机械加工切削参数汇总
切削参数表(刨刀)
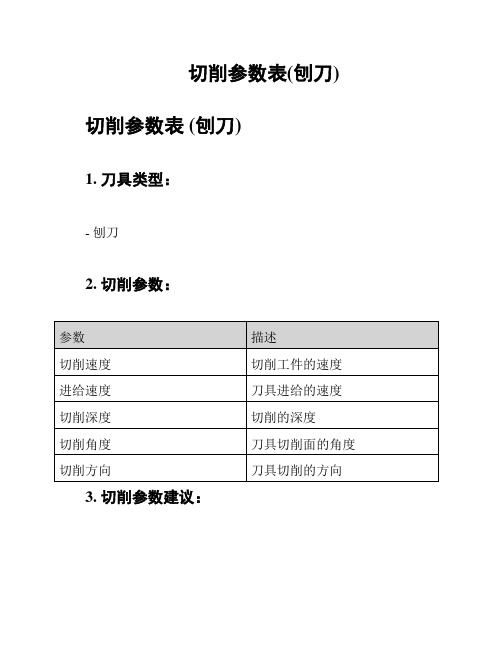
切削参数表(刨刀)切削参数表 (刨刀)
1. 刀具类型:
- 刨刀
2. 切削参数:
3. 切削参数建议:
- 切削速度:根据材料的硬度和切削表面的要求来确定合适的
切削速度。
一般来说,硬度越高的材料切削速度越低,切削表面要
求越高则切削速度越低。
- 进给速度:根据刀具的结构和工件的材料来确定合适的进给
速度。
一般来说,刀具结构越牢固,工件材料越硬则进给速度越低。
- 切削深度:根据工件材料和切削表面的要求来确定合适的切
削深度。
一般来说,材料越硬,切削表面要求越高则切削深度应适
当减小。
- 切削角度:根据刀具和工件的特点来选择合适的切削角度。
一般来说,角度较小的切削面可以减小切削力和切削温度。
- 切削方向:根据工件的形状和切削表面的要求来确定合适的
切削方向。
一般来说,切削方向应尽量与工件表面平行,以获得更
好的切削效果。
4. 注意事项:
- 在切削过程中,应保持刀具和工件的稳定性,避免刀具晃动
或工件移动,以免影响切削效果和安全性。
- 在切削前,应检查刀具的状况,确保刀具刃口的锋利度和完
整性。
- 在切削过程中,及时清除切屑和切削液,保持切削区域的清洁,并定期对刀具进行润滑和维护。
以上是切削参数表 (刨刀)的相关内容,希望对您有帮助。
机械加工 刀具切削参数表
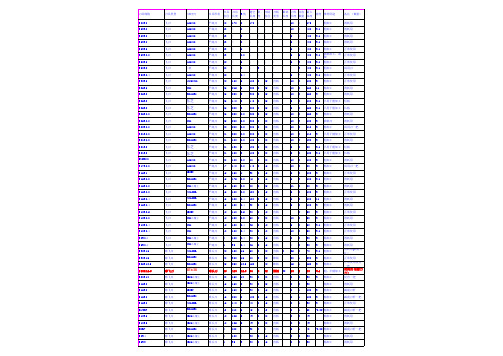
刀具类型 飞刀 飞刀 飞刀 飞刀 飞刀 飞刀 飞刀 飞刀 飞刀 飞刀 飞刀 飞刀 飞刀 飞刀 飞刀 飞刀 飞刀 飞刀 飞刀 飞刀 飞刀 飞刀 飞刀 飞刀 飞刀 飞刀 飞刀 飞刀 飞刀 飞刀 飞刀 飞刀 飞刀 飞刀 飞刀 球飞刀 球飞刀 球飞刀 球飞刀 球飞刀 球飞刀 球飞刀 球飞刀 球飞刀 球飞刀 球飞刀 球飞刀 球飞刀 球飞刀 球飞刀
刀具 长度 170 \ \ \ \ \ \ \ \ 180 215 220 140 200 220 200 200 200 180 130 180 180 140 160 175 160 180 180 120 110 120 120 100 100 95 120 300 250 120 160 160 160 200 140 110 105 105 100 100 95
R角 8 8 8 8 6 0.8 6 2 0.4 6 6 2 2 2 0.8 0.8 0.8 0.8 0.8 2 2 0.8 0.8 1 0.8 0.8 0.8 0.4 0.4 2.5 0.8 0.4 0.4 0.4 0.4 16 15 12.5 12.5 10 8 8 8 8 6 6 5 4 4 3
精度 推荐用途 粗加工 -0.1 -0.1 -0.1 -0.1 -0.1 -0.1 -0.1 -0.1 -0 0.1 -0 -0.1 -0.1 -0 -0 -0 -0 -0 -0.1 -0.1 -0 -0 -0 -0.1 -0 -0 0.1 -0 -0 -0 -0.1 -0.1 -0 -0 -0.1 -0 -0 -0.1 -0 粗加工 粗加工 精加工 粗加工 插铣加工,清 根 粗加工 粗加工 精加工 粗加工 精加工 粗加工 只用于粗加工 只用于粗加工 精加工 插铣刀 精加工 只用于精加工 粗加工 只用于粗加工 只用于粗加工 粗加工 精加工 精加工 粗加工 精加工 粗加工 粗加工 粗加工 粗加工 精加工 粗加工 粗加工 精加工 精加工 粗加工 精加工 精加工 粗,半精加工 精加工 精加工 -0 -0 -0 -0 精加工 精加工 精加工 精加工 精加工 精加工 -0 精加工 精加工 精加工
切削参数表(切割刀片)
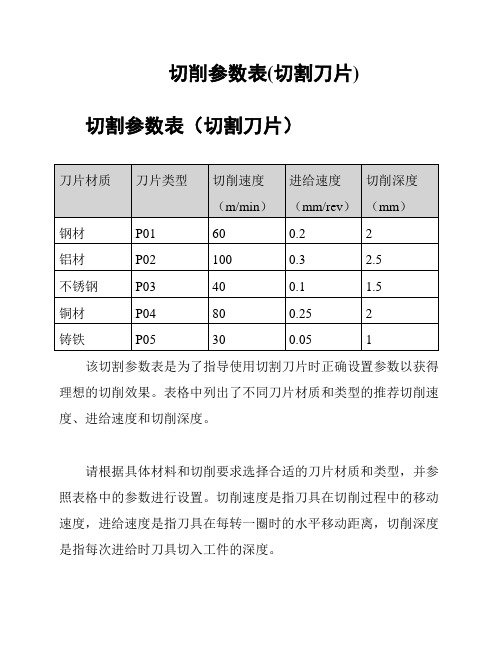
切削参数表(切割刀片)
切割参数表(切割刀片)
该切割参数表是为了指导使用切割刀片时正确设置参数以获得理想的切削效果。
表格中列出了不同刀片材质和类型的推荐切削速度、进给速度和切削深度。
请根据具体材料和切削要求选择合适的刀片材质和类型,并参照表格中的参数进行设置。
切削速度是指刀具在切削过程中的移动速度,进给速度是指刀具在每转一圈时的水平移动距离,切削深度是指每次进给时刀具切入工件的深度。
注意,根据具体切削情况需灵活调整参数。
遵循切削理论以及
经验来进行试切并观察切削效果,根据实际情况适当调整切削参数,以达到最佳切削效果和工件加工要求。
请妥善保管该参数表,并随时查阅以及更新切削参数。
如有任
何问题或需要进一步的帮助,请随时联系我们的技术支持团队。
切削参数和计算公式参考
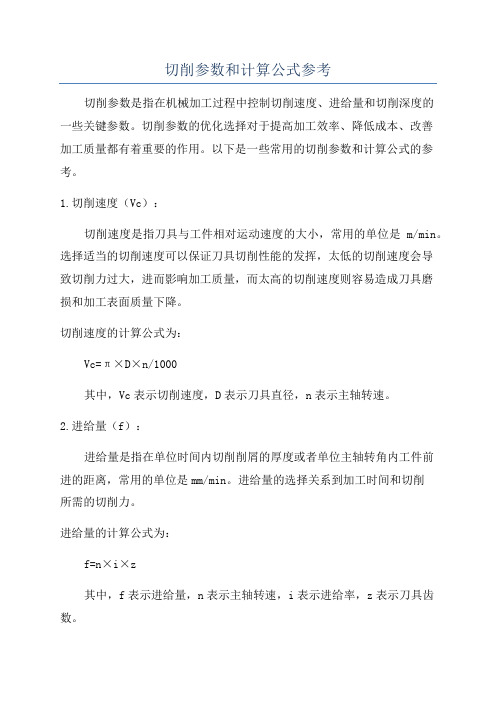
切削参数和计算公式参考切削参数是指在机械加工过程中控制切削速度、进给量和切削深度的一些关键参数。
切削参数的优化选择对于提高加工效率、降低成本、改善加工质量都有着重要的作用。
以下是一些常用的切削参数和计算公式的参考。
1.切削速度(Vc):切削速度是指刀具与工件相对运动速度的大小,常用的单位是m/min。
选择适当的切削速度可以保证刀具切削性能的发挥,太低的切削速度会导致切削力过大,进而影响加工质量,而太高的切削速度则容易造成刀具磨损和加工表面质量下降。
切削速度的计算公式为:Vc=π×D×n/1000其中,Vc表示切削速度,D表示刀具直径,n表示主轴转速。
2.进给量(f):进给量是指在单位时间内切削削屑的厚度或者单位主轴转角内工件前进的距离,常用的单位是mm/min。
进给量的选择关系到加工时间和切削所需的切削力。
进给量的计算公式为:f=n×i×z其中,f表示进给量,n表示主轴转速,i表示进给率,z表示刀具齿数。
3. 切削深度(ap):切削深度是指切削层厚度的大小,即刀具和工件之间的垂直距离。
切削深度的选择应根据工件材料和刀具性能来进行合理的安排。
4.切削力(Fc,Fr):切削力是指刀具对工件施加的力,也是切削参数的重要指标之一、切削力的大小与切削材料的性质、切削速度、进给量和切削深度等因素有关。
切削力的计算公式为:Fc = k × ap × f其中,Fc表示切削力,k表示切削力系数。
5.切削功率(P):切削功率是指切削过程中单位时间内切削所需要的能量,常用单位为W。
切削功率的计算可以帮助选取合适的切削参数,保证切削过程的稳定性和高效性。
切削功率的计算公式为:P=Fc×Vc/6000其中,P表示切削功率,Fc表示切削力,Vc表示切削速度。
综上所述,切削参数的选择是一项复杂的任务,需要结合实际加工情况、刀具性能和工件要求等多方面因素进行综合考虑。
切削参数表(车刀)
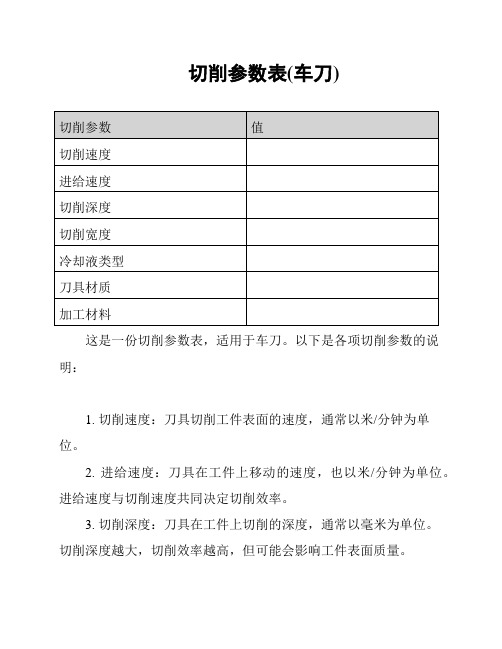
切削参数表(车刀)
这是一份切削参数表,适用于车刀。
以下是各项切削参数的说明:
1. 切削速度:刀具切削工件表面的速度,通常以米/分钟为单位。
2. 进给速度:刀具在工件上移动的速度,也以米/分钟为单位。
进给速度与切削速度共同决定切削效率。
3. 切削深度:刀具在工件上切削的深度,通常以毫米为单位。
切削深度越大,切削效率越高,但可能会影响工件表面质量。
4. 切削宽度:刀具在工件上切削的宽度,同样以毫米为单位。
切削宽度也是影响切削效果和工件表面质量的重要参数。
5. 冷却液类型:在加工过程中使用的冷却液的类型,根据加工材料和切削条件选择适合的冷却液。
6. 刀具材质:车刀的刀具材质,根据加工材料和切削条件选择合适的刀具材料。
7. 加工材料:要加工的工件材料,根据工件材料选择适当的切削参数。
以上是切削参数表的内容,根据具体的加工需求和条件,调整这些参数可以获得更好的切削效果。
记得根据实际情况进行测试和调整参数,以确保安全和高效的切削操作。
机械加工切削全参数推荐表
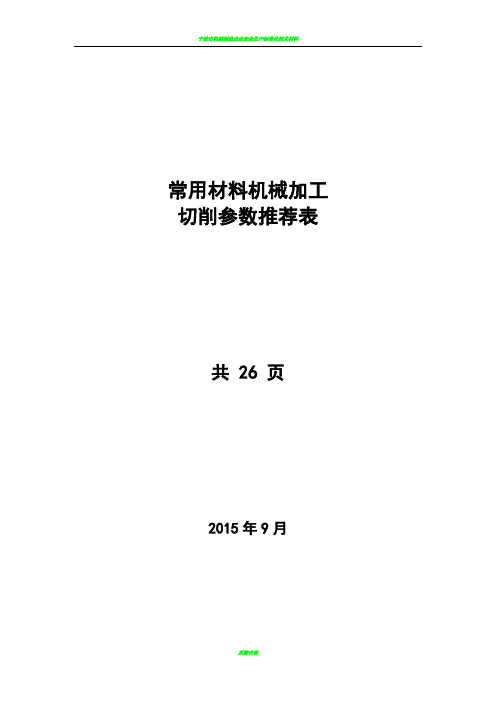
常用材料机械加工切削参数推荐表共 26 页2015年9月目录1 切削用量选定原则 (3)2 车削加工切削参数推荐表 (3)2.1 车削要素 (3)2.2 车削参数 (4)3 铣削加工切削参数推荐表 (11)3.1 铣削要素 (11)3.2 铣削参数 (12)4 磨削加工切削参数推荐表 (22)4.1 磨削要素 (22)4.2 平面磨削 (22)4.3 外圆磨削 (23)4.4 内圆磨削 (24)1 切削用量选定原则选择机械加工切削用量就是指具体确定切削工序的切削深度、进给量、切削速度及刀具耐用度。
选择切削用量时,要综合考虑生产率、加工质量和加工成本。
从切削加工生产率考虑:切削深度、进给量、切削速度中任何一个参数增加一倍,都可提高生产率一倍。
从刀具耐用度考虑:应首先采用最大的切削深度,再选用大的进给量,然后根据确定的刀具耐用度选择切削速度。
从加工质量考虑:精加工时,采用较小的切削深度和进给量,采用较高的切削速度。
2 车削加工切削参数推荐表2.1 车削要素切削速度v :工件旋转的线速度,单位为m/min 。
进给量f :工件每旋转一周,工件与刀具相对位移量,单位为mm/r 。
切削深度a p :垂直于进给运动方向测量的切削层横截面尺寸,单位为mm 。
Ra :以轮廓算术平均偏差评定的表面粗糙度参数,单位为μm 。
d w :工件直径,单位为mm 。
外圆车削示意图内圆车削示意图切削速度与转速关系:3.3181000nd dnv ==π m/mind vd vn3.3181000==πr/minv:切削速度,工件旋转的线速度,单位为m/min。
n:工件的转速,单位为r/min。
d:工件观察点直径,单位为mm。
2.2 车削参数45钢热轧状态(硬度:187HB)外圆车削45钢热轧状态(硬度:187HB)内圆车削45钢调质状态(硬度:28~32HRC)外圆车削45钢调质状态(硬度:28~32HRC)内圆车削40Cr钢热轧状态(硬度:212HB)外圆车削40Cr钢热轧状态(硬度:212HB)内圆车削40Cr钢调质状态(硬度:28~32HRC)外圆车削40Cr钢调质状态(硬度:28~32HRC)内圆车削H62硬化状态(硬度:164HB)外圆车削H62硬化状态(硬度:164HB)内圆车削2A12-T4固溶处理并时效状态(硬度:105HB)外圆车削2A12-T4固溶处理并时效状态(硬度:105HB)内圆车削TC4固溶处理并时效状态(硬度:320~380HB)外圆车削TC4固溶处理并时效状态(硬度:320~380HB)内圆车削3 铣削加工切削参数推荐表3.1 铣削要素铣削速度v :铣刀旋转运动的线速度,单位为m/min 。
机械加工的切削参数
机械加工的切削参数机械加工是通过切削工具对工件进行削除材料的加工过程。
切削参数是指在机械加工过程中,用于控制切削过程的一些重要参数。
在机械加工中,选择合适的切削参数可以有效提高加工质量和生产效率。
本文将详细介绍机械加工的切削参数。
1. 加工速度(Cutting Speed)加工速度是指工件表面的任意点在切削过程中所接受到的线速度。
它与切削刀具转速和切削刀具直径有关。
加工速度的选择应根据工件材料、刀具材料和刀具类型来确定。
通常,应选择适当的加工速度,以保证加工表面质量的要求,同时避免刀具磨损过快。
2. 进给速度(Feed Rate)进给速度是指刀具相对于工件的线速度。
它与切削刃数、切削深度和加工速度有关。
进给速度的选择应根据工件材料、刀具材料和切削刃数来确定。
一般来说,进给速度应选取适当的值,以保证加工精度的要求,同时提高生产效率。
3. 切削深度(Cutting Depth)切削深度是指刀具进入工件的深度。
切削深度的选择应根据工件材料、刀具材料和加工要求来确定。
一般来说,切削深度不宜过大,以避免切削力过大引起刀具破损或加工表面质量下降。
4. 切削量(Cutting Amount)切削量是指单位时间内切削掉的工件材料体积。
切削量的选择应根据工件材料、刀具材料和加工要求来确定。
通常,切削量应合理选择,以提高生产效率,同时避免刀具磨损过快或加工表面质量下降。
5. 主轴速度(Spindle Speed)主轴速度是指切削刀具的转速。
主轴速度的选择应根据刀具材料、切削深度和切削量来确定。
合理选择主轴速度可以保证刀具的使用寿命和加工表面质量。
6. 切削角度(Cutting Angle)切削角度是指刀具刃口与切削方向之间的夹角。
切削角度的选择应根据工件材料、刀具材料和加工要求来确定。
合理选择切削角度可以提高切削效率和加工表面质量。
7. 切削液(Cutting Fluid)切削液是指在切削过程中加入的润滑冷却剂。
切削液的选择应根据工件材料、刀具材料和切削条件来确定。
机械加工切削全参数表
机械加工切削全参数表 Document serial number【UU89WT-UU98YT-UU8CB-UUUT-UUT108】常用材料机械加工切削参数推荐表共 26 页2015年9月目录1 切削用量选定原则选择机械加工切削用量就是指具体确定切削工序的切削深度、进给量、切削速度及刀具耐用度。
选择切削用量时,要综合考虑生产率、加工质量和加工成本。
从切削加工生产率考虑:切削深度、进给量、切削速度中任何一个参数增加一倍,都可提高生产率一倍。
从刀具耐用度考虑:应首先采用最大的切削深度,再选用大的进给量,然后根据确定的刀具耐用度选择切削速度。
从加工质量考虑:精加工时,采用较小的切削深度和进给量,采用较高的切削速度。
2 车削加工切削参数推荐表车削要素切削速度v:工件旋转的线速度,单位为m/min。
进给量f:工件每旋转一周,工件与刀具相对位移量,单位为mm/r。
切削深度a:垂直于进给运动方向测量的切削层横截面尺寸,单位为pmm。
Ra :以轮廓算术平均偏差评定的表面粗糙度参数,单位为μm。
d:工件直径,单位为mm。
w外圆车削示意图内圆车削示意图切削速度与转速关系:3.3181000nddnv ==π m/mindvd v n 3.3181000==π r/min v :切削速度,工件旋转的线速度,单位为m/min 。
n :工件的转速,单位为r/min 。
d :工件观察点直径,单位为mm 。
车削参数45钢热轧状态(硬度:187HB )外圆车削45钢热轧状态(硬度:187HB )内圆车削45钢调质状态(硬度:28~32HRC)外圆车削32HRC)内圆车削45钢调质状态(硬度:28~40Cr钢热轧状态(硬度:212HB)外圆车削40Cr钢热轧状态(硬度:212HB)内圆车削40Cr钢调质状态(硬度:28~32HRC)外圆车削28~32HRC)内圆车削40Cr钢调质状态(硬度:H62硬化状态(硬度:164HB)外圆车削H62硬化状态(硬度:164HB)内圆车削2A12-T4固溶处理并时效状态(硬度:105HB)外圆车削2A12-T4固溶处理并时效状态(硬度:105HB)内圆车削TC4固溶处理并时效状态(硬度:320~380HB)外圆车削380HB)内圆车削TC4固溶处理并时效状态(硬度:320~3 铣削加工切削参数推荐表 铣削要素铣削速度v :铣刀旋转运动的线速度,单位为m/min 。
ti,tc4的切削参数
ti,tc4的切削参数Ti和TC4是常见的金属材料,通常用于机械加工。
切削参数是指在加工过程中用于控制切削过程的各种参数,包括切削速度、进给速度、切削深度等。
下面我会从多个角度来回答关于Ti和TC4的切削参数的问题。
首先,让我们讨论一下切削速度。
切削速度是指刀具在加工过程中相对于工件表面的线速度。
对于Ti和TC4这样的金属材料,通常推荐的切削速度范围是多种。
一般来说,对于钛合金TC4,切削速度在50~80m/min之间比较合适;对于钛Ti材料,切削速度在90~120m/min之间比较合适。
当然,这些数值还会受到刀具材料、刀具类型、加工方式等因素的影响。
其次,进给速度也是切削过程中非常重要的参数。
进给速度是指刀具在加工过程中沿着工件表面的运动速度。
一般来说,对于Ti 和TC4材料,推荐的进给速度范围是0.05~0.15mm/r。
当然,具体的进给速度还会受到切削深度、刀具类型等因素的影响。
另外,切削深度也是需要考虑的重要参数。
切削深度是指刀具在加工过程中进入工件的深度。
对于Ti和TC4这样的金属材料,一般来说,推荐的切削深度范围是0.5~3mm。
需要根据具体的加工情况和工件要求来确定切削深度。
除了上述提到的切削参数外,还有一些其他因素也会影响到切削过程,比如刀具的选择、冷却润滑等。
在实际加工中,需要综合考虑这些因素,结合具体的加工要求和机床设备特点来确定最佳的切削参数。
综上所述,Ti和TC4的切削参数涉及到切削速度、进给速度、切削深度等多个方面的因素。
在实际应用中,需要根据具体的加工要求和材料特性来合理选择切削参数,以确保加工质量和效率。
机械加工切削参数汇总
机械加工切削参数汇总机械加工切削参数是指在机械加工过程中,用于控制和调整刀具、工件和切削液等各种切削因素的参数。
它直接影响着切削质量、加工效率和机床寿命等方面。
下面将对机械加工切削参数进行汇总,详细介绍各个参数的含义和影响因素。
1.切削速度:切削速度是指刀具在加工过程中切削物体的相对运动速度。
它的大小决定了刀具与工件之间的相对运动速度,直接影响到加工表面质量、切削力和刀具磨损等。
切削速度的选择应根据材料性质、工件形状和加工要求等因素进行合理调整,以确保加工效果。
2.进给速度:进给速度是指工件和刀具相互之间的相对运动速度。
它的大小决定了每刀削一定长度的工件所需的时间,影响着加工效率和表面质量。
进给速度的选择应根据切削力和刀具寿命等因素进行合理调整,以保证切削质量和加工效率。
3.切削深度:切削深度是指刀具在一次切削过程中进入工件的深度。
它的大小决定了切削的削屑量和切削力的大小,直接影响着切削质量和刀具寿命。
切削深度的选择应根据工件材料和加工要求等因素进行合理调整,以获得最佳的加工效果。
4.切削角度:切削角度是指刀具边刃与工件之间的夹角。
它的大小决定了刀具与工件之间的切削面积和切削力的方向,直接影响切削质量和刀具寿命。
切削角度的选择应根据材料的切削性质、加工质量要求和刀具结构等因素进行合理调整,以获得最佳的加工效果。
5.切削液:切削液是一种应用于切削过程中的液体,用于冷却切削区域、润滑切削面和清洁削屑等。
它的选择和使用能够有效地提高切削质量和刀具寿命,降低切削力和摩擦系数。
切削液的种类和使用方法应根据材料和工艺要求等因素进行合理选择和调整。
6.切削力:切削力是指刀具切削工件时所受到的力。
它的大小决定了切削的削屑量和切削加工的负荷情况,直接影响着加工效果和机床寿命。
切削力的大小主要受切削速度、进给速度、切削深度和切削角度等参数的影响,应合理调整以控制切削负荷和提高加工效果。
综上所述,机械加工切削参数是一系列重要的工艺参数,它们的选择和调整直接关系到加工质量、切削力和刀具寿命等方面。
- 1、下载文档前请自行甄别文档内容的完整性,平台不提供额外的编辑、内容补充、找答案等附加服务。
- 2、"仅部分预览"的文档,不可在线预览部分如存在完整性等问题,可反馈申请退款(可完整预览的文档不适用该条件!)。
- 3、如文档侵犯您的权益,请联系客服反馈,我们会尽快为您处理(人工客服工作时间:9:00-18:30)。
例外的切削速度
工件重量为300公斤时,n
带 <300转/分;公斤300<工
中 件重量<1000公斤时,n<
心 架
200转/分;公斤1000<工 件重量<3000公斤时,n< 100转/分;工件体积较大
切 或偏心量大时,切削时必须
削 再适当降低转速,务必结合
实际情况做好维稳加工。
带
车削细长轴类时,需用尾 顶,切削转速须根据实际情
800
30 560~670 730~909 1000 1100
677~812 1000 1200
410 820 1000
640~840 1000
630
40 530~630 632~790 870 988
514~610 760 1000
356 712 870
480~630 760
585
采用钻 削方式
50 425~510 495~618 680 770
直径
10
20
30
40
50
60
涂
70
层 80
硬 90
质 合
A3 100
金 200
刀
300
具
400
500
600
700
800
900
1000
型材
锻件毛坯车 调质件转速 加工
削转速77 120
转速
150
1200
1300
1300
1000
1200
1200
818
1200
1200
610
1000
1100
470
750
950
1200
1300
960
1200 1200
1100
1200
785
1200 1200
1000
1100
585
1000 1100
910
1000
451
750 950
680
950
384
637 796
580
800
326
537 670
485
700
288
630 45 260
560
、 40
228
280 Cr 114
470 587 420 525 375 468 187 233
800 26~31
30~38
42 47
25~30
37 46
17
34 42
23~31 37
28
即可
900 23.5~28 26~33
37 42
22~26
33 41
15
30 37
21~28 33
26
1000 22~26
24~30
34 38
20~24
30 37
14
28 34
20~26 30
23
刀 具
材 料
300 71~84
83~104
115 130 Mn 67~80 Ti
100 126
400 53~63
63~79
87 98
51~61
76 95
200
176
普 157
通 铸
139
钢 69
47
35
400 490
270~360 430
352 430
235~310 376
314 385
210~280 336
278
顶 况适当降低20%左右。根据
针 尾定承受转速的耐热状态和
车 工艺系统刚性可进行适当调 削 整,普通类尾定一般不超
550转/分。
34
53
66 79
32
29
46
57 69
27
25
41
51 61
24
23
37
46 55
22
53 66 46 57 41 51 37 46
46
53 62
40
46 55
35
41 48
400
637
796
340
537
670
300
470
587
270
420
525
238
375
468
119
187
233
80
126
157
60
95
118
47
75
93
40
63
78
精加工 转速 180
材 料
锻件粗加工 转速74
型材加 工转速
精加工 转速
材 料
锻件及 调质件 加工转 速110
1300
1100
1300 1300
340
42C rMo
190~254 300
138 170
95~116 150
94 115
64~84 100
70 87
48~63 76
342
297
YW 1 、 YT 14
普 通 铸 钢 毛 坯
265 239 119
76
56
80~95
75~83 Q42
高 0、 65~75
速 钢
Q55 0、
55~65
刀 45# 30~35 等
30
37 44
29~39 56 25~34 48 23~30 43 22~28 39
加 孔长/孔径=1,转速×
工 深
0.65;孔长/孔径=2,转速 ×0.65×0.9;孔长/孔径 =3,转速×0.65×0.8;依
孔
次类推。
表中数据为有冷液切削相关材料正火外圆面的转速,车削端面提20%转速。 加工等材调质件外圆则需降低该转速的12%,加工相同材质件内 孔时则需降低35%。切断或车槽时则需按照型材加工转速的70%,车螺纹按该速度的50%即可。高速部分为数控车床转速,普通车床转速可根据设 备状况适当降低20%转速。特殊情况再根据实际情况确定。
刀 具
材 料
直径
10
型材
锻件毛坯车 调质件转速 正火
削转速68 100
转速
110
1000~1200 1000~1200 1200
常见材料车削转速
精加工 转速 125
材 锻件加工转 料 速65
型材加 工转速 96
精加工 转速 120
材 铸钢毛 料 坯45
铸钢正 常粗车 90
精加工 转速 110
材 料
1200
470 560
420 495
375
440
42C rMo
187 220
126 145
95 110
75 88
63 72
一般加工 精加工 转速 转速
1300 1100 1200 1100 1000 1000 850~950 980 700~880 785 500~680 650 350~480 565 258~340 490 280~330 436 210~278 390 105~122 198 70~92 128 53~69 99 41~56 80 35~46 65
车削、镗削 深孔
430
30 360
Cr Mn
320
Ti 168
189
76
126 157
110
142
57
95 118
85
112
45
75 93
66
94
38
63 78
55
型材加 工转速 120
精加工 转速
材 料
1300 1100
1200 1100
1200 1100
1000 1000
750 880
637 740
537 660
45 80 260~310 310~390 430 488 、 254~304 376 470
90
YT1 5
A3
100
235~280 212~254
280~349 247~309
385 437 340 380
40 Cr
227~272
及 200~240
30
336 300
420 375
200 106~1126 123~154 170 190 Cr 100~120 150 187
406~480 600 750
278 556 680
380~510 600
477
60 360~430 420~527 580 658
345~410 510 637
237 474 580
325~430 510
396
90~110
70 300~360 355~445 490 555
290~348 430 537
500 42~51
48~61
68 77
40~48
60 75
27
54 68
38~51 60
48
用合金
600 35~42
41~52
5
46 58
32~42 51
40
刀按照
相关速
700 30~36
35~44
49 55
29~35
43 53
20
40 49
27~36 43
31
度加工
1100~1200 1200 1200
700 1200 1200
加工转速 精加工 刀 材 粗加工 68 转速96 具 料 转速74
刀材 具料
转速26
1200 1200
1000
20 616~740 880~1100 1200 1200
900~1000 1200 1200