电火花加工原理
电火花加工原理
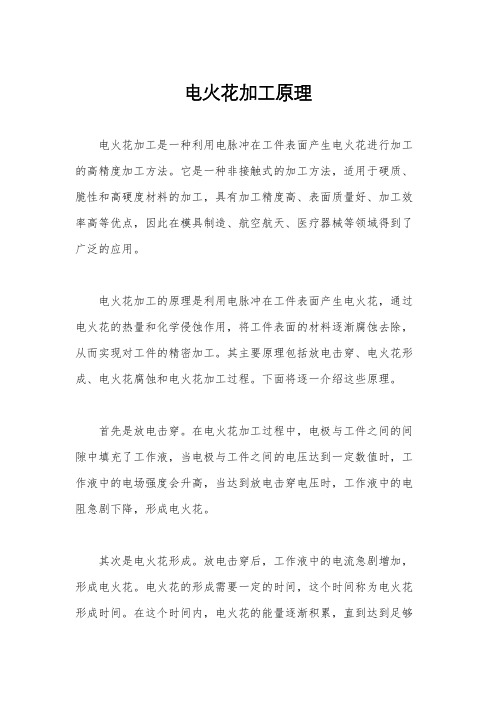
电火花加工原理电火花加工是一种利用电脉冲在工件表面产生电火花进行加工的高精度加工方法。
它是一种非接触式的加工方法,适用于硬质、脆性和高硬度材料的加工,具有加工精度高、表面质量好、加工效率高等优点,因此在模具制造、航空航天、医疗器械等领域得到了广泛的应用。
电火花加工的原理是利用电脉冲在工件表面产生电火花,通过电火花的热量和化学侵蚀作用,将工件表面的材料逐渐腐蚀去除,从而实现对工件的精密加工。
其主要原理包括放电击穿、电火花形成、电火花腐蚀和电火花加工过程。
下面将逐一介绍这些原理。
首先是放电击穿。
在电火花加工过程中,电极与工件之间的间隙中填充了工作液,当电极与工件之间的电压达到一定数值时,工作液中的电场强度会升高,当达到放电击穿电压时,工作液中的电阻急剧下降,形成电火花。
其次是电火花形成。
放电击穿后,工作液中的电流急剧增加,形成电火花。
电火花的形成需要一定的时间,这个时间称为电火花形成时间。
在这个时间内,电火花的能量逐渐积累,直到达到足够的能量,电火花才能在工件表面产生化学侵蚀作用。
然后是电火花腐蚀。
电火花在工件表面产生后,会产生高温和高压,使工件表面的材料发生化学反应,产生气体和金属离子,从而使工件表面的材料逐渐腐蚀去除。
这个过程需要一定的时间,称为电火花腐蚀时间。
最后是电火花加工过程。
在电火花腐蚀的作用下,工件表面的材料逐渐被腐蚀去除,从而实现对工件的精密加工。
在电火花加工过程中,工作液中的电场强度、电流密度、电火花频率等参数会对加工效果产生影响,需要根据具体加工要求进行调整。
总的来说,电火花加工是一种利用电脉冲在工件表面产生电火花进行加工的高精度加工方法,其原理包括放电击穿、电火花形成、电火花腐蚀和电火花加工过程。
通过合理调整工作液中的电场强度、电流密度、电火花频率等参数,可以实现对硬质、脆性和高硬度材料的精密加工,具有重要的应用价值。
电火花加工原理简述
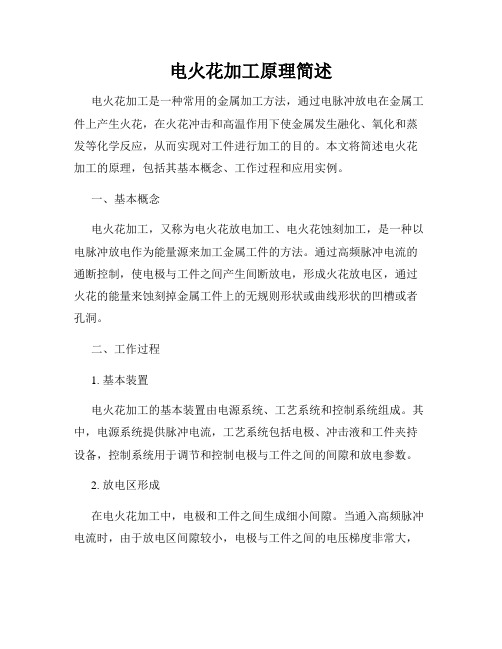
电火花加工原理简述电火花加工是一种常用的金属加工方法,通过电脉冲放电在金属工件上产生火花,在火花冲击和高温作用下使金属发生融化、氧化和蒸发等化学反应,从而实现对工件进行加工的目的。
本文将简述电火花加工的原理,包括其基本概念、工作过程和应用实例。
一、基本概念电火花加工,又称为电火花放电加工、电火花蚀刻加工,是一种以电脉冲放电作为能量源来加工金属工件的方法。
通过高频脉冲电流的通断控制,使电极与工件之间产生间断放电,形成火花放电区,通过火花的能量来蚀刻掉金属工件上的无规则形状或曲线形状的凹槽或者孔洞。
二、工作过程1. 基本装置电火花加工的基本装置由电源系统、工艺系统和控制系统组成。
其中,电源系统提供脉冲电流,工艺系统包括电极、冲击液和工件夹持设备,控制系统用于调节和控制电极与工件之间的间隙和放电参数。
2. 放电区形成在电火花加工中,电极和工件之间生成细小间隙。
当通入高频脉冲电流时,由于放电区间隙较小,电极与工件之间的电压梯度非常大,随着电压上升到一定值,间隙内空气被电离形成放电通道,从而使间隙电压骤降。
3. 火花放电当间隙电压骤降时,电极和工件之间产生放电,形成火花放电区域。
火花放电区域的高温和高压使空气在瞬间膨胀,形成冲击波和等离子区。
冲击波和等离子体对工件表面产生腐蚀和剥蚀作用,从而加工出所需形状的凹槽或孔洞。
4. 脉冲控制脉冲电流的控制是电火花加工中至关重要的一步。
通过调节脉冲电流的幅值、宽度和频率等参数,可以控制火花放电能量的大小和放电的稳定性,从而实现对工件加工精度的控制。
三、应用实例电火花加工是一种在模具制造、航空航天、汽车制造和微细加工等领域广泛应用的加工方法。
它被用于加工各种形状复杂、硬度高的金属材料,如工模、模具、钨钢、硬质合金等。
以模具制造为例,电火花加工在制造模具的过程中,能够加工出精细的孔洞和复杂的曲线形状。
相比传统机械加工,电火花加工可以避免工具磨损、提高加工精度和表面质量。
电火花加工工作原理
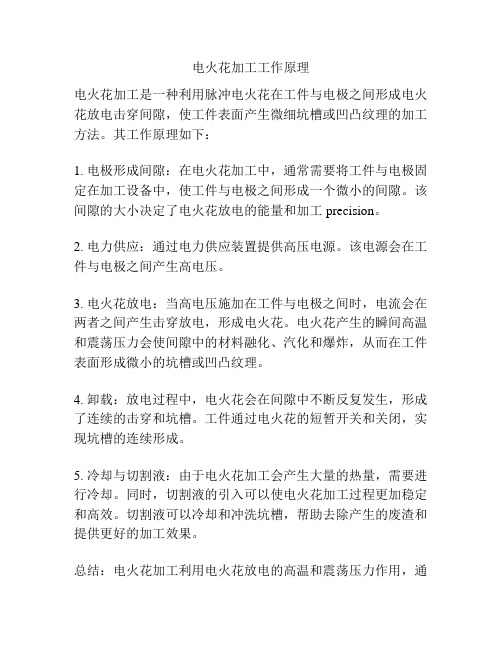
电火花加工工作原理
电火花加工是一种利用脉冲电火花在工件与电极之间形成电火花放电击穿间隙,使工件表面产生微细坑槽或凹凸纹理的加工方法。
其工作原理如下:
1. 电极形成间隙:在电火花加工中,通常需要将工件与电极固定在加工设备中,使工件与电极之间形成一个微小的间隙。
该间隙的大小决定了电火花放电的能量和加工 precision。
2. 电力供应:通过电力供应装置提供高压电源。
该电源会在工件与电极之间产生高电压。
3. 电火花放电:当高电压施加在工件与电极之间时,电流会在两者之间产生击穿放电,形成电火花。
电火花产生的瞬间高温和震荡压力会使间隙中的材料融化、汽化和爆炸,从而在工件表面形成微小的坑槽或凹凸纹理。
4. 卸载:放电过程中,电火花会在间隙中不断反复发生,形成了连续的击穿和坑槽。
工件通过电火花的短暂开关和关闭,实现坑槽的连续形成。
5. 冷却与切割液:由于电火花加工会产生大量的热量,需要进行冷却。
同时,切割液的引入可以使电火花加工过程更加稳定和高效。
切割液可以冷却和冲洗坑槽,帮助去除产生的废渣和提供更好的加工效果。
总结:电火花加工利用电火花放电的高温和震荡压力作用,通
过间隙中材料的融化、汽化和爆炸形成微小的坑槽或凹凸纹理。
同时,通过不断重复的放电过程和切割液的引入,实现了连续的加工效果。
电火花机加工原理
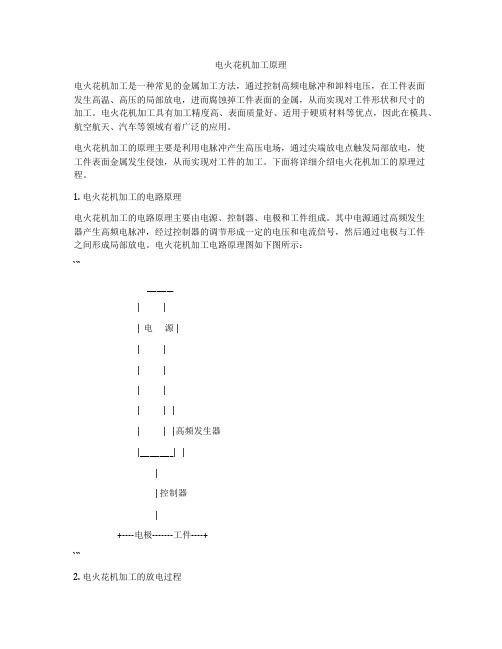
电火花机加工原理电火花机加工是一种常见的金属加工方法,通过控制高频电脉冲和卸料电压,在工件表面发生高温、高压的局部放电,进而腐蚀掉工件表面的金属,从而实现对工件形状和尺寸的加工。
电火花机加工具有加工精度高、表面质量好、适用于硬质材料等优点,因此在模具、航空航天、汽车等领域有着广泛的应用。
电火花机加工的原理主要是利用电脉冲产生高压电场,通过尖端放电点触发局部放电,使工件表面金属发生侵蚀,从而实现对工件的加工。
下面将详细介绍电火花机加工的原理过程。
1. 电火花机加工的电路原理电火花机加工的电路原理主要由电源、控制器、电极和工件组成。
其中电源通过高频发生器产生高频电脉冲,经过控制器的调节形成一定的电压和电流信号,然后通过电极与工件之间形成局部放电。
电火花机加工电路原理图如下图所示:```________| || 电源 || || || || | || | |高频发生器|__________| ||| 控制器|+----电极-------工件----+```2. 电火花机加工的放电过程电火花机加工的放电过程是通过高频电脉冲产生高压电场,使工件表面金属发生局部放电,从而腐蚀掉工件表面的金属,实现对工件的加工。
放电的过程主要包括以下几个步骤:(1) 电极与工件的间隙放电在电火花机加工过程中,电极与工件之间形成一定的间隙,通过高频电脉冲产生高压电场,使电极与工件之间发生局部放电,从而在工件表面产生高温高压的电晕,进而使工件表面金属发生侵蚀,实现对工件的加工。
(2) 电极与工件的间隙维持在电火花机加工过程中,电极与工件之间的间隙需要保持一定的距离,以保证局部放电能够有效地腐蚀掉工件表面的金属。
因此,电火花机加工中常常需要用到一定的间隙调节装置,以保持电极与工件之间的间隙稳定。
(3) 放电的频率和脉冲宽度电火花机加工中的放电频率和脉冲宽度是影响加工效果的重要因素。
放电频率越高,脉冲宽度越短,工件表面金属的侵蚀速度就越快,加工效率就越高。
电火花加工的原理和应用
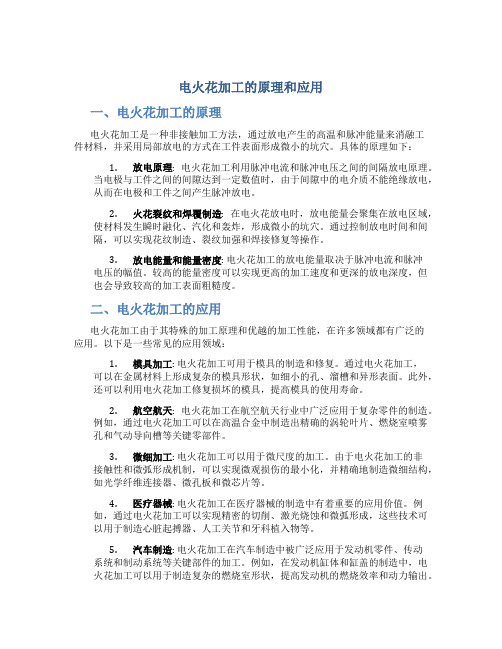
电火花加工的原理和应用一、电火花加工的原理电火花加工是一种非接触加工方法,通过放电产生的高温和脉冲能量来消融工件材料,并采用局部放电的方式在工件表面形成微小的坑穴。
具体的原理如下:1.放电原理: 电火花加工利用脉冲电流和脉冲电压之间的间隔放电原理。
当电极与工件之间的间隙达到一定数值时,由于间隙中的电介质不能绝缘放电,从而在电极和工件之间产生脉冲放电。
2.火花裂纹和焊覆制造: 在电火花放电时,放电能量会聚集在放电区域,使材料发生瞬时融化、汽化和轰炸,形成微小的坑穴。
通过控制放电时间和间隔,可以实现花纹制造、裂纹加强和焊接修复等操作。
3.放电能量和能量密度: 电火花加工的放电能量取决于脉冲电流和脉冲电压的幅值。
较高的能量密度可以实现更高的加工速度和更深的放电深度,但也会导致较高的加工表面粗糙度。
二、电火花加工的应用电火花加工由于其特殊的加工原理和优越的加工性能,在许多领域都有广泛的应用。
以下是一些常见的应用领域:1.模具加工: 电火花加工可用于模具的制造和修复。
通过电火花加工,可以在金属材料上形成复杂的模具形状,如细小的孔、溜槽和异形表面。
此外,还可以利用电火花加工修复损坏的模具,提高模具的使用寿命。
2.航空航天: 电火花加工在航空航天行业中广泛应用于复杂零件的制造。
例如,通过电火花加工可以在高温合金中制造出精确的涡轮叶片、燃烧室喷雾孔和气动导向槽等关键零部件。
3.微细加工: 电火花加工可以用于微尺度的加工。
由于电火花加工的非接触性和微弧形成机制,可以实现微观损伤的最小化,并精确地制造微细结构,如光学纤维连接器、微孔板和微芯片等。
4.医疗器械: 电火花加工在医疗器械的制造中有着重要的应用价值。
例如,通过电火花加工可以实现精密的切削、激光烧蚀和微弧形成,这些技术可以用于制造心脏起搏器、人工关节和牙科植入物等。
5.汽车制造: 电火花加工在汽车制造中被广泛应用于发动机零件、传动系统和制动系统等关键部件的加工。
简述电火花加工的原理
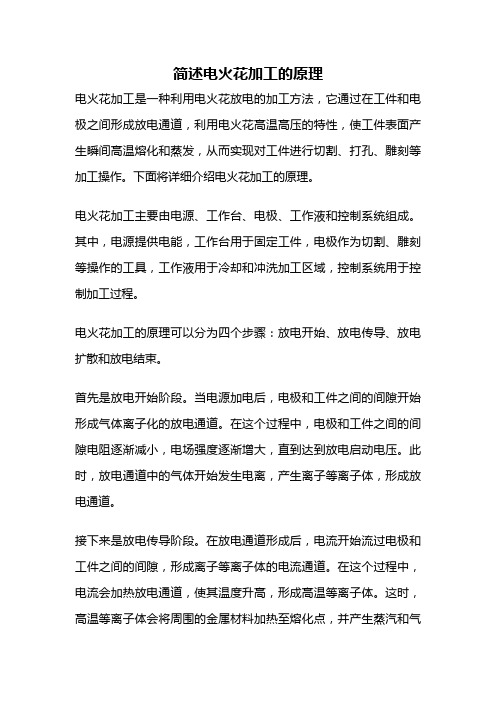
简述电火花加工的原理电火花加工是一种利用电火花放电的加工方法,它通过在工件和电极之间形成放电通道,利用电火花高温高压的特性,使工件表面产生瞬间高温熔化和蒸发,从而实现对工件进行切割、打孔、雕刻等加工操作。
下面将详细介绍电火花加工的原理。
电火花加工主要由电源、工作台、电极、工作液和控制系统组成。
其中,电源提供电能,工作台用于固定工件,电极作为切割、雕刻等操作的工具,工作液用于冷却和冲洗加工区域,控制系统用于控制加工过程。
电火花加工的原理可以分为四个步骤:放电开始、放电传导、放电扩散和放电结束。
首先是放电开始阶段。
当电源加电后,电极和工件之间的间隙开始形成气体离子化的放电通道。
在这个过程中,电极和工件之间的间隙电阻逐渐减小,电场强度逐渐增大,直到达到放电启动电压。
此时,放电通道中的气体开始发生电离,产生离子等离子体,形成放电通道。
接下来是放电传导阶段。
在放电通道形成后,电流开始流过电极和工件之间的间隙,形成离子等离子体的电流通道。
在这个过程中,电流会加热放电通道,使其温度升高,形成高温等离子体。
这时,高温等离子体会将周围的金属材料加热至熔化点,并产生蒸汽和气体。
然后是放电扩散阶段。
在高温等离子体的作用下,工件表面的金属材料开始瞬间熔化和蒸发,形成微小的颗粒和气体。
这些颗粒和气体被冷却液冲洗走,同时放电通道也会不断扩散,使加工孔径逐渐增大。
最后是放电结束阶段。
在放电过程中,电极和工件之间的间隙会不断增加,电阻也会增大。
当电流无法维持放电通道时,放电就会结束。
此时,加工区域会有一定的凹坑和残留物,需要进行后续的处理。
总结起来,电火花加工利用放电通道的高温高压特性,通过瞬间熔化和蒸发工件表面的金属材料,实现对工件的切割、打孔、雕刻等加工操作。
其原理是通过电源提供电能,形成放电通道,使工件表面产生高温等离子体,从而实现加工目的。
电火花加工具有加工精度高、加工效率高、适用于各种材料等优点,广泛应用于模具制造、航空航天、汽车制造等领域。
电火花加工工艺原理
电火花加工工艺原理电火花加工工艺是一种先进的金属加工技术,它利用电火花放电的原理来加工各种复杂形状的金属工件,具有高精度、高效率的特点。
本文将介绍电火花加工的工艺原理及其应用。
一、电火花加工的工艺原理电火花加工是利用电极间产生的电火花放电来加工金属工件的一种加工方法。
其基本原理是通过在工作液中形成电火花放电,使电极和工件之间的物质得以熔化和蒸发,从而实现金属的加工和雕刻。
1. 电火花放电原理电火花放电是指在两个电极之间形成了高电压和高频率的电弧放电现象。
在电火花加工中,通过控制脉冲电流,使电极和工件之间产生高频率、低能量的电火花放电。
放电时,电极和工件之间的电气能量会被转化为热能,使局部区域的温度瞬间升高,金属发生熔化和蒸发。
2. 工作液的作用工作液在电火花加工中起到冷却和冲击的作用。
当电极和工件之间放电时,会产生大量的热量,如果没有适当的冷却措施,会导致电极和工件过热,甚至损坏。
工作液可以通过冷却电极和工件,降低温度,保证加工质量。
工作液还能冲击熔化和蒸发的金属颗粒,防止其重新附着在工件表面,保证加工效果。
常用的工作液有脱脂剂、冷却液和去离子水等。
3. 电极和工件的选择在电火花加工中,电极和工件的选择对加工效果至关重要。
一般情况下,电极采用导电性好的材料,如铜、铜合金等,而工件则可以选择硬度较高的金属材料,如钢铁、铝合金等。
二、电火花加工的应用电火花加工广泛应用于模具制造、航空航天、汽车零部件、电子元件等领域。
其优点是可以加工各种复杂形状的工件,无需切削力,不会产生应力和变形,加工精度高。
1. 模具制造电火花加工在模具制造中有着重要的应用。
模具通常具有复杂的形状和细小的结构,传统的机械加工难以满足加工要求。
而电火花加工可以通过控制电极的运动轨迹和放电参数,精确地加工出模具的形状和细节,提高模具的加工精度和质量。
2. 航空航天在航空航天领域,电火花加工被广泛应用于加工航空发动机的复杂零部件。
航空发动机通常由大量的叶片和导向器组成,其形状复杂,表面光滑度要求高。
瞬间明白电火花加工的原理
瞬间明白电火花加工的原理
电火花加工是一种利用电脑控制的放电脉冲,在工件表面产生高能量的电火花,并通过放电过程中的电弧和脉冲电流来熔化和蚀刻工件材料的加工方法。
具体的原理如下:
1. 工件和电极:电火花加工通常用到两个电极,分别为工件电极和刀具电极。
工件电极是要进行加工的工件本身,刀具电极则是用来激发电火花的钨电极。
2. 放电过程:刀具电极靠近工件电极,形成微小间隙。
随后,施加高频高电压脉冲,形成电火花。
电火花在两个电极之间产生强烈的电场和热量,当电火花通过间隙时,迅速产生气化蒸汽和高温等离子体。
3. 腐蚀过程:高温等离子体导致工件表面的金属材料熔化,并形成电弧和脉冲电流。
这些电弧和电流会将融化的金属材料迅速蒸发,同时也会快速将电极上的材料侵蚀掉。
这个过程将交替进行,每一次放电都会腐蚀和熔化一小部分工件表面。
4. 冲击效应:除了瞬间的高温作用外,电火花加工还具有冲击效应。
焦耳定律表明,根据电流强度和通过时间的乘积可以得出腐蚀剂对工件的侵蚀深度。
电火花加工中,每当电火花形成和消失时,都会产生冲击波,进一步促进金属材料的蒸发。
总结起来,电火花加工利用脉冲电流和电弧的高温和高能量,通过瞬间的熔化、蚀刻和侵蚀,来实现对工件材料的加工和修复。
这种加工方法广泛应用于制造业中,特别是用于具有复杂形状和高硬度的金属材料加工,例如模具、工具和精密零部件等。
电火花机床加工原理
电火花机床加工原理
电火花机床是一种利用脉冲电火花放电的工具,用来加工金属材料,特别是硬质材料。
其原理主要包括以下几个方面。
1. 放电原理:电火花机床通过高频脉冲电压使电极与工件之间产生放电现象。
电极与工件之间形成的电场达到一定程度时,电荷就会在两者之间跃迁,从而产生电火花放电。
2. 热膨胀原理:电火花放电会产生高温和高压,导致材料瞬间熔化和汽化,同时产生很高的气压。
高压气体将瞬间扩散并冲击材料表面,形成坑洞。
3. 融化与溶解原理:电火花放电产生的高温可以使工件表面部分区域瞬间熔化或溶解。
熔化的金属会形成一定深度和形状的陷凹区域。
4. 剥离原理:电火花放电时,电极和工件之间的电荷转移会导致工件表面附着的一层物质(如氧化物)剥离并喷射出去。
综上所述,电火花机床利用高频脉冲电压引发放电现象,通过热膨胀、溶解、剥离等原理,对金属材料进行加工。
电火花加工可以达到高精度和微细加工,特别适用于硬质材料的加工。
电火花加工的基本原理和优缺点
电火花加工的基本原理和优缺点前言电火花加工是一种常用于制造业的先进加工技术,它可以精确地切割金属材料,实现复杂零件的加工。
本文将介绍电火花加工的基本原理以及其优缺点。
一、电火花加工的基本原理电火花加工是利用脉冲电火花在工件与电极之间产生放电,瞬时高温点熔化工件,通过去除熔融金属颗粒来完成加工的一种技术。
其基本原理如下:1.电极和工件的导电性:电火花加工中,工件材料和电极都需要具备良好的导电性。
工件通常是金属材料,而电极则通常选择铜或铜合金制成。
2.电火花放电:通过控制电极与工件之间的放电间隙和电气参数,使用脉冲电源施加高压电流至电极,产生强大的电场。
当电场强度超过工作介质的击穿电场强度时,电极和工件之间产生放电,形成电火花。
3.电火花的热效应:电火花的放电会使介质发生局部熔化,形成高温熔融的电火花区。
高温电火花区对工件表面进行剥蚀,并将熔融金属颗粒击碎,从而实现加工。
4.工作液的冷却和清洗:为了稳定电火花放电的过程,防止电极和工件过热,电火花加工通常需要使用工作液进行冷却和清洗。
工作液不仅能降低电极和工件的温度,还可以冲洗加工过程中产生的碎屑。
二、电火花加工的优点电火花加工在现代制造业中被广泛应用,并具有以下优点:1.加工精度高:电火花加工能够制造出高精度的零件,加工精度可达到0.001mm,甚至更高。
这使得电火花加工适用于制造精密器件和模具等需求高精度的产品。
2.适用于任意硬度的材料:电火花加工不受被加工材料硬度的限制,可以加工任何导电材料,无论是高硬度的钢铁材料,还是脆性的陶瓷材料,都可以进行有效加工。
3.无影响材料外形特征:由于电火花加工是通过放电熔化工件表面来实现加工的,不需要接触工件表面,因此可以保持材料的原始形状和特征。
这种非接触加工方式最大程度地避免了材料变形和应力引起的问题。
4.适用于复杂几何形状:电火花加工具有良好的灵活性,可以加工出复杂的几何形状,如细小孔洞、内外轮廓形状复杂的零件等。
- 1、下载文档前请自行甄别文档内容的完整性,平台不提供额外的编辑、内容补充、找答案等附加服务。
- 2、"仅部分预览"的文档,不可在线预览部分如存在完整性等问题,可反馈申请退款(可完整预览的文档不适用该条件!)。
- 3、如文档侵犯您的权益,请联系客服反馈,我们会尽快为您处理(人工客服工作时间:9:00-18:30)。
电火花加工技术学院:机械与汽车工程学院专业:材控10-2班姓名:徐鹏学号:201001021047电火花加工技术电火花是一种加工工艺,主要是利用具有特定几何形状的放电电极(EDM电极)在金属(导电)部件上烧灼出电极的几何形状。
电火花加工工艺常用于冲裁模和铸模的生产。
利用火花放电时产生的腐蚀现象对材料进行尺寸加工的方法,叫电火花加工。
电火花加工是在较低的电压范围内,在液体介质中的火花放电。
电火花加工主要由机械厂完成。
电火花是一种自激放电,其特点如下:火花放电的两个电极间在放电前具较高的电压,当两电极接近时,其间介质被击穿后,随即发生火花放电。
伴随击穿过程,两电极间的电阻急剧变小,两极之间的电压也随之急剧变低。
火花通道必须在维持暂短的时间(通常为10-7-10-3s)后及时熄灭,才可保持火花放电的“冷极”特性(即通道能量转换的热能来不及传至电极纵深),使通道能量作用于极小范围。
通道能量的作用,可使电极局部被腐蚀。
工具电极和工件之间并不直接接触,而是有一个火花放电间隙0.1—0.01mm,间隙中充满工作液。
加工过程中没有宏观切削力火花放电时,局部、瞬时爆炸力的平均值很小,不足以引起工件的变形和位移。
可以“以柔克刚”由于电火花加工直接利用电能和热能来去除金属材料,与工件材料的强度和硬度等关系不大,因此町以用软的工具电极加工硬的工件,实现“以柔克刚”。
可以加工任何难加工的金属材料和导电材料由于加工中材料的去除是靠放电时的电、热作用实现的,材料的可加工性主要取决于材料的导电性及热学特性,如熔点、沸点、比热容、导热系数、电阻率等,而几乎与其力学性能(硬度、强度等)无关。
这样可以突破传统切削加工对刀具的限制,可以实现用软的工具加工硬、韧的工件甚至可以加工聚晶金刚行、立方氮化硼一类的超硬材料。
目前电极材料多采用紫铜或石墨,因此工具电极较容易加工。
可以加工形状复杂的表面由于可以简单地将工具电极的形状复制到工件上,因此特别适用于复杂表面形状工件的加工,如复杂型腔模具加工等。
特别是数控技术的采用,使得用简单的电极加工复杂形状零件成为现实。
可以加工特殊要求的零件可以加工薄壁、弹性、低刚度、微细小孔、异形小孔、深小孔等有特殊要求的零件。
由于加工中工具电极和工件不直接接触,没有机械加工的切削力,因此适宜加工低刚度工件及微细加工。
电火花加工原理电火花加工时,脉冲电源的一极接工具电极,另一极接工件电极,两极均浸入具有一定绝缘度的液体介质(常用煤油或矿物油或去离子水)中。
工具电极由自动进给调节装置控制,以保证工具与工件在正常加工时维持一很小的放电间隙(0.01~0.05mm)。
当脉冲电压加到两极之间,便将当时条件下极间最近点的液体介质击穿,形成放电通道。
由于通道的截面积很小,放电时间极短,致使能量高度集中(10~107W/mm),放电区域产生的瞬时高温足以使材料熔化甚至蒸发,以致形成一个小凹坑。
第一次脉冲放电结束之后,经过很短的间隔时间,第二个脉冲又在另一极间最近点击穿放电。
如此周而复始高频率地循环下去,工具电极不断地向工件进给,它的形状最终就复制在工件上,形成所需要的加工表面。
与此同时,总能量的一小部分也释放到工具电极上,从而造成工具损耗。
从上看出,进行电火花加工必须具备三个条件:必须采用脉冲电源;必须采用自动进给调节装置,以保持工具电极与工件电极间微小的放电间隙;火花放电必须在具有一定绝缘强度(10~107Ω ·m)的液体介质中进行。
电火花加工具有如下特点:可以加工任何高强度、高硬度、高韧性、高脆性以及高纯度的导电材料;加工时无明显机械力,适用于低刚度工件和微细结构的加工:脉冲参数可依据需要调节,可在同一台机床上进行粗加工、半精加工和精加工;电火花加工后的表面呈现的凹坑,有利于贮油和降低噪声;生产效率低于切削加工;放电过程有部分能量消耗在工具电极上,导致电极损耗,影响成形精度。
电火花加工是利用浸在工作液中的两极间脉冲放电时产生的电蚀作用蚀除导电材料的特种加工方法,又称放电加工或电蚀加工,英文简称EDM。
发明与发展1943年,苏联学者拉扎连科夫妇研究发明电火花加工,之后随着脉冲电源和控制系统的改进,而迅速发展起来。
最初使用的脉冲电源是简单的电阻-电容回路。
50年代初,改进为电阻-电感-电容等回路。
同时,还采用脉冲发电机之类的所谓长脉冲电源,使蚀除效率提高,工具电极相对损耗降低。
随后又出现了大功率电子管,闸流管等高频脉冲电源,使在同样表面粗糙度条件下的生产率得以提高。
60年代中期,出现了晶体管和可控硅脉冲电源,提高了能源效率和降低了工具电极损耗,并扩大了粗精加工的可调范围。
到70年代,出现了高低压复合脉冲、多回路脉冲、等幅脉冲和可调波形脉冲等电源,在加工表面粗糙度、加工精度和降低工具电极损耗等方面又有了新的进展。
在控制系统方面,从最初简单地保持放电间隙,控制工具电极的进退,逐步发展到利用微型计算机,对电参数和非电参数等各种因素进行适时控制。
进行电火花加工时,工具电极和工件分别接脉冲电源的两极,并浸入工作液中,或将工作液充入放电间隙。
通过间隙自动控制系统控制工具电极向工件进给,当两电极间的间隙达到一定距离时,两电极上施加的脉冲电压将工作液击穿,产生火花放电。
在放电的微细通道中瞬时集中大量的热能,温度可高达一万摄氏度以上,压力也有急剧变化,从而使这一点工作表面局部微量的金属材料立刻熔化、气化,并爆炸式地飞溅到工作液中,迅速冷凝,形成固体的金属微粒,被工作液带走。
这时在工件表面上便留下一个微小的凹坑痕迹,放电短暂停歇,两电极间工作液恢复绝缘状态。
紧接着,下一个脉冲电压又在两电极相对接近的另一点处击穿,产生火花放电,重复上述过程。
这样,虽然每个脉冲放电蚀除的金属量极少,但因每秒有成千上万次脉冲放电作用,就能蚀除较多的金属,具有一定的生产率。
在保持工具电极与工件之间恒定放电间隙的条件下,一边蚀除工件金属,一边使工具电极不断地向工件进给,最后便加工出与工具电极形状相对应的形状来。
因此,只要改变工具电极的形状和工具电极与工件之间的相对运动方式,就能加工出各种复杂的型面。
工具电极常用导电性良好、熔点较高、易加工的耐电蚀材料,如铜、石墨、铜钨合金和钼等。
在加工过程中,工具电极也有损耗,但小于工件金属的蚀除量,甚至接近于无损耗。
工作液作为放电介质,在加工过程中还起着冷却、排屑等作用。
常用的工作液是粘度较低、闪点较高、性能稳定的介质,如煤油、去离子水和乳化液等分类及使用说明按照工具电极的形式及其与工件之间相对运动的特征,可将电火花加工方式分为五类:利用成型工具电极,相对工件作简单进给运动的电火花成形加工;利用轴向移动的金属丝作工具电极,工件按所需形状和尺寸作轨迹运动,以切割导电材料的电火花线切割加工;利用金属丝或成形导电磨轮作工具电极,进行小孔磨削或成形磨削的电火花磨削;用于加工螺纹环规、螺纹塞规、齿轮等的电火花共轭回转加工;小孔加工、刻印、表面合金化、表面强化等其他种类的加工。
电火花加工能加工普通切削加工方法难以切削的材料和复杂形状工件;加工时无切削力;不产生毛刺和刀痕沟纹等缺陷;工具电极材料无须比工件材料硬;直接使用电能加工,便于实现自动化;加工后表面产生变质层,在某些应用中须进一步去除;工作液的净化和加工中产生的烟雾污染处理比较麻烦。
电火花加工的主要用于加工具有复杂形状的型孔和型腔的模具和零件;加工各种硬、脆材料,如硬质合金和淬火钢等;加工深细孔、异形孔、深槽、窄缝和切割薄片等;加工各种成形刀具、样本和螺纹环规等工具和量具。
电火花加工特点1:电火花加工速度与表面质量模具在电火花机加工一般会采用粗、中、精分档加工方式。
粗加工采用大功率、低损耗的实现,而中、精加工电极相对损耗大,但一般情况下中、精加工余量较少,因此电极损耗也极小,可以通过加工尺寸控制进行补偿,或在不影响精度要求时予以忽略。
2:电火花碳渣与排渣电火花机加工在产生碳渣和排除碳渣平衡的条件下才能顺利进行。
实际中往往以牺牲加工速度去排除碳渣,例如在中、精加工时采用高电压,大休止脉波等等。
另一个影响排除碳渣的原因是加工面形状复杂,使排屑路径不畅通。
唯有积极开创良好排除的条件,对症的采取一些方法来积极处理。
3:电火花工件与电极相互损耗电火花机放电脉波时间长,有利于降低电极损耗。
电火花机粗加工一般采用长放电脉波和大电流放电,加工速度快电极损耗小。
在精加工时,小电流放电必须减小放电脉波时间,这样不仅加大了电极损耗,也大幅度降低了加工速度。
电火花加工是与机械加工完全不同的一种新工艺。
随着工业生产的发展和科学技术的进步,具有高熔点、高硬度、高强度、高脆性,高粘性和高纯度等性能的新材料不断出现。
具有各种复杂结构与特殊工艺要求的工件越来越多,这就使得传统的机械加工方法不能加工或难于加工。
因此,人们除了进一步发展和完善机械加工法之外,还努力寻求新的加工方法。
电火花加工法能够适应生产发展的需要,并在应用中显示出很多优异性能,因此,得到了迅速发展和日益广泛的应用。
电火花加工的应用电火花加工主要用于模具生产中的型孔、型腔加工,已成为模具制造业的主导加工方法,推动了模具行业的技术进步。
电火花加工零件的数量在3000件以下时,比模具冲压零件在经济上更加合理。
按工艺过程中工具与工件相对运动的特点和用途不同,电火花加工可大体分为:电火花成形加工、电火花线切割加工、电火花磨削加工、电火花展成加工、非金属电火花加工和电火花表面强化等。
(1)电火花成形加工该方法是通过工具电极相对于工件作进给运动,将工件电极的形状和尺寸复制在工件上,从而加工出所需要的零件。
它包括电火花型腔加工和穿孔加工两种。
电火花型腔加工主要用于加工各类热锻模、压铸模、挤压模、塑料模和胶木膜的型腔。
电火花穿孔加工主要用于型孔(圆孔、方孔、多边形孔、异形孔)、曲线孔(弯孔、螺旋孔)、小孔和微孔的加工。
近年来,为了解决小孔加工中电极截面小、易变形、孔的深径比大、排屑困难等问题,在电火花穿孔加工中发展了高速小孔加工,取得良好的社会经济效益。
(2)电火花线切割加工该方法是利用移动的细金属丝作工具电极,按预定的轨迹进行脉冲放电切割。
按金属丝电极移动的速度大小分为高速走丝和低速走丝线切割。
我国普通采用高速走丝线切割,近年来正在发展低速走丝线切割,高速走丝时,金属丝电极是直径为φ0.02~φ0.3mm的高强度钼丝,往复运动速度为8~10m/s。
低速走丝时,多采用铜丝,线电极以小于0.2m/s的速度作单方向低速运动。
线切割时,电极丝不断移动,其损耗很小,因而加工精度较高。
其平均加工精度可达 0.0lmm,大大高于电火花成形加工。
表面粗糙度Ra值可达1.6 或更小。
国内外数控电火花线切割都采用了不同水平的微机数控系统,实现了电火花线切割数控化。