电镀铜
电镀铜工艺-专业介绍

02 电镀铜工艺流程
前处理
01
02
03
表面清洁
去除工件表面的油污、锈 迹和杂质,确保工件表面 干净。
表面粗化
通过物理或化学方法对工 件表面进行粗化处理,增 加表面能,提高镀层附着 力。
敏化处理
在工件表面形成一层敏化 膜,提高工件与镀层的结 合力。
电镀铜
电解铜沉积
在电场作用下,铜离子在 工件表面还原成金属铜, 形成电镀层。
研究电镀铜层的微观结构和性能,以优化电镀铜工艺,提高镀层质量。
环保型电镀铜技术的推广与应用
推广无氰、低氰、低毒的电镀铜工艺,减少对环 境的污染和危害。
研发可回收再利用的电镀铜技术,降低资源消耗 和生产成本。
探索生物可降解的电镀铜添加剂,实现绿色环保 的生产方式。
电镀铜与其他表面处理技术的结合与创新
氰化电镀铜溶液含有剧毒的氰化物,需要严格的安全措施和废水处理。
焦磷酸盐电镀铜
焦磷酸盐电镀铜具有镀层均匀、 整平性好、结晶细致等特点,适
用于装饰性和功能性电镀。
适用于钢铁、锌合金、铝合金等 基材的电镀,具有良好的结合力
和耐腐蚀性。
焦磷酸盐电镀铜溶液稳定性较好, 但溶液成分复杂,维护成本较高。
预镀镍-铜-镍三层电镀
电镀铜工艺-专业介绍
目 录
• 电镀铜工艺简介 • 电镀铜工艺流程 • 电镀铜的种类与特性 • 电镀铜的环保问题与对策 • 电镀铜的发展趋势与未来展望
01 电镀铜工艺简介
电镀铜的定义
电镀铜是一种通过电解方法在金 属表面沉积一层铜的工艺过程。
电镀铜工艺利用电解池原理,通 过铜离子在阴极上还原成铜,形
成致密的铜镀层。
电镀铜层具有良好的导电性、耐 腐蚀性和装饰性,广泛应用于电 子、通讯、航空航天电子产品制造
电镀工艺学-电镀铜

3
此外,铜镀层也用于局部防止渗碳,增加导电性能和润滑 性能,电铸以及印刷电路板孔金属化等。
镀铜溶液的种类虽然很多,但在生产中常用的主要为: 氰化物镀铜电解液 酸性硫酸盐镀铜电解液 焦磷酸盐镀铜电解液等 还有柠檬酸—酒石酸盐镀铜、HEDP镀铜、氨三乙酸镀铜、 L—胺镀铜及氟硼酸盐镀铜等工艺 。
2005 FH
2005 FH
电镀工艺学 06-1-68
16
1.4 操作条件的影响
(1)温度 操作温度随镀液浓度高低而异。浓度较低控制在 20℃~60 ℃ ,高浓度控制在50 ℃~80 ℃ 。温 度高时可以提高阴 极电流效率,但降低阴极极化和引起氰化钠分解,从而产生碳 酸钠和氨。为了缩短电镀时 间,一般采用50 ℃~ 65 ℃ ;预镀为 30 ℃ ~40 ℃ 。
6
CL-3光亮剂/mL·L-1
5-7
CL-4光亮剂/mL·L-1 KUBRITE KC-3调整剂/mL·L-1 KUBRITE KC-2调整剂/mL·L-1 KUBRITE KC-1调整剂/mL·L-1
5 30-50 5-7 5
温度/℃
18-50
50-60
55-65 55-65 55-65 55-65 45-60
氰化物剧毒,对人体有害且污染环境,生产时必须制订 严格的安全技术制度并设置槽边排风设备和废水,废气治理 设施。
2005 FH
电镀工艺学 06-1-68
5
成分及工作条件
表7—1 氰化物镀铜工艺规范
配
方
1
2
3
4
5
氰化亚铜CuCN/g·L-1 红铜盐/g·L-1
8 -35 35-45 50-70
55-85 130-200
氢氧化钾KOH/g·L-1
电镀铜原理

电镀铜原理
电镀铜原理是利用电化学原理,在铜质基材上通过电解方法沉积一层薄而均匀的铜层。
具体的步骤如下:
1. 准备工作:准备一块纯铜质的阳极和需要镀铜的物体作为阴极。
将两者分别连接到正负极,放置在含有铜离子的电解液中。
2. 铜离子在电解液中:电解液通常是含有铜盐的溶液,如铜硫酸或铜氯化物。
当电流通过电解液时,铜盐分解成铜离子和阴离子。
3. 阴极反应:阴极上的铜离子通过电化学还原反应被还原成纯铜,并沉积在阴极表面。
反应方程式为:Cu2+ + 2e- → Cu。
4. 阳极反应:阳极上同时发生氧化反应,阴离子被氧化成气体(如氧或氯气)。
反应方程式为:2Cl- - 2e- → Cl2 + 2e-。
5. 镀铜过程:经过一定时间的运行,阴极表面积累的铜层逐渐增厚,直到达到所需的厚度。
如果需要更厚的铜层,可以延长电解时间。
6. 电流密度控制:在电镀过程中,控制电流密度非常重要。
适当的电流密度可以确保铜层的均匀和牢固性。
过高的电流密度可能导致铜层不均匀,过低的电流密度可能导致铜层松散容易脱落。
通过以上步骤,就可以在物体表面成功实现电镀铜,使其具备铜的外观和性质。
《电镀铜技术》课件
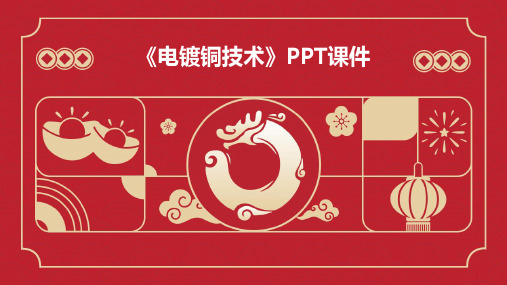
目录
CONTENTS
• 电镀铜技术概述 • 电镀铜的工艺流程 • 电镀铜的设备与材料 • 电镀铜的环保与安全 • 电镀铜的发展趋势与未来展望
01 电镀铜技术概述
CHAPTER
电镀铜的定义
电镀铜是一种通过电解方法在金属表面沉积一层铜的过程。
电镀铜技术广泛应用于电子、航空航天、汽车、建筑等领域 。
分类处理
电镀铜废弃物应按照危险废物和一般废物的分类原则进行 分类处理。危险废物应交由有资质的单位进行处置,一般 废物可按照当地有关规定进行处置。
合理利用
对于可回收利用的电镀铜废弃物,应进行合理利用,减少 资源浪费。
规范处置
对于不能回收利用的电镀铜废弃物,应按照国家和地方有 关规定进行规范处置,防止对环境造成二次污染。 Nhomakorabea调整pH值
通过加入酸或碱调整溶液 的pH值,保持电镀液的稳 定性。
电镀铜的操作步骤
挂具准备
根据工件形状和大小,选择合适 的挂具,确保工件在电镀过程中 稳定悬挂。
电镀液的加热
将电镀液加热至适宜的温度,以 提高电镀效率和镀层质量。
通电电镀
将工件浸入电镀液中,通过直流 电源通电进行电镀。控制电流密 度、电镀时间和温度等参数,以 获得良好的镀层质量。
03
汽车行业
电镀铜被用于汽车零部件的制造 ,以提高耐腐蚀性和外观质量。
02
航空航天
电镀铜被用于制造高性能的航空 航天材料,以提高耐腐蚀性和导
电性。
04
建筑行业
电镀铜被用于建筑装饰和结构件 的制造,以提高耐腐蚀性和美观
度。
02 电镀铜的工艺流程
CHAPTER
前处理
表面清洁
电镀铜
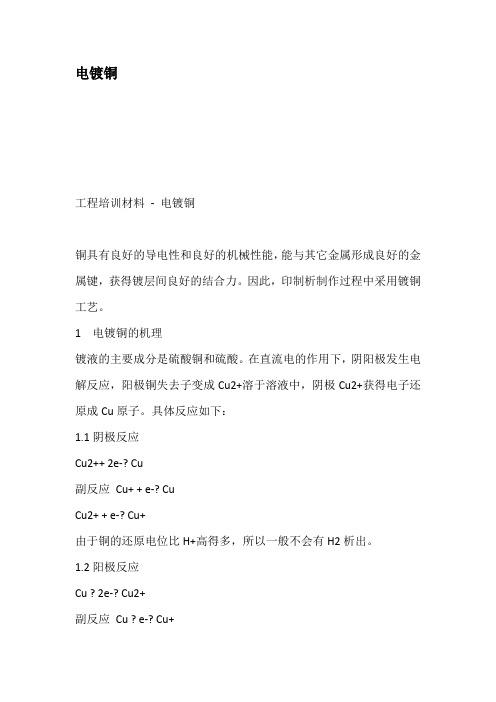
电镀铜工程培训材料- 电镀铜铜具有良好的导电性和良好的机械性能,能与其它金属形成良好的金属键,获得镀层间良好的结合力。
因此,印制析制作过程中采用镀铜工艺。
1 电镀铜的机理镀液的主要成分是硫酸铜和硫酸。
在直流电的作用下,阴阳极发生电解反应,阳极铜失去子变成Cu2+溶于溶液中,阴极Cu2+获得电子还原成Cu原子。
具体反应如下:1.1 阴极反应Cu2++ 2e-? Cu副反应Cu+ + e-? CuCu2+ + e-? Cu+由于铜的还原电位比H+高得多,所以一般不会有H2析出。
1.2 阳极反应Cu ? 2e-? Cu2+副反应Cu ? e-? Cu+在足够硫酸环境下,亦有如下反应2 Cu+ + 1/2O2 + 2H+? 2 Cu2+ + H2O当硫酸含量较低时,有如下反应2 Cu+ + 2H2O ? 2 Cu(OH)2 + 2H+2 Cu(OH)2 ? Cu2O + H2OCu2O即成“铜粉”,有Cu2O出现时镀层会变得疏松粗糙。
2 电镀锡机理电镀锡与电镀铜机理一样利用电解作用获得金属镀层。
阴极反应Sn2+ + 2e- ? Sn阳极反应Sn - 2e- ? Sn2+镀锡溶液主要成分是硫酸亚锡与硫酸。
3 电镀线各药水缸成份及作用3.1 除油缸主要成份为酸性除油剂,它可以清除板面污渍,指纹及菲林碎等杂质,获得清洁的基铜表面。
3.2 微蚀缸主要成份硫酸钠和硫酸溶液,如本公司所用的也有硫酸和双氧水型。
微蚀作用可以除待镀线路与孔内镀层的氧化层,增加其表面的粗糙度,从而提高与镀层有结合力。
3.3 浸酸缸主要成份H2SO4浸酸缸可以去除铜表面轻微的氧化层,同时防止污物污染铜缸。
3.4 镀铜缸进行电化学反应的场所,主要成份硫酸铜,硫酸,盐酸以及电镀铜添加剂。
3.4.1 硫酸铜是镀浴液中的主盐,它在水溶液中电离出铜离子,铜离子阴极上获得电子沉积出镀铜层。
控制浓度50-90g/L提高其浓度可以提高允许电流密度,避免烧板,但含量过高,会降低镀液的分散能力。
电镀铜工艺流程(一)

电镀铜工艺流程(一)电镀铜工艺工艺流程•清洗:将待处理的金属表面清洗干净,去除油污和其他杂质。
•预处理:对金属表面进行处理,如脱脂、除锈、去污等,以便于下一步的处理。
•电镀:将金属置于电解槽内,通过电流使含有铜离子的溶液析出金属铜,从而在金属表面上形成一层铜膜。
电镀过程中需要控制电流密度、温度等参数,以保证铜膜的均匀性和质量。
•冲洗:将电镀后的金属表面进行冲洗,去除残留的电镀液和化学药品。
•烘干:将冲洗后的金属表面进行烘干处理,以去除表面上的水分。
•收尾处理:电镀完成后还需要进行表面处理,如打磨、抛光、喷漆等,以增强其美观性和耐腐蚀性。
工艺特点•电镀铜具有很高的导电性、耐磨性和耐腐蚀性,适用于制造电器、机械和金属制品等工业品。
•电镀铜可实现对金属表面的精密加工,可在微米级别上控制镀层的厚度和均匀性。
•电镀铜工艺简单、成本低、加工效率高。
工艺应用•电子工业:用于制造印制电路板、电子元器件、电子设备外壳等。
•制造业:用于制造机械零件、汽车零配件、制冷设备等。
•建筑行业:用于制造门窗、天花板、护栏等装饰品。
总之,电镀铜工艺具有广泛的应用前景,对于提高工业品的外观、性能和质量起到了重要的作用。
工艺的优缺点优点1.铜镀层有良好的导电性和导热性。
2.镀层均匀性好,不会对原型造成形状的变化。
3.铜层具有良好的耐腐蚀性,可保护金属基材不受化学侵蚀。
4.镀铜工艺简单、操作方便、处理时间短。
缺点1.镀铜液对环境污染较为严重,做好废液处理工作非常重要。
2.镀铜液中含有若干有害物质,需要在处理时加以防护。
3.镀铜液的操作条件较为苛刻,对温度、电流密度等参数需严格控制。
工艺的发展趋势1.低污染工艺:开发低污染的镀铜工艺,降低对环境的危害。
2.高效工艺:提高镀铜效率,缩短处理时间,降低成本。
3.智能工艺:运用互联网、物联网、人工智能等技术,实现自动化生产和智能化管理。
4.多层复合工艺:研究多层复合的镀铜工艺,以满足产品特殊的性能要求。
电镀铜
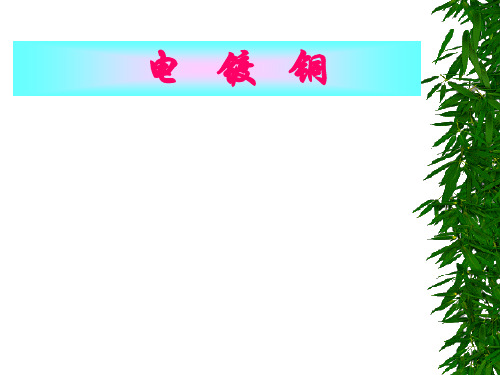
4、阴极移动(摇摆)+空气搅拌+连续 过滤 不但搅拌力度大,还能不断净化镀液, 可消除针孔气泡、节瘤等,使镀层质量 更好。
七、镀铜及设备参数控制
1、酸性清洁槽 酸性清洁剂:6-8% 温度:RT 每周换槽 2、微蚀槽 SPS:5-10g/l 硫酸:2.5-3.5% 温度:RT 每周换槽
电 镀 铜
一、电镀的简单原理
电镀指借助外界直流电的作用,在 溶液中进行电解反应,使导电体例如金 属的表面沉积一金属或合金层。 阳极:Cu- 2e- = Cu2+ 阴极: Cu2++2e-=Cu
1、法拉第定律
定律:在镀液进行电镀时(电解)阴极 上所“附积”的金属重量与所通过的电 量成正比。 例:库仑=安培*秒 1库仑的电量在100%的阳极效率下可以 镀出0.3294mg的纯铜,那么每1安培小 时可以镀出1.186g的纯铜。
球状磷铜球装在钛蓝里最好,一是同 重量时它的表面积最大,二是通过添加 磷铜球可维持阳极面积的稳定性,不会 在使用中出现上大下小的现象。
六、镀铜的注意点
1、阳极与阴极 阳极比阴极短7-8cm,可以防止电力 线分布不均产生边缘烧焦,阳极与阴极 间的距离一般要求至少15~20cm,阳极 比阴极窄10cm,阳极面积与阴极面积 之比为1.5~2:1。
2、阴极膜
定义:电镀进行时越接近被镀物表面时 其金属离子浓度愈低,现以其浓度下降 1%处起直到被镀物表面为止的一薄层 液膜称之为“阴极膜”。 此膜因被镀物外形而厚薄不同,凸起处 较薄,及高电流区;凹处较厚,及低电 流区。
3、镀液的电阻
RT(总电阻)=R1(外层及接点)+R2(大 液体)+R3(阴极膜) 电路板在进行量产时待镀面积大时需要上百 安培电流,为了得到良好的镀层电压多控制 在5伏以下,按A=V/R看来,其总电阻必须控 制很小,要保持外路及接点的低R1,加热镀 液降低R2,搅拌镀液降低R3。否则电压太高 会造成水被电解,影响电镀品质。
电镀铜工艺-专业介绍
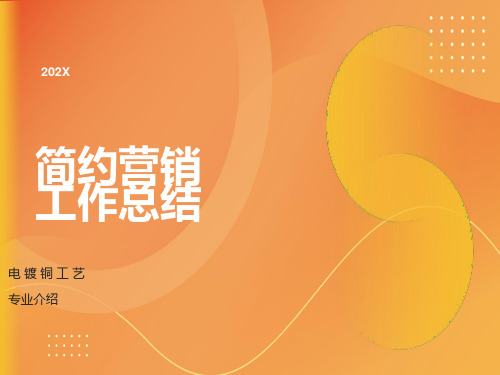
电镀铜阳极表面积估算方法
圆形钛篮铜阳极表面积估算方法
— dlf /2
=3.14 d=钛篮直径 l=钛篮长度 f=系数
方形钛篮铜阳极表面积估算方法
— 1.33lwf
l=钛篮长度 w=钛篮宽度 f=系数
f与铜球直径有关:
直径=12mm f=2.2
对铜镀层的基本要求
对镀铜液的基本要求
鍍液穩定,便于維護,對雜質的容忍性高,對溫度
一致。
04
電流密度範圍寬,如在赫爾槽2A下,全板鍍層均勻
板的板厚孔徑比較大時,仍能達Ts:Th接近1:1。
03
单击此处添加正文,文字是您思想的提炼,为了演示发布的良好效果,请言简意赅地阐述您的观点。
密度下,也能得到均勻細致的鍍層,以保證在印制
為何不用電解銅或無氧銅作陽极???
銅粉多,陽极泥多。 鍍層易產生毛刺和粗糙。 銅离子濃度逐漸升高,難以控制。 添加劑消耗量大。 陽极利用率低。
磷銅陽极的特色
通電后磷銅表面形成一層黑色(或棕黑)的薄膜 黑色(或棕黑色)薄膜為Cu3P又稱磷銅陽极膜 磷銅陽极膜的作用 — 陽极膜本身對(Cu+--e→Cu2+)反應有催化、加速作用,從而 減少Cu+的積累。 — 陽极膜形成后能抑制Cu+的繼續產生 — 陽极膜的電導率為1.5X104 -1 cm-1具有金屬導電性 — 磷銅較純銅陽极化小(1A/dm2 P0.04-0.065%磷銅的陽极化 比無氧銅低50mv-80mv)不會導致陽极钝化。 — 陽极膜會使微小晶粒從陽級脫落的現象大大減少 — 陽极膜在一定程度上阻止了銅陽极的過快溶解
02
单击此处添加正文,文字是您思想的提炼,为了演示发布的良好效果,请言简意赅地阐述您的观点。
- 1、下载文档前请自行甄别文档内容的完整性,平台不提供额外的编辑、内容补充、找答案等附加服务。
- 2、"仅部分预览"的文档,不可在线预览部分如存在完整性等问题,可反馈申请退款(可完整预览的文档不适用该条件!)。
- 3、如文档侵犯您的权益,请联系客服反馈,我们会尽快为您处理(人工客服工作时间:9:00-18:30)。
电镀铜工程培训材料- 电镀铜铜具有良好的导电性和良好的机械性能,能与其它金属形成良好的金属键,获得镀层间良好的结合力。
因此,印制析制作过程中采用镀铜工艺。
1 电镀铜的机理镀液的主要成分是硫酸铜和硫酸。
在直流电的作用下,阴阳极发生电解反应,阳极铜失去子变成Cu2+溶于溶液中,阴极Cu2+获得电子还原成Cu原子。
具体反应如下:1.1 阴极反应Cu2++ 2e-? Cu副反应Cu+ + e-? CuCu2+ + e-? Cu+由于铜的还原电位比H+高得多,所以一般不会有H2析出。
1.2 阳极反应Cu ? 2e-? Cu2+副反应Cu ? e-? Cu+在足够硫酸环境下,亦有如下反应2 Cu+ + 1/2O2 + 2H+? 2 Cu2+ + H2O当硫酸含量较低时,有如下反应2 Cu+ + 2H2O ? 2 Cu(OH)2 + 2H+2 Cu(OH)2 ? Cu2O + H2OCu2O即成“铜粉”,有Cu2O出现时镀层会变得疏松粗糙。
2 电镀锡机理电镀锡与电镀铜机理一样利用电解作用获得金属镀层。
阴极反应Sn2+ + 2e- ? Sn阳极反应Sn - 2e- ? Sn2+镀锡溶液主要成分是硫酸亚锡与硫酸。
3 电镀线各药水缸成份及作用3.1 除油缸主要成份为酸性除油剂,它可以清除板面污渍,指纹及菲林碎等杂质,获得清洁的基铜表面。
3.2 微蚀缸主要成份硫酸钠和硫酸溶液,如本公司所用的也有硫酸和双氧水型。
微蚀作用可以除待镀线路与孔内镀层的氧化层,增加其表面的粗糙度,从而提高与镀层有结合力。
3.3 浸酸缸主要成份H2SO4浸酸缸可以去除铜表面轻微的氧化层,同时防止污物污染铜缸。
3.4 镀铜缸进行电化学反应的场所,主要成份硫酸铜,硫酸,盐酸以及电镀铜添加剂。
3.4.1 硫酸铜是镀浴液中的主盐,它在水溶液中电离出铜离子,铜离子阴极上获得电子沉积出镀铜层。
控制浓度50-90g/L提高其浓度可以提高允许电流密度,避免烧板,但含量过高,会降低镀液的分散能力。
3.4.2 硫酸主要作用是增加溶液的导电性。
浓度低则镀液分散能力下降;浓度高则镀液分散力较好,但镀层的延展性会降低,控制浓度8-14%3.4.3 氯离子氯离子是阳极活化剂,可以使阳极正常溶解。
浓度过低时,易出现烧板和针孔;当浓度过高时,会使镀层亮度下降,低电流区发暗甚至在阳极表面出现一层白色膜,使阳极钝化。
3.4.4 添加剂电镀添加剂可以帮助获得良好镀层,主要含有光亮剂,整平剂,润湿剂,分散剂等。
它可以使镀液获得良好的分散能力和深镀能力,使镀层有足够的强度和导电性,延展性,同时使板面镀层厚度和孔壁镀铜厚度之比接近1:1。
镀液中Cl-与添加剂协同作用将使我们获得满意的镀层。
添加剂的消耗根据电量来补加。
添加剂消耗速度大小受槽液配制,缸温,空气搅拌,电流密度等多种因素的影响。
另采用赫尔槽分析办法来进行调整。
添加剂分解后的副产物是铜缸中污染物的主要来源。
3.4.5 镀锡缸硫酸亚锡是槽液中的主盐。
硫酸提供酸性环境,另有有机添加剂,其作用与铜缸基本一致,但与镀铜缸相比,可不用补加Cl-及不需要空气搅拌。
4 操作条件对镀铜品质的影响4.1 温度温度对镀铜影响很大。
提高温度则加快添加剂的分解,增加其消耗量,镀层光亮度降低甚至镀层粗糙。
温度太低,则消耗量降低,但在高电流区易烧板。
温度控在20-300C。
4.2 搅拌空气搅拌:使用无油的空气泵,空气最好要经过滤净化。
其作用可使镀液强烈翻动,增加电镀的均匀性,同时提供足够氧气,从而使溶液中的Cu+氧化成Cu2+,消除Cu+的影响。
打气管的布置:1”管子平行阴极布置在缸底,打气孔径2-3mm,孔距80-120mm孔中心线与垂直方向成450角。
打气布置的位置亦直接影响电镀的品质。
空气搅拌的剧烈程度亦直接影响添加剂的消耗量。
同时空气搅拌亦要求镀液清洁,一般都与溶液的连续过滤配合使用。
4.3 过滤过滤可以净化溶液,及时去除机械杂质,防止铜粒出现,同时使槽液流动,将滤槽中经冷却的镀液循环入镀槽,达到控制温度的作用。
过滤要求使用5-10mm的棉芯,每小时至少过滤一次浴液。
加碳芯过滤可进一步清除缸中有机质及污染物。
4.4 摇摆机械摇摆通过机械作用使阴极产生移动,有利于增强电镀均匀性。
移动方向与阳极呈一定的角度,可促进孔内溶液的流动性,亦可及时赶去吸附有板面的小气泡。
移动幅度20-30mm,频率5-25次/分钟。
5 溶液的维护1. 定期分析调整镀液各组分的浓度,使之保持在最佳状态。
一般铜缸每两天做一次赫尔槽,分析一次氯离子,每周分析一次硫酸铜,硫酸。
2. 添加剂的补需及时:因添加剂的不断消耗,补充不及时会产生板面粗糙等问题。
根据电量损耗自动补加或经计算后手动补加。
另根据赫尔槽显示调整添加剂的含量。
3. 碳处理:电镀槽液中添加剂分解的副产物,同时干膜及板材等溶出物均会对槽液构成污染。
因此要定期做活性碳处理,处理步骤如下:1) 将镀槽液抽至碳处理缸中2) 开启加热器升温3) 450C左右时,边搅拌边加入4ml/L的H2O2,并充分搅拌两小时4) 升温至60?50C保温,继续搅拌3小时。
5) 冷却至400C,加入3-5g/L活性碳细粉,搅拌两小时。
6) 关闭搅拌器,让溶沉淀7) 将槽液过滤至贮备缸8) 贮备缸自滤,充分滤去碳粉9) 抽入镀铜缸中,经分析补料调整光剂,补加添加剂,以低电流10-15ASF电解3-4小时后试板。
6 电流控制当其它操作条件(温度,摇摆,搅拌等)一定时,镀液所允许的电流密度范围就一定了。
不同的电镀添加剂所允许的电流密度范围有所不同,但通常在8-35ASF。
电流密度不同,析铜的沉积速率也不同。
实验显示,电流密度与沉积速率仅在10-28ASF范围内大致呈线性关系。
本公司测算以22.5ASF电流密度电镀60分钟可得到1mil厚度的镀铜有了以上的关系式,则可计算电镀时电流的大小,如需获得N mil厚度之镀铜,则计算电镀时间如下:在计算时,最重要的是估算电镀面积,用计算机CAM辅助制造可较精确地计算其面积(包括孔壁面积)电镀FA制作过程1. 什么叫“FA”?“FA”是英文(First Article)缩写,意为“首部(件)制作指示”2. 为什么要做“FA”?线路板的线路分布及镀铜要求(客户要求)各有不同所以电流大小也不同,为达到客户的要求,同时避免产品大批量的坏点(镀薄/镀厚),新板都要经过小批量的试验,经检查合格后,方可批量生产,目的是降低报废降低成本。
3. 电流纸计算方法:板面积*镀铜面积*电流密度*每巴块数1) 镀铜面积:线路图形及孔壁的面积(由CAD/CAM房提供)2) 电流密度:在单位面积上通过电流的大小,目前我们用的电流密度为22.5ASF;意为:22.5A的电流通过1ft2 60分钟,可沉积,铜厚1MIL。
4. FA试作过程:1) 根据MI要求,计算电流值2) 将数据输入PP电脑ALT+2程序中3) 按正常生产条件试做一巴4) 取2块试板做切片,(由4/F IPQC负责)5) 蚀板后检查线宽、线间,线距pad 板厚,孔径等6) 根据切片报告(合格)和FA检查报告(合格)填写正本电流纸,由高工审批,复印副本并盖合格章发送生产部,5. FA常见问题及改善方法:常见问题原因影响改善方法镀厚1) 线间小2) 独立位(线)3) 电流过大? 退膜不清? 短路? 移线间? 加电镀块? 加板电镀工序? 减小电流镀薄1) 电流过小2) 大铜面位? 爆孔? 镀铜不均匀? 敷锡不良? 加大电流? 加板电镀工序7 常见问题处理坏点可能原因改善方法离层 1. 镀前微蚀不足2. 镀前板面油污3. 镀前板面因存放太久而氧化 1. 调整或更改微蚀液2. 加强板面清洁保持操作时板面洁3. 存放板时要保持干燥,清洁,且放时间不能久坏点可能原因改善方法烧板1. 含铜量太低2. 电流密度过大3. 液温低4. 光亮剂失调5. 搅拌差6. 阴阳极距离太短 1. 补充硫酸铜到规定值2. 适当降低电流密度3. 调整液温4. 补充光剂5. 检查打气状态,并调整6. 检查阴阳极,排除故障坏点可能原因改善方法溶蚀(线路缺口开路) 1. 线路或孔壁电镀后未上锡2. 夹具上残留酸液而深锡3. 镀锡偏薄,蚀板时产生蚀铜4. 线路胶迹未除尽 1. 检查电镀夹具,保持其完整性2. 加强夹具清洗,保持水洗液位3. 检查镀锡浓度4. 光剂补充(侯氏槽分析)5. 检查火牛工作状况,保证其正常工作6. 电镀前检查板面坏点可能原因改善方法针孔 1. 氯离子含量偏低2. 缸温偏低3. 光剂失调4. 搅拌不足5. 过滤不足或循环泵漏气,产生气泡6. 缸液污染严重 1. 补加HCl2. 调整缸温3. 赫氏槽分析补料或CVS分析调整4. 检查打气,保证其均匀性检查摇摆,保证摆幅,频率均匀正常5. 检查过滤泵是否漏气6. 活性碳处理孔开 1. 微蚀时间过长2. 微蚀速率过高3. 孔壁镀锡厚度不足 1. 控制微蚀时间2. 调整微蚀速率3. 镀锡缸调整参数铜粒或塞孔 1. 缸中铜粒或其它杂物2. 前工序杂质入孔 1. 拖缸板进行电解2. 改善循环系统3. 清洗缸底杂物4. 前工序(DR,PTH) 改善电镀铜培训测试一。
电镀铜的机理是什么?二。
电镀锡的作用是什么?电镀锡不良会出现什么问题?三。
电镀铜缸中有哪些成分?请简要分析添加剂的作用。
四。
电镀常见的问题有哪些?请试举一例说明其解决方案。
五。
电镀为什么要做FA?FA作用是什么?六。
影响电镀品质的操作条件有哪些?试举例说明。
七。
微蚀缸的作用是什么?微蚀缸易发生什么问题?如何对此进行控制?。