齿轮表面淬火硬化层分布形式
齿轮淬火的最佳[1]..(戴忠森)
![齿轮淬火的最佳[1]..(戴忠森)](https://img.taocdn.com/s3/m/6f0fd8f34693daef5ef73da0.png)
齿轮淬火的“最佳”硬化层深与“适当”硬化层深戴忠森众所周知,齿轮的淬硬层深“过浅”,对接触和弯曲承载能力都不利。
但淬硬层也不是越深越好,最佳或适当的硬化层深度,可使齿面和齿根都具有较高的强度(承载能力)。
另外,不同的热处理方法,其“最佳”值也不是一样的。
二十世纪七、八十年代,随着齿轮强度计算方法ISO标准的公布,以及国内GB/3480“圆柱齿轮承载能力计算方法”标准的实施,特别是工业硬齿面齿轮的广泛采用,国内外齿轮工作者(专家、学者),就热处理硬化层深问题,进行了大量的试验研究和理论分析。
其实质都是基于接触(弯曲)疲劳强度,其核心问题是:疲劳裂纹发生(萌生)在何处?破坏后的形状是点蚀(pitting贝壳状),还是片蚀(剥落spalling)?研究表明,一般软齿面大多是点蚀,而硬齿面大齿轮大多是剥落(片蚀)。
疲劳裂纹的萌生,有可能在表面,也有可能在表层。
至今,有关硬齿面齿轮接触疲劳强度(剥落)计算的理论和方法,主要有:最大剪切应);正交剪切应力(τyz);当量剪切应力(τeffa);深部接触应力;最大剪切力τmax(τ45°应力/剪切强度的峰值;正交剪切应力/强度(硬度)(τyz/HV)max;当量剪切应力/强度的峰值等,通过理论计算可以确定接触疲劳强度(安全系数);或者确定最佳淬硬层深度。
这些理论和方法一直都有争议,因此至今也没有一个权威的理论和方法被大家所能完全接受。
所谓“最佳硬化层深”,其说法也是较含糊的,而且众说不一,以渗碳淬火齿轮为例,德国DIN3990,硬化(渗碳)层深度,给出一个经验公式:(推荐)Eht= 0.15m n(m n——法面模数)(1)。
该经验公式,有一个突出的问题,就是未考虑实际载荷的情况。
所以,对于轻载齿轮,允许比经验公式稍浅的硬化层深度。
Thomas Tobie近年来提出在用ISO/DIN 进行标准化承载能力计算时,考虑硬化层深度对承载能力的影响,引入了影响系数Z Eht(接触承载能力影响系数);УEht(弯曲承载能力影响系数)。
感应淬火全齿宽硬化工艺你了解多少?
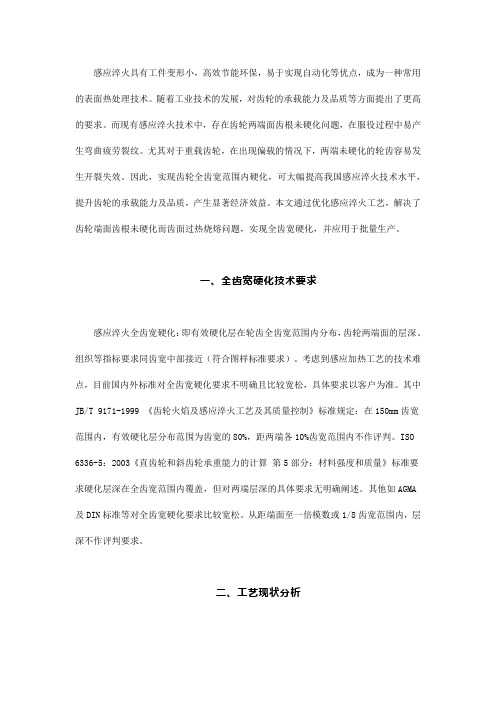
感应淬火具有工件变形小,高效节能环保,易于实现自动化等优点,成为一种常用的表面热处理技术。
随着工业技术的发展,对齿轮的承载能力及品质等方面提出了更高的要求。
而现有感应淬火技术中,存在齿轮两端面齿根未硬化问题,在服役过程中易产生弯曲疲劳裂纹。
尤其对于重载齿轮,在出现偏载的情况下,两端未硬化的轮齿容易发生开裂失效。
因此,实现齿轮全齿宽范围内硬化,可大幅提高我国感应淬火技术水平,提升齿轮的承载能力及品质,产生显著经济效益。
本文通过优化感应淬火工艺,解决了齿轮端面齿根未硬化而齿面过热烧熔问题,实现全齿宽硬化,并应用于批量生产。
一、全齿宽硬化技术要求感应淬火全齿宽硬化:即有效硬化层在轮齿全齿宽范围内分布,齿轮两端面的层深、组织等指标要求同齿宽中部接近(符合图样标准要求)。
考虑到感应加热工艺的技术难点,目前国内外标准对全齿宽硬化要求不明确且比较宽松,具体要求以客户为准。
其中JB/T 9171-1999 《齿轮火焰及感应淬火工艺及其质量控制》标准规定:在150mm齿宽范围内,有效硬化层分布范围为齿宽的80%,距两端各10%齿宽范围内不作评判。
ISO 6336-5:2003《直齿轮和斜齿轮承重能力的计算第5部分:材料强度和质量》标准要求硬化层深在全齿宽范围内覆盖,但对两端层深的具体要求无明确阐述。
其他如AGMA 及DIN标准等对全齿宽硬化要求比较宽松。
从距端面至一倍模数或1/8齿宽范围内,层深不作评判要求。
二、工艺现状分析感应淬火工艺的问题点包括:尖角处涡流集中加热温度高,而内圆角不易加热等。
因此,齿轮在感应加热过程中易出现端部齿面尖角过热烧熔,而内圆角位置的齿根未硬化或硬化层深不足问题,如图1所示。
由于国内外标准对端面的硬化层深要求比较宽松,通常采取降低加热功率方法,防止齿轮出现端面烧熔这一明显的外观质量缺陷,而忽略了端面齿根硬化层深严重偏浅或未硬化的质量隐患。
降低了齿轮的承载能力及品质,存在早期失效风险。
针对该问题,本文通过设计新型感应器结构及调整工艺参数,对感应淬火工艺进行了优化。
硬齿面齿轮常用热处理方式

硬齿面齿轮常用热处理方式概述硬齿面齿轮是一种常见的机械传动元件,用于传递动力和扭矩。
为了提高其硬度和耐磨性,常常需要进行热处理。
本文将介绍硬齿面齿轮常用的热处理方式,包括淬火、渗碳、氮化等。
1. 淬火(Quenching)淬火是一种通过快速冷却来改变材料的组织结构和性能的方法。
对于硬齿面齿轮来说,淬火可以提高其硬度和强度,增加其耐磨性和使用寿命。
淬火过程中,首先将齿轮加热至适当的温度,使其达到奥氏体组织。
然后迅速将其浸入冷却介质中,如水或油中,以快速降低温度。
这样可以使奥氏体转变为马氏体组织,并产生较高的硬度。
2. 渗碳(Carburizing)渗碳是一种通过在材料表面添加富含碳元素的材料层来增加表面硬度和耐磨性的方法。
对于硬齿面齿轮来说,渗碳可以提高其表面硬度,增加其抗磨损能力。
渗碳过程中,首先将齿轮放置在含有富含碳元素的固体、液体或气体环境中。
通过加热和保持一定时间,使碳元素渗透到齿轮表面,并与基体材料发生化学反应。
这样可以形成一层富含碳元素的淬火层,提高齿轮的硬度。
3. 氮化(Nitriding)氮化是一种通过在材料表面添加氮元素来提高硬度和耐磨性的方法。
对于硬齿面齿轮来说,氮化可以增加其表面硬度,改善其抗疲劳性能。
氮化过程中,首先将齿轮放置在富含氨气的环境中。
通过加热和保持一定时间,使氨气分解并释放出氮原子。
这些氮原子会渗透到齿轮表面,并与基体材料发生化学反应。
这样可以形成一层富含氮元素的淬火层,提高齿轮的硬度。
4. 碳氮共渗(Carbonitriding)碳氮共渗是一种通过在材料表面同时添加碳和氮元素来提高硬度和耐磨性的方法。
对于硬齿面齿轮来说,碳氮共渗可以增加其表面硬度,并改善其抗疲劳性能和韧性。
碳氮共渗过程中,首先将齿轮放置在含有富含碳和氮元素的固体、液体或气体环境中。
通过加热和保持一定时间,使碳和氮元素渗透到齿轮表面,并与基体材料发生化学反应。
这样可以形成一层富含碳和氮元素的淬火层,提高齿轮的硬度。
谈齿轮渗碳淬火有效硬化层及硬度梯度

浅谈齿轮渗碳淬火有效硬化层及硬度梯度随着机械工业的发展,对齿轮的质量要求日益提高,而齿轮的强度寿命和制造精度与热处理质量有很大关系。
为了检验齿轮材料热处理质量,在1987年以前,我国的齿轮渗碳淬火内在质量检验标准多为终态金相检验标准。
由于检测仪器的精度、分辨率等因素以及检验人员的经验参差不齐,造成检验结果有很大差异和争议。
为了解决金相法内在检验存在的弊端,机械部在1987年借鉴了DIN.ISO等标准中有关内容,修订了我国现行齿轮渗碳淬火内在质量检验标准。
此检验标准中,其金相组织检验标准基本与原标准相似,主要是对渗碳层深度及碳浓度梯度的测定作了较大的修改。
下面就渗碳层深度和碳浓度梯度分别采用金相法与硬度法测定进行简述。
一、渗碳层深度的检测1.1、金相法1.1.1、取本体或与零件材料成分相同,预先热处理状态基本相似的圆试样或齿形试样进行检测。
1.1.2、送检试样热处理状态为平衡状态,即退火状态。
1.1.3、低碳钢渗层深度为:过共析层+共析层+1/2亚共析层。
1.1.4、低碳合金钢渗层深度为:过共析层+共析层+亚共析层。
1.2、硬度法1.2.1、取样方法同金相法取样方法一致。
1.2.2、送检试样状态为淬火+回火状态。
1.2.3、渗碳深度用有效硬化层来表示,其极限硬度根据不同要求进行选择。
1.2.4、有效硬化层深度(DCp):从试样表面测至极限硬度(如HV550)之间垂直距离。
1.3、两种关于渗碳深度检测的方法存在着一定的对应关系,下面用图形来描述。
从图中可看出:DCp(芯部)>DCp(HV500)>DCp(HV550)DCp(HV550)对应渗碳层中碳含量约为0.35~0.38%,此界限处即为金相法中1/2亚共析层处。
DCp(HV500)对应渗碳层中碳含量约为0.31~0.33%,此界限处为金相法中1/2亚共析层处。
DCp(芯部)对应渗碳层中碳含量为基体碳含量,一般为0.17~0.23%,此界限处为金相法中基体组织。
渗碳淬火齿轮件的硬化层深设计与控制
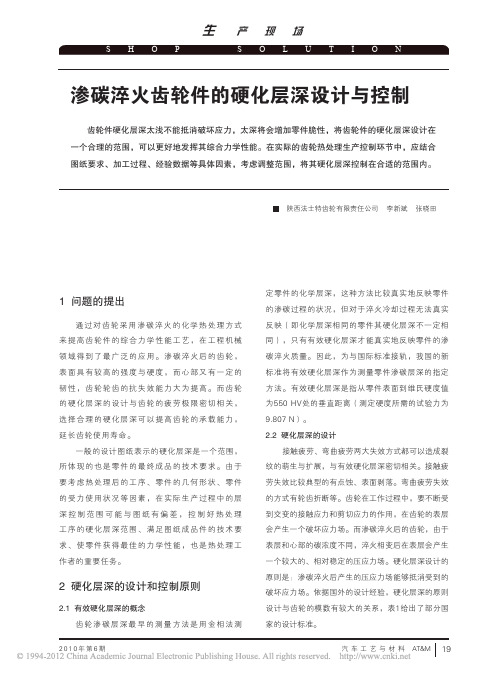
汽 车 工 艺 与 材 料 AT&M 19
生 产现场
SHOP
SOLUTION
表1
国家
美国ANSI/ ACMA2004
美国ANSI/ ACMA2001
英国 BS公司
德国DIN3990
模数/mm 层深/mm
1.45~1.85 0.25~0.50
设计标准
1.85~2.45
2.45~3.00
0.38~0.64
另据资料提供的经验公式也可作为齿轮硬化层深
设max·u )/〔HV·cosβb·(u
±1)2〕
(1)
式中,t 为渗碳层的最小深度,mm;a 为相啮合齿
轮 副 的 公 称 中 心 距 , m m ;α t 为 齿 轮 端 面 啮 合 角 , (°);δ max为最大接触应力,MPa;u 为相啮合 齿轮副齿数比(z 2/z 1);HV为齿面渗碳层的维氏硬 度;βb为基圆螺旋角,(°);小括号中的“+”用 于外啮合,“-”用于内啮合。
2.3 热处理工艺过程对硬化层深的控制
针对热处理渗碳环节,其对硬化层深的控制要综
齿轮齿根的淬硬层深度研究

tse y mir h r n s e tr a a i u a d n d d p h,a d c re p n i g c r e fmi rh r n s S h r e e e t e td b c o a d e st se tv ro s h e e e t r n ors o dn u vso co ad esV . ad n d d ph w r r w e e d a n,b s d o ih t e o eald p h o e h r e e a e o l e e t t d b a so n e i c l o mu a a e n wh c h v r l e t ft a d n d ly rc u d b si e y me n fa mp r a r l . h ma i f
硬齿面齿轮常用热处理方式

硬齿面齿轮常用热处理方式硬齿面齿轮是机械传动中常用的重要零件,其热处理方式对于提高齿轮的强度和耐磨性至关重要。
本文将详细介绍硬齿面齿轮的常用热处理方式。
一、淬火淬火是一种常用的硬化处理方法,其原理是将经过加热后的工件迅速浸入水或油中进行冷却,使其表面形成高硬度、高强度和高耐磨性的硬化层。
淬火适用于碳钢、合金钢等材料制造的硬齿面齿轮。
二、渗碳渗碳是一种将碳元素渗入工件表面形成高碳化层的方法,其原理是在一定温度下,在含有碳元素的气体或液体中进行加热处理。
渗碳可以提高工件表面硬度和耐磨性,适用于低碳钢等材料制造的硬齿面齿轮。
三、氮化氮化是一种将氮元素渗入工件表面形成高氮化层的方法,其原理是在一定温度下,在含有氨气或其他含氮化合物的气体中进行加热处理。
氮化可以提高工件表面硬度、耐磨性和疲劳强度,适用于不锈钢等材料制造的硬齿面齿轮。
四、表面强化表面强化是一种通过机械或物理方法在工件表面形成高硬度、高强度和高耐磨性的处理方法。
常用的表面强化方法包括喷丸、电火花加工、激光加工等。
表面强化可以提高工件表面的力学性能和耐磨性,适用于各种材料制造的硬齿面齿轮。
五、回火回火是一种将淬火后的工件在一定温度下进行加热处理后再进行冷却的方法。
回火可以降低淬火后产生的残余应力,提高工件整体性能和韧性,适用于各种材料制造的硬齿面齿轮。
六、低温淬火低温淬火是一种将经过加热后的工件在较低温度下进行冷却处理的方法,其原理是通过控制淬火温度和时间来控制淬硬层的厚度和硬度。
低温淬火可以提高工件表面的硬度、耐磨性和韧性,适用于各种材料制造的硬齿面齿轮。
七、高温淬火高温淬火是一种将经过加热后的工件在较高温度下进行冷却处理的方法,其原理是通过控制淬火温度和时间来控制淬硬层的厚度和硬度。
高温淬火可以提高工件表面的硬度、耐磨性和韧性,适用于各种材料制造的硬齿面齿轮。
八、总结本文介绍了硬齿面齿轮常用的热处理方式,包括淬火、渗碳、氮化、表面强化、回火、低温淬火和高温淬火等。
齿轮的材料及热处理方法

齿轮的材料及热处理齿轮的材料渗碳硬化钢这是指低碳合金钢。
含碳量为 0.15% ∼ 0.20% 的钢中添加了 Ni,Cr,Mo,Mn 等元素,通过渗碳淬火处理提高表面硬度后使用。
在日本,一般使用的材料如下表所示。
铝青铜铸造合金青铜铸造合金机械结构用碳素钢钢材最为普及的材料,亦是本公司使用最多的材料。
可以施加高频淬火处理。
铬钼钢钢材经过淬火,回火,高频淬火后使用。
淬火对轮齿表面进行硬化处理以提高轮齿强度。
方法有很多,具有代表性的有以下几种。
渗碳淬火渗碳 => 淬火 => 洗净 => 回火 => 喷砂处理 => 检查【方法】一般使用碳酸气进行气体渗碳。
- 表面硬度⋯⋯⋯ 55 - 60HRC- 硬化深度⋯⋯⋯ 1.0 ㎜左右(使用负载越大,硬化层就需越深)低碳合金钢在渗碳环境中加热到转变点以上并保持这个温度,碳素从表面渗入。
碳素渗入后,与 S45C 等在同等条件下进行淬火处理,表面硬度提高。
【特点】由表面到中心部,硬度由硬到软连续变化,所以表面硬而内部富有韧性。
材料一般使用 SCM415 等。
左图 / 渗碳淬火炉右图 / 齿轮的淬火层高频淬火【方法】调质材 => 淬火 => 回火【特点】只有被感应圈所加热的周围产生硬化。
根据形状使用各种不同的感应器,不熟悉的话,会产生裂纹及翘曲变形。
为了防止淬火裂纹,使用含硫,含磷量少的材料。
通常,含碳量在 0.55% 以下的材料产生淬火裂纹的可能性比较小。
材料牌号有 S45C,SCM440 等等。
左图 / 淬火设备右图 / 回火炉。
- 1、下载文档前请自行甄别文档内容的完整性,平台不提供额外的编辑、内容补充、找答案等附加服务。
- 2、"仅部分预览"的文档,不可在线预览部分如存在完整性等问题,可反馈申请退款(可完整预览的文档不适用该条件!)。
- 3、如文档侵犯您的权益,请联系客服反馈,我们会尽快为您处理(人工客服工作时间:9:00-18:30)。
齿轮表面淬火硬化层分布形式
一般情况下,齿轮的表面淬火的分布形式。
强化效果以及应用范围有如下几个方面的内容:
1)回转加热淬火法:齿面耐磨性提高;弯曲疲劳强度没有多大影响,许用弯曲应力低于该钢材调质后的水平;处理齿轮直径由设备功率决定;
2)回转加热淬火法:齿面耐磨性级除根弯曲疲劳强度都得到提高;许用弯曲应力比调质状态提高30%~50%;可部分代替渗碳齿轮;处理齿轮直径由设备功率决定;
3)单齿连续加热淬火法:齿面耐磨性提高;弯曲疲劳强度受一定影响;许用弯曲应力低于该钢材调质后的水平;齿轮直径不受现在限制,齿轮直径不受限制,m≥8。
兆威机电通过在齿轮及齿轮箱领域十二年的专业设计、开发、生产,通过行业的对比及大量的实验测试数据设计开发出微型减速电机,微型减速马达,行星齿轮箱电机,齿轮箱电机,减速齿轮箱电机。