熔铸生产过程记录表
熔铸车间工艺操作规程

熔铸车间工艺操作规程(总8页)-CAL-FENGHAI.-(YICAI)-Company One1-CAL-本页仅作为文档封面,使用请直接删除铝镁业有限公司操作规程文件名称:熔铸车间工艺操作规程文件编号:HDQ/J101版本:A版受控状态:实施日期:2015年5月1日编制:审核:批准:文件更改记录1、目的通过确定圆铸锭生产过程的工艺要求和操作方法,以确保所生产的圆铸锭符合内控质量标准的要求,最大限度地实现熔铸车间生产活动的高效率、高成品率。
2、适用范围适用于6000系铝合金,外径为Ф85-Ф178圆铸锭的生产作业活动。
3、职责:3.1 炉前班长对合金的化学成份是否合格负责。
3.2 熔炼工对熔炼温度是否符合工艺要求,金属烧损率是否超标,油耗是否达到节能要求,同时对灰渣中金属铝是否回收干净,是否降低环境污染负责。
3.3 铸造工对铸造温度是否符合工艺要求,铸锭晶粒度是否达到1级标准,铸锭直径、弯曲度和表面质量是否符合内控质量标准要求负责。
3.4 锯切工对圆铸锭的定尺长度,切斜度和产品标识负责。
4、工艺操作规程:4.1 熔铸生产流程图配料→装炉→熔炼→扒渣→合金化→精炼→扒渣→静置→细化→铸造▲→锯切→交付▲表示特殊过程4.2 配料(责任人:带班主任)4.2.1 配料前准备4.2.1.1 车间主任以填写《铸棒生产计划单》的形式对各班班长下达生产任务,规定合金牌号、铸棒规格、生产时间和熔炉编号。
4.2.1.2 到限根据生产计划单准备备料及相关工具等。
4.2.2 原铝锭的使用:不同品位的原铝锭,适合于配制不同牌号的合金,在配制合金时,应按表1的规定选用原铝锭。
表1注:纯度高的铝锭可以代替纯度低的铝锭使用,但反之则不行。
4.2.3 配料计算的有关规定a)镁:按镁锭含镁量为100%计算。
b)铝硅中间合金:规定理论含硅量为12%,每批硅种进厂应取三个试样化验含硅量,取其算出平均值为计算依据。
c) 铜、锌:按含铜、含锌100%计算。
熔铸车间开会记录

熔铸车间开会记录熔铸车间会议记录会议主题:提高熔铸车间生产效率与品质管理会议时间:XXXX年XX月XX日会议地点:熔铸车间会议室主持人:XXX(熔铸车间经理)与会人员:熔铸车间全体员工会议内容:一、会议开场1.主持人对与会员工表示欢迎,并简要介绍本次会议的目的和议程。
二、车间生产效率1.主持人介绍近期车间生产效率下降的问题,提出存在的主要原因,并邀请与会员工发表意见,共同探讨提高生产效率的措施。
2.与会员工纷纷发表意见,主要包括:(1)设立目标管理制度,明确生产任务和目标,定期进行检查和评估;(2)加强设备维护,及时进行检修和保养,防止设备故障对生产造成影响;(3)加强生产流程管理,优化产品生产流程,减少制造中的浪费;(4)改进员工培训和技能提升,提高员工的生产能力和技术水平;(5)定期开展生产效率评估和改进工作,并在沟通中及时解决问题。
三、品质管理1.主持人对车间近期的品质问题进行了分析,并说明品质问题给车间带来的不良影响。
2.与会员工就品质管理进行了深入的讨论,提出了以下意见:(1)加强原料采购管理,选择合格的供应商,并建立质量跟踪机制;(2)严格执行工艺流程,加强产品检验,确保每一个产品都符合质量要求;(3)加强员工培训,提高员工对产品品质的认识和重视程度;(4)建立品质改进机制,对已经发现的问题进行深入分析,并采取有效的改进措施;(5)主动接受上级和客户的意见和反馈,及时处理投诉,并采取措施避免类似问题的再次发生。
四、总结和达成共识1.主持人总结了会议的内容,并强调车间提高生产效率和品质管理的重要性。
2.与会员工纷纷表示愿意积极参与节约原材料、提高生产效率和加强品质管理的活动,并提出自己的建议和承诺。
3.主持人对与会员工的积极态度表示肯定,并承诺将会将会议的成果整理,制定相应的措施和计划,并将有效执行并监督落实。
会议结束时间:XX时XX分记录人:XXX(熔铸车间记录员)备注:根据会议内容进行了详尽的记录,待会议纪要完成后,将会以电子邮件的形式发送给所有与会人员,并抄送至相关部门。
熔铸车间工艺流程
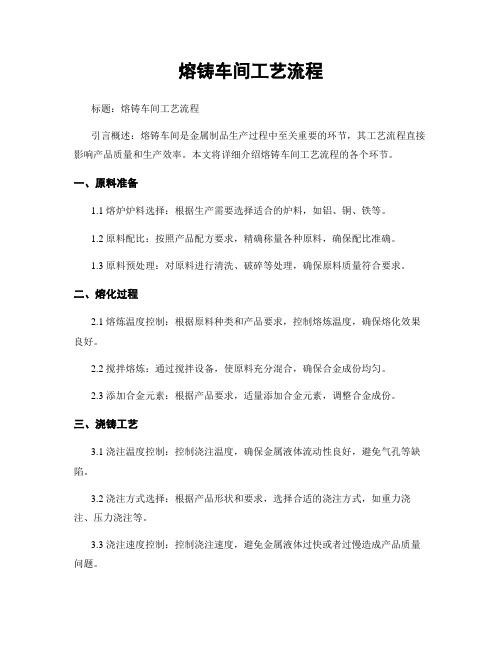
熔铸车间工艺流程标题:熔铸车间工艺流程引言概述:熔铸车间是金属制品生产过程中至关重要的环节,其工艺流程直接影响产品质量和生产效率。
本文将详细介绍熔铸车间工艺流程的各个环节。
一、原料准备1.1 熔炉炉料选择:根据生产需要选择适合的炉料,如铝、铜、铁等。
1.2 原料配比:按照产品配方要求,精确称量各种原料,确保配比准确。
1.3 原料预处理:对原料进行清洗、破碎等处理,确保原料质量符合要求。
二、熔化过程2.1 熔炼温度控制:根据原料种类和产品要求,控制熔炼温度,确保熔化效果良好。
2.2 搅拌熔炼:通过搅拌设备,使原料充分混合,确保合金成份均匀。
2.3 添加合金元素:根据产品要求,适量添加合金元素,调整合金成份。
三、浇铸工艺3.1 浇注温度控制:控制浇注温度,确保金属液体流动性良好,避免气孔等缺陷。
3.2 浇注方式选择:根据产品形状和要求,选择合适的浇注方式,如重力浇注、压力浇注等。
3.3 浇注速度控制:控制浇注速度,避免金属液体过快或者过慢造成产品质量问题。
四、冷却处理4.1 自然冷却:待产品彻底凝固后,进行自然冷却,确保产品结构稳定。
4.2 退火处理:对特殊要求的产品进行退火处理,提高产品的力学性能。
4.3 表面处理:对产品进行表面清理、抛光等处理,提高产品外观质量。
五、成品检验5.1 外观检验:对产品外观进行检查,确保无明显缺陷。
5.2 尺寸检验:测量产品尺寸,确保符合设计要求。
5.3 化学成份检验:通过化学分析仪器检测产品合金成份,确保合金成份准确。
结论:熔铸车间工艺流程是金属制品生产中不可或者缺的环节,惟独严格按照工艺流程进行操作,才干生产出高质量的产品。
通过对每一个环节的详细控制和检验,可以确保产品质量和生产效率的提升。
熔铸工艺流程图

铸轧、铸造的相关知识——肖立隆(晟通技术总顾问)1 熔铸工艺流程图:电解铝液调温调成分交货2 炉子准备:烘炉烘炉曲线升温过程中不损害炉子寿命3 炉料要求和加料顺序: 炉料要求: 无吸水,无油污加料顺序:废料 中间合金 铝锭 化平后铜、锌等 镁 添加剂 取样4 熔化: Q=dT C TM ⎰201+L+dT C TTM⎰2C 1——固体比热:0.215卡/克0C ; C 2——液体比热:0.198卡/克0C L ——熔化潜热:94.6卡/克0C 黑度:0.25 熔化时的增气反应:铝和水发生反应: 2Al+3H 2O=Al 2O 3+6[H]火焰炉燃烧时发反应: C m H n +O 2 CO+CO 2+H 2O 6 熔体中氢的平衡溶解度:S=K 2H P7 影响熔体含气量的因素: 1) 合金元素影响:V MeO / V Me > 1 < 1 = 1 α 氧化铝膜密度3.47克/㎝3,致密,可防止继续氧化:γ 氧化铝膜表面疏松,存在φ50—100×10-10 m 的小孔,在熔炼温度下含有1—2%的水分;在9000C 以上时,γ完全变成α氧化铝,密度增到3.97克/㎝3,体积收缩13%,氧化铝易被搅入铝液中。
2) 熔体温度影响: 3) 熔体停留时间影响: 4) 空气湿度影响: 8 熔化时的造渣反应:有关化学元素的氧化物生成自由能几种氧化物和熔融铝可能发生的化学反应式:3SiO2 + 4Al = 2Al2O3+ 3Si 3FeO + 2Al = Al2O3+ 3FeCr2O3+ 2Al = Al2O3+ 2Cr SiO2+ 2Mg = 2MgO + Si9 电解铝液的情况:温度高:900——9300C炉内停留时间长:24小时以上含气量高,氧化夹渣多,结晶核心钝化10 调成分调温:1)加入废料、中间合金、铝锭; 2)加入铜、锌等其他金属3)加入镁和其他添加剂; 4)快速升温5) 取样分析11 精炼:基本原理:1)吸附净化:依靠精炼剂产生的吸附作用达到去氧化夹杂和气体的目的。
综合实验一 铝合金制备

综合实验一铝合金制备、加工及改性实验1.1 铝合金的熔炼、铸锭与固溶-时效处理实验指导书实验学时:4 实验类型:综合、设计型前修课程名称:材料工程基础适用专业:材料类本科生一实验目的掌握铝合金熔化的基本原理,并应用在熔化的实践中。
熔炼是使金属合金化的一种方法,它是采用加热的方式改变金属物态,使基体金属和合金化组元按要求的配比熔制成成分均匀的熔体,并使其满足内部纯洁度,铸造温度和其他特定条件的一种工艺过程。
熔体的质量对铝材的加工性能和最终使用性能产生决定性的影响,如果熔体质量先天不足,将给制品的使用带来潜在的危险。
因此,熔炼又是对加工制品的质量起支配作用的一道关键工序。
而铸造是一种使液态金属冷凝成型的方法,它是将符合铸造的液态金属通过一系列浇注工具浇入到具有一定形状的铸模(结晶器)中,使液态金属在重力场或外力场(如电磁力、离心力、振动惯性力、压力等)的作用下充满铸模型腔,冷却并凝固成具有铸模型腔形状的铸锭或铸件的工艺过程。
铝合金的铸锭法有很多,根据铸锭相对铸模二实验内容铝铜合金的熔炼工艺流程铝合金铸锭方法连续铸造法无模铸造(无接触铸造):电磁铸造等三实验要求严格控制熔化工艺参数和规程1. 熔炼温度熔炼温度愈高,合金化程度愈完全,但熔体氧化吸氢倾向愈大,铸锭形成粗晶组织和裂纹的倾向性愈大。
通常,铝合金的熔炼温度都控制在合金液相线温度以上50~100℃的范围内。
从图1的Al-Cu相图可知,Al-5%Cu的液相线温度大致为660~670℃,因此,它的熔炼温度应定在710(720)℃~760(770)℃之间。
浇注温度为730℃左右。
图1 铝铜二元状态图2.熔炼时间熔炼时间是指从装炉升温开始到熔体出炉为止,炉料以固态和液态形式停留于熔炉中的总时间。
熔炼时间越长,则熔炉生产率越低,炉料氧化吸气程度愈严重,铸锭形成粗晶组织和裂纹的倾向性愈大。
精炼后的熔体,在炉中停留愈久,则熔体重新污染,成分发生变化,变形处理失效的可能性愈大。
熔铸法制备ZL104铝合金
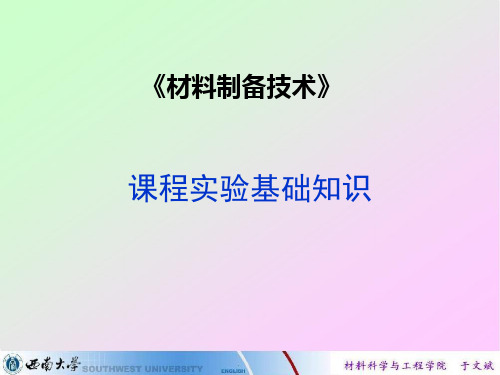
注意事项
• • 1.操作前应由指导教师讲解设备、仪器 等的使用和安全知识。 2.学生以分组进行操作,可分为准备、 熔炼、浇铸等几组。
• 备注:炉料计算依据 • ZL104成分:Si 9%;Mg 0.3%;Mn 0.45% • 元素烧损: 5% 20% 5%
• 熔炼重量:
1000g
• 原料:硅铝明Si 12%;Al-10%Mn中间合金。
• 6.精炼处理:调整温度到710-730C,加 入1-1.5﹪氯化锌精炼除气除渣,搅拌溶液 5-15分钟,然后加入镁锭。 • 备注:取样与未精炼对比。
实验准备:
设备仪器:熔化电炉,温控仪,电阻烘箱。
原辅材料:铝锭,硅铝锭,镁锭,铝锰合金,氯
化锌,氯化钠,氟化钠,氯化钾,冰晶石 Na3AlF6,氧化锌,水玻璃等。 装置工具:坩埚,锭模,浇包,钟罩等。 其它:安全用品,记录表等。
Hale Waihona Puke 实验过程1. 配制熔剂: (1)精炼剂:氯化锌托盘400-500C烘烤3-4h。 (2)变质剂:配制钠盐变质剂。配方如下: 原料 氯化钠 氯化钾 氟化钠 冰晶石 用量﹪ 50 10 30 10 55 15 30 称量后机械混合,电阻烘箱200-250oC烘烤2-4h 装干燥瓶备用。
《材料制备技术》
课程实验基础知识
一、铝合金的熔炼与铸造
• 实验目的: • 1.加深对课堂内容的理解,增加对材料设 计和制备的认识。 • 2.掌握铝合金铸锭的生产工艺和过程。 • 3.学会使用材料制备研究用的常用设备和 仪器装置。
• 实验要求: • 1.学生进行实验前应根据课堂教学内容制 定实验方案,要尽可能详细准确,并交指导 教师审核修改。 • 2.操作前应由指导教师讲解设备和仪器的 作用和用法,注意事项和安全事项,并做好 安全防护。 • 3.认真记录实验所用的原材料、设备、仪 器、装置和工具、实验过程、工艺参数和实 验结果,提交实验报告。
工艺检查记录表

检查结果:(主要问题点及整改)
内容 部门
问题描述
问题点 图片
1.熔铸车间配料 生产记录在做 假,记录全部是 A356的重量,实 际废轮也在加
2.5#熔炼炉气 氛温度要求500 ~1000℃,实际 46℃,铝水温度 仪表显示284 ℃,热电偶处陶 瓷已坏需更换
3.灭火器4月份 没有点检
责任人
完成日期
复查情况及 时间
扣款
已完成
4.打磨后清洗设 备点检卡记录不 及时,有些班都 很长时间没有记 录了
《设备操作 规程》的要
求
5.热水洗温度超 出工艺范围,要 求50~60℃,实 际显示76℃
《前处理作 业指导书》 操作内容第5
点前处理
1.以上检查不符合项各责任部门在5月2日前完成整改计划,并提交。 2.以上通报,希各相关部门引以为戒,踏踏实实做好每项工作,问题点及时整改。
工艺纪律检查通报
不符合 条款
《记录控制 程序》
纠正措施
责任人
完成日期
复查情况及 时间
扣款
没有整改
《投料配比 作业指导书 》操作内容 第4点温度控
制
已完成
《消防安全 规定》
已完成
第 1 页,共 5 页
内容 部门
问题描述
4.23#机生产的 5460 5#模没有 工艺卡和设备点 检卡
5.5#熔化炉打 印温度处合格证 已过期,需更换
检测 《X光检查作 业指导书》 操作内容第8 点产品叠放
(最高 1.7m)
第 2 页,共 5 页
没有整改
没有整改
水位是到了 ,但水需更
换太混了
已完成
内容 部门
问题描述
9.5#熔炼炉温 度记录打印纸4 月25日已打印 完,需更换
铝型材熔铸工艺规程

铝型材熔铸工艺规程——熔铸精炼除气氮气工业要求1 主题与范围本规程规定了熔铸生产工艺技术要求及操作规范.本规程适用于挤压用铝的熔炼,铸造,均质生产.2 生产前的准备工作2.1检查贮油罐的油位是否达到最低值,燃烧器,油枪是否正常,炉门开启是否灵活,炉门的密封是否良好。
2.2检查铸造平台,供水系统是否正常。
A)检查铸造平台保温材料,结晶器,引锭头,流槽等是否完好,安装好陶瓷过滤板或过滤布。
B)每次铸造前必须试水,通入铸造机正常铸造水量,检查结晶器出水环喷水角度是否良好,水帘的成形情况及溢水孔有否漏水,溢水孔有漏绝不能铸造。
若有堵塞,应立即拆洗,清除杂物。
C)铸造前引锭座必须上升至正常起动位置并调好水平。
D)若铸造机长时间不用或由于天气潮湿造成引锭头生锈,在铸造前全部引锭头必须涂一次猪油。
E)铸造用水必须经过小于1MM过滤,铸造用水的水温应低于40摄氏度。
2.3熔炼炉停炉达一个月以上或者新制的炉子,必须烘炉后才能使用。
2.3.1烘炉首先打开炉门与放水口用木柴点火烘炉,防止大明火,根据炉内温度与火的大小随时调整炉门开启的大小,控制在150摄氏度以下,升温的速度不大于10摄氏度/H;两天后将炉温按10摄氏度升到250摄氏度,无水汽蒸发后,用一台小燃烧器加热烘,四天后用两台小燃烧器热烘,温升按15摄氏度/H升至500摄氏度,五天后升至600摄氏度,六天后将温度按16℃/h的速度升至800℃,恒温10小时以上,烘炉终止。
2.4备料2.4.1合金的配比按HD/QB-2004《内部质量控制标准》执行。
2.4.2熔炼工根据配料员填写的《配料、熔炼、铸造及化学分析结果记录表》,作为配料指令,将铝锭、镁锭、铝硅合金(或金属硅)、金属添加剂、型材废料、挤压压余、熔铸锯切头、接料斗中的大块铝块、复熔铝锭等计量后分批运上炉前操作平台,并做好相应记录。
2.4.3覆盖剂、精炼剂、打渣剂烘干备用。
2.4.4各种炉料不准淋雨受潮或与其它料混放,不准混杂其它金属。
- 1、下载文档前请自行甄别文档内容的完整性,平台不提供额外的编辑、内容补充、找答案等附加服务。
- 2、"仅部分预览"的文档,不可在线预览部分如存在完整性等问题,可反馈申请退款(可完整预览的文档不适用该条件!)。
- 3、如文档侵犯您的权益,请联系客服反馈,我们会尽快为您处理(人工客服工作时间:9:00-18:30)。
检验项目
技术要求
检查数量
实测数据
自检判定
确认人
成形良好,表面粗糙度均
1外观
匀。无缩松、多料、缺料等
全检
1件有浇不足,
其它符合要合格
***
求
铸造缺陷。全检。
2
冒口咼度
>35mm
5%
38,40,42,39,37
合格
***
3
顶出销痕迹咼度
0±0.5mm
5%
0.2,0.23,0.2,0.25,0.2
合格
***
4
燃烧室直径
062±0.35mm
1%
62.08,62.10,62.05,62.12
合格
***
5
燃烧室中心距
216+0.3mm
2%
216.12,216.08
合格
***
6
燃烧室粗糙度
RБайду номын сангаас25
全检
符合要求
合格
***
检验结论:
废品1件(编号:101102TR024),其它合格
检验员/日期:
***
黄色:熔炼工填写
熔铸批次号
101102
模号
1
天然气压力
4.5KPa
配(加)料记录
时间
原材料名称
配料重料
时间
原材料名称
配料重料
8:
00
铝锭、
旧料
200Kg
15:15
铝锭、
旧料
200Kg
11:
25
铝锭、
旧料
250Kg
13:
08
铝锭、
旧料
250Kg
工艺参数记录
时间
熔炼
熔剂
静置
化学
含气 弯折角 铸态试 浇注
浇注 留模 确认人
熔铸生产过程记录表
编号:
生产 日期
10.11.2
材料
牌号
ZL101
班
次
白
产品名称 及型号
462汽缸
盖
生产数
11
0
操作者
******
砂芯批次号
1
2
3
4
5
6
7
8
9
101101
101101
101101
101030
101029
101101
101101
101101
1011001
101031
101030
铝锭批次号101027
蓝色:浇注工填写
绿色:检验员填写
时间
温度C
用量Kg时间min
成分
量 弓折用 棒强度温度c
时间s时间s确认人
135〜
8:25
780
1
25
合格
合格
合格
720
7 150***
140
140〜
11:05
762
1
23
合格
合格
合格
712
7 150***
145
生产过程异常记录
时间
异常情况
处置记录
8:50
断左油道
修复定位芯头间隙,
9:02恢复。
检验记录