提高锻件质量有效方法
锻件质量控制
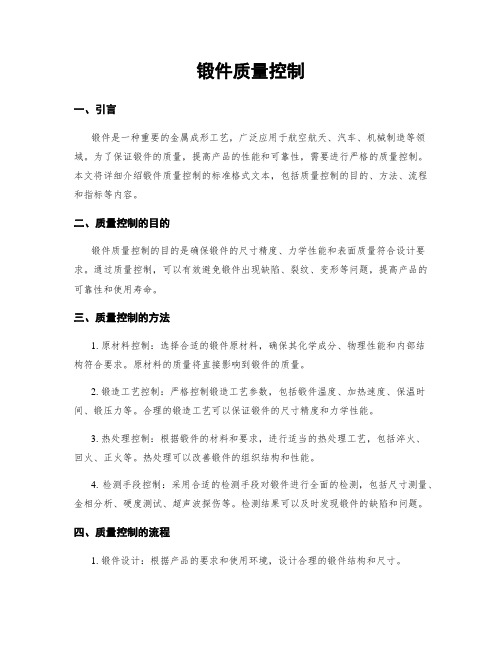
锻件质量控制一、引言锻件是一种重要的金属成形工艺,广泛应用于航空航天、汽车、机械制造等领域。
为了保证锻件的质量,提高产品的性能和可靠性,需要进行严格的质量控制。
本文将详细介绍锻件质量控制的标准格式文本,包括质量控制的目的、方法、流程和指标等内容。
二、质量控制的目的锻件质量控制的目的是确保锻件的尺寸精度、力学性能和表面质量符合设计要求。
通过质量控制,可以有效避免锻件出现缺陷、裂纹、变形等问题,提高产品的可靠性和使用寿命。
三、质量控制的方法1. 原材料控制:选择合适的锻件原材料,确保其化学成分、物理性能和内部结构符合要求。
原材料的质量将直接影响到锻件的质量。
2. 锻造工艺控制:严格控制锻造工艺参数,包括锻件温度、加热速度、保温时间、锻压力等。
合理的锻造工艺可以保证锻件的尺寸精度和力学性能。
3. 热处理控制:根据锻件的材料和要求,进行适当的热处理工艺,包括淬火、回火、正火等。
热处理可以改善锻件的组织结构和性能。
4. 检测手段控制:采用合适的检测手段对锻件进行全面的检测,包括尺寸测量、金相分析、硬度测试、超声波探伤等。
检测结果可以及时发现锻件的缺陷和问题。
四、质量控制的流程1. 锻件设计:根据产品的要求和使用环境,设计合理的锻件结构和尺寸。
2. 原材料采购:选择合适的原材料供应商,对原材料进行严格的检验和验收。
3. 锻造过程控制:根据锻件的形状和材料,确定合适的锻造工艺参数,进行锻造生产。
4. 热处理过程控制:根据锻件的材料和要求,进行适当的热处理工艺,控制热处理参数。
5. 检测和评估:对锻件进行全面的检测,评估锻件的质量和性能是否符合要求。
6. 修正和改进:根据检测结果,对不合格的锻件进行修正或改进,确保产品质量。
五、质量控制的指标1. 尺寸精度:按照设计要求,对锻件的尺寸进行测量,控制尺寸偏差在允许范围内。
2. 力学性能:通过硬度测试、拉伸试验等手段,评估锻件的强度、韧性和延展性等力学性能指标。
3. 表面质量:对锻件的表面进行检查,控制表面缺陷、氧化层和裂纹等问题。
锻件质量控制

锻件质量控制引言概述:锻件作为一种重要的金属加工工艺,广泛应用于航空、汽车、机械等行业。
然而,由于锻件制造过程中存在一系列的复杂因素,如材料性能、工艺参数等,导致锻件质量控制成为一个关键的问题。
本文将从五个方面详细阐述锻件质量控制的重要性和方法。
一、材料选择1.1 材料性能要求:锻件的质量控制首先要从材料选择入手。
根据锻件的使用环境和要求,选择合适的材料。
考虑材料的强度、韧性、耐磨性等特性,确保锻件在使用过程中能够满足要求。
1.2 材料检测方法:采用适当的材料检测方法,如化学成分分析、金相分析、硬度测试等,对原材料进行严格检验,以确保材料的质量符合要求。
1.3 材料热处理:根据锻件的材料和使用要求,进行适当的热处理,如退火、正火、淬火等,以提高材料的力学性能和组织结构,从而提高锻件的质量。
二、工艺参数控制2.1 温度控制:锻件的温度是影响锻件质量的重要因素之一。
在锻造过程中,要控制好锻件的加热温度和保温时间,避免温度过高或过低导致材料的结构破坏或质量问题。
2.2 压力控制:锻造过程中的锻压力度对于锻件的成形和质量控制至关重要。
要根据锻件的形状和材料的特性,合理控制锻压力度,避免过大或过小导致锻件的变形或裂纹等问题。
2.3 冷却控制:锻件的冷却过程也是影响锻件质量的重要因素。
要根据锻件的材料和形状,合理选择冷却介质和冷却速度,避免锻件的变形和内部应力过大,保证锻件的质量。
三、工艺检测3.1 尺寸检测:通过测量锻件的尺寸,判断锻件的成形是否符合要求。
可以采用三坐标测量仪、投影仪等设备进行尺寸检测,确保锻件的几何形状和尺寸精度符合设计要求。
3.2 缺陷检测:通过无损检测方法,如超声波检测、磁粉检测等,对锻件进行缺陷检测,如裂纹、气孔等。
及时发现并修复锻件的缺陷,以提高锻件的质量。
3.3 组织检测:通过金相显微镜等设备,对锻件的金相组织进行观察和分析,判断锻件的组织结构是否均匀、致密,以及是否存在晶粒长大等问题,确保锻件的组织质量符合要求。
锻件质量控制

锻件质量控制锻件质量控制引言锻件质量控制的基本原理锻件质量控制的基本原理是通过控制和管理锻件的各个环节,以达到符合技术要求和客户需求的产品质量。
主要包括以下几个方面:1. 原材料的选择和检验:要使用高质量的原材料进行锻件生产,对原材料进行严格的检验和筛选,确保无缺陷和杂质。
2. 锻造工艺控制:锻造工艺是影响锻件质量的关键因素之一。
必须制定合理的工艺参数,包括锻件的温度、压力和变形量等,以保证锻件的均匀性和机械性能。
3. 热处理控制:热处理是提高锻件性能的关键步骤,必须控制好热处理工艺和参数,例如加热温度、保温时间和冷却速度等,以获得理想的组织和性能。
4. 检测和检验:要对锻件进行全面的检测和检验,包括外观检查、尺寸测量、材料成分分析以及机械性能测试等,以确保锻件的质量符合标准要求。
锻件质量控制的方法和工具为了实现锻件质量的控制,我们可以采用以下几种方法和工具:1. 统计过程控制(SPC):采集和分析锻造过程中的数据,通过统计方法判断和控制过程的稳定性和一致性,及时发现问题并做出调整。
2. 全面质量管理(TQM):引入全面质量管理的理念和方法,通过持续改进和全员参与来提高质量水平,建立质量文化,确保质量始终处于可控状态。
3. 先进的检测技术:利用先进的检测设备和技术,如X射线探伤、超声波检测和磁粉探伤等,对锻件进行无损检测,提高检测的准确性和效率。
4. 故障模式与影响分析(FMEA):通过分析锻件的故障模式和影响,制定相应的防控措施,降低故障概率,提高锻件的可靠性和寿命。
锻件质量控制的挑战与展望锻件质量控制面临着许多挑战和难题。
例如,锻件的形状复杂,内部组织不均匀,如何保证每一个锻件都符合质量要求是一个关键问题。
锻件质量的控制需要耗费大量的资源和人力,如何提高效率和降低成本也是一个需要解决的问题。
,随着科技的发展和创新,锻件质量控制将面临更多的机遇和挑战。
新型材料的应用、智能制造技术的发展以及数据分析和等技术的应用,将为锻件质量控制提供更多的可能性和解决方案。
锻件质量控制

锻件质量控制一、引言锻件是一种常见的金属加工工艺,广泛应用于汽车、航空航天、机械制造等行业。
为了确保锻件的质量,需要进行严格的质量控制。
本文将详细介绍锻件质量控制的标准格式文本,包括质量控制目标、质量控制方法、质量控制标准等内容。
二、质量控制目标1. 提高锻件的机械性能:通过合理的锻造工艺和材料选择,使锻件具有良好的力学性能,如强度、韧性、硬度等。
2. 保证锻件的尺寸精度:控制锻件的尺寸偏差在合理范围内,确保锻件能够符合设计要求并与其他零部件配合良好。
3. 提高锻件的表面质量:控制锻件的表面缺陷,如气泡、夹杂、裂纹等,确保锻件的表面光洁度和无损伤。
三、质量控制方法1. 工艺参数控制:根据锻件的材料和形状特点,合理选择锻造工艺参数,如锻造温度、锻造速度、锻造压力等,以确保锻件的质量。
2. 检测手段应用:采用合适的检测手段对锻件进行质量检测,如超声波检测、磁粉检测、尺寸测量等,及时发现并排除锻件的缺陷。
3. 质量控制流程:建立完善的质量控制流程,包括原材料检验、锻造工艺控制、质量检测、表面处理等环节,确保每个环节都符合质量要求。
四、质量控制标准1. 强度标准:根据锻件的使用场景和设计要求,确定锻件的强度标准。
例如,对于汽车发动机曲轴锻件,其强度标准应满足相关国家标准。
2. 尺寸精度标准:根据锻件的设计图纸要求,确定锻件的尺寸精度标准。
例如,对于航空发动机涡轮叶片锻件,其尺寸精度应满足航空行业标准。
3. 表面质量标准:根据锻件的使用要求,确定锻件的表面质量标准。
例如,对于机械制造中的锻件,其表面质量应满足相关行业标准。
五、质量控制措施1. 质量培训:对参与锻件生产和质量控制的人员进行培训,提高其质量意识和技能水平,确保质量控制措施的有效实施。
2. 设备维护:定期对锻件生产设备进行维护保养,确保设备的正常运行,避免设备故障对锻件质量造成影响。
3. 过程监控:对锻件生产过程进行实时监控,及时发现并纠正生产过程中的异常情况,确保锻件的质量稳定。
锻件生产中质量控制的节点及问题修复(二)

锻件生产中质量控制的节点及问题修复(二)引言概述:锻件生产中的质量控制对于确保产品质量和客户满意度至关重要。
本文将在前一篇文章的基础上继续探讨锻件生产中的质量控制的节点和问题修复。
通过对质量控制节点的认识和解决问题的方法,可以提高锻件生产的质量,降低质量风险,增加企业竞争力。
正文:一、原材料质量控制1. 严格选择合格的锻造原材料供应商2. 对原材料进行质量检测,包括化学成分、机械性能等3. 建立合理的原材料进货检验标准4. 定期对原材料供应商进行评估和管理二、锻件成型质量控制1. 控制锻造温度和时间,确保锻造工艺参数符合要求2. 检查锻件表面质量,确保无裂纹、麻花、气孔等缺陷3. 进行锻件尺寸测量,保障尺寸精度符合设计要求4. 对锻件进行硬度测试,评估材料的力学性能5. 利用无损检测技术对锻件进行质检,发现隐蔽缺陷三、热处理质量控制1. 控制热处理温度和时间,保持合适的工艺参数2. 定期对热处理设备和工艺进行校准和维护3. 检查热处理后的锻件组织和性能,确保满足要求4. 严禁出现过热、过淬和组织不均匀等质量问题5. 对热处理过程进行记录和跟踪,便于问题溯源和控制四、机械加工质量控制1. 选择合适的加工工艺和工装,确保加工质量2. 进行加工参数的精确控制,包括切削速度、进给量等3. 定期检查和保养加工设备,确保设备的正常运行4. 对加工后的锻件进行尺寸检测,确保精度符合要求5. 建立合理的加工过程记录和质量跟踪机制,用于分析和改进五、最终产品质量控制1. 对锻件进行总体质量检查,确保无缺陷和问题2. 进行性能测试,包括强度、硬度、韧性等方面3. 进行外观检测,包括表面光洁度、形状等方面4. 进行功能验证,确保锻件能满足设计要求5. 建立合理的产品质量追溯体系,便于问题修复和质量管理总结:锻件生产中质量控制的节点及问题修复是确保产品质量的关键。
通过对原材料、成型、热处理、机械加工和最终产品的质量控制,可以降低质量风险,提高产品质量和客户满意度。
锻件质量控制的工作内容(二)
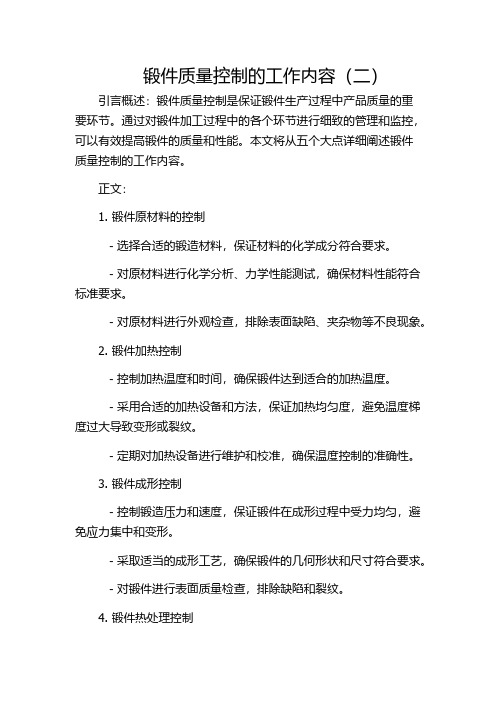
锻件质量控制的工作内容(二)引言概述:锻件质量控制是保证锻件生产过程中产品质量的重要环节。
通过对锻件加工过程中的各个环节进行细致的管理和监控,可以有效提高锻件的质量和性能。
本文将从五个大点详细阐述锻件质量控制的工作内容。
正文:1. 锻件原材料的控制- 选择合适的锻造材料,保证材料的化学成分符合要求。
- 对原材料进行化学分析、力学性能测试,确保材料性能符合标准要求。
- 对原材料进行外观检查,排除表面缺陷、夹杂物等不良现象。
2. 锻件加热控制- 控制加热温度和时间,确保锻件达到适合的加热温度。
- 采用合适的加热设备和方法,保证加热均匀度,避免温度梯度过大导致变形或裂纹。
- 定期对加热设备进行维护和校准,确保温度控制的准确性。
3. 锻件成形控制- 控制锻造压力和速度,保证锻件在成形过程中受力均匀,避免应力集中和变形。
- 采取适当的成形工艺,确保锻件的几何形状和尺寸符合要求。
- 对锻件进行表面质量检查,排除缺陷和裂纹。
4. 锻件热处理控制- 选择合适的热处理工艺,根据锻件的材料和性能要求进行退火、正火、淬火等处理。
- 控制热处理温度和时间,确保锻件达到所需的组织结构和硬度。
- 对热处理设备进行定期检查和维护,保证热处理过程的稳定性和可靠性。
5. 锻件检测与检验- 采用合适的检测方法,如超声波检测、射线检测、磁粉检测等,检查锻件的内部和外部缺陷。
- 进行硬度测试、拉伸试验、冲击试验等力学性能测试,确保锻件的力学性能符合标准。
- 进行尺寸测量和形状检查,检验锻件的几何尺寸和外观质量。
总结:锻件质量控制的工作内容包括锻件原材料的控制、锻件加热控制、锻件成形控制、锻件热处理控制以及锻件检测与检验。
通过严格管理和监控每个环节,可以保证锻件的质量和性能达到设计要求,提高产品的可靠性和安全性。
锻件质量控制的方法与要点(二)
锻件质量控制的方法与要点(二)在锻件生产过程中,质量控制是至关重要的。
它不仅直接关系到产品的质量,还涉及到生产效率和成本控制。
本文将介绍锻件质量控制的方法和要点,以帮助企业提升锻件的质量水平。
引言概述:随着科技的不断进步,锻件在航空、汽车、机械等行业中的应用越来越广泛。
但由于锻件生产过程中的复杂性和多变性,质量控制成为制约锻件产品质量和生产效率的重要因素。
为了提高锻件质量,必须采取一系列的控制方法和关注要点。
一、材料选择和质量检验1.选择合适的材料:根据锻件的应用环境和技术要求,选择具有良好机械性能和耐热性能的材料,以确保锻件的质量。
2.材料质量检验:在材料进厂之前,进行严格的材料质量检验,包括化学成分、力学性能和金相组织等方面的检测,以确保原材料符合要求。
3.瑕疵检测:利用无损检测技术对材料进行瑕疵检测,检查是否存在裂纹、夹杂物等缺陷,以避免这些缺陷对锻件的影响。
二、锻造过程控制1.合理设计模具:根据锻件的形状、尺寸和结构等要求,合理设计模具,并进行模具的加热控制,以保证锻件的成形质量。
2.锻造温度控制:合理控制锻造温度,避免过高或过低的温度对锻件的性能造成不良影响。
3.保持压力和变形速度的控制:在锻造过程中,保持适当的压力和变形速度,以确保锻件的均匀性和一致性。
4.锻件冷却控制:在锻件完成后,进行合理的冷却处理,以消除内部应力,提高锻件的强度和韧性。
5.锻件尺寸和形状控制:通过更细致的模具设计和更精确的锻造工艺控制,实现锻件尺寸和形状的精确控制。
三、热处理和表面处理1.热处理工艺的选择:根据锻件的材料和要求,选择合适的热处理工艺,以改善锻件的组织结构和性能。
2.热处理温度和时间的控制:在热处理过程中,控制温度和时间,确保锻件的热处理效果符合要求。
3.表面处理的选择:根据锻件的应用要求,选择合适的表面处理方式,如表面涂层、镀层等,以提高锻件的耐腐蚀性和装饰性。
四、非破坏性检测和尺寸检验1.非破坏性检测方法的选择:根据锻件的形状和结构,选择合适的非破坏性检测方法,如超声波检测、磁粉检测等,以检测锻件的内部缺陷。
锻件质量控制
锻件质量控制引言概述:锻件是一种常见的金属加工工艺,广泛应用于航空航天、汽车、机械制造等领域。
在生产过程中,保证锻件的质量是至关重要的。
本文将从材料选择、工艺控制、检测手段、质量管理和人员培训等五个方面来探讨如何进行锻件质量控制。
一、材料选择1.1 选择合适的原材料在进行锻件生产之前,首先要选择合适的原材料,包括金属材料的种类、牌号和质量等。
原材料的质量直接影响到锻件的成品质量。
1.2 严格控制原材料的化学成分在进行锻件生产前,要对原材料的化学成分进行严格控制,确保符合相关标准和要求。
化学成分不合格会导致锻件的性能不稳定,影响使用寿命。
1.3 确保原材料的完整性和无缺陷在选择原材料时,要确保其表面光洁,无明显的缺陷和裂纹。
原材料的完整性对于锻件的质量有着重要的影响。
二、工艺控制2.1 严格控制锻造温度和压力在进行锻造过程中,要严格控制锻造温度和压力,确保锻件的成形质量和尺寸精度。
温度和压力的控制是保证锻件质量的关键。
2.2 控制锻造速度和变形量在锻造过程中,要控制锻造速度和变形量,避免过快或过慢导致锻件的内部组织不均匀或尺寸不稳定。
合理的速度和变形量有助于提高锻件的力学性能。
2.3 确保锻造工艺的稳定性和可控性在进行锻造过程中,要确保工艺的稳定性和可控性,避免因参数变化导致锻件质量的波动。
稳定的工艺是保证锻件质量稳定的基础。
三、检测手段3.1 使用先进的无损检测技术在锻件生产过程中,要使用先进的无损检测技术,如超声波检测、磁粉检测等,对锻件进行全面的检测,确保无缺陷和内部质量问题。
3.2 进行尺寸和形状检测除了无损检测外,还要对锻件的尺寸和形状进行检测,确保符合设计要求。
尺寸和形状的偏差会直接影响到锻件的使用效果。
3.3 定期进行质量抽检在生产过程中,要定期进行质量抽检,对锻件的质量进行把关。
及时发现问题并进行处理,确保产品质量符合标准。
四、质量管理4.1 建立完善的质量管理体系在进行锻件生产过程中,要建立完善的质量管理体系,包括质量标准、质量控制流程、质量记录等,确保每一道工序都符合质量要求。
锻件质量控制
锻件质量控制一、引言锻件是一种常见的金属加工工艺,广泛应用于各个领域。
为了保证锻件的质量,提高产品的可靠性和性能,需要进行严格的质量控制。
本文将详细介绍锻件质量控制的标准格式,包括质量控制的目的、范围、方法和要求等内容。
二、质量控制的目的锻件质量控制的目的是确保锻件的尺寸精度、力学性能和表面质量符合设计要求,以满足产品的使用需求。
通过质量控制,可以降低产品的不合格率,提高生产效率,降低生产成本,增强企业的竞争力。
三、质量控制的范围锻件质量控制的范围包括以下几个方面:1. 尺寸精度控制:对锻件的尺寸进行严格控制,确保尺寸误差在允许范围内。
2. 力学性能控制:对锻件的力学性能进行测试和评估,确保其强度、韧性等性能指标符合要求。
3. 表面质量控制:对锻件的表面进行检查,确保表面无裂纹、气孔、夹杂等缺陷,并满足表面光洁度要求。
4. 化学成分控制:对锻件的化学成分进行分析和检测,确保成分符合设计要求。
四、质量控制的方法锻件质量控制可以通过以下几种方法进行:1. 技术文件控制:制定和执行相关的技术文件,包括工艺文件、检验规程、工作指导书等,确保生产过程的规范化和标准化。
2. 检验和测试:使用合适的检验和测试方法,对锻件的尺寸、力学性能、表面质量等进行检测和评估。
常用的方法包括三坐标测量、拉伸试验、硬度测试、金相检查等。
3. 过程控制:通过控制锻件的加热温度、锻造速度、锻造力度等工艺参数,确保锻件的质量稳定性。
4. 不良品控制:建立不良品处理和追溯体系,对不合格的锻件进行分类、处理和追溯,以避免不合格产品流入市场。
五、质量控制的要求锻件质量控制需要满足以下几个要求:1. 全员参与:质量控制是企业的全员责任,每个员工都应该对质量负责,积极参与质量控制活动。
2. 持续改进:质量控制应该是一个持续改进的过程,通过不断改进工艺、提高设备精度、培训员工等方式,提高产品质量。
3. 数据分析:通过收集和分析质量数据,了解生产过程中存在的问题和缺陷,并采取相应的措施进行改进。
提高锻件质量有效方法
要求: 具有足够的疲劳强度和结构刚度,须选 用高强度材料; 具有合理的结构形状; 原材料通常选用45号钢、 35CrMo、 42CrMo 和18CrNiWA 等合金钢; 表面质量及尺寸精度要求很高 。
为了提高连杆锻造质量, 除把好原材 料、下料、加热、切边、热处理、清理等 关外,最主要的是解决好工艺、工装设计。 本文从模具设计参数选择出发, 总结出模锻 件质量与锻模设计的关系。
工字形截面两筋板高而窄中间腹板宽而薄,不允许有折叠产生,而横截面 有矩形凸台和圆形凸台的工字形杆身截面在锻造过程中容易在转角处产生 折叠。
图2工字形杆身横截面有矩形矩凸台
图3 工字形杆身横截面有圆形矩凸台
图4 形成锻件折叠过程
要避免在锻造过程中ቤተ መጻሕፍቲ ባይዱ工字形杆身上 圆角处产生折叠,采取的措施有: 1) 送入终锻前的毛坯采用预锻或自由 锻制坯成合适的杆身形状; 2) 在设计预锻模膛时,要适当加大工 字形杆身上的圆角和内斜度; 3) 控制预锻后坯料的截面积,使预锻 后坯料放到终锻模膛中变形时,大体上在 充满两筋以后终锻的过程刚好结束,而不 是充满终锻模膛后尚还有大量多余金属外 流,由此可避免在终锻时产生折叠。
4.2锻件折叠
4.2锻件折叠
锻件产生塑性变形时,由于金属的流动、 转折处易形成折叠; 当锻件圆角小,制坯尺寸、润滑和操作 不当,易产生折叠; 尤其是 10t 以下的模锻锤,滚挤、弯曲、 预锻、终锻在同一锻模上,锻造时更易产 生折叠。
( 1) 工字形杆身折叠(图2—4) ( 2) 圆弧过度处折叠(图5) ( 3) 连杆大头平面周向折叠
根据生产大中型连杆模锻件的经验,总结 出大中型连杆模锻时选取中心距收缩率Z 参 数,如表1所示。
表1 中心距收缩率选取参数 Z
- 1、下载文档前请自行甄别文档内容的完整性,平台不提供额外的编辑、内容补充、找答案等附加服务。
- 2、"仅部分预览"的文档,不可在线预览部分如存在完整性等问题,可反馈申请退款(可完整预览的文档不适用该条件!)。
- 3、如文档侵犯您的权益,请联系客服反馈,我们会尽快为您处理(人工客服工作时间:9:00-18:30)。
工字形截面两筋板高而窄中间腹板宽而薄,不允许有折叠产生,而横截面 有矩形凸台和圆形凸台的工字形杆身截面在锻造过程中容易在转角处产生 折叠。
图2工字形杆身横截面有矩形矩凸台
图3 工字形杆身横截面有圆形矩凸台
图4 形成锻件折叠过程
要避免在锻造过程中在工字形杆身上 圆角处产生折叠,采取的措施有: 1) 送入终锻前的毛坯采用预锻或自由 锻制坯成合适的杆身形状; 2) 在设计预锻模膛时,要适当加大工 字形杆身上的圆角和内斜度; 3) 控制预锻后坯料的截面积,使预锻 后坯料放到终锻模膛中变形时,大体上在 充满两筋以后终锻的过程刚好结束,而不 是充满终锻模膛后尚还有大量多余金属外 流,由此可避免在终锻时产生折叠。
提高锻件质量有效方法
——大中型柴油机连杆模锻件
姓名: 学号: 专业:材料加工工程 指导教师:
目录
பைடு நூலகம்
目录
1、序言 2、提高锻件质量有效方法分类 3、连杆锻件 4、连杆模锻件质量问题及有效解决方法 5、总结
1、序言
1、序言
锻件毛坯质量的好坏直接影响成品的 质量,也就是说提高锻件质量,对提高锻 件精度、节约金属材料、降低锻造成本、 提高生产效率有着重要意义,所以要有效 的寻找提高锻件质量的有效方法。
要求: 具有足够的疲劳强度和结构刚度,须选 用高强度材料; 具有合理的结构形状; 原材料通常选用45号钢、 35CrMo、 42CrMo 和18CrNiWA 等合金钢; 表面质量及尺寸精度要求很高 。
为了提高连杆锻造质量, 除把好原材 料、下料、加热、切边、热处理、清理等 关外,最主要的是解决好工艺、工装设计。 本文从模具设计参数选择出发, 总结出模锻 件质量与锻模设计的关系。
谢谢观看!
根据公式 H = h( 1 +δ% ) 式中 H —热锻件图高度 尺寸 ( mm) h —冷锻件图高度 尺寸 ( mm) δ—收缩率 (% ) 计算得到:
H = ( 94-1.1)×( 1+1.25%) ≈94mm
(式中94mm为图1中280连杆锻件大、小 头高度尺寸,1.1mm为高度尺寸的下差) 图 1 280 连杆锻件简图
4.2锻件折叠
4.2锻件折叠
锻件产生塑性变形时,由于金属的流动、 转折处易形成折叠; 当锻件圆角小,制坯尺寸、润滑和操作 不当,易产生折叠; 尤其是 10t 以下的模锻锤,滚挤、弯曲、 预锻、终锻在同一锻模上,锻造时更易产 生折叠。
( 1) 工字形杆身折叠(图2—4) ( 2) 圆弧过度处折叠(图5) ( 3) 连杆大头平面周向折叠
4、连杆模锻件质量问题及有效解决方法
4、连杆模锻件质量问题及有效解决方法
大中型连杆模锻件通常尺寸较大,质 量较重。由于受到锻模尺寸的限制,考虑 到模锻锤上操作的劳动强度和锻模易破裂 及成本等因素,一般不设计制坯模腔,更 大连杆甚至没有设计预锻模腔,而是采用 自由锻制坯 。
锻件质量与模具设计时所选择的参数的 关系非常大。 若参数选择不当,将导致锻模返修甚 至锻件返修和报废,严重影响生产进度,增 加生产成本。
2、提高锻件质量有效方法分类
2、提高锻件质量有效方法分类
2.1以切代锻 2.2仿形切割成形 2.3胎模锻代替自由锻 2.4以压代锻 2.5锯头代替剁头 2.6建立健全质量保证体系
3、连杆锻件
3、连杆锻件
定义:连杆是柴油机的重要零件之一,它 将 活塞和曲轴连接起来,把气缸内燃料所 产生的气体压力传递到曲轴上去,输出扭 矩。
图5 R 280圆弧处折叠形成过程 5 280 如图5 所示为280连杆容易在R280 圆弧过度处产生折 叠,这是由于在自由锻制坯时大头与杆身交界处圆弧半径 偏小或斜度过大,在模锻成形时,由于此处需要的金属较 多,坯料难以充满,形成空穴,按照最小阻尼定律,金属 充满后,多余金属充填空穴,以至形成折叠,其变形过程 如图10a、b、c,后经修改圆弧半径和斜度,消除了端部折 叠。
根据生产大中型连杆模锻件的经验,总结 出大中型连杆模锻时选取中心距收缩率Z 参 数,如表1所示。
表1 中心距收缩率选取参数 Z
5、总结
5、总结
通过对有代表性的大中型柴油机连杆在蒸 汽—空气模锻锤锻造时,易产生的连杆模锻件高 度尺寸锻不靠,连杆的工字形杆身、圆弧过度处、 大头平面周向折叠及连杆大小头孔中心距超长等 几种常见质量问题的形成原因进行了分析,提出 了合理选择锻模设计参数、结构,对大中型连杆 模锻件高度尺寸超差、折叠、大小头孔中心距超 长等质量问题得到有效控制,解决了模锻工艺的 关键难点,经过长期大批量生产实践表明:锻造 质量问题的产生有很多情况是由于工艺、工装设 计不当造成的,只要选取了合理的技术参数,一 些常见质量问题是可以得到很好解决。
因模具设计参数选择不当而产生的主 要缺陷有: ( 1) 锻件高度锻不靠, 缺肉充不满; ( 2) 折叠; ( 3) 中心距超长等。
4.1锻件高度锻不靠
4.1锻件高度锻不靠
由于连杆质量较大,尤其是大头料多, 因此需要的锻造力较大,往往产生小头较 能锻靠,在大头锻不靠情况。 为避免锻件高度方向因锻不靠超差造 成缺肉充不满或锻造次数过多,锻模寿命 降低,大型连杆热锻件图高度尺寸在设计 模具时采用下差设计法,即把锻件图上锻 件下差尺寸作为计算热锻件尺寸时的锻件 名义尺寸,选取的收缩率为1.25%。 如图1所示 280机车柴油机连杆锻件即采 用了此法。
3.3连杆大小头孔中心距超长
3.3连杆大小头孔中心距超长
连杆大小头孔中心距是连杆机械加工的定位尺 寸,因没有加工余量,在模锻时也不因模膛磨损 和变形而发生变化。 产生中心距超长原因主要是弯曲、翘曲部分 在热校正时伸长,而此时的温度又偏低,使伸长 部分收缩不回去,而影响校正温度的有工序次数 及工序间的配合快慢,杆身横截面形状和尺寸、 连杆及锻模材质等。