炼钢用铁合金烘烤要求及加入时机
铁合金烘烤技术方案

铁合金烘烤装置技术方案江苏欧亚环保科技有限公司一、前言合金烘烤炉是烘烤铁合金的专用设备,通过对硅铁、锰铁、铬铁、钼铁、钛铁、钒铁等合金炉料进行脱水份烘烤,在200℃内进行脱游离水分烘烤,在400-600℃内进行脱结晶水分烘烤。
使合金达到要求温度,能满足炼钢工艺要求,实现缩短冶炼时间,提高钢材质量的目的。
对比传统烧嘴直接燃烧烘烤,热风式烘烤炉具有如下优势:1、热风炉与烘烤料仓采用分离式结构。
煤气可以充分燃烧,避免一氧化碳中毒事故。
2、安全措施齐全,热风炉内设置有火焰检测装置,对炉内燃烧状态进行实时监控。
3、优化煤气管路敷设、废气排放少,减少污染源及事故源。
4、采用专利技术重新设计热风燃烧、循环管路;极大提高了热能利用效率。
5、加热后废气及合金粉尘通过接入车间现有除尘管道排出,不增加尾气及合金粉尘污染。
6、所有外露高温管路均采用双层隔离结构,内壁风冷。
7、热风烘烤料仓内布置热风放散管,合金均匀受热,避免烧结。
8、人机交互简单、直观,操作方便。
二、设备总述铁合金烘烤是炼钢的必备工序之一。
通过采用合适的烘烤工艺,可以去除铁合金的吸附水和结晶水,降低铁合金带入钢液的水,有利于降低钢液的H含量,以满足炼钢工艺的使用要求。
本套装置采用热风式烘烤,由一套合金烘烤系统,一套热风炉;四个料仓,两个称重料斗组成。
其中两个料仓为一组,共用一个称重料斗。
热风炉产生的热量由调温风机调整至合适的温度、压力后再通过热风管道输送到各个烘烤料仓,料仓内安装有放热管,将热风分散到料仓内对合金原料进行烘烤、干燥脱水。
图一、设备预览图三、技术参数序号 项 目 参数1 成品料量(单炉) 最大容积:25m32 料仓形式矩阵式4 热风鼓风机 全压:8915-9698Pa热风量8588-11883m3/h5 冷风风量 2844 m3/h6 燃气热值(高炉煤气) 约700KJ/Nm37 烘烤温度 约350℃8 烘烤时间 连续烘烤9 烘烤热效率 ≥75%10 火焰监测器 紫外光型11 点火方式 电子点火12 燃烧率 98% 序号 名称1 热风炉体2 热风管路3 热风风机4 煤气烧嘴5 称重下料装置6 废气回收管路7 烘烤料仓8 热风回收管路13 燃烧器形式 内混式燃烧器14 电源 TN-S三相五线15 操作方式 就地点火+远程检测16 料仓出口下料能力(单仓) 5t/h三、设备主要结构说明:1、整体结构1.1钢结构机架:图2、钢结构机架地面框架型结构架,主体材料使用H型钢焊制成,底脚板使用预埋地脚螺栓固定,应力分布均匀,刚性好,结构合理。
6 转炉炼钢对铁合金的要求,常用铁合金的主要成分

转炉炼钢对铁合金的主要要求是:
(1)铁合金块度应合适,为10~50mm;精炼用合金块度为10~30mm,成分和数量要准确。
(2)在保证钢质量的前提下,选用价格便宜的铁合金,以降低钢的成本。
(3)铁合金应保持干燥、干净。
(4)铁合金成分应符合技术标准规定,以避免炼钢操作失误。
如硅铁中的铝、钙含量,沸腾钢脱氧用锰铁的硅含量,都直接影响钢水的脱氧程度。
转炉脱氧合金化常用的铁合金有Fe-Mn、Fe-Si、Mn-Si合金、Ca-Si合金、铝、Fe-A1、Ba-Ca-Si 合金、Ba-AI-Si合金等。
1-7 转炉炼钢对增碳剂有什么要求?
转炉冶炼中、高碳钢种时,使用含杂质很少的石油焦作为增碳剂。
对顶吹转炉炼钢用增碳剂的要求是固定碳要高,灰分、挥发分和硫、磷、氮等杂质含量要低,并要干燥,干净,粒度要适中。
其固定碳ωC≥96%,挥发分≤1.0%,ωS≤0.5%,水分≤0.5%,粒度在1~5mm;粒度太细容易烧损,太粗加入后浮在钢液表面,不容易被钢水吸收。
2023年精炼钢包烘烤安全技术操作规程

2023年精炼钢包烘烤安全技术操作规程____年精炼钢包烘烤安全技术操作规程第一章总则第一条目的和依据为了加强精炼钢包烘烤的安全管理,确保人员和设备的安全,根据国家相关法律法规,制定本规程。
第二条适用范围本规程适用于精炼钢包烘烤操作过程中的安全管理。
第三条定义1. 精炼钢包:指用于冶炼精炼钢的设备。
2. 烘烤:指进行精炼钢包干燥处理的过程。
第四条职责分工1. 生产主管负责组织和实施烘烤工作,并对烘烤人员进行培训和指导。
2. 烘烤人员负责具体的烘烤操作工作,并按照规程要求进行操作。
第二章安全管理第五条安全责任制1. 烘烤工作由生产主管统一负责,并严格执行安全操作规程。
2. 烘烤人员必须按照安全操作规程进行操作,确保人员和设备的安全。
第六条安全培训1. 烘烤人员必须持有相关岗位操作证书,经过培训合格后方可上岗。
2. 每年进行不少于一次的安全培训,提高烘烤人员的安全意识和操作技能。
第七条安全制度1. 制定相应的安全操作规程,对烘烤工作进行安全控制。
2. 定期检查和维护烘烤设备,确保设备的完好和安全运行。
第八条安全设施1. 确保工作场所的安全通道畅通,配备必要的灭火器材和紧急救援设备。
2. 配备防护装备,如防护眼镜、耳塞等,确保作业人员的安全。
第九条应急预案1. 制定针对烘烤工作的应急预案,明确各种紧急情况下的应对措施。
2. 每位烘烤人员必须熟悉应急预案并能熟练操作。
第三章操作规程第十条烘烤前准备1. 烘烤人员必须戴好防护装备,并检查相关设备的完好性。
2. 烘烤人员必须检查烘烤设备的电源接地是否正常,并检查设备的运行状态。
第十一条烘烤操作1. 烘烤过程中禁止使用易燃物品,必须保持工作区域的整洁。
2. 烘烤人员必须按照操作规程进行烘烤,严禁擅自改变操作方式。
3. 烘烤结束后,要及时关闭设备电源,确保设备的安全。
第十二条紧急情况处理1. 在发生火灾或其他紧急情况时,烘烤人员必须迅速采取措施,并第一时间报告相关负责人。
2023年铁水罐烘烤安全操作规程

2023年铁水罐烘烤安全操作规程第一章绪论1.1 在高温炼钢过程中,铁水罐是必不可少的设备之一。
为了保证生产过程的安全与效率,特制定本安全操作规程。
1.2 本规程适用于所有铁水罐烘烤作业,包括但不限于新罐烘烤、维修后的罐体烘烤等。
1.3 所有参与铁水罐烘烤作业的人员都必须严格按照本规程进行操作。
第二章作业前准备与检查2.1 操作人员在进入作业现场前,应熟悉铁水罐烘烤设备的结构、性能、安全操作规程以及相关控制系统。
2.2 操作人员应正确佩戴个人防护装备,包括安全帽、耐高温手套、防护眼镜、防护服等。
2.3 在进行铁水罐烘烤前,应对烘烤设备进行检查,确保设备完好无损、无泄漏,并确认附件设备和管道系统联通畅通。
2.4 检查并确保作业现场的通风、排烟设备正常运行,并进行充足的通风。
2.5 检查并确保烘烤设备的温度和烘烤速率符合铁水罐的技术要求。
第三章铁水罐烘烤操作规程3.1 在进行铁水罐烘烤前,应将铁水罐中的残留物清理干净。
3.2 确保铁水罐上的放空、进气孔及排污阀门畅通,并确保紧密密封。
3.3 在开始烘烤之前,应确保烘烤设备和控制系统正常运行,并进行预热。
3.4 确认烘烤设备达到所需温度后,将烘烤设备的加热源调整到合适的位置,并调整加热功率。
3.5 开始烘烤后,操作人员应始终保持对烘烤设备和罐体的监控,并及时处理设备故障或异常情况。
3.6 在烘烤过程中,操作人员应注意观察罐体表面的变化,一旦发现罐体出现渗漏、变形或其他异常情况,应立即停止烘烤并报告上级。
3.7 烘烤过程中应定期检测罐体表面温度,并确保温度不超过允许范围。
3.8 在烘烤结束后,应按照工艺要求冷却罐体,并确保罐体完全冷却。
第四章安全事故应急处置4.1 在铁水罐烘烤过程中,如发生火灾、爆炸或其他安全事故,应立即按照应急预案进行处置。
4.2 在应急处置过程中,应迅速切断电源、气源等供应,并组织人员撤离危险区域。
4.3 作业现场配备消防器材和救护设备,并确保操作人员熟悉使用方法。
一炼钢煤气烘烤操作规程
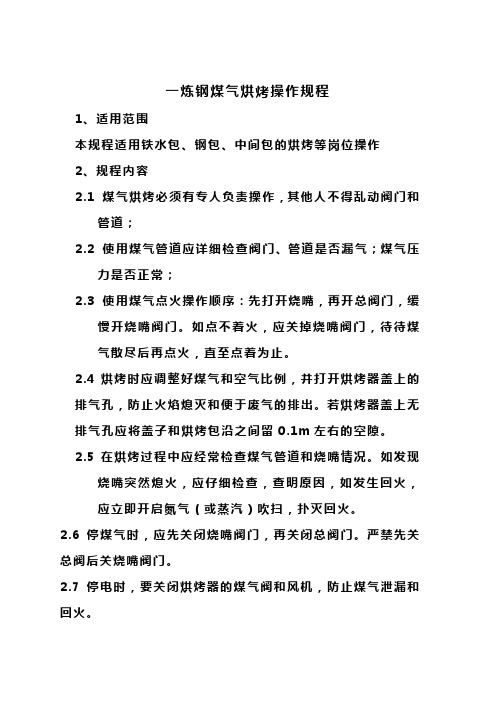
一炼钢煤气烘烤操作规程
1、适用范围
本规程适用铁水包、钢包、中间包的烘烤等岗位操作
2、规程内容
2.1 煤气烘烤必须有专人负责操作,其他人不得乱动阀门和
管道;
2.2 使用煤气管道应详细检查阀门、管道是否漏气;煤气压
力是否正常;
2.3 使用煤气点火操作顺序:先打开烧嘴,再开总阀门,缓
慢开烧嘴阀门。
如点不着火,应关掉烧嘴阀门,待待煤
气散尽后再点火,直至点着为止。
2.4烘烤时应调整好煤气和空气比例,并打开烘烤器盖上的
排气孔,防止火焰熄灭和便于废气的排出。
若烘烤器盖上无排气孔应将盖子和烘烤包沿之间留0.1m左右的空隙。
2.5在烘烤过程中应经常检查煤气管道和烧嘴情况。
如发现
烧嘴突然熄火,应仔细检查,查明原因,如发生回火,
应立即开启氮气(或蒸汽)吹扫,扑灭回火。
2.6停煤气时,应先关闭烧嘴阀门,再关闭总阀门。
严禁先关总阀后关烧嘴阀门。
2.7停电时,要关闭烘烤器的煤气阀和风机,防止煤气泄漏和回火。
2.8在煤气使用区发现有人头晕、恶心、眼花等煤气中毒先兆,应先将中毒者立即带出现场,并通知煤气防护站处理。
3、注意事项
3.1、煤气区域操作不得少于两人,一人操作、一人监护,
煤气点火、停止的联系要有专人负责。
3.2、使用煤气压力不得低于规定范围。
3.3、煤气直管道阀门、喷咀阀门、法兰处经常用肥皂水试
漏,发现问题立即通知有关部门及时处理。
3.4、经常对操作人员进行煤气使用专门安全教育。
一炼钢
2012年2月22日。
钢水包烘烤技术要求

钢包烘烤方案
钢包是盛储钢水的容器,钢水进入钢包后,在传输和浇注过程中要损失大量热量,其中钢包内衬蓄热占据很大一部分热量损失,因此对钢包早使用前必须充分地烘烤升温。
具体烘烤方案如下:
1、旧包烘烤工艺:
前 30 分钟,以缓速加热速度预热钢包,待温度升至 100℃后,以大火烘烤将钢包加热到所需温度要求,并保温 1 小时(冶炼材质为高锰钢时,钢包烘烤温度应达到 800℃以上;冶炼材质为合金钢时,钢包烘烤温度应达到 600℃以上)。
0.5 时间h
图 1 旧包烘烤工艺
2、新包烘烤工艺:
未经使用新购置的钢包,应以 50-70 ℃/h 升温速率,中小火烘烤 12-24 小时,最终烘烤
温度应大于800℃。
时间h
图 2 新包烘烤工艺
注意事项:
1)从室温升温至100℃,应有缓慢的升温速度,升温速度过快,大量气化水分无法排出,会产生破坏性蒸汽压力,使耐火材料产生裂纹或打结料产生掉皮现象。
2)烘烤期间,做好炉情况的观察、监控和维护工作,可以及时发现不正常情况,以便采取措施,保证烘烤顺利进行。
3)对烘烤中出现的不正常现象和问题采取的相应措施,都应做出原始记录,以便日后存查,并从中吸取教训,作为改进烘烤工作的依据。
4)设立警戒线,非操作人员严禁入内。
铁合金在线烘烤技术及实践
( 福建三钢炼钢厂 ,福建 三明 350 ) 6 0 0
摘要 : 炼钢厂铁合金烘烤 的原理和方案进行研究 和探讨 ,初步制定 了铁合金在线烘烤工艺方案,并对铁合金在线烘烤工艺进行优 对 化改造 ,实现 了铁 合金 的在 线烘烤 。实践表明 :铁合金可烘烤至 3 0℃以上 ,利用烘烤 的铁 合金料 可使平均 出钢温度降低 5 . 0 0 4℃,
气和料仓进 热烟气两部分; 因进 热烟气管径偏小 ,且阻
力大影响热烟气流速,及料仓下部 ( 震料 口)不严密性,
为此料仓下部 ( 震料 口)进入风单位流量 大于 热烟气 , 冷
却合金温度 的同时, 造成引风机吸引热烟气 作用降低。 大
部分 热烟气停 留在 热气发生炉并 冒出炉外和供热烟气 管 道处, 热气发生 炉和供热烟气管道常保持在高温状态, 加
废 烟气 由引风机 从料仓 中上部抽 出,完成加热过程 。
铁合 金料在料仓 中的烘烤 周期最小 应为 1 0~ 10mi, 5 8 n 而试验烘烤 2 0 i 4 n料仓温度小于 10℃。 m 0 经过一个月的 调试,未能达到预期 目标要求 。 存在的 问题有:①管道热 损失大,热烟气 总管温度最高达 54℃,热烟 气支管表面 5
21 0 2年 第 4 1卷 第 5期
VO1 41 N O. 201 . 5 2
童
加
熟
I NDUS T砌 AL HEATI NG
4 9
DO : 1 . 6  ̄ sn 0 2 13 .020 .1 I 03 9 .i .1 0 —6 92 1.50 7 9 s
铁合金在线烘烤技术及实践
£ 为管道长度, 为管道附件 、 m; 阀门等局部热损失系数 。
铁合金烘烤炉说明
合金烘烤炉说明书合金烘烤炉是烘烤铁合金的专用设备,通过对硅铁、锰铁、铬铁、钼铁、钛铁、钒铁等合金炉料进行脱水份烘烤,在200℃内进行脱游离水份烘烤,在400-600℃内进行脱结晶水份烘烤。
使合金达到要求温度,能满足炼钢工艺要求,实现缩短冶炼时间,提高钢材质量的目的。
一、技术说明:由于合金料在200℃左右脱游离水,在400-600℃内脱结晶水,合金料需要脱水,加热温度必须达到400℃以上,因此铁合金烘烤装置作为烘烤铁合金的专用设备,必须满足以下要求:1、合金料经过加热,达到400-500℃;2、加热形式:间接加热形式,采用烘烤炉形式,形成过热风(500-600℃),用过热风加热合金块;3、燃烧采用过氧燃烧,煤气燃烧率在99%以上,形成无害烟气;4、燃烧器口采用耐热钢,延长使用寿命;5、控制方式:手动控制;自动点火;6、点火气体:乙炔或天然气;7、燃烧介质:转炉煤气;二、工作原理及特点:1、转炉煤气通过燃烧器燃烧,产生约1200℃左右的高温烟气,吹进燃烧室,在燃烧室内与所配冷风初步混合,并在高温下进一步反应,燃尽高炉煤气(一氧化碳);形成无毒的约800℃左右的高温烟气;在燃烧室末端,热烟气与配风充分混合,形成500-600℃左右的热风。
2、由于合金使用上,炼钢是间断性出料,加热是连续性加热,且加热的热风喷口在合金料仓的底部,形成自下向上逆流加热,使料仓出料接近热风温度,达到400-500℃。
3、由于热风温度过高,为保证热效率,可以给热风管道加保温。
三、设备构成:设备由转炉煤气燃烧器,混风用热风炉,助燃风机,冷风混风风机,热风管路及电控系统组成。
1、燃烧器含自动点火烧嘴:自动点火烧嘴和煤气烧嘴头均为不锈钢;2、混风用热风炉由燃烧室,内衬(不锈钢)及热风炉外壳组成,混风机构实现最后热风,实现烘烤用的热风3、观火孔可以清楚观测火焰样式,掌控火焰燃烧情况。
4、助燃风机供烧嘴燃烧用空气。
5、冷风混风风机直接进入混风用热风炉,迅速提升自己温度,降低高温热风温度,调和成工艺需要的热风温度。
钢包烘烤补充规定
生产间隙、计划检修时煤气使用管理规定(暂行)1、钢包烘烤(上线使用温度大于800℃)1.1炼钢停产时间小于2小时,钢包下线后做保温烘烤。
要求包沿必须清理干净,放包时包中心轴和包盖中心轴尽量重合(相距不得大于100mm),包盖和包沿间距不大于100mm,烘烤时采用中火(煤气参考流量:钢包在线烘烤器0.5~0.55t/h)。
根据包的使用时间,提前1小时(卧式烘烤器提前1.5小时)开到大火(煤气流量≥0.9t/h)烘烤到使用。
1.2停产时间大于2小时小于4小时,提前90分钟大火烘烤,停产时间大于4小时小于6小时,提前2小时大火烘烤,停产时间大于6小时小于8小时,提前3小时大火烘烤。
大于8小时小于24小时,提前4小时烘烤,停产时长大于24小时小于72小时,提前5小时大火烘烤,当钢包停烤时间大于72小时,包耐材温度已经降到环境温度时,应提前8小时(小火1小时、中火2小时、大火5小时)逐渐升温到使用(卧式烘烤器将大火延长至7小时)。
冬季将烘烤时间在以上基础上提前30分钟。
1.3烘烤时间根据各个钢包上线的顺序依次延迟烘烤30分钟。
2、铁包烘烤:停产时间小于3小时,采取落盖保温措施,大于3小时,兑铁前提前1小时大火烘烤。
大于6小时,提前2小时烘烤,大于12小时,提前3小时烘烤,大于24小时,提前4小时烘烤。
冬季在此基础上提前30分钟烘烤。
3、中包烘烤:(上线使用温度大于1000℃)提前3.5小时。
冬季小火烘烤时间在此基础上提前30分钟。
4、大火烘烤煤气压力大于4000pa,煤气流量大于0.9 t/h(约700m3/h)。
如烘烤压力低,调度室必须向煤气柜反馈信息进行调整。
5、正常情况下,只允许离线烘烤一个备用包,耕生公司必须合理调配上线钢包,避免生产过程中一个以上的钢包同时下线。
6、如果由于各种原因(如天气潮冷、煤气压力不足等)造成冷修包烘烤周期延长影响钢包周转,现场管理人员在向调度室汇报并征得同意后可以启用全部离线钢包烘烤器。
铁合金行业矿热电炉的开炉及烘炉工作事项
铁合金行业矿热电炉的开炉及烘炉工作事项铁合金矿热电炉的开炉、烘炉工作。
(1)烘炉电炉炉体砌成后,在正式投产前需进行烘炉。
所谓烘炉,就是采用加热的方法,使炉衬和电极逐步适应加料熔炼的一种操作。
烘炉的主要目的是烘干炉衬和焙烧电极。
烘炉质量不仅会影响炉衬的使用寿命,而且还会影响电炉是否能顺利投产。
例如炉衬烘烤不良,就会使炉体使用寿命减少,并影响开炉和延缓整个冶炼过程,再如在矿热炉中如果电极焙烧不良,则不仅会延缓冶炼过程,而且还会给操作带来困难,甚至无法维持正常冶炼。
电炉的烘炉,在一般情况下应严格按照烘炉进度表进行。
烘炉时间的长短,主要取决于炉子的大小、炉衬的种类、所炼铁合金的品种及烘炉的方法。
整个烘炉过程分为两个阶段:第一阶段是柴烘、油烘或者焦烘,其目的是焙烧电极,使电极具有一定的承受电流的能力;第二阶段是电烘,其目的是进一步焙烧电极、烘干炉衬,并使炉衬达到一定温度以适应加料熔炼。
(2)烘炉前的准备工作①检查和试车各设备系统必须进行全面的检查和试车(如导电系统、水冷系统、电极吊挂系统、配料系统、电极升降系统、电极压放系统、吊运系统,封闭炉还包括封闭系统、煤气净化系统等)。
②垫黏土砖为了防止电极与炉底相黏结,应先在电极底下的炭砖上垫一层65mm的黏土砖,而后将有底电极平稳地坐落在黏土砖上。
③装电极糊在有底电极壳内装入足够量的电极糊,保证电极筒内铜瓦以上的糊柱高度为2〜3m,以便获得烧结致密的电极。
④把持器放到上限位置将电极把持器放到上限位置,使电极有足够长的工作端,以保证在随后的供电过程中有足够长的烧结电极。
⑤电极筒扎孔电极在焙烧过程中有大量挥发分逸出,为了保证挥发分顺利外逸,加快电极烧结速度,并防止电极筒胀坏,在电极工作端部的电极壳上,可均匀地扎一些孔径为2mm的小孔。
⑥铁口放钢管在出铁口内放一直径为80〜100mm内小外大的钢管,中间填以焦粉,两端塞以泥球,有时为了便于通风,出铁口可以不堵。
⑦调节冷却水和风量烘炉初期电极和其它设备承受的热量较少,因而在开始循环冷却水只需开到最小量,保持水流畅通就行。
- 1、下载文档前请自行甄别文档内容的完整性,平台不提供额外的编辑、内容补充、找答案等附加服务。
- 2、"仅部分预览"的文档,不可在线预览部分如存在完整性等问题,可反馈申请退款(可完整预览的文档不适用该条件!)。
- 3、如文档侵犯您的权益,请联系客服反馈,我们会尽快为您处理(人工客服工作时间:9:00-18:30)。
1、块度及烘烤要求
铁合金
项目
硅铁
硅锰
锰铁
铬铁
钨铁
块度(kg)
0.5~4
0.5~10
0.5~10
0.5~10
0.5~5
烘烤
600~800℃(一般钢种≥2小时,不锈钢≥4小时)
铁合金
项目
钛铁
钒铁
钼铁
硼铁
铝锭
块度(kg)
0.2~4
0.2~6
0.2~4
0.2~2
30~50
铝
冶炼含Al钢当脱氧良好时抬电极扒出全部炉渣加在镜面上。用耙子将Al锭打入钢液,及时造渣。
8~15
70~80
3、加入铁合金对钢水温度的影响
合金铁
调1%对钢液温度影响℃
1570℃
1620℃
硅铁(45% Si)
+0.5
+8.8
硅铁(75% Si)
+16.5
钛铁(25% Ti)
+1.0
锰铁(75% Mn)
-13.2
-10
钒铁(40% V)
-9.1
铬铁(60% Cr)
-15.3
-12.5
钨铁(65% W)
-7.2
硅锰(17%Si、70%Mn)
-7.8
-2.3
硅锰(20%Si、70%Mn)
-6.7
-0.6
钼铁
-12.1
镍
-12.6
95~98
钼铁
装料时加入。对同时含V、含Al的钢种在加Al5分钟后而不迟于出钢前5分钟加入。
含钒≥0.5
≥25
95~98
含钒<0.5
≥10
锰铁
在薄渣下加入,如需调Cr于加Cr铁前加入。
≥10
95~98
硅铁
在出钢前加入
含Si钢
10~20
93~97
其它钢种
≥5
钛铁
在出钢前加入
不含Ti钢
5~10
不计烧损
含Ti≤0.15
5~10
30~50
含Ti≥0.20
10~15
55~65
铬铁
在薄渣下或第一批脱氧剂后加入,对同时含W的钢号应在第一批脱氧剂后加入,还原中期补加不足部分。
≥10
95~97
铌铁
在还原期加入
≥40
95~99
硼铁
硼铁在调完化学成分插铝加钛后用铁皮包好插入钢中或当钢包中有五分之一至四分之一钢水时加入钢流上。要计量准确,块度≤25mm。
干燥
100~150℃干燥≥4小时
铁合金
项目
中锰
金属锰
电解锰
硅钙块
无碳铬
块度(kg)
0.5~10
烘烤
100~150℃干燥≥4小时
2、加入时机
合金铁
加入时机及要求
最终调整量(%)
最终调整距出钢时间(分)
还原期补加回收(%)
钨铁
氧化末期或薄渣下加入
≤0.3
≥20
95
>0.3
≥40
镍
装料时装在炉四周,严禁装在电极下面。尽量在氧化期调整。还原期调整量不超过0.10%