是影响全塔温度分布的重要原因,且后一因素的影响往往更为显著。
(2)灵敏板一个正常操作的精馏塔当受到某一外界因素的干扰(如回流比、进料组成发生波动等),全塔各板的组成发生变动,全塔的温度分布也将发生相应的变化。
因此,有可能用测量温度的方法预示塔内组成尤其是塔顶馏出液的变化。
在一定总压下,塔顶温度是馏出液组成的直接反映。
但在高纯度分离时,在塔顶(或塔底)相当高的一个塔段中温度变化极小,典型的温度分布曲线如图9-46所示。
这样,当塔顶温度有了可觉察的变化,馏出液组成的波动早已超出允许的范围。
以乙苯-苯乙烯在8kPa下减压精馏为例,当塔顶馏出液中含乙苯由99.9%降至90%时,泡点变化仅为0.7℃。
可见高纯度分离时一般不能用测量塔顶温度的方法来控制馏出液的质量。
仔细分析操作条件变动前后温度分别的变化,即可发现在精馏段或提馏段的某些塔板上,温度变化量最为显著,或者说,这些塔板的温度对外界干扰因素的反映最灵敏,故将这些塔板称之为灵敏板。
将感温元件安置在灵敏板上可以较早觉察精馏操作所受到的干扰;而且灵敏板比较靠近进料口,可在塔顶馏出液组成尚未产生变化之前先感受到进料参数的变动并即使采取调节手段,以稳定馏出液的组成。
9.7 间歇精馏9.7.1 间歇精馏过程的特点当混合液的分离要求较高而料液品种或组成经常变化时,采用间歇精馏的操作方式比较灵活机动。
从精馏装置看,间歇精馏与连续精馏大致相同。
作间歇精馏时,料液成批投入精馏釜,逐步加热气化,待釜液组成降至规定值后将其一次排出。
由此不难理解,间歇精馏过程具有如下特点:①间歇精馏为非定态过程。
在精馏过程中,釜液组成不断降低。
若在操作时保持回流比不变,则馏出液组成将随之下降;反之,为使馏出液组成保持不变,则在精馏过程中应不断加大回流比。
为达到预定的要求,实际操作可以灵活多样。