振动频谱分析在立磨减速机故障诊断中的运用
振动信号的频谱分析与故障诊断

振动信号的频谱分析与故障诊断频谱分析是一种常用的信号处理技术,可以对振动信号进行分析和故障诊断。
本文将介绍频谱分析的原理和应用,并探讨其在故障诊断中的作用。
一、频谱分析的原理频谱分析是将一个信号分解成一系列频率成分的过程。
它基于傅里叶变换原理,将时域上的信号转换为频域上的频谱。
通过频谱分析,可以更直观地了解信号的频率特性和频率成分。
在振动信号处理中,频谱分析可以帮助我们获取振动信号的频率谱。
频率谱可以用图形表示,横轴表示频率,纵轴表示振幅。
通过分析频率谱,可以发现信号中的主要频率成分,从而进行故障诊断和分析。
二、频谱分析的方法1. 傅里叶变换(Fourier Transform)傅里叶变换是将信号从时域转换到频域的重要方法。
它将一个连续时域的信号转换为一个连续频域的频谱。
傅里叶变换可以精确地表示信号的频谱信息,但对计算机实现来说,计算量较大。
2. 快速傅里叶变换(Fast Fourier Transform,FFT)为了克服傅里叶变换的计算复杂度,人们提出了快速傅里叶变换算法。
FFT是一种高效的离散傅里叶变换方法,可以在计算机上快速计算信号的频谱。
FFT广泛应用于振动信号处理中,可以实时获得信号的频谱特征。
三、频谱分析在故障诊断中的应用1. 故障特征提取频谱分析可以帮助我们提取振动信号中的故障特征。
不同的故障在频谱上表现出不同的频率成分和振幅分布。
通过比较正常信号和故障信号的频谱特征,可以判断故障类型和程度。
2. 故障诊断频谱分析可以根据特定故障的频率特征,对故障进行诊断。
例如,对于轴承故障,通常会在频谱上出现与旋转频率相关的峰值,通过检测这些峰值可以判断轴承是否发生故障。
3. 故障监测与预警通过对振动信号进行实时频谱分析,可以实现故障的监测与预警。
当频谱中出现异常的频率成分时,说明设备可能存在故障隐患,及早发现并采取措施进行维修,可以避免设备故障进一步恶化。
四、频谱分析的局限性频谱分析虽然是一种有效的振动信号处理方法,但也存在一定的局限性。
机械振动信号的频谱分析与故障检测研究
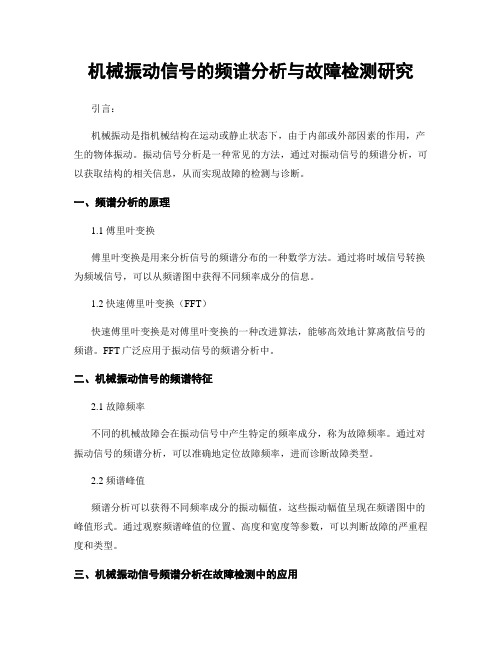
机械振动信号的频谱分析与故障检测研究引言:机械振动是指机械结构在运动或静止状态下,由于内部或外部因素的作用,产生的物体振动。
振动信号分析是一种常见的方法,通过对振动信号的频谱分析,可以获取结构的相关信息,从而实现故障的检测与诊断。
一、频谱分析的原理1.1 傅里叶变换傅里叶变换是用来分析信号的频谱分布的一种数学方法。
通过将时域信号转换为频域信号,可以从频谱图中获得不同频率成分的信息。
1.2 快速傅里叶变换(FFT)快速傅里叶变换是对傅里叶变换的一种改进算法,能够高效地计算离散信号的频谱。
FFT广泛应用于振动信号的频谱分析中。
二、机械振动信号的频谱特征2.1 故障频率不同的机械故障会在振动信号中产生特定的频率成分,称为故障频率。
通过对振动信号的频谱分析,可以准确地定位故障频率,进而诊断故障类型。
2.2 频谱峰值频谱分析可以获得不同频率成分的振动幅值,这些振动幅值呈现在频谱图中的峰值形式。
通过观察频谱峰值的位置、高度和宽度等参数,可以判断故障的严重程度和类型。
三、机械振动信号频谱分析在故障检测中的应用3.1 轴承故障检测轴承是机械设备中常见的易损件,其故障会导致严重的后果。
通过对轴承振动信号进行频谱分析,可以鉴别出轴承的故障类型,例如内圈、外圈和滚珠故障等,并及时采取维修措施,避免发生更大的损失。
3.2 齿轮故障检测齿轮是传动系统中的重要组成部分,其故障会导致传动失效和严重的振动问题。
频谱分析可以识别齿轮传动中的故障频率,如齿轮啮合频率、谐波频率等,从而指示齿轮的磨损、损伤或松动,实现齿轮系统的故障预警和维护。
3.3 机械结构故障检测机械结构的故障常常表现为共振频率的变化。
通过对结构振动信号的频谱特征进行分析,可以判断结构的固有频率是否发生变化,进而判断结构的稳定性和可靠性。
四、振动信号频谱分析的发展趋势与挑战4.1 多维频谱分析传统的振动信号频谱分析主要针对单一变量进行,未能充分利用多维数据的信息。
利用振动信号分析故障诊断方法研究

利用振动信号分析故障诊断方法研究引言:振动信号是一种常见的故障诊断手段,通过对机械或电气设备产生的振动信号进行分析,可以有效地判断设备的工作状态和潜在故障。
近年来,随着科学技术的发展,振动信号分析在工业领域得到了广泛的应用。
本文旨在探讨利用振动信号分析进行故障诊断的方法及其研究意义。
一、振动信号分析的原理振动信号是机械设备在运行过程中由于内部结构、运动部件等原因所产生的振动,其特征包括振动频率、振幅、相位等。
振动信号分析的核心原理是通过对振动信号的频谱分析,确定故障特征频率,从而判断设备是否存在故障。
二、常见的振动信号分析技术1. FFT频谱分析快速傅里叶变换(FFT)是一种基于傅里叶变换的频谱分析方法,通过FFT分析振动信号的功率谱密度,可以得到频率信息。
利用频谱分析技术,可以检测设备内部的故障频率,如轴承的谐波频率、齿轮的啮合频率等。
2. 小波分析小波分析是一种时频分析方法,通过对振动信号进行小波变换,可以同时获得时域和频域的信息。
小波分析相对于FFT分析更具优势,可以有效地提取出瞬时频率、瞬时幅值等特征,对非平稳信号的分析具有较好的效果。
3. 非线性分析振动信号中包含了丰富的非线性特征,如共振、周期倍频、离散谱等,通过对振动信号进行相空间重构、Lyapunov指数计算等非线性分析方法,可以有效地判断设备是否存在故障。
三、利用振动信号分析故障诊断的应用振动信号分析在工业领域具有广泛的应用,可以用于早期故障预测、设备状态监测、故障诊断等方面。
1. 早期故障预测通过对设备产生的振动信号进行分析,可以提前检测到设备存在的潜在故障,并采取相应的维护措施。
例如,在风力发电机组中,通过监测主轴箱的振动信号可以判断主轴箱内轴承是否存在异常磨损,从而预测轴承故障的发生时间。
2. 设备状态监测振动信号可以反映设备的实时工作状态,通过对振动信号的监测与分析,可以及时了解设备的运行情况。
例如,在石油钻机上安装振动传感器,可以实时监测钻杆的振动情况,通过对振动信号的分析,可以判断钻具是否受损,避免钻具折断等事故的发生。
振动信号分析与故障诊断

振动信号分析与故障诊断振动信号是在很多机械设备中常见的一个现象。
通过分析振动信号,可以获取各种设备的运行状态和性能指标,进而进行故障诊断和预测。
振动信号分析与故障诊断在工业生产中具有重要的应用价值。
振动信号分析是指对振动信号进行处理、提取特征,并进行分析和诊断。
振动信号携带了机械设备的运行状态信息,包含了频域、时域和幅值等多维度的数据。
通过对振动信号进行分析,可以获得设备的各种振动特征,如振动频率、振动幅值、振动模态等。
振动信号分析的方法包括频谱分析、时频分析、小波分析等。
其中,频谱分析是最为常用的方法之一。
频谱分析通过将时域的振动信号转化为频域信号,可以清晰地展示出不同频率分量所占的比例。
通过观察频谱图,可以得出关于故障频率或共振频率的信息。
振动信号的故障诊断是指通过分析振动信号的特征和变化,判断设备是否存在故障,并确定故障的类型和原因。
常见的故障类型包括轴承故障、齿轮故障、偏心故障等。
不同类型的故障在振动信号中表现出不同的特征,如频率的变化、幅值的异常等。
轴承故障是振动信号中常见的故障类型。
轴承故障通常表现为频谱中出现明显的多个高频峰。
通过分析这些高频峰的特点,可以确定轴承故障的类型,例如滚珠疲劳、滚道剥皮等。
另外,轴承故障还会引起振动信号的幅值增大和频率的变化。
齿轮故障是振动信号中另一常见的故障类型。
齿轮故障通常表现为频谱中出现特定的频率分量,称为齿轮特征频率。
通过分析这些特征频率的变化和幅值的异常,可以判断齿轮故障的类型,如齿面磨损、齿根断裂等。
振动信号分析与故障诊断的应用范围广泛。
在制造业中,振动信号分析可以用来监测和评估设备的性能和健康状况。
通过对振动信号进行实时监测和分析,可以及时发现设备的故障和异常,采取相应的维修和保养措施,避免因故障带来的生产停顿和损失。
在航空航天领域,振动信号分析与故障诊断可以应用于航空发动机、飞机结构和飞行控制系统等。
通过对振动信号进行监测和分析,可以判断航空设备的性能和可靠性,并提前做好维修和更换的准备,确保航空器的安全运行。
减速机振动异常原因及振动频谱数据浅析

减速机振动异常原因及振动频谱数据浅析摘要:在众多工业领域生产过程中,减速机属于常见的机械设备,齿轮是减速机中的关键部件。
在实际工作中,齿轮的工作状况与减速机整体运行有着密切的关系,一旦齿轮出现异常,将会影响减速机设备的运行,甚至威胁减速机运行阶段的安全性。
关键词:减速机;震动1 减速机设备振动异常原因及案例1.1 减速机设备振动异常的原因导致减速机设备振动异常的原因较多,比如:齿面点蚀、齿面磨损、齿面胶合、齿轮断齿、齿轮偏心等。
设备振动异常的原因可划分为齿轮磨损、齿轮裂纹、齿面断齿、齿面偏心、齿轮不对中5种原因。
1.1.1 齿轮磨损在减速机设备内齿轮属于关键部件,是减速机设备力传动的核心,随着使用时间的增加,齿轮受到不断承载冲击、润滑油内杂质等因素的影响,齿轮表面会出现不同程度的磨损,一般会有摩擦磨损、粘着磨损、磨粒磨损、腐蚀磨损4种。
当齿轮磨损后表现出的故障信息,频谱中会有被故障齿轮激起齿轮本身的固有频率,并在齿轮的固有频率两侧分布有故障齿轮转轴频率的边频带,不过最为明显的表现是振动总量会增加,频谱中的2倍、3倍齿轮啮合频率分量幅值增加速度会很快,比1倍啮合频率幅值增长速度更快,因此,我们经常以分析各阶频谱分量的增长速度,如高次谐波分量比基频增长速度快,来判定齿轮的磨损故障。
在磨损后期,啮合频率两侧边带的幅值会很高、边带数会增加,因此,边带分析比啮合频率能更好地反映出齿轮磨损状态。
1.1.2 齿轮裂纹减速机长期受到承载力冲击的影响,齿轮啮合在载荷的多次重复咬合作用下,轮齿弯曲应力超过弯曲持久极限时,齿根部分因超出材料疲劳极限,将产生疲劳裂纹。
当齿轮出现裂纹时会在振动频谱中出现以n*转频为主的频域特性信号,一般在低频阶段。
在时域波形中会体现出以齿轮旋转频率为周期的冲击脉冲信号。
1.1.3 齿轮断齿当齿轮裂纹逐渐延伸,齿轮无法承受传动载荷时,最终将引起断齿现象。
当齿轮在工作中受到严重的冲击、偏载以及材质不均匀等其他因素也会造成齿轮断裂现象。
机械振动信号的频谱分析与故障识别
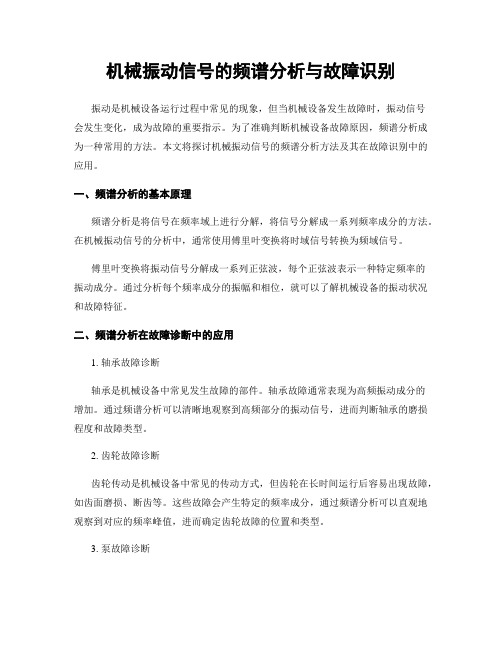
机械振动信号的频谱分析与故障识别振动是机械设备运行过程中常见的现象,但当机械设备发生故障时,振动信号会发生变化,成为故障的重要指示。
为了准确判断机械设备故障原因,频谱分析成为一种常用的方法。
本文将探讨机械振动信号的频谱分析方法及其在故障识别中的应用。
一、频谱分析的基本原理频谱分析是将信号在频率域上进行分解,将信号分解成一系列频率成分的方法。
在机械振动信号的分析中,通常使用傅里叶变换将时域信号转换为频域信号。
傅里叶变换将振动信号分解成一系列正弦波,每个正弦波表示一种特定频率的振动成分。
通过分析每个频率成分的振幅和相位,就可以了解机械设备的振动状况和故障特征。
二、频谱分析在故障诊断中的应用1. 轴承故障诊断轴承是机械设备中常见发生故障的部件。
轴承故障通常表现为高频振动成分的增加。
通过频谱分析可以清晰地观察到高频部分的振动信号,进而判断轴承的磨损程度和故障类型。
2. 齿轮故障诊断齿轮传动是机械设备中常见的传动方式,但齿轮在长时间运行后容易出现故障,如齿面磨损、断齿等。
这些故障会产生特定的频率成分,通过频谱分析可以直观地观察到对应的频率峰值,进而确定齿轮故障的位置和类型。
3. 泵故障诊断泵是常见的机械设备之一,其内部复杂的运动机构容易受到外界因素的影响。
频谱分析可以帮助识别泵的不同故障类型,例如轴承故障、叶片磨损等。
三、频谱分析方法频谱分析有多种方法,常见的有傅里叶变换、快速傅里叶变换(FFT)、小波变换等。
1. 傅里叶变换傅里叶变换是一种精确的频谱分析方法,但计算量较大,不适用于实时监测。
可以通过将信号分段,再进行傅里叶变换来解决这一问题。
2. 快速傅里叶变换(FFT)FFT是一种将信号进行快速傅里叶变换的算法,通过采样和插值的方法,可以有效地降低计算时间。
FFT广泛应用于机械振动信号的频谱分析,尤其适用于实时监测和故障诊断。
3. 小波变换小波变换是一种时频分析方法,在处理非稳态信号方面比傅里叶变换更具优势。
振动状态监测及故障诊断技术应用

2.4.2 滑动轴承
滑动轴承可能有多种故障,其中包括间隙过大,油膜振荡以及摩擦。造成这些故障的原因是装配不当,润滑不良,负荷欠妥,长久磨损及轴承设计不当等。滑动轴承的故障一般在频谱图上表现为半频故障,间隙过大时(4~10)倍频分量较显著,类似于机械松动的现象,但轴向振动较大;油膜涡动有较大的径向振动,频谱图中有明显而稳定的涡动频率分量(42%~48%),可能有高次谐波分量。
a) 内环的频率为:fr=n/60
b) 保持架的旋转频率(或滚动体的公转频率):fc=1/2{1-d/D(cosa)}fr
c) 外环故障频率:Zfc=Z/2{1-d/D(cosa)}fr
d) 内环故障频率:Zfi= Z/2{1+d/D(cosa)}fr
式中 Z——轴承滚动体个数
D——轴承的节径
d——滚动体直径
D. 负荷变化导致振动值变化
E. 时域波形稳定,每转出现1个、2个或3个峰值
2.3 机械松动
机械松动分为结构松动和转动部件松动,造成机械松动的原因是:安装不良、长期磨损、基础或机座损坏、零部件破坏。机械松动故障的频谱图和波形特征:
A.强径向振动,特别是垂直方向,出现3~10倍频
B.径向振动较大,尤其垂直径向振动较大
轴承按其结构分为滚动轴承和滑动轴承。滚动轴承在运转过程中由于各种原因引起损坏,如装配不当,润滑不良,水分和异物侵入,腐蚀和过载等可使轴承过早损坏。主要故障表现为:疲劳剥落、磨损、塑性变形、锈蚀、断裂、胶合、保持架损坏。
2.4.1 滚动轴承
滚动轴承的特征频率与故障具体部位、滚动轴承零件几何尺寸、轴承工作转速等因素有关。如果不计轴承各元件弹性变形,并认为滚动与滚道之间为纯滚动,则各故障特征频率为:
机械振动分析技术的使用方法与故障诊断

机械振动分析技术的使用方法与故障诊断引言:机械振动是工程中常见的现象,它可以帮助我们了解机器设备的运行状况并提前发现潜在的故障。
机械振动分析技术的使用方法与故障诊断可以帮助工程师有效地监测和优化机械设备的运行,提高生产效率和设备可靠性。
本文将介绍机械振动分析技术的基本原理、常用方法以及故障诊断的应用。
一、机械振动分析技术的基本原理机械振动是由于机器设备内部的不平衡、磨损、松动等问题而引起的。
机械振动分析技术基于分析和测量机械设备的振动特征,从中提取出与机械故障相关的信息。
机械振动分析技术的基本原理主要包括以下几个方面:1. 振动传感器的选择与安装:振动传感器是用来测量机器设备振动的重要工具。
传感器的选择要考虑到振动的频率范围和灵敏度等因素,安装位置要选择在受振部位附近,以便准确地捕捉振动信号。
2. 振动信号的采集与处理:振动信号经过传感器采集后,需要进行信号处理和分析。
常用的方法包括滤波、功率谱分析、包络分析等。
通过对振动信号的处理,可以得到振动频谱、振动波形等有助于故障诊断的信息。
3. 振动参数的评估与分析:通过对振动信号进行分析,可以得到一系列的振动参数,如振动速度、加速度、位移等。
这些参数可以帮助工程师判断设备运行的稳定性和故障的严重程度。
二、机械振动分析技术的常用方法1. 频域分析:频域分析是一种常用的机械振动分析方法,它可以将振动信号从时域转换到频域。
通过计算振动信号在不同频率上的能量分布情况,可以得到振动频谱,并从中分析出故障的特征频率。
常用的频域分析方法有傅里叶变换、功率谱分析等。
2. 时域分析:时域分析是振动信号分析的另一种重要方法,它主要关注振动信号在时间上的变化特征。
通过观察振动波形、周期、脉冲等特征,可以判断机械设备是否存在故障。
常用的时域分析方法有包络分析、峰值分析等。
3. 相位分析:相位分析是一种用于研究振动信号中各个频率分量之间的相对位置关系的方法。
通过分析振动信号的相位,可以判断机械部件之间的松动、偏心等问题。
- 1、下载文档前请自行甄别文档内容的完整性,平台不提供额外的编辑、内容补充、找答案等附加服务。
- 2、"仅部分预览"的文档,不可在线预览部分如存在完整性等问题,可反馈申请退款(可完整预览的文档不适用该条件!)。
- 3、如文档侵犯您的权益,请联系客服反馈,我们会尽快为您处理(人工客服工作时间:9:00-18:30)。
振动频谱分析在立磨减速机故障诊断中
的运用
摘要:目前,矿渣立磨减速机属于矿渣立磨设备之中的关键设备,其正常稳
定工作可以确保整个立磨机得以正常运行。
虽然由于诸多内外界因素的影响,在
具体生产阶段,矿渣立磨减速机可能会出现一些故障问题。
鉴于此,本文主要分
析振动频谱分析在立磨减速机故障诊断中的运用。
关键词:振动频谱分析;立磨减速机;故障
中图分类号:TQ172 文献标识码:A
1、引言
矿渣立磨为水泥、建材行业大型重负荷粉磨设备,整个立磨系统的关键主机
设备为减速机,作用自安于传递转速与扭矩,另外也肩负研磨与冲击符合的主体。
因为受到矿渣物料种类、水分、热风温度、料层厚度以及负载波动等工况因素的
影响,减速机处于动态冲击负荷环境之下运转,连接精密的重要传动部件像是齿轮、轴承易出现损坏,随即引发故障。
因为减速机重要船东部件放置在密闭箱体
之内,其内部引发故障的相对比较隐性,通常并不需要其他特殊检测方式,由此
则难以预知内部故障,在引发不正常状况且被迫发生停机的时候,该问题已经愈
演愈烈,这势必对生产与设备出现十分重大的损失。
2、立磨减速机故障分析
2.1、矿渣立磨机的基本工作原理
首先,矿渣在上料过程中经初次筛分磁选处理后,通过立磨进料口送至磨机
内部进行粉磨。
物料经由下锥体前侧的滑道落在磨盘上,磨盘在通电工作情况下
一直处于旋转状态,这样物料受离心力作用被甩向边缘,在磨盘、磨辊之间的剪
切力和磨辊压力几种力的共同作用被首次粉磨。
在首次粉磨过程中,被粉磨至一
定程度的物料在离心力作用下被甩向磨盘与磨机箱体之间的空隙之中,空隙下方
喷嘴吹出足够强的热风将粉磨合格的物料吹进磨盘上方的高效选粉机中,而物料
仍旧较大,粉磨不合格的则落在环形室,由刮料板收集排出磨机。
通过选粉机筛
选将合格的物料与不合格物料相分离,合格的矿渣粉在选粉机中被输出立磨设备
运输至成品库;而被刮料板所收集的不合格物料则需要经由立磨回料系统,再次
通过喂料阀行送至下锥体后侧的滑道进行立磨进行二次粉磨,直至所有物料粉磨
合格。
2.2、矿渣立磨减速机故障
弗兰德牌矿渣立磨减速系统主要由主减速器、轴承、监测系统、辅助减速机、润滑系统、超速离合器等模块组成,其常见的故障类型有减速器监测系统故障、
轴承损坏等。
矿渣立磨减速机监测故障的发展主要是由传感器故障、扭矩系统故障等引起的。
当立磨减速机在监测过程中,出现大量的扭矩峰值冲击报警,且部分扭矩特
征值有变大趋势,监测现场振动具有一定规律时,意味着立磨减速机监测系统可
能发生了故障。
根据大量实际案例分析,引起矿渣立磨减速机监测系统出现故障
的原因主要是由人为因素、外部因素造成的,如立磨机内部出现挂板等异物。
若
操作人员不小心将挂板等异物掉落在立磨机磨盘与磨辊之间的结合处,那么在矿
渣立磨减速机运行过程中,刮板受剪切力作用就会被挤压变形,进而对立磨机减
速机产生振动,引发扭矩异常,最终导致监测故障。
减速机轴承损坏的主要表现是减速机润滑油站低压供油过滤器进出口压差异常,主要是由过滤器滤芯有大量铁屑造成过滤器阻塞所引起,通过对铁屑样品进
行光谱分析发现为低高合金钢材质,而在减速机内部传动构件中,只有轴承保持
架为这种材质,由此可以初步判定是轴承发生了磨损。
3、振动频谱分析在立磨减速机故障诊断中的运用
3.1、高速轴处振动情况
高速轴处振动情况见图1。
图1 高速轴振动频谱图
从图1可以看出高速轴的1倍频16.563 Hz及其倍频,且幅度较高,阶数较多,依据转动部件旋转松动的故障特征:旋转部件与固定部件间间隙过大会产生
1倍频,严重时超过10倍。
据此认为该处转动部件高速轴轴承与外套间有松动迹象。
3.2、高速级(一级)齿轮啮合情况
在A处检测的速度频谱图中,高速级齿轮啮合频率265 Hz及其倍频,并伴
随高速轴转频的边频带16.55 Hz。
采用同样的方法,在加速度频谱中检测出高速级伞齿轮啮合频率266 Hz及
其倍频,在包络频谱中检测出高速级伞齿轮啮合频率266 Hz及其倍频,在高速
级伞齿轮啮合频率 265 Hz 附近检测出高速轴转频16.563 7 Hz 的边频带16.55 Hz。
综合以上情况:高速级大小齿轮啮合处,多个频谱图均出现高速级啮合频率
及其边频带,且幅值高阶数多。
依据传动齿轮齿面磨损的故障特征:以齿轮啮合
频率及其谐波为载波频率,齿轮所在轴转频及其倍频为调制频率的啮合频率调制,幅度较高。
分析认为高速级齿轮齿面出现严重磨损,重点检查齿面磨损情况。
依
据传动齿轮不对中的故障特征:出现齿轮啮合频率及其倍频。
认为高速级齿轮存
在不对中现象。
3.3、第二级圆柱齿轮啮合情况
在二级圆柱齿轮速度谱检测到圆柱齿轮啮合频率126 Hz 及其倍频,振动幅
值较高。
依据传动齿轮不对中的故障特征:出现齿轮啮合频率及其倍频,幅值较高。
初步认为二级圆柱齿轮存在不对中现象,应重点检查圆柱齿轮接触位置出现
的偏载磨损现象。
3.4、电动机、减速机联轴器对中情况
同理,在高速轴处速度图中检测出电动机轴转频16.5 Hz及其2倍频且2倍
频幅值相对较高,同样初步认为电动机、减速机间存在不对中现象。
3.5、扭矩信号检测减速器故障监测
矿渣立磨减速机监测系统主要由振动检测单元、分析软件、监测单元、PLC、和多种传感器(扭矩传感器、加速度传感器、转速传感器等)组成,这种监测系
统不仅可以记录传统的振动信号,可以实现非接触测量,而且扭矩检测系统的引
入还实现了对扭矩信号频谱和振动信号频域信息的分析,可以提供危险过载、设
备运行状态等信息,具有可靠性高优点。
作为减速机监测系统重要组成部分,利
用扭矩信号对矿渣立磨减速机的监测故障进行检测和诊断,无疑是一种有效的诊
断方法。
之所以可以通过扭矩信号来实现对减速机监测故障的检测诊断,主要是因为
立磨机设备中每一部件,尤其是重要部件都有属于其自身独特的啮合频率和转动
频率,这就为通过扭矩信号来判断部件各种频率是否正常,是否发生了故障提供
了理论依据。
利用扭矩检测系统对矿渣立磨减速机运行状态和重要部件进行检测,同时获
取对应的扭矩曲线频谱,通过对扭矩曲线和频谱分析,查看减速机是否存在明显
的有规律的振动,若有则初步判定发生故障的对象和位置,然后再进一步对故障
进行分析,包括部件损伤程度、磨损情况、变化趋势等,并根据扭矩提供检测信
息作出适当的检修安排,及时将故障解除。
3.6、轴承故障的检测及诊断
对于矿渣立磨减速机轴承磨损故障的检测和诊断,根据轴承磨损的表现和产生原因,可以采用如下方式:将立磨减速机拆解,对各级行星所有轴承进行仔细检查,若发现部分或全部轴承损坏,如轴承滚珠或内圈、外圈易发生严重的剥落、点蚀,保持架断裂、严重磨损,行星架上有许多细小的、片状的铁屑,则可确定减速机轴承发生了较为严重的磨损、损坏。
在检测过程中,若发现减速机各级行星架或轴承表面存在锈蚀现象,则需要对齿轮润滑油进行抽样检测,若检测结果显示润滑油水分变大,则表明有水渗入润滑油,造成减速机轴承和行星架发生锈蚀,引起减速机轴承损坏故障。
4、结束语
矿渣立磨减速机作为矿渣立磨设备中的核心设备,其正常稳定工作是整个立磨机正常工作的重要保障。
虽然因各种因素影响,在实际生产过程中,矿渣立磨减速机可能会发生这样那样的故障,但以弗兰德立磨减速机为代表的,随着矿渣立磨减速机工作性能的不断提高,故障检测诊断方法的不断先进成熟,相信矿渣立磨减速机故障会得到较好的解决。
参考文献:
[1]石建国.在线振动监测系统在立磨减速机上的应用[J].新世纪水泥导报,2020,26(03):82-85.
[2]刘安.浅析矿渣立磨减速机故障状态的检测与诊断[J].世界有色金
属,2017(01):143-144.
[3]王淼清. 基于小波分析的矿渣立磨减速机故障诊断技术[D].江西理工大学,2016.
[4]郭进. 立磨减速机动态特性模拟及疲劳寿命分析[D].重庆大学,2015.
[5]张秀全,张中国.JLP220立磨减速机故障分析及解决措施[J].中国水
泥,2015(01):77-79.
[6]李巍,陈静君,孔令彬,王永向.使用扭矩信号检测与诊断立磨减速机的故障[J].水泥,2014(07):48-50.。