基础知识 存储器产品制造工艺概要
IC基础知识及制造工艺流程
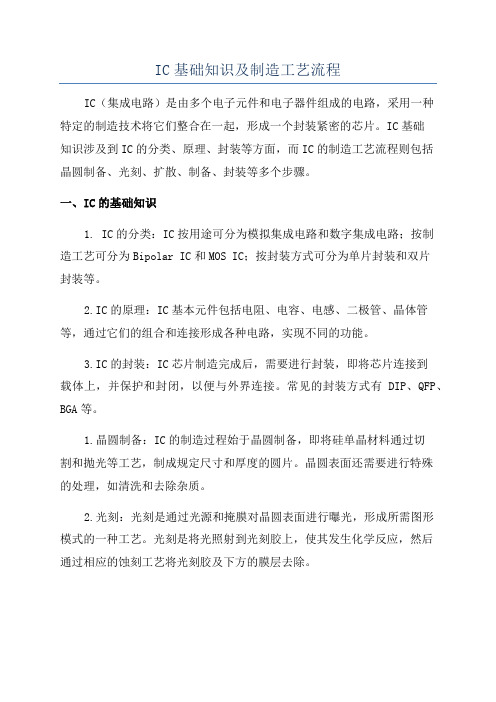
IC基础知识及制造工艺流程IC(集成电路)是由多个电子元件和电子器件组成的电路,采用一种特定的制造技术将它们整合在一起,形成一个封装紧密的芯片。
IC基础知识涉及到IC的分类、原理、封装等方面,而IC的制造工艺流程则包括晶圆制备、光刻、扩散、制备、封装等多个步骤。
一、IC的基础知识1. IC的分类:IC按用途可分为模拟集成电路和数字集成电路;按制造工艺可分为Bipolar IC和MOS IC;按封装方式可分为单片封装和双片封装等。
2.IC的原理:IC基本元件包括电阻、电容、电感、二极管、晶体管等,通过它们的组合和连接形成各种电路,实现不同的功能。
3.IC的封装:IC芯片制造完成后,需要进行封装,即将芯片连接到载体上,并保护和封闭,以便与外界连接。
常见的封装方式有DIP、QFP、BGA等。
1.晶圆制备:IC的制造过程始于晶圆制备,即将硅单晶材料通过切割和抛光等工艺,制成规定尺寸和厚度的圆片。
晶圆表面还需要进行特殊的处理,如清洗和去除杂质。
2.光刻:光刻是通过光源和掩膜对晶圆表面进行曝光,形成所需图形模式的一种工艺。
光刻是将光照射到光刻胶上,使其发生化学反应,然后通过相应的蚀刻工艺将光刻胶及下方的膜层去除。
3.扩散:扩散是将所需的杂质原子(如硼、磷等)掺入晶圆内部,形成p区和n区,以便实现PN结的形成。
扩散过程需要在高温条件下进行,使杂质原子能够在晶格中扩散。
4.制备:制备过程是将晶圆表面的绝缘层开孔,形成连接电路,然后通过金属线或导线连接各个元件。
制备步骤包括物理蚀刻、金属蒸镀、光刻等。
5.封装:IC芯片制造完成后,需要进行封装,将芯片连接到载体上,并保护和封闭。
封装工艺包括焊接引脚、防尘、封胶等步骤。
6.测试:IC制造完成后,需要进行各种电性能和可靠性测试,以确保芯片的质量和功能。
测试内容包括电流、电压、频率等方面的测试。
在IC制造的过程中,上述步骤是不断重复的,每一次重复都会在前一步骤的基础上进行,逐渐形成多层结构,最终形成完整的IC芯片。
制造工艺基础
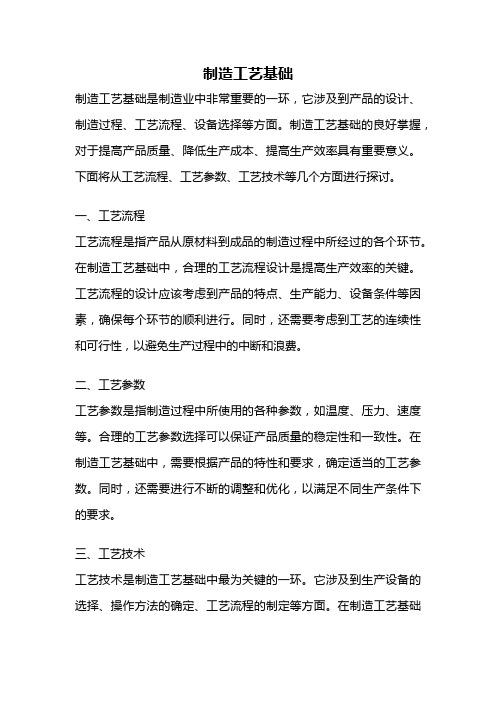
制造工艺基础制造工艺基础是制造业中非常重要的一环,它涉及到产品的设计、制造过程、工艺流程、设备选择等方面。
制造工艺基础的良好掌握,对于提高产品质量、降低生产成本、提高生产效率具有重要意义。
下面将从工艺流程、工艺参数、工艺技术等几个方面进行探讨。
一、工艺流程工艺流程是指产品从原材料到成品的制造过程中所经过的各个环节。
在制造工艺基础中,合理的工艺流程设计是提高生产效率的关键。
工艺流程的设计应该考虑到产品的特点、生产能力、设备条件等因素,确保每个环节的顺利进行。
同时,还需要考虑到工艺的连续性和可行性,以避免生产过程中的中断和浪费。
二、工艺参数工艺参数是指制造过程中所使用的各种参数,如温度、压力、速度等。
合理的工艺参数选择可以保证产品质量的稳定性和一致性。
在制造工艺基础中,需要根据产品的特性和要求,确定适当的工艺参数。
同时,还需要进行不断的调整和优化,以满足不同生产条件下的要求。
三、工艺技术工艺技术是制造工艺基础中最为关键的一环。
它涉及到生产设备的选择、操作方法的确定、工艺流程的制定等方面。
在制造工艺基础中,需要掌握各种工艺技术,同时还需要不断地学习和更新。
只有不断地提高自己的工艺技术水平,才能适应不断变化的市场需求和生产环境。
四、工艺改进随着科技的进步和市场的发展,制造工艺也在不断地改进和创新。
工艺改进可以通过提高产品的质量、降低生产成本、提高生产效率等方面来实现。
在制造工艺基础中,需要注重工艺改进的研究和实践。
只有不断地进行工艺改进,才能保持竞争优势,适应市场的需求。
总结起来,制造工艺基础是制造业中必不可少的一部分。
它对于产品质量、生产效率、生产成本等方面都有着重要的影响。
只有在工艺流程、工艺参数、工艺技术等方面做好基础工作,才能提高制造业的竞争力,实现可持续发展。
因此,我们应该重视制造工艺基础的学习和实践,不断提高自己的工艺水平。
只有这样,才能在激烈的市场竞争中立于不败之地。
了解计算机硬件的制造工艺
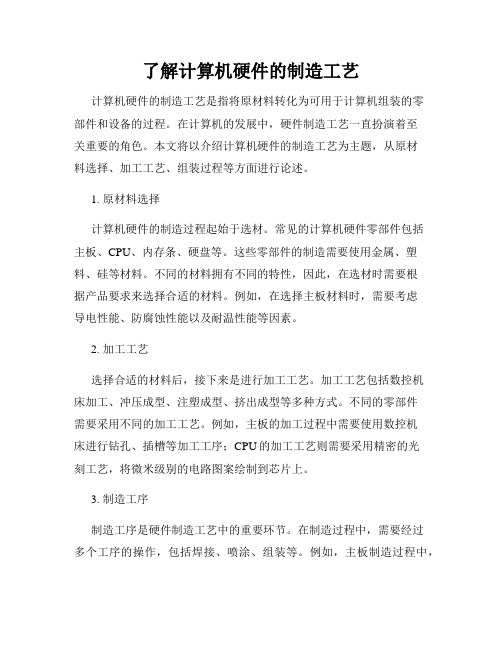
了解计算机硬件的制造工艺计算机硬件的制造工艺是指将原材料转化为可用于计算机组装的零部件和设备的过程。
在计算机的发展中,硬件制造工艺一直扮演着至关重要的角色。
本文将以介绍计算机硬件的制造工艺为主题,从原材料选择、加工工艺、组装过程等方面进行论述。
1. 原材料选择计算机硬件的制造过程起始于选材。
常见的计算机硬件零部件包括主板、CPU、内存条、硬盘等。
这些零部件的制造需要使用金属、塑料、硅等材料。
不同的材料拥有不同的特性,因此,在选材时需要根据产品要求来选择合适的材料。
例如,在选择主板材料时,需要考虑导电性能、防腐蚀性能以及耐温性能等因素。
2. 加工工艺选择合适的材料后,接下来是进行加工工艺。
加工工艺包括数控机床加工、冲压成型、注塑成型、挤出成型等多种方式。
不同的零部件需要采用不同的加工工艺。
例如,主板的加工过程中需要使用数控机床进行钻孔、插槽等加工工序;CPU的加工工艺则需要采用精密的光刻工艺,将微米级别的电路图案绘制到芯片上。
3. 制造工序制造工序是硬件制造工艺中的重要环节。
在制造过程中,需要经过多个工序的操作,包括焊接、喷涂、组装等。
例如,主板制造过程中,需要进行焊接工序,将电子元件与主板连接;硬盘的制造过程则需要进行喷涂工序,以提高硬盘的抗腐蚀性能。
4. 质量检测在硬件制造过程中,质量检测是不可或缺的环节。
质量检测可以通过人工检测和自动化测试设备进行。
人工检测可以通过目视检查进行,检查是否存在瑕疵或错误。
自动化测试设备可以进行电气性能测试、故障检测等。
在质量检测过程中,需要对硬件零部件进行逐一检查,确保产品的质量符合标准。
5. 组装过程组装是硬件制造工艺的最后一个环节。
在组装过程中,需要将各个零部件按照设计要求进行组装,形成最终的计算机产品。
组装过程需要注意连接的可靠性、组件的匹配性以及产品的外观。
组装完成后,还需要进行功能测试,确保计算机硬件的正常运行。
总结:计算机硬件的制造工艺涉及到原材料选择、加工工艺、制造工序、质量检测和组装过程等方面。
半导体存储器件及其制造方法
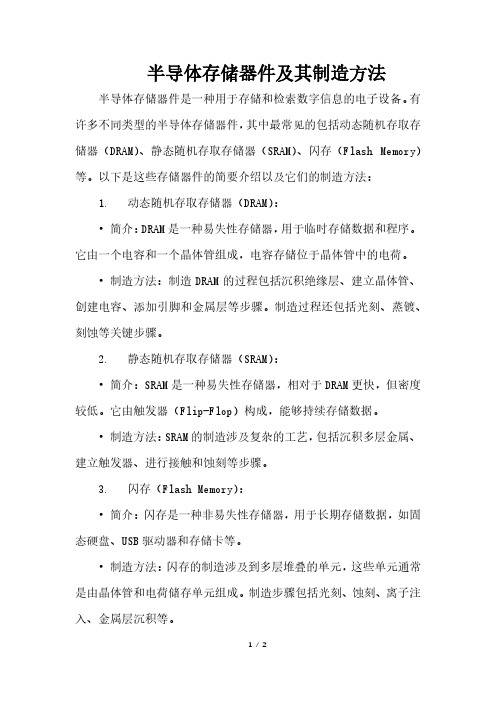
半导体存储器件及其制造方法半导体存储器件是一种用于存储和检索数字信息的电子设备。
有许多不同类型的半导体存储器件,其中最常见的包括动态随机存取存储器(DRAM)、静态随机存取存储器(SRAM)、闪存(Flash Memory)等。
以下是这些存储器件的简要介绍以及它们的制造方法:1. 动态随机存取存储器(DRAM):•简介:DRAM是一种易失性存储器,用于临时存储数据和程序。
它由一个电容和一个晶体管组成,电容存储位于晶体管中的电荷。
•制造方法:制造DRAM的过程包括沉积绝缘层、建立晶体管、创建电容、添加引脚和金属层等步骤。
制造过程还包括光刻、蒸镀、刻蚀等关键步骤。
2. 静态随机存取存储器(SRAM):•简介:SRAM是一种易失性存储器,相对于DRAM更快,但密度较低。
它由触发器(Flip-Flop)构成,能够持续存储数据。
•制造方法:SRAM的制造涉及复杂的工艺,包括沉积多层金属、建立触发器、进行接触和蚀刻等步骤。
3. 闪存(Flash Memory):•简介:闪存是一种非易失性存储器,用于长期存储数据,如固态硬盘、USB驱动器和存储卡等。
•制造方法:闪存的制造涉及到多层堆叠的单元,这些单元通常是由晶体管和电荷储存单元组成。
制造步骤包括光刻、蚀刻、离子注入、金属层沉积等。
4. 存储器的3D堆叠技术:•简介:为了增加存储密度,现代存储器制造趋向于使用3D堆叠技术,允许多个存储层叠加在一起,而不是仅仅在一个平面上布置。
•制造方法:3D堆叠技术的制造包括垂直集成和多层互连的复杂过程,如通过先进的封装技术和纳米加工技术实现。
这些存储器器件的制造方法涉及到先进的半导体工艺技术,包括光刻、蚀刻、离子注入、金属沉积、化学机械抛光等步骤。
这些技术的不断发展推动着存储器件的性能提升和制造成本的降低。
《DRAM制造工艺》课件

薄膜沉积技术
薄膜沉积技术用于在芯片上沉 积薄膜材料,包括化学气相沉 积(CVD)和物理气相沉积(PVD) 等方法。
纳米制造技术
随着DRAM存储容量的不断增 加,纳米制造技术成为实现高 集成度和小尺寸的关键技术。
四、DRAM产业现状及发展趋势
DRAM行业现状
全球DRAM市场规模庞大, 主要由少数大型制造商垄断, 但也存在着激烈的竞争。
《DRAM制造工艺》PPT 课件
# DRAM制造工艺
一、DRAM简介
DRAM的定义
动态随机存取存储器(DRAM) 是一种基于电容的半导体存 储器,用于在计算机和其他 电子设备中临时存储数据。
DRAM的种类
常见的DRAM种类有SDRAM、 DDR、DDR2、DDR3和 DDR4等,每一代都有提高 存储容量和速度的改进。
DRAM的特点
DRAM具有高集成度、低功 耗、易于扩展等特点,是计 算机存储系统中的核心组件。
二、DRAM的制造工艺
DRAM制造工艺涉及多个步骤,包括前处理、晶圆制造、晶圆测试、芯片刻 蚀、挖孔、金属沉积、金属刻蚀和重复层叠等。
三、DRAM制造工艺中的关键技术
光刻技术
光刻技术是制造DRAM中非常 关键的步骤,用于在芯片表面 上形成复杂的电路结构。
2
DRAM制造工艺的未来趋势
未来DRAM制造工艺将更加注重提高存储密度、降低功耗和增强性能。3源自DRAM制造工艺的应用前景
DRAM作为计算机存储的重要组成部分,在未来的科技发展中将发挥越来越重要 的作用。
DRAM产业链分析
DRAM产业链包括芯片制造 厂商、封装测试厂商、模块 厂商和品牌厂商等环节。
DRAM产业发展趋势
随着人工智能、物联网和云 计算等技术的兴起,DRAM 产业将面临新的发展机遇。
半导体 存储 生产工艺

半导体存储器生产工艺一、半导体材料准备半导体存储器的制造需要使用高纯度的半导体材料,包括硅、锗等。
这些材料需要在生产前进行准备和检验,以确保其质量和纯度。
二、芯片设计芯片设计是制造存储器的重要环节,包括电路设计、版图设计、性能测试等步骤。
设计过程中需要考虑存储器的容量、速度、功耗等多种因素。
三、芯片制造芯片制造是将设计好的芯片通过光刻、刻蚀、薄膜制备、掺杂等工艺,在半导体衬底上加工出所需的电路和结构。
制造过程中需要严格控制温度、湿度、压力等参数,以确保芯片的质量和性能。
四、封装测试封装测试是将制造好的芯片进行封装、焊接、引线、测试等操作,以确保芯片能够正常工作。
封装过程中需要注意保护芯片的电路和结构,防止机械损伤和电气故障。
测试过程中需要对芯片的逻辑功能、电学性能、可靠性等进行检测和评估。
五、成品检测与标识成品检测与标识是对生产出来的存储器进行检测和标识,以确保产品的质量和性能符合要求。
检测内容包括外观检测、性能测试、可靠性测试等,标识内容包括产品型号、容量、生产日期等。
六、成品包装与配送成品包装与配送是将检测合格的存储器进行包装,以保护产品在运输过程中不受损伤,并按照客户的需求进行配送。
包装内容包括防震缓冲材料、防水防潮保护等,配送方式包括快递、物流等。
七、生产过程中的质量控制生产过程中的质量控制是保证存储器产品质量的关键环节,包括原材料检验、生产过程控制、成品检测等步骤。
质量控制过程中需要遵循相关标准和规范,对不合格的产品进行追溯和纠正。
八、环境与设备管理环境与设备管理是保障存储器产品质量和生产效率的重要因素。
良好的工作环境可以避免产品受到污染和故障,高效的设备管理可以提高生产效率和降低成本。
具体措施包括保持生产场所的清洁和安全、定期维护和检查设备、及时更换损坏的设备等。
基础工艺知识点总结
基础工艺知识点总结工艺是指用来制作或加工产品的方法和技术。
在制作产品的过程中,工艺起着至关重要的作用。
工艺知识是指对工艺制作过程中所需的技术、设备、原材料等方面的认识和理解。
掌握了工艺知识,我们才能够更加熟练地操作设备,更好地控制制作过程,从而生产出高质量的产品。
基础工艺知识点包括但不限于以下几个方面:一、加工工艺1.工艺流程:加工的每一个环节都要有相应的工艺流程,需要按照流程依次进行,不能随意更改。
比如,金属加工的工艺流程包括:锻造、铸造、焊接、热处理等,每个工艺都有其特定的流程。
2.加工方法:加工方法包括了机械加工、焊接、冷热处理、三坐标测量等多种形式的技术手段。
3.数控加工:数控加工是指利用计算机控制机床进行自动化加工的方式,广泛应用于零部件的制作,可以提高生产效率和产品质量。
4.车削、铣削、冲压等工艺:这些是常用的金属加工工艺,要熟练掌握相关设备的操作和编程。
5.注塑、压铸、挤压等工艺:这些是塑料、铝合金等非金属材料的加工工艺,需要对模具和设备有一定的了解。
二、焊接工艺1.焊接方式:焊接方式包括电弧焊、气体保护焊、电阻焊等多种方式,需要根据材料的种类和要求来选择合适的焊接方式。
2.焊接材料:焊接所用的材料包括焊丝、焊剂、焊条等,需要根据具体需求和工件材料来选择合适的焊接材料。
3.焊接参数:焊接参数包括焊接电流、电压、焊接速度、焊接时间等,不同的材料和焊接方式需要设置不同的焊接参数。
4.焊接质量控制:焊接后需要对焊缝进行质量检验,包括外观检查、探伤、X射线检测等多种方式。
5.焊接工艺优化:根据不同的材料和要求,需要对焊接工艺进行优化,以提高焊接质量和效率。
三、模具制造工艺1.模具设计:模具设计需要考虑到产品的形状、尺寸、材料等多个因素,需要有一定的设计能力和经验。
2.模具加工:模具制造需要用到车床、铣床、线切割机、电火花机等设备,需要熟练掌握这些设备的操作。
3.模具材料:模具材料需要具备一定的硬度、抗压性、耐磨性等特性,需要选择合适的模具材料。
《DRAM制造工艺》课件
这些设备具有高精度和高效率的特点,能够实现大规模和连续生产,是 DRAM制造工艺中的重要组成部分。
03
设备维护
为了确保设备的稳定性和使用寿命,需要进行定期的维护和保养,包括
清洁、检查和更换易损件等。
制造材料介绍
制造材料
DRAM制造过程中需要使用到各种材 料,如硅片、金属、绝缘材料等。这 些材料的质量和纯度对DRAM的性能 和可靠性有着至关重要的影响。
加强环保措施
引入环保技术和设备,减少废弃物排放,加 强废弃物处理和循环利用。
05
DRAM制造技术的发展 趋势
当前技术的发展状况
3D堆叠技术
通过垂直堆叠存储单元,提高存储密度。
嵌入式DRAM技术
将DRAM集成到逻辑芯片中,提高集成度和性 能。
新型存储器技术
如FeRAM、MRAM等,作为下一代存储器技术,具有高速、低功耗等优点。
技术发展对DRAM产业的影响
促进产业升级
技术进步将推动DRAM产业不断升级,提高产业整体 竞争力。
降低成本
技术进步将降低DRAM的制造成本,使更多人能够享 受到高性能、大容量的存储产品。
拓展应用领域
随着技术的进步,DRAM的应用领域将进一步拓展, 如人工智能、物联网等领域。
DRAM的应用领域
总结词
计算机内存、图形处理、数据处理等
详细描述
DRAM广泛应用于计算机内存、图形处理、数据处理等领域,作为主内存或显存 ,提供快速的数据读写速度。
DRAM的发展历程
总结词
从20世纪70年代至今的发展历程
详细描述
DRAM的发展历程可以分为几个阶段,包括256K、1M、4M、16M、64M、256M、1G、2G、4G等不同容量 和速度的DRAM产品,随着技术的不断进步,未来还将有更高容量的DRAM出现。
内存卡生产工艺
内存卡生产工艺内存卡是一种用于存储数据的电子设备,也被称为存储卡、闪存卡或者闪存卡片。
内存卡的生产工艺是指将原材料加工成成品的过程,涉及到多个步骤和工艺流程。
1. 材料准备:内存卡的主要材料是塑料、金属、电子元件和闪存芯片等。
在生产之前,需要准备好所需的所有材料。
2. 固化剂混合:将塑料原料与固化剂进行混合,形成固化剂溶液。
固化剂的主要作用是增强塑料材料的硬度和耐磨性。
3. 塑料注塑:将固化剂溶液注入注塑机中,经过高温加热后,将塑料材料注入模具中形成内存卡的外壳。
注塑是内存卡生产的重要步骤,注塑机的控制精度直接影响着内存卡的质量。
4. 金属加工:将金属材料加工成内存卡的接口部分,如USB接口或SD卡接口。
这包括金属的切削、折弯、冲压等工艺。
5. 电路板组装:将电子元件按照设计要求进行布局,然后进行焊接固定,形成电路板。
电路板是内存卡的核心部件,包括控制芯片、存储芯片、电容器、电阻等。
6. 芯片焊接:将闪存芯片通过焊接工艺固定在电路板上,形成内存卡的存储单元。
焊接工艺要求焊点的牢固性和电气连接的可靠性。
7. 测试与质检:对生产好的内存卡进行功能性测试和质量检查,确保内存卡的正常使用和质量可靠。
8. 组件组装:将内存卡的外壳、电路板和其他组件进行组装,形成完整的内存卡产品。
9. 产品包装:对内存卡进行产品包装,包括塑料包装、纸盒包装、气泡袋包装等。
10. 成品检验:对包装好的内存卡进行最终的检验,确保产品符合质量标准和规定要求。
以上是内存卡的生产工艺的主要步骤,不同厂商及产品可能会有一些差异。
内存卡的生产工艺要求工艺熟练,技术要求高,以确保内存卡产品的品质和性能。
存储器芯片封装技术详解
存储器芯片封装技术详解2022/4/23存储器想必大家已经非常熟悉了,大到物联网服务器终端,小到我们日常应用的手机、电脑等电子设备,都离不开它。
作为计算机的“记忆”装置,其主要功能是存放程序和数据。
一般来说,存储器可分为两类:易失性存储器和非易失性存储器。
其中,“易失性存储器”是指断电以后,内存信息流失的存储器,例如 DRAM(动态随机存取存储器),包括电脑中的内存条。
而“非失性存储器”是指断电之后,内存信息仍然存在的存储器,主要有 NOR Flash 和 NANDFlash 两种。
存储器的发展趋势存储器作为电子元器件的重要组成部分,在半导体产品中占有很大比例。
根据IC Insights 统计,即使全球市场持续受到 COVID-19 的影响,存储产品的年增长率仍将突破 12%,达到 124.1B$,并且在数据中心和云服务器应用上发展巨大。
根据其预测,在不久的将来,存储的需求将保持 10.8% 的增长率,同时均价也将以 7.3% 的年增长率逐年上升,将成为芯片行业最大增长点之一。
虽然,大众普遍对于存储器已有初步认知,但对于其制造流程还是不甚了解。
根据产业链划分,存储器制造流程的核心环节主要包括四个部分,即 IC 设计、芯片制造、芯片封装、成品测试。
其中芯片封装与成品测试属于芯片制造的最后环节,也是决定着产品是否成功的关键步骤。
长电科技具备核心封测技术和自 2004 年以来的大量生产经验,能有效把控存储封装良品率,助力存储产品迅速发展。
目前全球存储器封装技术几经变迁,封装工艺逐渐由双列直插的通孔插装型转向表面贴装的封装形式,其中先进的封装技术是发展主流,包括晶圆级封装(WLP)、三维封装(3DP)和系统级封装(SiP)等。
存储器和终端厂商在成本允许的条件下,采用先进封装技术能够提升存储性能,以适应新一代高频、高速、大容量存储芯片的需求。
长电解决方案迎击挑战存储器的封装工艺制程主要分为圆片超薄磨划、堆叠装片、打线、后段封装几个环节。
- 1、下载文档前请自行甄别文档内容的完整性,平台不提供额外的编辑、内容补充、找答案等附加服务。
- 2、"仅部分预览"的文档,不可在线预览部分如存在完整性等问题,可反馈申请退款(可完整预览的文档不适用该条件!)。
- 3、如文档侵犯您的权益,请联系客服反馈,我们会尽快为您处理(人工客服工作时间:9:00-18:30)。
1.4 CVD(Chemical Vapor Deposition) 化学气相沉积 化学气相沉积:利用化学反应法来形成薄膜的成膜技术。主要有硅外延生长法,热CVD法和等离子CVD 法。 1.4.1 硅外延生长法(epitaxial growth)能生长出和单晶衬底的原子排列(A,B,C)同样的单晶薄膜。 1.4.2热CVD法:可分为常压CVD法和低压CVD法(LPCVD)。栅电极的多晶硅通常利用热CVD法,将SiH4或 Si2H6气体热分解(约650c)淀积而成。作为层间绝缘膜TEOS形成的SiO2膜具有台阶侧面部被覆性能好 的优点。而SiH4和PH3、BH3形成的BPSG在高温下有较好的流动性、广泛地被用来制作表面平坦性好的 层间绝缘膜。 1.4.3等离子CVD 等离子CVD可在200c以下淀积形成层间绝缘膜、避免了铝布线后高温制膜对于金属线的损伤。在 集成电路制造的最后一道工序的芯片保护膜的淀积方面得到了广泛地运用。
2.7 Cover 层的形成 为了防止水分及封装对于铝线的损伤,我们在金属层上加以特殊的保护膜。诸如SiON,PSG和SiN 双层膜。由于封装所采用的塑料和保护膜具有不同的膨胀率,为了防止由此所带来的龟裂,我们再 在保护膜之上覆以树脂予以隔离保护。
最后为了便于以后的的封装和测试,产品需进行背面减薄。一般可以在(180um-480um)范围内实 施减薄。
2.4 源漏栅的形成 2.4.1在讲源漏栅的形成之前有必要说一下阈值电压的如何控制。我们通过向基板注入杂质 的方法来控制阈值电压Vt,我们以提高B的注入量来提高n腔Vt,反之以注入P或As来降低Vt。而 对于P腔晶体管Vt的控制则以增加P或As的注入量来提高Vt,增加B的注入量来降低Vt。 2.4.2在栅极氧化膜形成后,我们在基板上用CVD的方法淀积无掺杂多晶硅,为了降低阻 抗我们通常再加以P的热扩散。在接下来的栅电极光刻和干刻工艺之后形成栅极,最后n腔领域 注入As,p腔领域注入BF2+,随后的热扩散在0.3um厚度区域内形成源(source)和漏(Drain),其 浓度约为10E20/cm3。
2.5 存储单元的形成 我们在这一节中以stack型电容单元为例。在晶体管形成之后,我们通过接触孔(Hole)将数 线(digital)和扩散层连接,通过真空蒸溅射法表面淀积Wsi,光刻和干刻之后形成数线。其间我 们在接触孔(Hole)中填入掺有P的多晶硅。随后,是绝缘膜的形成(BPSG)。连接stack电极和扩散 层的容孔和stack多晶硅极图形也将在光刻和干刻后形成。为了提高电容的容量我们考虑以加大 电极表面积的手段,因此,在NEC公司采用了半球状HSG(hemispherical grain)多晶硅来作为电 极材料,使有效增大了1.5到2倍。 stack多晶硅极形成后在其表面生长一层氮化膜并加以氧化, 如此氮化膜和氧化膜共存的2层结构我们称之为容量薄膜。最后,表面覆以容量多晶硅并刻出图 形作为电容的另一电极。
外延生长的原子排列
•1.5 Diffusion 扩散 向半导体中掺杂的方法有扩散法和离子注入法。扩散法是将掺杂气体导入放有硅片的高温炉中, 将杂质扩散到硅片内的一种方法。此方法适用于同时进行多枚硅片的掺杂(批量生产),同时容易获 得高浓度掺杂硅片。杂质扩散有两道工序:预扩散和主扩散。 在集成电路制造工艺中,采用硼(B)作为p型杂质,而用磷(P)作为n型杂质。他们都具有比较高 的固溶度,除此之外,还使用砷(As)和锑(Sb)等扩散系数较小的杂质,这对于不希望产生杂质再分 布的场合是有效的。另外,根据炉芯管所通气体的不同,将有N2参与的热扩散作为一种离子注入后 损伤恢复的退火过程。将有氢气参与的热氧化称作水蒸汽氧化,反之称作干法氧化。 •1.6 Sputter 金属溅射 所谓溅射是用高速粒子(如氩离子等)撞击固体表面,将固体表面的原子撞击出来。利用这一 现象来形成薄膜的技术。即使等离子体中的离子加速,撞击原料靶材,将撞击出的靶材原子淀积到 对面的基片表面形成薄膜。溅射法与真空蒸发法相比有以下的特点:台阶部分的被覆性好,可形成大 面积的均质薄膜,可获得和化合物靶材同一成分的薄膜,可获得良好的密接性能。因而,电极和布 线用的铝合金(Al-Si,Al-Si-Cu)等都是利用溅射法形成的。最常用的溅射法是在平行平板电极间接 上高频(13.56MHz)电源,是氩气(压力为1Pa)离子化,在靶材(例如,Al)一侧的电极上加上自偏压, 使离子加速与之撞击。由靶材溅射出来的原子淀积在另一侧电极上的基片上,如图:
2.3 器件隔离 器件隔离由两种方法。即使用pn结来进行隔离的pn结隔离法和利用绝缘物进行隔离的绝缘体隔 离法。绝缘体隔离法通常用二氧化硅作为绝缘体、因而也称该二氧化硅为隔离墙。二氧化硅隔离使 用于器件区域的侧面、器件区域底部的隔离则用pn结隔离来实现。用二氧化硅作为绝缘体的一种比 较成熟的方法是硅的部分氧化工艺LOCOS(local oxidation of Si)如下图。在非绝缘领域覆以氮化 硅,需绝缘领域利用光刻及干刻去除覆盖层,利用氧化速度快的湿法氧化形成厚度为0.5-1um的二氧 化硅隔离墙。这一工艺可以将比较后的二氧化硅膜以半埋入式嵌入基板表面有利于减少表面的台阶 高度。其缺点是氧化反应会潜入氮化膜边缘部分的下面。形成类似鸟的嘴部的形状,常称之为鸟嘴 (bird’s beak)。难以使器件隔离区的宽度小于某一定值。另外,我们常用干法氧化的方法来制成 优质的二氧化硅膜以避免晶体管阈值电压的变化和沟道中载流子迁移率的下降。
SiO2腐蚀断面 RIE刻蚀装置
RIE刻蚀适用反应气体及生成物
1.3 Ion Implant 离子注入 离子注入法通常是将掺入半导体中的杂质在离子源中离子化,然后将通过了质量分析磁极后选定 了的离子进行加速,注入基片中去。杂质的注入量可通过测量流过基片的电流大小来正确地控制。离 子由基片的表面到停止,形成近似的高斯分布。注入时通常采用光刻胶和SiO2作掩膜,掩膜的厚度以 不使杂质穿透为原则,随杂质的种类、加速电压的大小及注入量的不同而异。离子束的注入角度通常 偏离基片法线方向7度左右,以防止发生沟道效应。(离子直接进入基片的深层)。离子注入后,要在 800c-1000c的高温下进行热处理,以使离子注入时产生的结晶晶格损伤得以恢复。
•2产品制造工艺流程概要
2.1 硅基板的选择 2.2 Well的形成 2.3 器件隔离
2.4 源漏栅的形成
2.5 存储单元的形成 2.6 布线技术 2.7 Cover 层的形成
1.1 Photo Lithograph(PR) 光刻 在使用掩膜进行光或X线曝光时,将掩膜图形,或在使用不需要掩膜的电子束曝光时,将数据式 图形复制在半导体硅片表面的光刻胶上,形成光刻胶像。在LSI制造过程中,一般需用20-30道光刻工 序。现在的主流技术都采用紫外线(UV)为光源。 光源有 :水银灯 g线(波长:436nm) I线(波长:365nm)
为提高成膜的速度,通常利用磁场来增加离子的密度,这种装置称为
磁控溅射装置
•2产品制造工艺流程概要
2.1 硅基板的选择 我们为什么采用硅单晶作为集成电路的材料理由: 1)集成电路的基础工艺技术是平面技术,首先将硅表面氧化,然后根据各元器件图形用腐蚀法在二 氧化硅上开设窗口,通过该窗口掺入杂质。多次实施这种平面工艺,在硅片表面形成各种平面的元 器件。这种技术之所以能实施的关键在于:能比较容易地获得适应这些工艺的优质二氧化硅膜。 2)晶体管(特别是MOS晶体管)的特性很大程度上受硅和二氧化硅界面的缺陷、二氧化硅膜中移动电荷 的影响。Si(100)/SiO2界面只有十万分之一的缺陷,用人工的方法是很难获得比此更为优质的界面 的。 3)单晶硅和二氧化硅是由地球上存在数量占第1、2位的氧和硅所构成的。是一种储量大、安全、稳定 和使用方便的工业材料。 2.2 Well的形成 作为CMOS晶体管形成的基台、我们分别在浓度为10E16-10E18、深度为1-5um的基板表面形成 P和N型扩散区域(阱well) 。P型一般采用B、N型采用P。表面经浅层注入后采用高温热处理的方法 将掺杂离子引入基板深层。如图所示。
2.4 源漏栅的形成 2.4.3 在此我想补充说明一下N腔晶体管的LDD(lightly doped drain)构造。为了缓和源漏 极附近的高电位差延长晶体管的使用寿命,在源漏极附近形成浓度为10E17-10E18的n-扩散区域, 如图所示:栅极形成之后为了形成n-区我们进行LDD P注入,而后在栅极两侧以二氧化硅形成侧墙, 之后再进行SD(源漏)的As注入。在此n-,n+分别代表浓度的高低。
激光 KrF (波长:248nm) 波长越短有助于形成更精细的图形。 工艺流程包括以下几个方面: 1.光刻胶的涂覆 2.预烘 3.曝光 4.显影 5.后烘
6.腐蚀(离子注入)
7.光刻胶的Βιβλιοθήκη 除1.2 Etching 腐蚀技术 腐蚀技术是利用化学腐蚀法把材料的某一部分去除的技术。通常,是用光刻工艺形成的光刻胶作 掩膜对下层材料进行腐蚀。 腐蚀技术可分为两大类:湿法腐蚀-进行腐蚀的化学物质是溶液;干法腐蚀(一般称为刻蚀)-进行 刻蚀的物质是气体。 1.2.1湿法腐蚀: 采用溶液进行的湿法腐蚀是一种各向同性腐蚀。如左图,一般适用于非精细图形的 加工。典型的腐蚀液有: SiO2 (缓冲HF液,含NH4F); SiN (H3PO4 180c) ; Al H3PO4+CH3COOH+HNO3) 1.2.2干法腐蚀:干法腐蚀分为各向同性刻蚀和各向异性刻蚀两种。光刻胶去胶装置,氧的等离子体和 光刻胶反应形成H2O和CO2气体,属于各向同性刻蚀。而精细图形的形成是靠纵方向的刻蚀,横方向不 进行刻蚀的各向异性刻蚀法来实现的。如下图的反应型离子刻蚀(RIE:reactive ion etching),利用 离子诱导化学反应进行各向异性刻蚀。
谨以此机会共勉:
爱心、细心、耐心、责任心去建设一流的代工生 产线。
•1 个别工艺介绍
1.1 Photo Lithograph(PR) 光刻 1.2 Etching 腐蚀技术
1.3 Ion Implant 离子注入