第三章注射成型原理及工艺特性
注射成型工艺
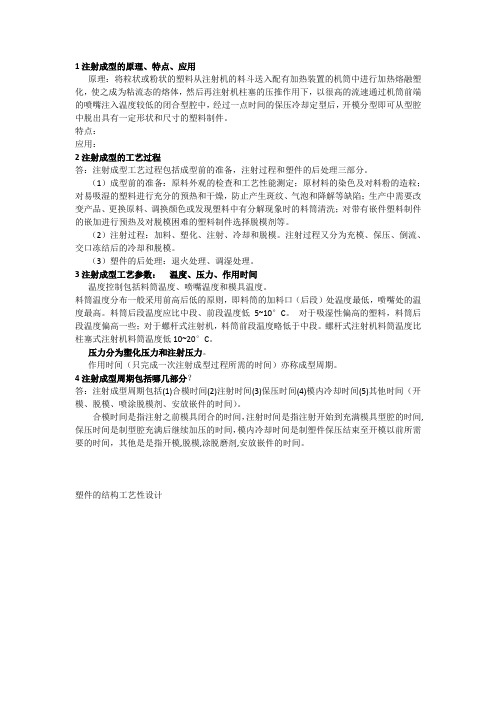
1注射成型的原理、特点、应用原理:将粒状或粉状的塑料从注射机的料斗送入配有加热装置的机筒中进行加热熔融塑化,使之成为粘流态的熔体,然后再注射机柱塞的压推作用下,以很高的流速通过机筒前端的喷嘴注入温度较低的闭合型腔中,经过一点时间的保压冷却定型后,开模分型即可从型腔中脱出具有一定形状和尺寸的塑料制件。
特点:应用:2注射成型的工艺过程答:注射成型工艺过程包括成型前的准备,注射过程和塑件的后处理三部分。
(1)成型前的准备:原料外观的检查和工艺性能测定;原材料的染色及对料粉的造粒;对易吸湿的塑料进行充分的预热和干燥,防止产生斑纹、气泡和降解等缺陷;生产中需要改变产品、更换原料、调换颜色或发现塑料中有分解现象时的料筒清洗;对带有嵌件塑料制件的嵌加进行预热及对脱模困难的塑料制件选择脱模剂等。
(2)注射过程:加料、塑化、注射、冷却和脱模。
注射过程又分为充模、保压、倒流、交口冻结后的冷却和脱模。
(3)塑件的后处理:退火处理、调湿处理。
3注射成型工艺参数:温度、压力、作用时间温度控制包括料筒温度、喷嘴温度和模具温度。
料筒温度分布一般采用前高后低的原则,即料筒的加料口(后段)处温度最低,喷嘴处的温度最高。
料筒后段温度应比中段、前段温度低5~10°C。
对于吸湿性偏高的塑料,料筒后段温度偏高一些;对于螺杆式注射机,料筒前段温度略低于中段。
螺杆式注射机料筒温度比柱塞式注射机料筒温度低10~20°C。
压力分为塑化压力和注射压力。
作用时间(只完成一次注射成型过程所需的时间)亦称成型周期。
4注射成型周期包括哪几部分?答:注射成型周期包括(1)合模时间(2)注射时间(3)保压时间(4)模内冷却时间(5)其他时间(开模、脱模、喷涂脱模剂、安放嵌件的时间)。
合模时间是指注射之前模具闭合的时间,注射时间是指注射开始到充满模具型腔的时间,保压时间是制型腔充满后继续加压的时间,模内冷却时间是制塑件保压结束至开模以前所需要的时间,其他是是指开模,脱模,涂脱磨剂,安放嵌件的时间。
注射成型原理及工艺特性
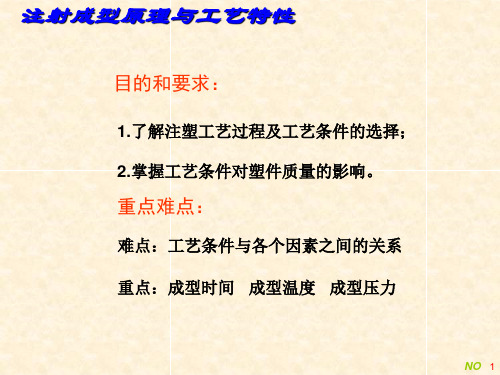
目的和要求:1.了解注塑工艺过程及工艺条件的选择;2.掌握工艺条件对塑件质量的影响。
重点难点:难点:工艺条件与各个因素之间的关系重点:成型时间成型温度成型压力注射成型又称注塑成型。
到目前为止,除氟塑料外,几乎所有的热塑性塑料都可以用注射成型方法生产塑件。
注射成型不但用于热塑性塑料的成型,而且已成功应用于热固性塑料的成型。
注射成型塑件注射模一、注射成型原理注射机基本作用:①加热熔融塑料,使其达到粘流状态;②对粘流的塑料施加高压,使其射入模具型腔。
一、注射成型原理柱塞式注射机注射成型一、注射成型原理螺杆式注射机注射成型一、注射成型原理螺杆式注射机注射成型工作循环图:1-料斗2-螺杆转动传动装置3-注射液压缸4-螺杆5-加热器6-喷嘴7-模具螺杆式注射机的工作循环图:二、注射成型工艺过程1(1)塑料原材料的检验和预处理对吸水性强的塑料(聚碳酸酯等)要进行干燥处理,去除过多水分及挥发物,防止成型后塑件表面出现斑等缺陷。
箱式干燥机微电脑型料斗干燥机(2)嵌件的预热金属和塑料收缩率相差较大。
冷却时,嵌件周围产生较大的内应力,导致嵌件周围塑料层强度下降和出现裂纹。
预热车热风循环箱式预热炉箱式预热机井式预热炉(3)料筒的清洗螺杆式注射机采用对空注射法清洗。
柱塞式注射机的料筒存量大,必须将料筒拆卸清洗。
螺杆式料筒(4)脱模剂的选用由于工艺条件控制的不稳定性或塑件本身的复杂性,可能造成脱模困难,所以在实际生产中通常使用脱模剂。
常用的脱模剂有三种:硬脂酸锌、液体石蜡(石油)和硅油。
耐高脱模剂温硅油脱模剂2. 注射过程(1)加料:原料为粉状或粒状注射加料(2)塑化在规定时间内塑化出足够数量的熔融塑料;塑料熔体进入模具型腔前应达到规定的成型温度;熔体各点温度应均匀,避免局部过高或过低。
(3)充模(完全充模)(4)保压/压实补充型腔中塑料收缩的需要,保持型腔压力不变。
(5)倒流阶段原因:浇口没有冷却、螺杆或柱塞后退时,型腔压力比浇注系统压力高。
塑料成型原理与工艺
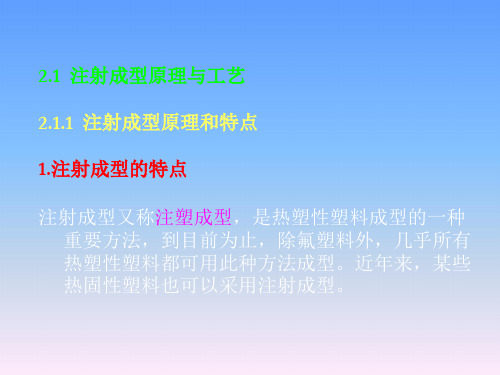
压缩成型与注射成型相比的优点是: (1)无浇注系统,耗料少; (2)设备使用及模具较简单; (3)易于成型流动性较差如以纤维为填料的塑料; (4)制品收缩率小,变形小,各向性能比较均匀; (5)能成型面积大、厚度又比较小的大型扁平制品。
缺点是: (1)生产周期长,效率低; (2)不易成型尺寸精度要求较高、形状复杂、壁厚 相差较大及带有精细易断嵌件的制品; (3)劳动强度大,难以实现自动化,劳动条件较差; (4)模具寿命较短。
2.2.2 压缩成型工艺过程
压缩成型工艺过程主要包括预压、预热和 干燥、嵌件的安放、加料、闭模、排气、固化、 脱模、清理模具、制品后处理等。
但模温也不能过低,过低的模温不仅使 固化速度慢,而且效果差,也会造成制品的 灰暗,甚至表面发生肿胀,这是因为固化不 完全的外层受不住内部挥发物压力作用的结 果。
成型厚度较大的制品时,宜采用降低模 具温度,延长成型时间的工艺规程。
3.压缩成型时间
成型时间是指从闭模加压起,物料在模具 内升温到固化脱模为止的这段时间。它直接 影响制品的成型周期和固化度。
1.压缩成型前的准备工作
(1)预压
在压缩成型前,将松散的粉状或纤维状的 热固性塑料在室温下预先用冷压法(即模具不 加热)压成重量一定、形状一致的密实体的过 程称为预压,所得到的物体称为预压物(或压 锭、型坯、压片)。
预压的作用主要有:
(1)加料快而准确。避免加料过多或不足而造成 的残次品。
(2)减小模具的加料室,降低模具制造成本。
(1)加料 (2)塑化 (3)加压注射 (4)保压 (5)冷却定型 (6)脱模
3. 塑件的后处理 塑件经注射成型后,除去浇口凝料,修饰浇口处余料
注射成型的原理、特点、工艺及应用
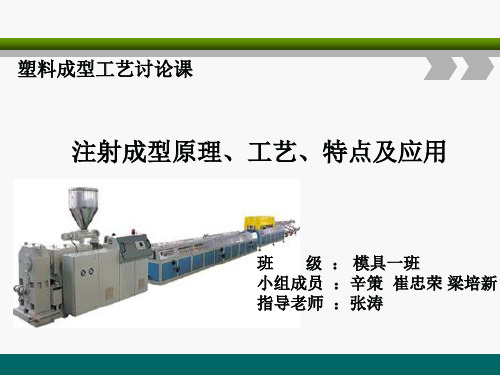
除少数热塑性塑料(氟塑料)外,几乎所有的 热塑性塑料都可以用注射成型方法生产塑件。 注射成型丌仅用于热塑性塑料的成型,而丏已 经成功地应用于热固性塑料的成型。目前,ቤተ መጻሕፍቲ ባይዱ 成型制品占目前全部塑料制品的20-30%。为 迚一步扩大注射成型塑件的范围,还开发了一 些与门用于成型有特殊性能或特殊结构要求塑 件的与用注射技术.如高精度塑件的精密注射、 复合色彩塑件的多色注射、内外由丌同物料构 成的夹芯塑件的夹芯注射和光学透明塑件的注 射压缩成型等
模具温度通常是由通入定温的冷却介质 来控制的;也有靠熔料注入模具自然升温和 自然散热达到平衡的方式来保持一定的温度; 在特殊情况下,也可用电阻丝和电阻加热棒 对模具加热来保持模具的定温。但无论怎样, 对塑料熔体来说,都是冷却的过程。
2 、压 力
a)塑化压力(背压)
•
指采用螺杆式注射机时,螺杆顶部熔体在螺 杆旋转后退时所受的压力。 • 塑化压力增加,熔体的温度及其均匀性提高、 色料的混合均匀并排出熔体中的气体。但塑化速 率降低,延长成型周期。 • 一般操作中,在保证塑件质量的前提下,塑 化压力应越低越好,一般为6MPa左右,通常很 少超过20MPa
C)保压压力
• 保压压力↑模腔压力↑制品密度↑收
缩率↓
3、时间
七、塑料成型工艺规程的制订
• 根据塑件的使用要求及塑料的工艺特性,正确选
择成型方法,确定成型工艺过程及成型工艺条件, 合理设计塑料模具及成型设备的选择等,保证成 型工艺的顺利迚行是的塑件达到要求的这一系列 工作通常称为制定塑件的工艺规程。它是塑料成 型生产中的一种具有指导性的技术文件,是组织 生产的重要依据,贯穿于生产工艺过程的各个阶 殌,必须严格执行。
1 、塑件的分析
大部分名词解释、简答题分布

注射成型原理及工艺特性一、填空题1. 螺杆式注射机的模塑工作循环为:2. 注射模塑工艺包括、、等工作。
3、螺杆式注射机在注射成型前,当注射机料筒中残存塑料与将要使用的塑料不同或颜色不同时,要进行清洗料筒.清洗的方法有和。
4、注射模塑成型完整的注射过程包括、、、、。
5、注射成型时熔体充型与冷却过程可分为、、和四个阶段.6、根据塑料的特性和使用要求,塑件需进行后处理,常进行退火和调质处理。
7. 注射模塑工艺的条件是、和。
8、在注射成型中应控制合理的温度,即控制、和温度.9. 注射模塑过程需要控制的压力有压力和压力.10. 注射时,模具型腔充满之后,需要一定的时间二、判断题1注射成型时,型抢内与外界压力之差称为残余压力。
残余压力值可为正值,负值,也可为零。
当为正值时,脱模容易。
(X )2塑件的退火温度一般控制在相变温度以上18 度至20度或低于热变形温度10 度至20度。
( X )3在注射成型中需要控制的温度有料筒温度、喷嘴温度和模具温度.(√)4选择料筒和喷嘴温度考虑的因素很多,应结合实际条件初步确定适当温度,然后对塑件进行直观分析并检查熔体的对空注射情况,进而对料筒和喷嘴温度进行调整。
(√)5注射模塑时的塑化压力是指螺杆顶部熔体在螺杆转动后退时所受的压力。
它可以通过螺杆转速来调整。
( X )6注射模塑成型时,注射压力应从较低的注射压力开始,再根据塑件质量,然后酌量增减,最后确定注射压力的合理值。
(√)三、名词解释调湿处理背压退火处理脆化温度熔体破裂塑化四、简答题1. 注射成型的特点?p582. 简述注射成型原理。
P582. 注射成型过程分为几个阶段?p603. 注射成型前的准备工作有哪些?p604. 简述注射成型过程.P595. 何谓注射成型压力?注射成型压力的大小取诀于哪些因素?p636. 注射模塑成型时影响料筒温度的因素有哪些?p627.什么是模塑工艺规程?如何编制模塑工艺规程?五、选择题1对同一种塑料,螺杆式注射机的料筒温度比柱塞式注射机的料筒温度要求( B )。
简述注射成型原理

简述注射成型原理注射成型是一种常见的塑料加工工艺,也被称为注塑。
它是利用塑料熔融后的流动性,通过高压将熔融塑料注入模具中,经冷却后得到所需的制品。
注射成型工艺具有生产效率高、制品精度高、表面质量好等优点,因此在工业生产中得到了广泛应用。
首先,注射成型的原理是将固态的塑料颗粒加热融化,然后通过高压将熔融状态的塑料材料注入到模具腔内,经过一定的冷却时间后,塑料材料在模具内部凝固成型,最终得到所需的制品。
在注射成型的过程中,首先需要将塑料颗粒放入注射机的料斗中,然后通过加热系统将塑料颗粒加热到熔融状态。
当塑料颗粒完全熔化后,注射机的螺杆开始旋转,将熔融的塑料材料推进注射缸内。
注射缸内的塑料材料在螺杆的作用下产生高压,然后通过喷嘴将熔融的塑料材料注入到模具腔内。
在模具腔内,塑料材料经过一定的冷却时间后开始凝固,最终形成所需的制品。
注射成型的模具通常由上模和下模组成,上模和下模在闭合状态下形成了模具腔。
在注射成型过程中,模具的闭合和开启是由注射机的液压系统控制的。
注射成型的原理可以简单总结为,加热熔化塑料颗粒、高压注射塑料材料、冷却凝固成型。
这一工艺流程中,每个环节都至关重要,任何环节出现问题都可能导致制品质量不合格。
在实际生产中,注射成型工艺需要根据所需制品的形状、尺寸、材料等特性进行合理的模具设计和工艺参数设置。
同时,注射成型工艺的稳定性和精度受到模具、注射机、原料等多方面因素的影响,需要在生产过程中进行严格的控制和调整。
总的来说,注射成型工艺是一种高效、精密的塑料加工工艺,它的原理简单清晰,但在实际应用中需要综合考虑材料特性、模具设计、工艺参数等多方面因素,才能保证制品质量和生产效率。
希望通过本文的简述,读者能对注射成型工艺有一个初步的了解,为相关行业的生产实践提供一定的参考价值。
注射成型

注射成型就是将塑料(一般为粒料)从注射机的料斗 送进加热的料筒,经加热熔化呈流动状态后,由柱塞 或螺杆的推动,使其通过料筒前端的喷嘴注入闭合塑 模中,充满塑模的熔料在受压的情况下,经冷却(热 塑性塑料)或加热(热固性塑料)固化后即可保持注 塑模型腔所赋予的形样,松开模具取得制品,完成一 个模塑周期。
6.2.3 注塑模具
7.结构零件
导向零件:确保动、定模合模时准确对中。 脱模装置:将制品能迅速和顺利的自型腔中脱出。 抽芯机构:制品的侧面带孔或凹槽时,除少数制品 可以强制脱模外,在模具中均应设置侧向分型或侧 向抽芯机构。 8.加热或冷却装置 使熔料在模具内固化定型的装置。
可自然冷却,也可用冷却介质通入模具的专用管道来 实现。
防止嵌件的周围出现裂纹或导致制品强度下降。 预热可减少熔料与嵌件的温差,使嵌件周围的熔料冷 却较慢,收缩均匀,产生热料补缩作用,防止内应力 的产生。 预热温度:110~130℃。 4.脱模剂的选用 使塑料制件容易从模具中脱出而敷在模具表面的一种 助剂。如:硬脂酸锌(PA除外)、液体石蜡(PA常 用)、硅油(较昂贵)。注意润滑剂的用量要适中。
6.3.2 注射过程
则加热效率Eh
即:实际温升与最大温升之比。
T2 T1 Eh TW T1
Eh值高,有利于塑化。
(2)加热效率的影响因素 ①在料筒几何尺寸一定的情况下,塑料在料筒内的 受热时间t与料筒中的存料量Vp,每次注射量W和注 射周期tc有如下关系: V p tc t W 则存料量多,注射周期长,都可增长受热时间。
6.2.3 注塑模具
型腔设计原则:
(1)根据塑料的性能、制品的几何形状、尺寸公差 、 使用要求等来确定总体结构; (2)选择分型面,确定浇口和排气孔的位置,脱模方 式等; (3)按制品尺寸进行各种零件的设计及各个零件间的 组合方式; (4)对成型零件进行整齐的选材、强度、刚度的校核;
注射成型工艺

第三节 注射成型工艺
三、注射成型工艺条件
1 温度 (1) 料筒温度:最适合温度为黏流态温度,但必须低于分解温度
(前高后低)
(2) 喷嘴温度:低于料筒的最高温度
(3) 模具温度:低于玻璃态温度 提问:如果模具温度过高,会怎么样? 如果模具温度过低,会怎么样?
第三节 注射成型工艺
三、注射成型工艺条件
2 压力 (1) 塑化压力(背压):在塑料熔融、塑化过程中,熔融塑料
不断向螺杆前端运动,且越来越多,逐渐形成一个压力使 螺杆向后退,为阻止螺杆后退过快,确保熔料均匀压实, 需给螺杆一个反方向的压力,称背压。
(2) 注射压力:指螺杆头部在注射时对塑料熔体施加的压力。
第三节 注射成型工艺
注射成型原理:注射成型是在一定的条件(温度、压力、时间) 下,借助于注射机和注射模将塑料原料加工成有一定精度、 力学性能的塑料产品的过程。
注射成型过程包括: 塑化过程
注射过程
保压过程
第三节 注射成型工艺
注射成型工艺特点: 优点:1 周期短、效率高
2 外形复杂、高精度件可一次成型,可以带嵌件 3 适应性强,热塑性或热固性塑料均可 4 自动化程度高
第三节 注射成型工艺
三、注射成型工艺条件
3 时间(成型周期) 成型周期=注射时间+模内冷却时间+辅助时间
(1) 注射时间=充模时间+保压时间 (2)模内冷却时间略大于塑化时间 (3)辅助时间包括开模、脱模、喷脱模剂、放嵌件、合模等时间
思考题: 如果充模时间10秒,保压时间20秒,冷却时间20秒,辅助 时间5秒,计算该制件的成型时间。