激光复合焊应用说明
激光复合焊工艺在造船厂的应用(4)
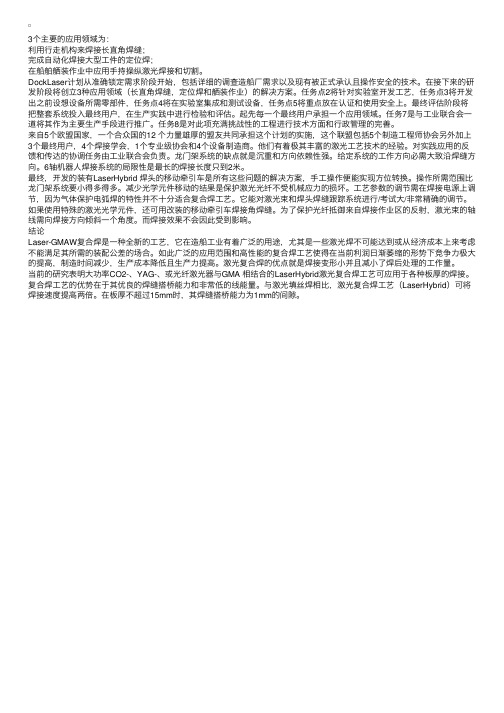
3个主要的应⽤领域为:利⽤⾏⾛机构来焊接长直⾓焊缝;完成⾃动化焊接⼤型⼯件的定位焊;在船舶舾装作业中应⽤⼿持操纵激光焊接和切割。
DockLaser计划从准确锁定需求阶段开始,包括详细的调查造船⼚需求以及现有被正式承认且操作安全的技术。
在接下来的研发阶段将创⽴3种应⽤领域(长直⾓焊缝,定位焊和舾装作业)的解决⽅案。
任务点2将针对实验室开发⼯艺,任务点3将开发出之前设想设备所需零部件,任务点4将在实验室集成和测试设备,任务点5将重点放在认证和使⽤安全上。
最终评估阶段将把整套系统投⼊最终⽤户,在⽣产实践中进⾏检验和评估。
起先每⼀个最终⽤户承担⼀个应⽤领域。
任务7是与⼯业联合会⼀道将其作为主要⽣产⼿段进⾏推⼴。
任务8是对此项充满挑战性的⼯程进⾏技术⽅⾯和⾏政管理的完善。
来⾃5个欧盟国家,⼀个合众国的12 个⼒量雄厚的盟友共同承担这个计划的实施,这个联盟包括5个制造⼯程师协会另外加上3个最终⽤户,4个焊接学会,1个专业级协会和4个设备制造商。
他们有着极其丰富的激光⼯艺技术的经验。
对实践应⽤的反馈和传达的协调任务由⼯业联合会负责。
龙门架系统的缺点就是沉重和⽅向依赖性强。
给定系统的⼯作⽅向必需⼤致沿焊缝⽅向。
6轴机器⼈焊接系统的局限性是最长的焊接长度只到2⽶。
最终,开发的装有LaserHybrid 焊头的移动牵引车是所有这些问题的解决⽅案,⼿⼯操作便能实现⽅位转换。
操作所需范围⽐龙门架系统要⼩得多得多。
减少光学元件移动的结果是保护激光光纤不受机械应⼒的损坏。
⼯艺参数的调节需在焊接电源上调节,因为⽓体保护电弧焊的特性并不⼗分适合复合焊⼯艺。
它能对激光束和焊头焊缝跟踪系统进⾏/考试⼤/⾮常精确的调节。
如果使⽤特殊的激光光学元件,还可⽤改装的移动牵引车焊接⾓焊缝。
为了保护光纤抵御来⾃焊接作业区的反射,激光束的轴线需向焊接⽅向倾斜⼀个⾓度。
⽽焊接效果不会因此受到影响。
结论Laser-GMAW复合焊是⼀种全新的⼯艺,它在造船⼯业有着⼴泛的⽤途,尤其是⼀些激光焊不可能达到或从经济成本上来考虑不能满⾜其所需的装配公差的场合。
激光-MIG复合焊接技术

02
激光-MIG复合焊接技术 优势
高效率
01
激光-MIG复合焊接技术通过结合 激光的高能量密度和MIG焊接的 填充特性,实现了快速、高效的 焊接过程。
02
与传统的焊接方法相比,激光MIG复合焊接技术能够显著减少 焊接时间和成本,提高生产效率 。
高质量
激光-MIG复合焊接技术能够获得具 有优异力学性能和美观外观的焊接接 头,如高强度、高致密性和低变形等 。
05
激光-MIG复合焊接技术 未来发展展望
技术创新
激光与MIG焊接工艺的优化
通过改进激光与MIG焊接的工艺参数,提高焊接质量和效率,降低生产成本。
新型激光器与MIG焊机的研发
研发更高功率、更稳定、更可靠的激光器和MIG焊机,以满足更广泛的应用需求。
智能化与自动化焊接系统的研发
利用先进的传感器、控制系统和人工智能技术,实现焊接过程的智能化和自动化,提高焊 接质量和效率。
1 2 3
激光与电弧的相互作用机制
激光与电弧在复合焊接过程中如何相互影响,提 高焊接效率和质量,是亟待解决的关键问题。
焊接过程的稳定性
激光和电弧的协同作用导致焊接过程变得更加复 杂,如何保持焊接过程的稳定性和一致性是一个 挑战。
高效能量传输与控制
如何实现激光和电弧的高效能量传输与控制,以 获得更好的焊接效果,是另一个需要克服的技术 瓶颈。
THANKS FOR WATCHING
感谢您的观看
市场前景
市场需求增长
随着制造业的发展和技术的进步, 激光-MIG复合焊接技术的应用领 域不断扩大,市场需求也将持续 增长。
技术竞争加剧
随着激光-MIG复合焊接技术的不 断发展和应用拓展,技术竞争将 更加激烈,企业需要不断提高技 术水平和创新能力,以保持竞争 优势。
3.22 激光电弧复合焊的应用讲解

4)LAH与其它焊接方法对比
表1 LAH与其它焊接方法相关参数对比
5)工业实际应用
(1)大众Phaeton(辉腾)车型 激光-MIG复合焊:激光功率2.9KW、Ar保护、焊速4.2m/min.,
焊丝AlSi12,送丝速度4.2m/min.焊缝长度达357cm。
(2)丹麦Odense造船厂 激光 - 电弧复合焊代替激光焊,装配精度从 0.4mm 降到 1mm,节 省机加成本且提高效率。
3. 小结
激光可与多种电弧组成复合焊,以激光 -MIG 复合焊研究和
应用最多,特别是对铝板和中厚钢板的焊接适应性强、对焊
前装配要焊接过程是否采用填丝主要考虑的影响因素是什么?
2)为什么激光 -MIG 复合焊焊接铝合金比单独采用激光焊接铝
合金有明显优势?
(2)激光与MIG复合焊
a:填丝焊接过程稳定,改善冶金性能 b:提高间隙适应性,改善成形和组织
c:减少热输入,稳定焊接过程
图3 激光-MIG复合焊的实际焊接
(3)激光与等离子弧复合焊
a:提高焊速,提高焊接效率 B:延长冷却时间,减少硬化和残余应力的敏感性
实例:采用该方式对0.16mm锌板的焊速高达90m/min.,单独用 激光焊在48m/min.时则不稳定,产生缺陷。
图1 激光-电弧同轴复合示意图
2)旁轴式
激光和电弧不在同一轴线上(图2,非对称热源)
图2 激光-电弧旁轴复合示意图
3)激光与不同电弧的复合
(1)激光与TIG复合焊 a:低功率激光器代替高功率焊接
b: 薄件高速焊接
c:增加熔深,改善成形 d:降低装配要求 实例:CO2激光器功率0.8KW,TIG电流为90A,焊速为2m/min.时, 相当于5KW激光器焊接能力。
激光复合焊在造船中的应用

激光复合焊在造船中的应用激光束焊接以其焊速快、变形小和易实现自动化等优点而广泛应用于结构钢焊接中。
电弧激光混合气体保护焊的主要优点是:在焊接较宽根部间隙时,弥合根部间隙能力大大增强,焊接速度大大提高。
激光焊和电弧焊长期以来都用于工业生产,在材料连接成形技术领域应用广泛。
根据能量传输的物理过程和所获得的能量流不同,这两种工艺各有各的应用领域。
激光焊是通过一个光导纤维电缆或反射镜,将能量以高能红外相干辐射的方式从激光源传输到加工工件。
电弧焊是通过弧柱,使热量以高能电流的方式传递到工件。
激光辐射得到的焊接热影响区非常窄且热影响区的深宽比(深焊效应)很大。
由于激光焊工艺的聚焦直径很小,致使它的间隙弥合能力较低,但从另一个方面来说,激光焊可以达到很高的焊接速度。
电弧焊工艺能量密度较低,但它能在工件表面形成较大的焦点,焊接速度较低。
将这两种工艺相结合,取长补短,发挥各自优势,不仅能获得较好的质量优势和生产效益,而且降低了成本。
这种复合焊接工艺在造船业中受到青睐。
另外不能忽视的原因是,该工艺焊缝容许的公差大、焊接速度较高,且能够达到良好的机械性能指标。
自20世纪70年代以来,人们就已经知道了如何将激光焊与电弧焊合并成一个混合焊接工艺,但是此后很长一段时间都没有开展进一步的研究工作。
目前,研究者已将注意力转移到该课题,并试图在激光焊和电弧焊的复合焊工艺中将两者的优势结合起来。
然而,在早期激光光源设备还未被证明适合于工业应用;如今,在很多制造企业,激光光源设备已成为标准设备了。
我们将激光焊与其他焊接工艺结合称之为“复合”焊接工艺。
这意味着激光束和电弧同时作用于一个焊接区,相互影响,相互支持。
研究目的之一在于弄清楚该复合工艺特性对焊接性能有多大提高。
运用CO2激光/电弧(GMAW熔化极气体保护焊)复合焊工艺的一个典型领域是造船业。
本文主要展示和讨论复合焊在造船领域的应用前景。
1 激光束焊接工艺的注意事项激光束焊不仅需要较高的激光功率,而且需要高品质的光束,才能获得理想的“深焊效应”。
激光焊接使用说明

激光焊接使用说明
激光焊接是一种利用激光束对材料进行焊接的技术。
激光焊接具有高能量密度、高精度、高速焊接等特点,广泛应用于金属材料的焊接加工领域。
以下是激光焊接的使用说明:
1. 准备工作:首先,确定待焊接的材料类型和厚度,选择合适的激光焊接机器。
然后,确保焊接机器的工作环境清洁、稳定,并进行必要的校准和调试。
2. 材料准备:将待焊接的材料进行清洁、除油、除尘等处理。
对于不同类型的材料,可能需要进行预处理,如表面涂层、切割等。
3. 安全措施:在进行激光焊接时,务必佩戴防护眼镜,以防止激光对眼睛造成伤害。
确保工作区域没有其他人员进入或对焊接过程产生干扰。
4. 焊接参数调整:根据焊接材料和厚度的不同,需要调整激光焊接机器的参数,如功率、波长、焦距等。
通常,通过测试焊接样品来确定最佳参数。
5. 焊接操作:将激光焊接机器对准焊接部位,调整焦距和焊接速度,开始焊接。
保持稳定的手持或固定焊接头,保持均匀的焊接速度和焊接压力,以确保焊接质量。
6. 焊接质检:完成焊接后,检查焊缝的质量和强度。
如果需要,可以进行非破坏性测试或破坏性测试来验证焊接的质量。
7. 后续处理:根据需要,可以进行后续处理工艺,如抛光、清洗、热处理等,以达到所需的外观和性能要求。
需要注意的是,激光焊接是一项高精密度的工艺,对操作者的要求较高。
在使用前,务必熟悉和掌握激光焊接机器的操作手册,并在安全规范下进行操作。
激光电弧复合焊在钢结构中的应用

激光电弧复合焊在钢结构中的应用下载提示:该文档是本店铺精心编制而成的,希望大家下载后,能够帮助大家解决实际问题。
文档下载后可定制修改,请根据实际需要进行调整和使用,谢谢!本店铺为大家提供各种类型的实用资料,如教育随笔、日记赏析、句子摘抄、古诗大全、经典美文、话题作文、工作总结、词语解析、文案摘录、其他资料等等,想了解不同资料格式和写法,敬请关注!Download tips: This document is carefully compiled by this editor. I hope that after you download it, it can help you solve practical problems. The document can be customized and modified after downloading, please adjust and use it according to actual needs, thank you! In addition, this shop provides you with various types of practical materials, such as educational essays, diary appreciation, sentence excerpts, ancient poems, classic articles, topic composition, work summary, word parsing, copy excerpts, other materials and so on, want to know different data formats and writing methods, please pay attention!激光电弧复合焊在钢结构中的应用1. 简介激光电弧复合焊(LaserArc Hybrid Welding,简称LAHW)作为一种先进的焊接技术,在钢结构制造中具有广泛的应用前景。
激光复合焊接及其应用ppt课件
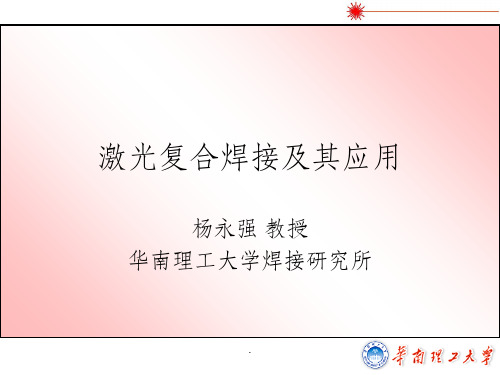
SWEDEN
.
MAG/HYBRID 接头性能对比 (3mm板)
焊丝 OK 12.51 母材 SB 45 含硼钢. (2-8mm) 20kW CO2激光器+MAG
Phaeton 2002 德国大众汽车 辉腾豪华铝合金轿车
车门焊缝总长 4980mm, 其中激光-MIG复. 合焊缝48条, 长3570mm, 激光焊缝11条, 长1030mm, MIG焊缝7条, 长380mm
不同焊接方法双边焊的热输入量对比
(5mm 碳钢板角接接头)
150
250
200
100
150
100 50
50
0
MA1G
TW2IN
HYB3RID
LA4SER
0 M A1G
T W2I N
H Y3B R I D
120 %
100
不同焊接方法单边焊的相对热输入量
与相对横向收缩辆对比
(5mm 碳钢板角接接头)
200 %
.
激光稳定小电流CO2短路过渡气体保护焊
电压
电流
电压
Байду номын сангаасCO2气体保护焊短路过程波形图(I=50A v=1.5m/min)
电流
.
激光功率1200W复合CO2气体保护焊短路过程波形图(I=50A v=1.5m/min)
激光-CO2短路电弧复合热源焊接电流、电压波形图 Ø1.0mm, I=80A, U=16V, V=0.9m/min, CO2 20 l/min, 晶
Audi A8
.
激光-电弧复合焊接在汽车零件制造中的应用
.
40Cr减震器缸体焊接
技术要求:1.
2.
3. 4. 5.
激光焊接使用说明
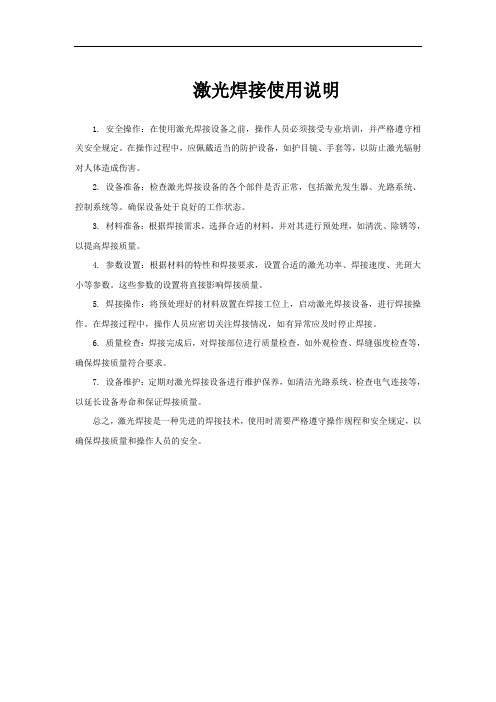
激光焊接使用说明
1. 安全操作:在使用激光焊接设备之前,操作人员必须接受专业培训,并严格遵守相关安全规定。
在操作过程中,应佩戴适当的防护设备,如护目镜、手套等,以防止激光辐射对人体造成伤害。
2. 设备准备:检查激光焊接设备的各个部件是否正常,包括激光发生器、光路系统、控制系统等。
确保设备处于良好的工作状态。
3. 材料准备:根据焊接需求,选择合适的材料,并对其进行预处理,如清洗、除锈等,以提高焊接质量。
4. 参数设置:根据材料的特性和焊接要求,设置合适的激光功率、焊接速度、光斑大小等参数。
这些参数的设置将直接影响焊接质量。
5. 焊接操作:将预处理好的材料放置在焊接工位上,启动激光焊接设备,进行焊接操作。
在焊接过程中,操作人员应密切关注焊接情况,如有异常应及时停止焊接。
6. 质量检查:焊接完成后,对焊接部位进行质量检查,如外观检查、焊缝强度检查等,确保焊接质量符合要求。
7. 设备维护:定期对激光焊接设备进行维护保养,如清洁光路系统、检查电气连接等,以延长设备寿命和保证焊接质量。
总之,激光焊接是一种先进的焊接技术,使用时需要严格遵守操作规程和安全规定,以确保焊接质量和操作人员的安全。
- 1、下载文档前请自行甄别文档内容的完整性,平台不提供额外的编辑、内容补充、找答案等附加服务。
- 2、"仅部分预览"的文档,不可在线预览部分如存在完整性等问题,可反馈申请退款(可完整预览的文档不适用该条件!)。
- 3、如文档侵犯您的权益,请联系客服反馈,我们会尽快为您处理(人工客服工作时间:9:00-18:30)。
激光复合焊应用说明
大族激光科技产业集团股份有限公司
目录
1激光电弧复合焊设备说明 (3)
2激光电弧复合焊原理 (3)
3操作说明 (4)
4基本焊接工艺说明 (5)
1激光电弧复合焊设备说明
激光电弧复合焊设备主要由以下部分组成,包括:激光器、弧焊机及送丝机、机器人(机床)及控制器、复合焊接头等,如下图所示。
弧焊机和激光器与机器人(机床)控制器相连形成一个整体。
2激光电弧复合焊原理
在激光电弧复合焊接过程中,焊丝、激光束、母材及焊接方向之间的关系如下图所示:
激光电弧复合焊原理图
在上图中,d1为焦点与工件的距离;d2为焊丝与激光光斑中心的距离(光丝距离),为保证焊接质量,需调整上述两参数;d3为电极与母材表面之间的距离,决定了焊丝的干伸长度。
d1值的大小决定了激光照射在母材表面光斑的大小,影响焊接的深度,同时与激光焊接时表面成型及飞渐情况有关。
d2距离的大小决定了电弧熔池与激光熔池两者之间的关系,为了得到最佳
的焊接效率及表面成形,特别是在进行全透焊接时,控制d2的大小很重要。
d3距离过大一方面会使送丝变得不稳定,另一方面会使电弧过长,易产生电弧摆动,出现烧边现象,使得焊接过程不稳定;过小则焊接电弧太短,易形成短路。
一般控制d3约15mm,在焊接过程中所通过焊接电源的弧长修正进行微调,从而保证焊接的稳定性。
焊接方向为前送丝,即电弧在前,激光在后(铝合金焊接相反),焊接方向与焊缝成型及间隙适应性有关,同时前送丝可减少焊接烟尘对未焊接头的污染(吹气方向决定)。
送丝角度约45度,角度对弧焊的深度有一定的影响,相对小角度而言,大角度可获得较大的熔深。
在进行确定材料的焊接时,首先需确定激光焊接深度的参数及电弧稳定焊接的参数,特别是电弧焊接的参数,因为电弧稳定与否直接影响焊缝的外观。
根据不同的工艺需求,还需确定激光与电弧熔池之间的位置关系,即d2的大小。
d2确定的是激光与电弧之间相互作用的效果,如下图所示:
d2约为2mm时(图C),激光与电弧相互作用的效果最为明显,即电弧对母材的加热更有利于激光的吸收,同时电弧对激光等离子云起到一定的抑制效果,可增加激光的熔深,而激光对电弧又可起到一定的引导作用,使电弧更加稳定。
所以激光与电弧不是简单的叠加,而是相互作用,合适的距离可使激光与电弧的作用最为明显,从而获得最大的熔深。
3操作说明
本司采用的弧焊机为福尼斯TPS系列焊机,与自熔焊接相比,复合焊操作主要是增加了弧焊机、送丝机、复合焊接头的操作。
弧焊机的操作详见《RCU5000i操作说明》。
送丝机的操作详见《送丝机操作说明》。
复合焊接头由激光焊接头和弧焊枪组合而成,见下图:
激光焊接头与弧焊枪的相对位置关系可通过复合焊接头上的螺孔进行上下、左右、前后方向调整,螺孔位置见下图:
弧焊枪的操作说明详见《焊枪操作说明》。
4基本焊接工艺说明
在进行复合焊接之前,可先进行纯电弧焊接调试,设置焊丝干伸长度约15mm,焊丝进丝角度约450,焊接过程中可能遇到的问题主要有:
(1)电弧起弧不稳定、起始位置焊缝过高、收弧弧坑等;
(2)焊接过程飞溅大;
(3)焊缝成形差,表面粗糙、咬边、气孔等,如下图所示:
上述负象主要在于起弧方式、起弧电流、收弧电流、送丝速度及弧长的设定。
由于焊接过程电弧采用一元化控制,即通过确定送丝速度来确定焊接电流及电压,要想提高焊接电流则需提高送丝速度。
在送丝速度较低时,由于焊接电流较
低,焊接过程中熔滴过渡不稳定,熔滴不能形成稳定的射流过渡,所以焊接过程电弧不稳定,飞溅大。
同时,弧长对于焊接过程的稳定性也起到了重要作用,电弧过短则焊接时容易形成短路且飞溅大,造成不稳定;电弧过长,则容易形成断路,并且焊缝较宽、焊深浅,无法实现高速焊接,通过调节焊机的弧长修正功能可实现弧长在一定范围内的修正(调节范围为-30%~30%),且调节过程可实现在线连续调节,即在焊接过程中连续调节进行弧长修正,通过观察焊接过程变化来确定调节量。
调节面板如下图:
a b
上图a中,设置选项包括Job号(焊接时调用的程序号)、送丝速度、弧长修正、脉冲修正、焊枪开关模式、工艺,说明如下:
(1)送丝速度决定了焊接电流及电压,时间决定了焊接时焊丝的填充量,会影响
焊后焊缝余高;
(2)弧长修正可对弧长在一定范围内进行修正,这对于焊接过程飞溅及焊接稳
定性具有重要作用;
(3)脉冲修正可对焊接时的脉冲进行调节(-5~5),通过调节,可对脉冲频率及
峰值功率进行调节,从而影响焊接的稳定性及弧焊深度;
(4)焊枪开关模式具有多种选择方式,包括2步、4步、S2步、S4步、点焊,
试验中通过反复试验,S2步方式能够较好的优化起弧和收弧位置焊缝成形,S2步调节参数如图b所示,主要设置包括起弧电流、起弧电流持续时间、电弧电流与焊接电流过渡时间、收弧电流、收弧电流持续时间、焊接电流与收弧电流过渡时间。
与起弧相关的设置决定了起弧的稳定性及起始焊缝的成形,在焊接开始时,起始位置机器人起步速度较正常焊接慢,如果起弧电流及时间不进行调节,则起始焊缝凸起较高,所以需调节起弧电流的大小及持续时间,降低起弧电流可降低送丝速度,从而降低了起始位置的焊丝填充量,与速度相匹配获得大小均匀的焊缝,但起始电流的大小、持续时间及与焊接电流的过渡时间均会影响起弧的稳定性,为保证焊接质量需反复进行调试;
与收弧相关的设置主要用于解决收弧处弧坑的大小,若焊接结束时没有收弧控制功能,焊接电流瞬间关闭后将在收弧处形成较大的弧坑,影响焊接质量,通过调节收弧电流在一个合适的较小电流,时间调节好收弧电流的持续时间及与正常焊接电流的过渡时间,可消除收弧弧坑。
在初始试验参数焊接效果较差的情况下,通过提高送丝速度(焊接电流提高)并进行一定的弧长修正及起弧收弧控制,焊接过程变得较为稳定且飞溅小,焊缝成形均匀,如下图所示:
在调节好弧焊焊接稳定性及焊缝成形后,进行激光与电弧的复合焊接调试。
随着板厚的增加,在进行激光复合焊穿透焊接时,焊缝下漏现象难以控制。
在焊丝直径的选择上,小直径焊丝焊接时临界电流(熔滴形成射流过渡时的电流)较低,在相同的送丝速度下焊接电流较小,热输入较小,同时焊缝的填充金属也较少,更易获得小焊宽及余高的焊缝成形。
在焊接速度较慢的情况下,同时为保证达到临界焊接电流,又必须保证较快的送丝速度,在这种情况下宜选用小直径焊丝,便于控制焊缝的高度。
焊接过程中的主要难点在于焊接起始位置的成形控制,一方面是焊接起始位置焊缝的高度控制,另一方面是焊接起始位置背面下漏控制,两种情况如下图所示:
焊接起始位置问题的出现主要原因在于起步时机器人运动速度较慢造成的,处理起始位置焊缝过高的问题主要是通过控制焊接起始电流及过渡时间。
处理起始位置熔滴下漏的问题必须设置激光起始等待或爬长时间,必要时可在焊缝起始位置放置引弧板。
焊机参数调节可在焊接过程中进行,实时调节。