第三章金属的塑性变形和加工硬化
机械工程材料练习题参考答案
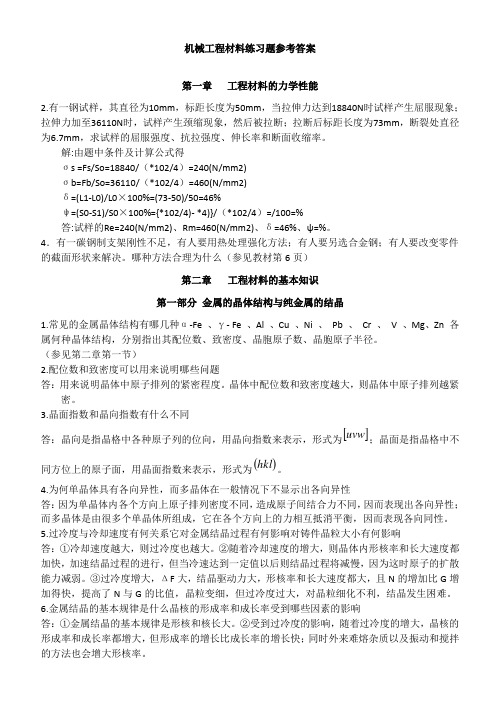
机械工程材料练习题参考答案第一章工程材料的力学性能2.有一钢试样,其直径为10mm,标距长度为50mm,当拉伸力达到18840N时试样产生屈服现象;拉伸力加至36110N时,试样产生颈缩现象,然后被拉断;拉断后标距长度为73mm,断裂处直径为6.7mm,求试样的屈服强度、抗拉强度、伸长率和断面收缩率。
解:由题中条件及计算公式得σs =Fs/So=18840/(*102/4)=240(N/mm2)σb=Fb/So=36110/(*102/4)=460(N/mm2)δ=(L1-L0)/L0×100%=(73-50)/50=46%ψ=(S0-S1)/S0×100%={*102/4)- *4)}/(*102/4)=/100=%答:试样的Re=240(N/mm2)、Rm=460(N/mm2)、δ=46%、ψ=%。
4.有一碳钢制支架刚性不足,有人要用热处理强化方法;有人要另选合金钢;有人要改变零件的截面形状来解决。
哪种方法合理为什么(参见教材第6页)第二章工程材料的基本知识第一部分金属的晶体结构与纯金属的结晶1.常见的金属晶体结构有哪几种α-Fe 、γ- Fe 、Al 、Cu 、Ni 、Pb 、Cr 、V 、Mg、Zn 各属何种晶体结构,分别指出其配位数、致密度、晶胞原子数、晶胞原子半径。
(参见第二章第一节)2.配位数和致密度可以用来说明哪些问题答:用来说明晶体中原子排列的紧密程度。
晶体中配位数和致密度越大,则晶体中原子排列越紧密。
3.晶面指数和晶向指数有什么不同答:晶向是指晶格中各种原子列的位向,用晶向指数来表示,形式为[]uvw;晶面是指晶格中不同方位上的原子面,用晶面指数来表示,形式为() hkl。
4.为何单晶体具有各向异性,而多晶体在一般情况下不显示出各向异性答:因为单晶体内各个方向上原子排列密度不同,造成原子间结合力不同,因而表现出各向异性;而多晶体是由很多个单晶体所组成,它在各个方向上的力相互抵消平衡,因而表现各向同性。
金属的塑性变形与再结晶(3)
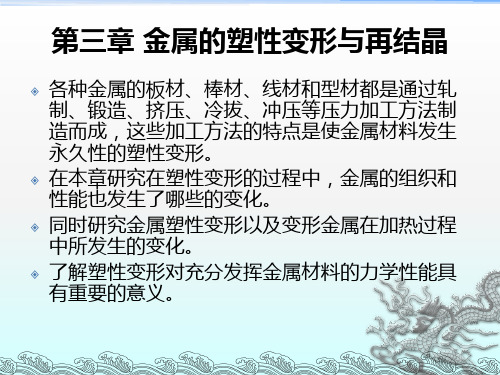
同一滑移面上若有大量的位错移出,则在晶体表 面形成一条滑移线。
位错在晶体中移动时所需切应力很小,因为当位错中心前 进一个原子间距时,一齐移动的只是位错中心少数原子, 而且其位移量都不大,形成逐步滑移,这就比一齐移动所 需的临界切应力要小得多,这称为“位错的易动性”。
研究表明,亚晶界的存在使晶体的变形抗力增加, 是引起加工硬化的重要因素之一。
3.形变织构
在塑性变形过程中,当金属按一定的方向变形量 很大时(变形量大于70%以上),多晶体中原来任 意位向的各晶粒的取向会大致趋于一致,这种有 序化结构叫作“变形织构”,又称为“择优取 向”,
金属材料的加工方式不同形成不同类型的织构: 拉拔时形成的织构称为丝织构,其特征是各个晶 粒的某一晶向平行于拉拔方向;轧制时形成的织 构称为板织构,其特征是不仅某一晶面平行于轧 制平面,而且某一晶向也平行于轧制方向。
3.变形引起的内应力
在金属塑性变形过程中,大约有10%的能量转化为内应力而残留在金属中, 使其内能增加。
这些残留于金属内部且平衡于金属内部的应力称为残余内应力。它是由于金 属在外力作用下各部分发生不均匀的塑性变形而产生的。
内应力一般可分为三种类型:Βιβλιοθήκη (1)宏观内应力(第一类内应力)
金属材料在塑性变形时,由于各部分变形不均匀,使整个工件或在较大的 宏观范围内(如表层与心部)产生的残余应力。
3.1.2多晶体金属塑性变形的特点
大多数金属材料是由多晶体组成的。 多晶体塑性变形的实质与单晶体一样。 要考虑到晶粒彼此之间在变形过程中的约束作用,以及晶界对塑性变形的影
第三章_金属冷塑性变形解析
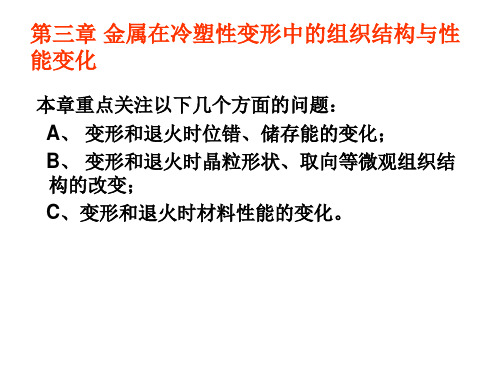
在变形过程中,随着变形程度的增加,位错密度 的变化规律如下:
bL
二、储存能的测定方法 储存能的确定是很难的。 其测量的方法有:热量法、X-射线法,还可根据 某些物理或机械性能来间接确定。
采用热量法测定储存能,我们还必须关注材料的 化学成分、晶粒尺寸、变形程度和变形温度。 总体情况是:1)变形程度增加,储存能增大; 2)变形方式不同,剩余功的变化会导致储存能的 变化;如铜,拉伸时是3.2-5.7 J/mol,压缩时是 3.8-8.3J/mol,拉拔时是-95J/mol。 3)低和中应变条件下,细晶的储存能比粗晶大, 但高应变条件下,储存能与晶粒无关。
轧制织构不仅有平行于轧制方向的特殊结晶学 方向,而且在轧制面上还有一个低指数平面。
面心立方晶格金属和合金有相当简单而又显著
的轧制织构,这就是{110}<112>;同时带有各不相
同的大量次级织构,在铜金属中,直到变形很大而
接近{112}<111>时,这些次级织构还都是杂乱的。
次级织构对再结晶织构退火的生长有影响。
图3.2 Stored energies of deformation for different orientations in the α fibre of cold-rolled iron and steel
3.2 金属组织结构的变化
• 金属塑性变形的物理实质基本上就是位错的运动, 位错运动的结果就产生了塑性变形。 • 在位错的运动过程中,位错、溶质原子、间隙位 置原子、空位、第二相质点都会发生相互作用, 引起位错的数量、分布和组态的变化。从微观角 度来看,这就是金属组织结构在塑性变形过程中 或变形后的主要变化。
第三章 金属在冷塑性变形中的组织结构与性 能变化
《金属材料与热处理》第三章金属的塑性变形对组织性能
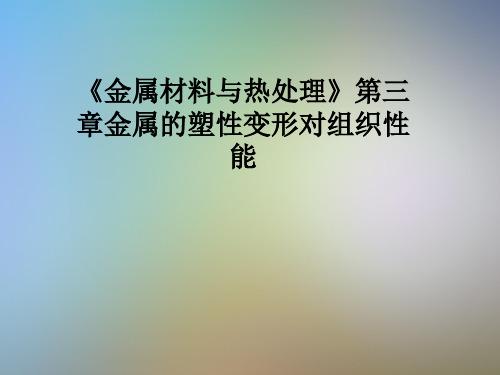
重冷塑性变形的金属,经1小时加热后能完全再结晶的 最低温度来表示。
最低再结晶温度:
T再=0.4T熔点 式中温度单位为绝对温度(K)。
8
学习情境三:金属的塑性变形对组织性能的影响 3.2
(3)再结晶温度影响因素:
1)变形程度 ➢2)金金属属再纯结度晶前:塑纯性度变越形高的, 最相低对再变结形晶量温称度为也预就先越变低形 度➢。3)预;加先热变速形度越大, 金属的晶体缺陷就越多, 组织越不 稳➢➢杂再定质结, 最和晶低合是再金一结元扩晶素散温(过度高程也熔, 需就点一越元定低素时;)间阻才碍能原完子成扩;散和晶 ➢界➢当提迁预高移先加, 可变热显形速著度度提达会高一使最定再低大结再小晶结后在晶,较最温高低度温再;度结下晶发温生度;趋于某 一➢高原稳纯始定度晶值铝粒。(越99粗.9大9,9再%结)最晶低温再度结越晶高温。度为80 ℃; ➢工业纯铝(99.0%)最低再结晶温度提高到290 ℃。
3
学习情境三:金属的塑性变形对组织性能的影响 3.2
3、热加工晶粒大小控制措施
(1).控制较低的加工终了温度 (2).控制较大的变形程度 (3).控制较快的冷却速度
0
学习情境三:金属的塑性变形对组织性能的影响 3.2
3、产生残余内应力 ➢定义:外力去除后,金属内部残留下来的应力。
产生原因:金属发生塑性变形时,内部变形不均匀, 位错、空位等晶体缺陷增多,会产生残余内应力。
➢1)宏观内应力 ➢2)微观残余应力 ➢3)晶格畸变应力
1
学习情境三:金属的塑性变形对组织性能的影响 3.2
3
学习情境三:金属的塑性变形对组织性能的影响 3.1
第一节 金属的塑性变形
第三章 材料的力学行为习题参考答案

第三章材料的力学行为习题参考答案一、解释下列名词1、加工硬化2、回复3、再结晶4、热加工5、冷加工答:1、加工硬化:随着塑性变形的增加,金属的强度、硬度迅速增加;塑性、韧性迅速下降的现象。
2、回复:加热温度较低时,变形金属中的一些点缺陷和位错,在某些晶内发生迁移变化的过程。
3、再结晶:被加热到较高的温度时,原子也具有较大的活动能力,使晶粒的外形开始变化。
从破碎拉长的晶粒变成新的等轴晶粒。
和变形前的晶粒形状相似,晶格类型相同,把这一阶段称为“再结晶”。
4、热加工:将金属加热到再结晶温度以上一定温度进行压力加工。
5、冷加工:在再结晶温度以下进行的压力加工。
二、填空题1、塑性变形的方式主要有滑移和孪生,而大多数情况下是滑移。
2、滑移常沿晶体中原子密度最大的晶面及晶向发生。
3、在体心立方晶格中, 原子密度最大的晶面是{110},有 6 个,原子密度最大的晶向是<111>,有2个;在面心立方晶格中, 原子密度最大的晶面是{111},有 4 个,原子密度最大的晶向是<111>,有3个。
两者比较,具有面心立方晶格的金属塑性较好,其原因是滑移系和滑移方向多。
4、多晶体金属的塑性变形由于受到晶界和晶粒位向的影响,与单晶体金属相比,塑性变形抗力增大。
5、金属在塑性变形时,随变形量的增加,变形抗力迅速增大,即强度、硬度升高,塑性、韧性下降,产生所谓加工硬化现象。
这种现象可通过再结晶加以消除。
6、变形金属在加热时,会发生回复、再结晶和晶粒长大三个阶段的变化。
7、冷绕成形的钢质弹簧,成形后应进行回复退火,温度约为250~300℃。
8、回复退火也称去应力退火。
9、冷拉拔钢丝, 如变形量大, 拉拔工序间应穿插再结晶退火,目的是消除加工硬化。
10、热加工与冷加工的划分应以再结晶温度为界线。
在再结晶温度以下的塑性变形称为冷加工;在再结晶温度以上的塑性变形称为热加工。
三、简答题1、产生加工硬化的原因是什么?加工硬化在金属加工中有什么利弊?答:⑴随着变形的增加,晶粒逐渐被拉长,直至破碎,这样使各晶粒都破碎成细碎的亚晶粒,变形愈大,晶粒破碎的程度愈大,这样使位错密度显著增加;同时细碎的亚晶粒也随着晶粒的拉长而被拉长。
《材料成型技术与基础》全套PPT电子课件教案-第03章 单晶体与多晶体的塑性变形等
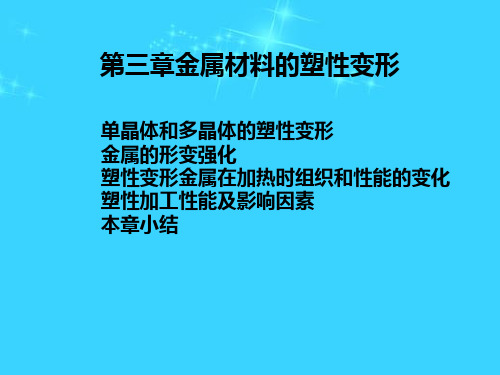
拉拔时金属应力状态
第三章金属材料的塑性变形
本章小结
锻造、轧ቤተ መጻሕፍቲ ባይዱ、挤压、冲压等都是塑性变形。这些 塑性变形的目的不仅是为了得到零件的外形和尺寸, 更重要的是为了改善金属的组织和性能。
塑性变形的主要形式是滑移和孪生,是在切应力 的作用下进行的,塑性变形将产生形变强化,形成纤 维组织,具有各向异性。塑性变形后的 金属加热时会 产生回复或再结晶及晶粒长大,其形变强化现象消除。
滑移特点:①滑移是在切 应力作用下完成的;②滑 移时移动的距离是原子间 距的整数倍;③滑移的同 时由于正应力组成的力偶 作用,推动晶体转动,力 图使滑移面转向与外力一 致的方向。④滑移的实质 是位错运动的结果。因此 滑移的实际临界切应力远 远大于理论临界切应力。
第三章金属材料的塑性变形
单晶体滑移变形示意图
定义:经冷变形的金属当加热到T再时,会在变形最激 烈的区域自发形成新的细小等轴晶粒,叫做再结 晶这一过程实质上也是一个形核和长大的过程, 但晶格类型不变,只是改变了晶粒外形. T再T熔
※金属再结晶后,消除了残余应力和形变强化现象 晶粒长大 冷变形和热变形 金属纤维组织及其应用
第三章金属材料的塑性变形
第三章金属材料的塑性变形
单晶体和多晶体的塑性变形 金属的形变强化 塑性变形金属在加热时组织和性能的变化 塑性加工性能及影响因素 本章小结
第三章金属材料的塑性变形
单晶体的塑性变形 1.滑移 2.孪生 1.晶粒取向对塑性变形的影响 2.晶界对塑性变形的影响
第三章金属材料的塑性变形
锌单晶体的滑移变形示意图
第三章金属材料的塑性变形
未变形 弹性变形 弹塑性变形 塑性变形
位错运动引起的滑移变形示意图
第三章金属材料的塑性变形
《材料力学性能》第三章塑性变形
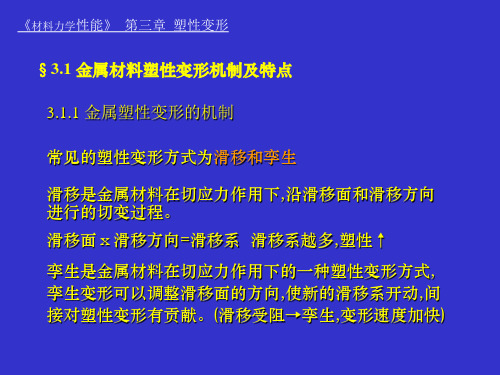
3.4.3 弯曲试验
1、弯曲试验分为三点弯曲和四点弯曲,试样主要有矩形 截面和圆形截面。
《材料力学性能》 第三章 塑性变形
试验时,在试件跨距的中心测定绕度,绘成P~fmax关系 曲线,即弯曲图。
由左图可知,塑性材料的 力学性能由拉伸试验测定, 而不采用弯曲试验;脆性 材料根据弯曲图求得:
Mb bb ; M b Pb L 4 , Pb K 2 W 3 W d 0 32, bh2 6
生产上用得最多的是A级、B级和C级,即HRA(金钢石圆锥压头、 60kgf负荷),HRB(1/16"钢球压头、100kgf负荷)和HRC(金钢石圆 锥压头、150kgf负荷),而其中又以HRC用得最普遍。
《材料力学性能》 第三章 塑性变形
洛氏硬度的测量方法
洛氏硬度试验过程示意图
《材料力学性能》 第三章 塑性变形
2、洛氏硬度 洛氏硬度的测量原理 洛氏硬度是以压痕陷凹深度作为计量硬度值的指标。
洛氏硬度的压头分硬质和软质两种。硬质的由顶角为120°的金 钢石圆锥体制成,适于测定淬火钢材等较硬的金属材料;软质的 为直径1/16“(1.5875mm)或1/8”(3.175mm)的钢球,适于退火钢、 有色金属等较软材料硬度值的测定。洛氏硬度所加负荷根据被试 金属本身硬软不等作不同规定,随不同压头和所加不同负荷的搭 配出现了各种称号的洛氏硬度级。
《材料力学性能》 第三章 塑性变形
维氏硬度
维氏硬度试验法开始于1925年。 维氏硬度的测定原理和布氏硬 度相同,也是根据单位压痕陷凹 面积上承受的负荷,即应力值 作为硬度值的计量指标。
所不同的是维氏硬度采用锥面夹角为136°的四方 角锥体,由金钢石制成。
《材料力学性能》 第三章 塑性变形
8.金属的塑性变形和加工硬化

8.金属的塑性变形和加工硬化1.加工硬化:金属在冷塑性变形过程中,随着变形程度增加,其强度和硬度提高而塑性(延伸率、面缩率)则降低,这种现象称为加工硬化。
2.面心立方金属单晶体的应力-应变曲线。
ⅰ硬化系数θ较小,一般认为在此阶段只有一个滑移系统起作用,强化作用不大,称位易滑移阶段。
ⅱ硬化系数θ最大且大体上是常数,对于各种面心立方金属具有相同的数量级,故称为线性硬化阶段。
ⅲ硬化系数θ随变形量的增加而逐渐减小,故称为抛物线强化阶段。
3.对应力-应变曲线影响的主要因素。
4.面心立方金属形变单晶体的表面现象。
ⅰ除了照明特别好(暗场),用光学显微镜一般看不到滑移线。
ⅱ光学显微镜在暗场下可以看到滑移线,线长随应变的增加而递减,电镜观察到的单个滑移线比第一阶段粗而短。
ⅲ出现滑移带,带中包括许多靠的很近的滑移线,应变增加,带间不在增加新的线,形变集中在原来的带中,滑移带端出现了碎化现象。
5.面心立方金属单晶体的加工硬化理论。
6.多晶体是通过晶界把取向不同,形状大小不同,成分结构不同的晶粒结合在一起的集合体。
晶界对塑性变形过程的影响,主要是在温度较低时晶界阻碍滑移进行引起的障碍强化作用和变形连续性要求晶界附近多系滑移引起的强化作用。
ⅰ障碍强化作用ⅱ多系滑强化作用ⅲ多晶体变形的不均匀性7.金属多晶体应力-应变曲线ⅰ点阵类型和金属种类的影响ⅱ变形温度于应变速率的影响a.随温度升高可能开动新的滑移系统。
b.随温度升高可在变形过程中出现回复和再结晶现象,引起金属软化,减弱加工硬化。
c.随温度升高可能出现新的塑性变形机理,使加工硬化减弱。
8.细化晶粒对金属材料的力学性能有何影响?有哪些途径可以细化晶粒?细化晶粒可以提高韧性,有助于防止脆性断裂发生,可以降低脆性转化温度,提高材料使用范围,在低强度钢中,利用细化晶粒来提高屈服强度有明显效果。
细化途径:(1)改变结晶过程中的凝固条件,尽量增加冷却速度,另一方面调节合金成分以提高液体金属过冷能力,使形核率增加,进而获得细化的初生晶粒。
- 1、下载文档前请自行甄别文档内容的完整性,平台不提供额外的编辑、内容补充、找答案等附加服务。
- 2、"仅部分预览"的文档,不可在线预览部分如存在完整性等问题,可反馈申请退款(可完整预览的文档不适用该条件!)。
- 3、如文档侵犯您的权益,请联系客服反馈,我们会尽快为您处理(人工客服工作时间:9:00-18:30)。
3.1 单晶体的塑性变形
加工硬化-金属塑性变形中,变形程度增 加,其强度和硬度提高而塑性则降低。
金属在冷塑性变形过程中,为什么会出 现强化现象?如何实现强化?受哪些因素 影响以及其强化的变化规律如何呢?
首先来分析纯金属单晶体的塑性变形过程
图3.1 典型金属的应力-应变曲线
• 要实现塑性变形从一个晶粒传递到下一个晶粒, 就必须外加以更大的力,这就是晶界的障碍强 化作用。
2.多系滑移强化作用
• 多晶体材料中,一个晶粒产生滑移变形而不破坏 晶界连续性,相邻的晶粒必须有相应协调变形才 行。多晶体的塑性变形,一旦变形传播到相邻的 晶粒,就产生了多系滑移。位错运动遇到的障碍 比单系滑移多,阻力要增加。而且随着变形量的 增加,阻力增加很快,这就是多系滑移所产生的 强化作用。
第Ⅱ阶段:光学显微镜在暗场下可以看到滑移线, 线长随应变的增加而递减。电镜观察到的单个滑移 线比第1阶段的粗而短。
第Ⅲ阶段:出现滑移带,带中包括靠得很近的滑移 线。应变增加时,带间不再增加新线,形变集中在 原来的带中,带端出现了碎化现象。所谓碎化现象, 系指相互连接着的滑移带的侧向移动现象。
二、 BCC晶格单晶体的塑性变形 高纯度的BCC金属室温的应力应变曲线与FCC 金属的曲线相似。 如果含有微量杂质原子或在低温形变时,将产 生明显的屈服现象而得不到三个阶段的硬化曲 线。
2)在晶粒边界处变形程度都比晶粒内部小, 这既表明晶界处较难变形;也显示出晶界在促 进变形的不均匀分布上起很大作用。
• 晶界对塑性变形过程的影响,主要是在温度较 低时晶界阻碍滑移进行引起的障碍强化作用和 变形连续性要求晶界附近多系滑移引起的强化 作用。
1.晶界的障碍强化作用
• 由于晶界两侧晶粒取向不同,滑移从一个晶粒 延伸到下一个晶粒是不容易的,晶界存在着阻 碍塑性变形进行的作用。
加工硬化第三阶段有加工软化现象。
Cottrell和Stoke发现,如纯铝在90K变形至第 二阶段,继之升高温度,于室温下再进行实验 时,就有明显的屈服降落。这说明低温时的硬 化会部分地突然去除,显然低温变形时形成的 位错结构是不稳定的,到室温时发生某种变化 。由此证明,铝在室温下出现的屈服点,并不 是由于点缺陷的扩散或杂质原子偏聚到位错线 ,钉扎了位错所造成的。
由以上实验结果可知,易滑移阶段只在主滑移 系统上运动,第二阶段次滑移系统上的位错参 与了滑移变形,第三阶段则产生了螺位错的交 滑移。
2、影响应力一应变曲线的主要因素
1) 取向的影响
FCC金属单晶体的应力一应变曲线形状和试样的 取向关系很密切。
图3.3 单晶铝不同取向拉伸时 的应力-应变曲线 ---室温;—77K
图3.4 铌单晶体的加工硬化
三、HCP晶格单晶体的塑性变形 HCP金属的应力应变曲线的第Ⅰ阶段硬化率 θⅠ与FCC金属相近,但通常限于一组基面滑移 ,出现很长的第Ⅰ阶段,远远超过其他结构的 晶体,以致其第Ⅱ阶段还未充分发挥时试样就 已经断烈了。但条件合适时也会出现完整的三 个阶段。
图3.5 锌单晶的加工硬化
3) 温度的影响
温度升高时,0略有降低, Ⅲ而则显著降低, Ⅱ,Ⅲ变短, Ⅰ和Ⅱ与温度关系不大,而Ⅲ 则随温度升高而减小。
3、FCC金属形变单晶体的表面现象
面心立方晶体研究发现,无论层错能高低,只要是 处于同一个阶段形变,都具有相同特征的表面现象。
各阶段观测研究的结果简述如下:
第1阶段;用光学显微镜一般看不到滑移线。
3.2 金属多晶体的塑性变形
使用的大多数金属材料都是多晶体。多晶体是 通过晶界把取向不同、形状大小不同、成分结 构不同的晶粒结合在一起的集合体。多晶体的 塑性变形是许多单晶体塑性变形的集合。但是, 由于组成多晶体的各个晶粒取向不同,由于存 在着晶界及晶粒大小有差别,使得多晶体的塑 性变形和强化有许多不同于单晶体的特点。
2)金属的层错能和纯度的影响
层错能的高低影响到第Ⅲ阶段前的变形发展。 室温下的层错能高的金属,扩展位错很容易束 集及产生交滑移,Ⅱ值不超过4%-5%,应力 应变曲线很快进入第Ⅲ阶段;层错能低的金属, 因为扩张位错不易束集,位错交割困难,不易 产生多系滑移,则 Ⅱ可能超过20%以上。 杂质原子明显地影响到第Ⅰ阶段的长度。主要 从杂质原子对层错能影响和形成弥散的第二相 两个方面。
在各种结构的金属中,面心立方金属的硬化机 理研究得比较深入,下面重点以FCC金属为例 加以说明。
一、FCC晶格单晶体的塑形变形 1、应力一应变曲线
图3.2 面心立方单晶体典型的应力-应变曲线
典型曲线的三个阶段特征: 第一阶段特征: 1)加工硬化率( Ⅰ)很低; 2)滑移线细而长且均匀分布; 3)加工硬化速率对晶体位向和杂质十分敏感; 4)滑移线上的位错数可以很大; 5)三类晶体结构中,没有螺位错存在,这可能 是由于在相邻滑移面上两个异号螺位错相遇时, 由于交滑移而湮灭了。只有在层错能低的合金( 如Cu-10%Al)中才可以看到螺位错。
其位错组态常呈刃位错多极子排列。
第二阶段特征:
1)加工硬化率( Ⅱ )很高,且和应变量呈线 性关系;
2)加工硬化率对金属的种类或合金的成分(只 要为面心立方晶体)不敏感,对晶体的位向也不 敏感;
3)滑移线长度随应变量有如下规律:
l2
2
4)每根滑移线上位错数大致不变;5)其位错结构缠结, Nhomakorabea成胞状结构。
一、晶界在塑性变形中的作用 为了显示晶界对变形的影响,可将由几个晶粒 组成的大晶体承受变形并观察和测量它的变形 分布情况。如下图:
图3.6 总变形量相同时多晶铝的几个晶粒各处的实际变形量
由图可知: 1)总变形量相同时,在多晶体内,不仅各晶 粒所承受的实际变形量不同,而且每个晶粒内 部各处的实际变形程度也不一致。
第三阶段特征:
1)加工硬化速率( Ⅲ )降低,曲线呈抛物 线型;
2)变形温度和层错能对第三阶段有影响;
3)该阶段是一个热激活过程,该阶段开始时 的应力随温度的增加而快速减少;
4)内部组织变化的特征是:出现了滑移带。 随着变形量的增加,滑移都集中于滑移带内, 在滑移带之间不再出现新的滑移痕迹,而在滑 移带内可以看到交滑移。