大野耐一:精益生产的十条训诫
简介大野耐一的十条训诫
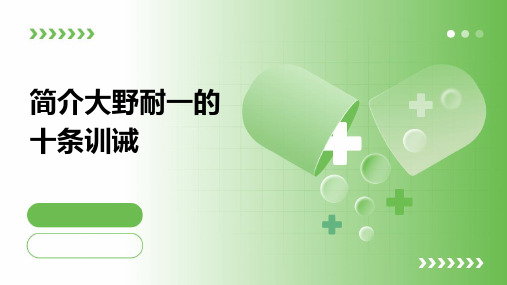
04
结论
04
结论
大野耐一十条训诫的价值和意义
促进精益生产
大野耐一的十条训诫是精益生产的核心理 念,对于提高生产效率、减少浪费、优化
流程等方面具有重要指导意义。
培养人才
大野耐一的训诫强调人才培养和团队协作, 有助于企业培养出高素质、有创造力的员 工,提升企业整体竞争力。
持续改进
大野耐一的训诫鼓励企业不断改进和创新, 适应市场变化,提高产品质量和服务水平。
在个人成长中的应用
训诫四 训诫五 训诫六 总结
追求本质,切勿轻信表面现象
严格要求,一丝不苟地工作
做正确的事,用正确的方法做事 大野耐一的十条训诫对于个人成长同样具有指导意义,能够帮
助个人提高工作效能,实现自我价值。
对现代社会的启示和影响
训诫七
不断学习,不断提高自己
训诫八
培养有全球视野的人才
训诫九
THANKS
感谢观看
THANKS
感谢观看
塑造企业文化
大野耐一的训诫融入企业文化中,有助于 塑造追求卓越、注重细节、持续改进的企 业氛围。
大野耐一十条训诫的价值和意义
促进精益生产
大野耐一的十条训诫是精益生产的核心理 念,对于提高生产效率、减少浪费、优化
流程等方面具有重要指导意义。
培养人才
大野耐一的训诫强调人才培养和团队协作, 有助于企业培养出高素质、有创造力的员 工,提升企业整体竞争力。
跨部门协作
鼓励不同部门之间的员工相互交流和 学习,共同践行大野耐一的训诫,实
现企业整体优化。
领导力推动
企业领导者应积极推动精益生产,践 行大野耐一的训诫,为员工树立榜样。
持续改进机制
建立持续改进的机制,鼓励员工发现 问题、提出改进意见,不断完善和优 化生产流程。
大野耐一的十条训诫

大野耐一的十条训诫-仔细观察生产现场(2009-12-21 08:58:45)转载▼分类:精益杂文标签:大野耐一丰田方式持续改善生产现场作者:若松义人一旦开始就不要放弃,半途而废会助长惰性不要自以为改善已经完成,需要做的工作还很多仔细观察生产现场年轻的丰田员工C自认为改善工作做得非常好,于是就跑到大野先生那里去汇报:“改善工作已经做好了。
”大野先生听了之后没有说话,和他一起来到生产现场。
转了一会儿,大野先生指着一台车床说:“去那里画一个圆圈。
”C觉得很奇怪,就在车床上画了个小圈。
“那么小的圈能站住人吗!重新画!”C赶忙又重新画了一个圈,然后大野先生只说了句“站在圆圈里仔细观察生产现场”就转身离开了。
大野先生的命令向来没人敢反驳,虽然不理解其中的缘由,C也只能乖乖地服从。
到了中午,C忍不住想去厕所,于是就从圆圈中走了出来。
可是没想到运气太差,刚好被路过的大野先生发现。
“为什么要走出去!”“只是想去一下厕所……”“吃完午饭后继续站在这里,出去的时候必须先和旁边的人打招呼。
”说完后大野先生又径自离去了。
C感到很无奈,不过也只能老老实实地站到了傍晚。
至于观察什么、为什么要观察,他也没有想太多,只是呆呆地站在那里瞪着眼睛看。
到了傍晚,大野先生走过来问:“发现什么问题了吗?”“还没有……”C只能胆怯地如实回答。
大野先生想了一下,又说:“今天可以下班了,明天继续站在这里观察。
”C非常想问是要观察什么,可是一想到大野先生一定会说“自己去想”,所以话到嘴边又咽了回去。
第二天早晨,C又重新站在圆圈中。
这回他好像发现了一些问题,不过,至于到底是什么却又说不清楚。
中午的时候,大野先生又走了过来。
“发现问题了吗?”“是的,不过好像说不清楚具体是什么问题。
”C还是如实地回答。
这回大野先生指着生产现场说:“看看工人们的工作方法。
你说…已经完成了改善‟,可是你的改善却让他们的工作效率更低。
既然已经发现了问题,那就赶紧想办法解决吧”。
简介大野耐一的十条训诫

• 第二次世界大战后,丰田年汽车销量下降到了区区3275辆
工人开始罢工,而且持续相当长时间 丰田几乎濒临破产
• 为了挽救丰田,日本银行组成一个银行团为丰田提供资金,但是提出的条件是:解雇3000名员工 ,经营层全部换班,公司一分为二:丰田销售公司、丰田汽车公司。 • 那时的丰田不但面临资金短缺,还面临着原材料供应不足,而且日本汽车制造业的生产率与美国 差距巨大。 • 在如此严峻的现实面前,丰田喜一郎提出:降低成本,消除不必要的浪费。用三年时间赶上美国 !否则,日本的汽车产业将难以为继! • “三年赶超美国”,创业者的雄心壮志与迫在眉睫目标让大野耐一这位职业经理人刻骨铭心。 • 由于这样的追赶意识,大野耐一从此把眼睛死死盯住现场。
简介大野耐一的十条训诫共45页
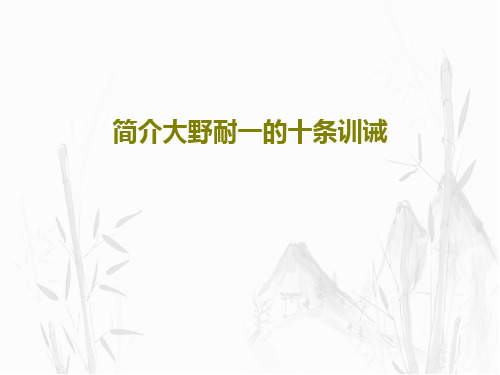
11、战争满足了,或曾经满足过人的 好斗的 本能, 但它同 时还满 足了人 对掠夺 ,破坏 以及残 酷的纪 律和专 制力的 欲望。 ——查·埃利奥 特 12、不应把纪律仅仅看成教育的手段 。纪律 是教育 过程的 结果, 首先是 学生集 体表现 在一切 生活领 域—— 生产、 日常生 活、学 校、文 化等领 域中努 力的结 果。— —马卡 连柯(名 言网)
13、遵守纪律的风气的培养,只有领 导者本 身在这 方面以 身作则 才能收 到成效 。—— 马卡连 柯 14、劳动者的组织性、纪律性、坚毅 精神以 及同全 世界劳 动者的 团结一 致,是 取得最 后胜利 的保证 。—— 列宁 摘自名言网
15、机会是不守纪律的。——雨果
谢谢!
36、自己的鞋子,自己知道紧在哪里。——西班牙
37、我们唯一不会改正的缺点是软弱。——拉罗什福科
xiexie! 38、我这个人走得很慢,但是我从不后退。——亚伯拉罕·林肯
ቤተ መጻሕፍቲ ባይዱ
39、勿问成功的秘诀为何,且尽全力做你应该做的事吧。——美华纳
40、学而不思则罔,思而不学则殆。——孔子
简介大野耐一的十条训诫

为了实现零次品的想法,Mr.大野提出了两个需要彻底执行的方案。
失败是一种公共财富
失败是去除浪费的最好机会
9
第一条 首先,我们就是成本,消除无用的浪费,否则没有提升
1. 浪费总会被习惯性地隐藏起来,所以首先要避免在工作中有 所隐藏
2. 重视微小的数字,重大的浪费就会呈现出来
10
重视微小的数字 重大的浪费就会呈现出来
大野耐一的十条训诫
1
大野耐一(Taiichi Ohno 1912-1990)
• • • • • • • 著名的丰田生产方式的创始人 被日本人称为:“日本复活之父”、“生产管理的教父”、“穿着 工装的圣贤” 1912年出生于中国大连 1932年毕业于名古屋高等工业学校机械科,同年进入丰田纺织公司 1943年调入丰田汽车公司 1949年任该公司机械厂厂长 后来历任丰田纺织公司和丰田合成公司会长
他日思夜想:为什么美国的生产率比我们高出几倍? 我们一定是存在着大量的浪费! 那么如何能找到更好的生产方式呢?
2
21世纪的竞争和挑战
客户要求:
o 多品种、少批量、快交期
对企业和客户都成为“死穴”的三个要素:
o 品质(高质量) o 价格(低成本) o 交期(快速度)
全球化竞争的残酷性
• 第二次世界大战后,丰田年汽车销量下降到了区区3275辆
工人开始罢工,而且持续相当长时间 丰田几乎濒临破产
• 为了挽救丰田,日本银行组成一个银行团为丰田提供资金,但是提出的条件是:解雇3000名员工 ,经营层全部换班,公司一分为二:丰田销售公司、丰田汽车公司。 • 那时的丰田不但面临资金短缺,还面临着原材料供应不足,而且日本汽车制造业的生产率与美国 差距巨大。 • 在如此严峻的现实面前,丰田喜一郎提出:降低成本,消除不必要的浪费。用三年时间赶上美国 !否则,日本的汽车产业将难以为继! • “三年赶超美国”,创业者的雄心壮志与迫在眉睫目标让大野耐一这位职业经理人刻骨铭心。 • 由于这样的追赶意识,大野耐一从此把眼睛死死盯住现场。
大野耐一的十条训诫

大野耐一的十条训诫大野耐一的十条训诫第1条首先,你就是成本,消除无用的浪费,否则没有提升浪费总会被习惯性地隐藏起来,所以首先要避免在工作中有所隐藏重视微小的数字,重大的浪费就会呈现出来不要用过去的数据预测未来,这只会让浪费继续下去效率是衡量工作的唯一标准,忙碌并不等于高效生产产品并不是目的,工作是要生产必要的产品第2条一旦开始就不要放弃,半途而废会助长惰性不要自以为改善已经完成,需要做的工作还很多避免应急处理,应急只是一种暂时的敷衍“竭尽全力”而不是“尽力而为”满意但不满足,自信但不自大第3条给他磨炼,以识别人的能力高下通过少量投入实现大量增产,这就是丰田快速成长的秘诀工作要由“是否必要”来决定,而不是“是否可能”绝不事先告诉答案,要让员工积极地思考在压力下培养员工,通过控制成本去完成改善改变员工的生产观念,帮助他们树立战胜困难的决心第4条要意识到竞争对手比你优秀透过表面看问题,抓住改善的时机一切问题都要在现场解决,一切问题都要立刻解决不要把问题留到明天,尽力在今天找到最好的解决方法微小的累积铸就了伟大的业绩第5条工作就是一步一个脚印,用十二分的辛苦去换取十分的成绩不要因为“完成”而停止,工作就是要不断追求更好在工作中添加自己的智慧错误的工作方式只会增强劳动强度培养下属发现问题和解决问题的能力第6条为了让下属心服口服,需要更长远的目光和更坚韧的努力将合适的人才放置在合适的职位上改善需要亲力亲为,这样才会得到下属的拥护在命令别人之前先尝试着自己动手大汗淋漓的工作状态只是欠缺智慧的表现第7条先接受任务,再去思考完成的方法坚信“一定能够完成”,其他的想法只会变成工作的阻碍每个人都拥有无限的智慧,关键是怎样激发和运用不要像评论家一样品头论足,这样的态度解决不了任何问题通过改善改变表面忙碌的状态第8条失败是成功之母,只有在失败中才能找到真正的自信如履薄冰的工作态度会帮你赢得更好的结果不要因为失败而放弃,要在“不想失败”的过程中积极地想办法上司的命令只会让下属变得惟命是从揭穿数字的骗局,从根本上掌控生产现场第9条不要强化劳动,不要过度劳动平均值不是最佳的选择,最短的时间才是最有效的动作失败的经验需要改善,成功的经验也需要改善将目标不断提高,将起点不断降低利润是最主要的问题,但是不能一切都由利润决定第10条客户投诉是成功的呼声,不要抱怨,不要逃避,深人思考,积极应对在改变别人之前先改变自己困难的事情简单做,简单的事情重复做“能够完成”的信心与“无法完成”的失意具有同样的力量组建优秀的团队,并随时做好改善的准备相关文档:●大野耐一语录●大野耐一名言●大野耐一的十条训诫●大野耐一的现场管理●大野耐一丰田生产方式●大学生访谈记录●大学生访谈录●大学生访谈实录●大学学长访谈录●采访大学生访谈记录。
大野耐一的十条训诫
“我现在把箱子里零件的价格告诉你,你来算算一共有多少钱。” A赶紧拿起算盘 (那时还没有计算器)。听到大野先生把数十种零件的价格一一说出来,甚至精确到 几角几分的程度,A真是感到非常敬佩。然而,计算的结果更是让他瞠目结舌。这些 看来不起眼的螺丝、按钮等零件,想着应该没有多少钱,可是全部加起来,竟然是个 很庞大的数字。
什么是 竭尽全力?
第三条 给他磨炼,以识别人的能力高下
1. 通过少量投入实现大量增产,这就是丰田快速成长的秘诀 2. 工作要由“是否必要”来决定,而不是“是否可能” 3. 在压力下培养员工,要让员工积极地思考 和 通过控制成本
去完成改善 4. 改变员工的生产观念,帮助他们树立战胜困难的决心
13
“A,你没有看见生产线旁边散落的零件吗?” “看见了。”“那为什么不把它们捡起 来?”
“您只是说让我跟在后面,并没说要把它们捡起来……”“赶快再去走一圈,把零件 全都捡起来!”于是,A又拿着箱子回到生产线,心想:“不就是捡零件,刚才告诉我 不就完了嘛?”可是嘴上却不敢说出来。一会儿时间,A就把零件全都捡好了。中间有 工人问他“你在做什么”,他只是轻轻地说了一句“这是大野先生的命令”,大家也只能 同情地说:“那加油啊!”
9
采取对策了吗?
加入丰田有5年时间的员工D刚刚加入提高新车型生产效率的团队,也是第一次与大野先生有直 接接触。
大野先生命令他到某零件厂商那里去指导看板(生产、搬运时使用的传票)的使用方法。 虽然那个零件厂商也采用了看板方式,可是由于不习惯使用方法,总是造成看板的丢失。 没见到看板就不能开始生产,这是基本的原则,目的是为了彻底防止生产加工中的浪费。 可是,那里的看板总是丢失,而原则必须要遵守,所以这给零件厂商和丰田都造成了很大的麻 烦。 为了应急,D总是补加看板,这种做法非常危险。万一丢失的看板被找回来,那么就等于有两分 订单,产量也会变成两倍,这就会造成过剩的库存浪费。 不过,年轻的D为了不影响零件的按时供应,还是冒险选择了增加看板的方式。 大野先生知道这件事后非常生气,喊道:“为什么不去寻找丢失的看板,谁让你自作主张!赶快 去把看板找回来!” D垂头丧气地在工厂里仔细找了一个多小时也没有找到,于是回来向大野先生汇 报说:“没有找到。” 谁知大野先生又生气地大喊:“才找了一个小时就跟我说没有找到!”
日本复活之父:丰田大野耐一的10条训诫
日本复活之父:丰田大野耐一的10条训诫!第1条首先,你就是成本,消除无用的浪费,否则没有提升浪费总会被习惯性地隐藏起来,所以首先要避免在工作中有所隐藏;重视微小的数字,重大的浪费就会呈现出来;不要用过去的数据预测未来,这只会让浪费继续下去;效率是衡量工作的唯一标准,忙碌并不等于高效;生产产品并不是目的,工作是要生产必要的产品。
第2条一旦开始就不要放弃,半途而废会助长惰性不要自以为改善已经完成,需要做的工作还很多;避免应急处理,应急只是一种暂时的敷衍;“竭尽全力”而不是“尽力而为”;满意但不满足,自信但不自大。
第3条给他磨炼,以识别人的能力高下通过少量投入实现大量增产,这就是快速成长的秘诀;工作要由“是否必要”来决定,而不是“是否可能”;绝不事先告诉答案,要让员工积极地思考;在压力下培养员工,通过控制成本去完成改善;改变员工的生产观念,帮助他们树立战胜困难的决心。
第4条要意识到竞争对手比你优秀透过表面看问题,抓住改善的时机;一切问题都要在现场解决,一切问题都要立刻解决;不要把问题留到明天,尽力在今天找到最好的解决方法;微小的累积铸就了伟大的业绩。
第5条工作就是一步一个脚印,用十二分的辛苦去换取十分的成绩不要因为“完成”而停止,工作就是要不断追求更好;在工作中添加自己的智慧;错误的工作方式只会增强劳动强度;培养下属发现问题和解决问题的能力。
第6条为了让下属心服口服,需要更长远的目光和更坚韧的努力将合适的人才放置在合适的职位上;改善需要亲力亲为,这样才会得到下属的拥护;在命令别人之前先尝试着自己动手;大汗淋漓的工作状态只是欠缺智慧的表现。
第7条先接受任务,再去思考完成的方法坚信“一定能够完成”,其他的想法只会变成工作的阻碍;每个人都拥有无限的智慧,关键是怎样激发和运用;不要像评论家一样品头论足,这样的态度解决不了任何问题;通过改善改变表面忙碌的状态。
第8条失败是成功之母,只有在失败中才能找到真正的自信如履薄冰的工作态度会帮你赢得更好的结果;不要因为失败而放弃,要在“不想失败”的过程中积极地想办法;上司的命令只会让下属变得惟命是从;揭穿数字的骗局,从根本上掌控生产现场。
精益知识:日本“生产管理教父”大野耐一的十条训诫
精益知识:日本“生产管理教父”大野耐一的十条训诫大野耐一(Taiichi Ohno 1912-1990)•丰田生产方式TPS创始人•被日本人称为:“日本复活之父”、“生产管理教父”、“穿着工装的圣贤”•1912年出生于中国大连•1932年毕业于名古屋高等工业学校机械科,同年进入丰田纺织公司•1943年调入丰田汽车公司•1949年任丰田汽车公司机械厂厂长•1975年担任丰田汽车公司副社长•后历任丰田纺织公司和丰田合成公司会长导读:大野耐一是丰田生产方式TPS的创始人,近几年频发“丰田汽车事件”,重新被圈内人提起他著名的十条管理训诫。
市场普遍认为,“丰田事件”的出现,是丰田汽车公司在制造理念中忘了大野训诫的第10条——客户投诉是成功的呼声,不要抱怨,不要逃避,深入思考,积极应对。
大野耐一十条训诫01. 重视成本要从清除浪费开始02. 一旦开始就要坚持到底03. 在逆境中激发潜能,贪图安逸只能让人日趋退步04. 困难总会先人一步,每时每刻都要做好迎接挑战的准备05. 工作就是一步一个脚印,用十二分的辛苦换取十分的成绩06. 为了让下属心服口服,需要更长远的目光和更坚韧的努力07. 先接受任务,再去思考完成的方法08. 失败是成功之母,只有在失败中才能找到真正的自信09. 不要强化劳动,不要过度劳动10. 客户投诉是企业成功的最好契机,不要抱怨,不要逃避,深入思考,积极应对。
第一条重视成本要从清除浪费开始•首先,你就是成本,消除无用的浪费,否则没有提升•浪费总会被习惯性的隐藏起来,所以首先要避免在工作中有所隐藏,management by fact.•重视微小的数字,重大的浪费就会呈现出来•不要用过去的数据(Old process model)预测未来,这只会让浪费继续下去•效率是衡量工作的唯一标准,忙碌并不等于高效•生产产品并不是目的,工作是要产生必要的产品,efficiency and effectiveness第二条一旦开始就不要放弃,半途而废会助长惰性•不要自以为改善已完成,需要做的工作还很多•避免应急处理,应急只是一种暂时性的敷衍•“竭尽全力”而不是“尽力而为”•满意但不满足,自信但不自大第三条给他磨炼,以认识别人的能力高下•通过少量的投入(NPI Validation,新产品导入验证)实现大量增产,这就是丰田汽车公司快速成长的秘诀•工作要由“是否必要”来决定,而不是“是否可能”•绝不事先告诉答案,要让员工积极地思考•在压力下培养员工,通过控制成本去完成改善•改变员工的生产观念,帮助他们树立战胜困难的决心第四条要意识到竞争对手比你优秀•透过表面看问题,抓住改善的时机•一切问题都要在现场解决,一切问题都要立刻解决•不要把问题留到明天,尽力在今天找到最好的解决方法•微小的积累铸就伟大的业绩•第五条工作就是一步一个脚印,用二十分钟的辛苦去换取十分成绩•不要因为“完成”而停止,工作就是要不断追求更好•在工作中添加自己的智慧•错误的工作方式只会增强劳动强度•培养下属发现问题和解决问题的能力第六条为了让下属心服口服,领导需要更长远的目光和更坚韧的努力•将合适的人才放置在合适的职位上•改善需要领导亲力亲为,这样才会得到下属的拥护•在命令别人之前先尝试着自己动手•大汗淋漓的工作状态只是欠缺智慧的表现•第七条先接受任务,再去思考完成的方法•坚信“一定能够完成”,其他的想法只会变成工作的阻碍•每个人都拥有无限的智慧,关键是怎样激发和运用•不要像评论专家一样品头论足,这样的态度解决不了问题•通过改善改变表面忙碌的状态第八条失败是成功之母,只有先在失败中才能找到真正的自信•如履薄冰的工作态度会帮你赢得更好的结果•不要因为失败而放弃,要在“不想不败”的过程中积极地想办法•上司的命令只会让下属变得惟命是从•揭穿数字的骗局,从根本上掌控生产现场第九条不要强化劳动,不要过度劳动•平均值不是最佳的选择,最短的时间才是最有效的动作•失败的经验需要改善,成功的经验也需要改善•将目标不断提高,将起点不断降低•利润是最主要的问题,但是不能一切都由(Short term)短期利润决定•第十条客户投诉是成功的呼声,不要抱怨,不要逃避,深入思考,积极应对•在改变别人之前先改变自己•困难的事情简单做,简单的事情重复做•“能够完成”的信心与“无法完成”的失意具有同样的力量•组建优秀的团队,并随时做好改善的准备。
大野耐一的十条训诫
一句话就把D问得低下了头。 大野先生又说:“其实很简单,你总是在自己以为会有的地方去找。” 一句话惊醒了D. 确实,他只是在自己认为可能会有的地方找过,而没有查找那些被忽视的角落,所以才总是找 不到。 于是,他又回到现场,在几乎想要放弃的时候,突然在零件箱的底下发现了看板。 查看其他的零件箱才发现,原来看板都在箱子底下。 经统计之后,他发现与丢失的看板数量刚好吻合。 D非常高兴,赶紧跑去汇报,可是大野先生的回话不是“做得不错”,而是“赶快想办法解决吧10”。
“A,你没有看见生产线旁边散落的零件吗?” “看见了。”“那为什么不把它们捡起 来?”
“您只是说让我跟在后面,并没说要把它们捡起来……”“赶快再去走一圈,把零件 全都捡起来!”于是,A又拿着箱子回到生产线,心想:“不就是捡零件,刚才告诉我 不就完了嘛?”可是嘴上却不敢说出来。一会儿时间,A就把零件全都捡好了。中间有 工人问他“你在做什么”,他只是轻轻地说了一句“这是大野先生的命令”,大家也只能 同情地说:“那加油啊!”
“怎么样,仅是散落在生产线的这些零件就是不小的一笔数目吧。”“确实感到非常 吃惊。”
“因为它们都是小的零件,所以没有人会去注意。如果是现金会怎么样?会捡起来 吗?如果是算盘上显示的这个金额,恐怕每个人都会抢着去捡吧。”
6
效率是衡量工作的唯一标准,忙碌并不等于高效
1946年的一天,大野先生突然将现场的工作人员召集在一起,说了下面的一席话: “从今天开始,每天只开工1小时。你们的工作中存在太多浪费,1小时就足够了。请大 家发挥潜能努力工作吧。” 听到这话,所有人都感到万分惊讶。一些人愤愤不平地说: “这不是开玩笑吗?我们这么努力地加班工作还完不成,怎么可能每天就工作1小时!” 大野先生的话确实让人摸不着头脑。当时,很多工人都是放弃休息,每天工作9个甚 至10个小时来完成任务。大野先生当然知道这种情况。工人们以为自己的辛苦劳动会 得到大野先生的认可,可是没想到他却说出这样一番话,真的让人非常气愤。
- 1、下载文档前请自行甄别文档内容的完整性,平台不提供额外的编辑、内容补充、找答案等附加服务。
- 2、"仅部分预览"的文档,不可在线预览部分如存在完整性等问题,可反馈申请退款(可完整预览的文档不适用该条件!)。
- 3、如文档侵犯您的权益,请联系客服反馈,我们会尽快为您处理(人工客服工作时间:9:00-18:30)。
• • “观看”、“观察”、“审视”,随时训练自己透彻了解现场的能力,这才是丰田方
•
虽然那个零件厂商也采用了看板方式,可是由于不习惯使用方法,总是造成看板的丢失。
•
没见到看板就不能开始生产,这是基本的原则,目的是为了彻底防止生产加工中的浪费。
•
可是,那里的看板总是丢失,而原则必须要遵守,所以这给零件厂商和丰田都造成了很大的麻烦。
•
为了应急,D总是补加看板,这种做法非常危险。万一丢失的看板被找回来,那么就等于有两分订单,产量也会变成两倍,这就会造成过剩的库存浪费。
•
一句话惊醒了D.确实,他只是在自己认为可能会有的地方找过,而没有查找那些被忽视的角落,所以才总是找不到。于是,他又回到现场,在几乎想要放弃的时候,突然在
零件箱的底下发现了看板。
•
查看其他的零件箱才发现,原来看板都在箱子底下。经统计之后,他发现与丢失的看板数量刚好吻合。
•
D非常高兴,赶紧跑去汇报,可是大野先生的回话不是“做得不错”,而是“赶快想办法解决吧”。
3.经常深处现场,仔细观察,发现问 题,再寻找真正的原因
• 很多时候,我也向大野先生汇报“改善已经完成”,可是却总是被反问道:“结果能 否经得起推敲?”大野先生始终认为,应该把现场当做一张白纸,一切问题都去现场 寻找答案。
• 丰田财团的创始人丰田佐吉先生为了发明自动织机,也曾无数次亲自拜访技术熟练的 老技师,大野先生也是一样。改围的人说:“经常去现场观察,才能发现应该做什么,应该改善什么。”
•
不过,年轻的D为了不影响零件的按时供应,还是冒险选择了增加看板的方式。
•
大野先生知道这件事后非常生气,喊道:“为什么不去寻找丢失的看板,谁让你自作主张!赶快去把看板找回来!”
•
D垂头丧气地在工厂里仔细找了一个多小时也没有找到,于是回来向大野先生汇报说:“没有找到。”
•
谁知大野先生又生气地大喊:“才找了一个小时就跟我说没有找到!”
5.反复提问五次为什么
• D的工作当然不是寻找看板这么简单。大野先生要求他调查看 板丢失的原因,寻找改善的方法并防止问题的再次发生。
• D在调查之后发现,由于零件箱上的油非常多,所以贴在箱子 上的看板都被粘到了箱子底下。于是他提出把看板贴在箱子的 侧面。从此以后,看板就再没有丢失,看板方式也在那里彻底 地贯彻了下来。
式。
• 避免应急处理,应急只是一种暂时的敷衍。
4.采取对策了吗?
•
加入丰田有5年时间的员工D刚刚加入提高新车型生产效率的团队,也是第一次与大野先生有直接接触。虽然之前也听说过大野先生的严厉几乎到了恐怖的程度,可是实际工
作后才真正被他的执著和严谨所震撼。
•
大野先生命令他到某零件厂商那里去指导看板(生产、搬运时使用的传票)的使用方法。
• C赶忙又重新画了一个圈,然后大野先生只说了句“站在圆圈里仔细观察生产现场”就转身离开了。 • • 大野先生的命令向来没人敢反驳,虽然不理解其中的缘由,C也只能乖乖地服从。
• 到了中午,C忍不住想去厕所,于是就从圆圈中走了出来。可是没想到运气太差,刚好被路过的大 野先生发现。
1.仔细观察生产现场
2.重视改善的结果
• 某个生产厂家邀请大野耐一先生去参观指导。 大野先生向随行的陪同人员问道:“这项作业 大概需要多长时间?”
• “15分钟左右吧。”职员们一般对现场不太了 解,所以只是应付地回答了一下。可是没想到 大野先生却停下脚步,站在那里一直观察。15 分钟后,作业仍然没有结束。于是他对随行人 员说:“好像还没有结束啊。因为工作方法中 存在很多浪费才拖延了时间,所以赶快改善 吧!”
“为什么要走出去!” “只是想去一下厕所……” “吃完午饭后继续站在这里,出去的时候必须先和旁边的人打招呼。” 说完后大野先生又径自离去了。C感到很无奈,不过也只能老老实实地站到了傍晚。至于观察什么、为什么要观察,他也没有想太多,只是呆呆地站在那里瞪着眼睛看。 到了傍晚,大野先生走过来问:“发现什么问题了吗?” “还没有……”C只能胆怯地如实回答。 大野先生想了一下,又说:“今天可以下班了,明天继续站在这里观察。” C非常想问是要观察什么,可是一想到大野先生一定会说“自己去想”,所以话到嘴边又咽了回去。 第二天早晨,C又重新站在圆圈中。这回他好像发现了一些问题,不过,至于到底是什么却又说不清楚。 中午的时候,大野先生又走了过来。 “发现问题了吗?” “是的,不过好像说不清楚具体是什么问题。” C还是如实地回答。这回大野先生指着生产现场说:“看看工人们的工作方法。你说‘已经完成了改善’,可是你的改善却让他们的工作效率更低。既然已经发现了问题,那就赶紧 想办法解决吧”。 听到这些话,C确实感到了问题的所在。于是,他赶紧找现场的工人谈话,询问他们的意见,然后积极地加以解决。 C自以为改善已经完成,可是却没有观察改善的结果。虽然大野先生一眼就看穿了这个问题,但是并没有直接指出来,而是让他站在圆圈中自己观察。这深刻地教会了C两个问题: 用一天半的时间去观察现场,这种经历对C来说一定终身难忘,并对今后的工作产生了深远的影响。
•
D只得灰头土脸地回去了,可是仍然一无所获。D想着,既然已经找了这么长时间,如果再继续找下去可能又会被大野先生批评没有效率,所以赶紧又跑回来报告:“我已经
仔细地找了很长时间,可是仍然没有找到。”
•
这回大野先生温和地说:“你说没有找到,可是你想过为什么会找不到吗?”
•
一句话就把D问得低下了头。大野先生又说:“其实很简单,你总是在自己以为会有的地方去找。”
大野耐一: 精益生产的十条训诫
1.仔细观察生产现场
• 年轻的丰田员工C自认为改善工作做得非常好,于是就跑到大野先生那里去汇报:“改善工作已经 做好了。”
• 大野先生听了之后没有说话,和他一起来到生产现场。转了一会儿,大野先生指着一台车床说: “去那里画一个圆圈。”
• C觉得很奇怪,就在车床上画了个小圈。 • • “那么小的圈能站住人吗!重新画!”