A08M-6.1-02汽车零件渗碳淬火技术条件-有效硬化层深度.tds
感应淬火汽车零件的材料、硬度及硬化层设计探讨

感应淬火汽车零件的材料、硬度及硬化层设计探讨■ 林信智感应淬火的钢号虽然越来越多,但作为结构钢的中碳钢和中碳低合金钢仍是首选材料。
感应淬火零件的表面硬度、硬化层深度和硬化层形状,都与所用材料有关。
而这些技术指标又与零件的力学性能相关联。
一、感应淬火汽车零件的材料选用感应淬火汽车零件常用的材料是中碳钢或中碳低合金钢。
汽车零件生产遵循低成本、高效率原则。
而中碳钢(或中碳低合金钢)是比较廉价的钢材。
感应淬火在各种热处理工艺中又是最节能、最环保、最廉价的热处理工艺方法。
中碳钢零件经感应淬火后又能获得优良的力学性能。
因此,感应淬火的汽车零件定当大量应用中碳钢材料。
1. 感应淬火汽车零件材料(1)曲轴、凸轮轴、钢板销、变速拨叉、摇臂轴、输出凸摘要:介绍了感应淬火汽车零件的材料、淬火硬度和硬化层深度的设计问题,特别是内圆角处硬化层的设计问题。
关键词:感应淬火;汽车;材料;硬化层扫码了解更多缘等多用45钢制造。
(2)轿车转向齿条、转向阀套、输入轴、飞轮齿圈用45钢或40钢制造。
(3)配气系统的推杆、离合器拨叉用35钢或40钢制造。
(4)轿车轮毂轴承的内圈(法兰轴)、外圈和钟形壳(等速万向节)多用55钢或50钢制造。
(5)轮毂轴、花键轴、半轴、转向节、转向输入轴、传动轴凸缘、三销套等用40Cr 、45Cr 钢制造。
(6)重型汽车曲轴、半轴、贯通轴、变速器输出轴用42CrMo 钢制造。
(7)少数轮毂轴承内圈和外圈用滚动轴承钢GCr15或弹簧钢65Mn 制造。
(8)轻型汽车(或轿车)的曲轴、凸轮轴,多用球墨铸铁(QT600—3、QT700—2)制造。
日本许多感应淬火汽车零件用35钢制造,淬火冷却介质为自来水,硬度可达到52~58HRC ,能够满足使用要求,生产管理简化,生产成本降低。
刘宗昌教授曾有论述:低碳钢淬火得到位错型的马氏体,由于位错是可以滑动的,正是这种滑动的位错使马氏体具有一定的塑性,因而断裂韧性较高。
而当w C >0.4%时,马氏体的韧性降低了,变得硬而脆,即使经过低温回火,韧性亦较差。
钢的渗碳硬化深度的检测方法
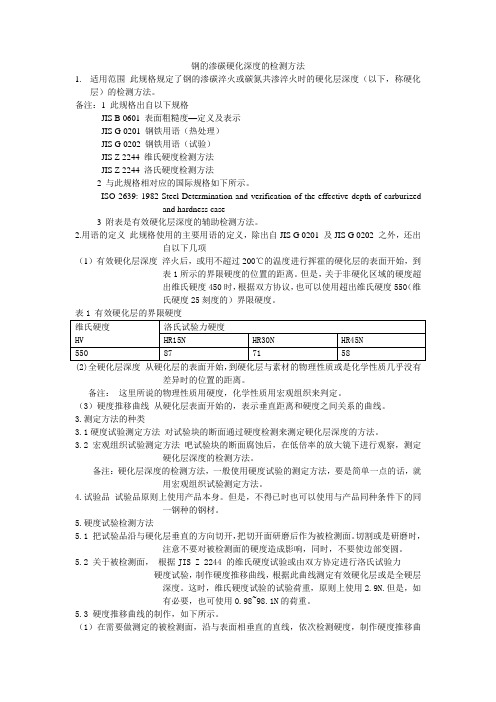
钢的渗碳硬化深度的检测方法1.适用范围此规格规定了钢的渗碳淬火或碳氮共渗淬火时的硬化层深度(以下,称硬化层)的检测方法。
备注:1 此规格出自以下规格JIS B 0601 表面粗糙度—定义及表示JIS G 0201 钢铁用语(热处理)JIS G 0202 钢铁用语(试验)JIS Z 2244 维氏硬度检测方法JIS Z 2244 洛氏硬度检测方法2 与此规格相对应的国际规格如下所示。
ISO 2639: 1982 Steel-Determination and verification of the effective depth of carburizedand hardness case3 附表是有效硬化层深度的辅助检测方法。
2.用语的定义此规格使用的主要用语的定义,除出自JIS G 0201 及JIS G 0202 之外,还出自以下几项(1)有效硬化层深度淬火后,或用不超过200℃的温度进行挥霍的硬化层的表面开始,到表1所示的界限硬度的位置的距离。
但是,关于非硬化区域的硬度超出维氏硬度450时,根据双方协议,也可以使用超出维氏硬度550(维氏硬度25刻度的)界限硬度。
(2)全硬化层深度从硬化层的表面开始,到硬化层与素材的物理性质或是化学性质几乎没有差异时的位置的距离。
备注:这里所说的物理性质用硬度,化学性质用宏观组织来判定。
(3)硬度推移曲线从硬化层表面开始的,表示垂直距离和硬度之间关系的曲线。
3.测定方法的种类3.1硬度试验测定方法对试验块的断面通过硬度检测来测定硬化层深度的方法。
3.2宏观组织试验测定方法吧试验块的断面腐蚀后,在低倍率的放大镜下进行观察,测定硬化层深度的检测方法。
备注:硬化层深度的检测方法,一般使用硬度试验的测定方法,要是简单一点的话,就用宏观组织试验测定方法。
4.试验品试验品原则上使用产品本身。
但是,不得已时也可以使用与产品同种条件下的同一钢种的钢材。
5.硬度试验检测方法5.1 把试验品沿与硬化层垂直的方向切开,把切开面研磨后作为被检测面。
热处理技术条件在零件图上的表示方法

热处理技术条件在零件涂上的表示方法1总则1.1 由效硬化层深度代号为:表面淬火回火——DS;渗碳或碳氮共渗淬火回火——DC;渗氮——DN。
1.2 技术要求中硬度和有效硬化层深度的指标值可用以下三种方法表示:a)一般采用:标出上、下限,如60~65HRC,DC=0.8~1.2;b)也可采用:偏差表示法,如600+5HRC,DC=0.8+0.40;c)特殊情况可只标下限值或上限值,如不小于50HRC,不大于229HRS。
1.3 复杂零件或其它原因技术要求难以标注,文字也难以表达时,则需另绘标注热处理技术要求的图。
2 正火、退火、淬火回火零件2.1 正火、退火、淬火回火零件标注硬度要求一般用布氏硬度(GB/T231)、洛氏硬度(GB/T230)表示,也可以用其它硬度表示。
2.2 局部热处理零件需将有硬化要求的部位在图形上用点划线框处。
轴对称零件或在不致引起误会情况下,也可用一条粗点划线画在热处理部位外侧表示。
3表面淬火零件3.1 表面淬火的表面硬度可用维氏硬度(GB/T4340)、表面洛氏硬度(GB/T1818)、洛氏硬度(GB/T230)表示。
但标准包括两部分:硬度值和相应的试验力。
如620~780HV30。
试验力选取与最小有效硬化层深度有关。
3.2 有效硬化层深度的标注包括三部分:深度代号、界限硬度值和要求的深度。
界限硬度只可根据最低表面硬度值按表选取,特殊情况,也可采用其它商定界限硬度值。
同样需在DS后标明。
如:620~780 HV30 DS500=0.8~1.6 (范围表示法)。
4 渗碳和碳氮共渗零件渗碳和碳氮共渗后淬火回火的零件的表面硬度,通常用维氏硬度或洛氏硬度表示。
对应的最小的有效硬化层深度和试验力与表面淬火零件相同。
其有效硬化层深度DC的表示法与DS基本相同,只是它的界限硬度值是恒定的,通常取550HV1,而且标注时一般可省略,特殊情况下可不采用此值,此时DC后必须注明商定的界限硬度值和试验力。
A08M-20.1-2002汽车用无缝钢管技术条件-普通用管 .tds
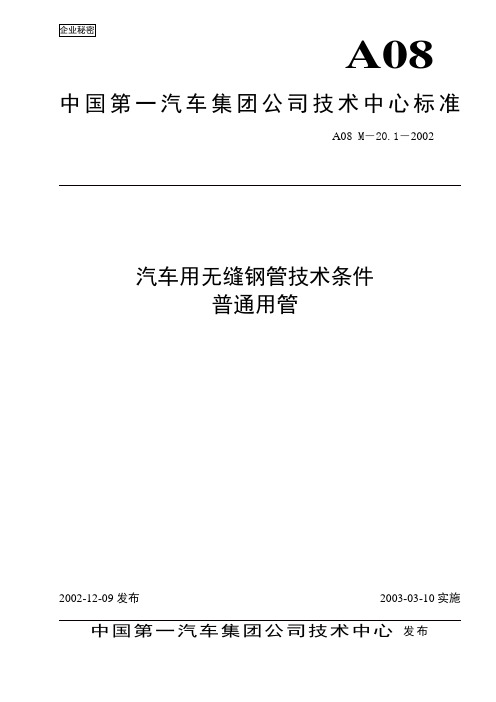
B:0.0005~0.0035
0.035
0.035
0.30
40Cr
0.37~0.44
0.17~0.37
0.50~0.80
—
0.035
0.035
0.80~1.10钢、低合金钢钢管的纵向力学性能。
A 级:一般钢管的力学性能应符合表2中的规定;
表2
0.17~0.37
0.50~0.80
—
0.035
0.035
0.25
16Mn
0.12~0.20
0.20~0.55
1.20~1.60
—
0.045
0.045
0.30
45 Mn2
0.42~0.49
0.17~0.37
1.40~1.80
—
0.035
0.035
0.30
40MnB
0.37~0.44
0.17~0.37
GB241液压试验方法
GB 246压扁试验方法
GB 699优质碳素结构钢钢号和一般技术条件
GB1591低合金结构钢技术条件
GB/T 3077合金结构钢技术条件
GB 8162结构用无缝钢管
3
尺寸、外形及重量按GB 8162 和双方协议的有关规定执行。
4
4.1 牌号、化学成分和残余元素
4.1.1 牌号和化学成分应符合表1中的规定。
牌号
力学性能
工艺性能
бb
MPa
бS
MPa
δ5
%
压扁试验平板间距H
(最小值为壁厚的5倍)
mm
不小于
08AL
325
195
26
2/3 D
渗碳钢的渗碳淬火指定标准hes
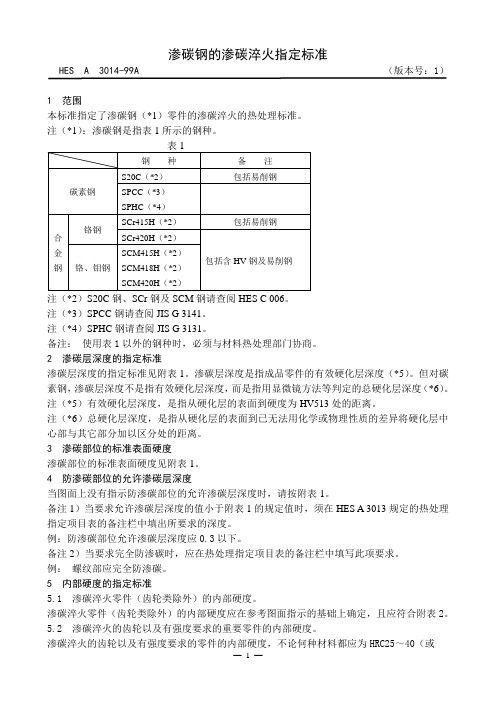
渗碳钢的渗碳淬火指定标准HES A 3014-99A(版本号:1)1 范围本标准指定了渗碳钢(*1)零件的渗碳淬火的热处理标准。
注(*1):渗碳钢是指表1所示的钢种。
注(*2)S20C钢、SCr钢及SCM钢请查阅HES C 006。
注(*3)SPCC钢请查阅JIS G 3141。
注(*4)SPHC钢请查阅JIS G 3131。
备注:使用表1以外的钢种时,必须与材料热处理部门协商。
2 渗碳层深度的指定标准渗碳层深度的指定标准见附表1。
渗碳层深度是指成品零件的有效硬化层深度(*5)。
但对碳素钢,渗碳层深度不是指有效硬化层深度,而是指用显微镜方法等判定的总硬化层深度(*6)。
注(*5)有效硬化层深度,是指从硬化层的表面到硬度为HV513处的距离。
注(*6)总硬化层深度,是指从硬化层的表面到已无法用化学或物理性质的差异将硬化层中心部与其它部分加以区分处的距离。
3 渗碳部位的标准表面硬度渗碳部位的标准表面硬度见附表1。
4防渗碳部位的允许渗碳层深度当图面上没有指示防渗碳部位的允许渗碳层深度时,请按附表1。
备注1)当要求允许渗碳层深度的值小于附表1的规定值时,须在HES A 3013规定的热处理指定项目表的备注栏中填出所要求的深度。
例:防渗碳部位允许渗碳层深度应0.3以下。
备注2)当要求完全防渗碳时,应在热处理指定项目表的备注栏中填写此项要求。
例:螺纹部应完全防渗碳。
5 内部硬度的指定标准5.1 渗碳淬火零件(齿轮类除外)的内部硬度。
渗碳淬火零件(齿轮类除外)的内部硬度应在参考图面指示的基础上确定,且应符合附表2。
5.2 渗碳淬火的齿轮以及有强度要求的重要零件的内部硬度。
渗碳淬火的齿轮以及有强度要求的零件的内部硬度,不论何种材料都应为HRC25~40(或HRC25~38),此种情况,内部硬度不应是参考指示(*7)。
注(*7)齿轮及强度有要求的其它零件,其强度特别是冲击强度对内部硬度影响很大。
如超过了HRC40会导致低冲击值。
渗碳淬火齿轮有效硬化层深
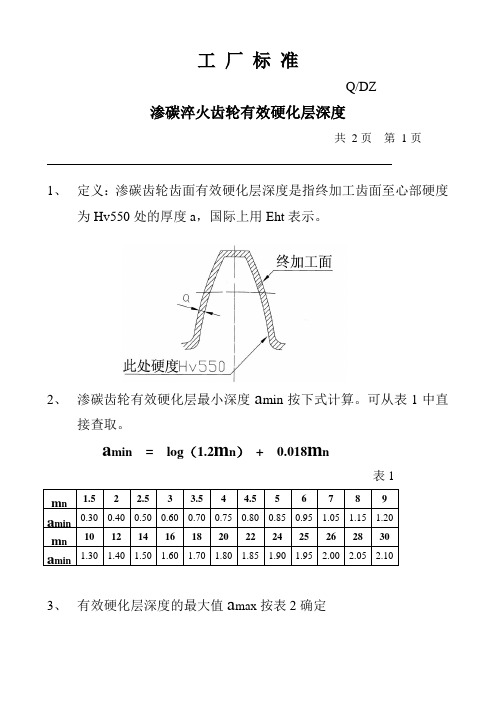
工厂标准
Q/DZ
渗碳淬火齿轮有效硬化层深度
共2页第1页
1、定义:渗碳齿轮齿面有效硬化层深度是指终加工齿面至心部硬度
为Hv550处的厚度a,国际上用Eht表示。
2、渗碳齿轮有效硬化层最小深度a min按下式计算。
可从表1中直
接查取。
a min= log(1.2m n)+ 0.018m n
表1
3、有效硬化层深度的最大值a max按表2确定
共2页第2页
表2
4、本规定适用于轧钢机械、连铸机械、炼焦机械、冶炼机械、装卸
机械的传动齿轮。
5、特殊工况用渗碳齿轮的有效硬化层深度,可根据接触剪应力的大
小另行确定。
6.、本表对于Mn≤8的齿轮而言,其推荐的渗碳深度是合理的,但对于Mn>8的齿轮而言,其数据缺乏合理性。
7. 对于合理的渗碳层深度各国、各公司的标准不同,而且差距还比较大。
各国及各行业推荐的渗碳层深度见表3
表3 各国及各行业推荐的渗碳层深度
注:根据JB/T 8853-2001《圆柱齿轮减速机》渗碳层的深度根据模数选择,当Mn=1.5~6时,渗碳层深度ht=(0.2~0.3)Mn;
当Mn=7~18时,渗碳层的深度ht=(0.15~0.25)Mn(小模数取大值,大模数取小值)。
渗碳件质量检查
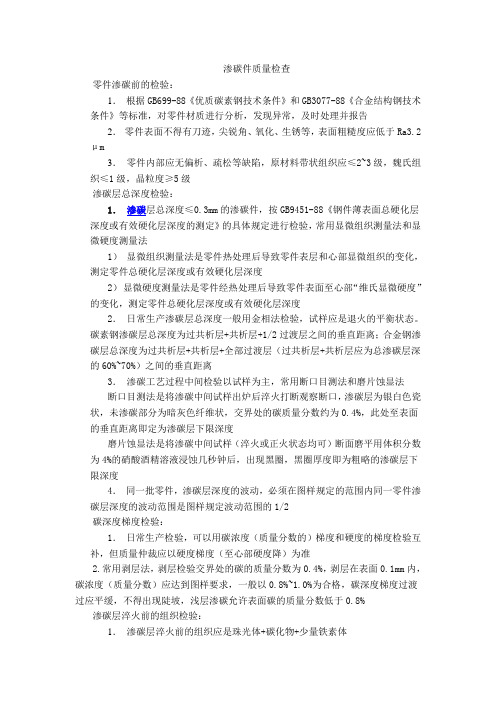
渗碳件质量检查零件渗碳前的检验:1.根据GB699-88《优质碳素钢技术条件》和GB3077-88《合金结构钢技术条件》等标准,对零件材质进行分析,发现异常,及时处理并报告2.零件表面不得有刀迹,尖锐角、氧化、生锈等,表面粗糙度应低于Ra3.2μm3.零件内部应无偏析、疏松等缺陷,原材料带状组织应≤2~3级,魏氏组织≤1级,晶粒度≥5级渗碳层总深度检验:1.渗碳层总深度≤0.3mm的渗碳件,按GB9451-88《钢件薄表面总硬化层深度或有效硬化层深度的测定》的具体规定进行检验,常用显微组织测量法和显微硬度测量法1)显微组织测量法是零件热处理后导致零件表层和心部显微组织的变化,测定零件总硬化层深度或有效硬化层深度2)显微硬度测量法是零件经热处理后导致零件表面至心部“维氏显微硬度”的变化,测定零件总硬化层深度或有效硬化层深度2.日常生产渗碳层总深度一般用金相法检验,试样应是退火的平衡状态。
碳素钢渗碳层总深度为过共析层+共析层+1/2过渡层之间的垂直距离;合金钢渗碳层总深度为过共析层+共析层+全部过渡层(过共析层+共析层应为总渗碳层深的60%~70%)之间的垂直距离3.渗碳工艺过程中间检验以试样为主,常用断口目测法和磨片蚀显法断口目测法是将渗碳中间试样出炉后淬火打断观察断口,渗碳层为银白色瓷状,未渗碳部分为暗灰色纤维状,交界处的碳质量分数约为0.4%,此处至表面的垂直距离即定为渗碳层下限深度磨片蚀显法是将渗碳中间试样(淬火或正火状态均可)断面磨平用体积分数为4%的硝酸酒精溶液浸蚀几秒钟后,出现黑圈,黑圈厚度即为粗略的渗碳层下限深度4.同一批零件,渗碳层深度的波动,必须在图样规定的范围内同一零件渗碳层深度的波动范围是图样规定波动范围的1/2碳深度梯度检验:1.日常生产检验,可以用碳浓度(质量分数的)梯度和硬度的梯度检验互补,但质量仲裁应以硬度梯度(至心部硬度降)为准2.常用剥层法,剥层检验交界处的碳的质量分数为0.4%,剥层在表面0.1mm内,碳浓度(质量分数)应达到图样要求,一般以0.8%~1.0%为合格,碳深度梯度过渡过应平缓,不得出现陡坡,浅层渗碳允许表面碳的质量分数低于0.8% 渗碳层淬火前的组织检验:1.渗碳层淬火前的组织应是珠光体+碳化物+少量铁素体2.渗碳层中有大块或网状碳化物,应建议两次淬火或一次正火,一次淬火,一般碳化物级别小于6级3.渗碳后,心部出现3级以上带状组织或晶粒度小于5级时,应正火后,重新检验合格方可淬火4.渗碳层中出现网状碳化物与游离铁素体不合格时应正火消除渗碳件淬、回火后的硬度检验:1.渗碳件表面硬度检验时,应去除氧化皮,脱碳层、增碳层,应以洛氏和维氏硬度计检验为准2.硬度应符合图样或技术文件规定,一般碳钢(10、20钢)硬度在50~55HRC 或58~63HRC,合金钢硬度在58~63HRC3.硬度终检以实物为准,但允许用随炉不同位置两个以上的试样代替实物检验。
渗碳热处理相关的标准
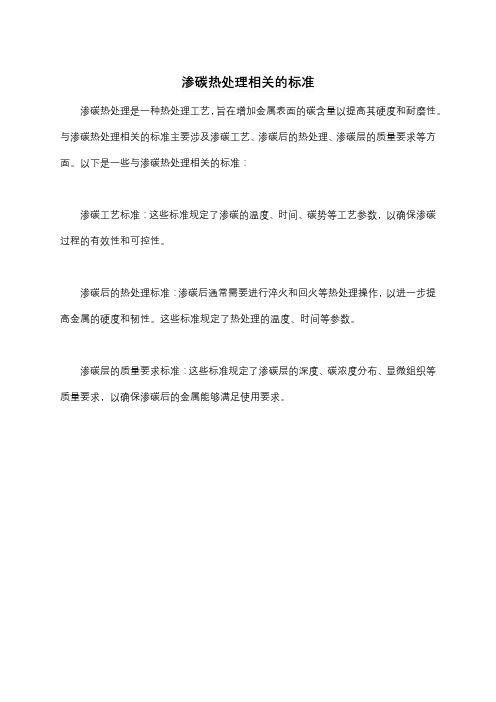
渗碳热处理相关的标准
渗碳热处理是一种热处理工艺,旨在增加金属表面的碳含量以提高其硬度和耐磨性。
与渗碳热处理相关的标准主要涉及渗碳工艺、渗碳后的热处理、渗碳层的质量要求等方面。
以下是一些与渗碳热处理相关的标准:
渗碳工艺标准:这些标准规定了渗碳的温度、时间、碳势等工艺参数,以确保渗碳过程的有效性和可控性。
渗碳后的热处理标准:渗碳后通常需要进行淬火和回火等热处理操作,以进一步提高金属的硬度和韧性。
这些标准规定了热处理的温度、时间等参数。
渗碳层的质量要求标准:这些标准规定了渗碳层的深度、碳浓度分布、显微组织等质量要求,以确保渗碳后的金属能够满足使用要求。
- 1、下载文档前请自行甄别文档内容的完整性,平台不提供额外的编辑、内容补充、找答案等附加服务。
- 2、"仅部分预览"的文档,不可在线预览部分如存在完整性等问题,可反馈申请退款(可完整预览的文档不适用该条件!)。
- 3、如文档侵犯您的权益,请联系客服反馈,我们会尽快为您处理(人工客服工作时间:9:00-18:30)。
1
本标准是《汽车零件渗碳淬火技术条件》系列标准的第一项。该系列标准的预计结构由五项标准组成,名称如下:
汽车零件渗碳淬火技术条件 有效硬化层深度
汽车零件渗碳淬火技术条件 表面硬度
汽车零件渗碳淬火技术条件 心部硬度
汽车零件渗碳淬火技术条件 尾部螺纹
汽车零件渗碳淬火技术条件 金相检验。
本标准由中国第一汽车集团公司技术中心提出并归口。
16
16.1
16.2
16.3
16.4
16.5
16.6
17
有效硬化层深度标注方法:
产品图样上应标注:有效硬化层深度的字母标志、界限硬度值、硬度符号、试验力、有效硬化层深度范围及采用的标准号。
示例1:DC550HV10.50~0.80按A08M-6.1
有效硬化层深度范围
试验力,1kgf
维氏硬度用符号
界限硬度值
本标准由中国第一汽车集团公司技术中心材料部金属材料研究室负责起草。
本标准主要起草人: 徐香秋、刘柯军。
汽车零件渗碳淬火技术条件
有效硬化层深度
11
本标准规定了汽车பைடு நூலகம்碳淬火零件的有效硬化层深度技术要求、试验方法、检验规则及图样标注。
本标准适用于深度大于0.10mm的汽车零件渗碳淬火有效硬化层深度的选定及检测。
GB 9451 钢件薄表面总硬化层深或有效硬化层深度的测定
13
下列术语和定义适用于本标准。
13.1
界限硬度值
确定有效硬化层深度所规定的硬度值。
13.2
有效硬化层深度
从零件表面到所规定的界限硬度值处的垂直距离,用字母DC表示。
14
4.1界限硬度值根据钢材的平均含碳量确定,见表1。
表1
序号
平均含碳量,(C)%
中型车变速箱齿轮、转向零件、差速器齿轮、活塞销等
7
1.0~1.40
>5~7
重型车变速箱齿轮、轻型车后桥主、从动锥齿轮等
8
1.20~1.60
>7~9
重型车变速箱齿轮、中型车主减速器齿轮等
9
1.50~1.90
>9~11
重型车主减速器齿轮等
10
1.70~2.10
>11
重型车主减速器齿轮等
15
有效硬化层深度的试验方法按GB 9450或GB 9451中规定执行。
12
下列文件中的条款通过本标准的引用而成为本标准的条款。凡是注日期的引用文件,其随后所有的修改单(不包括勘误的内容)或修订版均不适用于本标准,然而,鼓励根据本标准达成协议的各方研究是否可使用这些文件的最新版本。凡是不注日期的引用文件,其最新版本适用于本标准。
GB 9450 钢件渗碳淬火有效硬化层深度的测定和校核
界限硬度值,HV
1
0.30±0.025
630
2
0.25±0.025
600
3
0.20±0.025
550
4
0.15±0.025
500
5
0.10+0.025
450
4.2 有效硬化层深度共分八个级别,按不同的用途和齿轮模数选取,见表2。
表2
序号
有效硬化层深度
mm
齿轮模数
Mn
用例
1
0.10~0.30
-
垫片、气门帽等耐磨件等
2
0.30~0.50
>1~2
轿车传动器齿轮、轿车同步器齿毂、齿套等
3
0.40~0.70
>1~2
轿车传动器齿轮、轻型车同步器齿毂、齿套等
4
0.50~0.80
>2~3
轿车主从动锥齿轮、中型车同步器齿毂、齿套等
5
0.60~1.0
>3~4
轻型车变速箱齿轮、轴及重型车同步器齿毂、齿套等
6
0.80~1.20
>4~5
有效硬化层深度的字母标志
示例2:DC550HV0.30.10~0.30按A08M-6.1
有效硬化层深度范围
试验力,0.3kgf
维氏硬度用符号
界限硬度值
有效硬化层深度的字母标志