电镀填孔工艺影响因素
电镀质量六大影响因素

电镀质量六大影响因素影响电镀质量的因素很多,包括镀液的各种成分以及各种电镀工艺参数,下面讨论其中的主要因素。
(l) pH值的影响镀液中的pH值影响氢的放电电位、碱性夹杂物的沉淀,还影响络合物或水化物的组成以及添加剂的吸附程度。
但是,对各种因素的影响程度一般不可预见。
最佳的pH值往往要通过试验决定。
在含有络合剂离子的镀液中,pH值可能影响存在的各种络合物的平衡,因而必须根据浓度来考虑。
电镀过程中,若pH值增大,则阴极效率比阳极效率高,pH值减小则反之。
通过加入适当的缓冲剂可以将pH值稳定在一定的范围。
(2)添加剂的影响镀液中的光亮剂、整平剂、润湿剂等添加剂能明显改善镀层组织。
这些添加剂有无机和有机之分,无机添加剂在电解液中形成高分散度的氢氧化物或硫化物胶体,吸附在阴极表面阻碍金属析出,提高阴极极化作用。
有机添加剂多为表面活性物质,它们会吸附在阴极表面形成一层吸附膜,阻碍金属析出,因而提高阴极极化作用。
另外,某些有机添加剂在电解液中形成胶体,会与金属离子络合形成胶体一金属离子型络合物,阻碍金属离子放电而提高阴极极化作用。
(3)电流密度的影响任何电镀液都必须有一个能产生正常镀层的电流密度范围。
当电流密度过低时,阴极极化作用较小,镀层结晶粗大,甚至没有镀层。
随着电流密度的增加,阴极极化作用也随着增加,镀层晶粒越来越细。
当电流密度过高,超过极限电流密度时,镀层质量开始恶化,甚至出现海绵体、枝晶状、“烧焦”及发黑等。
电流密度的上限和下限是由电镀液的本性、浓度、温度和搅拌等因素决定的。
一般情况下,主盐浓度增大,镀液温度升高,以及有搅拌的条件下,可以允许采用较大的电流密度。
(4)电流波形的影响电流波形的影响是通过阴极电位和电流密度的变化来影响阴极沉积过程的,它进而影响镀层的组织结构甚至成分,使镀层性能和外观发生变化。
实践证明,三相全波整流和稳压直流相当,对镀层组织几乎没有什么影响,而其他波形则影响较大。
例如,单相半波会使镀铬层产生无光泽的黑灰色;单相全波会使焦磷酸盐镀铜及铜锡合金镀层光亮。
盲孔填孔不良分析

电镀盲孔填孔不良分析目前多阶HDI板的层间互连大多采用微孔叠孔及交错连接方式设计,一般采用电镀铜填孔方式进行导通,但电镀填盲孔技术与传统电镀有一定差别,且在工艺参数,流程设计,设备方面更有严格要求,填孔过程中出现空洞、凹陷、漏填也是厂内控制的难点,下面将厂内填孔缺陷进行分析,提供些填孔不良的思路;一、填孔不良分析:针对厂内填孔不良切片分析分类,统计如下:序号缺陷分类不良图片不良比例1 凹陷75%2 漏填15%3 空洞5%二、原因分析:通过切片分析确认,不良主要为凹陷、漏填、空洞,其中凹陷、漏填比例较高,其次为空洞,现针对厂内填孔不良可能原因进行分析.2.1添加剂浓度失调:盲孔的填孔主要是通过添加剂中各组成分的协调作用、吸附差异平衡化完成,浓度失控势必会造成添加剂在盲孔内吸附平衡的破坏影响填孔效果.2.2打气喷管堵塞:填孔槽打气大小直接影响到填孔过程中孔内药水交换效果,若打气效果差必然会造成孔内药水交换导致填孔效果欠佳凹陷值偏大.2.3导电性不良:夹头或挂具损坏、飞靶和V型座接触不好,导致电流分布不均,板内电流小区域必然会出现盲孔凹陷或漏填现象.2.4填孔前微蚀异常:填孔前微蚀不足均可能导致个别盲孔孔内导电不良,孔内电阻偏高,在填孔时不利于添加剂分布导致填孔失败.2.5板子入槽时变形导致局部盲孔突起,局部盲孔漏填或凹陷.2.6泵浦吸入口漏气,必然会造成大量空气进入槽内,通过过滤泵循环过滤将起泡带入整个槽内通过气流进入盲孔,阻碍孔内药水交换导致盲孔漏填现象.三、效果验证:实验前通过对药水调整至最佳状态,检查打气管道、夹头(挂具)、打气状况,维修设备接触不良处并用稀硫酸清洗、微蚀速率控制在20—30u”,保证板为垂直状态后进行填孔测试,测试结果无异常.四、结论:通过改善前后对比可以看出:厂内填孔不良主要为药水浓度、打气、导电性、填孔前微蚀量异常及槽内有气泡导致填孔异常,当然影响盲孔填孔异常的因素还有很多,只有平时做到长期监控,细心维护设备,认真排查造成填孔不良的每一个可能因素,才能真正运用好填孔技术,解决厂内填孔异常.。
电镀控制条件及影响因素
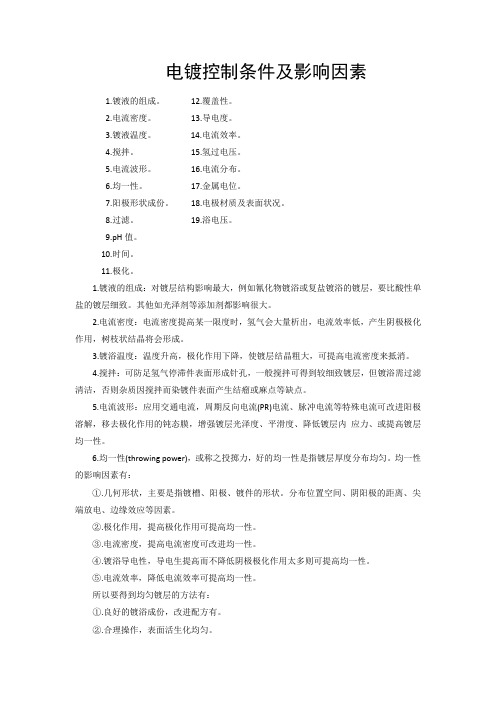
电镀控制条件及影响因素1.镀液的组成。
12.覆盖性。
2.电流密度。
13.导电度。
3.镀液温度。
14.电流效率。
4.搅拌。
15.氢过电压。
5.电流波形。
16.电流分布。
6.均一性。
17.金属电位。
7.阳极形状成份。
18.电极材质及表面状况。
8.过滤。
19.浴电压。
9.pH值。
10.时间。
11.极化。
1.镀液的组成:对镀层结构影响最大,例如氰化物镀浴或复盐镀浴的镀层,要比酸性单盐的镀层细致。
其他如光泽剂等添加剂都影响很大。
2.电流密度:电流密度提高某一限度时,氢气会大量析出,电流效率低,产生阴极极化作用,树枝状结晶将会形成。
3.镀浴温度:温度升高,极化作用下降,使镀层结晶粗大,可提高电流密度来抵消。
4.搅拌:可防足氢气停滞件表面形成针孔,一般搅拌可得到较细致镀层,但镀浴需过滤清洁,否则杂质因搅拌而染镀件表面产生结瘤或麻点等缺点。
5.电流波形:应用交通电流,周期反向电流(PR)电流、脉冲电流等特殊电流可改进阳极溶解,移去极化作用的钝态膜,增强镀层光泽度、平滑度、降低镀层内应力、或提高镀层均一性。
6.均一性(throwing power),或称之投掷力,好的均一性是指镀层厚度分布均匀。
均一性的影响因素有:①.几何形状,主要是指镀槽、阳极、镀件的形状。
分布位置空间、阴阳极的距离、尖端放电、边缘效应等因素。
②.极化作用,提高极化作用可提高均一性。
③.电流密度,提高电流密度可改进均一性。
④.镀浴导电性,导电生提高而不降低阴极极化作用太多则可提高均一性。
⑤.电流效率,降低电流效率可提高均一性。
所以要得到均匀镀层的方法有:①.良好的镀浴成份,改进配方有。
②.合理操作,表面活生化均匀。
③.合理镀装挂,以得到最佳电流均匀分布,防止析出气体累积于盲孔或低洼部分。
④.调节阴阳极间之距离及高度。
⑤.应用阳极形状善电流分布。
⑥.加设辅助电极、输电装置、绝缘屏障等改进电流分布。
⑦.应用冲击电流、在电镀前用较大电流进行短时间电镀。
PCB电镀填孔的机理分析及其影响因素

首先考虑抑制剂的抑制因子为 和光亮剂的 加速因子 相结合饱和的表面,吸附竞争动力学 简单的量化描述如下:
式(1)
由于在这些电解质溶液中,光亮剂SPS的浓
度
要远小于抑制剂PEG的浓度 ,因此可
以假定一个刚浸入到电解液的样品只被抑制剂浸
润。此外,在铜沉积过程中空气/水界面的抑制剂
关键词 填孔;曲率吸附机制;机理 中图分类号:TN41 文献标识码:A 文章编号:1009-0096(2018)09-0028-10
Analysis mechanism and effectors of Via-filling Plating for PCB
Liu Zhenquan Wu Peichang Lin Chunqin Chen Guangang Abstract CEAC play an important role for micro-via filling by electroplating, the organic additive can accelerate the electrical deposition rate of the blind hole bottom, also inhibit the electrical deposition rate of the suface and corner of blind hole to be filled. In this text, we carried on analysis about CEAC and function of organic additive for micro-via filling by electroplating detailed, got optimistic ratio of three kind organic additives for micro-via filling by electroplating at last, and inducted effectors of PCB boards during macrovia filling by electroplating. Key words Hole Filling; CEAC; Mechanism
电镀加工出现问题的原因及解决办法
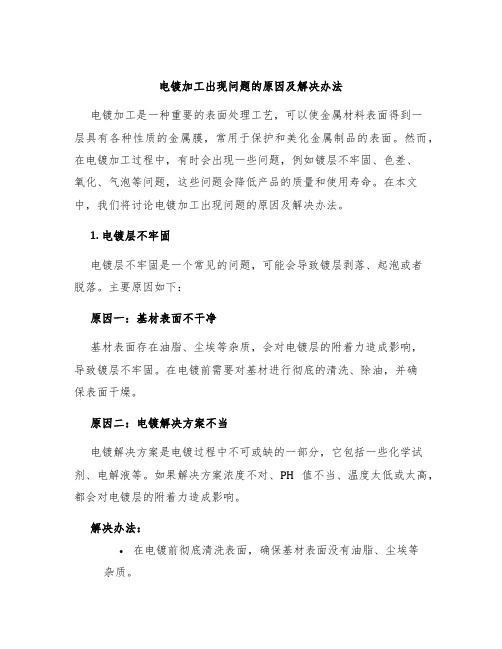
电镀加工出现问题的原因及解决办法电镀加工是一种重要的表面处理工艺,可以使金属材料表面得到一层具有各种性质的金属膜,常用于保护和美化金属制品的表面。
然而,在电镀加工过程中,有时会出现一些问题,例如镀层不牢固、色差、氧化、气泡等问题,这些问题会降低产品的质量和使用寿命。
在本文中,我们将讨论电镀加工出现问题的原因及解决办法。
1. 电镀层不牢固电镀层不牢固是一个常见的问题,可能会导致镀层剥落、起泡或者脱落。
主要原因如下:原因一:基材表面不干净基材表面存在油脂、尘埃等杂质,会对电镀层的附着力造成影响,导致镀层不牢固。
在电镀前需要对基材进行彻底的清洗、除油,并确保表面干燥。
原因二:电镀解决方案不当电镀解决方案是电镀过程中不可或缺的一部分,它包括一些化学试剂、电解液等。
如果解决方案浓度不对、PH值不当、温度太低或太高,都会对电镀层的附着力造成影响。
解决办法:•在电镀前彻底清洗表面,确保基材表面没有油脂、尘埃等杂质。
•在电镀解决方案中,加入一些添加剂,例如促进剂、增容剂等,来增强电镀层的附着力。
2. 镀层色差在电镀过程中,有时会出现镀层色差的问题,主要原因如下:原因一:电解液浓度不均电解液浓度的不均匀会导致镀层颜色不均匀。
例如,电解液中某些添加剂如果浓度过高或者过低,都可能导致镀层颜色的不同。
原因二:镀层表面存在缺陷镀层表面存在气泡、孔洞等缺陷也会导致镀层颜色不均匀。
解决办法:•定期检查电解液浓度,确保其均匀。
•彻底清洗基材的表面,确保表面无污染和缺陷。
3. 氧化问题氧化是电镀过程中另一个常见的问题,可以影响镀层的附着力和外观。
主要原因如下:原因一:电解液中的氧化物电解液中含有氧化物,而这些氧化物经常与电解液中的金属离子发生反应,从而导致镀层表面氧化。
原因二:镀层表面缺氧缺乏足够的电解气体氧分子也会导致金属离子表面氧化。
解决办法:•检查电解液中氧化物的含量,并确定其是否应该加入或减少。
•向电解液中添加抗氧化剂。
影响电镀质量的内部和外部因素分析

影响电镀质量的内部和外部因素分析电镀是一门重要的基础工艺。
产品零件经过电镀加工,在零件表面镀覆一层具有一定物理化学性能的电镀层,将赋予零件如装饰防护、耐磨、减磨等新的功能。
这些功能将对产品的使用性能产生重要的影响。
我公司产品为纺织机械设备,部分零件以电镀硬铬和镀锌为主。
镀硬铬为了提高耐磨性;镀锌件主要为外露件,起到防锈、美观的作用。
电镀件质量的好坏直接影响着设备的整体质量,因此必须对影响电镀质量的因素全面分析并严格控制。
影响电镀质量的因素包括内部因素和外部因素两个方面。
一、内部因素电镀车间内部严格的质量管理是电镀零件质量的有力保障。
为了从根本上提高电镀质量,并获得优质镀层的目的,对影响电镀质量的每一个内部环节都应有一个全面的认识。
(一)前处理因素镀层与基体之间的结合力、防腐性能和外观质量的好坏,与零部件镀前表面处理的优劣有着直接关系。
附着于零件表面的油、锈、氧化皮等污物,就是妨碍电镀液与金属基体充分接触的中间障碍物,在这种表面上不可能形成合格的电镀层。
当镀件上附着极薄的甚至肉眼看不见的油膜和氧化膜时,虽然得到外观正常、结晶细致的镀层,但是结合强度大为降低。
因此,做好零件的前处理,是整个电镀工序获得良好结果的先决条件。
首先,必须保证除油和酸洗溶液的浓度和纯度,溶液中漂浮的油污要及时清理干净;其次,除锈液杂质达到一定量时,将会影响镀层质量,所以要定期更换。
(二)电镀药液因素在电镀生产中,由于各种原因,导致各种有害杂质进入电镀液。
杂质的种类繁多,大致有金属杂质、金属氧化物、非金属杂质和种种不溶性悬浮物、有机杂质等。
各种镀液所含杂质的种类不尽相同,对同一种杂质的容忍程度也不相同。
当一种或几种有害杂质积累到一定程度时,就会影响镀液性能和镀层质量,因此,不能等到杂质积累到造成危害时,才处理电镀液。
另外,电镀药液各成分含量有一个最佳工艺范围,应对槽子药液定期进行化验分析,保证各成份在工艺范围内;同时,根据生产任务量、实际经验和化验结果,在杂质积累到有可能影响电镀层质量之前,净化处理电镀液,以保证电镀药液的稳定性。
电镀件常见不良原因分析
电镀件常见不良原因分析电镀件是一种常见的表面处理方式,用于保护和美化金属制品。
然而,在电镀过程中,常会出现不良现象,例如涂层不均匀、气泡、黑点、膜裂纹等问题。
这些问题的产生往往是由于一系列原因导致的。
下面,就电镀件常见不良原因进行分析。
1.基材准备不当电镀前的基材处理非常重要,如果没有正确准备基材,会直接影响到电镀效果。
常见的基材准备不当原因有:-表面清洁不彻底:基材表面可能存在油污、灰尘等杂质,如果未经彻底清洁,这些杂质会影响镀层的附着力和均匀性。
-钝化处理不当:钝化处理可以增强镀层与基材之间的结合力,但处理时间、温度、浓度等参数不正确,会导致镀层不牢固。
2.电解液质量不合格电解液是电镀过程中的核心部分,如果电解液质量不合格,会直接影响到电镀效果。
常见的电解液质量问题有:-含杂质过多:电镀液中可能存在各种杂质,如金属离子、有机物等,它们会影响到电镀膜的致密性和均匀性。
-配方参数不正确:电解液的配方包括各种成分的浓度和比例,如果配方参数不正确,会导致镀层的颜色、硬度等性能不达标。
3.电镀工艺控制不当电镀工艺过程中的各个环节都需要精确控制,否则会产生不良现象。
常见的电镀工艺控制不当原因有:-电流密度不均匀:电镀过程中,电流密度分布不均匀会导致镀层厚度不均匀,甚至出现孔洞等问题。
-温度控制不准确:电镀过程中的温度控制对于镀层的质量和均匀性非常重要,如果温度控制不准确,会影响到电解液的反应速率和镀层的结构。
4.设备维护不当电镀设备的维护工作也是保证电镀质量的关键。
常见的设备维护不当原因有:-阴极和阳极污染:设备内部的阴极和阳极可能会受到电解液的腐蚀,长期使用后会产生污染物,需要定期清洗和更换。
-设备参数不稳定:设备的电流、温度、电压等参数需保持稳定,如果设备参数不稳定,会导致镀层质量下降。
综上所述,电镀件常见的不良现象往往由基材准备不当、电解液质量不合格、电镀工艺控制不当和设备维护不当等原因导致。
为确保电镀质量,操作人员应遵循正确的工艺流程,提高工作细致性和耐心性,严格控制每个环节的参数和条件,以及定期维护设备,确保设备的正常运行。
电镀填孔工艺影响因素
科技成果:电镀填孔工艺影响因素电子产品的体积日趋轻薄短小,通盲孔上直接叠孔(viaonHole或Viaonvia)是获得高密度互连的设计方法。
要做好叠孔,首先应将孔底平坦性做好。
典型的平坦孔面的制作方法有好几种,电镀填孔(ViaFillingPlating)工艺就是其中具有代表性的一种。
电镀填孔工艺除了可以减少额外制程开发的必要性,也与现行的工艺设备兼容,有利于获得良好的可靠性。
电镀填孔有以下几方面的优点:(1)有利于设计叠孔(Stacked)和盘上孔(via.on.Pad):(2)改善电气性能,有助于高频设计;(3)有助于散热;(4)塞孔和电气互连一步完成;(5)盲孔内用电镀铜填满,可靠性更高,导电性能比导电胶更好。
电镀填孔是目前各PCB制造商和药水商研究的热门课题。
Atotech、Shipley、奥野、伊希特化及Ebara等国外知名药水厂商都已推出自己的产品,抢占市场份额。
2电镀填孔的影响参数电镀填孔工艺虽然已经研究了很多,但真正大规模生产尚有待时日。
其中一个因素就是,电镀填孔的影响因素很多。
如图1所示,电镀填孔的影响因素基本上可以分为三类:化学影响因素、物理影响因素与基板影响因素,其中化学影响因素又可以分为无机成分与有机添加剂。
下面将就上述三种影响因素一一加以简单介绍。
2.1化学影响因素2.1.1无机化学成分无机化学成分包括铜(Cu2+)离子、硫酸和氯化物。
(1)硫酸铜。
硫酸铜是镀液中铜离子的主要来源。
镀液中铜离子通过阴极和阳极之间的库仑平衡,维持浓度不变。
通常阳极材料和镀层材料是一样的,在这里铜既是阳极也是离子源。
当然,阳极也可以采用不溶性阳极,Cu2+采用槽外溶解补加的方式,如采用纯铜角、CuO粉末、CuCO3等。
但是,需要注意的是,采用槽外补加的方式,极易混入空气气泡,在低电流区使Cu2+处于超饱和临界状态,不易析出。
值得注意的是,提高铜离子浓度对通孔分散能力有负面影响。
(2)硫酸。
影响电镀加工的因素
影响电镀加工的因素电镀加工是一种常见的表面处理技术,它可以改善材料的耐腐蚀性、防腐性以及观感。
然而,电镀加工也存在着很多影响因素,下面我们来详细探讨一下这些方面。
材料的选择电镀加工的适用材料种类十分丰富。
一般而言,能导电且不容易氧化的材质比较适合进行电镀加工,如铜、不锈钢、镍等。
另外,在材料的选择过程中,还需要考虑到所需的电镀度以及细节处理要求等。
表面处理的影响在进行电镀加工之前,需要对材料进行浸泡、清洗、处理等操作。
这些表面处理的步骤直接影响着电镀加工的效果。
因此,在进行电镀加工前要确保表面处理充分,以避免对电镀效果的影响。
电镀环境的控制电镀环境温度、电流密度等因素,都会对电镀加工的质量造成一定的影响。
在进行电镀加工时,需要对环境进行精细的控制,以确保其达到最佳的电镀效果。
电镀液的配比电镀加工中使用的电镀液,对电镀效果直接产生影响。
如果电镀液的配方不合适,就会导致电镀质量下降、电镀黄变、失败率增加等问题的发生。
因此,在进行电镀加工前,需要根据具体情况精心配置电镀液。
电镀液的维护在进行电镀加工的过程中,电镀液的维护也是非常重要的。
如果不定期更换电镀液、不去除杂质等,就会对电镀质量造成一定的影响,甚至导致电镀不良、失效等问题的发生。
电镀工艺的选择不同的电镀工艺,对电镀效果的影响也是不同的。
因此,在进行电镀加工之前,需要评估不同的电镀工艺,并选取最合适的方案。
选用平衡的电镀工艺,不仅能提高电镀效率,保证操作的安全性,而且还可以减少后期不必要的维修。
良好的操作技能良好的电镀加工操作技能,也是保证电镀效果的重要因素。
电镀加工是一种精细的工艺,在操作时需要严格遵守操作规程,注意安全防护措施,保证操作的规范性和质量。
以上就是影响电镀加工的因素的介绍。
在实际的生产操作中,需要全面考虑这些因素,以保证电镀加工的效果达到预期。
电镀不良之原因分析及防范措施
电镀不良之原因分析及防范措施电镀不良是指电镀工艺过程中出现不符合要求的现象和问题,造成电镀层质量不达标的情况。
电镀不良的原因可以从多个方面进行分析,并采取相应的防范措施来提高电镀质量。
一、原料不合格电镀不良的一个主要原因是使用不合格的原料。
例如,如果使用了含有杂质、过高硬度、粒径不一致或含有过多镍离子等问题的电镀液,则会导致电镀层质量不良。
为避免这种情况的发生,应对电镀液进行严格的检验和筛选工作,确保原料的质量。
二、电镀工艺参数不合理不合理的电镀工艺参数也是电镀不良的一个原因。
比如,电镀液的温度、酸碱度、电流密度等参数都会对电镀质量产生影响。
温度过高或过低、酸碱度不合适、电流密度过大或过小等都可能导致电镀层出现问题。
因此,要根据实际情况调整电镀工艺参数,并严格控制每个参数的范围,确保电镀层质量稳定。
三、电镀设备质量不过关电镀设备的质量也会对电镀层质量产生影响。
例如,电解槽的设计和制造质量、电源的稳定性以及电极材料的选择等都会直接影响电镀质量。
因此,在选购设备时,要选择性能稳定、品质可靠的设备,并保证设备的维护和保养,提高设备的使用寿命和稳定性。
四、工艺操作不当不正确的工艺操作也是电镀不良的一个常见原因。
例如,电镀工艺操作的速度太快或太慢,工件的浸泡时间控制不准确等都可能导致电镀层质量不良。
因此,操作人员在进行电镀工艺操作时要严格按照程序进行,并且进行必要的培训和技术指导,提高工艺操作的准确性和稳定性。
综上所述,电镀不良的原因可以从原料、工艺参数、设备质量和工艺操作等多个方面进行分析。
为了防范电镀不良的发生,可以采取以下措施:1.选用优质的原料,并进行严格检验和筛选;2.根据实际情况调整电镀工艺参数,并进行严格的控制;3.选购品质可靠的设备,并保证设备的维护和保养;4.进行工艺操作前进行必要的培训和技术指导,确保操作的准确性和稳定性;5.建立完善的质量控制体系,对电镀过程进行监控和检测,及时处理不良产品;6.加强与供应商的合作,建立长期稳定的合作关系,确保原料和设备质量的稳定性。
- 1、下载文档前请自行甄别文档内容的完整性,平台不提供额外的编辑、内容补充、找答案等附加服务。
- 2、"仅部分预览"的文档,不可在线预览部分如存在完整性等问题,可反馈申请退款(可完整预览的文档不适用该条件!)。
- 3、如文档侵犯您的权益,请联系客服反馈,我们会尽快为您处理(人工客服工作时间:9:00-18:30)。
科技成果:电镀填孔工艺影响因素电子产品的体积日趋轻薄短小,通盲孔上直接叠孔(viaonHole或Viaonvia)是获得高密度互连的设计方法。
要做好叠孔,首先应将孔底平坦性做好。
典型的平坦孔面的制作方法有好几种,电镀填孔(ViaFillingPlating)工艺就是其中具有代表性的一种。
电镀填孔工艺除了可以减少额外制程开发的必要性,也与现行的工艺设备兼容,有利于获得良好的可靠性。
电镀填孔有以下几方面的优点:(1)有利于设计叠孔(Stacked)和盘上孔(via.on.Pad):(2)改善电气性能,有助于高频设计;(3)有助于散热;(4)塞孔和电气互连一步完成;(5)盲孔内用电镀铜填满,可靠性更高,导电性能比导电胶更好。
电镀填孔是目前各PCB制造商和药水商研究的热门课题。
Atotech、Shipley、奥野、伊希特化及Ebara等国外知名药水厂商都已推出自己的产品,抢占市场份额。
2电镀填孔的影响参数电镀填孔工艺虽然已经研究了很多,但真正大规模生产尚有待时日。
其中一个因素就是,电镀填孔的影响因素很多。
如图1所示,电镀填孔的影响因素基本上可以分为三类:化学影响因素、物理影响因素与基板影响因素,其中化学影响因素又可以分为无机成分与有机添加剂。
下面将就上述三种影响因素一一加以简单介绍。
2.1化学影响因素2.1.1无机化学成分无机化学成分包括铜(Cu2+)离子、硫酸和氯化物。
(1)硫酸铜。
硫酸铜是镀液中铜离子的主要来源。
镀液中铜离子通过阴极和阳极之间的库仑平衡,维持浓度不变。
通常阳极材料和镀层材料是一样的,在这里铜既是阳极也是离子源。
当然,阳极也可以采用不溶性阳极,Cu2+采用槽外溶解补加的方式,如采用纯铜角、CuO粉末、CuCO3等。
但是,需要注意的是,采用槽外补加的方式,极易混入空气气泡,在低电流区使Cu2+处于超饱和临界状态,不易析出。
值得注意的是,提高铜离子浓度对通孔分散能力有负面影响。
(2)硫酸。
硫酸用于增强镀液的导电性,增加硫酸浓度可以降低槽液的电阻与提高电镀的效率。
但是如果填孔电镀过程中硫酸浓度增加,影响填孔的铜离子补充,将造成填孔不良。
在填孔电镀时一般会使用低硫酸浓度系统,以期获得较好的填孔效果。
(3)酸铜比。
传统的高酸低铜(Cw+:Ccu2+=8~13)体系适用于通孔电镀,电镀填孔应采用低酸高铜(Cw+:Ccu2+=3~10)镀液体系。
这是因为为了获得良好的填孔效果,微导通孔内的电镀速率应大于基板表面的电镀速率,在这种情况下,与传统的电镀通孔的电镀溶液相比,溶液配方由高酸低铜改为低酸高铜,保证了凹陷处铜离子的供应无后顾之忧。
(4)氯离子。
氯离子的作用主要是让铜离子与金属铜在双电层间形成稳定转换的电子传递桥梁。
在电镀过程中,氯离子在阳极可帮助均匀溶解咬蚀磷铜球,在阳极表面形成一层均匀的阳极膜。
在阴极与抑制剂协同作用让铜离子稳定沉积,降低极化,使镀层精细。
另外,常规的氯离子分析是在紫外可见光分光光度计进行的,而由于电镀填孔镀液对氯离子浓度的要求较严格,同时硫酸铜镀液呈蓝色,对分光光度计的测量影响很大,所以应考虑采用自动电位滴定分析。
2、1.2有机添加剂采用有机添加剂可以使镀层铜晶粒精细化,改善分散能力,使镀层光亮、整平。
酸性镀铜液中添加剂类型主要有三种:载运剂(Carrier)、整平剂(Leveler)和光亮剂(Brighte ner)。
(1)载运剂。
载运剂是高分子的聚醇类化合物。
载运剂被阴极表面吸附,与氯离子一起作用抑制电镀速率,使高低电流区的差异降低(亦即增加极化电阻),让电镀铜能均匀的持续沉积。
抑制剂同时可充当润湿剂,降低界面的表面张力(降低接触角),让镀液更容易进入孔内增加传质效果。
在填孔电镀中,抑制剂也可以铜层均匀沉积。
(2)整平剂。
整平剂通常是含氮有机物,主要功能是吸附在高电流密度区(凸起区或转角处),使该处的电镀速度趋缓但不影响低电流密度区(凹陷区)的电镀,借此来整平表面,是电镀时的必要添加剂。
一般地,电镀填孔采用高铜低酸系统会使镀层粗糙,研究表明,加入整平剂可有效改善镀层不良的问题。
(3)光亮剂。
光亮剂通常足含硫有机物,在电镀中主要作用是帮助铜离子加速在阴极还原,同时形成新的镀铜晶核(降低表面扩散沉积能量),使铜层结构变得更细致。
光亮剂在填孔电镀中的另一个作用是,若孔内有较多的光亮剂分配比率,可以帮助盲孔孔内电镀铜迅速沉积。
对于激光盲孔的填孔电镀而言,三种添加剂全用,且整平剂的用量还要适当地提高,使在板面上较高电流区,形成整平剂与Cu2+竞争的局面,阻止面铜长快长厚。
相对地,微导通孔中光亮剂分布较多的凹陷处有机会镀得快一点,这种理念与做法与IC镀铜制程的D emasceneCopperPlating颇为相似。
2.2物理影响参数需要研究的物理参数有:阳极类型、阴阳极间距、电流密度、搅动、温度、整流器和波形等。
(1)阳极类型。
谈到阳极类型,不外乎是可溶性阳极与不溶性阳极。
可溶性阳极通常是含磷铜球,容易产生阳极泥,污染镀液,影响镀液性能。
不溶性阳极,亦称惰性阳极,一般是涂覆有钽和锆混合氧化物的钛网来组成。
不溶性阳极,稳定性好,无需进行阳极维护,无阳极泥产生,脉冲或直流电镀均适用;不过,添加剂消耗量较大。
(2)阴阳极间距。
电镀填孔工艺中阴极与阳极之间的间距设计是非常重要的,而且不同类型的设备的设计也不尽相同。
不过,需要指出的是,不论如何设计,都不应违背法拉第定律。
(3)搅拌。
搅拌的种类很多,有机械摇摆、电震动、气震动、空气搅拌、射流(Educto r)等。
对于电镀填孔,一般都倾向于在传统铜缸的配置基础上,增加射流设计。
不过,究竟是底部喷流还是侧面射流,在缸内喷流管与空气搅拌管如何布局;每小时的射流量为多少;射流管与阴极间距多少;如果是采用侧面射流,则射流是在阳极前面还是后面;如果是采用底部射流,是否会造成搅拌不均匀,镀液搅拌上弱下强;射流管上射流的数量、间距、角度都是在铜缸设计时不得不考虑的因素,而且还要进行大量的试验。
另外,最理想的方式就是每根射流管都接入流量计,从而达到监控流量的目的。
由于射流量大,溶液容易发热,所以温度控制也很重要。
(4)电流密度与温度。
低电流密度和低温可以降低表面铜的沉积速率,同时提供足够的Cu2+和光亮剂到孔内。
在这种条件下,填孔能力得以加强,但同时也降低了电镀效率。
(5)整流器。
整流器是电镀工艺中的一个重要环节。
目前,对于电镀填孔的研究多局限于全板电镀,若是考虑到图形电镀填孔,则阴极面积将变得很小。
此时,对于整流器的输出精度提出了很高的要求。
整流器的输出精度的选择应依产品的线条和过孔的尺寸来定。
线条愈细、孔愈小,对整流器的精度要求应更高。
通常应选择输出精度在5%以内的整流器为宜。
选择的整流器精度过高会增加设备的投资。
整流器的输出电缆配线,首先应将整流器尽量安放在镀槽边上,这样可以减少输出电缆的长度,减少脉冲电流上升时间。
整流器输出电缆线规格的选择应满足在80%最大输出电流时输出电缆的线路压降在0.6V以内。
通常是按2.5A/mm2的载流量来计算所需的电缆截面积。
电缆的截面积过小或电缆长度过长、线路压降太大,会导致输出电流达不到生产所需的电流值。
对于槽宽大于1.6m的镀槽,应考虑采用双边进电的方式,并且双边电缆的长度应相等。
这样,才能保证双边电流误差控制在一定范围内。
镀槽上的每根飞巴的两面应各连接一台整流器,这样可以对镀件的两个面的电流分别予以调整。
(6)波形。
目前,从波形角度来看,电镀填孔有脉冲电镀和直流电镀两种。
这两种电镀填孔方式都已有人研究过。
直流电镀填孔采用传统的整流器,操作方便,但是若在制板较厚,就无能为力了。
脉冲电镀填孔采用。
PPR整流器,操作步骤多,但对于较厚的在制板的加工能力强。
2.3基板的影响基板对电镀填孔的影响也是不可忽视的,一般有介质层材料、孔形、厚径比、化学铜镀层等因素。
(1)介质层材料。
介质层材料对填孔有影响。
与玻纤增强材料相比,非玻璃增强材料更容易填孔。
值得注意的是,孔内玻纤突出物对化学铜有不利的影响。
在这种情况下,电镀填孔的难点在于提高化学镀层种子层(seedlayer)的附着力,而非填孔工艺本身。
事实上,在玻纤增强基板上电镀填孔已经应用于实际生产中。
(2)孔形。
(3)厚径比。
目前针对不同形状,不同尺寸孔的填孔技术,不论是制造商还是开发商都对其非常重视。
填孔能力受孔厚径比的影响很大。
相对来讲,DC系统在商业上应用更多。
在生产中,孔的尺寸范围将更窄,一般直径80gm~120gm,孔深40gm~80gm,厚径比不超过1:1。
(4)化学镀铜层。
化学铜镀层的厚度、均匀性及化学镀铜后的放置时间都影响填孔性能。
化学铜过薄或厚度不均,其填孔效果较差。
通常,建议化学铜厚度>0.3um时进行填孔。
另外,化学铜的氧化对填孔效果也有负面影响。
3结束语以上主要是对电镀填孔影响因素做了一些最基本的探讨,另外一些因素并未提及。
如镀液是否为非染料系的,因为非染料的药液稳定性好,不易形成有害的副产物。
还有如阳极挡板设计,现在对电镀填孔的研究多集中在全板电镀,对于图形电镀填孔的研究还不多。
当进行图形电镀时,为了保证电镀的均匀性,挡板设计就显得尤为重要,而挡板设计往往又是电镀设备制造商的专利。
此外,由于图形电镀涉及到干膜,干膜对镀液性能有影响,所以,应对干膜做溶出实验,从而确定活性炭处理周期。
无论怎样,目前对于电镀填孔技术来讲,下面几项结论已为大家所接受:(1)镀液配方。
采用高铜低酸的电镀液配方,同时控制添加剂的比例,能保证镀层品质和填孔效果良好,有效的添加剂监控是非常重要的;(2)电流密度和操作温度。
低电流密度和低温可以降低表面铜的沉积速率,同时提供足够的Cuz’和光亮剂到孔内。
在这种条件下,填孔能力得以加强,但同时也降低了电镀效率。
(3)设备类型。
电镀填孔对设备的要求很高。
①采用可溶性阳极一一阳极的溶解可能导致添加剂的副反应。
②采用不溶性阳极一一水电解会产生大量的氧气,过量消耗有机添加剂。
③搅拌一一搅拌应稳定均匀。
不恰当的搅拌不仅会引起填孔能力下降,而且还会导致镀层品质变差。
④阴/阳极间距一一阴/阳极间距与挡板的设计应综合考虑,否则将导致电力线分布不均。
(4)添加剂副产物的监控。
有机添加剂副产物积累过多的表现之一,就是填孔能力下降。
应通过Hull槽或CVS有效控制镀液中的添加剂含量。
批量生产时,如何有效除去添加剂的降解副产物非常重要。
(5)通、盲孔同时电镀,通孔的电镀深镀能力会受到影响。
总之,善用设备、药液、添加剂及操作参数,将是电镀填孔成功的关键。