巴鲁夫BALLUFF压力传感器安装应注意事项
柏林精密传感器(Balluff)系列加速度传感器产品介绍说明书

Sensor systems for turbomachineryAccelerometers with external charge amplifiersCA202C A280C A 306C A 134C A901100 pC/g (400 g)-55 to 260o C 0.5 to 8000 Hz100 pC/g (500 g)-55 to 260o C0.5 to 10000 Hz 50 pC/g (100 g)-55 to 500o C 5 to 3000 Hz 10 pC/g (500 g)-196 to 500oC 0.5 to 6000 Hz 10 pC/g (500 g)-196 to 700o C3 to 3700 HzTransducer Cable Softline, armouredEC 112 - MI EC 069 - MI MI, overbraided EC 119 (390) - softline, armouredEC 222 - softlineMIEC 119 (390)For heavy-duty gas and steam turbines. Piezoelectric accelerometer for use over an extended temperature range.For heavy-duty and aero-derivative gas turbines, gearboxes, compressors and marine applications. Multi-purpose, compact piezoelectric accelerometer for use over an extended temperature range.For aero-derivative and industrial gas turbines. Piezoelectric accelerometer for use at high temperatures. Similar parts are standard with numerous OEMs.For cryogenic applications and gas turbines. Piezoelectric accelerometer for use over a very wide temperature range.For heavy-duty gas turbines. Piezoelectric accelerometer for use at extreme temperatures. Similar parts are standard with numerous OEMs.Galvanic separationExtension cable Conditioner Cable EC 153 - softline K2xx (3xx)2 or 3-wire transmissionIPC 704 in ABA 160GSI 127 galvanicseparation unit GSI 127• Power supply for 2-wireand 3-wire transmissionsystems installed inpotentially explosive environments• µA to mV conversion for long distance (2-wire)signal transmission, up to 1000 m• V to V conversion for short distance (3-wire) signal transmission• Galvanic separation, 4 kV RMS• High rejection of frame voltage• DIN rail mounting • Ex certified versionsIPC 704 conditioner • Signal conditioner for CA and CP sensors • Configurable high-pass and low-pass filters, freq. range 0.5 Hz to 20 kHz • Optional integrator for a velocity output signal • Optional 2-wire current or 3-wire voltage transmission • Ex certified versionsABA 1xx industrial housings • Protection againstmechanical damage, waterand dust (IP66 rated)• Several models and configurations, suitable for1 up to 10 conditioners • Diecast polyester or aluminium enclosure, fully insulated and corrosion resistant• Ex certified versionsEC 153 - softline EC 153 - softline Softline, armouredAccelerometers with built-in or attached electronicsCE134CE281CE311CE68SE125 µA/g (400 g)-55 to 350o C5 to 10000 Hz10 µA/g (200 g)-55 to 260oC3 to 10000 Hz50 µA/g (40 g)-55 to 125o C2 to 8000 Hz100 mV/g (80 g)-55 to 120o C0.5 to 9000 Hz2 mA/g (4 g)0 to 75o C0.2 to 750 HzTransducer Cable Extension cableEC 319 - softlineSoftline, armouredSoftlineEE 139Softline, armouredSoftline, armouredEE 143EC 175EC 175ThreadedBayonetFor heavy-duty gas turbines, aero-derivative gas turbines and compressors.Piezoelectric accelerometer with attached electronics, for use over an extendedtemperature range.For gearboxes, compressors, pumps and fans. Compact piezoelectric accelerometerwith attached electronics, for use over an extended temperature range.For heavy-duty gas and steam turbines. Piezoelectric accelerometer with built-inelectronics, for use in industrial environments.For auxiliary machines. Multi-purpose, compact piezoelectric accelerometer withbuilt-in electronics, for use in industrial environments.For slow-speed rotating machines, hydro turbines and fans. High-sensitivitypiezoresistive accelerometer.Galvanic separationJunction box CableK2xxJB 116 (JB 105)K2xxJB 116 (JB 105)Softline, armouredSoftlineSoftlineSoftline, armouredJB 1xx junction boxes• Protection againstmechanical damage, waterand dust (IP65 rated)• Several models available• Diecast polyester oraluminium enclosure, fullyinsulated and corrosionresistant• Ex certified versions2-wire transmission2-wire transmissionGSI 127 galvanicseparation unitGSI 127• Power supply for 2-wireand 3-wire transmissionsystems installed inpotentially explosiveenvironments• µA to mV conversion forlong distance (2-wire)signal transmission, upto 1000 m• V to V conversion for shortdistance (3-wire) signaltransmission• Galvanic separation,4 kV RMS• High rejection offrame voltage• DIN rail mounting• Ex certified versionsCP103C P 235C P211C P50x 232 pC/bar (20 bar)Overload up to 250 bar-196 to 700o C 2 to 10000 Hz 750 pC/bar (20 bar)Overload up to 100 bar-55 to 520oC 2 to 10000 Hz 25 pC/bar (250 bar)Overload up to 350 bar-196 to 777o C 2 to 15000 Hz 90 pC/barOverload up to 100 bar -70 to 560o C 0.5 to 20000 Hz MI MI MI MI, overbraidedEC 153EC 119 (390)Dynamic pressure sensors for combustion monitoringTransducerCable Very high temperature dynamic pressure sensor. Similar parts are standard with numerous OEMs.High temperature, very high sensitivity dynamic pressure sensor. Similar parts are standard with numerous OEMs.High-temperature dynamic pressure sensors. The GaPO 4 (gallium phosphate) piezoelectric material used ensures outstanding thermal behaviour (no pyroelectricity) and virtually constant sensitivity. Similar parts are standard with numerous OEMs. An active acceleration compensation is available.Very high temperature, compact dynamic pressure sensor. Mostly used for laboratory measurements in extreme environments.Extension cable Galvanic separationConditioner Cable K2xxSoftline Softline, armoured 3 x IPC 704 in ABA 151IPC 704 in ABA 1506 x IPC 704 in ABA 153IPC 704 conditioners• Signal conditioner for CA and CP sensors• Configurable high-pass andlow-pass filters, freq. range 0.5 Hz to 20 kHz • Optional integrator for avelocity output signal• Optional 2-wire current or 3-wire voltage transmission• Ex certified versions 2-wire transmissionGSI 127 galvanicseparation unitGSI 127• Power supply for 2-wire and 3-wire transmission systems installed in potentially explosive environments• µA to mV conversion for long distance (2-wire) signal transmission, up to 1000 m• V to V conversion for short distance (3-wire) signal transmission• Galvanic separation,4 kV RMS • High rejection of frame voltage• DIN rail mounting • Ex certified versionsProximity probes for all displacement measurements8 mV/µm or 2.5 µA/µm (2 mm range)-40 to 180o C 5mm Ø tip8 mV/µm or 2.5 µA/µm (2 mm range)4 mV/µm or 1.25 µA/µm (4 mm range)-40 to 180o C 8.2mm Ø tip 4 mV/µm or 1.25 µA/µm (4 mm range)-25 to 140oC12.7mm Ø tip Pressure proof, 100 bar (tip)4 mV/µm or 1.25 µA/µm (4 mm range)-25 to 140o C 12.7mm Ø tip Pressure proof, 100 bar (tip)Reverse mount 8 mV/µm or 2.5 µA/µm (2 mm range)4 mV/µm or 1.25 µA/µm (4 mm range)-40 to 180o C8.2mm Ø tip Reverse mount 1.33 mV/µm or 0.417 µA/µm (12 mm range)-40 to 180oC 18mm Ø tip1.33 mV/µm or 0.417 µA/µm (12 mm range)-25 to 140o C 25 mm Ø tip Pressure proof, 100 bar (tip)Transducer Cable PA 151Softline KS 107SoftlineSoftline Probe adaptor SoftlineSoftline Softline T Q 401T Q402T Q 422T Q432T Q 412T Q 403T Q423JB 118SG 101 (102)Junction box / protection Galvanic separationConditioner Cable K2xx (3xx)EA 401 (402, 403)EA 401 (402, 403)Flexible conduitMovable, armoured IQS 45x in ABA 1503 x IQS 45x in ABA 1516 x IQS 45x in ABA 153SoftlineDisplacement range from 0.2 to 12 mm. For measuring relative vibration, axial thrust, differential expansion and phase reference on turbomachinery. Transmissiondistances over 1000 m. Various body lengths and tip diameters are standard. High pressure versions, reversible mounting, armoured cable protection and probe adapters are available. These products are compliant with API 670 standards.IQS 45x conditioners• Signal conditioner forTQ 4xx probes • Optional 2-wire current or 3-wire voltage transmission • Diecast aluminium enclosure• Ex certified versions2 or 3-wire transmission GSI 127 galvanicseparation unit GSI 127• Power supply for 2-wireand 3-wire transmission systems installed in potentially explosive environments • µA to mV conversion for long distance (2-wire)signal transmission, up to 1000 m• V to V conversion for shortdistance (3-wire) signal transmission• Galvanic separation,4 kV RMS • High rejection of frame voltage • DIN rail mounting• Ex certified versionsVE210E W140L S 12020 mV / mm/s(1000 mm/s)-29 to 204o C 10 to 1000 Hz 50 mV / mm/s 50 µA / mm/s (100 mm/s)-25 to 80oC0.5 to 400 Hz20 mV / mm/s(1000 mm/s)-29 to 121o C10 to 1000 Hz0.2 to 2 mm ice -55 to 120oC2 to 33 mm -15 to 125o CEC 119 - softline, armoured EC 440 - 3-wire (voltage transmission)EC 439 - 2-wire (current transmission) Velocity sensorsIce detection systemAir gap monitoring system Transducer Extension cable ED 121 - softline ED 120 - softlineC V213C V214For low-speed machines such as hydroelectric turbomachinery. Low-speed velocity transducer with a stainless steel body and a protection rating of IP68, ideal for moist or corrosive environments. The body of the VE 210 transducer includes the signal conditioner electronics.For hydro and steam turbines. Low-speed velocity transducers, resistant to dust and moisture (IP64 rated).For large hydroelectric generators. Monitors the air gap between the rotor and stator.For all gas turbines. Detects initiation of ice on gas turbine inlets. Used by turbine de-icing systems to optimise the use of bleed air.Controller Junction box Conditioner Cable ILS 730 in ABA 151JB 116 (105)K2xx DIC 413K509 (709)ILS 730 conditioner• Signal conditioner for LS air gap transducer• Three voltage-based outputs (pole profile, rotor profile, min. gap); oneselectable 4-20 mA output (factory setting)• Diecast aluminiumenclosure 2-wire transmissionComplete monitoring solutionsOne sourceRequest a complete solution from Meggitt. In our facility in Switzerland more than 600 employees combine their expertise and commitment to design and build all parts of our system: sensors for harsh environments (measuring vibration, dynamic pressure, displacement, blade tip clearance, etc), high performance monitoring systems and software. Our sales and support network delivers outstanding service worldwide.Plant asset management systemTurbine health management systemPiezoelectric Dynamic pressure Proximity Piezoelectric MicrowaveCase studiesHeavy-duty gas turbine: Siemens SGT5-4000F Combustion and vibration monitoring (VM600 with CP and CA sensors)The SGT5-4000F (V94.3A) dry low-NO X gas turbine (GT) is one of the most powerful in operation, designed for large-scale applications with more than 280 MW ISO output. Meggitt is the exclusive supplier of protection and monitoring equipment for this GT, Siemens’ proven workhorse, with more than three hundred units in operation worldwide.One of the major industrial challenges with heavy-duty GTs is to combine the highest possible efficiency with extremely low NO X emissions and lowcombustion temperatures. Measuring the dynamic pressure at different locations in the combustor is a proven way to control combustion. Thus, pulsation monitoring systems are essential during both tuning and operation.The sensors and monitoring equipment provided by Meggitt allow Siemens to control combustion parameters such as fuel injection, which leads to extremely low emissions, reduced fuel consumption and long intervals between major inspections. Our sensing and monitoring systems on the SGT5-4000F include extreme temperature dynamic pressure sensors (CP 216), high sensitivity piezoelectric accelerometers (CA 201 and CA 901) and protection and monitoring systems (VM600).Meggitt is proud to have contributed to making theSGT5-4000F one of the most efficient GTs availablefor power generation applications.Hydro turbine-generator: Cahora Bassa hydro power plant (Mozambique)Air gap and vibration monitoring (VM600 with CE, LS, SE and TQ sensors)The Cahora Bassa dam on the Zambezi river was completed in 1975 and renovated in 2003; its plant comprises five Francis turbines with a total power of 2.1 GW. Within the renovation project, Alstom selected Meggitt to provide machinery vibration and generator air gap sensors with a networked protection and condition monitoring system. Condition monitoring of hydroelectric generators is critically important, especially monitoring the distance between the rotor poles and the stator walls, called air gap. To increase efficiency in generators, the air gap is reduced to a minimum. However, both the stator and the rotor on large hydroelectric machines can be quite flexible and their shape and location are affected in operation by centrifugal, thermal and magnetic forces. This means that the air gap can only be effectively measured while the generator is in service. In the absence of effective monitoring, efficiency would decrease and potential machine damage could occur.In Cahora Bassa, each generator is equipped with a capacitive air gap measurement system (4x LS 120 sensors with ILS 730 conditioners). This on-line system is used when the machine is rotating and withstands the extremely high magnetic fields in the air gap. Furthermore, each turbo generator has piezoresistive, low-noise, low-frequency SE 120 accelerometers to measure the bearings’ absolute vibrations. On rotating parts, the relative shaftSGT5-4000F (© Siemens AG)Balance-of-plant: Yonghung thermal power plant (South Korea)Proximity, displacement and vibration monitoring (VM600 with TQ and CE sensors)Yonghung is the largest coal-fired power plant in South Korea. Each 870 MW supercritical unit is designed for variable pressure operation at 3600 RPM and 560°C. Yonghung is designed with the philosophy of preserving the environment using two stage combustion with low-NO X burners followed by selective catalytic reduction.To ensure efficient plant operation and to achieve their environmental objectives, Yonghung TPP has 22 VM600 racks that provide over 800 dynamic measurement points on units 3 and 4. These Meggitt systems secure and monitor a variety of machines for the steam turbine and the balance-of-plant in Yonghung, such as BFP (boiler feed pump) turbines, BFP motors, forced daft fans, primary air fans, condensate pumps (booster and water), blowers and air compressors.At Yonghung TPP, Meggitt’s highly reliable sensors for harsh environments measure a range of vibration and displacement characteristics. Proximity probes (TQ 402) and piezoelectric accelerometers (CE 680) measure shaft position, relative shaft vibration (x-y), rotational speed of shaft and bearing broad-band absolute vibration. Furthermore, Vibro-Meter sensors on the primary air fan enable the pre-heater system to use hot air to remove moisture from coal before the combustion process, which reduces NO X emissions. The machinery protection functions and the condition monitoring functions of the VM600 system then process the signals and provide a complete data overview. This is necessary to maintain an efficient plant operation through diagnostics and plant health management.vibration is performed by the TQ 402 proximity probes. The stator’s structural vibrations are monitored with compact piezoelectric accelerometers (CE 680). Coupled with our sensors, the VM600 protection and condition monitoring system ensures the highest safety level during operation.Early detection of air gap anomalies using the equipment supplied by Meggitt enables condition monitoring of Cahora Bassa hydroelectric generators. As a result, plant efficiency is optimised, generator damage can be avoided and operators can more efficientlypredict and plan maintenance outages.Cahora Bassa HPP (courtesy of Hidroelectrica de Cahora Bassa)Yonghung TPP (courtesy of Vibro Korea)。
巴鲁夫超声波传感器常见故障及处理方案 传感器维护和修理保养

巴鲁夫超声波传感器常见故障及处理方案传感器维护和修理保养巴鲁夫BALLUFF超声波传感器常见故障及处理方案1、通电后不工作,无显示,传感器无声响原因:①电源未接通,或正负极接反。
②工作电压太低,物位仪未工作或太高,仪器已坏。
解决方法:①检查线路,按说明书连接线。
②使用12—24V直流电源,与经销商联系。
2、传感器有工作声,无显示原因:①已进行过程序关显示操作。
②曾接过高压,显示芯片已损坏。
解决方法:①按B键打开显示。
②与经销商联系。
3、有显示有声响,但数字不随距离更改而变化原因:①输入工作电压太低,超声波物位仪末正常工作。
②超声波物位仪的传感器或功率驱动器已损坏。
解决方法:①使用12—24V直流电源。
②与经销商联系。
4、有显示,有声响,测量值乱跳或数值不随距离变原因:①物位仪安装太歪斜。
②脉冲强度设置不当,造成余振或衍射大。
③有两台以上的物位仪在工作,造成相互干挠。
④工况区电磁干挠太大。
解决方法:①将传感器轴线调整到与目标平面垂直。
②一般1—3m内量程,发射脉冲强度为2—5.③设法除去相互干扰。
④找出干挠源,屏敞干挠。
5、传感器有声响,显示器显Lon或out原因:①超出物位仪量程。
②测面距探头太近。
③不恰当的用在高粉尘。
高泡沫。
高蒸汽环境中或工作温度太高或太低;脉冲强度设置不当。
解决方法:①将物位仪实际量程调至物位仪工作量程之内。
②将应用环境调整至要求范围。
③修改发射脉冲强度大小,至显示稳定。
6、传感器有声响,物位显示值误差十几公分以上原因:①安装不垂直,造成多次反射。
②安装太靠罐壁,声波中途反射。
③检查差值bAd的设定是否正确。
④检查温度的示值是否正常。
解决方法:①请反复调整安装位置。
②正确设定bAd值。
③若温度差大,可调整“CB”值到正确值。
7、4—20mA输出不正常;偏高,偏低,跳动原因:①负载电阻过大。
②量程FS被修改、输出微调参数AL 或AH被修改。
③电源整流、滤波不好。
④通电时间不够。
巴鲁夫 机床传感器 说明书

用于机床的传感器严酷环境中的高精度反馈巴 鲁 夫机床制造水平的创新与进步,决定性地推动了工业生产过程的技术变革。
自动化技术的进步,又通常源于传感器技术的提升。
机床行业正在不断经历着,并将继续经历一系列技术进步——提高产品性能,灵活性及可靠运行时间。
巴鲁夫,作为数十载服务机床制造业的传感器制造商,将继续致力于以“服务机床行业”为宗旨,推动机床制造业的发展。
用于机床的传感器严酷环境中的高精度反馈电容开关 BCS机床应用的最佳选择圆柱形外壳系列光电传感器应用于机床工业圆柱形外壳机电式单档位/多档位组合行程开关和限位开关带安全开关元件的机电式单档位/多档位组合行程开关和限位开关单档位及多档位机电式/感应式组合行程开关和限位开关作为主令控制设备几乎用于所有自动控制的应用中,尤其用于传输线和机床的定位和限位。
无论您在何处使用,我们的机械结构均能保证安全可靠的开关动作。
它们专为确保在极端严酷的应用环境(诸如振动、冲击、撞击或冷却液润滑液侵蚀)中可靠应用而开发设计,数十年的应用证明了它们的价值。
我们的单档位及多档位组合行程开关和限位开关能够提供符合DIN 43697和DIN 43693标准以及满足特殊应用需求的外壳。
种类齐全的附件能够满足客户的特殊应用条件和结构。
机电式和感应式单档位/多档位组合行程开关和限位开关自动控制的经典之作BNS多档位组合行程开关快速更换顶杆模块的问题解决专家www.balluff.co对刀具最优化的计划和管理是现代生产设备无差错刀具安装,保证停机时间最短的必要因素。
刀具管理的关键组件是刀具识别系统。
所有的刀具信息,诸如ID 识别码,刀具寿命,几何尺寸等,均可保存在粘结在刀具上的记忆芯片中。
数据的载入(和读回)无需接触,因此无磨损。
当将刀具安装到机床上,数据会随即读入机床的存储器中,防止错误的数据写入。
当刀具从机床上卸下时,经过改写的数据会刷新存储芯片。
采用识别系统的另外一个优势是能够最优化管理刀具的寿命。
压力传感器安装注意事项
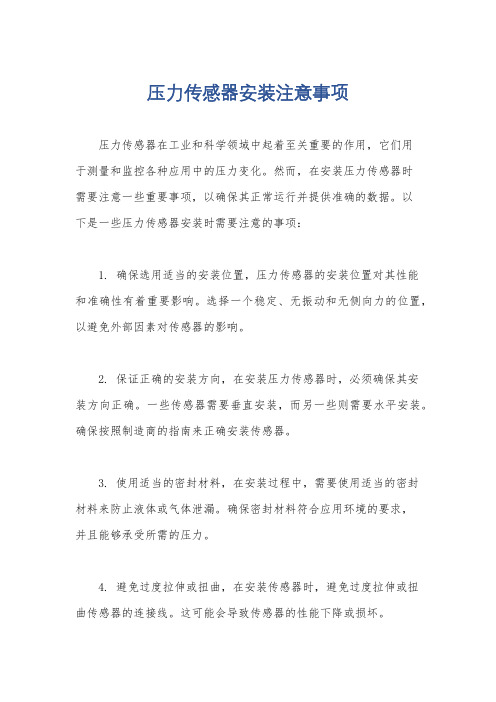
压力传感器安装注意事项压力传感器在工业和科学领域中起着至关重要的作用,它们用于测量和监控各种应用中的压力变化。
然而,在安装压力传感器时需要注意一些重要事项,以确保其正常运行并提供准确的数据。
以下是一些压力传感器安装时需要注意的事项:1. 确保选用适当的安装位置,压力传感器的安装位置对其性能和准确性有着重要影响。
选择一个稳定、无振动和无侧向力的位置,以避免外部因素对传感器的影响。
2. 保证正确的安装方向,在安装压力传感器时,必须确保其安装方向正确。
一些传感器需要垂直安装,而另一些则需要水平安装。
确保按照制造商的指南来正确安装传感器。
3. 使用适当的密封材料,在安装过程中,需要使用适当的密封材料来防止液体或气体泄漏。
确保密封材料符合应用环境的要求,并且能够承受所需的压力。
4. 避免过度拉伸或扭曲,在安装传感器时,避免过度拉伸或扭曲传感器的连接线。
这可能会导致传感器的性能下降或损坏。
5. 使用适当的安装工具,在安装过程中,使用适当的工具来紧固传感器。
确保不要使用过大的力量,以免损坏传感器。
6. 进行校准和测试,在安装完成后,需要进行校准和测试以确保传感器的准确性和稳定性。
校准过程应该按照制造商的指南进行,并且需要在实际应用条件下进行测试。
总之,正确的安装是确保压力传感器正常工作和提供准确数据的关键。
遵循制造商的指南,并且在安装前仔细阅读安装手册是非常重要的。
通过遵循这些注意事项,可以确保压力传感器在应用中能够可靠地工作并提供准确的数据。
压力传感器的使用注意事项

压力传感器的使用注意事项随着科技的不断进步和应用领域的不断扩大,压力传感器成为了现代工业领域不可或缺的一部分。
无论是在汽车制造、机器人技术还是医疗设备领域,压力传感器都扮演着重要的角色。
然而,尽管这一技术的发展带来了巨大的便利和效率提升,但在使用压力传感器时,我们也需要注意一些事项,以确保其正常工作并发挥出最佳性能。
首先,我们需要注意安装压力传感器时的位置选择。
传感器的位置直接影响到其测量结果的准确性。
通常情况下,我们应选择位于测量点附近的合适位置安装传感器。
避免将传感器直接安装在液体或气体的流动区域,否则,可能会导致流体的速度变化引起的测量误差。
此外,我们还需要注意避免将传感器暴露在高温或腐蚀性环境中,这可能会对传感器产生损坏。
其次,我们应当正确连接压力传感器和测量仪器。
在连接过程中,我们需要确保传感器与测量设备之间的电缆连接牢固可靠,并避免弯折或拉伸。
同时,在接线时需要注意引脚的正确连接,错位的引脚会导致测量结果的错误。
此外,应当使用与传感器规格相匹配的电缆,并避免使用过长或过短的电缆,以免影响传感器的工作稳定性。
另外,我们也需要注意对传感器的保养与维护。
定期清洁传感器表面,确保其免受灰尘、油渍等污染物的侵袭。
尽量避免碰撞或震动传感器,以防损坏传感器内部的敏感零件。
当发现传感器出现故障或工作异常时,我们应及时排除故障或更换传感器以保证工作正常。
此外,我们还需要关注传感器的工作环境。
在一些特殊的工作环境下,如高温、低温、高压或低压环境,我们需要选择适应性更强的传感器。
不同环境对传感器的要求不同,需要注意选择符合要求的传感器型号。
此外,在使用过程中,应合理安排工作时间和工作周期,避免过载使用传感器,以免加速传感器的老化,影响其使用寿命。
最后,我们应当学会正确解读和分析传感器的测量结果。
虽然传感器能够准确地获取压力信号,但对于测量信号的分析和应用还需要进一步的加工和研究。
在实际应用中,我们需要根据不同的场景和需求设置合理的测量范围,以减小测量误差。
巴鲁夫位移传感器说明书

系列 冲击负载 振动 极性反接保护 过电压保护 绝缘强度 外壳防护等级 符合 IEC 60529 外壳材料 安装方式 10.2 mm 不锈钢管耐压强度 8 mm 不锈钢管耐压强度 连接方式 电磁兼容性测试: 无线电放射干扰 (RF) 静电干扰 (ESD) 电磁场干扰 (RFI) 瞬间高速干扰脉冲 (BURST) 因高频场感应干扰引起的 线路噪声 标准额定检测长度 [mm] 直径8 mm金属管 检测长度至1016 mm
BTL5-E1_-M_ _ _ _-... 4...20 mA或20...4 mA ≤ 500 Ω ≤ 0.66 µA
BTL5-C1_-M_ _ _ _-... 0...20 mA或20...0 mA ≤ 500 Ω ≤ 0.66 µA
BTL5-G11-M_ _ _ _-... –10...10 V及10...–10 V 最大 5 mA ≤ 5 mV ≤ 0.33 mV
一般数据 模拟量接口 数字脉冲接口 SSI 接口 CANopen 接口 PROFIBUS-DP 接口 用于液压缸定位 的传感器 定位磁环与浮子 安装提示 特殊型号系列
BTL5-A11... 0 V 输出 10...0 V 0...10 V GND +24 V DC (GND)
≤ 5 µm 系统分辨率/最小 2 µm f = 2 kHz ±100 µm(至500 mm 额定检测长度) ±0.02 % (500...4500 mm 额定检测长度) [150 µV/°C + (5 ppm/°C × P × U/L)] × ∆T [0.6 µA/°C + (10 ppm/°C × P × I/L)] × ∆T 20...28 V DC ≤ 150 mA 有 Transzorb保护二极管 500 V DC(外壳对地) –40...+85 °C –40...+100 °C
巴洛夫(Balluff)阀门和变压器传感器产品概述说明书

5.1/cylindert Technical Reference pPart Number Index7Accessories 6Connectors 5Cylinder & Valve SensorsCylinder &Valve Sensorso Product Overview Cylinder & ValveCylinder &Valve Sensors ContentsContents Selection GuideMagnetic Field Sensors –BMF 103–BMF 273–BMF 303–BMF 305–BMF 307–BMF 315–BMF 21–BMF 32–BMF Prox Style –Installation/Mounting –BIL Magneto-Inductive Strokemaster ®Cylinder Position Sensors High Pressure Sensors Power Clamp &GripperCylinder & Valve SensorsCylinder sensors are used to provide end-of-stroke and position detection for hydraulic and pneumatic cylinder applications.Hydraulic cylinder walls are typically made of steel. Since inductive and magnetic fieldsensors cannot “see” through the steel cylinder wall to detect the piston inside, hydrauliccylinders use pressure-rated inductive sensors that can handle direct exposure to pressurized hydraulic fluid in the cylinder to provide end-of-stroke detection. A specialized inductive sensor is bolted or threaded into the cylinder end cap. The sensing face of the inductive sensor directly detects the cylinder rod or cushion as it reaches its end of travel.For non-contact, wear-free position detection of pneumatic cylinder piston position, Balluff magnetic field sensors use magneto-resistive technology to detect the piston magnet through the aluminum wall of the cylinder. Typically two sensors areemployed to provide end-of-stroke detection in both directions, or can be placed anywhere along the length of the cylinder to detect cylinder position.Advantages of Balluff magnetic fieldsensors include universal compatibility with either “Hall Effect” or “Reed Switch” cylinder magnet polarizations, reduction or elimination of double switch points, higher noise immunity,and elimination of electrical contact wear and sticking. Magnetic field sensors are available in a variety of cylinder-friendly mountingconfigurations, as well as with special features like weld field immunity.5.2Selection Guide 5.5BMF 103 Compact 5.8BMF 273 C-Slot5.9BMF 303 Miniature Slot Mount5.12BMF 305 Universal & Universal Metal 5.22BMF 307 T -Slot5.24BMF 315 Drop In T -Slot 5.27BMF 21 Tie-Rod5.29BMF 32 Rugged Duty5.32BMF 07M, 08M, 12M Prox Style 5.34Installation Hints5.35BMF T echnology Comparison5.36BIL Magneto-Inductive Position Sensor 5.41Strokemaster ®5.45High Pressure Sensors 5.52Power Clamp & GripperC o u r t e s y o f C M A /F l o d y n e /H y d r a d y n e ▪ M o t i o n C o n t r o l ▪ H y d r a u l i c ▪ P n e u m a t i c ▪ E l e c t r i c a l ▪ M e c h a n i c a l ▪ (800) 426-5480 ▪ w w w .c m a f h .c o mCylinder &Valve SensorsSelection GuideC o u r t e s y o f C M A /F l o d y n e /H y d r a d y n e ▪ M o t i o n C o n t r o l ▪ H y d r a u l i c ▪ P n e u m a t i c ▪ E l e c t r i c a l ▪ M e c h a n i c a l ▪ (800) 426-5480 ▪ w w w .c m a f h .c o mSelection GuideCylinder &Valve Sensors5.4Selection GuideSelection GuideBILStrokemasterC o u r t e s y o f C M A /F l o d y n e /H y d r a d y n e ▪ M o t i o n C o n t r o l ▪ H y d r a u l i c ▪ P n e u m a t i c ▪ E l e c t r i c a l ▪ M e c h a n i c a l ▪ (800) 426-5480 ▪ w w w .c m a f h .c o m。
巴卢夫超声波传感器说明书
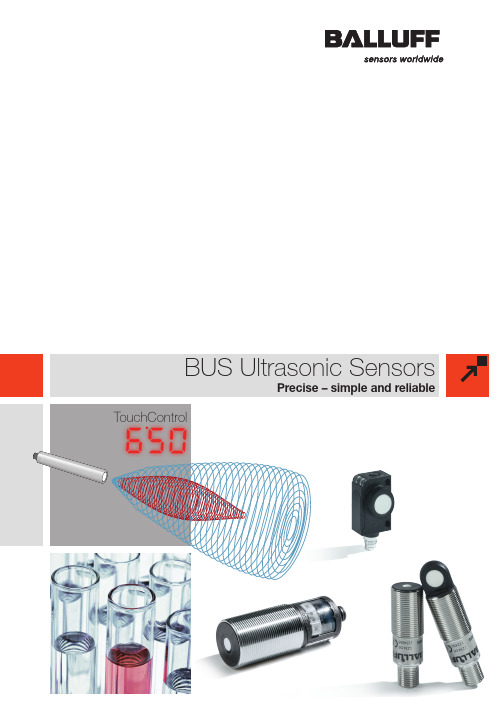
BUS Ultrasonic SensorsPrecise – simple and reliable TouchControl2Use maximumprecision with Balluffultrasonic sensors. With over 50 years of sensor experience, Balluff is a leading globalsensor specialist with its own line of connectivity products for everyarea of factory automation. Balluff is based in Germany and has atight international network of 54 representatives and subsidiaries.Balluff stands for comprehensive systems from a single source, con-tinuous innovation, state-of-the-art technology, highest quality, andgreatest reliability. That's not all: Balluff also stands for exceptionalcustomer orientation, customized solutions, fast worldwide service,and outstanding application assistance.High-quality, innovative products – certified in accordancewith DIN ISO 9001:2008 (EN 29001) – are a secure foundation foroptimized value creation for our customers.Whether electronic and mechanical sensors, rotary and linear trans-ducers, identification systems or optimized connection technologyfor high-performance automation, Balluff masters not only the entiretechnological variety with all of the different operating principles, butalso provides technology that fulfills regional quality standards andis suitable for use worldwide. Wherever you are in the world, Ballufftechnology is never far away. You won't have to look far for younearest Balluff expert.Balluff products increase performance, quality and productivityaround the world every day. They satisfy prerequisites for meetingdemands for greater performance and cost reductions on the globalmarket. Even in the most demanding areas. No matter how stringentyour requirements may be, Balluff delivers state-of-the-art solutions.Ultrasonic Sensors Precise – simple and reliableRegardless of color and materialBUS ultrasonic sensors are perfect for distance measurement or position detection of granules, fluids and powders. They measure fill levels, heights and sag without making contact as well as count and monitor the presence of objects.They are extremely versatile, operate independently of color and sur-face finish, and are not affected by transparent objects that generate strong reflections.Ultrasonic sensors are precision all-rounders designed for critical situations. Dust, dirt and steam do not pose a problem.Broad detection range – high precisionTheir detection range extends from 20 mm to 8 m, meaning that even longer object distances can be handled without problem. Their high resolution and small blind zones ensure extreme precision. Integral synchronization means that the sensors do not interfere with one another.Switching and analog variantsOur BUS ultrasonic sensors differ form one another in their output signal. Each series is available as a switching or analog version, whereby all analog versions are available with voltage or current output (0...10 V or 4...20 mA). The BUS M30 includes variants with two switching outputs, one switching and one analog output or two switching outputs and one analog output so that one sensor can adopt the function of a second sensor.IO-LinkBUS 18M sensors with push/pull output are equipped with anIO-Link interface that enables a change from SIO mode to IO-Link mode.Table of contents 3 Media 4 Industries, application areas 5 Application areas, sensor selection 6 Modes 7 M30 tubular-style housing 8 M18 tubular-style housing 10 R06 block-style housing 12 M12 tubular-style housing 14 Q80 block-style housing 1534Ultrasonic SensorsMediaLiquidsClear water, cloudy liquids, oils or black coffee — ultrasonic sensors can be used with nearly any liquid. The liquid surface should have no foam.ColorsRed, green, yellow or blue — all make no difference to Balluff ultrasonic sensors: they reliably detect all colors.ContrastsBlack objects against a black background or white on white — even with weak contrasts, our BUS sensors measure without ifs and buts.Transparent layersGlass plates, Plexiglas and razor thin foils — BUS ultrasonic sensors reliably detect transparent layers.Material surfacesWhether velvet, wool or leather — nearly all clothing materials can be simply detected with our BUS ultrasonic sensors.Surfaces of bulk materialsFine sand, shavings or coarse-grainedmaterials — in the areas of fill-level measure-ment, our ultrasonic sensors are unbeatable.The all-rounders, even for difficult environmentsBecause the distance to the object is de-termined via a sound transit time, ultrasonic sensors have excellent background suppres-sion. With their transit time measurement, ultrasonic sensors can record the measuredvalue with highly-precise resolution. Some sensors to even 0.025 mm.The sensors are able to measure in dusty air or through paint spray mist. Nearly all materi-als that reflect the sound are detected. Eventhin foils, crystal clear materials and different colors are no problem for ultrasonic sensors. Thin deposits on the sensor membrane do not affect sensor function.Ultrasonic SensorsIndustries, application areasHandling and automation Bottling and packaging Automotive industryBUS ultrasonic sensors are particularly wellsuited for the following industries■■Handling and automation■■Specialty machine construction■■Automotive industry■■Bottling and packaging■■Pharmaceutical industry■■Plastic and rubber industry■■Timber and furniture industry■■Paper and printing industry■■Conveying■■Commercial vehicles■■Scales■■Agricultural machinery■■Food processing machinery■■Office and information technology■■Construction andbuilding material machinery■■Textile machineryUltrasonic sensors can be used in many application areasOther applications on the next pageHeight andwidth measurementThrough the use ofmultiple BUS M30 orBUS _18M ultrasonicsensors, three-dimen-sional measurements canbe made for everythingfrom small boxes to largecartons.Foil tear monitoringUltrasonic sensorswith switching outputcan be used for foil tearmonitoring. If largewaves are formed in thefoil, the sensor shouldbe operated as a diffusereflective sensor. Thisoperating mode functionsreliably even if the soundis reflected by waves inthe foil.Detection of peopleIf people need to bedetected, a sensorshould be used that hasan operating scanningrange that is considerablygreater than the requiredmeasurement distance.The greater the operatingscanning range, the lowerthe ultrasonic frequency.And the better absorbentpieces of clothing, suchas wool, can be detected.Presence verificationBUS detect filled orempty pallets andmeasure the content oftransport containers. If abox or a container is tobe inspected with multiplesensors, they can besynchronized with eachother.Robot positioningDue to their smalldimensions, BUS areideally suited for exactlypositioning robot arms:BUS_18M ultrasonicsensors in threadedsleeve and BUS R06K inblock-style housing. 56The red areas are measured with a thin round rod (Ø 10 mm or 27 mm, depending on sensor type) and show the typical working range of a sensor.To obtain the blue areas, a plate is moved into the sound fields from the side. In doing so, the optimum angle of the plate to the sensor is set. This is thus the maximum detection range of the sensor.It is not possible to evaluate ultrasound reflections outside of the blue sound cones.Detection rangesDefinitions■■Blind zoneThe blind zone defines the smallest reliable scanning range of the sensor. There must be no objects or interfering reflections within the blind zone, as measurement errors may otherwise occur.■■Operating scanning rangeThe operating scanning range is the typical working range of a sensor. For objects with good reflective properties, it can also be used up to its limiting scanning range.■■Detection rangeThe detection range is measured using various standard reflectors.ObjectScanning rangeLimiting scanning rangeSensor selectionImportant selection criteria for an ultrasonic sensor are its scanning range and the associated, three-dimensional detection range.Fill-level monitoring In silos, bunkers, contain-ers – for all bulk materials (e.g., sand, gravel, coal, grain), our ultrasonic sen-sors are ideal.PositioningWhen scanning glass plates or other smooth and flat surfaces, make certain that the ultra-sound strikes the surface at a right angle.Object detectionBUS ultrasonic sensors sort containers and parts with different heights. BUS count objects. And with absolute reliability.Wire-breakage monitoringWhen winding and unwinding a wire rope, ultrasonic sensors with analog output detect its position on the layer.Stack-height detection Whether wooden boards, glass plates, paper or color plastic plates, BUS ultrasonic sensors measure stack heights with high precision.Ultrasonic SensorsModesThe ultrasonic sensor as a diffuse reflective sensor is theclassic operating mode. Compared to other sensor principles, it hassuperior background suppression. During operation, the switchingoutput is set as soon as the object is located within the set switchingdistance. The switch point has a hysteresis. The operating mode issuitable for, e.g., counting objects on a conveyor belt or for perform-ing presence verification.The ultrasonic sensor in window mode is an extended functionof the ultrasonic diffuse reflective sensor. In this case, the switchingoutput can only be set if the object is located within a window thatis defined by two window limits. This can be used to monitor, e.g.,the correct bottle size in a bottle crate. Bottles that are too tall or tooshort are sorted out. Window mode and the diffuse reflection ultra-sonic sensor can be set on all ultrasonic sensors that are equippedwith teach-in.The function of the diffuse reflection ultrasonic sensor is similar to that of a photoelectric sensor. Any reflector, such as a metal sheet, is sufficient. In window mode, the ultrasonic sensor is set so that the permanently mounted reflector lies within the window. The ultrasonic sensor returns a signal as soon as an object fully covers the reflector. It plays no role here whether the object completely absorbs or reflects away the sound. This operating mode is therefore used for materials than can be only poorly reflected, such as foam, or for scanning objects with irregular surfaces.Ultrasonic sensors with analog output output the measured dis-tance value as a voltage that is proportional to distance (0...10 V) or as current that is proportional distance (4...20 mA). For the ultrasonic sensors with analog output, the sensor-near and sensor-distant window limits of the analog characteristic as well as a rising or falling characteristic can be set. Depending on the sensor model and win-dow width, the resolution is between 0.025 mm and 0.36 mm. Ultrasonic sensors with IO-Link enable gapless communication through all levels of the system architecture: from the sensor to the top fieldbus level. Transmission of the measured distance value to the controller is bit serial.Set windowSetanalog windowSetwindowReflector Set switching distance7Ultrasonic SensorsM30 tubular-style housingInspecting transport boxes for completeness Performance shows up on conveyor belts. Multiple ultrasonic sensors simultaneously monitor transport containers for completeness. Reflective, transparent or different-colored surfaces are reliably detected. Inmultiplex operation, mutual interference of the sensors is prevented.TouchControlWith TouchControl, all settings are made on the sensors. The three-digit LED indicator continuously displays thecurrent distance value and automatically switches between mm and cm display. Two buttons are used to call up the configuration and navigate through the self-explanatory menu structure.Scanning range ■■Display with direct, measured value output for immediately visible results■■Numeric setting of the sensor via the display for completely presetting the sensor■■Automatic synchronization and multiplex operation for simultaneous operation of up to ten sensors■■5 scanning ranges with a measuring range from 30 mm to 8 m ■■1 or 2 switching outputs in PNP- or NPN-design ■■Analog output 4...20 mA and 0...10 VAutomatic changeover between current and voltage output ■■Analog output plus switching outputfor measurement that is proportional to distance with an additional limit value ■■Teach-in via 2 buttonsfor simple, menu-driven commissioning8Ultrasonic SensorsM30 tubular-style housingYou can find additional electrical accessories in our catalog Industrial Networking and Connectivity .You can find additional mechanical accessories in our catalog Accessories Line .9Ultrasonic SensorsM18 tubular-style housingControl foil sag and monitor roll diameterUsing an ultrasonic sensor with analog output, the material on a roll or a coil is detected and the roll drive or a brake readjusted. Another sensor with analog output readjusts the material infeed at the dancer roller as a function of the cable loop.■■Variant with 90° angled headfor individual installation situations ■■IO-Link interfacefor supporting the new industrial standard■■Automatic synchronization and multiplex operation for simultaneous operation of up to ten sensors■■4 scanning ranges with a measuring range from 20 mm to 1.3 m ■■1 push/pull switching output PNP- or NPN-switching ■■Analog output 4...20 mA or 0...10 V for analog distance measurements ■■Teach-in via control line (pin 5)IO-Link — the new standardWith the IO-Link interface, the prerequisites are filled for gapless communication through all levels of the system architecture all the way to the sensor. Commission-ing and maintenance of a machine are simplified and productivity increased.10Ultrasonic SensorsM18 tubular-style housingYou can find additional electrical accessories in our catalog Industrial Networking and Connectivity .You can find additional mechanical accessories in our catalog Accessories Line .BUS M18… straight BUS W18… angled11Ultrasonic SensorsR06 block-style housing■■Small ultrasonic sensor in block-style housing makes possible completely new solutions■■Same construction as many optical sensors a true alternative in critical applications ■■Option for focusing attachment for challenging measurement tasks■■■■1 switching output in PNP or NPN design ■■Analog output 4...20 mA or 0...10 V ■■Teach-in via a buttonFill-level measurement in narrow containersOn a rotary indexing table, narrow containers are filled with liquid or solid media. The ultrasonic sensor then checks the exact filling level.Focusing attachmentFor fill-level measurement through tiny openings with diameters to 5 mm, the sensor with focusing attachment is positioned directly over the measure-ment location. The tightly bundled sound field is incident exactly on the location that is to be measured.The blind zone of the sensor lies within the focusing attachment, makingmeasurement possible starting directly from the sound outlet.Comment: Can be used with BUS R06K1..-02/007-.. and BUS R06K1..-02/015-.. for measurements inboreholes and filling levels as well as for scanning circuit boards or highly transparent foils.12Operating scanning ranges 20–70 mm and 20–150 mm Operating scanning range 120–700 mmUltrasonic SensorsR06 block-style housingYou can find additional electrical accessories in our catalogIndustrial Networking and Connectivity .You can find additional mechanical accessories in our catalog Accessories Line .13Ultrasonic SensorsM12 tubular-style housing■■Stainless steel housing■■Measuring range from 25 mm to 200 mm ■■1 switching output in PNP or NPN design ■■Teach-in via line (PIN 2)You can find additional electrical accessories in our catalog Industrial Networking and Connectivity .You can find additional mechanical accessories in our catalog Accessories Line .Monitoring of packagesHigh hygienic requirements in the food industry place special demands on sensor technology. The ultrasonic sensor reliably monitors the proper sealing of packages and thereby ensures uniform quality.14Fill-level monitoring in silosThe fill level of bulk materials in a container is detected by a continuous measurement with ultrasonic sensors. The fill level can optionally be output by an analog signal or with two switching signals – as min./max. value.Ultrasonic SensorsQ80 block-style housing■■Measuring range from 600 mm to 6000 mm ■■2 switching outputs in PNP- or NPN-design ■■Analog output 4...20 mA or 0...10 V ■■Teach-in via line (PIN 5)You can find additional electrical accessories in our catalog Industrial Networking and Connectivity .15Balluff GmbHSchurwaldstrasse 973765 Neuhausen a.d.F .GermanyPhone +49 7158 173-0Fax +49 7158 5010******************Object DetectionLinear Position SensingFluid SensorsIndustrial IdentificationIndustrial Networking and ConnectivityAccessoriesServiceDoc. no. 892815/Mat. no. 227188 E Edition 1210; subject to changes.。
- 1、下载文档前请自行甄别文档内容的完整性,平台不提供额外的编辑、内容补充、找答案等附加服务。
- 2、"仅部分预览"的文档,不可在线预览部分如存在完整性等问题,可反馈申请退款(可完整预览的文档不适用该条件!)。
- 3、如文档侵犯您的权益,请联系客服反馈,我们会尽快为您处理(人工客服工作时间:9:00-18:30)。
巴鲁夫BALLUFF压力传感器安装应注意事项
BALLUFF巴鲁夫产品主要包括:
BNS完整的电子式和机电式行程开关系列、BOS光电开关、BES感应式接近开关、电容开关、BMF磁敏开关,RFID识别系统,以及各种插接件等。
在广阔的工业应用领域,尤其是机械装备领域为用户提供创新的、有经验的传感器运用方案。
巴鲁夫公司是电器领域中的一家中型企业。
1000多名职工从事生产和销售种类繁多的电子、机电传感器,位移传感器和识别系统。
品质一流、价格合理、服务完善及遍布全球的经销网络。
产品成功地应用在许多自动化领域。
balluff巴鲁夫是您定位控制元件的选择。
BALLUFF压力传感器的安装,直接关乎到压力测量结果的准确性,所以我们要引起高度重视。
巴鲁夫BALLUFF压力传感器在工艺管道上正确的安装位置与被测介质有关,为获效得的测量结果,巴鲁夫BALLUFF压力传感器安装应注意事项:
1.防止巴鲁夫BALLUFF压力传感器与腐蚀性或过热的介质接触;
2.防止渣滓在导管内沉积;
3.测量液体压力时,取压口应开在流程管道侧面,以避免沉淀积渣。
4.测量气体压力时,取压口应开在流程管道顶端,并且传感器也应安装在流程管道上部,以便积累的液体容易注入流程管道中。
5.导压管应安装在温度波动小的地方;
6.测量蒸汽或其它高温介质时,需接加缓冲管等冷凝器,不应使巴鲁夫BALLUFF压力传感器的工作温度超过极限。
7.冬季发生冰冻时,按装在室外的巴鲁夫BALLUFF压力传感器必需采取防冻措施,避免引压口内的液体因结冰体积膨胀,导至传感器损坏。
8.测量液体压力时,巴鲁夫BALLUFF压力传感器的安装位置应避免液体的冲击,以免传感器过压损坏。
9.接线时,将电缆穿过防水接头或绕性管并拧紧密封螺帽,以防雨水等通过电缆渗漏进巴鲁夫BALLUFF压力传感器壳体内。
端压力传感器即使在极其恶劣的环境中也能自如使用。
其紧凑式壳体完全由坚固的不锈钢制成。
参数设置符合VDMA标准,十分简捷。
特征
紧凑式不锈钢壳体
本地压力显示
双开关输出端
模拟输出信号
600bar
-40°C至125°C
IP67
可应用的领域风力发电设备离岸区域
制冷及空调技术。