车床切削用量选择与计算分解
切削用量及选择
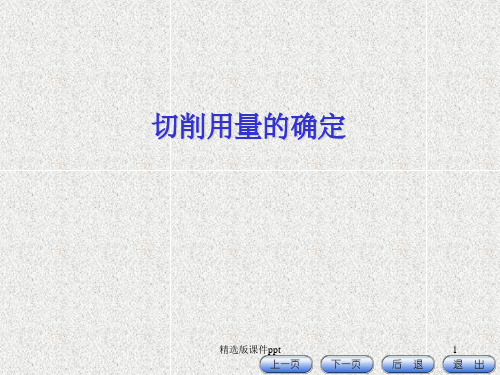
精选版课件ppt
14
3、切削用量对刀具耐用度的影响
(3) 进给量f与刀具耐用度的关系
当增大进给量后,切屑厚度增大,由切屑带着走的热量增 多,同时切屑与前刀面的接触长度增加,散热面积增大。 通过测试得知,切削温度随进给量的增加而升高,但温度 的升高幅度不及切削速度显著。
(4 )背吃刀量ap与刀具耐用度的关系
下课件ppt
33
4.分段切削背吃刀量
如果牙型较深,螺距较大,可分几次进给。每次进给 背吃刀量用螺纹深度减精加工背吃刀量所得的差按递减规 律分配。
螺纹分段切削示意图
常用螺纹切削进给次数与背吃刀量可参考表3-7~表3-9
精选版课件ppt
34
总结
1. 切削用量确定的步骤
背吃刀量的选择 →进给量的选择→切削速度的确定→校验 2. 提高切削用量的途径
13
3、 切削用量对刀具耐用度的影响 (1)刀具耐用度 所谓刀具耐用度,是指一把新刀从开始切削直到磨损量 达到磨损标准为止,在这期间所使用的总的切削时间, 用T表示。
(2) 切削速度vc与刀具耐用度的关系
切削速度是影响刀具耐用度的主要因素,其原因是当提高 切削速度时,单位时间的金属去除率会成正比例增加,刀 具与工件间的摩擦加剧,消耗于金属变形和摩擦的无用功 增加,因而产生过多的热量。因此,提高切削速度的结果 是:摩擦热大量的积聚在切屑底层而来不及传导出去,从 而使切削温度急剧升高,使刀具的耐用度大大降低。
精选版课件ppt
16
切削用量的选择:基本原则
选择切削用量的基本原则是首先选取尽可能大的背吃刀量; 其次要在机床动力和刚度允许的范围内,同时又满足已加 工表面粗糙度的要求的情况下,选取尽可能大的进给量, 最后利用《切削用量手册》选取或用公式计算确定最佳切 削速度。
确定切削用量及基本工时

(五)确定切削用量及基本工时。
工序Ⅰ:车削A面。
1.加工条件。
工件材料:灰口铸铁HT200。
σb=145 MP a。
铸造。
加工要求:粗、半精车A面并保证28mm的工序尺寸,R a=3.2µm机床C3163-1。
转塔式六角卧式车床。
刀具:刀片材料。
r =12. a o=6-8 b= -10 o=0.5 K r=90 n=15 2、计算切削用量。
(1)已知长度方向的加工余量为3±0.8mm 。
实际端面的最大加工余量为3.8mm 。
故分二次加工(粗车和半精车)。
长度加工公差IT 12级取-0.46 mm (入体方向)(2)进给量、根据《切削简明手册》(第3版)表1.4 当刀杆尺寸为16mm×25mm,ae≤3mm时,以及工件直径为Φ60mm时(由于凸台B 面的存在所以直径取Φ60mm)ƒ=0.6-0.8mm/r.按C3163-1车床说明书取ƒ=0.6mm/n。
由于存在间歇加工所以进给量乘以k=0.75—0.85 所以:实际进给量f=0.6×0.8=0.48 mm/r按C3163-1车床说明书ƒ=0.53mm/r(3)计算切削速度。
按《切削简明手册》表 1.27 ,切削速度的计算公式为(寿命选T=60min)刀具材料YG6V=C v/(T m·a p x v·f y v) ·kv其中:C v=158 x v=0.15 y v=0.4 M=0.2修正系数K o见《切削手册》表1.28k mv=1.15 k kv=0.8 k krv=0.8 k sv=1.04 k BV=0.81∴Vc =158/( 600.2·20.15·0.530.4) ·1.15·0.8·0.8·0.81·0.97=46.9(m/min)(4)确定机床主轴转速 ns=1000v c/ dw=229.8(r/min)按C3163-1车床说明书n=200 r/min所以实际切削速度V=40.8m/min(5)切削工时,按《工艺手册》表6.2-1由于铸造毛坯表面粗糙不平以及存在硬皮,为了切除硬皮表层以及为下一道工步做好准备T m=(L+L1+L2+L3)/n w x f=0.33(min) L=(65-0)/2=32.5 L1=3、L2=0、L3=02、精车1)已知粗加工余量为0.5mm。
车床切削用量选择与计算
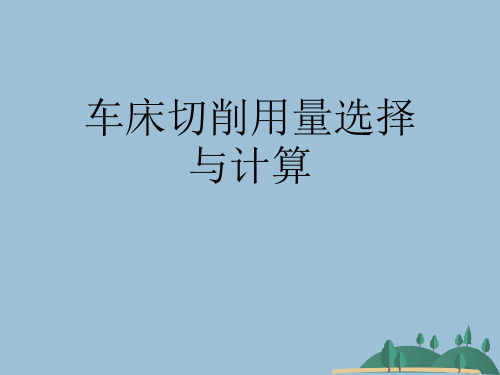
根据加工性质、加工要求、工件材料及刀具材料和尺寸 查切削用量手册并结合实践经验确定,并考虑以下几个方面:
dm—工件已加工表面的直径,(mm)
注意:切断、车槽时的切削深度为车刀主切削刃 的宽度
背吃刀量(也称切削深度)ap
——指工件已加工表面和待加工表面间 的垂直的距离。
背吃刀量的选择
• 根据加工性质和加工余量来确定
– 粗车时取ap=2~6mm; – 半精车时取ap=0.3~2mm; – 精车时取ap=0.1~0.3mm;
dm—工件已加工表面的直径,(mm)
在学习过程中多思、多问
车削加工切削用量的选择
切削用量选择方法
① 背吃刀量aP(mm)的选择
粗加工(Ra10~80μm)时,一次进给应尽可 能切除全部余量。在中等功率机床上,背吃 刀量可达8~l0mm。 半精加工(Ra1.25~l0μm)时,背吃刀量取 为0.5~2mm。 精加工(R)时,背吃刀量取为。
2、在切断、加工深孔或 用高速钢刀具加工时,宜选择 较低的进给速度,一般在20~50mm/min范围内选取。
3当加工精度、表面粗糙度要求较高时,进给速度应选 小些,一般在20~50mm/min范围内选取
4、刀具空行程时,特别是远距离“回零”时,可以采 用该机床数控系统设定的最高进给速度。
车削加工切削用量的选择
=(28.
用度确定最佳的切削速度。
解:(1)切削深度ap=(dw - dm)/2
加工大件、细长件和薄壁工件时,应选用较低的切削速度;
切削 用量的合理选择
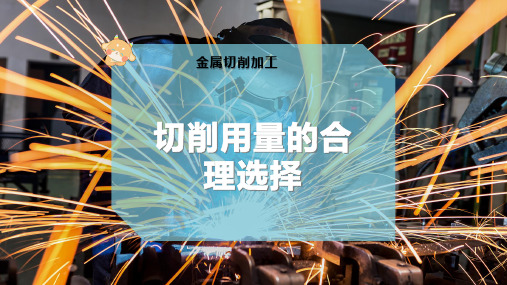
2)根据机床说明书,取机床实际进给量 =0.51mm/r。 3)检验机床进给机构允许的进给量。参考CA6140车床说 明书,查出机床进给机构允许的最大进给抗力为:FMfmax= 3528N。 计算切削时进给力为:
统、工件刚度以及精加工时表面粗糙度要求,确定进给量。
3)根据刀具寿命,确定切削速度。 4)所选定的切削用量应该是机床功率所允许的。
1.2切削用量的合理选择方法
1.背吃刀量的合理选择
背吃刀量一般是根据加工余量来确定。 粗加工(表面粗糙度Ra=50~12.5μm)时,尽可能一 次走刀即切除全部余量,在中等功率的机床上加工,取 ap=8~10mm;加工余量太大或余量不均匀、工艺系统刚性 不足或者断续切削时,可分几次走刀。 半精加工(Ra=6.3~3.2μm)时,取ap=0.5~2mm。 精加工(Ra=1.6~0.8μm)时,取ap=0.1~0.4mm。
1.5切削用量的优化概念
切削用量的优化是指在一定的预定目标及约束条件下, 选择最佳的切削用量。
在实际生产中,由于各种条件(加工零件、机床、刀 具、夹具等)都在变化,很难确定出一组最合理的切削用 量数值。
利用切削用量优化的方法,在确定加工条件下,综合 考虑各个因素,通过计算机辅助设计,能找出满足高效、 低成本、高利润和达到表面质量要求的一组最佳的切削用 量参数。实际切削用量的优化过程就是建立优化目标的数 学模型,用计算机求极值。主要目标函数有三个。
床功率是否允许。 在实际生产中,切削用量的合理选择,既可参照有关 手册的推荐数据,也可凭经验根据选择原则确定。
1.3车削用量的合理选择例题
车削切削用量选取参考表讲解学习
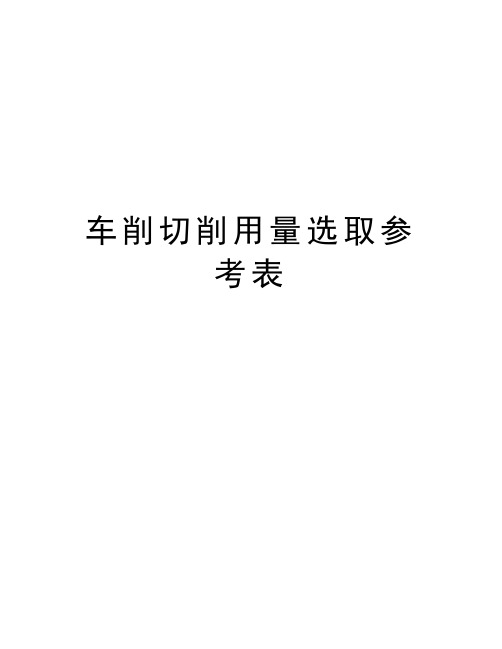
2.1
0.9
>360~500
1.4
0.7
1.5
0.7
1.5
0.8
1.7
0.8
1.9
0.9
2.2
1
1、粗加工,表面粗糙度为Ra50~12.5时,一次走刀应尽可能切除全部余量。
2、粗车背吃刀量的最大值是受车床功率的大小决定的。中等功率机床可以达到8~10mm。
二、高速钢及硬质合金车刀车削外圆及端面的粗车进给量
工件材料
车刀刀杆尺寸(mm)
工件 直径(mm)
切深
≤3
3~5
5~8
8~12
>12
进给量fmm/r
碳素结构钢、合金结构钢、耐热钢
16×25
20
0.3~0.4
—
—
—
—
40
0.4~0.5
0.3~0.4
—
—
—
60
0.5~0.7
0.4~0.6
0.3~0.5
—
—
100
0.6~0.9
0.5~0.7
0.5~0.6
0.4~0.5
275-335
0.25
8
17-21
0.5
66-72
82-90
0.75
YT5
105-120
0.5
215-245
0.4
高强度钢
225~350
1
20-26
0.18
90-105
115-135
0.18
YT15
150-185
0.18
380-440
0.13
>300HBS时宜用W12Cr4V5Co5及W2Mo9Cr4VCo8
车床切削用量如何选择
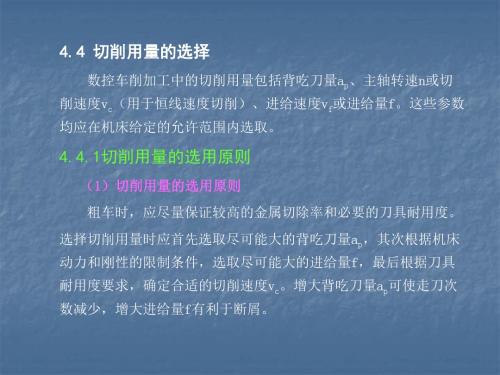
证同轴度。
(2)按粗、精加工划分工序
即粗加工中完成的那部分工艺过程为一道工序,精加工中完成的 那一部分工艺过程为一道工序。对毛坯余量较大和加工精度要求较高
的零件,应将粗车和精车分开,划分成两道或更多的工序。将粗车安
排在精度较低、功率较大的数控机床上进行,将精车安排在精度较高 的数控机床上完成。
这种划分方法适用于加工后变形较大,需粗、精加工分开的零件,
表4-3 硬质合金刀具切削用量推荐表
粗 加 工 刀具 材料 工件材料 切削速度 (m/min) 220 180 120 80 80 40 120 100 1600 进给量 (mm/r) 0.2 背吃刀量 mm 3 切削速度 (m/min) 260 精 加 工 进给量 (mm/r) 0.l 背吃刀量 mm 0.4 0.4 0.4 0.4 0.4 0.4 0.5 0.5 0.5
程。
确定走刀路线的总原则:在保证零件加工精度和表面质量的前 提下,尽量缩短走刀路线,以提高生产率;方便坐标值计算,减少
编程工作量,便于编程。对于多次重复的走刀路线,应编写子程序,
简化编程。
数控车床上加工零件时常用的走刀路线: (1)车圆弧的走刀路线分析 实际车圆弧时,需要多刀加工,先将大部分余量切除,最后才 车出所需圆弧。下面介绍车圆弧常用的加工路线。
4.4 切削用量的选择
数控车削加工中的切削用量包括背吃刀量ap、主轴转速n或切
削速度vc(用于恒线速度切削)、进给速度vf或进给量f。这些参数 均应在机床给定的允许范围内选取。
4.4.1切削用量的选用原则
(1)切削用量的选用原则 粗车时,应尽量保证较高的金属切除率和必要的刀具耐用度。 选择切削用量时应首先选取尽可能大的背吃刀量ap,其次根据机床 动力和刚性的限制条件,选取尽可能大的进给量f,最后根据刀具 耐用度要求,确定合适的切削速度vc。增大背吃刀量ap可使走刀次 数减少,增大进给量f有利于断屑。
切削用量选择

卧式数控车床切削用量选择作者:杨树诚单位:沈阳第一机床厂技术部日期:2005年09月本文着重提醒读者1.不要轻易按刀具样本的推荐值确定切削速度,那样刀具寿命很低。
一般情况下,硬质合金刀片可按刀具样本推荐值的0.64~0.71倍选择切削速度。
2.确定精加工和半精加工的进给量着眼于工件的表面粗糙度。
它还和刀尖半径有关。
文中列表表明三者对应关系,供选择进给量参考。
3.条件允许时希望粗加工吃刀深尽量大。
一方面有效提高生产率;一方面也为了消除表面硬皮.切除砂眼等缺陷,从而保护刀尖不与毛坯接触。
精加工时也不希望吃刀深太小,以免产生刮擦对粗糙度不利。
4.表5~表12列举了外圆.端面.内孔加工,切槽,车螺纹的切削用量推荐值。
供一般情况下采用。
目录一.原始资料 (1)二.选择切削用量的原则 (1)三.吃刀深αp (2)四.进给量f (2)五.切削速度V (4)六.切削用量推荐值 (5)切削用量选择关键词: 刀具耐用度 切削速度 表面粗糙度 进给量 吃刀深在售前服务编制加工工序卡以及调装设计中,都需要确定切削用量及计算节拍时间。
本文就卧式数控车床如何合理选择切削用量进行探讨。
一. 原始资料:无论编制加工工序卡-即制定工艺方案还是调装设计都需要掌握以下资 料,做为刀具选择.卡具设计以及选择切削用量的依据。
.1 工件图:包括形状.尺寸.公差.形位公差.粗糙度和其他技术要求。
特别强调的是本序 加工的部位必须明确,用于及可能影响装卡部位的形状要表示清楚。
2.毛坯图:毛坯形状.尺寸,加工余量,材料.硬度等。
3.生产纲领:即年产量或单件时间,这对招标项目尤为重要。
4.验收要求:机床验收时对工件考核什麽项目,有无Cp 值和其它要求。
5.用户对工件定位基准.卡紧面.辅助支承 等要求,或指定参考的卡具样式。
6. 对刀具选择要求:用国产刀具或国外指定厂家 的刀具,特殊刀具是否自备等。
7. 用户单位,件名.件号等也应标明,以便管理。
二 选择切削用量的原则:1. 总的要求:保证安全,不致发生人身事故或设备事故;保证加工质量。
车床的切削用量及单位
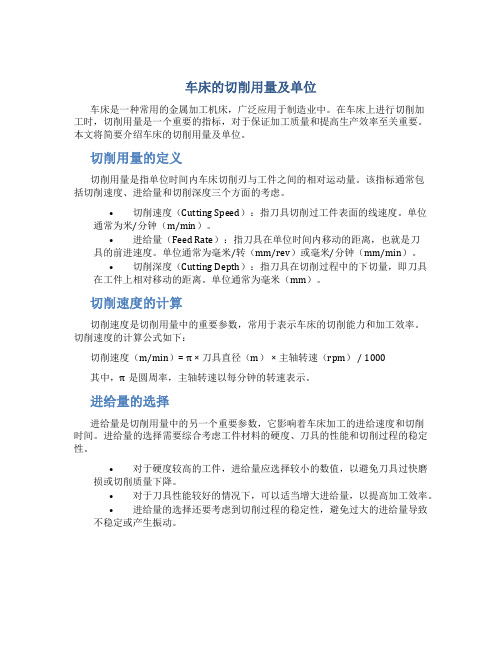
车床的切削用量及单位车床是一种常用的金属加工机床,广泛应用于制造业中。
在车床上进行切削加工时,切削用量是一个重要的指标,对于保证加工质量和提高生产效率至关重要。
本文将简要介绍车床的切削用量及单位。
切削用量的定义切削用量是指单位时间内车床切削刃与工件之间的相对运动量。
该指标通常包括切削速度、进给量和切削深度三个方面的考虑。
•切削速度(Cutting Speed):指刀具切削过工件表面的线速度。
单位通常为米/分钟(m/min)。
•进给量(Feed Rate):指刀具在单位时间内移动的距离,也就是刀具的前进速度。
单位通常为毫米/转(mm/rev)或毫米/分钟(mm/min)。
•切削深度(Cutting Depth):指刀具在切削过程中的下切量,即刀具在工件上相对移动的距离。
单位通常为毫米(mm)。
切削速度的计算切削速度是切削用量中的重要参数,常用于表示车床的切削能力和加工效率。
切削速度的计算公式如下:切削速度(m/min)= π × 刀具直径(m) × 主轴转速(rpm) / 1000其中,π是圆周率,主轴转速以每分钟的转速表示。
进给量的选择进给量是切削用量中的另一个重要参数,它影响着车床加工的进给速度和切削时间。
进给量的选择需要综合考虑工件材料的硬度、刀具的性能和切削过程的稳定性。
•对于硬度较高的工件,进给量应选择较小的数值,以避免刀具过快磨损或切削质量下降。
•对于刀具性能较好的情况下,可以适当增大进给量,以提高加工效率。
•进给量的选择还要考虑到切削过程的稳定性,避免过大的进给量导致不稳定或产生振动。
切削深度的控制切削深度是切削用量中的另一个重要参数,它直接影响到车床的切削性能和加工结果。
切削深度的选择需要根据工件的要求、刀具的刚度和车床的稳定性进行综合考虑。
•对于高精度要求的工件加工,通常选择较小的切削深度,以保证加工精度和表面质量。
•切削深度还应考虑到刀具的刚度,避免过大的切削深度导致刀具振动或断裂。
- 1、下载文档前请自行甄别文档内容的完整性,平台不提供额外的编辑、内容补充、找答案等附加服务。
- 2、"仅部分预览"的文档,不可在线预览部分如存在完整性等问题,可反馈申请退款(可完整预览的文档不适用该条件!)。
- 3、如文档侵犯您的权益,请联系客服反馈,我们会尽快为您处理(人工客服工作时间:9:00-18:30)。
根据加工性质、加工要求、工件材料及刀具材料和尺寸 查切削用量手册并结合实践经验确定,并考虑以下几个方面:
车削加工切削用量的选择
切削用量选择方法
② 进给量f(mm/r)和进给速度(mm/min)的选择 根据零件的表面粗糙度、加工精度要求、刀具及 工件材料等因素,参考切削用量手册选取。 实际操作加工时,需要根据公式vf=nf转换成进给 速度。
车削加工切削用量的选择
1、当工件的质量要求能得到保证时,为提高生产效率, 可选择较高的进给速度,一般100~200mm/min 2、在切断、加工深孔或 用高速钢刀具加工时,宜选择 较低的进给速度,一般在20~50mm/min范围内选取。 3当加工精度、表面粗糙度要求较高时,进给速度应选 小些,一般在20~50mm/min范围内选取
=3mm
(2)试车后切削深度ap=(dw - dm)/2 =(28.4 -24) /2 =2.2mm 手柄应转的格数为:2.2/0.05=44格
进给量f
工件每转一转时,车刀在进给运动方向上移动的距离 叫进给量,用(fr)表示,单位是mm/r(也叫每转进给量) 。 进给量还可表示进给运动时的速度,进给速度(fv )就是在 单位时间内刀具在进给方向上移动的距离, 单位mm/s, fv=n × fr 其中: n —主运动的转速,(mm/s); fr —每转进给量,(mm/r)
a. 应尽量避开积屑瘤产生的区域; b. 断续切削时,为减小冲击和热应力,要适当降低切削速度; c. 在易发生振动的情况下,切削速度应避开自激振动的临界速度; d. 加工大件、细长件和薄壁工件时,应选用较低的切削速度; e. 加工带外皮的工件时,应适当降低切削速度。
切削用量
切削用量(又叫切削三要素)是衡量车削运动大小的参数。 它包括切削深度、进给量、切削速度。 (1) 、切削深度ap (背吃刀量) 切削深度为工件上已加工表面和待加工表面间
(1)生产效率
(2)机床特性(机床功率)
(3)刀具差异(刀具耐用度) (4)加工表面粗糙度
车削加工切削用量的选择
切削用量选择原则
① 粗加工时切削用量的选择原则 首先选取尽可能 大的背吃刀量;其次要根据机床动力和刚性的限制 条件等,选取尽可能大的进给量;最后根据刀具耐 用度确定最佳的切削速度。
② 精加工时切削用量的选择原则 首先根据粗加工 后的余量确定背吃刀量;其次根据已加工表面的粗 糙度要求,选取较小的进给量;最后在保证刀具耐 用度的前提下,尽可能选取较高的切削速度。
解:时间T=L/(n×fr)
=800/(600 × 0.1)
=13.33(分)
切削速度V
主运动的线速度叫切削速度,单位为m/min。 车削外圆时的切削速度计算公式为: V=πdn/1000
其中: d—工件待加工表面的直径,(mm);
n—工件的转速,(r/min); V —切削速度,( m/min)。
– – – – 精加工时,应避免积屑瘤和鳞刺的产生 断续切削时,应降低切削速度 加工特殊工件时,应降低切削速度 避开自激振动的临界速度
例3:车削直径为300mm的铸铁带轮外圆, 若切削速度为60m/ min,试求车床主轴转速。
解:根据公式V=πdn/1000 得:n=1000V/ πd =1000 ×60/3.14 ×300 =63.69r/min
切削速度vc
——主运动的线速度。 车削时,刀具切削刃上某选定点相对于待加工表面 在主运动方向上的瞬时速度。
π dn
切削速度示意图
• 其它条件确定后,根据下列公式计算速度
Cv vc 1m m xv 60 T a p f
yv
Kv
• 根据上述速度值,计算机床的转速 • 根据选定的转速值再计算实际的切削速度 • 选择切削速度的注意事项
车床切削用量选择与计算
贾豪
2013年12月
车床切削用量选择与计算
• 科目:车床切削用量选择与计算 • 目的:通过本节课的学习,使同志们了解, 在实际加工过程中合理的选择切削深度、进 给量及主轴转速 • 内容: 1.了解切削用量三要素 2.切削用量的选择 • 3.掌握切削用量计算公式 • 方法:理论讲解 观看课件 总结讲评 时间:30分钟 要求: 1. 用心听,仔细记,遵守课堂纪律 2.在学习过程中多思、多问
Байду номын сангаас
重点
切削三要素 及其计算公 式。
难点
切削速度及 其计算公式。
学法指导
本节课,通过概念引出公式,制定几个小坡 度学习任务,使同志们逐步掌握本节内容。 同时,引导同志们养成善于提出问题、分析 问题、解决问题的习惯,培养自学能力,要 善于把课堂所学应用到实际生产中去。
车削加工切削用量的选择
切削用量选择原则
注意:在实际生产中,理论上计算出的主轴转 数应从车床转速表中最接近的一档选取。
进给量的确定 • 粗加工时
– 刚度和强度允许时,取大值
• 半精加工和精加工时
– 为提高生产率,进给量可适当放大; – 进给量不宜取得太小
• 进给量根据经验查表确定 • 特殊情况下,应按机床的说明书选择
进给量 f
——指工件每转一转时,车刀沿进给方向移动的 距离。
例2:车工件时主轴转速为n=600r/min,进 给量为fr=0.1mm/r,要将一根长800mm的 轴一刀车完要用多少时间?
– 粗车时取ap=2~6mm; – 半精车时取ap=0.3~2mm; – 精车时取ap=0.1~0.3mm;
• 在下列情况下,粗车多次走刀
– 刚度低,余量不均匀时; – 余量太大导致机床功率不足时; – 断续切削时
• 外圆车削时的背吃刀量
• 端面车削时的背吃刀量
例1:要将直径为30mm的轴一刀车至24mm,试问 切削深度是多少?若试车时测得直径为28.4mm, 这时中拖板(每格为0.05mm)手柄应转多少格? 解:(1)切削深度ap=(dw - dm)/2 =(30-24)/2
的垂直距离,单位为mm。即:ap=(dw-dm)/2
其中: dw—工件待加工表面的直径,(mm); dm—工件已加工表面的直径,(mm)
注意:切断、车槽时的切削深度为车刀主切削刃 的宽度
背吃刀量(也称切削深度)ap ——指工件已加工表面和待加工表面间
的垂直的距离。
背吃刀量的选择
• 根据加工性质和加工余量来确定
4、刀具空行程时,特别是远距离“回零”时,可以采 用该机床数控系统设定的最高进给速度。
车削加工切削用量的选择
切削用量选择方法
③ 切削速度vC(m/min)的选择 根据已经选定的背吃刀量、进给量及刀具耐用度选 择切削速度。 可用经验公式计算,也可根据生产实践经验在机床说明 书允许的切削速度范围内查表选取或者参考有关切削用 量手册选用。 在选择切削速度时,还应考虑以下几点:
车削加工切削用量的选择
切削用量选择方法
① 背吃刀量aP(mm)的选择 粗加工(Ra10~80μm)时,一次进给应尽可 能切除全部余量。在中等功率机床上,背吃 刀量可达8~l0mm。 半精加工(Ra1.25~l0μm)时,背吃刀量取 为0.5~2mm。 精加工(Ra0.32~1.25μm)时,背吃刀量取 为0.2~0.4mm。