装饰工程:无机人造大理石的原料、工艺及性能
人造大理石配方和生产法

人造大理石配方和生产法人造大理石的配方主要包括树脂、填充剂、颜料和添加剂等。
一般使用的主要树脂是聚酯树脂或丙烯酸树脂。
填充剂是增加材料密度的重要成分,常使用的填充剂有天然石粉、石英粉和玻璃纤维等。
颜料是为了使人造大理石具有不同的颜色和纹理,常使用的颜料有金属氧化物、有机颜料和无机颜料等。
添加剂包括稳定剂、消泡剂和硬化剂等,用于调节材料的性能和工艺特性。
首先,将预先准备好的树脂和填充剂、颜料等按照一定比例混合拌和,确保材料充分混合均匀。
在拌和过程中,根据需要可以加入一些添加剂,如稳定剂和消泡剂等,以提高材料的稳定性和加工性能。
接下来,将混合好的材料倒入模具中进行浇注。
模具可以根据客户需求定制不同的纹理和形状。
浇注好的材料需要进行振动处理,以去除空气泡和确保材料充分填充模具。
然后,对浇注好的材料进行整形和修整。
根据需要可以进行压制、切割、打磨等处理,使材料的表面平整光滑,并且形成所需的纹理和形状。
最后,将整形修整好的材料进行固化。
固化一般有两种方法,一种是室温固化,需要一定的时间来让材料自然固化;另一种是热固化,通过加热材料以加快固化速度。
人造大理石的生产过程中需要注意一些关键技术和问题。
首先,材料的混合拌和需要控制好比例和时间,以确保材料均匀混合,避免出现不均匀或凝结现象。
其次,模具的制作需要精准和耐用,以保证所制造的人造大理石的质量和形状。
最后,固化的温度和时间需要根据材料的特性来确定,以确保人造大理石的硬度和稳定性。
总之,人造大理石是一种使用树脂、填充剂、颜料和添加剂等原材料通过拌和、浇注、整形和固化等工艺制成的人工合成材料。
随着科技的进步和人们对装饰材料的需求不断增加,人造大理石在室内装饰和建筑装饰领域的应用前景非常广阔。
人造大理石生产工艺

人造大理石生产工艺人造大理石是一种以天然石材或矿物粉末为主要原料,通过化学合成或物理合成方法制成的一种人造石材。
其外观、质感和花纹与天然大理石非常相似,但价格更经济、颜色更丰富且具有一定的抗污性能。
人造大理石的主要生产工艺包括原料准备、原料混合、成型、固化、抛光和包装等步骤。
下面我们来详细介绍一下这个过程。
首先是原料准备。
人造大理石的主要原料包括天然石材粉末、填充物、增强材料、颜料、固化剂等。
这些原料需要经过严格的筛选、研磨和称重等操作,确保其质量和配比精确。
接下来是原料混合。
将经过准备的各种原料按照一定比例混合均匀。
这个步骤的目的是确保不同组分在成型过程中的分布均匀性,以及避免产生结块等问题。
然后是成型。
将混合均匀的原料放入模具中,通过振动、压制等方式,使原料成形。
成型的方式可以有压制法、挤出法、注塑法等不同的方式,具体的选择根据产品的形状和要求来决定。
成型完成后,进入固化阶段。
在固化过程中,原料中的固化剂会发生反应,使得原料逐渐固化硬化。
这个过程需要控制好时间和温度,以确保固化的效果和产品的质量。
固化完成后,进行抛光处理。
抛光主要是利用机械设备对产品表面进行打磨和抛光,使其表面光滑、平整,达到与天然大理石相似的效果。
最后是包装。
将成品进行分类、检查、包装。
包装可以选择木箱、木托盘、纸箱等不同的包装方式,以防止产品在运输过程中的损坏。
通过以上的工艺步骤,人造大理石的生产过程就完成了。
整个工艺过程需要严格控制各个环节的参数,确保产品质量和一致性。
同时,需要进行必要的质量检验,以确保产品符合相关的标准和要求。
人造大理石的生产工艺因生产厂家的不同可能会有所差异,但总体上可以按照以上的步骤进行操作。
人造大理石配方和生产法

人造大理石配方和生产法1.配方人造大理石的主要成分包括树脂、填料、增强材料、颜料等。
其中,树脂起到固化和粘合的作用,填料可以增加材料的硬度和稳定性,增强材料可以增加材料的强度和韧性,颜料用于给材料着色。
根据具体需求,可以对各个成分的比例进行调整。
2.生产方法(1)树脂混合:将树脂和固化剂按照一定比例混合,并进行搅拌,以保证树脂的均匀分散和固化剂的充分反应。
(2)填料添加:将填料按照一定比例添加到树脂混合物中,并进行充分搅拌,以保证填料均匀分散在树脂中。
(3)增强材料添加:根据需要,可以添加一些增强材料来提高材料的强度和韧性。
(4)颜料着色:根据需要,可以添加一些颜料来给材料着色,通过调整颜料的比例可以制作出不同颜色的人造大理石。
(5)搅拌和紧实:将上述混合物进行搅拌,以保证各个成分均匀混合。
然后将混合物倒入模具中,利用紧实机械将材料进行紧实,排除空气和使材料更加均匀。
(6)固化和硬化:将填充模具的混合物放置在合适的环境中进行固化和硬化。
通常使用真空机械来确保材料的固化和硬化过程中无气泡。
(7)剪切和修整:固化之后,将模具取出,使用剪切机械将多余的材料进行修整,保证产品的边缘光滑。
(8)抛光和打磨:经过剪切和修整之后,使用抛光机械对产品进行抛光和打磨,使产品表面光滑细腻。
(9)清洁和包装:经过抛光和打磨之后,使用清洁机械对产品进行清洁,并进行包装,以便运输和销售。
除了上述的传统生产方法,目前还有一种新型的生产方法,即3D打印技术。
利用3D打印机,可以直接将人造大理石的混合物打印成所需的形状,无需使用模具,大大提高了生产效率和灵活性。
综上所述,人造大理石的配方和生产法主要包括树脂混合、填料添加、增强材料添加、颜料着色、搅拌和紧实、固化和硬化、剪切和修整、抛光和打磨、清洁和包装等步骤。
这些步骤的具体操作和条件可以根据实际情况进行调整和改进。
人造大理石的生产方法不仅可以制作出高质量的产品,而且还可以根据需求进行个性化定制,满足不同客户的需求。
人造大理石配方和工艺(转)

生产石质人造大理石是以不饱和聚酯树脂为粘合剂,以石粉为主要填料,配以玻璃粉、矿渣石等为辅料加工制成。
石质人造大理石的生产工序包括原料选配、模具及其处理、混料、花纹制作、震捣成型、脱模修整等。
1.原料选配用于制作人造大理石的不饱和聚酯树型号很多,目前较为广泛使用的有197号、196号、195号等。
对于石质人造大理石面层的树脂,最好选用透明度高、防老化、阻燃性能优越、表面硬度高的品种。
对于石粉要求并不十分严格,除少数影响树脂固化者外,大多数石粉都可用作填料,但粒度和色泽有一定的要求。
原则上,石粉细,产品表面光泽度就高,但树脂用量多;反之,石粉粗糙,产品致密度差,光泽度低,但可节省树脂。
我们将石粉和碎玻璃粉进行筛分,各类筛分的百分比如:石粉和玻璃的筛分粒度(目) 占总重量的百分比(%)石粉玻璃粉粒度(目)占总重量的百分比(%) 石粉玻璃粉20~40 3.2 44.00 120~140 1.68 2.7040~60 3.7 21.75 140~160 9.8 1.5460~80 2.52 8.25 140~160 2.45 0.5880~100 12.40 9.0 160~180 19.16 2.53100~120 7.40 2.7 180~200 38.25 9.95带色石粉用于制作颜色相同的产品比较理想。
带色石粉不能用于制作白色人造大理石,而用白色石粉则可制作各种色彩的人造大理石。
因此尽可能选用白色纯净的汉白玉石粉、方解石石粉、白石石粉等。
这样不但能保证产品的色调美,而且制品的石质感强。
其他辅助填料,同样对粒度和色泽有不同的要求。
同时还必须考虑辅料与石粉之间的合理配比。
2、模具及其处理生产人造大理石所用的模具分为模板和边框部分。
模板的表面光泽度关系到制品的表面性能。
要求模板必须高度平整、光亮,并且具有一定的硬度。
模板先用清水洗净,若有油污需用洗衣粉或其他去油剂沾水擦洗。
用专用胶漆滚(一般用油印机滚)在模板上涂上脱模剂,晾晒干透以后再用胶滚涂上一层树脂作为面层。
无机人造大理石的原料、工艺及性能 (一)

无机人造大理石的原料、工艺及性能 (一)无机人造大理石是利用化学镶嵌技术将无机材料制造成的类大理石材料,具有天然大理石的外观和感觉,但在价格、耐用性和环保性方面都具有更大的优势。
本文将介绍无机人造大理石的原料、工艺及性能。
一、原料1.氧化铝粉末:是无机人造大理石的主要原料之一,通过高温焙烧氧化铝粉末可制成颜色鲜艳的大理石。
2.硅酸钙:是无机人造大理石的另一个主要原料,具有优美的质感和良好的物理性能。
3.石英砂:无机人造大理石中用量较小,用于增加强度和稳定性。
4.树脂:作为粘合剂和填充材料使用。
二、工艺生产无机人造大理石的工艺分为以下几个主要步骤:1.材料准备:按比例将各种原料混合并加入适量的树脂进行搅拌。
2.成型:用振动模压机将混合物压制成所需形状,然后置于烘干室进行固化,使成品充分发挥强度和稳定性。
3.研磨和抛光:成型后的无机人造大理石需进行表面处理,先磨去表层的粗糙度,然后再抛光,这样可以使表面更加均匀光滑,达到天然石材般的效果。
三、性能1.外观:无机人造大理石拥有天然大理石的纹理和光泽感,颜色丰富,可实现各种风格和需求。
2.环保性:由于其主要采用无机材料制成,没有对环境产生危害的有机溶剂和其他有害物质,所以无机人造大理石被认为是一种环保材料。
3.耐用性:由于其独特的制作工艺,无机人造大理石具有很强的耐久性和抗污染性能,易于清洁,不易损坏。
4.价格:与天然大理石相比,无机人造大理石的价格相对便宜,适用于那些对价格敏感的人群。
总结:无机人造大理石是一种外观达到天然大理石效果、价格适中、且具有优越的环保性、耐用性和易于处理的优良材料。
在不断提高人们的生活品质和满足人们的需求的同时,也能起到保护环境的作用。
人造大理石的执行标准

人造大理石的执行标准一、人造大理石制作原料及工艺人造大理石是一种优质的装饰材料,广泛应用于建筑、家具、墙面装饰等领域。
其制作原料包括填料、粘合剂和颜料。
填料可以使用天然石材、大理石粉或者人造材料,粘合剂包括树脂、水泥等,颜料则用于调整大理石的色彩。
人造大理石的制作工艺包括配料、搅拌、压制、固化、抛光等步骤。
其中最关键的是配料和搅拌,这直接影响到大理石的外观和质量。
二、人造大理石执行标准为了保证人造大理石的质量和安全性,国家制定了相关的执行标准,主要包括以下几个方面:1. 外观标准:人造大理石的表面应平整、无裂纹、气泡、色差等缺陷,颜色应匀称、自然。
2. 尺寸标准:人造大理石的厚度、长度、宽度应符合标准要求,同时还要考虑翘曲度、弯曲度、平直度等指标。
3. 物理性能标准:人造大理石应具有一定的硬度、抗压强度、防水性能、耐腐蚀性能等指标,以确保其使用寿命和安全性。
4. 化学性能标准:人造大理石应符合国家标准GB/T 288-2009中的相关要求,有限元含量不得超过1.0mg/kg,铜离子迁移量不得超过0.5mg/L,钡含量不得超过2mg/kg。
5. 环保标准:人造大理石应符合国家有关环保标准和法规,不含有害物质,不对人体和环境造成危害,同时也要注意减少能源消耗和二氧化碳排放。
三、人造大理石执行标准的相关标准编号和内容解析目前,国家发布的人造大理石执行标准主要包括以下几个:1. GB/T 3218-2013 人造大理石板材该标准规定了人造大理石板材的分类、起订量、外观质量、物理性能、化学性能、环境性能等多方面指标。
2. JC/T 2297-2013 人造大理石制品该标准规定了人造大理石制品的分类、尺寸、表面质量、物理性能、化学性能、环境性能等多方面指标。
3. QB/T 3980-2010 人造石英石该标准规定了人造石英石的分类、尺寸、表面质量、物理性能、化学性能、环境性能等多方面指标。
以上标准内容繁多,需要对标准进行逐条分析解读,以确保选购的人造大理石符合国家标准。
人造大理石配方和工艺
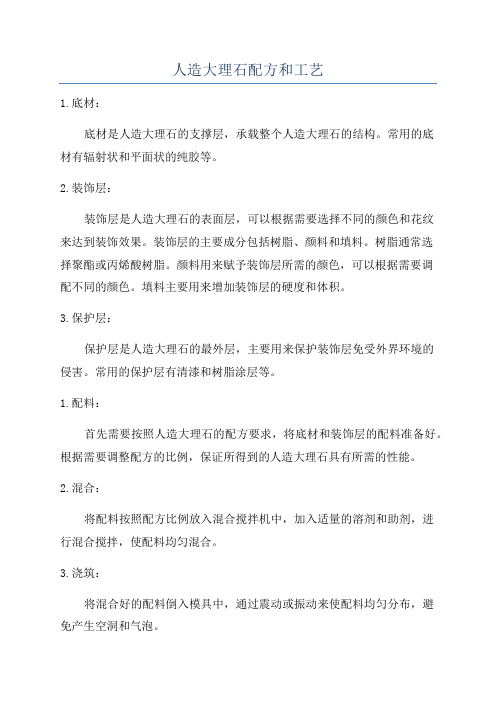
人造大理石配方和工艺1.底材:底材是人造大理石的支撑层,承载整个人造大理石的结构。
常用的底材有辐射状和平面状的纯胶等。
2.装饰层:装饰层是人造大理石的表面层,可以根据需要选择不同的颜色和花纹来达到装饰效果。
装饰层的主要成分包括树脂、颜料和填料。
树脂通常选择聚酯或丙烯酸树脂。
颜料用来赋予装饰层所需的颜色,可以根据需要调配不同的颜色。
填料主要用来增加装饰层的硬度和体积。
3.保护层:保护层是人造大理石的最外层,主要用来保护装饰层免受外界环境的侵害。
常用的保护层有清漆和树脂涂层等。
1.配料:首先需要按照人造大理石的配方要求,将底材和装饰层的配料准备好。
根据需要调整配方的比例,保证所得到的人造大理石具有所需的性能。
2.混合:将配料按照配方比例放入混合搅拌机中,加入适量的溶剂和助剂,进行混合搅拌,使配料均匀混合。
3.浇筑:将混合好的配料倒入模具中,通过震动或振动来使配料均匀分布,避免产生空洞和气泡。
4.加热:在浇筑完成后,需要将模具放入烘箱或加热仓中进行加热,通过加热使树脂固化,使人造大理石的整体性能得到提升。
5.修整:等到人造大理石完全固化后,将其取出模具,进行修整。
修整包括修剪边缘和磨光等工艺,使其表面光滑平整。
6.质检:对制作好的人造大理石进行质量检验,排除存在的缺陷和问题。
7.包装:对合格的人造大理石进行包装和出厂,确保产品的完整性和安全性。
以上是人造大理石的基本配方和工艺,人造大理石具有一定的美观性和耐用性,已经广泛应用于装饰、家具等领域。
随着科技的进步和生产工艺的改善,人造大理石的性能将会更加优越。
人造大理石介绍范文

人造大理石介绍范文人造大理石是一种通过合成材料制成的类似大理石的新型建筑装饰材料。
它通过将天然大理石肌理和色彩进行复制,然后与树脂和其他化学材料混合,制成石材板材。
人造大理石相比天然大理石具有很多优势,因此在建筑装饰领域被广泛应用。
本文将详细介绍人造大理石的制作工艺、特点和应用领域。
人造大理石的制作工艺可以分为三个主要步骤:颜料调配、模具嵌入和固化。
首先,按照设计要求将颜料与树脂等化学材料进行精确配比。
然后,将颜料混合物倒入预先准备好的模具中,模具通常是由铝合金制成。
在模具中,颜料混合物经过振动和压缩,以确保其均匀分布和排气。
最后,放入专门的固化室中,使其在一定的温度下固化。
整个过程类似于天然大理石在地壳中形成的过程。
固化后,将人造大理石板材从模具中取出,进行后续加工和抛光工作。
人造大理石相对于天然大理石具有以下几个明显的优点。
首先,人造大理石的颜色和纹理可以根据需要进行调配和控制,这使得其具有更广泛的应用范围和更多的设计空间。
其次,人造大理石质地均匀,没有天然大理石中的瑕疵和裂纹,更易于加工和抛光,使得其使用寿命更长。
此外,人造大理石的强度和耐磨性也优于天然大理石,减少了使用过程中可能出现的破损和损耗。
另外,由于人造大理石的制作过程控制精确,其尺寸和形状也更容易达到一致性和规格化,便于安装和施工。
最后,人造大理石的生产过程相对节能环保,减少了天然资源的消耗和对环境的影响,是一种可持续发展的建筑材料。
人造大理石目前在建筑装饰领域有着广泛的应用。
首先,人造大理石可以用于室内地面和墙面的装饰,为房间增添高贵、典雅的外观。
其次,人造大理石也常用于室外建筑的装饰,例如公共场所的人行道、广场等。
它能够承受大量的人流和车流,抵抗恶劣的气候条件,保持长时间的美观和品质。
此外,人造大理石还可以用于室内的其他装饰项目,如洗手台、台面、墙面装饰板等。
它易于清洁和维护,能够防水、防污;同时,由于其制作工艺的灵活性,可以满足不同客户和设计师的个性化需求。
- 1、下载文档前请自行甄别文档内容的完整性,平台不提供额外的编辑、内容补充、找答案等附加服务。
- 2、"仅部分预览"的文档,不可在线预览部分如存在完整性等问题,可反馈申请退款(可完整预览的文档不适用该条件!)。
- 3、如文档侵犯您的权益,请联系客服反馈,我们会尽快为您处理(人工客服工作时间:9:00-18:30)。
无机人造大理石的原料、工艺及性能
第1章无机人造大理石的原料组成及作用
无机人造大理石由高铝水泥、石英砂、石子、大砂及无机化工原料为主要原料制成。
8-21-1-1高铝水泥
高铝水泥是→种水硬性胶凝材料,主要化学成分是Ca0、Al203、Si02、Fe203、Mg0、Ti02等。
它能形成坚固耐用的人造大理石表面。
高铝水泥还具有水化快、放热集中、快硬、耐热、耐低温、抗硫酸盐浸蚀等性能。
生产元机人造大理石一般采用625号高铝水泥。
8-21-1-2石子、砂子和石英砂
生产元机人造大理石所用的石子、砂子和石英砂粒度要求不能过大或过小,要干净元杂质。
石子直径一般为5mm左右;砂子要用大砂;石英砂的粒度是80~l00目,硬度在40度以上。
石英砂具有
很高的硬度,可提高无机人造大理石的强度和耐磨性。
8-21-1-3元机.盐和有机外加剂
无机人造大理石所用的无机盐类有CaC12、MgC12、Na2S04、MgS04、Na2Si03和NH4A 1(S04) 2等。
其作用是加速人造大理石的硬化过程,提高早期强度。
例如CaCl2是易溶于水的无机盐,与水泥混合后能与铝酸三钙作用生成不溶性复盐---水化氯铝酸钙,并与氢氧化钙作用生成不溶
于氯化钙溶液的氧氯化钙,这样就增大了水泥浆中固相的比例,形成坚强的骨架,有助于水泥结构的
形成。
Na2S04掺入水泥中,能与水泥水化时析出的氢氧化钙作用,生成具有高度分散性的石膏,均匀分布在混凝土中,使水化硫酸钙迅速形成,大大缩短水泥的硬化时间。
除无机盐外,生产无机人造大
理石还必须使用少量具有表面活性的有机外加剂,它们是减水剂、早强剂、加气剂和消泡剂等。
1
减水剂
常用的减水剂是NN0(亚甲基二苯磺酸销)、MF(次甲基a-甲基苯磺酸销)、三聚氨酸胶甲醒树脂等。
其用量一般是拌和用水量的1‰左右。
早强剂
早强剂的主要作用是提高无机人造大理石的早期强度,加速硬化过程。
常用的早强剂是三乙醇胺、三异丙醇胺等。
早强剂的使用量在底料中一般是拌和用水量的0.5‰;面料中是1%~1.5%。
,
加气剂
加气剂是一种憎水性表面活性物质,如松香皂、烷基苯磺酸钠等。
在无机人造大理石中使用极少量的加气剂,可使大理石的变形能力增大,弹性模量降低,抗裂性和抗冲击性提高,不会因湿度、温度变化而发生裂纹,还能明显地提高抗冻性。
一般加气剂的使用量为高铝水泥用量的0.05‰。
若加气剂用量大,会产生大量空气细泡,且气泡多聚集在砂粒表面,削弱砂粒与水泥之间的胶结,导致强度降低。
第2章生产工艺
无机人造大理石的生产工艺流程为:模具处理→面料配制与浇注→底料配制与浇注→水中塑
化与养护→脱模晾干→包装8-21-2-1模具处理模具使用前,要检查所有焊缝是否牢固、严密,再用
熔化的沥青和石蜡浇灌模框两面的四边缝,以免水浸入框内影响产品质量。
每次脱模后的模具先用刮刀清理,然后用稀硫酸及清水刷洗干净,晾干。
使用时用净布擦干,再用脱模剂(液体石蜡)将四周擦匀。
8-21-2-2面料的配制与浇注
配制无机人造大理石的面料根据正面颜色和花纹而定。
例如生产黑底白纹大理石,可将高铝水
2
泥、铁黑、石英砂与适量的水(含有无机盐和有机外加剂)调成糊状,再用离铝水泥、石英砂和铁白粉用拌和水调成纹料,呈条纹状撒在面料上,浇注在模具玻璃板上,经机械振动,部分纹料发生位移,
从而形成不规则的黑底臼纹大理石图案。
若生产红底花岗岩,只需用不同的颜料制成彩色石子,先撒在玻璃板上,再将高铝水泥、铁红、石英砂用拌和水调成面料,浇注在玻璃板上,经机械振动即可形
成逼真的花岗岩图案。
面料浇注后大约lh可以浇注底料。
8-21-2-3底料的配制与浇注
底料一般采用高铝水泥、石子、砂子、石英砂,用拌合水调成糊状浇注在面料上,底料浇注时要上满,用抹子打平,边角要充实;但底料填充时不得高于模具框沿。
然后保持水平放在工作台上,让其自然硬化,1h后放入水中塑化和养护。
8-21-2-4水中塑化与养护
水中塑化时要注意模具平稳和定时换水,换水时切忌冲坏底料面。
塑化过程中间可用细布将产品背面底部的白色碱层及灰浆轻轻擦去。
水中养护约需70h.
8-2l-2-5脱模与晾干
水中养护70h后出池,晾放1h,然后脱模。
脱模时轻击模具四周,用力要均匀,以防玻璃破裂和产品边角损坏。
出模后的大理石块直立在通风良好的架子上,块间保持一定距离,让其自然晾干(一般
不少于7d)。
晾干后,把大理石背面的毛边用刮刀修理整齐并清除背面上的浮砂。
8-21-2-6包装
无机人造大理石的包装要求要精细,箱子不可过大。
箱内装填要严实,以免运输过程中受振损坏。
装箱时每两块大理石之间要正面相对并用纸隔开,以免因摩擦损坏表面。
第3章无机人造大理石的理化性能
3
作为高级建筑装饰材料的无机人造大理石应具有一定硬度,表面硬度应不低于47度(指甲划过
应不留痕迹);光泽度要好;吸水率要低于9%;抗压性能应达到5kN/cm2以上,抗折性能不低于500N/ cm2;抗冻性能应在-15℃左右元变化;同时还应耐酸、耐碱,在3%盐酸或氢氧化钠溶液中浸泡24h
无变化。
第4章常见质量问题分析
8-2l-4-l沙眼、雾光和脱光
出模后的大理石常发现正面局部有很小的沙眼,这是由于浇注面料后振动不够,料浆内的气泡
排除不净或脱模剂擦得不匀,或面料配制过稠而引起。
因此,模具要仔细处理,脱模剂要涂擦均匀,面料调制要稀稠适当,浇注时不要有堆积现象。
雾光是产品正面有光而不亮,可能是模具背面边缝未封严造成塑化进水而引起。
脱光是产品正面出现无光现象,是由上面料后振动时间过长,面料拌和不均匀,砂粒过粗或掺砂子过多等所致。
8-2l-4-2泛白和龟裂
泛白是指产品晾干后局部或大面积出现云雾状白点,这是由于水中塑化时间短或换水次数少,
或出模后晾放通风不好造成的。
过早包装也会出现泛自现象。
龟裂是指产品表面局部出现裂纹现象,是由于水中塑化时间短,过早出模,受强光暴晒或纹料和
面料中水泥比例过大及纹料过厚等原因所致。
8-21-4-3粘模与底面脱离
粘模是指产品正面亮层局部或大面积粘结在模具玻璃板上,这是由于模具处理时酸洗不好,面
料水泥比例过小或砂子用量过大,或振动时间过长,粗砂击穿面料层或水泥凝固时间短,水泥标号低
等原因所致。
4
底面脱离是指出模时产品的底面脱离上面的现象。
这是由于面料加拌和水量过大,或面料上完后凝固时间过长,或使用的底料和面料水泥型号不同等原因所致。
8-21-4-4难脱模和脱损
难脱模是指产品不易从模具中脱出。
脱损是脱模时产品破裂。
这是因为模具四周边框向里倾斜或模框四边未涂好脱模剂,或是产品凝固时间不够。
稀酸处理模具后,未用清水很好冲洗也会引起上述现象。
8-214-5边角沙眼、毛边和厚度不匀
边角沙眼是因为浇注时边角填料不实,或边角有石子堆积所致。
毛边是由于上完底料后填刮不好,底料超出模具框边内沿而造成。
厚度不匀是上完底料后填刮不平,或放入水中塑化时放置不平,
及换水时直接冲击产品背面的结果。
5。