设备时间稼动率
自动化设备的稼动率与可动率

自动化设备的稼动率与可动率稼动率和可动率是衡量自动化设备运行效率和稳定性的重要指标。
稼动率指设备实际运行时间与总运行时间的比值,而可动率则是设备正常运行时间与总运行时间的比值。
本文将详细介绍自动化设备的稼动率和可动率的概念、计算方法以及提高稼动率和可动率的措施。
一、稼动率的概念和计算方法稼动率是指设备实际运行时间与总运行时间的比值,用于衡量设备的运行效率和利用率。
稼动率的计算公式如下:稼动率 = (设备实际运行时间 / 总运行时间) × 100%设备实际运行时间是指设备在某一时间段内实际运行的时间,总运行时间是指设备在同一时间段内应该运行的总时间。
二、可动率的概念和计算方法可动率是指设备正常运行时间与总运行时间的比值,用于衡量设备的稳定性和可靠性。
可动率的计算公式如下:可动率 = (设备正常运行时间 / 总运行时间) × 100%设备正常运行时间是指设备在某一时间段内没有发生故障或停机的时间,总运行时间是指设备在同一时间段内应该运行的总时间。
三、提高稼动率和可动率的措施1. 定期维护保养:设备的定期维护保养能够减少故障发生的概率,提高设备的可动率和稼动率。
2. 增加备件库存:合理的备件库存能够减少设备故障时的停机时间,提高设备的可动率。
3. 优化设备调度:合理的设备调度能够减少设备的闲置时间,提高设备的稼动率。
4. 增加设备的自动化程度:增加设备的自动化程度能够减少人为因素对设备运行的影响,提高设备的稼动率和可动率。
5. 提供员工培训:提供员工相关的培训能够提高员工对设备操作和维护的技能,减少设备故障的发生,提高设备的可动率和稼动率。
6. 引入先进的监控系统:引入先进的监控系统可以实时监测设备的运行状态,及时发现并解决潜在问题,提高设备的可动率和稼动率。
7. 进行设备性能优化:通过对设备性能的优化,可以提高设备的运行效率和稳定性,提高设备的稼动率和可动率。
总结:稼动率和可动率是衡量自动化设备运行效率和稳定性的重要指标。
自动化设备的稼动率与可动率

自动化设备的稼动率与可动率稼动率和可动率是衡量自动化设备运行效率的重要指标。
稼动率是指设备在规定时间内正常运行的时间占总运行时间的比例,可动率是指设备在规定时间内能够正常运行的时间占总运行时间的比例。
本文将详细介绍自动化设备的稼动率和可动率的定义、计算方法以及提高稼动率和可动率的措施。
一、稼动率的定义和计算方法稼动率是指设备在规定时间内正常运行的时间占总运行时间的比例。
稼动率的计算公式为:稼动率 = (设备正常运行时间 / 总运行时间) × 100%其中,设备正常运行时间是指设备在规定时间内能够正常运行的时间,总运行时间是指设备在规定时间内的总运行时间。
二、可动率的定义和计算方法可动率是指设备在规定时间内能够正常运行的时间占总运行时间的比例。
可动率的计算公式为:可动率 = (设备正常运行时间 / 总运行时间) × 100%可动率与稼动率的计算方法相同,但可动率更加注重设备的可靠性和可用性,是稼动率的一个补充指标。
三、提高稼动率和可动率的措施1. 预防性维护:定期对设备进行检修和保养,及时发现并排除潜在故障,减少设备停机时间。
2. 故障预测与预警:利用先进的监测设备和技术,对设备进行故障预测和预警,及时采取措施,避免设备故障导致的停机。
3. 提高设备可靠性:采用高质量的设备和零部件,提高设备的可靠性和稳定性,减少故障发生的可能性。
4. 优化生产计划:合理安排生产计划,避免设备过载或者闲置,最大限度地提高设备的利用率。
5. 培训操作人员:提供全面的培训,使操作人员能够熟练掌握设备的操作和维护技能,减少人为因素导致的设备故障。
6. 引入自动化控制系统:利用先进的自动化控制系统,提高设备的自动化程度,减少人为操作错误和设备故障的可能性。
7. 数据分析和优化:通过对设备运行数据的分析,找出影响稼动率和可动率的关键因素,并采取相应的优化措施。
8. 保养管理:建立完善的设备保养管理制度,定期对设备进行保养和检修,确保设备处于良好的工作状态。
设备稼动率的计算公式举例
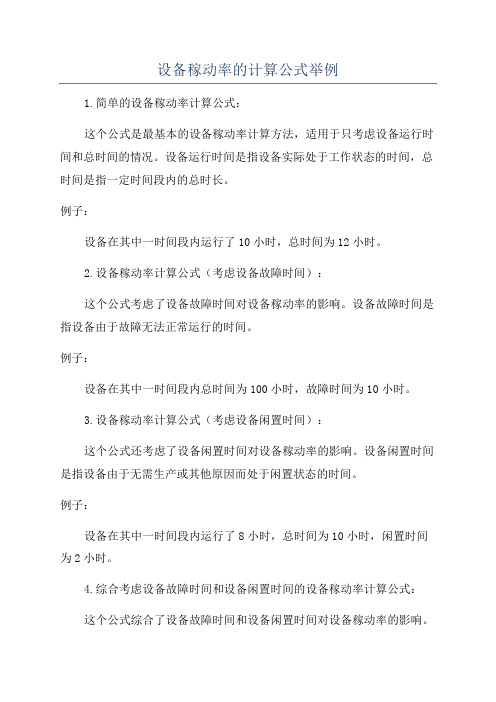
设备稼动率的计算公式举例
1.简单的设备稼动率计算公式:
这个公式是最基本的设备稼动率计算方法,适用于只考虑设备运行时间和总时间的情况。
设备运行时间是指设备实际处于工作状态的时间,总时间是指一定时间段内的总时长。
例子:
设备在其中一时间段内运行了10小时,总时间为12小时。
2.设备稼动率计算公式(考虑设备故障时间):
这个公式考虑了设备故障时间对设备稼动率的影响。
设备故障时间是指设备由于故障无法正常运行的时间。
例子:
设备在其中一时间段内总时间为100小时,故障时间为10小时。
3.设备稼动率计算公式(考虑设备闲置时间):
这个公式还考虑了设备闲置时间对设备稼动率的影响。
设备闲置时间是指设备由于无需生产或其他原因而处于闲置状态的时间。
例子:
设备在其中一时间段内运行了8小时,总时间为10小时,闲置时间为2小时。
4.综合考虑设备故障时间和设备闲置时间的设备稼动率计算公式:
这个公式综合了设备故障时间和设备闲置时间对设备稼动率的影响。
例子:
设备在其中一时间段内运行了7小时,总时间为10小时,故障时间为1小时,闲置时间为1小时。
需要注意的是,设备稼动率只是一个衡量设备利用率的指标,不能单独判断设备的运行效率,还需要结合其他指标进行综合分析。
此外,稼动率的计算公式可根据具体情况进行调整和扩展,以满足实际需求。
稼动率简介

稼动率简介时间稼动率是指相对于生产时间(负荷时间),实际生产物品的时间(稼动时间)所占的比率。
是以机器设备的稼动时间除以最大负荷时间而得。
而稼动时间是指负荷时间减掉换模、换刀具、故障、调整等的时间。
因此要提高稼动率,就必须要减少换模具、换刀具、故障、调整的损失时间。
如果能将这些损失时间减为零,那么稼动率就可以达到百分之百。
参数最大操作时间:设备可用的最大时间负荷时间:最大操作时间扣除停机(Shutdown, SD)损失;停机(Shutdown, SD)损失:计划上的休止时间,如休假、教育训练、保养等稼动时间:负荷时间扣除停止时间停止时间:包括批次转换及制程异常、设备异常停止及修复时间。
公式由以上的定义,即可算出最常用的稼动率定义-设备稼动率(也称为时间稼动率),其公式为:时间稼动率= 稼动时间 / 负荷时间目的:减少停止时间,通过资源整合,管理优化,进行资源充分利用,降低成本,提高效率。
性能稼动率/实质稼动率/速度稼动率时间稼动率并无法完全表现设备对生产的贡献程度;例如,相同的设备,相等的稼动时间,可能因效率的不同,而有不同的产能,此类效率降低的损失则称为性能损失。
在此定义速度稼动率如下:速度稼动率= 基准周期时间/ 实际周期时间基准周期时间:设备原设计产出单位产量所需的时间。
实际周期时间:目前设备实际产出单位产量所需的时间。
并定义实质稼动率与性能稼动率如下:实质稼动率= 生产量×实际周期时间/稼动时间性能稼动率= 速度稼动率×实质稼动率性能稼动时间:性能稼动时间=稼动时间×性能稼动率=稼动时间-性能损失时间其中性能损失包括速度低落的损失与短暂停机的损失。
由以上定义可知,若性能稼动率变小,则可判定生产相关设备的效率降低。
价值稼动时间与设备综合效率(Overall Equipment Effectiveness)性能稼动时间表示设备产出产品的时间,但无法表示设备产出良率的好坏,因此定义「价值稼动时间」来表示真正能产出良品的有价值时间,其定义如下:价值稼动时间=性能稼动时间×良品率而设备的有效使用程度则以「设备总合效率」来判定,其定义如下:设备综合效率(OEE)=时间稼动率×性能稼动率×良品率稼动率与开动率因翻译的不同,有的地方也将稼动率翻译为开动率,于是也有相对应的性能开动率/时间开动率等词汇,其实质上为相同内容。
自动化设备的稼动率与可动率

自动化设备的稼动率与可动率自动化设备的稼动率与可动率是衡量设备运行效率和生产能力的重要指标。
稼动率是指设备在一定时间内运行的时间与总时间的比值,可动率是指设备在一定时间内能够正常运行的时间与总时间的比值。
本文将详细介绍自动化设备的稼动率与可动率的定义、计算方法以及影响因素。
一、稼动率和可动率的定义和计算方法1. 稼动率的定义和计算方法稼动率是指设备在一定时间内实际运行的时间与总时间的比值,通常以百分比表示。
稼动率的计算公式如下:稼动率 = (设备运行时间 / 总时间) × 100%其中,设备运行时间是指设备正常运行的时间,不包括停机、维修和故障等非运行时间;总时间是指设备应该运行的总时间,包括设备运行时间和非运行时间。
2. 可动率的定义和计算方法可动率是指设备在一定时间内能够正常运行的时间与总时间的比值,通常以百分比表示。
可动率的计算公式如下:可动率 = (设备正常运行时间 / 总时间) × 100%其中,设备正常运行时间是指设备在一定时间内没有发生停机、维修和故障等非正常运行情况的时间;总时间是指设备应该运行的总时间,包括设备正常运行时间和非正常运行时间。
二、影响稼动率和可动率的因素1. 设备故障率和维修时间设备故障率是指设备在一定时间内发生故障的频率,维修时间是指修复设备故障所需的时间。
设备故障率高、维修时间长会导致设备的非正常运行时间增加,从而降低稼动率和可动率。
2. 生产计划和调度安排合理的生产计划和调度安排可以避免设备闲置和过载运行的情况,提高设备的稼动率和可动率。
同时,合理的停机维护计划可以减少设备的非正常运行时间,提高可动率。
3. 设备质量和性能设备质量和性能直接影响设备的稳定性和可靠性。
高质量、高性能的设备更容易保持正常运行状态,降低故障率和维修时间,提高稼动率和可动率。
4. 操作人员的技能和管理水平操作人员的技能和管理水平对设备的运行效率和稳定性有重要影响。
稼动率、OEE资料

一.稼动率是指设备在所能提供的时间内,创造价值时间(value added time)所占的比重二.六大损耗与OEE设备的有效使用程度则以「设备综合效率」来判定:OEE(Overall Equipment Effectiveness设备综合效率)OEE=时间稼动率(设备稼动率) x 性能稼动率 x 良品率OEE=可用率*表现指数*质量指数)(时间稼动率(可用率or设备稼动率),性能稼动率(表现指数),良品率(质量指数)1.时间稼动率(设备稼动率)=稼动时间/负荷时间=(负荷时间-停机时间)/负荷时间1.1稼动时间= 负荷时间-停机时间(换模、刀具工具更换、调整、故障停止、上下流等待、质量维持、确认、工件不良、操作失误、作业缓滞停止等时间)1.2负荷时间 = 实际作业时间[计划作业时间-提前停止时间(或+延时时间)]-计划停止时间(包含早晚例会、休息时间、始业点检、安全点检、自主保全、体制展开、试作、休假等)时间稼动率并无法完全表现设备对生产的贡献程度。
例如,相同的设备,相等的稼动时间,可能因效率的不同,而有不同的产能,此类效率降低的损失则称为性能损失。
因此定义速度稼动率,并定义实质稼动率与性能稼动率。
2.性能稼动率=实质稼动率X速度稼动率=(理论节拍*生产数量)/稼动时间2.1实质稼动率=(实际节拍*生产数量)/稼动时间2.2速度稼动率 = 理论节拍/实际节拍2.3理论节拍:以设计部门设定的参数为依据,或者依据需求量与人员的匹配,决定生产单个产品所需的时间。
制订生产计划时,拿来作为标准的依据,以决定生产产品的理论数量。
2.4实际节拍:因作业环境和限制条件等影响,实际稼动的平均时间。
节拍:生产一个单位制品需要的时间间隔2.5净稼动时间=稼动时间-[(实际节拍-理论节拍)X产量]2.6性能稼动时间=稼动时间×性能稼动率 =稼动时间-性能损失时间其中性能损失包括速度低落的损失与短暂停机的损失。
机台稼动率计算公式
机台稼动率计算公式
机台稼动率是指生产设备或生产线在一定时间内实际运行时间与总时间之比。
机台稼动率计算公式如下:
机台稼动率=(实际运行时间÷总时间)×100%
其中,实际运行时间是指设备或生产线实际运行的时间,包括生产时间、清洁维护时间、调试时间等,总时间是指设备或生产线应该运行的总时间,包括生产时间、停机时间、计划维护时间等。
举例来说,某生产线在一天内总共应该运行16小时,但实际运行时间只有12小时,其中还包括1小时的清洁维护时间和1小时的调试时间。
则该生产线的机台稼动率为:
机台稼动率=(12÷16)×100%=75%
即该生产线在该天内的机台稼动率为75%。
稼动率的计算方式
稼动率的计算方式稼动率是指设备、设施、资源等在一定时间内实际使用的时间与可使用的总时间之比,用以反映设备或资源的利用率。
稼动率的计算方法可以根据具体情况使用不同的公式。
一、简单稼动率计算方法简单稼动率是最基本的稼动率计算方法,适用于有明确型号和固定生产时间的单一设备或工序。
1.简单稼动率=实际工作时间/总可用时间其中,实际工作时间是指实际使用设备进行生产或工作的时间,总可用时间是指设备可连续使用的总时间,包括生产时间、维护时间、待机时间等。
举个例子,设备在一天内的使用情况如下:-实际生产时间:8小时-维护时间:1小时-待机时间:3小时则该设备的总可用时间为8小时+1小时+3小时=12小时,简单稼动率=8小时/12小时=0.67,即67%。
2.对于在一段时间内有多次开机和关机的设备,可以使用以下公式计算简单稼动率:简单稼动率=∑(实际工作时间i)/(∑(总可用时间i))其中,i代表第i次生产或工作周期。
实际工作时间i是指每一周期内设备实际工作的时间,总可用时间i是指每一周期内设备可连续使用的总时间。
二、综合稼动率计算方法综合稼动率是在简单稼动率的基础上进行改进,适用于多设备、复杂生产线或工艺流程中的稼动率计算。
在这种情况下,无法简单地将所有设备和时间相加,需要进行加权计算。
1.综合稼动率=∑(设备i的实际工作时间)/(∑(设备i的总可用时间)×设备i的权重)其中,i代表第i个设备。
设备i的实际工作时间是指设备i在一段时间内实际工作的总时间,设备i的总可用时间是指设备i在一段时间内总共可连续使用的总时间,设备i的权重是指设备i在整个生产过程中的重要程度或使用比例。
举个例子,生产线有三个设备:-设备A的实际工作时间:100小时-设备A的总可用时间:120小时-设备A的权重:0.4-设备B的实际工作时间:80小时-设备B的总可用时间:90小时-设备B的权重:0.3-设备C的实际工作时间:90小时-设备C的总可用时间:100小时-设备C的权重:0.3则综合稼动率=(100小时+80小时+90小时)/((120小时×0.4)+(90小时×0.3)+(100小时×0.3))。
自动化设备的稼动率与可动率
自动化设备的稼动率与可动率一、稼动率的定义和计算方法稼动率是指设备在一定时间内正常工作的时间占总时间的比例,是衡量设备利用率的重要指标。
稼动率的计算方法如下:稼动率(%)=(设备正常工作时间 / 总时间)× 100%其中,设备正常工作时间是指设备在正常运行状态下进行工作的时间,不包括停机、维修、更换工装等非正常工作时间。
总时间是指设备在一定时间段内的总工作时间。
二、可动率的定义和计算方法可动率是指设备在一定时间内能够正常运行的时间占总时间的比例,是衡量设备可靠性的重要指标。
可动率的计算方法如下:可动率(%)=(设备正常工作时间 / 总时间)× 100%可动率与稼动率的区别在于,可动率不考虑设备处于非正常工作状态的时间,只关注设备能够正常运行的时间。
三、稼动率和可动率的重要性1. 评估设备利用率:稼动率和可动率可以反映设备的利用率,帮助企业评估设备的生产效率和资源利用情况。
高稼动率和可动率意味着设备能够充分利用,提高生产效率。
2. 衡量设备可靠性:可动率反映了设备的可靠性和故障率,高可动率代表设备故障率低,能够稳定运行,减少停机时间和维修成本。
3. 提高生产计划准确性:稼动率和可动率的监控可以帮助企业更准确地制定生产计划,合理安排设备的使用和维护,避免生产过程中的停机和延误。
4. 优化设备维护策略:稼动率和可动率的分析可以帮助企业优化设备的维护策略,合理安排维护时间和维护内容,延长设备的使用寿命。
四、提高稼动率和可动率的方法1. 设备维护管理:定期进行设备维护,包括清洁、润滑、更换易损件等,减少设备故障和停机时间。
2. 运行监控和故障预警:安装监控设备,实时监测设备运行状态,及时发现故障并采取措施修复,避免长时间停机。
3. 培训和技能提升:提供员工培训,提高操作技能和维修能力,减少人为操作错误和设备故障。
4. 设备更新和升级:及时更新老旧设备,采用新技术和自动化设备,提高设备的可靠性和稼动率。
设备时间稼动率的计算方法
设备时间稼动率的计算方法设备时间稼动率是指设备在生产过程中的有效运行时间与总运行时间的比率,它反映了设备的利用率和生产效率。
在制造业中,设备时间稼动率是一个重要的指标,它直接影响着生产成本和产品质量。
设备时间稼动率的计算方法一般采用以下公式:设备时间稼动率 = (设备总运行时间 - 设备停机时间)/ 设备总运行时间 * 100%其中,设备总运行时间是指设备在某一时间段内的总工作时间,设备停机时间是指设备在该时间段内因故障、维修、调试等原因无法正常运行的时间。
为了更好地理解设备时间稼动率的计算方法,下面将结合实际案例进行详细说明。
假设某工厂生产线上的一台设备在一天内总共工作10小时,其中由于维修、故障等原因停机时间总计为2小时。
那么,设备时间稼动率的计算如下:设备时间稼动率 = (10小时 - 2小时)/ 10小时 * 100% = 80%这意味着该设备在这一天内的时间稼动率为80%。
换言之,该设备在生产过程中有20%的时间是无法正常运行的。
设备时间稼动率的计算方法可以帮助企业评估设备的利用效率和生产效率,从而及时发现设备运行中存在的问题,并采取相应的措施进行改善。
当设备时间稼动率较高时,说明设备的利用率较高,生产效率较好;反之,设备时间稼动率较低时,则需要进一步分析造成设备停机的原因,并采取相应的措施进行改善,以提高设备的时间稼动率。
除了计算设备时间稼动率,企业还可以通过其他方式来提高设备的利用率和生产效率。
首先,定期对设备进行维护保养,及时清理设备故障和故障原因,确保设备正常运行。
其次,加强设备操作员的培训,提高其操作设备的技能水平,减少操作错误和设备故障的发生。
此外,对设备进行合理的调度和排产,避免因为生产计划不合理导致设备运行时间过长或过短。
设备时间稼动率是衡量设备利用率和生产效率的重要指标,通过合理计算和分析设备时间稼动率,企业可以及时发现设备运行中存在的问题,并采取相应的措施进行改善,以提高设备的时间稼动率,从而提高生产效率和降低生产成本。
- 1、下载文档前请自行甄别文档内容的完整性,平台不提供额外的编辑、内容补充、找答案等附加服务。
- 2、"仅部分预览"的文档,不可在线预览部分如存在完整性等问题,可反馈申请退款(可完整预览的文档不适用该条件!)。
- 3、如文档侵犯您的权益,请联系客服反馈,我们会尽快为您处理(人工客服工作时间:9:00-18:30)。
准备时间
换模操 作时间
内换模
1
调整时间
整理
产品1
前外换模
产品2
后外换模
现代企业设备管理系列
稼动率提升方法
人员离岗
明确的职责 确定的休息 适时地人员定岗
1
现代企业设备管理系列
谢谢!
1
1
现代企业设备管理系列
设备时间稼动率管理记录表(单台设备)
年 月
系别
设备名称 1 2 3 4 5 6 7 8 9 10 11 12
设备编号 13 14 15 16 17 18 19
系长确认 20 21 22 23 24 25 26 27 28 29 30 31
项目
总 体
计划时间 稼动时间 停止时间
3.生产产品的质量
良品率
1
现代企业设备管理系列
A.总日历时间 10 计划停机时间(年休、定修、节假日) 10 其他计划停止(早晚会、设备点检等) 120
计划停止
B.负荷时间(总的可用生产时间)100 10 设备故障、作业停止等 10 批次转换、开机试机等
非计划停机
C.稼动时间(实际运行时间)80 10 速度损失(空转、速度降低、短暂停) D.有效运行时间(净稼动时间)70 10 不合格品时间损失 E.合格品净生产时间(价值稼动时间)60
设备时间稼动率的计算:
某一线体实行双班生产,上班时间分别是早上 8:00--20:00 及20:00—06:00,那么,每班的日历时间 则为10小时。 每班就餐时间为一个小时,上下时段各休息15分钟 ,设备点检时间为10分钟,则每班计划停机时间为1小 时40分钟。 在生产过程中,单台设备因设备模具故障出现了10 分钟的停机,因更换模具停机1小时,因人员离岗等其他 原因停机10分钟,则非计划停机时间为1小时20分钟。 由此,设备时间稼动率=(日历时间-计划停机时间非计划停机时间)/(日历时间-计划停机时间)=( 10*60-100-80)/(10*60-100)=84%
停线记录明细: 项目 设备故障 工装故障 品质异常 品质检验 物料等待 人员离岗 设备调试 (非计划) 现场整理
1
2
3
4
5
6
7
8
9
10
11
12
13
14
15
16
17
18
19
20
21
22
23
24
25
26
27
28
29
30
31
设 备 停 止 时 间 记 录
设备点检
设备调试 (计划性) 其他停止 合计
1
现代企业设备管理系列
设备停止的主要类别
设备故障 品质异常及确认
批次转换
人员离岗
物料等待
异常恢复
1
现代企业设备管理系列
稼动率提升方法
设备故障
设备的维护与保养 故障原因的分析与对策的执行 设备备件的管理 人员技能的提升
1
现代企业设备管理系列
稼动率提升方法
批次转换及物料等待
换模的标准化作业 及时的工具及物料供应 及时的原材料配送
1
现代企业设备管理系列
设备时间稼动率:
指设备相对于生产时间(负荷时间) ,实际生产物品的时间(稼动时间)所占 的比率
1
现代企业设备管理系列
影响设备时间稼动率的因素 设备时间稼动率是表达设备开停机关系 的衡量标准,在负荷时间一定的情况下 ,影响设备时间稼动率的因素就是停机 时间。
1
现代企业设备管理系列
现代企业设备管理系列
设备时间稼动率概述
屈艳龙
1
现代企业设备管理系列
培训内容 设备时间稼动率概念 设备时间稼动率的计算
提高设备时间稼动率的方法
1
现代企业设备管理系列
如何衡量设备的使 用价值?如何提高 设备的效率?
1
现代企业设备管理系列
1.设备的开动与停止
设备时间稼动率
2.设备动时的性能损失
设备性能稼动率