通过试验确定最佳切削参数
数控机床加工塑料材料的最佳切削参数选择方法

数控机床加工塑料材料的最佳切削参数选择方法数控机床是现代制造业中常用的一种机械设备,它通过计算机控制来实现工件的加工。
在数控机床加工中,选择合适的切削参数对于保证加工质量、提高生产效率至关重要。
本文将介绍数控机床加工塑料材料的最佳切削参数选择方法,帮助读者更好地进行相关工作。
首先,要选择合适的切削速度。
切削速度直接影响加工效率和表面质量。
一般来说,对于塑料材料,切削速度应尽可能高。
较高的切削速度可以有效减少刀具与工件的摩擦热,防止塑料材料的熔化和变形。
但是,切削速度过高也会使刀具表面过热,导致热疲劳和脱碳等问题。
因此,在选择切削速度时,应根据具体塑料材料的性质,结合试验和经验确定最佳速度范围。
其次,要选择适当的进给速度。
进给速度对加工表面质量和切削力有较大影响。
过低的进给速度会使刀具与工件接触时间过长,容易引起切削力过大,导致刀具损伤或工件变形。
而过高的进给速度则会导致加工表面粗糙度增加,甚至出现划痕等质量问题。
因此,在选择进给速度时,应综合考虑切削力和加工精度,确定最佳速度范围。
此外,还需选择适宜的切削深度。
切削深度是指每次切削中刀具相对于工件的进给量。
切削深度过大会使切削力增大,容易导致刀具磨损和工件变形;切削深度过小则会增加加工时间和工序数,降低加工效率。
因此,在选择切削深度时,应综合考虑切削力和加工效率,确定最佳深度范围。
最后,要选择合适的刀具类型和刀具材料。
塑料材料具有软化、热熔和热膨胀等特点,对刀具材料的选择提出了一定的要求。
一般来说,使用高速钻石刀具或者立铣刀可以获得较好的加工效果。
高速钻石刀具具有较高的硬度和耐磨性,能够有效减小切削力和摩擦热,保证加工表面质量;立铣刀具有多刃设计,可以通过分散切削力,减少塑料材料的热变形。
此外,还要根据具体情况选择合适的刀具涂层,提高刀具的抗磨性和切削性能。
综上所述,数控机床加工塑料材料的最佳切削参数选择方法包括选择合适的切削速度、进给速度、切削深度以及刀具类型和材料。
切断刀切削参数
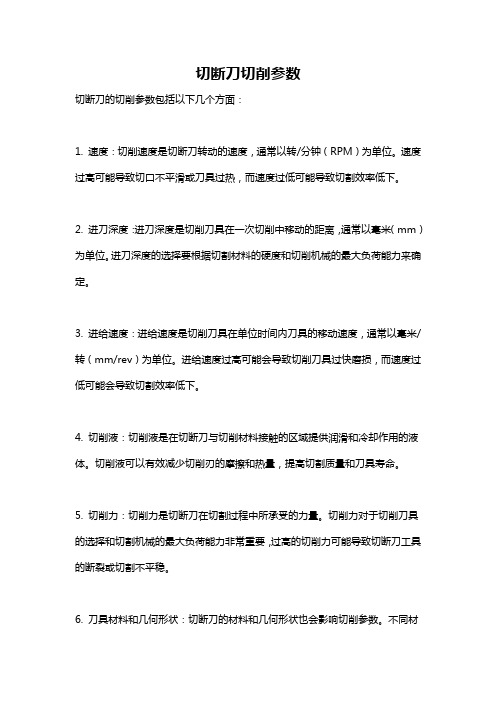
切断刀切削参数
切断刀的切削参数包括以下几个方面:
1. 速度:切削速度是切断刀转动的速度,通常以转/分钟(RPM)为单位。
速度过高可能导致切口不平滑或刀具过热,而速度过低可能导致切割效率低下。
2. 进刀深度:进刀深度是切削刀具在一次切削中移动的距离,通常以毫米(mm)为单位。
进刀深度的选择要根据切割材料的硬度和切削机械的最大负荷能力来确定。
3. 进给速度:进给速度是切削刀具在单位时间内刀具的移动速度,通常以毫米/转(mm/rev)为单位。
进给速度过高可能会导致切削刀具过快磨损,而速度过低可能会导致切割效率低下。
4. 切削液:切削液是在切断刀与切削材料接触的区域提供润滑和冷却作用的液体。
切削液可以有效减少切削刃的摩擦和热量,提高切割质量和刀具寿命。
5. 切削力:切削力是切断刀在切割过程中所承受的力量。
切削力对于切削刀具的选择和切割机械的最大负荷能力非常重要,过高的切削力可能导致切断刀工具的断裂或切割不平稳。
6. 刀具材料和几何形状:切断刀的材料和几何形状也会影响切削参数。
不同材
料和几何形状的切断刀具适用于不同类型的切割任务,选择合适的切断刀具可以提高切割效率和切割质量。
这些切削参数的选择需要根据切割材料的特性、切削机械的性能和切割要求来确定,可以通过试验和经验来确定最佳的切削参数。
切削速度对照表

切削速度对照表
切削速度对照表是数控加工中必不可少的参考工具。
切削速度直接影响到切削效率和加工质量,因此制定一份科学合理的切削速度对照表非常必要。
以下是本文的主要内容:
一、什么是切削速度对照表
切削速度对照表是指在不同材质、不同加工方式下,切削刀具所适用的切削速度范围。
它是在加工过程中确保安全、高效、精准加工的重要参考工具。
二、切削速度对照表的制定原则
1、根据不同材料与不同加工方式,设置不同的切削速度。
2、基于刀具的材质和刀具的类型,制定适当的切削参数。
3、根据加工和切削机床的性能,确定一定的加工速度和进给速度。
三、实际应用
1、选取适当的切削速度
在加工材料时,应首先了解该材料的硬度和其他物理性质等特征,以选择合适的切削速度。
一般而言,材料硬度越高,切削速度越低。
2、合理调整进给速度
在保证切削速度稳定的情况下,应根据加工尺寸的要求,调整相应的
进给速度。
进给速度应合理,过快容易导致加工表面粗糙,过慢则会
拖长加工时间。
3、切削参数实测
实际加工过程中,需要对切削速度对照表中的参数进行实测,确定最
终的切削参数。
此时需要根据加工对象,不断试验和探索,以逐步找
到最佳的切削参数组合。
总之,制定一份合理科学的切削速度对照表,需要同时考虑刀具材质、加工对象、工作条件以及加工精度等多方面因素。
希望本文可以对需
要设计或使用切削速度对照表的人员提供一些帮助。
通过试验确定最佳切削参数

通过试验确定最佳切削参数在同样满足零件加工品质的前提下,数控机床提高加工效率关键在于如何使金属切除率达到最大。
本文主要讨论了在铝合金材料的加工中,针对特定的数控机床、刀具和装夹系统如何来确定金属切除率最大的切削参数的问题。
一、引言提高数控机床使用效率是目前大家普遍关心的问题,具有关资料介绍,国外数控机床在两班制工作下开动率达到60%~70%,国内往往只能达到20%~30%。
造成数控机床使用率低的原因归纳起来就是管理和技术两方面的问题,刀具和切削参数选择是数控加工的主要技术问题之一。
例如1800010mm高速钢刀具加工铝合金,刀具允许的最高切削速度为300mm/min,机床转速为8750r/min,而相同规格的合金刀,刀具允许的最高切削速度可达600mm/min甚至更高,机床转速可以达到17510r/min,显而易见,这种机床采用高速刚刀具是不合适的。
如果机床设备、加工刀具和加工对象已经明确后,研究如何正确选择切削参数对提高加工效率、降低加工成本具有实际意义。
什么是正确的切削参数,笔者认为应该是针对特定的机床、特定的刀具和刀夹、特定的加工材料在满足零件加工品质的前提下,使材料的切除率达到最大的一组切削参数。
这组参数如何确定,有人提出了通过计算机优化设计选择最佳铣削参数的方法,目前也已经有文献报道可以利用现代切削过程仿真和优化技术,在少量试验的基础上借助合理的数学模型、工程分析和仿真等先进手段,快速获取理想的切削参数数据。
而对我们来说,刀具的种类是有限的,几把常用的刀具基本上能完成90%的加工量,在这种情况下,通过切削试验方法来获取这些刀具的正确切削参数是比较现实的手段。
二、试验目的和方法1.试验目的在特定机床、刀夹、刀具和刀具长度组合条件下,选定合适的每齿切削量和轴向切深,通过采用一系列不同切削速度及径向切深,观察加工过程的情况,从声音和加工表面的质量来判断,发生加工振颤的情况,从而找出相同的零件加工品质下(平稳的切削,未发生振颤),材料的切除率达到最大的铣削参数。
铣螺纹检查不合格原因

铣螺纹检查不合格原因一、引言螺纹加工作为机械零件加工中常见的一种加工方式,广泛应用于各行各业。
螺纹对于机械零件的连接和传递力量起到至关重要的作用。
然而,在铣螺纹加工过程中,有时会遇到螺纹检查不合格的情况,这给零件的质量和性能带来了一定的风险。
本文将探讨铣螺纹检查不合格的原因,并提供相应的解决方案。
二、铣螺纹检查不合格的原因1.切割刀具选择不当一种常见的螺纹检查不合格原因是切削刀具的选择不当。
切削刀具的选择应根据螺纹类型和工件材料来确定,如果选择不当,可能导致铣刀后退、螺纹不清晰等问题。
2.切削参数设置错误切削参数的设置对于螺纹加工的质量至关重要。
如果切削速度过高、进给速度过慢或切削深度不当,都可能导致螺纹加工质量下降,甚至出现刀具破损等问题。
3.加工工艺不合理在进行螺纹加工时,如果加工工艺不合理,也会导致最终的螺纹检查不合格。
例如,切削刃数选择不当、刀具重心偏移、工件固定不稳等因素都可能对螺纹加工质量产生负面影响。
4.机床精度问题机床的精度和稳定性对于螺纹加工至关重要。
如果机床的精度不足或存在震动等问题,都会影响螺纹的加工质量。
5.操作不规范操作人员在进行螺纹加工时如不熟悉操作规程或对螺纹加工没有足够的经验,也容易导致螺纹检查不合格。
操作不规范包括进给速度不稳定、刀具角度调整不当等问题。
三、改善措施针对铣螺纹检查不合格的原因,以下是一些改善措施的建议:1.合理选择切削刀具根据不同的螺纹类型和工件材料,选择合适的切削刀具。
切削刀具的选择应考虑刀具材料、刀具形状和切削角度等因素。
2.正确设置切削参数合理设置切削速度、进给速度和切削深度等切削参数。
通过试验和经验总结,找到最佳的切削参数组合,以提高螺纹加工的质量。
3.优化加工工艺在加工螺纹时,优化加工工艺,确保刀具重心合理、切削刃数适宜并保证工件的稳定夹持。
合理的加工工艺可以提高螺纹的加工质量。
4.提高机床精度及时维护和调整机床,保持机床的精度和稳定性。
数控机床加工不同硬度材料的最佳切削参数选择方法
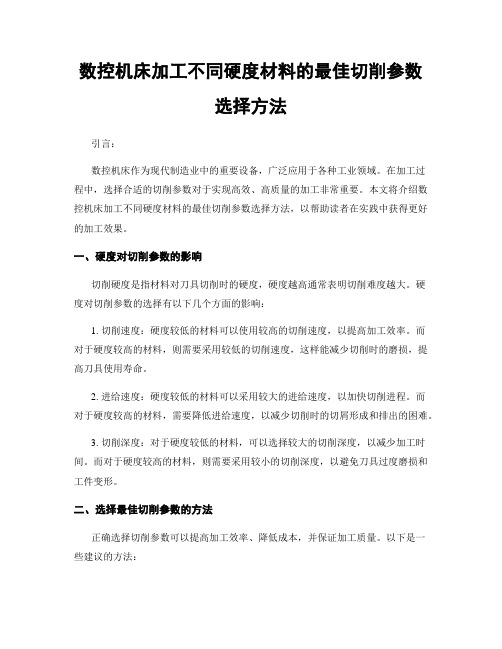
数控机床加工不同硬度材料的最佳切削参数选择方法引言:数控机床作为现代制造业中的重要设备,广泛应用于各种工业领域。
在加工过程中,选择合适的切削参数对于实现高效、高质量的加工非常重要。
本文将介绍数控机床加工不同硬度材料的最佳切削参数选择方法,以帮助读者在实践中获得更好的加工效果。
一、硬度对切削参数的影响切削硬度是指材料对刀具切削时的硬度,硬度越高通常表明切削难度越大。
硬度对切削参数的选择有以下几个方面的影响:1. 切削速度:硬度较低的材料可以使用较高的切削速度,以提高加工效率。
而对于硬度较高的材料,则需要采用较低的切削速度,这样能减少切削时的磨损,提高刀具使用寿命。
2. 进给速度:硬度较低的材料可以采用较大的进给速度,以加快切削进程。
而对于硬度较高的材料,需要降低进给速度,以减少切削时的切屑形成和排出的困难。
3. 切削深度:对于硬度较低的材料,可以选择较大的切削深度,以减少加工时间。
而对于硬度较高的材料,则需要采用较小的切削深度,以避免刀具过度磨损和工件变形。
二、选择最佳切削参数的方法正确选择切削参数可以提高加工效率、降低成本,并保证加工质量。
以下是一些建议的方法:1. 参考切削参数手册:数控机床切削参数手册是宝贵的参考资料,其中列出了不同硬度材料的推荐切削参数。
可以根据工件材料的硬度,查找手册并参考建议的切削参数进行调整。
2. 经验法则:经验法则可以作为初步选择切削参数的参考。
例如,对于硬度较低的材料,可以尝试切削速度为材料硬度的2倍,进给速度为材料硬度的0.5倍,切削深度为3mm。
然后根据实际情况进行微调。
3. 切削试验:切削试验是一种有效的方法,可以根据试验结果来选择最佳切削参数。
在实际加工之前,可以准备一块与工件材料相似的试验材料,进行切削试验,并记录加工时间、表面粗糙度、切削力等参数。
根据实验结果调整切削参数,以得到最佳加工效果。
4. 刀具选择:选择合适的刀具也是选择最佳切削参数的重要因素。
切削参数优化
切削参数优化
切削参数优化是指在保证加工质量和生产效率的前提下,通过对加工材料、刀具、加工工艺等因素进行优化,使切削工具的切削刃口处于最佳状态,以达到最佳加工效果的过程。
切削参数包括切削速度、进给速度、切削深度和切削宽度。
优化切削参数可以使刀具使用寿命更长,加工质量更稳定,并且可以提高加工效率和降低生产成本。
以下是进行切削参数优化的几个步骤:
1.确定切削性能指标:加工品质、切削力、切削温度、切削力矩、切屑卷成程度等。
2.实验研究:通过试验确定最佳切削速度、进给速度、切削深度和切削宽度。
3.分析应力和变形状态:对加工材料的应力和变形状态进行分析,确定合适的切削速度、进给速度等参数。
4.选择合适的刀具:选择适合材料和加工工艺的刀具,使其在切削过程中表现出最佳性能。
5.实践验证:在实际生产中验证切削参数的优化效果,并对其进行调整和改进。
在进行切削参数优化时,需要考虑到加工材料的硬度、韧性、热处理状态以及加工的精度要求等因素。
同时,选择合适的刀具材料和涂层技术也是优化切削参数的关键。
圆柱齿轮加工工艺中的加工效率提升与优化
圆柱齿轮加工工艺中的加工效率提升与优化在圆柱齿轮加工工艺中,提高加工效率和优化工艺对于提高生产效率和降低成本非常重要。
本文将介绍几种提升加工效率和优化齿轮加工工艺的方法。
1. 刀具选择与磨损监测在圆柱齿轮加工中,正确选择合适的刀具非常重要。
刀具的选择应根据工件的材料和要求进行匹配。
对于加工难度较高的材料,应选用高速钢或硬质合金刀具,以确保切削性能和刀具寿命。
此外,还需要定期对刀具进行磨损监测,及时更换磨损严重的刀具,以保证加工质量和效率。
2. 优化切削参数合理设置切削参数可以提高圆柱齿轮加工的效率。
切削速度、进给速度和切削深度是影响切削效率的重要参数。
通过对不同材料和工件的试切试验,可以确定最佳切削参数组合,以提高切削效率。
3. 引入先进的加工设备与技术引入先进的加工设备和技术也是提高加工效率的一种重要方式。
例如,采用数控机床可以实现高精度的自动化加工,极大提高了加工效率和加工质量。
另外,还可以考虑引入融合加工、高速切削和干润滑等先进技术,以进一步提高加工效率和优化工艺。
4. 工艺优化与工序优化在加工过程中,进行工艺和工序的优化也能带来较大的效益。
例如,通过改进工件的设计和结构,减少加工量和加工工序,可以降低生产成本,并提高加工效率。
此外,合理设置各个工序的先后顺序和加工顺序,可以避免重复操作和不必要的等待时间,从而提高整体加工效率。
5. 进行加工工艺优化的数据分析随着互联网和大数据技术的发展,利用数据分析来优化加工工艺的效果越来越好。
通过采集和分析加工过程中的实时数据,可以获取各项工艺参数的详细信息,并通过数据分析来发现潜在的问题和改进空间。
基于数据分析的加工工艺优化方法能够更加精确地确定最佳加工参数,从而提高加工效率和优化工艺。
总结起来,圆柱齿轮加工工艺中的加工效率提升与优化需通过刀具选择与磨损监测、优化切削参数、引入先进的加工设备与技术、工艺优化与工序优化以及进行加工工艺优化的数据分析等多方面的方法来实现。
多轴加工工艺优化方案
多轴加工工艺优化方案多轴加工工艺优化方案多轴加工是一种高效、高精度的加工工艺,可以同时进行多个轴向的加工操作。
通过合理的工艺优化方案,可以提高加工效率、降低成本,并保证加工质量。
下面将从步骤思考的角度,介绍多轴加工工艺优化的方案。
第一步:了解加工需求在进行多轴加工工艺优化之前,首先需要了解加工需求。
这包括加工零件的尺寸要求、加工材料的性质、加工量和加工周期等。
通过全面了解加工需求,可以为后续的工艺设计提供参考。
第二步:分析加工工艺在了解加工需求的基础上,需要对加工工艺进行分析。
这包括确定加工过程中所需的加工步骤、加工工具和加工顺序等。
同时,还需要考虑工艺中可能存在的问题,如切削力过大、切削温度过高等。
通过仔细分析,可以找出工艺中的瓶颈和改进点。
第三步:选择合适的多轴加工设备多轴加工需要专用的设备来实现同时进行多个轴向的加工操作。
在选择设备时,需要考虑设备的精度、稳定性和可靠性等因素。
同时,还需要根据加工需求确定设备的加工能力和适用范围。
选择合适的设备是多轴加工工艺优化的基础。
第四步:设计合理的刀具路径多轴加工的刀具路径设计是关键的一步。
刀具路径的设计应充分考虑切削力分布和切削温度分布的均匀性,以及避免碰撞和干涉等问题。
合理的刀具路径设计可以提高加工效率,减少刀具磨损,并保证加工质量。
第五步:优化切削参数切削参数的选择对多轴加工工艺的效果影响很大。
合理的切削参数可以降低切削力和切削温度,减少刀具磨损,延长刀具寿命,同时还可以提高加工效率和加工质量。
通过试验和仿真分析,可以确定合适的切削参数。
第六步:优化冷却润滑系统冷却润滑系统是多轴加工中的重要组成部分。
通过合理优化冷却润滑系统,可以降低切削温度,减少刀具磨损,并提高切削液的利用率。
常见的优化措施包括优化切削液的喷射方式和喷射位置,以及控制切削液的流量和温度等。
第七步:加工过程监控与优化在多轴加工过程中,应实时监控加工状态,及时发现并解决问题。
通过合理的加工数据采集和分析,可以优化加工过程,减少加工误差,提高加工精度。
机械加工质量控制
机械加工质量控制一、引言机械加工是制造业中非常重要的一个环节,它涉及到产品的精度、表面质量和功能性能等方面。
为了确保机械加工的质量,需要建立一套有效的质量控制体系,以提高产品的质量稳定性和生产效率。
本文将详细介绍机械加工质量控制的标准格式文本。
二、质量控制目标1. 提高产品的加工精度:通过控制加工工艺参数和加工设备的精度,确保产品的尺寸和形状符合设计要求。
2. 保证产品的表面质量:控制加工过程中的切削速度、进给速度和切削液的使用,以获得良好的表面光洁度和光滑度。
3. 提升产品的功能性能:通过控制加工工艺和材料的选择,确保产品的功能性能满足客户的需求。
三、质量控制步骤1. 设计加工工艺:根据产品的要求和加工工艺的特点,确定合适的加工工艺路线,并编制详细的工艺文件。
2. 选择合适的加工设备:根据产品的加工要求和工艺文件,选择适当的加工设备,包括数控机床、切削工具和夹具等。
3. 进行加工试验:在正式加工之前,进行加工试验,确定合适的切削参数和加工工艺,并记录相关数据。
4. 进行首件加工:在正式批量加工之前,进行首件加工,验证加工工艺和设备的可行性,并进行质量检验。
5. 进行中间检验:在批量加工过程中,进行定期的中间检验,确保产品的质量稳定性。
6. 进行最终检验:在产品加工完成后,进行最终检验,确保产品的质量符合要求。
7. 处理不良品:对于不合格的产品,及时进行处理,找出问题的原因,并采取措施进行改进。
四、质量控制方法1. 测量与检测:使用合适的测量工具和设备,对产品的尺寸、形状和表面质量进行测量和检测,确保其符合设计要求。
2. 切削参数控制:控制切削速度、进给速度和切削液的使用,以获得良好的加工效果和表面质量。
3. 加工设备维护:定期对加工设备进行维护保养,确保其精度和稳定性。
4. 材料选择:选择合适的材料,以确保产品的功能性能满足客户的需求。
5. 过程监控:通过实时监控加工过程中的参数和数据,及时发现问题并采取措施进行调整。
- 1、下载文档前请自行甄别文档内容的完整性,平台不提供额外的编辑、内容补充、找答案等附加服务。
- 2、"仅部分预览"的文档,不可在线预览部分如存在完整性等问题,可反馈申请退款(可完整预览的文档不适用该条件!)。
- 3、如文档侵犯您的权益,请联系客服反馈,我们会尽快为您处理(人工客服工作时间:9:00-18:30)。
在同样满足零件加工品质的前提下,数控机床提高加工效率关键在于如何使金属切除率达到最大。
本文主要讨论了在铝合金材料的加工中,针对特定的数控机床、刀具和装夹系统如何来确定金属切除率最大的切削参数的问题。
一、引言
提高数控机床使用效率是目前大家普遍关心的问题,具有关资料介绍,国外数控机床在两班制工作下开动率达到60%~70%,国内往往只能达到20%~30%。
造成数控机床10mm高速钢刀具加工铝合金,刀具允许的最高切削速度为300mm/min,机床转速为8750r/min,而相同规格的合金刀,刀具允许的最高切削速度可达600mm/min甚至更高,机床转速可以达到17510r/min,显而易见,这种机床采用高速刚刀具是不合适的。
如果机床设备、加工刀具和加工对象已经明确后,研究如何正确选择切削参数对提高加工效率、降低加工成本具有实际意义。
Φ使用率低的原因归纳起来就是管理和技术两方面的问题,刀具和切削参数选择是数控加工的主要技术问题之一。
例如18000转的机床,用
什么是正确的切削参数,笔者认为应该是针对特定的机床、特定的刀具和刀夹、特定的加工材料在满足零件加工品质的前提下,使材料的切除率达到最大的一组切削参数。
这组参数如何确定,有人提出了通过计算机优化设计选择最佳铣削参数的方法,目前也已经有文献报道可以利用现代切削过程仿真和优化技术,在少量试验的基础上借助合理的数学模型、工程分析和仿真等先进手段,快速获取理想的切削参数数据。
而对我们来说,刀具的种类是有限的,几把常用的刀具基本上能完成90%的加工量,在这种情况下,通过切削试验方法来获取这些刀具的正确切削参数是比较现实的手段。
二、试验目的和方法
1.试验目的
在特定机床、刀夹、刀具和刀具长度组合条件下,选定合适的每齿切削量和轴向切深,通过采用一系列不同切削速度及径向切深,观察加工过程的情况,从声音和加工表面的质量来判断,发生加工振颤的情况,从而找出相同的零件加工品质下(平稳的切削,未发生振颤),材料的切除率达到最大的铣削参数。
2.试验条件
数控机床:MIKRON UCP710五轴加工中心,主轴最大转速18000r/min,功率15kW,最大进给速度
20m/min;
刀具:FETTE LW225硬质合金立铣刀螺旋角,刀具供应商推荐的提供的极限参数:加工低硅含量铝合金时,最大切削速度Vc800mm/min,最大进给Fz为0.115mm/齿,最大轴向切深ap15mm,相应径向切深5mm,该刀具是我们最常用的刀具之一;︒10mm,长度66mm,2齿,30Φ,直径
夹具:HSK刀柄,Φ42mm;
加工材料:LF5铝合金,该材料是我们最常用的加工材料;
冷却液:Blasocut2000乳化液
3.试验方法
准备外形尺寸80mm×100mm×150mm的工件,把工件装入虎钳,长80mm边高出虎钳40mm,刀具装入HSK刀夹后,露出长度35mm,在工件上加工成高8mm宽1mm的8级台阶,见图1。
图1
确定试验的主轴转速范围:按照最大切削速度计算,刀具可以承受的最高转速为25478r/min,根据机床的性能和平时的经验,我们选择主轴转速在7000~14000r/min这个范围进行试验,对应的切削速度为220~440mm/min。
确定切削深度和每齿进给量:在整个试验中,保持轴向切深和每齿切削量不变,我们选择ap8mm和Fz0.1mm/齿,此时径向切深最大可为ae8mm。
每齿进给量不变,就意味着当主轴转速改变时,刀具的进给率将改变,这样做主要考虑到两个因素,一是每一个工步刀具可以具备相同的刀屑载荷,二是每齿进给量对表面粗糙度的影响最大,每一个工步每齿进给量保持不变后,就具备了可比性。
编写试验程序:在不同的高度上,进行一系列平行铣削工步。
从一个工步到下一个工步提高主轴转速,共分8个工步,以1000r/min的增量,从7000r/min到14000r/min。
径向切深从3mm增加到8mm,一个循环后每次增加1mm。
评估切削:倾听,然后观察。
从不同工步的声音可以感觉出在哪里发生颤振。
然后,在切削完成后,检查工件表面质量。
工件要求搭靠山,铣完一台阶过后拿出工件观察,确定加工表面是显示平稳切削、轻微颤振还是严重颤振。
记录完后,把工件放回原来装夹位置继续下一次加工。
三、试验结果和分析
试验结果如表1所示,绿色表示平稳切削,黄色表示有轻微颤动,红色表示有剧烈颤动。
可以看到,当径向切深为3mm时,所有的工步显示稳定切削,当径向切深为4mm时,某些工步开始出现轻微振颤,当径向切深增加到足够高时,一些工步便出现严重振颤。
加工中出现这种现象是普遍存在的,主要是因为每个主轴、刀夹和刀具系统都有几组频率,当刀具切削工件产生的撞击震动的频率和这些系统固有频率接近时,就会产生振颤现象,造成表面波纹,影响表面粗糙度。
振颤不是机床的缺陷,它是物理缺陷,是不可避免的。
振颤会引起表面波纹是毫无疑问的,因为整个试验采用的每齿进给量是一定的,如果不发生振颤,所有工步的表面粗糙度应该是基本一致的。
这也是试验中为什么要保持每齿进给量一定的主要原因。
从试验结果还可以看到,当主轴转速在14000r/min时,平稳切削时的材料切除率是67200mm3/min,而当主轴转速在11000r/min时,平稳切削时的材料切除率是140800mm3/min,也就是说,尽管好像采用了较高的主轴转速,但是,此时的加工效率却并不是最高,换而言之,这种切削参数组合并不是最佳的。
试验中,我们得到两个平稳切削主轴转速7000r/min和11000r/min,它们的材料切除率分别为89600mm3/min 和140800mm3/min,后者要更佳。
机床、刀具、刀夹组成的系统固有频率,事先往往无从知晓,如果只根据刀具寿命参数和机床参数来选择切削参数是得不到这样的结果的。
四、结论
本试验在一种机床、刀柄、刀具、刀具长度、工件材料、每齿切削量和轴向进给量的组合下,找到了平稳切削的最佳转速,它的转速并没有达到最高。
所以说要想提高金属切除率,一味地提高转速是不现实的,只有找到一组比较合理的参数组合才是最实际的。
需要注意的是,在上述组合中任何一项条件改变,结果将改变,读者可根据自己的实际情况,去寻找合理的切削参数(具有较高的金属切除率条件下),这将对提高加工质量,缩短加工时间有着重大的意义。