流量的PLC控制系统设计
基于PLC的流量控制系统
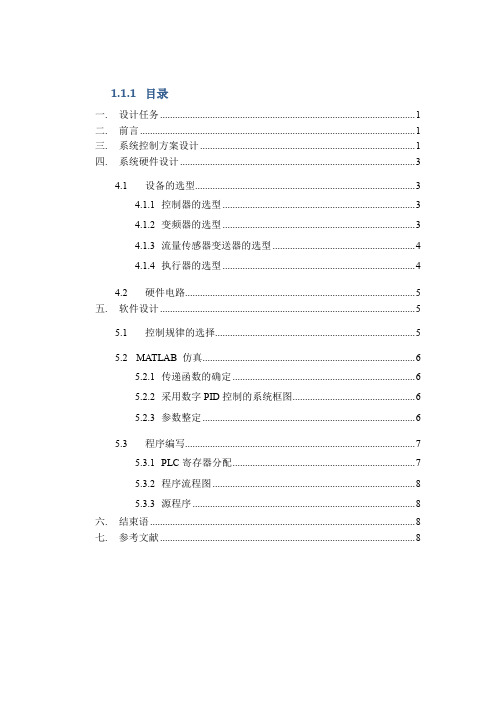
1.1.1目录一.设计任务 (1)二.前言 (1)三.系统控制方案设计 (1)四.系统硬件设计 (3)4.1设备的选型 (3)4.1.1控制器的选型 (3)4.1.2变频器的选型 (3)4.1.3流量传感器变送器的选型 (4)4.1.4执行器的选型 (4)4.2硬件电路 (5)五.软件设计 (5)5.1控制规律的选择 (5)5.2MATLAB 仿真 (6)5.2.1传递函数的确定 (6)5.2.2采用数字PID控制的系统框图 (6)5.2.3参数整定 (6)5.3程序编写 (7)5.3.1PLC寄存器分配 (7)5.3.2程序流程图 (8)5.3.3源程序 (8)六.结束语 (8)七.参考文献 (8)设计题目:智能化流量控制系统设计一.设计任务1、系统构成:系统主要由流量传感器,PLC控制系统、对象、执行器(查找资料自己选择)等组成.传感器、对象、控制器、执行器可查找资料自行选择,控制器选择PLC 为控制器.PLC类型自选。
2、写出流量测量与控制过程,绘制流量控制系统组成框图。
3、系统硬件电路设计自选。
4、编制流量测量控制程序:软件采用模块化程序结构设计,由流量采集程序、流量校准程序、流量控制程序等部分组成二.前言本课程设计来源于工业工程中对于流量的监测和控制过程,其目的是利用PLC来实现过程自动控制。
目前,PLC使用范围可覆盖从替代继电器的简单控制到更复杂的自动化控制,应用领域极为广泛,涉及到所有与自动检测、自动化控制有关的工业及民用领域。
PLC通过模拟量I/O模块和A/D、D/A模块实现模拟量与数字量之间的转换,并对模拟量进行闭环控制。
三.系统控制方案设计图1 控制系统的工艺流程图如图1所示为该控制系统的工艺流程图,该控制系统主要是控制流过管道水的流量,由于系统对控制要求不高,故系统采用单回路控制,被控对象为水的流量,控制量为水泵电机的转速,控制器选用PLC和变频器,传感变送器选用电磁流量传感变送器,执行器选用水泵。
PID流量控制
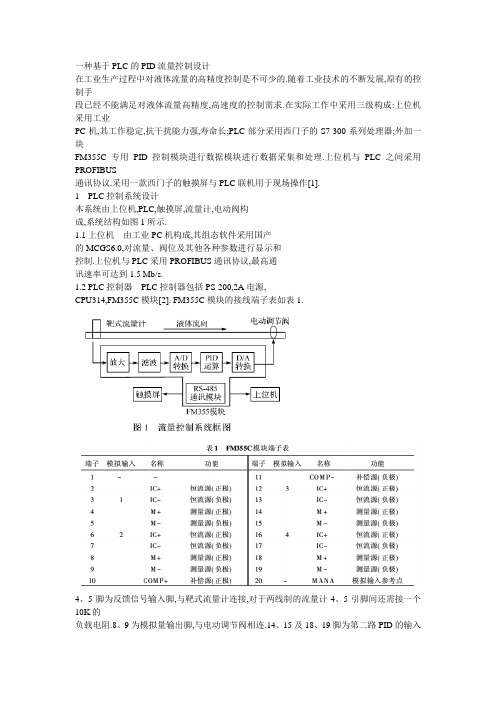
一种基于PLC的PID流量控制设计在工业生产过程中对液体流量的高精度控制是不可少的.随着工业技术的不断发展,原有的控制手段已经不能满足对液体流量高精度,高速度的控制需求.在实际工作中采用三级构成:上位机采用工业PC机,其工作稳定,抗干扰能力强,寿命长;PLC部分采用西门子的S7-300系列处理器;外加一块FM355C专用PID控制模块进行数据模块进行数据采集和处理.上位机与PLC之间采用PROFIBUS通讯协议.采用一款西门子的触摸屏与PLC联机用于现场操作[1].1PLC控制系统设计本系统由上位机,PLC,触摸屏,流量计,电动阀构成,系统结构如图1所示.1.1上位机由工业PC机构成,其组态软件采用国产的MCGS6.0,对流量、阀位及其他各种参数进行显示和控制.上位机与PLC采用PROFIBUS通讯协议,最高通讯速率可达到1.5 Mb/s.1.2 PLC控制器PLC控制器包括PS-200,2A电源,CPU314,FM355C模块[2]. FM355C模块的接线端子表如表1.4、5脚为反馈信号输入脚,与靶式流量计连接,对于两线制的流量计4、5引脚间还需接一个10K的负载电阻.8、9为模拟量输出脚,与电动调节阀相连.14、15及18、19脚为第二路PID的输入与输出.1.3传感器和动作机构流量采集采用数字靶式流量计,该种流量计采用累计计数的工作方式,1 s钟累计1次,工作范围40~1 000 L/h,对大流量的采集较为精确.V型调节球阀利用球芯转动与阀座打开相割打开面积(V形窗口)来调节介质流量,调节性能、自洁性能好,适用于高粘度、悬浮液、纸浆告示不干净、含纤维介质场合.采用直连方式与执行机构连接,具有结构紧凑、尺寸小、重量轻、阻力小、动作稳定可靠等优点.流量计和调节阀的信号范围为4~20 mA,与PLC连接.1.4触摸屏采用西门子的TD100触摸屏,与PLC通过PROFIBUS总线相连.使用PROTOOLS6.0编辑界面监控各种参数.当上位机出现故障时,触摸屏可替代上位机操作,提高了系统的可靠性.2PID算法当被控对象的结构和参数不能完全掌握,或得不到精确的数学模型时,控制理论的其他技术难以采用时,系统控制器的结构和参数必须领先经验和现场调试来确定,这时应用PID控制技术最为方便,即利用比例、积分、微分计算出控制量进行控制[3].PID控制为3环节叠加,公式为:m(t) = Kpe(t)+Kpτde(t)dt+KiTi∫i0e(t)dt,其中Kp为比例系数,Kd为微分系数,τ为微分时间常数,Ki为积分系数.对于离散系统的PID公式为:P(k) = Kp{E(k)+TTi∑kj=0E(j)+TdT[E(k)-E(k-1)]}.3配置PID程序模块对西门子的PLC采用SIMA TIC STEP7 V5.3编程.进入STEP7的编程环境后首先通过“工程向导”配置硬件和网络参数,选用的电源模块为PS-200 2A ,中央处理器为CPU 314IFM,PID控制器为FM355 C型.完成配置后打开OB1主程序块(图2),调用FB31模块(STEP7中有LAD,STL ,FBD三种编程方式,STL为语句表编程方式,其他两种为图形调用方式).其中DB31为分配给FB31的背景块.FB31有如下几个参数必须设置:COM_RST参数地址DB31.DBX44. 0 BOOL型. FM355的启动开关.CHANNEL参数地址DB31.DBX2.0 BOOL型.控制端的通道号(每块FM355含两个通道).LMN_RE参数地址DB31.DBX52BOOL,参数类型为REAL型(32位浮点数).存储的是在未启动PID控制时的阀位值(即手动控制值),取值范围为0~100(系统将默认这些数值为电动阀的开度百分数),该参数在PID控制启动后不起作用.LMN_REON参数地址DB31.DBX6.4,参数类型BOOL型(在STEP7中为1位二进制数).当为1时PID控制关闭,LMN_RE的值作为输出值送给电动调节阀.当为0时,PID控制超作用,LMN_RE无效.PHASE参数地址DB31.DBD4,参数类型INT型(16位无符号整数).PID的相位控制,为1时控制相位反向180°.SP_RE参数地址DB31.DBD48,参数类型REAL型.PID 控制的设定值,取值范围为0~100(%).PID控制启动后模块通过计算该值与采集值的差值ER来改变输出值,仅当LMN_REON为0时有效.DEADB_W参数地址DB31.DBD104,参数类型REAL型.默认值为0,单位值为0,单位Hz.不工作区带宽设定值,差值ER将通过这个参数滤波.它关系到PID控制的性湖北大学学报(自然科学版)第28卷能.GAIN参数地址为DB31.DBD108,参数类型为REAL型.默认值为1.增益控制值,增益过大会提高系统的趋近速度,但同时会增大系统波动,导致系统不稳定.增益过小则会使系统的趋近速度变慢.TI参数地址为DB31.DBD112,参数类型REAL型.默认值为3000,单位s.积分时间常数.TI=0时,无积分环节.TD参数地址为DB31.DBD116,参数类型REAL型.默认值为0,单位s.微分时间常数.TD=0时,无微分环节.TM_LAG参数地址为DB31.DBD120,参数类型REAL型.默认值为5,单位s.微分时间延迟设置.LOAD_PAR参数地址为DB31.DBX44.3,参数类型为BOOL型.PID控制的启动开关,每次启动PID或改变PID参数后必须将此位置1,系统每次检查到此位为1,则将所有参数下载到FM355模块,然后将此位复位[4].4PID参数的调整方法PID参数的设置一方面是要根据控制对象的具体情况而定;另一方面是经验.Kp可控制幅值震荡,Kp大则会出现幅值震荡的幅度大,但震荡频率小,系统达到稳定时间长;Ki是解决动作响应的速度快慢的,Ki大了响应速度慢,反之则快;Kd是消除静态误差的,一般Kd设置都比较小,而且对系统影响比较小[5].5试验结论本系统在葛店的新武大有机硅厂通过测试.测试中流体采用甲醇,测试范围为50~250 L/h.以设定值为200 L/h的系统阶跃响应曲线为例,系统延迟时间td=3.5 s,上升时间tΓ=5 s,峰值时间tp=7 s,调节时间ts=28.5 s,超调量公式为:δ%=h(tp)-h(∞)h(∞)×100%,在试验中h(tp)=290,h(∞)=200,所以δ%=45%.经过调试后,本系统被证明完全能胜任有机硅生产过程中,对甲醇流量的精确控制. 参考文献:[1]周军,海心.电气控制及PLC[M].北京:机械工业出版社,2001:90 135.[2]余雷声,方宗达.电器控制与PLC应用[M].北京:机械工业出版社,1999:126 152.[3]陶永华,尹怕欣,葛芦生.新型PID控制及其应用[M].北京:机械工业出版社,1998.[4] Kember G, Dubay R. PID gain scheduling using fuzzy logic[J]. JSA Transactions, 2000,39(3):317 325.[5] Liu G P, Daley S. Optimal-tuning nonlinear PID controllers for unstable processes based on gain and phase marginspecifications: a fuzzy neural approach[J]. Fuzzy Sets and Systems, 2002: 128(1):95 106.The PID control system of flow measuring based on PLCXIAO Lei, XIE Ju-fang(School of Phisics and Electronic Technology, Hubei University, Wuhan 430062, China) Abstract:Described a kind of PID control system based on PIC. The system is composed of supervisor PC, PLC control block, the touch screen ,the flow measuring probe and the electrically operated valve. The system reads the flow measuring from the probe and then calculate the output value by using PID algorithm. The value output to the electrically operated valve to control the flow.The system also can be used in hard condition with high quality.Key words:flow measuring control system; PID; PLC; FM355C(责任编辑晏建章)。
基于PLC的流量监控系统设计说明
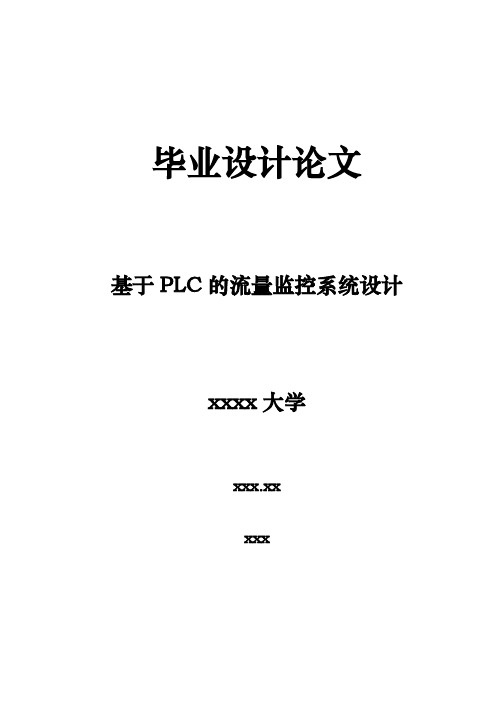
毕业设计论文基于PLC的流量监控系统设计xxxx大学xxx.xxxxx目录1 选题背景2方案论证3 开发设计过程4 结果分析5 总结参考文献致谢附录A:MAIN主程序:附录B:CPU技术规范附录C :EM 235模拟量输入,输出和组合模块的技术规范基于PLC的流量监控系统设计1 选题背景本毕业设计课题来自实验室建设。
目的是利用PLC来实现过程控制。
目前,PLC使用范围可覆盖从替代继电器的简单控制到更复杂的自动化控制。
应用领域极为广泛,覆盖所有与自动检测,自动化控制有关的工业及民用领域,包括各种机床、机械、电力设施、民用设施、环境保护设备等等。
PLC通过模拟量I/O模块,实现模拟量与数字量之间的A/D、D/A转换,并对模拟量进行闭环PID控制。
用MCGS组态软件组态配置工业控制监控系统,对数据进行实时监控。
2方案论证本毕业设计原理是利用扩展模块EM235(AI4/AQ1*12位)进行数据采集,然后把采集到的数据利用程序进行工程量转换,给定量与输入量相减得出偏换,送到执行器,从而构成的是单闭环控制。
采用增量式PID,具有以下优点:(1)增量算法控制误动作影响小。
(2)增量算法控制易于实现手动/自动无扰动切换。
(3)不产生积分失控,易获得较好的调节品质。
在实际应用中,在以步进电机或多圈电位器作执行器件的系统中,则采用增量式PID算法。
MCGS即"监视与控制通用系统",英文全称为Monitor and Control Generated System。
MCGS是为工业过程控制和实时监测领域服务的通用计算机系统软件,具有功能完善、操作简便、可视性好、可维护性强的突出特点。
MCGS 工控组态软件是一套32位工控组态软件,集流程控制、数据采集、设备控制与输出数据与曲线等诸多强大功能于一身,广泛应用于石油、电力、化工、钢铁、矿山、冶金、机械等多种工程领域。
所以用MCGS作为本次毕业设计的开发软件是很有必要的。
流量的PLC控制系统设计
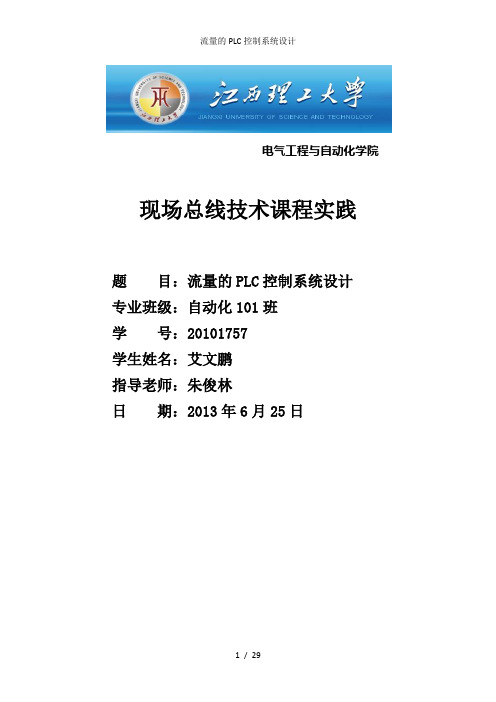
电气工程与自动化学院现场总线技术课程实践题目:流量的PLC控制系统设计专业班级:自动化101班学号:20101757学生姓名:艾文鹏指导老师:朱俊林日期:2013年6月25日流量控制是过程控制系统的一个关键。
采用工业控制计算机, 根据专家系统确定最优工况的各试验流量, 通过AD采集模块接收流量计传感器的数据, 对采集的相应数据进行处理分析并向PLC发出指令, PLC采用PI控制方法, 通过PI控制的参数设定及自整定。
根据PI调节的输出与输入的偏差成正比, 还与偏差对时间的积分成正比, 消除了控制过程中产生的静差, 实现了流量闭环调节的精确控制。
设计了监控软件、PLC软件、PLC与工控计算机的通信软件, 实现了流量的控制、数据采集和处理。
试验表明, PI控制方法对流量的调节具有较好的稳定性和动态特性。
讨论计算机水流量PLC 监控系统。
选用电磁流量计和经典文丘里管流量计系统。
结合杰控组态软件制作出人机界面,把组态与PLC 进行连接,组态与PLC 间不断进行交换数据,通过组态画面实时反映现场流量的实时变化情况,然后定义与组态王实时数据库中变量相对应的监控系统中的设备,通过PLC 采集设备的数据,并通过通信接口把数据传输给计算机。
关键词:流量计;PLC ;人机界面;控制系统; 流量调节; PI控制摘要 (2)第一章引言 (4)1.1 设计目的 (4)1.2 设计主要过程 (4)1.3 设计主要内容 (5)1.3.1 硬件模块设计 (5)1.3.2 组态软件的应用设计 (5)1.3.3 基于STEP-7的程序设计 (5)1.3.4 综合设计 (6)第二章系统的硬件选型 (7)2.1 硬件选型 (7)2.2 选型的步骤 (8)2.3 选型的结果 (8)2.4 选型技术参数 (9)第三章系统的硬件结构设计 (11)3.1 整体结构设计 (11)3.2 硬件连接图 (11)3.3 系统I/O分配表 (12)3.4 硬件组态和变频器参数 (13)3.4.1 硬件组态配置 (13)3.4.2 变频器参数设定 (14)第四章系统软件设计 (15)4.1 软件设计整体构架 (15)4.1.1 杰控组态软件设计 (15)4.1.2 组态设计 (16)4.1.3 PLC程序设计流程图 (22)4.1.4 程序设计梯形图 (22)4.2 问题及其解决方法 (25)4.3 调试过程及方法 (25)4.4 软件调试结果 (26)第五章设计总结 (28)参考文献 (29)第一章引言1.1 设计目的本次课程设计的目的是采用西门子S7-300系列PLC来实现过程控制系统的设计。
PLC在流量控制系统中的应用案例

PLC在流量控制系统中的应用案例流量控制系统是自动化控制中的一个重要应用领域,可以应用于水处理、工业生产、环保等诸多领域。
PLC(可编程逻辑控制器)因其在工业自动化中的功能,特别是对数字和模拟输入/输出操作的能力,成为了流量控制系统中最重要的控制器之一。
本文将探讨PLC在流量控制系统中的应用案例。
一、PLC控制阀门的开闭PLC通过控制流量阀门的开闭,实现流量控制系统中流量的准确控制。
PLC控制阀门的开闭,需要对阀门位置进行反馈控制,即需要在PLC中安装反馈传感器,以检测阀门的位置。
在阀门的开关过程中,PLC可以根据预先设定的开启/关闭时间、阀门的旋转角度等参数实现对阀门的准确控制,从而实现流量控制。
二、PLC实现PID控制PID控制是一种用于工业自动控制中的一种自适应控制方法,其基本原理是按比例调节、积分时间和微调时间来调节控制器的输出,实现对被控制物(例如流量阀门或流量传感器)的精确控制。
传统的PID控制需要使用独立的PID控制器,为了实现在线程序修改,需要对现场的设备进行频繁的调整。
而PLC可以集成PID算法并在线实时调整参数,使控制系统更加智能化,大大简化了控制系统的维护。
三、PLC控制流量传感器流量传感器是流量控制系统中最重要的感应装置之一,可以实现对流量的实时监测。
PLC可以通过传感器检测实时流量信号并将其反馈给PLC,PLC再根据预设的控制程序进行反馈,从而实现精确控制。
同时,PLC还可以使用数据采集卡将流量传感器的信号转换为数字信号,以便于对数据进行存储、处理和分析。
四、PLC实现流量的计算PLC可以通过编写测量算法,将传感器的数字信号转换为流量值,并将其储存在控制器内存中。
此外,PLC还可以将流量数据转输到上位机等设备中,以便于进行数据存储、处理和报告分析。
PLC在流量控制系统中的应用模式基本类似,但实际应用却因环境和行业不同,而存在着各自的应用要求。
在任何情况下,PLC的优势在于其灵活可塑性,可根据不同环境的要求进行定制。
基于PLC的流量与压力控制系统的研究运用

基于PLC的流量与压力控制系统的研究运用摘要随着科技的不断发展,PLC控制系统已经成为工业控制领域中最为常见和重要的控制方式之一。
本文主要介绍了基于PLC的流量与压力控制系统的研究运用。
首先对PLC技术进行了简要介绍,随后对流量与压力控制系统的原理与结构进行了详细分析,最后通过实验验证了基于PLC的流量与压力控制系统的可行性和实用性。
关键词:PLC;流量控制;压力控制;控制系统一、引言PLC是可编程逻辑控制器的缩写,它是一种专门用于工业控制领域的电子设备。
在工业生产中,PLC可以完成逻辑控制和运行控制等任务,通过其高度的灵活性和可编程性,能够满足不同工业场景的需求。
流量与压力是工业生产中重要的物理参数,对于保证生产过程的稳定性和质量具有至关重要的作用。
基于PLC的流量与压力控制系统的研究和运用具有很大的现实意义。
二、PLC技术的特点PLC是一种硬件可编程控制器,它的工作原理是通过控制不同的逻辑元件,如继电器、计数器、定时器等,来实现对工业生产过程的控制。
PLC具有以下几个特点:1. 可编程性强:PLC可以通过编程灵活地修改和调整控制逻辑,适应不同的生产需求;2. 稳定可靠:PLC的硬件结构稳定,能够在恶劣的工作环境下正常运行;3. 易于维护:PLC的模块化设计和可编程特性,使得故障检测和维护更加方便。
基于以上特点,PLC在工业控制领域得到了广泛的应用,成为了工业自动化的重要组成部分。
三、流量与压力控制系统的原理与结构流量与压力是工业生产中常见的控制对象,控制系统的主要目标是实现对流体的流量和压力进行精确的控制。
流量与压力控制系统的结构包括传感器、执行元件、控制器和执行装置等组成。
1. 传感器:传感器用于对流体的流量和压力进行检测和监控,将采集到的信息反馈给控制器;2. 控制器:控制器接收传感器反馈的信息,并根据预设的控制逻辑计算出控制命令,向执行装置发出控制信号;3. 执行装置:执行装置根据控制命令对流量阀门和压力阀门进行控制,调整流体的流量和压力。
基于PLC的流量比值控制系统设计
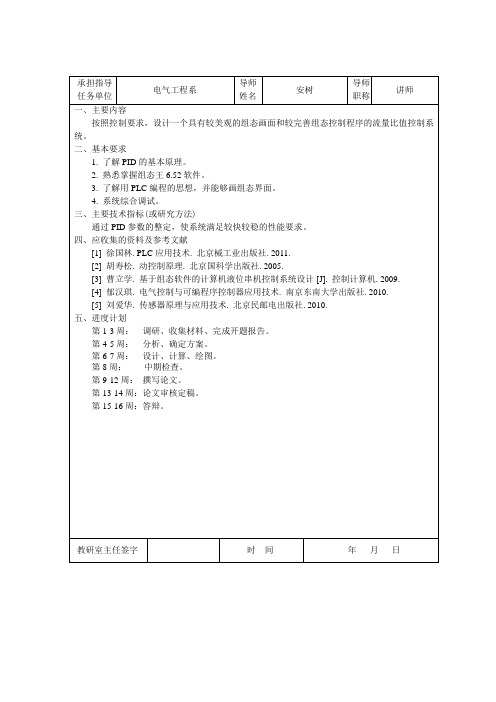
毕业设计开题报告摘要流量比值控制系统的设计,主要是用PLC控制液体的比例,以便提高工业的智能化,通过流量比值控制可以使得工业上液体的混合准确,能够更好地控制液体的比例,节约资源。
本设计采用PLC为核心对液体流量进行控制,通过合理的设计,提高流量控制水平,进而改善流量运行的稳定性,使其更加精确。
本文主要介绍了流量的比值控制系统总体方案设计、设计过程、组成、列出流量控制的流程图,并给出了系统组成框图,分析流量逻辑关系,提出了编程方法。
通过A/D采集模块接收流量计传感器的数据,对采集的相应数据进行处理分析并发出指令,该设计采用PID控制方法,通过PID控制的参数设定及自整定。
根据PI调节的输出与输入的偏差成正比,还与偏差对时间的积分成正比,消除了控制过程中产生的静差。
本设计实现了流量双闭环调节的精确控制,这种控制方法对流量的调节具有较好的稳定性和动态特性。
关键词:流量PLC比值PIDAbstractThe design of flow ratio control system, PLC is mainly used to control the ratio of liquid, in order to improve the intelligence industry, through flow ratio control can make industrial liquid mixing accurate, better able to control liquid ratio, save resources.This design uses PLC as the core of the liquid flow control, through reasonable design, improve the flow of control level, thereby improving the flow stability of ru nning, making them more precise. This paper mainly introduces the flow ratio contro l system scheme design, design process, composition, list the flow chart flow control, an d gives the block diagram of the system, analyzes the flow of logic relation, put fort the programming method. Receiving flow meter sensor through the A/D acquisition m odule data, the corresponding data processing analysis and instruction, the design adopt PID control method, setting and tuning the parameters of PID control. According to the deviation of output and input is proportional to the PI regulation, also with the deviati on on time is proportional to the integral, and eliminates the static error generated in the control process.This design realizes the accurate control of flow of double closed loop regulation, this control method has better stability and dynamic characteristics of flow regulation.Key words:Flow PLC Ratio PID目录第1章绪论 (1)1.1课题研究的目的意义 (1)1.2国内外研究现状 (1)1.3论文研究内容 (2)第2章系统控制方案设计 (3)2.1系统整体方案的设计 (3)2.1.1方案论证 (3)2.1.2方案选择 (4)2.1.3双闭环比值控制系统的结构 (4)2.2双闭环比值控制系统的特点与分析 (5)2.3控制方案的比较和确定 (6)2.4流量比值控制系统的组成及原理图 (6)2.5流量比值系统控制流程 (8)第3章系统的硬件设计 (9)3.1PLC的基本知识 (9)3.1.1PLC硬件介绍 (9)3.1.2编程语言 (10)3.2设备的选型 (10)3.2.1PLC及其转换模块的选型 (11)3.2.2变频器的选型 (13)3.2.3水泵电机的选型 (15)3.2.4电磁流量计的选型 (16)3.2.5调节阀的选型 (17)3.3系统主电路分析及其设计 (18)第4章系统的软件设计 (20)4.1流量比值控制逻辑图 (20)4.2系统I/O分配 (20)4.3系统I/O接线图 (21)4.4系统控制过程 (21)4.4.1程序初始化与故障分析 (21)4.4.2PID初始化及程序分析 (23)第5章仿真设计 (25)5.1组态王介绍 (25)5.2组态画面 (25)Ⅰ5.3监控画面 (25)第6章结论 (28)参考文献 (29)致谢 (30)附录 (31)附录A外文资料 (31)附录B电路总图 (42)附录C流程图 (43)附录D程序 (44)Ⅱ石家庄铁道大学四方学院毕业设计第1章绪论1.1 课题研究的目的意义在生产过程、科学研究和其他产业领域中,可编程序自动控制技术的应用都是十分广泛的,在自动控制的设备中,可编程序自动控制亦比其它的控制方法使用得更普遍。
流量比值控制系统的设计
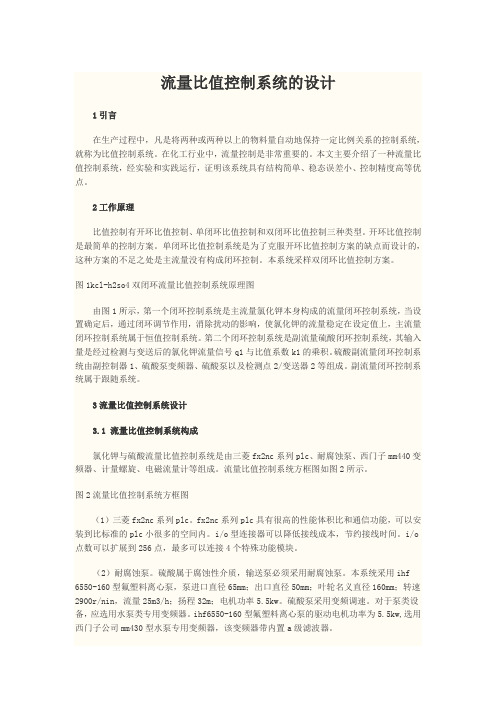
流量比值控制系统的设计1引言在生产过程中,凡是将两种或两种以上的物料量自动地保持一定比例关系的控制系统,就称为比值控制系统。
在化工行业中,流量控制是非常重要的。
本文主要介绍了一种流量比值控制系统,经实验和实践运行,证明该系统具有结构简单、稳态误差小、控制精度高等优点。
2工作原理比值控制有开环比值控制、单闭环比值控制和双闭环比值控制三种类型。
开环比值控制是最简单的控制方案。
单闭环比值控制系统是为了克服开环比值控制方案的缺点而设计的,这种方案的不足之处是主流量没有构成闭环控制。
本系统采样双闭环比值控制方案。
图1kcl-h2so4双闭环流量比值控制系统原理图由图1所示,第一个闭环控制系统是主流量氯化钾本身构成的流量闭环控制系统,当设置确定后,通过闭环调节作用,消除扰动的影响,使氯化钾的流量稳定在设定值上,主流量闭环控制系统属于恒值控制系统。
第二个闭环控制系统是副流量硫酸闭环控制系统,其输入量是经过检测与变送后的氯化钾流量信号q1与比值系数k1的乘积。
硫酸副流量闭环控制系统由副控制器1、硫酸泵变频器、硫酸泵以及检测点2/变送器2等组成。
副流量闭环控制系统属于跟随系统。
3流量比值控制系统设计3.1 流量比值控制系统构成氯化钾与硫酸流量比值控制系统是由三菱fx2nc系列plc、耐腐蚀泵、西门子mm440变频器、计量螺旋、电磁流量计等组成。
流量比值控制系统方框图如图2所示。
图2流量比值控制系统方框图(1)三菱fx2nc系列plc。
fx2nc系列plc具有很高的性能体积比和通信功能,可以安装到比标准的plc小很多的空间内。
i/o型连接器可以降低接线成本,节约接线时间。
i/o 点数可以扩展到256点,最多可以连接4个特殊功能模块。
(2)耐腐蚀泵。
硫酸属于腐蚀性介质,输送泵必须采用耐腐蚀泵。
本系统采用ihf 6550-160型氟塑料离心泵,泵进口直径65mm;出口直径50mm;叶轮名义直径160mm;转速2900r/nin,流量25m3/h;扬程32m;电机功率5.5kw。
- 1、下载文档前请自行甄别文档内容的完整性,平台不提供额外的编辑、内容补充、找答案等附加服务。
- 2、"仅部分预览"的文档,不可在线预览部分如存在完整性等问题,可反馈申请退款(可完整预览的文档不适用该条件!)。
- 3、如文档侵犯您的权益,请联系客服反馈,我们会尽快为您处理(人工客服工作时间:9:00-18:30)。
电气工程与自动化学院现场总线技术课程实践题目:流量的PLC控制系统设计专业班级:自动化101班学号:20101757学生姓名:艾文鹏指导老师:朱俊林日期:2013年6月25日摘要流量控制是过程控制系统的一个关键.采用工业控制计算机,根据专家系统确定最优工况的各试验流量, 通过AD采集模块接收流量计传感器的数据,对采集的相应数据进行处理分析并向PLC发出指令, PLC采用PI控制方法,通过PI控制的参数设定及自整定.根据PI调节的输出与输入的偏差成正比,还与偏差对时间的积分成正比,消除了控制过程中产生的静差,实现了流量闭环调节的精确控制.设计了监控软件、PLC软件、PLC与工控计算机的通信软件, 实现了流量的控制、数据采集和处理。
试验表明, PI控制方法对流量的调节具有较好的稳定性和动态特性.讨论计算机水流量PLC 监控系统。
选用电磁流量计和经典文丘里管流量计系统。
结合杰控组态软件制作出人机界面,把组态与PLC 进行连接,组态与PLC 间不断进行交换数据,通过组态画面实时反映现场流量的实时变化情况,然后定义与组态王实时数据库中变量相对应的监控系统中的设备,通过PLC 采集设备的数据,并通过通信接口把数据传输给计算机。
关键词:流量计;PLC ;人机界面;控制系统; 流量调节; PI控制目录摘要 (2)第一章引言 (4)1.1 设计目的 (4)1.2 设计主要过程 (4)1.3 设计主要内容 (5)1.3.1 硬件模块设计 (5)1.3.2 组态软件的应用设计 (5)1.3.3 基于STEP-7的程序设计 (5)1.3.4 综合设计 (6)第二章系统的硬件选型 (7)2.1 硬件选型 (7)2.2 选型的步骤 (8)2.3 选型的结果 (8)2.4 选型技术参数 (9)第三章系统的硬件结构设计 (11)3.1 整体结构设计 (11)3.2 硬件连接图 (11)3.3 系统I/O分配表 (12)3.4 硬件组态和变频器参数 (13)3.4.1 硬件组态配置 (13)3.4.2 变频器参数设定 (14)第四章系统软件设计 (16)4.1 软件设计整体构架 (16)4.1.1 杰控组态软件设计 (16)4.1.2 组态设计 (17)4.1.3 PLC程序设计流程图 (23)4.1.4 程序设计梯形图 (24)4.2 问题及其解决方法 (26)4.3 调试过程及方法 (26)4.4 软件调试结果 (27)第五章设计总结 (29)参考文献 (30)第一章引言1。
1 设计目的本次课程设计的目的是采用西门子S7—300系列PLC来实现过程控制系统的设计.学习使用变频器,并对其内控与外控模式运用自如;掌握PLC控制单元的使用,对西门子S7—300编程进而对整个过程进行控制;学会使用A\D、D\A转换模块,了解其工作机制,熟知模数、数模换换的接口地址通过模拟量I/O模块,并对其进行编程采集与控制;与此同时,学会使用不同的传感器件流量计、电磁阀等的控制欲使用。
熟悉杰控组态软件的使用方法,根据所给资料自己独立绘出一个上位机,设置相应的变量,使整个上位机与我们的硬件设备连接起来,并对模拟量进行闭环PID控制,达到PLC编程-上位机控制-实现整个流量的PLC过程控制系统的要求。
通过杰控组态软件进行相应的实时监控,其显示的内容包括启动、停止按钮、PID参数给定窗口、给定流量、实际流量、相应的实时曲线显示窗口等功能,从而形成一个完整的过程控制系统。
当今,PLC的使用范围越来越广,从替代继电器的简单控制到更复杂的自动化控制.应用于所有与自动检测,自动化控制有关的工业及民用领域,包括各种机床、机械、电力设施、民用设施、环境保护设备等等。
可知,现在的工业生产和各领域的机械控制都是与此密切相关的,对其学习研究具有重大意义。
1。
2 设计主要过程考虑到这次是对过程控制系统的初次整体设计,本设计分为四个步骤进行,分别为:第一步,过程控制柜模块选取,所选取的流量传感器、电磁阀等硬件的连接和变频器的控制方式设置;第二步,基于杰控组态软件的上位机设计,我们需要根据资料学习的东西包括项目管理、设备通信、运行数据库、画面制作、画面显示、变量报警等,通过这些木块的学习进而组合形成一个我们需要的界面控制台;第三步,基于STEP-7的S7—300PLC程序的设计,使用FB41背景数据块和FC105、FC106模块实现整个环节的A/D、D/A、PID闭环控制系统的设计;第四步,所有部分的综合控制设计,将前期设计的所有模块进行所有的整合一体设计调试,最终实现我们的设计要求。
1。
3 设计主要内容1。
3。
1 硬件模块设计我们需要的物理设备有主要有,一个储水箱、一个装水箱、流量计一个、电动阀一个、变频器一个,水泵一个和若干开关水管等材料构成。
1。
3。
2 组态软件的应用设计组态软件系统是集多年 PLC 工程应用、开发和服务经验,基于 Windows NT 、Windows 2000/XP 操作平台,独立研制开发的纯 32 位、高档次的软件,其运行稳定、速度快、简单易用、功能强大、扩展性好,能为用户提供经济完善的工业自动化监控解决方案。
本次组态软件需要使用的功能有,首先,学会如何使用项目管理包括备份和调入等;完成设备通讯的设计,主要包括S7TCP驱动安装、启动驱动、定义设备数据表、监视设备数据表,设备数据表的定义至关重要,它是直接和我们的程序控制连接起来的纽带;紧接着就是画面制作了,按照设计的需求绘制一个相对美观的界面,然后添加一些静态文本、按键、文本框、曲线图、柱状图等,从而构成一个完整的控制界面;选择相应的画面,启动画面显示。
1。
3。
3 基于STEP—7的程序设计本次程序设计主要采用梯形图的方式,设计的过程首先使用模数转换模块FC105对流量计的数值进行实时采集,SCALE功能接受一个整型值(IN),并将其转换为以工程单位表示的介于下限和上限(LO_LIM和HI_LIM)之间的实型值。
将结果写入OUT。
FC105转换得到的数值再作为FB41模块进行PID调节,然后将调节得出的结果送给数模转换模块FC106进行转换,SCALE功能接受一个整型值(IN),并将其转换为以工程单位表示的介于下限和上限(LO_LIM和HI_LIM)之间的实型值。
将结果写入OUT。
输出的结果再送给变频器,从而实现变频器的外控模式调节,从而实现流量的控制.1。
3.4 综合设计完成了上述各个模块之后,再进行综合设计,整个过程控制系统就是由硬件外围电路和设备加软件控制部分控制的.我们通过PLC编程,再与组态软件进行链接,实现一个控制界面,继而控制物理设备的完整控制系统.第二章系统的硬件选型2.1 硬件选型本设计硬件主要包括,过程控制系统设备一套(包括三个流动水箱、一个储水水箱、若干水管、开关若干、抽水泵一个等)、流量计一个、电动阀一个、变频器一套等。
考虑到流量的精度和准确度,本设计采用上海艾特自动化仪表有限公司的MLF-1流量计,基本参数有:流量精度为0。
5级,输出信号为4—20毫安,量程范围为0.3立方米,口径10毫米等变频器采用西门子全新一代标准变频器MicroMaster420,它是全新一代模块化设计的多功能标准变频器。
它友好的用户界面,让你的安装、操作和控制象玩游戏一样灵活方便。
全新的IGBT技术、强大的通讯能力、精确的控制性能、和高可靠性都让控制变成一种乐趣.水泵电动机采用浙江松久电机有限公司的A02-7112系列三项异步电动机,功率为370W,额定电压380伏,额定电流1。
0A,额定频率50HZ,转速2780r/min,绝缘等级B,噪声65dB硬件组态采用可编程控制器CPU 314C—2 PN/DP,CPU 314C—2 DP 是紧凑型CPU,适合安装在分布式结构中。
通过其扩展工作存储器,该紧凑型CPU也适用于中等规模的应用。
集成的数字量和模拟量输入和输出可与过程信号直接连接。
集成的的PROFIBUS DP 主站/从站以及 PROFINET IO 控制器/I-设备接口,用于 PROFIBUS 和 PROFINET 的分布式连接。
这使得 CPU 314C—2 PN/DP 可作为进行快速处理的分布式单元使用,也可作为 PROFIBUS 和 PROFINET 系统中具有低端现场总线系统的上位控制器。
采用西门子电源模块PS307/5A,6ES7307—1EA01-0AA0西门子PS307/5A/10A 电源模块单元为S7-300/ET 200M提供电源,将120/230伏交流电压转变到所需要的24伏直流工作电压输出电流2安、5安或10安。
S7—300需要24伏直流电源。
PS 307负载电源模块将120 或230伏交流电压转变为24伏直流工作电压。
24伏直流电源用来为SIMATIC S7-300和传感器及执行元件供电模拟量输入采用SM331,命令地址为6ES7 331—7KF02—OABO,标称型号是AI8*12Bit,光电隔离,U/I/热电偶/电阻中断,诊断;分辨率9、12、14位,八位模拟量输入。
模拟量输出采用SM332,命令地址为6ES7 332-5HD01-OABO,标称型号是AO4*12Bit,光电隔离,U/I诊断;分辨率11、12位,四位模拟量输出。
数字量模块 SM 323 数字量输入/ 输出模块,8 输入,8输出。
24VDC;8出,24VDC,0.5A,晶体管输出,光电隔离,扩展温度范围PS 307 5AAI8*12Bit 6ES7 331-7KF02-OABOAO4*12Bit 6ES7 332-5HD01—OABODI8/DO8*DC24V/0,5A 6ES7 323-1BH01—0AA02.2 选型的步骤硬件的选型是从本设计的核心去实现的,硬件方面要符合标准输入电压、电流、频率等。
因此选型的步骤可以分为如下几步来进行:1、了解设计所提供的硬件资源,根据所有的设备进行实践选型;2、确定流量最大时流量计的最大值,以确定所选AD采集设备符合要求;3、确定电源模块是否符合设备的规格;4、确定变频器所能设置的最大频率值;5、确定DA采集到的数据值是否符合设备要求;2.3 选型的结果最终确定采用的硬件设备主要有,上海艾特自动化仪表有限公司的MLF—1流量计,变频器采用西门子全新一代标准变频器MicroMaster420,水泵电动机采用浙江松久电机有限公司的A02—7112系列三项异步电动机,硬件组态采用可编程控制器CPU 314C-2 PN/DP。
2。
4 选型技术参数一、MLF —1流量计基本参数有:流量精度为0.5级,输出信号为4-20毫安,量程范围为0.3立方米,口径10毫米等.二、变频器MicroMaster420200V —240V ±10%,单相/三相,交流,0.12kW-5。