拉延筋成形力计算公式(中文)
Autoform 拉延筋教学

Autoform V4.1.x Drawbead拉延筋在Autoform V4.1.x 中的可以使用两种不同方式的拉延筋:1、几何拉延筋,就是在压边圈和凹模上使用和实际一样的几何模型;2、简化的拉延筋(或等效拉延筋),即Autoform称之为拉延筋模型。
拉延筋模型不使用实际的几何模型,而是用曲线来模拟,曲线为实际的拉延筋中心的位置,并赋予实际的拉延筋的宽度和约束阻力因子(Fore factor)。
从理论上讲,使用几何拉延筋更能接近实际,但是实际的几何拉延筋有着很多不利的因素,相比较而言还是建议使用简化的拉延筋模型,主要不利的原因有如下几点:1、使用几何拉延筋需要定义额外的模具,准备开始模拟需要花费更长的时间,当需要调整拉延筋时,需要转向CAD系统重新修改拉延筋;2、在压边圈闭合(Binder closure)阶段必须分成非常小的时间步长进行模拟以确保程序识别的小的圆角半径并由足够的单元数量来表示。
仅有这样才能在模拟过程中的保证正确的拉延筋的约束阻力;3、另外,使用几何拉延筋必须使用弹塑性壳单元(Shell element)来进行模拟计算,因为在板料厚度和拉延筋的圆角半径的比率需要使用弹塑性壳单元。
相反,使用简化的拉延筋模型具有如下优点:1、可快速的优化拉延筋参数:在开发工作的初始阶段,对于是否需要拉延筋或需要的拉延筋阻力大小是不确定的;2、模具的几何模型不要修改:拉延筋的优化只需要曲线和阻力系数;3、减少计算时间:不需要拉延筋几何形状成形,所以计算时可以使用大的时间步长。
而且没有不适宜的需要使用弹塑性壳单元的板料料厚与圆角半径的比率,整个模拟过程可以使用增强的模单元来计算,可以大大的缩减计算时间。
因此,如果的确想应用几何拉延筋来模拟计算,建议在最后验证阶段采用,以获取一个比较精确的结果。
另外,使用简化的拉延筋模型,对于拉延模拟评价可以使用结果变量摩擦剪切应力(Friction Shear Stress)来检查它的影响。
基于Dynaform的汽车覆盖件成形中拉延筋的设置与数值模拟_图文

基于Dynaform的汽车覆盖件成形中拉延筋的设置与数值模拟_图文模具技术2020 . No. 639文章编号:100124934(2020 0620039203基于Dynaform 的汽车覆盖件成形中拉延筋的设置与数值模拟郭敏杰, 曾珊琪(陕西科技大学机电工程学院, 陕西西安710021摘要:使用 ETA 公司的CA E 软件Dynaform , 通过求解器L S 2Dyna 计算, 利用E TA/Po st 2p rocessor 来模拟某轿车引擎盖内板的拉深成形。
通过模拟结果的比较, 最终确定拉延筋的最佳布置方案及拉延筋的优化形式等。
缩短了模具设计周期, 降低了设计成本, 提高车身质量。
关键词:Dynaform ; 拉延筋; 汽车覆盖件; 中图分类号:TP391. 9Abstract :By i si twa re ETA/Dynaf or m , t he f or mi ng p rocess of aca r e ngine i calculated by LS 2Dyna a nd si mulated by ETA/Post 2p rocessor. The op ti mal a nd s hap e of draw bea d were deter mi ned by comp a ri ng t he si mulation re 2sults. The i mp roved design could shorte n t he develop me nt cycle of die , reduce design cost a nd i mp rove t he quality of ca r body.K eyw ords :Dynaf or m ; drawbea d ; aut omobile cover ; numerical si mulation0引言拉深件的质量在很大程度上受材料流动的影响。
拉延筋技术
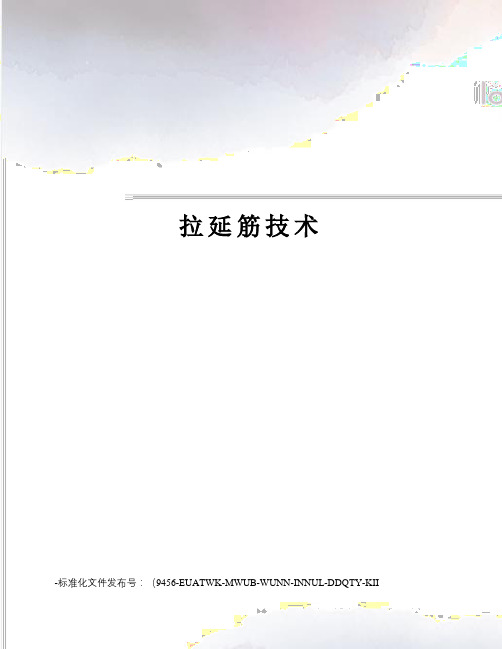
拉延筋技术-标准化文件发布号:(9456-EUATWK-MWUB-WUNN-INNUL-DDQTY-KII拉延筋技术1.拉延筋在板料拉深中的作用拉深成形生产中,尤其是象车身覆盖件等这样的大型工件的拉深工序中,往往会因为零件几何型面的不对称,使得板坯在成形时各处材料沿凹模口的流动速度不均衡(图1一1),造成拉深后的工件,局部减薄量大出现颈缩或者破裂,而有些部位出现起皱、波纹等质量缺陷。
为了改善这种状况,需要在压料面上控制对工件不同部位提供的进料阻力(毛坯在进入凹模前遇到的阻力),即在需要材料多的部位相应的进料阻力小,而在需要材料少的部位相应的进料阻力大(图1一),从而平衡坯料在凹模口部的流动速度差异(图1),提高零件成形质量。
改变压料面上进料阻力的方法有:1.改变压边力或采用变压边力压边2.改变压料面与模具之间的间隙3.改变凹模口圆角半径4.设置拉延筋等。
设置拉延筋是应用较灵活方便、修改较容易的一种方法,主要表现为:(1) 控制变形区材料的进料阻力,调节冲压变形区的拉力及其分布(2) 通过对拉延筋各项参数的适当配置,能够通过均衡工件各部分的进料阻力来调节材料的流动情况,增加坯料流动的稳定性,得到变形均匀的冲压件;(3) 使用拉延筋后,压料面间隙可适当加大,表面精度可适当降低,从而减少压料面的磨损,降低模具制造成本(4) 通过增加径向拉应力,使材料的塑性变形程度、硬化程度得以提高,减少由于变形不足而产生的松弛回弹以及波纹等缺陷,提高工件的刚度(5) 可防止因凸缘周边材料不均匀流动而不可避免产生的皱纹进入修边线内,减轻或消除复杂零件悬空部分因材料集中而发生的内皱现象(6) 拉延筋提供的进料阻力,可以在一定程度上降低对压床吨位的需求;通过增加胀形成分和增大进料阻力,可减小板料外形尺寸,提高材料利用率。
目前 ,在多数板料拉深中,拉延筋是必不可少的模具组成部分,针对拉延筋的研究己经成为当今板料冲压成形领域的重要课题之一。
拉延
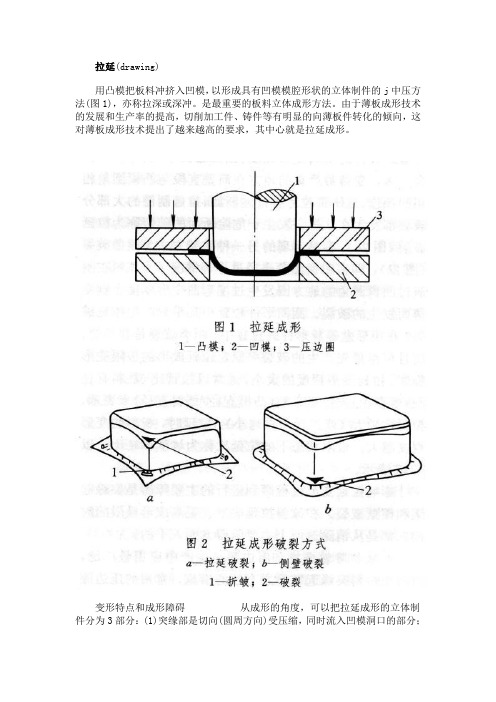
拉延(drawing)用凸模把板料冲挤入凹模,以形成具有凹模模腔形状的立体制件的j中压方法(图1),亦称拉深或深冲。
是最重要的板料立体成形方法。
由于薄板成形技术的发展和生产率的提高,切削加工件、铸件等有明显的向薄板件转化的倾向,这对薄板成形技术提出了越来越高的要求,其中心就是拉延成形。
变形特点和成形障碍从成形的角度,可以把拉延成形的立体制件分为3部分:(1)突缘部是切向(圆周方向)受压缩,同时流入凹模洞口的部分;(2)筒壁部分是传递凸模力的部分;(3)底部是受到凸模力作用的部分。
拉延成形实质上是突缘部的变形。
拉延过程就是使坯料突缘部逐步收缩形成筒壁的过程。
作为拉延成形的特征,在突缘部,由于切向压应力的存在,有产生起皱(见压缩失稳)的危险。
为防止起皱必须设有压边装置。
筒壁部在拉延成形过程中传递并支承凸模力,是拉延成形制件的传力区。
筒壁部材料的承载能力决定着拉延件的最大变形程度。
拉延过程中,制件的筒壁会变薄,变薄最严重的地方在筒壁直段与凸模圆角相切的部位,这一部位称作危险断面,拉延制件的大部分破裂都发生在这里。
发生于危险断面的破裂称为拉延破裂(图2a)。
容易出现的另一种破裂方式为侧壁破裂(图26),即在凹模圆角半径过小等情况下,坯料在刚流过凹模圆角的地方因发生过度弯曲变形厚度急剧变薄而发生的破裂。
圆筒形件拉延中几乎只产生拉延破裂,在矩形盒等异形件的拉延中,两类破裂是共存的,而且根据最先产生的破裂来规定拉延成形的极限变形程度。
拉延变形程度的大小,通常以拉延比(坯料直径/凸模直径)或拉延系数(凸模直径/坯料直径)来表示,拉延比越大(或拉延系数越小),拉延时,板料的变形程度越大。
极限状态下的拉延比称为极限拉延比,以LDR表示。
影响拉延变形过程顺利进行的主要障碍是突缘起皱和筒壁破裂。
在改善拉延成形、提高成形极限的时候,都是从消除这两个主要障碍方面入手的。
起皱和防皱措施压边圈是生产中应用最广泛,对防止板料突缘起皱行之有效的措施。
板料成形中等效拉延筋阻力的模拟计算方法

σ2 | - ( r + 1)σ f = (2 r + 1) ( |σ 1 | +|σ 2 | ) - r| σ 1 +
式 ( 15 )中 ,当 ε≥0 时 , ± 号取正 ; 反之取负 。 2151112 切向应力 σ1 与切向应变 ε 1 的关系 将式 ( 9 ) 和式 ( 10 ) 分别代入式 ( 14 ) 、 式 ( 15 ) 中 ,可得对应于板料初始加载时 ,板料中的切向应力 σ1 和切向应变 ε 1 关系如下 。
2 等效拉延筋阻力的计算
211 等效拉延筋阻力 FDB R
图 1 所示为一半圆形拉延筋 。图中 R b 为凸筋 圆角半径 , R g 为凹筋圆角半径 , g 为凸凹筋单边间 隙 , h 为凸凹筋闭合深度 。板料通过拉延筋时 , 板料 与凸凹筋之间有 3 个接触弧 , 3 个接触弧 i = 1, 2, 3 φ, 2 φ,φ 所对应的接触角 θ 。φ可利用图 1 所示的 i = 板料与凸凹筋的几何关系求得 , 此处从略 。板料分 别在接触弧 1、 2、 3 处 3 次经历弯曲 、 附加拉伸和反 弯曲变形过程 。当退出接触弧 3 后 , 板料横截面中 的切向力即欲求的拉延筋阻力 FDB R , 可按如下公式 计算 。
F′ 3 分别为板料退出接触
弧 1、 2、 3 时由于反弯曲板 横截面所受反弯曲力 。
212 局部坐标系的设定
图 3 中 1、 2、 3 点表示各加载分支的载荷反转 ( ε σ ) 点 ,其中 ri , ri , i = 1, 2, 3 分别表示载荷反转点 i = 1, 2, 3 的应变和应力 。σs0 表示初始屈服应力 , σs1 、 σs2分别表示第一反向加载分支及第二加载分支 的新屈服应力 。考虑到板料在循环加载中存在的 B auschinger效应 , 假设加载分支 i 的载荷反转点应 力 σri和新屈服应力 σsi之间满足如下关系 σs0 ( 3) | σri - σsi | = 2 式 ( 3 )中初始屈服应力 σs0为
拉延模
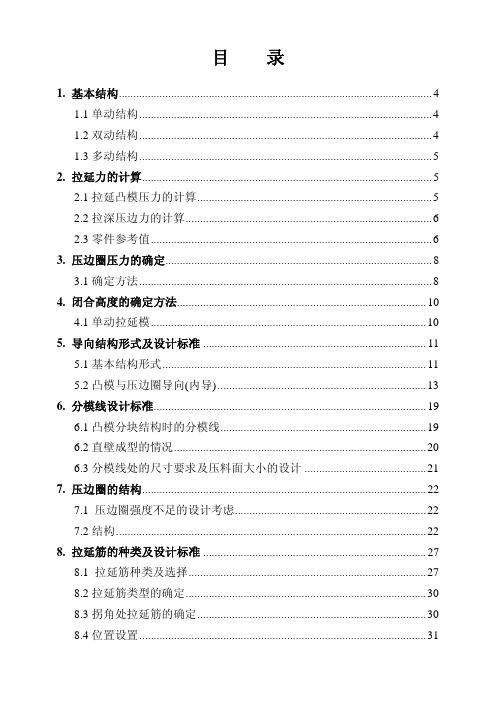
目录1. 基本结构 (4)1.1单动结构 (4)1.2双动结构 (4)1.3多动结构 (5)2. 拉延力的计算 (5)2.1拉延凸模压力的计算 (5)2.2拉深压边力的计算 (6)2.3零件参考值 (6)3. 压边圈压力的确定 (8)3.1确定方法 (8)4. 闭合高度的确定方法 (10)4.1单动拉延模 (10)5. 导向结构形式及设计标准 (11)5.1基本结构形式 (11)5.2凸模与压边圈导向(内导) (13)6. 分模线设计标准 (19)6.1凸模分块结构时的分模线 (19)6.2直壁成型的情况 (20)6.3分模线处的尺寸要求及压料面大小的设计 (21)7. 压边圈的结构 (22)7.1 压边圈强度不足的设计考虑 (22)7.2结构 (22)8. 拉延筋的种类及设计标准 (27)8.1 拉延筋种类及选择 (27)8.2拉延筋类型的确定 (30)8.3拐角处拉延筋的确定 (30)8.4位置设置 (31)8.5装配式拉延筋 (31)8.6外板件及拉延筋设计要求 (32)8.7拉延筋的布置 (32)8.8防斑点措施 (32)8.9拉延筋外观的要求 (32)8.10拉延筋形状及应用 (33)9. 坯料尺寸确定方法 (35)9.1确定坯料的方法 (35)9.2坯料尺寸计算方法 (35)10. 定位板设置 (37)10.1用途 (37)10.2设定标准 (37)10.3带传感器的定位板 (46)11. 安全限位 (49)11.1双动拉延凸模限位 (49)11.2压边圈限位 (51)12. 拉延标记 (53)12.1 用途 (53)12.2设计原则 (53)13. 通气孔 (55)13.1 目的 (55)13.2 设计标准 (56)13.3 结构 (59)14. 顶杆的结构设计 (60)14.1顶杆的形状 (60)14.2顶杆使用个数的决定 (61)14.3凹模顶杆组结构构造 (61)14.4组装顶杆平衡块的构造 (65)15. 安全护板 (69)15.1目的 (69)15.2安装结构 (69)16. 压边圈镦死块的设计标准 (71)16.1设计标准 (71)瑞鹄汽车模具有限公司 编号安徽 . 瑞鹄拉延模结构设计标准页码第4页 共72页1.基本结构1.1单动结构如图1所示。
拉、压、扭簧计算公式

拉、压、扭簧计算公式
拉力弹簧
拉力弹簧的k值与压力弹簧的计算公式相同
·拉力弹簧的初张力:初张力等于适足拉开互相紧贴的弹簧并圈所需的力,初张力在弹簧卷制成形后发生。
拉力弹簧在制作时,因钢丝材质、线径、弹簧指数、静电、润滑油脂、热处理、电镀等不同,使得每个拉力弹簧初始拉力产生不平均的现象。
所以安装各规格的拉力弹簧时,应预拉至各并圈之间稍为分开一些间距所需的力称为初张力。
·初张力=P-(k×F1)=最大负荷-(弹簧常数×拉伸长度)
·拉力弹簧的设计数据,除弹簧尺寸外,更需要计算出最大负荷及变位尺寸的负荷;
·弹簧常数:以k表示,当弹簧被拉伸时,每增加1mm距离的负荷(kgf/mm);
·弹簧常数公式(单位:kgf/mm):
G=线材的钢性模数:碳钢丝G=79300 ;不锈钢丝G=697300 ,磷青铜线G=4500 ,黄铜线G=350
d=线径
Do=OD=外径
Di=ID=内径
Dm=MD=中径=Do-d
N=总圈数
扭力弹簧
·弹簧常数:以k 表示,当弹簧被扭转时,每增加1°扭转角的负荷(kgf/mm).
·弹簧常数公式(单位:kgf/mm):
E=线材之钢性模数:琴钢丝E=21000 ,不锈钢丝E=19400 ,磷青铜线E=11200,黄铜线E=11200
d=线径
Do=OD=外径
Di=ID=内径
Dm=MD=中径=Do-d N=总圈数
R=负荷作用的力臂 p=3.1416。
基于Dynaform的汽车覆盖件成形中拉延筋的设置与数值模拟.
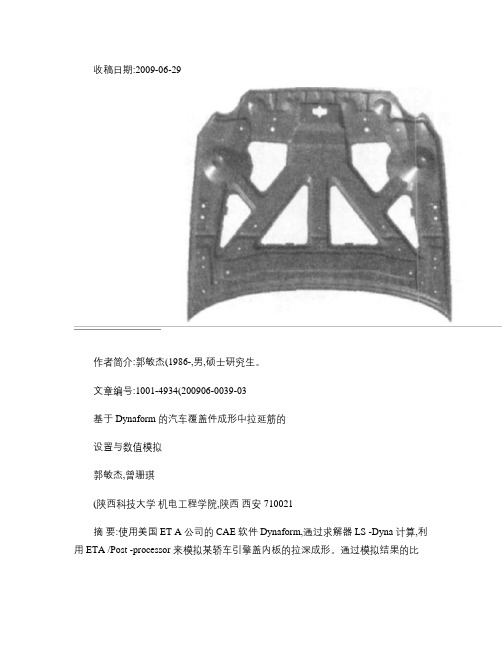
收稿日期:2009-06-29作者简介:郭敏杰(1986-,男,硕士研究生。
文章编号:1001-4934(200906-0039-03基于Dynaform 的汽车覆盖件成形中拉延筋的设置与数值模拟郭敏杰,曾珊琪(陕西科技大学机电工程学院,陕西西安 710021摘要:使用美国ET A 公司的CAE 软件Dynaform,通过求解器LS -Dyna 计算,利用ETA /Post -processor 来模拟某轿车引擎盖内板的拉深成形。
通过模拟结果的比较,最终确定拉延筋的最佳布置方案及拉延筋的优化形式等。
缩短了模具设计周期,降低了设计成本,提高车身质量。
关键词:Dynaform;拉延筋;汽车覆盖件;数值模拟中图分类号:T P391.9 文献标识码:BAbstract:By using increment simulation sof tware ETA/Dynafor m,the forming process of a car engine inner panal w as calculated by LS -Dyn a and simulated byETA/Post -pr ocessor.The optimal setting and sh ape of draw bead w ere deter mined by comparing the simulation r e -sults.T he impr oved design could shorten the development cycle of die,reduce design cost and improve the quality of car body.Keywords:Dynafor m;dr awbead;automobile cover;numerical simulation0 引言拉深件的质量在很大程度上受材料流动的影响。