转子轴心轨迹测量及控制台运动控制资料
机械故障诊断技术实验报告

E(:,1:4)=[]; %去掉 1 到 4 列
PJ=mean(E);%平均值
YXZ=sqrt(sum(E.^2)/length(E));%有效值
JF= YXZ^2;%均方值
YD= YXZ /PJ;%裕度指标
WD=sum((abs(E)-PJ).^3)/length(E)/(YXZ.^3);%歪度指标
2.转子实验台转速测量 磁电式传感器实质上是电涡流传感器,通过电涡流效应进行工作。当轮齿接
近传感器和离开传感器时,都会产生大小不同的脉冲信号,通过采集这些信号就 可以进行后续的数据分析,进而测量出回转系统的运行速度。
将磁电传感器安装在转子试验台上专用的传感器架上,使其探头对准测速用 15 齿齿轮的中部,调节探头与齿顶的距离,使测试距离为 1mm。在已知发讯齿轮 齿数的情况下,测得的传感器输出信号脉冲的频率就可以计算出测速齿轮的转 速。如设齿轮齿数为 N,转速为 n,脉冲频率为 f,则有:n=f/N 。
机械故障诊断技术实验
图 4 转子实验台轴心轨迹测量 图 5 转子实验台转速测量
图 6 转子实验台转子振动噪声测量
6
图 1 基于速度的振动测量的幅频谱图
转子实验台转子振动噪声测量
1、噪声测量结果计算如下
Matlab 程序代码:
首先把测量的数据拷入 Matlab 中安装目录下的 bin 文件下的以文件名为
data 的.txt 格式中。然后直接调用其中的数据进行构成矩阵。
clear all %清楚变量
E=importdata('data.txt');%提取 data.txt 的数据构成矩阵 E
QD=sum((abs(E)-PJ).^4)/length(E)/(YXZ.^4);%峭度指标
转子台综合实验指导书
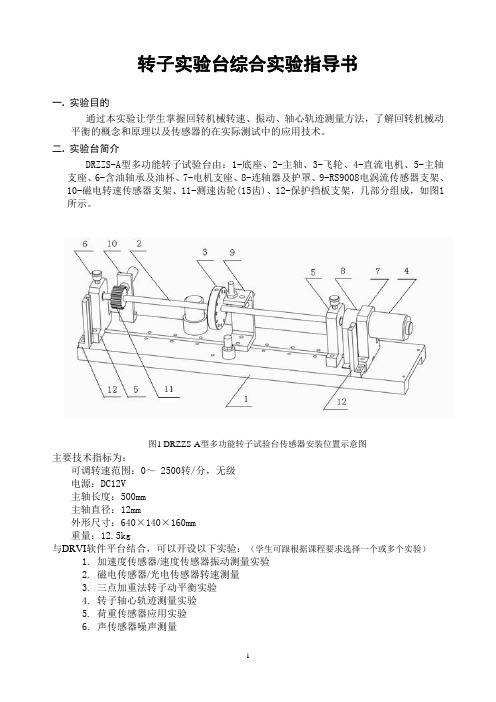
在图36.4的实验基础上增加窗函数和采样频率调节功能。
六、实验报告要求(实验报告统一用A4纸)
1.简述实验目的和原理。
2.整理和分析实验中得到的振动信号的数据,并分析其结果。
七、思考题
1.为什么要采用加速度传感器来测量振动信号?
2.常用的振动信号测量方式有那些?
八、附录
本实验的流程框图如图36.6所示。
1.加速度传感器/速度传感器振动测量实验
2.磁电传感器/光电传感器转速测量
3.三点加重法转子动平衡实验
4.转子轴心轨迹测量实验
5.荷重传感器应用实验
6.声传感器噪声测量
实验一转子实验台底座振动测量实验
(一)、加速度传感器振动测量实验
一、实验目的
通过本实验了解并掌握机械振动信号测量的基本方法。
二、实验原理
振动的幅值、频率和相位是振动的三个基本参数,称为振动三要素。
幅值:幅值是振动强度的标志,它可以用峰值、有效值、平均值等方法来表示。
频率:不同的频率成分反映系统内不同的振源。通过频谱分析可以确定主要频率成分及其幅值大小,从而寻找振源,采取相应的措施。
相位:振动信号的相位信息十分重要,如利用相位关系确定共振点、测量振型、旋转件动平衡、有源振动控制、降噪等。对于复杂振动的波形分析,各谐波的相位关系是不可缺少的。
在振动测量时,应合理选择测量参数,如振动位移是研究强度和变形的重要依据;振动加速度与作用力或载荷成正比,是研究动力强度和疲劳的重要依据;振动速度决定了噪声的高低,人对机械振动的敏感程度在很大频率范围内是由速度决定的。速度又与能量和功率有关,并决定动量的大小。
2. YD-37加速度传感器简介
压电传感器的力学模型可简化为一个单自由度质量—弹簧系统。根据压电效应的原理,当晶体上受到振动作用力后,将产生电荷量,该电荷量与作用力成正比,这就是压电传感器完成机电转换的工作原理。压电式加速度传感器在振动测试领域中应用广泛,可以测量各种环境中的振动量。
基于LabVIEW转子轴心轨迹测量与识别系统开发
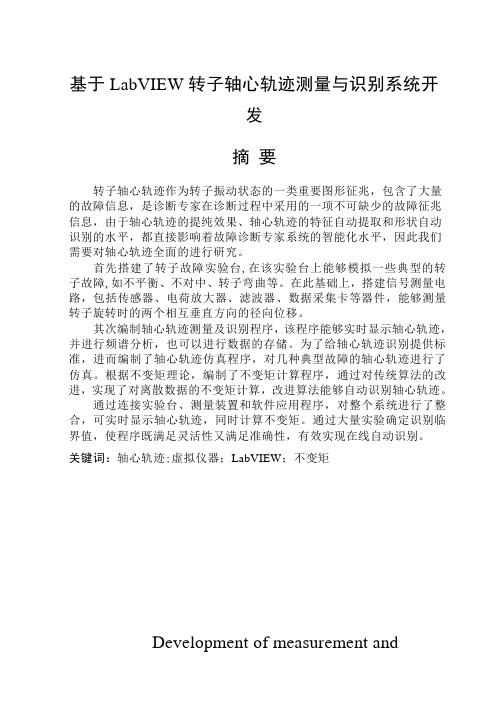
基于LabVIEW转子轴心轨迹测量与识别系统开发摘要转子轴心轨迹作为转子振动状态的一类重要图形征兆,包含了大量的故障信息,是诊断专家在诊断过程中采用的一项不可缺少的故障征兆信息,由于轴心轨迹的提纯效果、轴心轨迹的特征自动提取和形状自动识别的水平,都直接影响着故障诊断专家系统的智能化水平,因此我们需要对轴心轨迹全面的进行研究。
首先搭建了转子故障实验台,在该实验台上能够模拟一些典型的转子故障,如不平衡、不对中、转子弯曲等。
在此基础上,搭建信号测量电路,包括传感器、电荷放大器、滤波器、数据采集卡等器件,能够测量转子旋转时的两个相互垂直方向的径向位移。
其次编制轴心轨迹测量及识别程序,该程序能够实时显示轴心轨迹,并进行频谱分析,也可以进行数据的存储。
为了给轴心轨迹识别提供标准,进而编制了轴心轨迹仿真程序,对几种典型故障的轴心轨迹进行了仿真。
根据不变矩理论,编制了不变矩计算程序,通过对传统算法的改进,实现了对离散数据的不变矩计算,改进算法能够自动识别轴心轨迹。
通过连接实验台、测量装置和软件应用程序,对整个系统进行了整合,可实时显示轴心轨迹,同时计算不变矩。
通过大量实验确定识别临界值,使程序既满足灵活性又满足准确性,有效实现在线自动识别。
关键词:轴心轨迹;虚拟仪器;LabVIEW;不变矩Development of measurement andidentification of axis orbit system on LabVIEWAbstractThe rotor axis path as a kind of important graphic sign of rotor vibration state contains a large number of fault information is used in the process of diagnosis expert in the diagnosis of an indispensable fault symptom information.Axis path due to the effect of purification, the axis trajectory characteristics of the level of automatic extraction and automatic shape identification, directly affects the level of intelligent fault diagnosis expert system,So we need the axis trajectory comprehensive research.First set the rotor fault test-bed in the laboratory bench to simulate some of the typical rotor faults, such as imbalance, in the wrong, rotor bending, etc. On this basis, the structures, signal measuring circuit, including the data acquisition card, sensor, charge amplifier and filter device, to measure the axis trajectory radial displacement of two directions.Second axis trajectory measurement program, the program can real-time display the axis trajectory, and spectrum analysis, can also for data storage. To provide standards for axis path identification, and then compiled the axis trajectory simulation program, the axis trajectory of several typical faults are simulated.The recognition system is used as a means for identifying, invariant moment invariant moment calculation program, therefore, according to the features of the experiment, the moment invariant algorithm was improved, in order to meet the automatic identification.Finally integrate the compiled program can display the axis trajectoryand moment invariant can be calculated, and through experiments to determine the identification of the critical value, satisfies program meets the flexibility and accuracy, effectively realize online automatic identification. Key words:Axis trajectory;Virtual instrument; LabVIEW; Invariant moments目录摘要 (I)Abstract (II)第1章绪论................................................ - 1 -1.1 课题的背景................................................................................... - 1 -1.2 国内外研究现状........................................................................... - 2 -1.2.1 旋转机械轴心轨迹研究现状 ............................................. - 2 -1.2.2 转子轴心轨迹自动识别研究现状 ..................................... - 2 -1.3 研究的意义和主要内容 ............................................................... - 4 -1.3.1 研究的意义......................................................................... - 4 -1.3.2 研究的主要内容................................................................. - 4 - 第2章转子振动机理和轴心轨迹特征 ......................... - 5 -2.1 旋转机械振动机理分析 ............................................................... - 6 -2.2 转子振动的基本特征 ................................................................... - 7 -2.3 常见故障原因及轴心轨迹的特征 ............................................... - 8 -2.3.1 转子不平衡......................................................................... - 8 -2.3.2 转子不对中......................................................................... - 9 -2.3.3 转子弯曲............................................................................. - 9 -2.3.4 转子碰磨........................................................................... - 10 -2.3.5 油膜震荡........................................................................... - 11 -2.4 轴心轨迹测试方法及信号分析 ................................................. - 12 -2.5 本章小结..................................................................................... - 14 - 第3章 LabVIEW应用程序设计............................... - 15 -3.1 数据采集和轴心轨迹合成 ......................................................... - 15 -3.2 轴心轨迹仿真程序..................................................................... - 19 -3.3 不变矩计算程序......................................................................... - 21 -3.3.1 不变矩方法简介............................................................... - 21 -3.3.2 不变矩计算方法............................................................... - 22 -3.4 相似度计算程序......................................................................... - 24 -3.5 轴心轨迹自动识别程序 ............................................................. - 25 -3.6 本章小结..................................................................................... - 26 - 第4章实验系统与实验结果................................. - 27 -4.1 实验台的结构设计..................................................................... - 27 -4.2 测量装置..................................................................................... - 28 -4.2.1 传感器与测量电路 ........................................................... - 28 -4.2.2 数据采集卡....................................................................... - 29 -4.2.3 数据采集卡基本性能指标 ............................................... - 30 -4.3 实验结果分析............................................................................. - 31 -4.4 本章小结..................................................................................... - 32 - 结论...................................................... - 33 - 致谢...................................................... - 34 - 参考文献.................................................. - 35 - 附录...................................................... - 37 -第1章绪论1.1课题的背景旋转机械是机械设备的重要组成部分并且占有相当大的比重,如机械、化工、电力、冶金等行业的机床、汽轮机、发电机、压缩机等都是典型的旋转机器,它们以转子及其他回转部件作为工作的主体,一旦发生事故将造成巨大损失。
滑动轴承转子运动轨迹主动控制

( o eeo M cai l nier gS adn n e i , nnS adn 5 10 C ia C l g f ehnc g e n ,hn ogU i rt J a hn og 00 ,hn ) l aE n i v sy i 2 A s at ae nf tepneait o e c o ant et gadhg aai f yr ya i l r ao u— bt c: sdo s r os b i f l t m gecba n n i cpcyo hdo n mc u i t n or r B a s ly e r i i h t d bci j
的机械零件和产品都采用 了非圆异形 截面 ,即其横截
面不是 圆形 ,而是非 圆形状 ,如椭 圆、变椭 圆、摆线
等。为 了实现异形表 面的加工 ,需要控制刀具在切削
过程 中径向微移动 。传统的加工异形截 面的方法主要 是机械仿形加工…。近年来 ,一些新技术新材料 已应 用到非圆异形截面 的加工领域中 ,主要有特种加工方 法加工异形 截面 、新 型数 控仿形 系 统加 工异 形 截
l g ee to g e u rn s d v lp d, ih c n b s d fr n n ic lrfn c i ig T e d n mi d lo h f i lcr ma n tc re twa e eo e whc a e u e o o crua e ma h nn . h y a c mo e fs at n i
合的两输入两输出系统进行反馈解耦 ,设计了鲁棒 H 混合灵敏度控制器 。仿 真结果表明控制输 出能很好地跟踪外部参 考信号,并且该控制器对外部干扰有很强的抑制作用 ,得到 比较精确的椭圆轨迹跟踪结果。实验结果验证 了仿真结果的
教学转动机械中心偏差控制方法

教学转动机械中心偏差控制方法转动机械中心偏差控制是制造过程中非常重要的一项工作,它涉及到机械部件的制造质量和性能稳定性。
本文将从三个方面介绍转动机械中心偏差控制方法:偏差的检测与测量、偏差控制的原理和方法、以及实际操作中的注意事项。
一、偏差的检测与测量机械中心偏差是指转动轴心与设计轴心之间的距离差,通常使用测量仪器进行检测。
在实际操作中,常用的测量方法有以下几种:1.单边测量法:在机械部件上选择两个已知位置,通过测量这两个位置上的偏差,可以计算出机械中心的偏差。
2.轨迹法:利用测量仪器测量机械部件在运动中的轨迹,通过分析轨迹的形状和偏差,可以得到机械中心的偏差。
3.摆线法:利用摆线仪等测量仪器,测量机械部件的摆线形状和偏差,从而得到机械中心的偏差。
以上三种测量方法都有各自的优缺点,选择适合的方法根据具体情况进行。
二、偏差控制的原理和方法偏差控制的目标是使机械部件的中心偏差尽可能接近于设计要求,提高机械部件的精度和性能。
在实际操作中,常用的偏差控制方法有以下几种:1.设计优化:在机械部件的设计阶段,通过优化设计参数的选择和调整,以降低机械中心的偏差。
2.加工控制:在机械部件的加工过程中,通过合理的工艺和加工控制,控制加工误差,减小机械中心的偏差。
3.装配控制:在机械部件的装配过程中,通过合理的装配工艺和装配控制,保证各个零部件的几何相对关系,减小机械中心的偏差。
4.调整矫正:在机械部件加工和装配完毕后,通过调整和矫正机械部件的位置和几何关系,使机械中心的偏差达到设计要求。
以上偏差控制方法都是相互关联的,需要在机械制造的每个环节中注意。
三、注意事项在进行转动机械中心偏差控制时,需要注意以下几点:1.选取合适的测量仪器并掌握正确的测量方法,确保测量结果的准确性。
2.加工和装配过程中要严格控制加工误差和装配误差,避免误差的累积。
3.在进行调整和矫正时,要根据具体情况选择合适的调整方法和工具,避免过度调整导致新的偏差产生。
基于虚拟仪器的转子轴心轨迹监测系统的研究

基于虚拟仪器的转子轴心轨迹监测系统的研究转子轴心轨迹是判断机械转子运行状态和故障征兆的重要依据,由多功能转子实验台、数据采集卡和数据处理软件组成了基于LabVIEW的轴心轨迹监测系统。
连接多功能转子实验台、测控装置和数据处理软件,利用LabVIEW采集数据,可实时显示转子系统轴心轨迹。
通过大量实验确定识别故障类型,使程序能有效实现在线自动识别。
此系统可以准确的判断转子轴心轨迹的运行情况,进行诊断故障。
标签:转子;虚拟仪器;LabVIEW;轴心轨迹引言旋转机械的转子轴心轨迹图能够形象、直观地表现出设备的运转状态,图形中包含了大量的故障信号,是在故障诊断过程中不可缺少的,转子系统轴心轨迹的精度提升与自动化识别的研究水平决定着故障诊断系统的智能化水平,因此有着重要的研究价值。
基于虚拟仪器的监测平台已经在各行各业中得到了越来越广泛的应用。
它采用图形化的编程方式,编程简易,功能多样,能够用于监测各种机械设备,比传统仪器效率更高、成本更低。
将虚拟仪器设备用于故障诊断领域,能够充分发挥虚拟仪器的优点,为旋转机械故障诊断提供了更便捷的方法[1-3]。
1 监测原理由北京航天智控监测技术研究院生产的多功能转子实验台,配置HZ-891系列电涡流传感器,进行轴心轨迹测量,其主要结构如图1所示。
图1中,1、2为电涡流传感器,两个传感器在同一截面上相互垂直安装。
传感器获得位移信号,可反映转子的轴心轨迹。
转子轴心轨迹是由X、Y方向两个振动信号X(t)、Y(t)所组成的二维振动信号,也可以分别分解为各自频率下的一个个椭圆图谱[4]。
根据这个原理,可以将X(t)和Y(t)分解为X(t)=A1sin(2πf1t+φ1)+A2sin(2πf2t+φ2)+…Ansin(2πfnt+φn)=x1(t)+x2(t)+…xn(t)(1)Y(t)=B1sin(2πf1t+φ1)+B2sin(2πf2t+φ2)+…Bnsin(2πfnt+φn)=y1(t)+y2(t)+…yn(t)(2)上式中下标n表示振动信号中频率分量的数目,下式为各频率下的“轴心轨迹分量”将上面的轴心轨迹分量分解出来,就能够清晰地看到原本转子系统轴心轨迹的组成。
基于虚拟仪器的机械转子轴心轨迹分析

2008年11月Nov .2008第29卷 第6期Vol .29 No .6基于虚拟仪器的机械转子轴心轨迹分析罗开玉,李伯全,王小飞,潘海彬(江苏大学机械工程学院,江苏镇江212013)摘要:转子轴心轨迹是判断机械转子运行状态和故障征兆的重要依据,文中研究了几种机械转子典型故障及其对应的频率和轴心轨迹特征,运用Lab V I E W 软件平台,开发出智能控件化虚拟式轴心轨迹测试分析系统,调用由VC ++编写的动态链接库(DLL )函数实现对机械转子振动信号的采集.试验表明,转子轴心轨迹测试分析系统可实时显示轴心轨迹、轴心位置和两路相互垂直振动信号的波形和频谱,以此可以判断一些常见的旋转机械故障,计算出用来消除转子不平衡的平衡质量块的大小及坐标点位置.关键词:轴心轨迹;转子;虚拟仪器;Lab V I E W 中图分类号:T M930.19 文献标志码:A 文章编号:1671-7775(2008)06-0474-04Study on mechan i cal rotor axis locus based on vi rtual i n stru mentLUO Kai 2yu,L I B o 2quan,WAN G X iao 2fei,PAN Ha i 2bin(College of Mechanical Engineering,J iangsu University,Zhenjiang,J iangsu 212013,China )Abstract:Rot or axis l ocus is an i m portant basis for esti m ating the running states and faults of mechanical r ot or .Detailed r ot or faults were analyzed and several typ ical faults and corres ponding characteristics of their frequencies and orbits of shaft center line were studied .An axis l ocus analyzing syste m based on in 2telligent virtual contr ol was devel oped,and the signal acquisiti on and analysis were realized by using Lab 2V I E W 7.0and transferring the dyna m ic link library (DLL )functi on in VC ++.The results indicate that axis l ocus,axis l ocati on and the wave and s pectru m of t w o orthogonal vibrati on signals can be real 2ti m e dis p layed,and s o me common faults of r otating machinery can be diagnosed by using the measure ment syste m.Key words:axis l ocus;r ot or;virtual instru ment;Lab V I E W收稿日期:2008-04-18基金项目:国家自然科学基金资助项目(70571030);科技部科技型中小企业技术创新基金资助项目(06C262132001064);江苏大学高级人才基金资助项目(02JDG001);江苏大学第六批大学生科研课题立项项目(06A134)作者简介:罗开玉(1975—),女,湖北天门人,博士研究生,讲师(luoteacher@ ),主要从事虚拟仪器技术的研究.李伯全(1956—),男,江苏宜兴人,教授(libq@ujs .edu .cn ),主要从事现代测试系统与仪器技术的研究. 轴心轨迹作为旋转机械重要的图形征兆是从轴承或轴颈同一截面的两个相互垂直的方向上监测得到的一组振动信号中提取的有用故障信息,是诊断旋转机械故障的一种有效途径,一直是研究的热点[1,2].虚拟仪器技术实现了计算机技术和仪器技术的完美结合,突出优点在于能够和计算机技术结合,从而开拓了更多的功能,具有很大的灵活性,极大地提高了测试系统的处理能力,能够获得较高的经济效益.利用虚拟仪器可实现各种物理量的测试与分析[3-5],如可以对定子线圈的转子匝间短路故障进行识别[6]、自动获取压电装置的非线性的实时振动波形[7],以及监测和控制SSRF 数字电力设备[8]等.目前多采用多测点三维轴心轨迹方法[9]以及关联度[10]等方法识别转子的轴心轨迹来快速诊断旋转机械的故障,这些方法都必须实测转子的轴心轨迹,进行预处理后再进行判别机械转子的运行状第6期 罗开玉等:基于虚拟仪器的机械转子轴心轨迹分析475 态.文中基于虚拟仪器开发平台Lab V I E W 软件建立了转子轴心轨迹测试分析系统,测量轴系的振型.根据轴心轨迹确定转轴最大振幅值及其方向、转轴涡动方向及其频率,对具体的转子故障进行研究,得出几种典型故障及其对应的频率和轴心轨迹特征,诊断机器转子不平衡、不对中或油膜涡动等故障,利用故障的特征信息判断旋转机械转子运行状态和进行故障诊断,大大提高了机械转子运行状态的监测和控制能力,降低了成本.1 轴心轨迹测试分析系统的功能建模利用安装在同一截面内互相垂直的两个电涡流传感器对轴颈振动检测,获得对应于轴心两垂直方向上的瞬时位移的电流信号,再经过相应的处理,从而可获得转子的轴心轨迹[11,12].轴心轨迹可以看作由x,y 方向振动信号x (t ),y (t )所组成的二维振动信号,也可以分解为各频率分量下的一个个椭圆[2].根据这个思路,将x (t )和y(t )分解为x (t )=A 1sin (2πf 1t +<1)+A 2sin (2πf 2t +<2)+…+A l sin (2πf 1t +<1)=x 1(t )+x 2(t )+…+x l (t )(1)y (t )=B 1sin (2πf 1t +ψ1)+B 2sin (2πf 2t +ψ2)+…+B l sin (2πf 1t +ψ1)=y 1(t )+y 2(t )+…+y l (t )(2)式中下标l 是振动信号中频率分量的数目,则各频率下的“轴心轨迹分量”为x 1(t )=A 1sin (2πf 1t +<1)y 1(t )=B 1sin (2πf 1t +ψ1)x 2(t )=A 2sin (2πf 2t +<2)y 2(t )=B 2sin (2πf 2t +ψ1)……x l (t )=A l sin (2πf l t +<1)y l (t )=B l sin (2πf l t +ψ1)(3)将这些轴心轨迹分量分解绘制出来,就清楚地反映了原来轴心轨迹的组成.在分析单频轴心轨迹分解方法的基础上,将若干个感兴趣的频率分量叠加起来,就可以实现轴心轨迹的合成.为了简单起见,假设对任选的m 个频率{f 1,f 2,…,f m }对应的分量感兴趣,则合成后的两路信号为x (t )=6mk =1x A k sin (2πf k t +<xk )y (t )=6mk =1y A k sin (2πf k t +<yk )k ∈{1,2,…,m}(4)以x (t )和y (t )作为X -Y 轴上的x,y 坐标点,即可得到m 个频率分量合成的轴心轨迹.2 轴心轨迹测试分析系统的硬件构建系统硬件由数据采集仪(装有深圳德普施DRDAQ -EPP 数据采集卡和信号调理模块)、电涡流位移传感器、多功能转子试验台以及US B 连线和PC 机组成,如图1所示.从转子试验台两个电涡流传感器输出的是分别对应于轴心两个垂直方向上的瞬时位移的电流信号,该电流信号经过前置放大器、信号调理电路得到标准信号,由数据采集卡A /D 转换后经US B 输送到PC 机,然后用Lab V I E W 软件编写相应的应用程序对信号进行分析处理并显示结果.图1 测试分析系统结构Fig .1 Structure of measure ment syste m3 轴心轨迹测试分析系统的软件实现使用Lab V I E W 语言在W indows XP 系统上编制轴心轨迹测试分析系统的软件程序.文中构建的测试分析系统所采用的数据采集卡不能采用Lab V I E W 平台软件内部的DAQ 库直接对端口进行操作,数据采集卡的驱动程序是用传统编程语言编写的,Lab V I E W 语言不支持,要使其在Lab V I E W 环境下运行,必须编写适用于Lab V I E W 的接口驱动程序.测试分析系统的数据采集程序是在VC ++6.0下编写的动态链接库(DLL )形式的驱动程序,再利用LabV I E W 调用库函数CLF 节点访问该动态链接库,从而实现对数据的采集.在转子轴心轨迹测试分析系统中,用双通道对X 轴和Y 轴两个方向的信号进行采样,连接相关的通道,设置好采样频率和采样长度之后,就可实现数据的采集.476 第29卷程序中使用A I Acquire W avefor m s 函数同时采集两个传感器传入的数据,运用I ndex A rray 函数分别将两路信号索引.运用Butter worth Filter 低通数字滤波器,滤出高频干扰信号分量.信号经滤波处理后,水平和垂直方向的信号分别送到Graph 控件显示波形图,同时将两个方向的信号叠加在1个X Y Graph 控件上显示转子的轴心轨迹图.4 试验与结果分析通过设置前面板上的参数,即可控制数据采集卡进行数据采集、分析处理、图形数据显示、存储、打印及远程网络传输等.启动转子平台电机,调整到稳定转速,在前面板上设置好相应参数后点击面板中的“运行”按钮,观察和分析所得到位移信号的波形,并记录试验结果,轴心轨迹测试系统程序框图如图2所示.测试结果如图3~5所示的前面板右侧的轨迹图.其中图3所示的是转子平衡时的轴心轨迹图,图4所示的是转子不平衡时的轴心轨迹图,图5所示的是转子严重不平衡时的轴心轨迹图.图2 轴心轨迹测试系统程序框图Fig .2 D iagram of measure mentsystem图3 转子平衡时的轴心轨迹图Fig .3 Axis l ocus of balanceable r otor图4 转子不平衡时的轴心轨迹图Fig .4 Axis l ocus of i m balance r otor图5 转子严重不平衡时的轴心轨迹图Fig .5 Axis l ocus of severe i m balance r ot or试验结果表明,轴心轨迹包含着丰富的转子状态信息,通过模拟转子正常和非正常的多种状态,显示出平衡转子和不平衡转子的轴心轨迹图,由轴心轨迹图可以定性和定量判别机械转子的平衡状态和故障类型.同时,根据不平衡转子的轴心轨迹图,可以计算出平衡质量块的大小及坐标点位置,为消除转子不平衡提供了有效途径.5 结 论将虚拟仪器引入到轴心轨迹分析系统中,开发出基于LabV I E W 的轴心轨迹测试分析系统,可实时显示轴心轨迹和轴心位置,还可以显示两路相互垂直振动信号的波形和频谱.基于LabV I E W 的轴心轨迹监测系统,相对于传统的测试仪器,测试精度高,能准确显示轴心轨迹图,对促进机器转子故障诊断的自动化、智能化具有现实意义的推进作用.参考文献(References)[1] Joussellin Agnes,Chevalier Roger .D iagnosis of faults inE DF power p lants:fr om monit oring t o diagnosis[J ].A 2m erican Society of M echanical Engineers,Pressure V es 2selsand P iping D ivision ,1994,14(1):19-23.[2] Q in Shuren,Tang Baop ing .I ntelligent virtual contr ols -the measuring instru ment fr om whole t o part [J ].The Chinese Journal of M echanical Engineering ,2002,15(2):131-135.[3] 罗开玉,李伯全,孙 杰,等.基于虚拟仪器技术的应变测试系统[J ].江苏大学学报:自然科学版,2005,26(2):106-109.LUO Kai 2yu,L I Bo 2quan,S UN J ie,et al .Strain mea 2sure ment syste m based on virtual instru ment technol ogy [J ].Journal of J iangsu U niversity:N atural Science Edi 2tion ,2005,26(2):106-109.(in Chinese )[4] 李伯全,潘海彬,罗开玉,等.远程测控数据传输中的DataS ocket 技术应用[J ].江苏大学学报:自然科学版,2004,25(4):284-287.第6期 罗开玉等:基于虚拟仪器的机械转子轴心轨迹分析477 L IBo2quan,P AN Hai2bin,LUO Kai2yu,et al.App lica2ti on of data s ocket technol ogy in re mote data trans m is2si on measure ment and contr ol[J].Journal of J iangsuU niversity:N atural Science Edition,2004,25(4):284-287.(in Chinese)[5] 刘占生,张新江,杨建国,等.转子轴心轨迹故障诊断特征识别方法研究[J].哈尔滨工业大学学报,1998,30(6):22-25.L I U Zhan2sheng,ZHANG Xin2jiang,Y ANG J ian2guo,etal.A ne w coding method of r ot or whirl orbit[J].Jour2nal of Haerbin Institute of Technology,1998,30(6):22-25.(in Chinese)[6] W an Shuting,LüLuyong,L iu Q ing,et al.A virtual in2stru ment for the r ot or winding inter2turn short circuitfault of generat or[C]∥2006International Conference onPo w er Syste m s Technology(POW ERCON).Chongqing:[s.n.],2006:1-5.[7] J i m e′neza F J,De Frut os J.V irtual instru ment f ormeasure ment,p r ocessing data,and visualizati on of vi2brati on patterns of p iezoelectric devices[J].Co m puterS tandards&Interfaces,2005,27:653-663.[8] Tang Junl ong,Xu Ruinian,Chen Huanguang,et al.V irtual instru ment f or contr olling and monit oring digita2lized power supp ly in SSRF[J].N uclear Science andTechniques,2006,17(3):129-134.[9] 万 波,张来斌,王朝晖.基于多测点三维轴心轨迹旋转机械的快速诊断[J].计算机测量与控制,2007,10(15):1270-1272.WAN Bo,Z HANG Lai2bin,WANG Zhao2hui.Fast di2agnosis of r otary mechanis m based on multi2measuringpoints three2di m ensi onal axle centre trail[J].Co m puterM easure m ent&Control,2007,10(15):1270-1272.(in Chinese)[10] 万书亭,彭学志.发电机转子轴心轨迹形状自动识别方法的研究[J].华北电力大学学报,2004,31(5):26-29.WAN Shu2ting,PE NG Xue2zhi.Aut omatic identificati onof axis orbit shape of generat or r ot or[J].Journal ofN orth China Electric Po w er U niversity,2004,31(5):26-29.(in Chinese)[11] 袁中文.轴心轨迹图在机器故障诊断中的应用[J].抚顺石油学院学报,2001,21(3):41-44.Y UAN Zhong2wen.The app licati on of chart of axes trackon the diagnostics of mechines malfuncti on[J].Journalof Eushum Petroleum Institue,2001,21(3):41-44.(in Chinese)[12] 程 珩,杜岚松.旋转机械轴心轨迹故障诊断[J].太原理工大学学报,2003,34(5):552-554.CHE NG Hang,DU Lan2s ong.Fault diagnosis using axlecenter trail in revolving machinery[J].Journal ofTaiyuan U niversity of Technology,2003,34(5):552-554.(in Chinese)(责任编辑 祝贞学)。
机械故障诊断-轴心轨迹

实验项目(实验名称)轴心轨迹测量实验实验日期(年月日)实验地点(楼和门牌号)同组人(不含本人)实验台号(型号和序号)实验类型□验证性□综合性□√设计性□研究性□其他(在相应处画“√”)一、预习内容在回转机械状态监测与诊断中,常利用轴系同一截面上两路相互垂直的振动信号合成轴心轨迹来监测其运行状态和故障类型。
轴心轨迹直观地反映了转子瞬时运动状态,其形状和动态特性包含了丰富的故障征兆信息。
由于它可以直观、形象地表达出设备的运行状况,因而在诊断系统中得到广泛的应用。
几种常见故障的转子轴心轨迹如图1所示。
图1是在理想状况下常见的转子轴心轨迹图,它们分别对应着一种或者几种故障类型。
(a)是椭圆形图,它代表的是转子不平衡故障;(b)是芭蕉图,它代表的是转子不平衡和转子不对中综合故障;(c)是八字图,它代表的是转子不对中故障;(d)是内环图,它代表的是油膜涡动故障;(e)是无规则图,它代表的是油膜振动故障。
二、实验目的1、了解和掌握电涡流传感器测量的原理和方法,2、熟悉仪器及软件操作;3、观察转子台在转动时,转轴所产生的径向振动时域波形图;4、掌握回转机械轴心轨迹测量方法。
三、实验仪器设备1、计算机一台2、DRVI快速可重组虚拟仪器平台一套3、打印机一台4、转子实验台一套5、USB数据采集仪一台四、实验原理电涡流传感器采集到转轴的径向振动信号,将信号通过信号电缆送入转子台控制器,转子台控制器对信号调理后,将信号送入动态数据采集分析仪,在数据采集仪内实现模拟信号抗混滤波、A/D转换等步骤,最终转换为上层分析软件可处理的数字信号,最后将数字信号上传到计算机的分析软件,实现用户所需的各种分析功能。
电涡流传感器探头是系统的一个必要组成部分,它是采集、感受被测体信号的重要部分,它能精确地探测出被测体表面相对于探头端面间隙的变化。
通常探头由线圈、头部保护罩、不锈钢壳体、高频电缆、高频接头组成。
线圈是探头的核心部分,它是整个传感器系统的敏感元件,线圈的电气参数和物理几何尺寸决定传感器系统的线性量程及传感器的稳定性。
- 1、下载文档前请自行甄别文档内容的完整性,平台不提供额外的编辑、内容补充、找答案等附加服务。
- 2、"仅部分预览"的文档,不可在线预览部分如存在完整性等问题,可反馈申请退款(可完整预览的文档不适用该条件!)。
- 3、如文档侵犯您的权益,请联系客服反馈,我们会尽快为您处理(人工客服工作时间:9:00-18:30)。
综合测试实验报告题目:转子轴心轨迹测量控制台运动控制指导老师:弢班级:姓名:XXX姓名:XXX学号:学号:20XX年X月目录第一章轴心轨迹测量1.实验台简介 (5)2.实验原理 (5)3.实验仪器和设备 (5)4.实验基础 (6)4.1Simulink动态仿真 (6)4.2S-function的工作机制 (7)4.3C MEX-file S-function (7)5.数据采集程序设计 (8)5.1创建DDL文件 (8)5.2mdl文件示意图 (11)5.3GUI设计 (11)5.4信号处理 (13)5.4.1 未滤波getdata代码 (13)5.4.2 低通滤波getdata代码 (14)6.实验结果 (15)6.1采集信号前后示波器scope波形分析 (15)6.2采用滤波器前后波形分析 (16)6.3应用Bufferworth低通滤波器处理的实验结果 (17)6.3.1不同采样频率波形比较 (17)6.3.2不同低通区间的波形比较 (19)6.3.3不同截取长度波形比较 (21)6.3.4不同运转速度时波形比较 (22)7.实验结论 (23)8. 低通滤波的进一步尝试与研究 (24)8.1建立界面的m文件 (24)8.2 设计界面的效果图 (28)8.3 低通滤波结果 (29)第二章控制台运动控制1.实验原理 (30)2.实验基本要求 (31)3.实验基础 (31)3.1控制运动模块 (31)3.2 模块功能具体实现 (32)4. 实验结果 (33)4.1 重要参数设计 (33)4.2 程序图解 (34)5. 功能理解 (34)6. 分析 (36)7. 实验过程 (37)7.1 尝试一 (37)7.1.1 功能描述 (37)7.1.2 结论一 (37)7.2 尝试二 (38)7.2.1 功能描述 (39)7.2.2 结论二 (39)心得体会 (40)●XXX (40)●XXX (42)附录 (44)组员分工第一章转子轴心轨迹测量第二章控制台运动控制说明:实验过程中的每一个部分,两个小组成员基本上都是全部参与。
在完成整个实验的过程中,我们一起讨论,共同研究,克服一个个困难,最终顺利完成实验。
第一章轴心轨迹测量一、实验台简介DRZZS-A型多功能转子试验台由:1底座、2主轴、3飞轮、4直流电机、5主轴支座、6含油轴承及油杯、7电机支座、8连轴器及护罩、9RS9008电涡流传感器支架、10磁电转速传感器支架、11测速齿轮(15齿)、12保护挡板支架,几部分组成,如图1所示。
图1 DRZZS-A型多功能转子试验台传感器安装位置示意图主要技术指标为:可调转速范围:0~2500转/分,无级电源:DC12V主轴长度:500mm主轴直径:12mm外形尺寸:640×140×160mm重量:12.5kg二、实验原理轴心轨迹是转子运行时轴心的位置,在忽略轴的圆度误差的情况下,可以将两个电涡流位移传感器探头安装到实验台中部的传感器支架上,相互成90度,并调好两个探头到主轴的距离(约1.6mm),标准是使从前置器输出的信号刚好为0(mV)。
这时,转子实验台启动后两个传感器测量的就是它在两个垂直方向(X,Y)上的瞬时位移,合成为李沙育图就是转子的轴心运动轨迹。
三、实验仪器和设备1. 计算机(已安装MATLAB 软件) 1台2. DRVI 快速可重组虚拟仪器平台 1套3. 电涡流位移传感器 2套4. 转子试验台1套 5. 虚拟仪器数据采集工作台1台四、实验基础4.1 Simulink 动态仿真SIMULINK 是MATLAB 重要软件包,用于对动态系统建模和仿真,它适用于连续系统和离散系统,也适用线性系统和非线性系统。
它采用系统模块直观地描述系统典型环节,可十分方便地建立系统模型。
Simulink 模块包括一系列输入、状态和输出。
输出是采样时间、输入、模块状态的函数。
下面的方程描述了输入、输出和状态的数学关系。
+10=(t,,u) ()=(t,,u) ()=(t,,u) () =+k c d d u c dy f x x f x x f x x x x 输出求导更新其中,Simulink 模型的执行按下述几个步骤。
首先是初始化阶段。
在这个阶段Simulink 将库模块集合到模型,传播宽度、数据类型和采样时间,评估模块参数,确定模块执行顺序,分配内存。
然后是仿真阶段。
此时Simulink 进入一个仿真循环,循环的每次执行对应一个仿真步。
在每个仿真步,Simulink 按初始化阶段确定的顺序执行各个模块。
对每个模块,Simulink 计算模块在当前采样时间的状态、微分和输出,这将持续到仿真介绍。
下图描述了Simulink 的仿真过程。
4.2 S-function的工作机制S-function包括一系列的回调方法,用以执行每个仿真步骤所需的任务。
在一个模型的仿真过程中,每个仿真步骤,Simulink将调用各S-function的适当方法。
S-function的执行方法包括:1)初始化:在首次仿真循环中执行。
2)计算下一采样点:如果定义了一个可变采样步长的模块,这一步将计算下一次采样点,也就是计算下一步长。
3)计算在主要时间步中的输出:这一步结束之后,模块的输出端口在当前时间步是有效的。
4)更新主要时间步中的离散状态:所有的模块在该回调方法中,必须执行一次每次时间步都要执行的活动。
5)积分:这用于具有连续状态的或者具有非采样过零的模型。
4.3 C MEX-file S-function定义了S-function模块的C MEX-file必须在仿真过程中向Simulink提供模型信息。
mdlInitializeSize是Simulink与S-function交互时调用的第一个方法。
随后Simulink将调用其他S-function方法(都以mdl开头)。
仿真结束时,Simulink调用mdlTerminate。
利用C写的S-Function仿真步骤如下:五、数据采集程序设计5.1 创建DLL(work1 文件)#define S_FUNCTION_NAME work1 //S_Function文件名为work1 #define S_FUNCTION_LEVEL 2#include "simstruc.h"#include "abc.h"double buffer[5000];double buffer1[5000];int pnum;char ch[8];static void mdlInitializeSizes(SimStruct *S){ssSetNumSFcnParams(S, 0);if (ssGetNumSFcnParams(S) != ssGetSFcnParamsCount(S)) {return;}ssSetNumContStates(S, 0);ssSetNumDiscStates(S, 0);if (!ssSetNumInputPorts(S, 2)) return; ssSetInputPortWidth(S, 0, 1);ssSetInputPortRequiredContiguous(S, 0, true);ssSetInputPortWidth(S,1,1);ssSetInputPortRequiredContiguous(S,1,tr ue);ssSetInputPortDirectFeedThrough(S, 0, 1);ssSetInputPortDirectFeedThrough(S, 1, 1);if (!ssSetNumOutputPorts(S, 2)) return; ssSetOutputPortWidth(S, 0, 1); ssSetOutputPortWidth(S, 1, 1); ssSetNumSampleTimes(S, 1); ssSetNumRWork(S, 0); ssSetNumIWork(S, 0); ssSetNumPWork(S, 0); ssSetNumModes(S, 0);ssSetNumNonsampledZCs(S, 0); ssSetOptions(S, 0); }static void mdlInitializeSampleTimes(SimStruct *S) {ssSetSampleTime(S, 0, CONTINUOUS_SAMPLE_TIME); ssSetOffsetTime(S, 0, 0.0); }#define MDL_INITIALIZE_CONDITIONS#if defined(MDL_INITIALIZE_CONDITIONS)static void mdlInitializeConditions(SimStruct *S) { }#endif#define MDL_START//定义两个输入信号端口 //设置信号1接口宽度 //输入信号1的接口设置 //设置信号1接口宽度 //输入信号2的接口设置//直接反馈信号1输入接口设置 //直接反馈信号2输入接口设置#if defined(MDL_START)static void mdlStart(SimStruct *S) {const real_T *u1 = (const real_T *)ssGetInputPortRealSignalPtrs(S,0); //生成input1的S-Function 源文件const real_T *u2 = (const real_T *)ssGetInputPortRealSignalPtrs(S,1); //生成input2的S-Function 源文件 if(ADCardInit()!=1) {ssSetErrorStatus(S,"Sorry,can not find DAQCard!"); //报错提醒,未找到DAQCard }DAQ2(0x0C,5000,1024*4,buffer,buffer1); pnum=0;}#endifstatic void mdlOutputs(SimStruct *S, int_T tid) {int Length=1024*4;ReadDaq(3,Length,buffer);ReadDaq(4,Length,buffer1);real_T *x =ssGetOutputPortRealSignal(S,0);real_T *y =ssGetOutputPortRealSignal(S,1);if(pnum>=Length)pnum=0; *x=buffer[pnum];*y=buffer1[pnum]; pnum++; } //读取的buffer 长度 //从采集卡读取通道3的buffer //从采集卡读取通道4的buffer //获取坐标轴X 的输出指针 //获取坐标轴Y 的输出指针 //判断指针是否已满 //输出X 轴方向第pnum 个点的值 //输出Y 轴方向第pnum 个点的值 //指针加1#define MDL_UPDATE#if defined(MDL_UPDATE)static void mdlUpdate(SimStruct *S, int_T tid)//开启采集,0x0C 表示采集通道3、4 //初始化buf 指针位置{}#endif#define MDL_DERIVATIVES#if defined(MDL_DERIVATIVES)static void mdlDerivatives(SimStruct *S) {}#endifstatic void mdlTerminate(SimStruct *S) {ADCardQuit(); }#ifdef MATLAB_MEX_FILE#include "simulink.c"#else#include "cg_sfun.h"#endif5.2 work2.mdl示意图5.3 GUI 设计//退出采集卡clf resetset(gcf,'menubar','none')set(gcf,'color',[0.5 0.6 0.4])set(gcf,'unit','normalized','position',[0.2,0.2,0.5,0.35]); set(gcf,'defaultuicontrolunits','normalized')h_axes1=axes('position',[0.05,0.5,0.4,0.38]);ht1=uicontrol(gcf,'Style','toggle','position',[0.55,0.08,0.08,0.05],'horizontal','left','fon tname','楷体_GB2312','fontsize',14,'string','Grid X', 'callback',['axes(h_axes1),','grid']); //制作“Grid X ”按钮h_axes2=axes('position',[0.05,0.05,0.40,0.38]); ht2=uicontrol(gcf,'Style','toggle','position',[0.7,0.08,0.08,0.05],'horizontal','left','fontname','楷体_GB2312','fontsize',14,'string','Grid Y', 'callback',['axes(h_axes2),','grid']); //制作“Grid Y ”按钮h_axes3=axes('position',[0.50,0.3,0.45,0.58]);ht3=uicontrol(gcf,'Style','toggle','position',[0.85,0.08,0.08,0.05],'horizontal','left','fon tname','楷体_GB2312','fontsize',14,'string','Grid X-Y', 'callback',['axes(h_axes3),','grid']);//制作“Grid X-Y ”按钮hpush1=uicontrol(gcf,'Style','push','position',[0.55,0.20,0.08,0.05],'horizontal','left','f ontname','楷体_GB2312','fontsize',14,'string','采集'); //设置“采集”按钮的位置和大小hpush2=uicontrol(gcf,'Style','push','position',[0.7,0.20,0.08,0.05],'horizontal','left','fo ntname','楷体_GB2312','fontsize',14,'string','滤波'); //设置“滤波”按钮的位置和大小hpush2=uicontrol(gcf,'Style','push','position',[0.85,0.20,0.08,0.05],'horizontal','left','f ontname','楷体_GB2312','fontsize',14,'string','停止');//设置 “停止”按钮的位置和大小ht0=uicontrol(gcf,'Style','text',...'position',[0.34,0.92,0.27,0.043],'horizontal','left','fontname','楷体_GB2312','fontsize',25,'string','轴心轨迹测量实验')//取名figure 为“轴心轨迹测量实验” ht1=uicontrol(gcf,'Style','text',...'position',[0.2,0.89,0.10,0.028],'horizontal','left','fontname','楷体//设置背景颜色 //设置unit 位置//设置用户缺省控件单位属性值_GB2312','fontsize',16,'string','X轴向波形')//命名第1个图形窗口“X轴向波形”ht2=uicontrol(gcf,'Style','text',...'position',[0.2,0.435,0.10,0.028],'horizontal','left','fontname','楷体_GB2312','fontsize',16,'string','Y轴向波形')//命名第2个图形窗口“Y轴向波形”ht3=uicontrol(gcf,'Style','text',...'position',[0.65,0.89,0.15,0.028],'horizontal','left','fontname','楷体_GB2312','fontsize',16,'string','X-Y轴合成波形')//命名第3个图形窗口“X-Y轴合成波形”set(hpush1,'callback',['set_param(''work2'',''SimulationCommand'',''start''),',...'t=timer(''TimerFcn'',''getdata'',''Period'',2,''ExecutionMode'',''fixedSpacing'',''TasksT oExecute'',inf),',...//设置定时器,运行getdata文件,与上面是一行'pause(2);start(t);',... //暂停2秒并启动定时器]);//“停止”按键引起的回调set(hpush2,'callback','stop(t);set_param(''work2'',''SimulationCommand'',''stop'');'); //停止定时器,mdl文件停止运行信号采集及处理界面如下:5.4 信号处理5.4.1 未滤波getdata代码set_param('work2','SimulationCommand','stop'); // mdl文件停止运行x1=evalin('base','xd.signals.values');//读取保存到工作空间的信号xd并绘制出来axes(h_axes1); //设置联系,第1个图形窗口plot(x1(1:600));//在第1个图形窗口中绘制X轴向波形y1=evalin('base','yd.signals.values');//读取保存到工作空间的信号yd并绘制出来axes(h_axes2); //设置联系,第2个图形窗口plot(y1(1:600));//在第2个图形窗口中绘制Y轴向波形set_param('work2','SimulationCommand','start'); //mdl文件运行axes(h_axes3); //设置联系,第3个图形窗口plot(x1(1:600),y1(1:600));//在第3个图形窗口中绘制X-Y轴合成波形5.4.2 低通滤波getdata代码set_param('work2','SimulationCommand','stop'); // mdl文件停止运行x1=evalin('base','xd.signals.values');//读取保存到工作空间的信号xd并绘制出来axes(h_axes1); //设置联系,第1个图形窗口Fs=5000; //采样频率fp=280;fs=450;//设置通带截止频率, 阻带截止频率wp=2*fp/Fs;ws=2*fs/Fs;rp=0.1;rs=60; [N,Wc]=buttord(wp,ws,rp,rs);//估算得到Butterworth低通滤波器的最小阶数N和3dB截止频率Wc[b,a]=butter(N,Wc);//设计Butterworth低通滤波器x1t=filter(b,a,x1);plot(x1t(1:200));y1=evalin('base','yd.signals.values');//读取保存到工作空间的信号yd 并绘制出来 axes(h_axes2); y1t=filter(b,a,y1); plot(y1t(1:200)); axes(h_axes3);plot(x1t(1:200),y1t(1:200));//在第3个图形窗口中绘制X-Y 轴合成波形set_param('work2','SimulationCommand','start');六、实验结果6.1 采集信号前后示波器scope 波形分析 1) 未采集信号时两示波器scope 的信号波形X 轴向波形Y 轴向波形2) 采集转子试验台信号后两示波器scope的信号波形X 轴向波形Y 轴向波形//调用Bufferworth 低通滤波器 //在第1个图形窗口中绘制X 轴向波形//设置联系,第2个图形窗口 //调用Bufferworth 低通滤波器//在第2个图形窗口中绘制Y 轴向波形 //设置联系,第3个图形窗口//mdl 文件运行结果分析:未采集信号时,示波器scope中显示的是随机变化的信号,信号的均值在零附近,不能反映试验台转子的轴心轨迹具体位置;采集信号后,两示波器scope显示的波形体现出一定的规律性,信号的均值偏离零,体现出轴心的实际位置。