钢材控制轧制和控制冷却
控轧控冷1
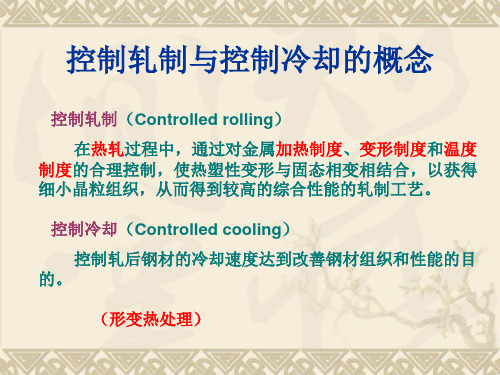
L0
拉伸性能
❖ 断面收缩率ψ: ❖ 断面收缩率ψ是评定材料塑性的主要指标。
AK A0 100%
A0
低碳钢的工程应力一工程应变曲线
true strain-stress line
2.0
Stress / MPa
1.5
Pm
Pb
1.0
0.5
0.0
0.0
0.5
1.0
1.5
2.0
载荷P压入被测材料表面,保持一定时间后卸除载荷,测出压 痕直径d,求出压痕面积F计算出平均应力值,以此为布氏硬度 值的计量指标,并用符号HB表示。
标注:D/P/T如120HB/10/3000/10,即表示此硬度值120 在D=10mm,P=3000kgf,T=10秒的条件下得到的。
简单标注:200~230HB
布氏硬度测定主要适用于各种未经淬火的钢、退火、
正火状态的钢;结构钢调质件;铸铁、有色金属、质地 轻软的轴承合金等原材料。
布氏硬度试验只可用来测定小于450HB的金属材料,
②洛氏硬度(HR)
基本原理—洛氏硬度属压入法洛氏硬度测定时需 要先后施加二次载荷(予载荷P1和主载荷P2)预 加载荷的目的是使压头与试样表面接触良好以保 证测量结果准确。洛氏硬度就是以主载荷引起的
对微量塑性变形的抗力
E /e
拉伸性能
❖ 抗拉强度b: ❖ 定义为试件断裂前所能承受的最大工程应力,
以前称为强度极限。取拉伸图上的最大载荷,即 对应于b点的载荷除以试件的原始截面积,即得抗 拉强度之值,记σ为b=b Pmax/A0
拉伸性能
延伸率: 材料的塑性常用延伸率表示。测定方法如下:拉伸
试验前测定试件的标距L0,拉伸断裂后测得标距为Lk, 然而按下式算出延伸率
控制轧制和控制冷却工艺讲义

控制轧制和控制冷却工艺讲义控制轧制和冷却工艺讲义一、轧制工艺控制1. 轧制温度控制a. 在热轧过程中,轧机和钢坯之间的接触摩擦会产生高温,因此需要控制轧机温度,避免过热。
b. 实时监测轧机温度,根据温度变化调整轧制速度和冷却水量,确保温度适中。
c. 使用专用液体和冷却器进行在线冷却,防止轧机过热引起事故。
2. 轧制力控制a. 测量轧机产生的轧制力,确保轧机施加的压力适中。
b. 监控轧制力的变化,根据钢坯的变形情况调整轧制力,使钢坯的形状和尺寸满足要求。
c. 根据轧制力的大小调整轧制速度,保持稳定的轧制负荷。
3. 轧制速度控制a. 根据不同钢材的特性和规格,调整轧制速度,确保成品钢材的质量和尺寸满足要求。
b. 控制轧制速度的稳定性,避免过快或过慢的轧制速度导致钢材质量不达标。
4. 轧辊调整控制a. 定期检查和调整轧辊的位置和间距,确保钢坯能够顺利通过轧机,避免产生不均匀的轧制力和过度变形。
b. 根据车间实际情况和轧制工艺要求,调整轧辊的工作方式和参数,使轧制过程更加稳定和高效。
二、冷却工艺控制1. 冷却水量控制a. 根据钢材的材质和规格,调整冷却水的流量和压力,确保钢材迅速冷却到所需温度。
b. 监测冷却水流量和温度,根据实时数据调整冷却水量,确保冷却效果和成品钢材的质量。
2. 冷却速度控制a. 根据不同的冷却工艺要求,调整冷却速度,使钢材的组织和性能满足要求。
b. 监控冷却速度的变化,根据实时数据调整冷却速度,确保成品钢材的质量和性能稳定。
3. 冷却方法控制a. 根据钢材的特性和要求,选择合适的冷却方法,如水冷、风冷等。
b. 根据不同冷却方法的特点和效果,调整冷却工艺参数,使冷却效果和成品钢材的质量最优化。
4. 冷却设备维护a. 定期检查和维护冷却设备,确保设备的正常运行和效果良好。
b. 清洗和更换冷却设备中的阻塞、损坏部件,保证冷却水的流量和质量。
以上是对控制轧制和控制冷却工艺的讲义,通过合理的工艺控制和设备维护,能够提高轧制和冷却过程的效率和质量,满足钢材的要求。
控制轧制与控制冷却

奥氏体晶粒的大小对钢材的力学性能有显著的 影响。一般用晶粒度表示晶粒的大小。因此, 影响。一般用晶粒度表示晶粒的大小。因此,测定奥 氏体的晶粒度通常作为鉴定钢材质量的指标之一。 氏体的晶粒度通常作为鉴定钢材质量的指标之一。
铁 碳 平 衡 相 图
二、钢的控制轧制
控制轧制是以钢的化学成分调整或添加微合 金元素Nb Nb、 Ti为基础 为基础, 金元素Nb、V、Ti为基础,在热轧过程中对钢 坯加热温度、 开轧温度、 变形量、 坯加热温度 、 开轧温度 、 变形量 、 终轧温度 等工艺参数实行合理控制, 等工艺参数实行合理控制 , 以细化奥氏体和 铁素体晶粒, 并通过沉淀强化、 铁素体晶粒 , 并通过沉淀强化 、 位错亚结构 强化充分发掘钢材内部潜力, 强化充分发掘钢材内部潜力 , 提高钢材力学 性能和使用性能。 性能和使用性能。
控轧控冷的物理冶金基础
轧后冷却速率对γ 轧后冷却速率对γ→α相变及其细化晶粒的 影响: 影响: 研究表明,提高轧后冷却速度能明显降低Ar 研究表明,提高轧后冷却速度能明显降低Ar3, 可抵消奥氏体晶粒细化及相变前形变给晶 粒细化带来的不利影响, 粒细化带来的不利影响,有力地增加了相 变细化晶粒作用。 变细化晶粒作用。这要求在控轧实践中对 冷却制度进行控制。 冷却制度进行控制。
控轧控冷的物理冶金基础
钢中溶质原子及第二相粒子: 钢中溶质原子及第二相粒子:在钢中适当添加 Nb、Ti等微合金元素 细化奥氏体晶粒. 等微合金元素, Nb、Ti等微合金元素,细化奥氏体晶粒. 这种利用高温形变再结晶与微合金元素溶解这种利用高温形变再结晶与微合金元素溶解析出的相互作用使晶粒充分细化的机制便是 控轧中控制奥氏体晶粒尺寸的主要的物理冶 金基础. 金基础.
控轧控冷的物理冶金基础
精选控制轧制和控制冷却工艺讲义

5.2.2现代化宽厚板厂控制轧制和控制冷却技术
近三十年以来 ,控制轧制和控制冷却技术在国外得到了迅速的发展 ,国外大多数宽厚板厂均采用控制轧制和控制冷却工艺 ,生产具有高强度、高韧性、良好焊接性的优质钢板。
获得细小铁素体晶粒的途径——三阶段控制轧制原理
奥氏体再结晶区域轧制 (≥ 950℃ )在奥氏体再结晶区域轧制时 ,轧件在轧机变形区内发生动态回复和不完全再结晶。在两道次之间的间隙时间内 ,完成静态回复和静态再结晶。加热后获得的奥氏体晶粒随着反复轧制——再结晶而逐渐变细。
图中第Ⅰ 阶段 ,由于轧件温度较高 ,奥氏体再结晶在短时间内完成且迅速长大 ,未见明显的晶粒细小。
不然,出于平整道次压下率确定不合适,引起晶粒严重不均,产生个别特大晶粒,造成混晶,导致性能下降。
道次变形分配
满足奥氏体再结晶区和未再结晶区临界变形量的要求,要考虑轧机设备能力及生产率的要求。压下量的分配一殷在奥氏体区采用大的道次变形量 ,以增加奥氏体的再结晶数量,细化晶粒。在未再结晶区在不发生部分再结晶的前提下,尽可能采用大的道次变形量,以增加形变带,为铁素体相变形核创造有利条件。在轧机能力比较小的条件下,采用在未再结晶区多道次、每道次小变形量并缩短中间停留时间的快轧控制方案,也取得较好的效果,而且不降低轧机产量。经验结论 在未再结晶区大于45—50%的总变形率有利于铁素休晶粒细化。
5.2板带钢控轧与控冷应用实例
5.2.1北极管线用针状铁素体钢
管线钢的发展历史
60年代末70年代初,美国石油组织在API 5LX和API 5LS标准中提出了微合金控轧钢X56、X60、X65三种钢 .这种钢突破了传统钢的观念,碳含量为0.1-0.14%,在钢中加入≤0.2%的Nb、V、Ti等合金元素,并通过控轧工艺使钢的力学性能得到显著改善。到1973年和1985年,API标准又相继增加了X70和X80钢,而后又开发了X100管线钢,碳含量降到0.01-0.04%,碳当量相应地降到0.35以下,真正出现了现代意义上的多元微合金化控轧控冷钢。
钢材的控制轧制和控制冷却
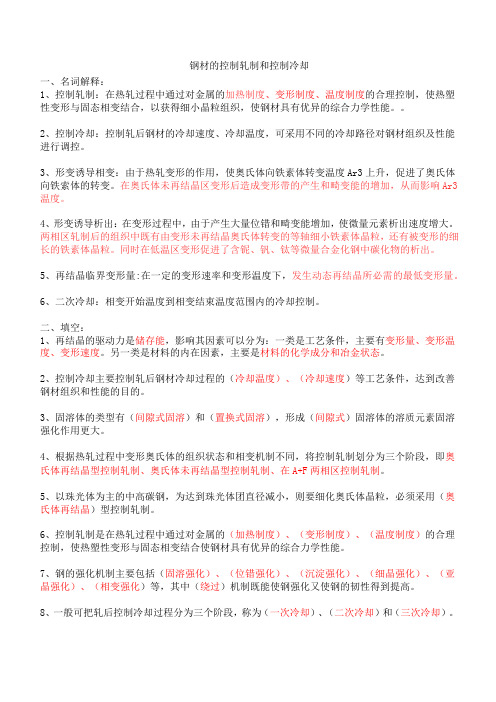
钢材的控制轧制和控制冷却一、名词解释:1、控制轧制:在热轧过程中通过对金属的加热制度、变形制度、温度制度的合理控制,使热塑性变形与固态相变结合,以获得细小晶粒组织,使钢材具有优异的综合力学性能。
2、控制冷却:控制轧后钢材的冷却速度、冷却温度,可采用不同的冷却路径对钢材组织及性能进行调控。
3、形变诱导相变:由于热轧变形的作用,使奥氏体向铁素体转变温度Ar3上升,促进了奥氏体向铁索体的转变。
在奥氏体未再结晶区变形后造成变形带的产生和畸变能的增加,从而影响Ar3温度。
4、形变诱导析出:在变形过程中,由于产生大量位错和畸变能增加,使微量元素析出速度增大。
两相区轧制后的组织中既有由变形未再结晶奥氏体转变的等轴细小铁素体晶粒,还有被变形的细长的铁素体晶粒。
同时在低温区变形促进了含铌、钒、钛等微量合金化钢中碳化物的析出。
5、再结晶临界变形量:在一定的变形速率和变形温度下,发生动态再结晶所必需的最低变形量。
6、二次冷却:相变开始温度到相变结束温度范围内的冷却控制。
二、填空:1、再结晶的驱动力是储存能,影响其因素可以分为:一类是工艺条件,主要有变形量、变形温度、变形速度。
另一类是材料的内在因素,主要是材料的化学成分和冶金状态。
2、控制冷却主要控制轧后钢材冷却过程的(冷却温度)、(冷却速度)等工艺条件,达到改善钢材组织和性能的目的。
3、固溶体的类型有(间隙式固溶)和(置换式固溶),形成(间隙式)固溶体的溶质元素固溶强化作用更大。
4、根据热轧过程中变形奥氏体的组织状态和相变机制不同,将控制轧制划分为三个阶段,即奥氏体再结晶型控制轧制、奥氏体未再结晶型控制轧制、在A+F两相区控制轧制。
5、以珠光体为主的中高碳钢,为达到珠光体团直径减小,则要细化奥氏体晶粒,必须采用(奥氏体再结晶)型控制轧制。
6、控制轧制是在热轧过程中通过对金属的(加热制度)、(变形制度)、(温度制度)的合理控制,使热塑性变形与固态相变结合使钢材具有优异的综合力学性能。
钢材控制轧制和控制冷却

钢材控制轧制和控制冷却(一)姓名:蔡翔班级:材控12学号:钢材控制轧制和控制冷却:控轧控冷是对热轧钢材进行组织性能控制的技术手段,目前已经广泛应用于热轧带钢、中厚板、型钢、棒线材和钢管等钢材生产的各个领域。
控轧控冷技术能够通过袭警抢话、相变强化等方式,使钢材的强度韧度得以提高。
Abstract: controlled rolling is controlled cooling of hot rolled steel organization performance control technology, has been widely used in the hot rolled strip steel, plate, steel, wire rod and steel pipe and other steel products production fields.Controlled rolling technology of controlled cooling can pass over assaulting a police officer, phase transformation strengthening and so on, to improve the strength of the steel toughness.关键词:宽厚板厂,控制轧制,控制冷却1.引言:控轧控冷技术的发展历史:20世纪之前,人们对金属显微组织已经有了一些早期研究和正确认识,已经观察到钢中的铁素体、渗碳体、珠光体、马氏体等组织。
20世纪代起开始有学者研究轧制温度和变形对材料组织性能的影响,这是人们对钢材组织性能控制的最初尝试,当时人们不仅已经能够使用金相显微镜来观察钢的组织形貌,而且还通过X射线衍射技术的使用加深了对金属微观组织结构的认识。
1980年OLAC层流层装置投产,控轧控冷在板带、棒线材等大面积应用,技术已成熟,理论进展发展迅速。
钢铁的控轧控冷工艺(TMCP)介绍
4.控制轧制的效应
(1)使钢材的强度和低温韧性有较大幅度的改善
控制轧制对细化晶粒有明显的作用,按常规轧制工艺, 铁素体晶粒最好的情况为7~8级,晶粒直径>20m,而 按控制轧制工艺,铁素体晶粒可达12级,其直径可为 5m。仅从这方面就可使钢材的强韧性能得到明显的改 善。
(2)可以充分发挥微量合金元素的作用
5.控制冷却的介绍
➢ 控制冷却存在的主要问题是高冷却速率下材料冷 却不均而发生较大残余应力、甚至翘曲的问题。 例如,作为控制冷却的极限结果,直接淬火的作 用早已为人们所认识。但是,其潜在的能力一直 未得到发挥,原因在于直接淬火条件下冷却均匀 性的问题一直没有得到解决,板形控制一直因扰 着人们。
5.控制冷却的介绍
对于控制冷却,有两个通俗说法:
(1)水是最廉价的合金元素 (可以用水替代合金元素来改变钢材的性能)
控制冷却的理念可以归纳为“水是最廉价的合金元素” 这样一句话。
(2)中国的多数(中板)轧机是世界上最干旱的轧机 (目前我们还没有充分利用好水的作用) -川崎水岛:12000 m3/h,迪林根:14000 m3/h -宝钢2050:14000 m3/h,1580: 13000 m3/h
钢铁的控轧控冷 工艺介绍
知识求索人
目录
1. 何为控轧控冷工艺? 2. 控轧控冷工艺的优势和应用 3. 控制轧制的类型 4. 控制轧制的效应 5. 控制冷却介绍
1.何为控轧控冷工艺?
➢ 控轧控冷工艺,又称TMCP(Thermo Mechanical Control Process:热机械控制工艺),是将控制轧制和控制冷却 技术结合起来的工艺,该工艺能够进一步提高钢材的强 韧性和获得合理的综合性能,并能够降低合金元素含量 和碳含量,节约贵重的合金元素,降低生产成本。TMCP 是20世纪钢铁业最伟大的成就之一!
控制轧制于控制冷却
1、控制轧制:在热轧过程中,通过对金属加热制度、变形制度和温度制度的合理控制,使热塑性形变与固态相变相结合,以获得细小的晶粒组织,使钢材具有优异的综合力学性能的轧制技术2、控制冷却:通过对控制轧后的钢材的冷却速度来改善钢材的组织性能.3、金属的强化:通过合金化,塑性变形和热处理等手段来提高金属的强度。
4、固溶强化:添加溶质元素使固溶体强度提高的方法.5、韧性:材料在塑性变形和断裂所吸收能量的能力。
6、微合金钢:钢种的合金含量小于0.1%。
7、IF钢:无间隙原子钢8、不锈钢:具有良好的抗腐蚀性能和抗氧化性的钢.9、变形抗力:在一定条件下材料变形单位面积的抵抗变形的力.10、在线常化工艺:在热轧无缝钢管中在轧管延伸工序后将钢管按常化热处理要求冷却到某一温度后在进加热炉然后就行减径轧制按照一定的速度冷却到常温。
11、变形温度贝氏体处理化工艺:在钢管轧制过程中不直接加热到马氏体温度一下,而是快速冷却带中温以后再置于静止的空气中冷却、以变形奥氏体转变为贝氏体省去回火工序。
12、高温变形淬火:钢管在稳定的奥氏体区域变形,而且一般温度在再结晶温度以上然后进行淬火,已获得马氏体组织。
13、低温相变淬火:将钢管加热到奥氏体状态,经一段保温冷却到Ac1高于M的某一中间温度进行变形后淬火的工艺。
14、非调质钢:将调质钢的化学成分进行调解并对轧制过程进行控制不进行调制其性能达到调制的水平。
1、控制轧制是指在热轧过程中通过对金属加热制度,温度制度,保险制度的控制而获得细小的晶粒2、控制冷却是控制轧后钢材的冷却速度来改善组织性能。
3、钢材的强化方法有固溶强化,变形强化,沉淀强化,弥散强化,亚晶强化,细晶强化,相变强化。
4、影响材料韧性有,化学成分,气体和夹杂物,晶粒细化,形变的影响,形变细化5、动态结晶是晶粒细化提高扩孔性的手段6、控制轧制的目标是为了获得较小的铁素体组织7、加快冷却速度可以获得细小的铁素体晶粒所以不产生奥氏体组织为界限8、贝氏体是结构性能钢有校坏的塑形焊接性能强韧性微合金钢是指钢中的合金元素总量小于0。
控轧与控冷
控轧与控冷一:名词解释控制轧制:是指在热轧过程中通加热制度,变形制度,温度制度的合理控制,使钢材具有优异综合理学性能的轧制新工艺。
控制冷却:是指控制轧后钢材的冷却速度达到改善组织和性能的目的。
金属强化:通过合金化,塑性变形,和热处理等手段提高金属材料的强度。
韧性:材料在断裂前在塑性变形和裂纹扩展时吸收能量的能力。
铁素体:铁或其内固溶体有一种或数种其他元素形成的体心立方固溶体。
奥氏体:γ铁内固溶有碳和其他元素的面立方固溶体。
贝氏体:钢在奥氏体化后被过冷到珠光体转变温度一下,马氏体转变温度以上这一中间温度区间,转变而成的有铁素体及其内分布着弥散的碳化物形成的亚稳定结构。
IF钢:又称无间隙,由于C,N含量低,在加入一定量TI,Nb使钢背固定成碳化物,氮化物或者碳氮化物,从而使钢无间隙存在。
不锈钢:在腐蚀介质中有良好的耐腐蚀性的钢。
双相钢:由马氏体或奥氏体基本两相组织构成的钢。
再结晶:经冷塑性变形的金属超过一定加热温度时,通过形核长大形成等轴晶粒无畸变新晶粒过程。
在线常化:在热轧无缝钢生产中,在轧管延伸工序后,将钢管按常化处理要求冷却到某一温度后,再进行加热炉生产,然后进行减轻轧制,按照一定冷却速度冷却至常温。
1·控制轧制与普通轧制的区别答:可以充分发挥微量元素的作用起沉淀强化,细化晶粒的作用;提高钢的强度的同时题干钢的韧性;降低了终轧温度,采用较低的卷曲温度,课消除或减少板卷头部,中部和尾部的强度差;采用低温大压下细化低碳钢的铁素体晶粒,提高强韧性。
2·控制冷却的目的答:节约冷床面积;防止或减轻转型材的翘曲和弯曲;降低残余应力;提高型材的力学性能及改善组织状态,简化生产工艺。
3·影响材料强韧性的因素答:化学成分;气体夹杂物;晶粒尺寸;沉淀析出;形变;相变组织等的影响。
其中气体夹杂物对韧性有害,晶粒越小,材料韧性越好。
4·提高材料强韧性的措施答:晶粒细化;冶炼:采用真空搅拌,减少有害成分;控扎:使形变强化,提高材料强韧性;热处理:阻止晶粒长大,使晶粒细化,提高强韧性。
控轧控冷
第一篇 控制轧制及 控制冷却理论
§1 钢的强化和韧化
— 钢的强化机制
金属材料的机械性能是指金属材料在外力(载荷)作用 时表现出来的性能。 包括强度、塑性、硬度、韧性及疲劳强度等。
§1.1钢的强化机制
对于钢材来说,在大多数情况下其力学性能是最重要的, 其中强度性能又居首位。
强度:金属材料抵抗塑性变形或断裂的能力,用给定 条件下所能承受的应力来表示。
S:形成硫化物,对韧性有害,解决办法:降低S含量或 者加入Zr和稀土元素以固定S,改善横行韧性。
3、压力加工工艺的控制 通过加工工艺控制晶粒度 材料理论韧性断裂强度 σc=(2Gγ/K)d-1/2 通过控制压力加工工艺可以控制晶粒的大小,改变 材料的韧性。 通过加工工艺控制晶体取向 钢在A+F或F区轧制后,F不发生再结晶,形成 {111}<110>织构,引起各向异性。 冷却工艺和材料的成分一起影响相变产物的种类、形貌、 数量等组织结构特征,从而影响材料的韧性。
3、影响因素 溶质与溶剂的原子半径差别 越大,强化效果越好; 有限固溶体中溶质元素溶解 量越大,强化效果越好; 溶质元素在溶剂中的饱和溶 解度越小,强化效果越好;
形成间隙固溶体的溶质元素 (C、N、B等)的强化效果 好于形成置换固溶体溶质元 素(如Mn、Si、P等)。
4、特点
提高合金的屈服强度、抗拉强度和硬度的同时,对其 它影响如下:
提高钢材韧性的途径
1、成分控制
合金元素加入基体(铁)中形成固溶体可强化合金,甚 至可析出第二相而强化合金,但同时合金元素含量的增 加也造成基体内缺陷的增加,降低材料的塑韧性。
V、Nb、Ti、Al、Zr等元素:能够细化晶粒,故既能提高 强度又能提高韧性; S、P:对韧性有害,尽量降低含量; C含量:C含量升高会增加钢中P的量,会降低钢的韧性, 故在钢种成分允许的范围内降低C含量; 钢中一般都含有二元以上的合金元素,合金组元之间有 交互作用,合金元素也可以通过不同途径影响断裂韧性, 故一般要具体分析,以使合金元素具有适当含量。
- 1、下载文档前请自行甄别文档内容的完整性,平台不提供额外的编辑、内容补充、找答案等附加服务。
- 2、"仅部分预览"的文档,不可在线预览部分如存在完整性等问题,可反馈申请退款(可完整预览的文档不适用该条件!)。
- 3、如文档侵犯您的权益,请联系客服反馈,我们会尽快为您处理(人工客服工作时间:9:00-18:30)。
钢材控制轧制与控制冷却姓名:蔡翔班级:材控12学号:钢材控制轧制与控制冷却摘要:控轧控冷就是对热轧钢材进行组织性能控制得技术手段,目前已经广泛应用于热轧带钢、中厚板、型钢、棒线材与钢管等钢材生产得各个领域。
控轧控冷技术能够通过袭警抢话、相变强化等方式,使钢材得强度韧度得以提高。
Abstract: controlled rolling is controlledcooling of hot rolled steel organization performance control technology, has been widely usedinthe hot rolled strip steel,plate,steel,wire rod and steelpipeand other steel products production fields。
Controlledrollingtechnology of controlled cooling can pas sover assaulting a police officer, phasetransformationstrengthening and so on,to improve the strengthofthe steeltoug hness、关键词:宽厚板厂,控制轧制,控制冷却1。
引言:控轧控冷技术得发展历史:20世纪之前,人们对金属显微组织已经有了一些早期研究与正确认识,已经观察到钢中得铁素体、渗碳体、珠光体、马氏体等组织。
20世纪20年代起开始有学者研究轧制温度与变形对材料组织性能得影响,这就是人们对钢材组织性能控制得最初尝试,当时人们不仅已经能够使用金相显微镜来观察钢得组织形貌,而且还通过X射线衍射技术得使用加深了对金属微观组织结构得认识、1980年OLAC层流层装置投产,控轧控冷在板带、棒线材等大面积应用,技术已成熟,理论进展发展迅速、2 控轧控冷技术得冶金学原理2。
1 钢得强化机理及对韧性得影响钢得强化机理主要有:固溶强化、析出强化、位错强化、细晶强化(晶界强化、亚晶强化)、相变强化等。
固溶强化,通过添加C、Mn、Si、Ni等合金元素来获得。
通过添加N b、V、Ti微合金元素及采用控制轧制工艺可实现细晶强化、析出强化、位错强化。
在采用强化手段提高钢得强度得同时,还必须考虑到强化手段对钢韧性得影响。
通常固溶强化(Ni元素除外)、析出强化、位错强化得结果导致脆性转变温度升高;而细晶强化使脆性转变温度下降。
因此通过控轧工艺以获得细小铁素体晶粒及采用奥氏体与铁素体两相区轧制获得铁素体亚晶组织,在提高钢得强度得同时,又可以降低脆性转变温度、加入Nb、Ti微合金元素后,由于析出强化使屈服强度上升,同时脆性转变温度也上升。
当采用控轧工艺后,细晶强化与析出强化共存,使屈服强度上升,脆性转变温度下降, 即提高了钢得强韧性。
V微合金元素细晶强化不明显,对改善钢得韧性不利,一般需与Nb组合使用,发挥V得析出强化与Nb得细晶强化得综合使用,以改善钢得强韧性。
钢中第二相组织得存在,对脆性转变温度有不利影响,因而尽可能降低其体积比或细化第二相组织使其均匀分布。
综合上述,细晶强化就是提高钢强韧性得最佳手段。
2.2获得细小铁素体晶粒得途径——三阶段控制轧制原理如上所述,细晶强化可获得高得强韧性,它可通过奥氏体再结晶区域控轧、奥氏体未再结晶区域控轧、奥氏体与铁素体两相区控轧来获得细小铁素体晶粒。
2.2、1 奥氏体再结晶区域轧制(≥950℃)在奥氏体再结晶区域轧制时, 轧件在轧机变形区内发生动态回复与不完全再结晶。
在两道次之间得间隙时间内, 完成静态回复与静态再结晶。
加热后获得得奥氏体晶粒随着反复轧制-—再结晶而逐渐变细。
图中第Ⅰ阶段, 由于轧件温度较高, 奥氏体再结晶在短时间内完成且迅速长大,未见明显得晶粒细小。
随着轧制温度得降低, 轧制道次得增多(即: 再结晶次数得增多),在低温再结晶区域(图中第Ⅱ阶段)轧制时,晶粒细化效果明显,强化作用充分体现出来,相变后得组织为细小等轴得铁素体晶粒与珠光体组织、2、2、2 奥氏体未再结晶区域轧制(〈950℃~Ar3)在奥氏体未再结晶区域(图中第Ⅲ阶段)轧制时,由于轧后得奥氏体不产生再结晶,因此随着轧制道次得增加,变形奥氏体晶粒沿轧制方向逐渐拉长,且在变形奥氏体晶粒中形成大量得变形带与位错。
变形奥氏体得晶界、变形带及位错等处就是铁素体形核部位。
随着变形量得增大,变形带数量增多,而且分布更均匀、另外奥氏体晶粒被拉长后,将阻碍铁素体晶粒得长大,因而相变后可获得更加细小得铁素体及珠光体组织。
对于微合金钢而言,微合金元素得碳氮化合物在相变时,优先在奥氏体晶界、变形带、位错处析出,从而阻碍铁素体、珠光体晶粒得长大。
2、2、3 奥氏体与铁素体两相区轧制(<Ar3)在(C+A)两相区(图中第Ⅳ阶段)高温区域轧制一定得道次,达到一定累积变形量,未相变得变形奥氏体由于变形而继续被拉长。
同时晶粒内形成得变形带及位错,在这些部位形成新得等轴铁素体晶粒。
而先析出得铁素体晶粒,由于塑性变形在晶粒内部形成大量得位错,并经回复形成亚晶结构。
这些亚晶结构使钢得强度提高,脆性转变温度降低、经(C+A)两相区轧制后,室温条件下金相组织较复杂,通常为由极细小得等轴铁素体、拉长得铁素体、具有亚晶结构得变形铁素体、极细小得珠光体组成得混合组织。
两相区轧制使相变后组织更加细小,同时产生了位错强化及亚晶强化,从而进一步提高了钢得强度与韧性。
2。
3 控制冷却得强韧性机理尽管控制轧制能有效地改善钢材得性能,但由于热变形因素得影响,使得钢得相变温度(Ar3)提高,致使铁素体在较高温度下析出, 在空冷过程中铁素体晶粒长大,从而使控制轧制效果受到限制。
因此,控制轧制必须配合加速冷却(即: 控制冷却)工艺,降低相变温度,进一步细化铁素体及珠光体组织,同时使Nb、Ti、V微合金元素得碳氮化合物更加弥散析出,进一步提高析出强化效应。
当冷却速度达到一定值时,轧后加速冷却得到得相变组织从铁素体与珠光体组织变成更细小得铁素体与贝氏体组织,贝氏体量随着冷却速度加快而增加,且生成得贝氏体组织极细,从而使钢板强度进一步提高、体现钢韧性指标得脆性转变温度受多种因素影响。
晶粒细化使脆性转变温度降低,而析出强化效应增强,珠光体与贝氏体得体积分量增加,使脆性转变温度升高。
加速冷却后最终脆性转变温度就是降低还就是升高,取决于上述两方面因素得综合作用结果。
只要合理选取加速冷却工艺,能在提高钢得强度得同时,维持高得韧性指标。
3 控制轧制得主要工艺参数控制轧制得主要工艺参数有:加热温度、加热时间、开轧温度、轧钢得变形量、精轧开轧温度、中间坯厚度与终轧温度。
3、1加热温度加热温度对Nb、V在奥氏体中得固溶量有很大得影响,在Nb、V能固溶得范围内尽量采用低温加热,使高温奥氏体晶粒不致于粗化,从而改善韧性、若加热温度过低,将存在部分未溶微合金碳氮化物,由于颗粒大于1000,不可能产生抑制奥氏体再结晶得作用。
适当提高再加热温度,使微合金元素得固溶量增加从而提高钢得强度与有效提高奥氏体得再结晶终止温度。
若再加热温度过高,则会使原始奥氏体晶粒粗化,从而使相变后得铁素体晶粒更粗大,不利于钢得韧性。
另外,板坯在炉加热时间对管线钢得探伤合格率有一定得影响、3、2轧钢得变形量轧钢过程中存在再结晶区域、部分再结晶区域与未再结晶区域。
为了细化铁素体晶粒,在γ再结晶区进行多道次大变形量(每道次变形量必须大于再结晶临界变形量)高温粗轧,通过形变/再结晶反复进行使奥氏体晶粒充分细化;同时还须保证粗轧结束时处于完全再结晶区,不能进入部分再结晶区,以免产生混晶组织、根据变形温度可知,此时变形处在部分再结晶区,奥氏体再结晶数量急剧增加。
同时变形量得增加使晶粒变形加剧,晶粒因发生畸变增加了储存能,发生再结晶时形核得驱动力增加,促进了再结晶得发生,使奥氏体晶粒更加细小,并最终获得细小得铁素体晶粒、在γ未再结晶区精轧时必须保证较大得累积变形量,这样才可使奥氏体晶粒充分压扁,在拉长得奥氏体晶粒内产生高密度得形变孪晶与形变带,同时微合金元素得碳氮化物因应变诱导析出,从而为铁素体转变提供更多得有利形核位置。
因此,在γ未再结晶区轧制时累积变形量越大,轧后铁素体晶粒得细化效果越好,改善钢综合性能得效果越显著。
3、3中间坯厚度γ再结晶区轧制结束后板坯待温时得厚度称为中间坯厚度。
适当增加中间坯厚度,可增大γ再结晶温度以下时得累积变形量(即精轧累积变形量),使变形奥氏体晶粒内部得形变能与形变缺陷增多,从而有利于提高相变驱动力,减少带状区域相变温度差,减小相变得不同时性,有利于铁素体均匀形核,最终使晶粒细化并减少带状组织,进一步改善钢得综合性能。
适当地增加中厚板轧件得中间坯厚度,致使表层奥氏体组织在低温时发生大变形,加上机架间除鳞高压水冷却、轧件与传送辊、轧辊得接触导热可快速降低表层组织得温度,促使表层组织发生应变诱导相变,在适当条件下可实现表层组织得超细晶化、在轧制过程中轧件表层组织硬化使其变形抗力逐渐增大,有利于变形向心部渗透,从而细化表层以下材料得晶粒,进而实现内部组织得细晶化。
4在中厚板中得应用中厚钢板“微合金化+控轧控冷"得生产工艺就是一种先进得优质中厚钢板生产工艺,可以取代多种钢板得“热轧+离线热处理”传统生产工艺,有效降低生产成本,就是生产高强度、高韧性优质钢板得工艺发展方向。
4。
1坯料加热钢坯加热温度得高低影响轧制前原始奥氏体晶粒得大小,从而影响钢材抗脆性断裂得能力。
为了使控轧控冷工艺生产得钢材具有良好得综合力学性能,要求钢坯加热温度应控制在1 100~1 250℃、考虑到二轧厂轧机主电机能力偏小,在这个温度范围轧制将很困难,为此将钢坯得加热温度定为1 150~1 280℃,在实际生产过程中根据轧制得温度情况在这个范围内进行调节。
正常情况下采用双炉模式生产,加热时间与保温时间都足够长,可使钢坯加热均匀。
4.2 坯料除鳞加热后坯料经除鳞箱进行初次除鳞,轧制时再根据板面情况利用机前机架间得高压水喷管进行二次除鳞,保证钢板表面质量良好,高压水压力应≥15 Mpa。
参考文献1、《管线钢得控轧控冷技术及其研究进展》高惠临2。
《合金元素与控轧控冷工艺在管线钢研制中得应用》丁文华3、《控轧控冷工艺在2 500 mm中厚板生产线上得应用》黄远坚王学志4、《单机架中厚板轧机得控轧控冷生产》钱振声(鞍钢设计研究院)5、《中厚钢板控轧控冷技术综述》陈瑛6.《控轧控冷工艺对低碳贝氏体钢组织性能得影响》李国彬7。
《控轧控冷技术得发展及在钢管轧制中应用得设想》王国栋。