八大浪费培训教材
合集下载
八大浪费培训教程

八大浪费---库存浪费
4.改善库存多的方法:
分类管理法----根据生产计划及交货期分批 购入原材料,保证最低库存量;通用性生产 物料考虑即时生产或即时送货的方式,降低 库存.
JIT库存管理----广告牌管理 控制在库金额
定期盘点
库存警示方法
八大浪费---过度加工
1.定义:
过度加工主要包含两种意思: 1) 多余的加工 2) 过分精细的加工
八大浪费
基本原则
▪ 准时参加 ▪ 手机静音或关机 ▪ 仔细聆听–他人说话时,尊重他人 ▪ 全心全力参与 ▪ 共同目标–有一个更深刻的理解 ▪ 培训结束时参加测试
Document Properties
Creator
:
Function
:
Verified
: Name here
Approver
: Name here
供应﹑管理方面考虑,采用最为合适的形状.
八大浪费---搬运浪费
搬运手段合理化
1. 搬运作业遵循原则: 机械化原则;自动化原则;标准化原则;均衡原则;及时原则; 直线原则;安全第一原则.
2. 搬运方法: 传送带; 定量搬运和定时搬运; 搬运工具的合理化.
3. 现场布置
八大浪费---过量生产
1.定义:
生产了过多的,超出客户或下游工序需求的数量
哈, 我把所 有的订单都 做完了
我们还得弄一个大点 的仓库!
我们马上就完工 了
结果呢?
八大浪费---过量生产
2.原因可能是…
过量计划:信息不准;计划错误;计划失当;信息传递不 畅;制程反应速度慢 前工序过量投入:工时不平衡;广告牌信息错误;不是 一个流;工作纪律差
等浪费,包
企业八大浪费培训ppt课件ppt
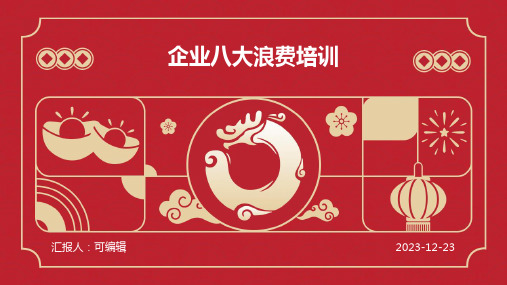
2. 更新设备和技术:引进先进的生产设备和工艺技术,提高加工效率和产品质量, 同时减少对人工操作的依赖,降低人为因素导致的加工浪费。
应对措施与解决方案
3. 提高员工技能水平
加强员工技能培训和技能认证,提高员工的技能水平 和操作熟练度,确保员工能够按照标准操作规程进行 生产,减少因操作不当导致的加工浪费。
表现
设备空转、操作员等待、生产流程停 滞等。
产生原因与影响
产生原因
生产计划安排不合理、设备故障率高、物料供应不及时等。
影响
降低生产效率、增加生产成本、影响产品质量和客户满意度等。
应对措施与解决方案
应对措施
优化生产计划、加强设备维护保养、提高物料供应的及时性等。
解决方案
采用精益生产管理、引入自动化和智能化设备、建立快速响应机制等。
引入自动化和智能化设备
通过自动化和智能化设备来替代人工操作, 提高生产效率。
08 管理浪费
CHAPTER
定义与表现
定义
管理浪费是指企业在管理过程中出现的资源浪费现象,如决策失误、组织结构 不合理、流程繁琐等。
表现
管理浪费通常表现为工作效率低下、资源分配不均、信息传递不畅、决策缓慢 等问题。
产生原因与影响
原因
管理浪费的产生原因主要包括管理层决策能力不足、组织结构复杂、缺乏有效的 管理制度和流程等。
影响
管理浪费会导致企业资源浪费、效率低下、竞争力下降,甚至可能导致企业破产 倒闭。
应对措施与解决方案
应对措施
提高管理层决策能力、优化组织结构 、简化流程、建立有效的管理制度和 流程等。
解决方案
引入先进的管理理念和方法,加强内 部培训和人才培养,建立科学的管理 体系和流程,提高企业整体的管理水 平。
应对措施与解决方案
3. 提高员工技能水平
加强员工技能培训和技能认证,提高员工的技能水平 和操作熟练度,确保员工能够按照标准操作规程进行 生产,减少因操作不当导致的加工浪费。
表现
设备空转、操作员等待、生产流程停 滞等。
产生原因与影响
产生原因
生产计划安排不合理、设备故障率高、物料供应不及时等。
影响
降低生产效率、增加生产成本、影响产品质量和客户满意度等。
应对措施与解决方案
应对措施
优化生产计划、加强设备维护保养、提高物料供应的及时性等。
解决方案
采用精益生产管理、引入自动化和智能化设备、建立快速响应机制等。
引入自动化和智能化设备
通过自动化和智能化设备来替代人工操作, 提高生产效率。
08 管理浪费
CHAPTER
定义与表现
定义
管理浪费是指企业在管理过程中出现的资源浪费现象,如决策失误、组织结构 不合理、流程繁琐等。
表现
管理浪费通常表现为工作效率低下、资源分配不均、信息传递不畅、决策缓慢 等问题。
产生原因与影响
原因
管理浪费的产生原因主要包括管理层决策能力不足、组织结构复杂、缺乏有效的 管理制度和流程等。
影响
管理浪费会导致企业资源浪费、效率低下、竞争力下降,甚至可能导致企业破产 倒闭。
应对措施与解决方案
应对措施
提高管理层决策能力、优化组织结构 、简化流程、建立有效的管理制度和 流程等。
解决方案
引入先进的管理理念和方法,加强内 部培训和人才培养,建立科学的管理 体系和流程,提高企业整体的管理水 平。
工厂八大浪费之管理的浪费培训资料
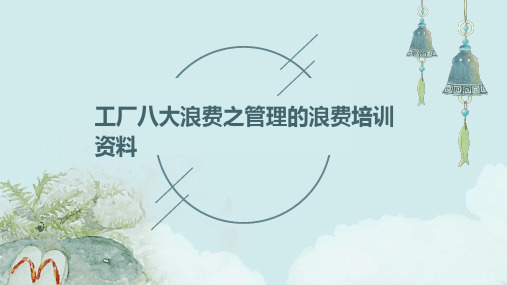
削弱企业竞争力
管理浪费可能导致企业运营效 率低下,难以满足市场需求,
从而削弱企业的竞争力。
案例分析
某制造企业由于组织结构臃肿,管理层次过多,导致生产 流程不畅,资源分配不合理,生产效率低下。经过优化管 理流程和组织结构后,生产效率得到显著提高。
某科技公司在研发阶段由于决策失误,导致项目进度延误 ,资源浪费严重。经过重新调整研发计划和资源分配,项 目最终得以成功完成。
成本评估
分析管理环节的成本构成 ,判断是否存在成本浪费 现象。
质量评估
评估管理流程对产品质量 的影响,判断是否存在质 量浪费现象。
实际操作
制定改进计划
根据识别和评估结果,制定针对 性的改进计划,明确改进目标和
方法。
实施改进措施
按照改进计划逐步实施改进措施, 不断优化管理流程,减少浪费现象 。
持续监控与评估
对改进措施的实施效果进行持续监 控和评估,确保改进成果的可持续 性。
04
管理浪费的根源与解决策略
根源分析
缺乏有效的管理流程
管理流程不清晰、不规范,导致资源分配不合理,工作效率低下 。
决策失误
管理者在决策过程中缺乏充分的信息和科学的方法,导致决策失误 ,造成资源浪费。
人员素质不高
员工和管理者素质不高,缺乏必要的技能和知识,导致管理效率低 下,浪费资源。
解决策略
优化管理流程
01
通过制定清晰、规范的管理流程,提高工作效率,减少资源浪
费。
提高决策水平
02
加强决策信息的收集和分析,采用科学的方法进行决策,降低
决策失误的风险。
培训与提高人员素质
03
通过培训、选拔和引进高素质人才,提高员工和管理者的素质
管理浪费可能导致企业运营效 率低下,难以满足市场需求,
从而削弱企业的竞争力。
案例分析
某制造企业由于组织结构臃肿,管理层次过多,导致生产 流程不畅,资源分配不合理,生产效率低下。经过优化管 理流程和组织结构后,生产效率得到显著提高。
某科技公司在研发阶段由于决策失误,导致项目进度延误 ,资源浪费严重。经过重新调整研发计划和资源分配,项 目最终得以成功完成。
成本评估
分析管理环节的成本构成 ,判断是否存在成本浪费 现象。
质量评估
评估管理流程对产品质量 的影响,判断是否存在质 量浪费现象。
实际操作
制定改进计划
根据识别和评估结果,制定针对 性的改进计划,明确改进目标和
方法。
实施改进措施
按照改进计划逐步实施改进措施, 不断优化管理流程,减少浪费现象 。
持续监控与评估
对改进措施的实施效果进行持续监 控和评估,确保改进成果的可持续 性。
04
管理浪费的根源与解决策略
根源分析
缺乏有效的管理流程
管理流程不清晰、不规范,导致资源分配不合理,工作效率低下 。
决策失误
管理者在决策过程中缺乏充分的信息和科学的方法,导致决策失误 ,造成资源浪费。
人员素质不高
员工和管理者素质不高,缺乏必要的技能和知识,导致管理效率低 下,浪费资源。
解决策略
优化管理流程
01
通过制定清晰、规范的管理流程,提高工作效率,减少资源浪
费。
提高决策水平
02
加强决策信息的收集和分析,采用科学的方法进行决策,降低
决策失误的风险。
培训与提高人员素质
03
通过培训、选拔和引进高素质人才,提高员工和管理者的素质
八大浪费教材

TPM推进科
TPM推进科
过量生产浪费
TPM推进科
二. 过量生产浪费
(四) 浪费的消除:
计划﹕管理信息系统
计算机信息集成控制 掌控不良(报废)率 实时校正计划
生产模式﹕精益生产
平衡改善 一个流(单次传送量标准) 缩短生产周期和切换速度
交付周期=∑(单件生产时间*批量)
TPM推进科
二. 过量生产浪费
多数发生于支援部门
计划变更 来料/制品/成品的检验 繁杂的审批过程
不必要非增值
完全属于浪费
过多的搬运
冗长的会议
TPM推进科
引子
增值活动 不必要但非 5% 增值活动 必要但非增 35% 值活动60%
顾客只愿意冲着那5%的增值掏腰 包
TPM推进科
制造业管理误区
离岛式车间布局
原料 仓库 A车间 B车间 C车间 D车间 成品 仓库
• 高的存货水平
TPM推进科
一. 不良品浪费
(三)不良品浪费产生原因
供应
制造
使用
来料不良﹕供应商流出不良品﹔物流破坏﹔进料检验﹑投入检查或后工序未发现﹔
制程不防呆﹔
制程不良﹕作业者损坏﹔设备﹑治工具不防呆﹔制程不防呆﹔
使用者破坏﹕未提醒﹔未按要求﹔人为破坏﹔不小心损坏﹔设计不防呆﹔
TPM推进科
一. 不良品浪费
过程浪费
TPM推进科
三. 过程浪费
(三) 浪费的产生:
流程﹕流程设计﹔车间、设备布局﹔参数设定﹔
制造系统柔性﹔浪费警觉性﹔条件局限性﹔
强度﹕系统稳定性﹔标准﹔
TPM推进科
三. 过程浪费
(四) 浪费的消除:
流程﹕简化生产流程﹔提高系统柔性﹔改变工作台面布置﹑摆放方式﹑参数设定﹔ “缩短距离﹑减少阻力﹑简化程序﹑精减过程” 强度﹕系统稳定性﹔制订强度标准﹔明确操作要求﹔制程防呆……
八大浪费精品教材

1.邊送邊做﹔ 2.划分節距線﹔ 3.依產距時間設定速度; 4..設立停線按紐。
(二) 浪費的產生:
工廠布局(Layout)﹕物流動線設計﹔設備局 限﹔工作地布局﹔前后工程分離﹔
設計兼容性(Compatibility)﹕業務擴充→新 增工序或設備﹔設備或物料變換→不適合﹔ 前景不明→未作整體規划﹔
四. 搬運的浪費
(一) 浪費的定義: 流程中因兩點間距離遠﹐而造成的
搬運 走動 等浪費﹐包括人和機器.
搬運本身是一種無附加價值的動 作,若分解開來又分為:放置,堆積, 移動,整列等動作浪費.
輸送帶帶來的浪費
1.取放的浪費﹔ 2.等待的浪費﹔ 3.在制品的浪費﹔
4.空間的浪費。 如何善待輸送帶
1﹑單元制生產方式﹔ 2﹑生產線平衡法﹔ 3﹑人機工作分離﹔ 4﹑全員生產性維護(TPM)﹔ 5﹑切換的改善﹔ 6﹑嫁動率,可動率的持續提升
1.檢核表法 : 照表操課 2. 層別法 : 抽絲剝繭 3. 柏拉圖法 : 擒賊擒王 4. 特性要因圖法 : 一網打盡 5. 直方圖法 : 明察秋毫 6. 管制圖法 : 瞭若指掌 7. 散佈圖法 : 關係分明
二. 制造過多的浪費
(一) 浪費的定義:前工程之投入量﹐超過后
工程單位時間內之需求量﹐而造成的浪費.
﹑零部件﹑半成品﹑成品等在庫﹐在庫發生
的原因有﹕ 存貨管理名言:
❖空閑時多制造的部分﹔ 庫存是必要的惡物
❖設備狀態良好時連續生產﹔
❖認為提前生產是高效率的表現﹔占用
❖認為有大量庫存才保險﹔
大量
资金
缓解 供需 矛盾
•库存三不 •不大批量生产
•不大批量搬运
•不大批量采购
(二)“在庫”作為資產本來是有價值的﹐ 但過多的話則會面臨以下風險﹕
(二) 浪費的產生:
工廠布局(Layout)﹕物流動線設計﹔設備局 限﹔工作地布局﹔前后工程分離﹔
設計兼容性(Compatibility)﹕業務擴充→新 增工序或設備﹔設備或物料變換→不適合﹔ 前景不明→未作整體規划﹔
四. 搬運的浪費
(一) 浪費的定義: 流程中因兩點間距離遠﹐而造成的
搬運 走動 等浪費﹐包括人和機器.
搬運本身是一種無附加價值的動 作,若分解開來又分為:放置,堆積, 移動,整列等動作浪費.
輸送帶帶來的浪費
1.取放的浪費﹔ 2.等待的浪費﹔ 3.在制品的浪費﹔
4.空間的浪費。 如何善待輸送帶
1﹑單元制生產方式﹔ 2﹑生產線平衡法﹔ 3﹑人機工作分離﹔ 4﹑全員生產性維護(TPM)﹔ 5﹑切換的改善﹔ 6﹑嫁動率,可動率的持續提升
1.檢核表法 : 照表操課 2. 層別法 : 抽絲剝繭 3. 柏拉圖法 : 擒賊擒王 4. 特性要因圖法 : 一網打盡 5. 直方圖法 : 明察秋毫 6. 管制圖法 : 瞭若指掌 7. 散佈圖法 : 關係分明
二. 制造過多的浪費
(一) 浪費的定義:前工程之投入量﹐超過后
工程單位時間內之需求量﹐而造成的浪費.
﹑零部件﹑半成品﹑成品等在庫﹐在庫發生
的原因有﹕ 存貨管理名言:
❖空閑時多制造的部分﹔ 庫存是必要的惡物
❖設備狀態良好時連續生產﹔
❖認為提前生產是高效率的表現﹔占用
❖認為有大量庫存才保險﹔
大量
资金
缓解 供需 矛盾
•库存三不 •不大批量生产
•不大批量搬运
•不大批量采购
(二)“在庫”作為資產本來是有價值的﹐ 但過多的話則會面臨以下風險﹕
八大浪费及八大改善教材.ppt

□ 动作范围的极小化
“手能够得着的配置及立式作业化" 按照作业方法,把部品或工具配置到作业者不需要移动身体就能作业的位置
17
3. 动作浪费
2.动作经济原则
动 作 分 析 的 原 则
18
原则 1. 取消不必要的动作 原则 2. 减少视觉的移动 原则 3. 组合两个以上的动作 原则 4. 材料和工具放在前方最近的位置 原则 5. 材料和工具的位置要与作业顺序相匹配 原则 6. 取出、放回要方便 原则 7. 利用没有成本的动力或重力 原则 8. 两手可以同时使用 原则 9. 避免Z形动作或急剧的方向转换 原则 10. 动作在最短距离内进行 原则 11. 器具/工具统合 原则 12. 要可以先入先出
20
3. 动作浪费
原则5. 材料和工具的位置要与作业顺序相匹配
改善前 不恰当的作业台的配置
改善后 恰当的作业台的配置
原则6. 取出、放回要方便
改善前 拿起放在作业台上的钳子 需要转换手势
改善后 把钳子放在漏斗型器具内使用
21
3. 动作浪费
原则 7. 利用无成本的动力或重力
改善前
作业完了后,伸手放到距离60㎝的 部品箱里
一般来说作业者
有一半的时间是 “无效的” !
6) 步行多
12) 重复/不必要的动作
任何不产生价值的人员和设备的动作
14
精益生产专家
3. 动作浪费
3.3 如何消除动作浪费
如何消除 ??? 1. 动作分析 2. 动作经济原则
15
3. 动作浪费
1.动作分析
动作研究:动作级别定义
16
3. 动作浪费
1. 动作分析
2
二、工厂常见的八大浪费
“手能够得着的配置及立式作业化" 按照作业方法,把部品或工具配置到作业者不需要移动身体就能作业的位置
17
3. 动作浪费
2.动作经济原则
动 作 分 析 的 原 则
18
原则 1. 取消不必要的动作 原则 2. 减少视觉的移动 原则 3. 组合两个以上的动作 原则 4. 材料和工具放在前方最近的位置 原则 5. 材料和工具的位置要与作业顺序相匹配 原则 6. 取出、放回要方便 原则 7. 利用没有成本的动力或重力 原则 8. 两手可以同时使用 原则 9. 避免Z形动作或急剧的方向转换 原则 10. 动作在最短距离内进行 原则 11. 器具/工具统合 原则 12. 要可以先入先出
20
3. 动作浪费
原则5. 材料和工具的位置要与作业顺序相匹配
改善前 不恰当的作业台的配置
改善后 恰当的作业台的配置
原则6. 取出、放回要方便
改善前 拿起放在作业台上的钳子 需要转换手势
改善后 把钳子放在漏斗型器具内使用
21
3. 动作浪费
原则 7. 利用无成本的动力或重力
改善前
作业完了后,伸手放到距离60㎝的 部品箱里
一般来说作业者
有一半的时间是 “无效的” !
6) 步行多
12) 重复/不必要的动作
任何不产生价值的人员和设备的动作
14
精益生产专家
3. 动作浪费
3.3 如何消除动作浪费
如何消除 ??? 1. 动作分析 2. 动作经济原则
15
3. 动作浪费
1.动作分析
动作研究:动作级别定义
16
3. 动作浪费
1. 动作分析
2
二、工厂常见的八大浪费
八大浪费培训PPT课件
以成本
降低成
-6/70-
成本节减思想:降低成本
需求 < 供给
通过降低成本来降低销售价格
销售价格
利润 成本
规范 标准 专业 高效
-7/70-
竞争力提升 品质提升 制造成本降低 企业形象提升
改善 消除浪费 标准化
设 改善等
心、
动作改善、作业流程改善、物流改善、 备模夹治具改善、品质改善、管理
八大浪费、三无工程(无责任、无关
-29/70-
3.搬运的浪费
整个冲压过程包括取产品、冲压、 放置产品,其中取产品与摆放产 品占了50%的作业时间,并且这 些动作并不产生价值。
冲压完的产品要先放到周转车 上,再搬运到点焊工位点焊, 这些搬运过程都是浪费,为什 么不把冲压与焊接设备放在一 起呢?
规范 标准 专业 高效
-30/70-
3.搬运的浪费
规范 标准 专业 高效
-35/70-
八大浪费
1.制造过多的浪费 2.等待的浪费 3.搬运的浪费 4.加工的浪费 5.库存的浪费 6.动作的浪费 7.不良的浪费 8.管理的浪费
规范 标准 专业 高效
-36/70-
SUCCESS
THANK YOU
2019/8/1
规范 标准 专业 高效
-37/70-
5.库存的浪费
制
移动
40%
造
所谓的附加值指的是通过加工或组装提 高产品的价值,其余的都是非附加值,就 浪费。
活
附加价值动作
15%
TOYOTA汽车公司
动
非效率的 ‘工作’ 40%
11 /72
定义 95%以上是浪费
规范 标准 专业 高效
-11/70-
降低成
-6/70-
成本节减思想:降低成本
需求 < 供给
通过降低成本来降低销售价格
销售价格
利润 成本
规范 标准 专业 高效
-7/70-
竞争力提升 品质提升 制造成本降低 企业形象提升
改善 消除浪费 标准化
设 改善等
心、
动作改善、作业流程改善、物流改善、 备模夹治具改善、品质改善、管理
八大浪费、三无工程(无责任、无关
-29/70-
3.搬运的浪费
整个冲压过程包括取产品、冲压、 放置产品,其中取产品与摆放产 品占了50%的作业时间,并且这 些动作并不产生价值。
冲压完的产品要先放到周转车 上,再搬运到点焊工位点焊, 这些搬运过程都是浪费,为什 么不把冲压与焊接设备放在一 起呢?
规范 标准 专业 高效
-30/70-
3.搬运的浪费
规范 标准 专业 高效
-35/70-
八大浪费
1.制造过多的浪费 2.等待的浪费 3.搬运的浪费 4.加工的浪费 5.库存的浪费 6.动作的浪费 7.不良的浪费 8.管理的浪费
规范 标准 专业 高效
-36/70-
SUCCESS
THANK YOU
2019/8/1
规范 标准 专业 高效
-37/70-
5.库存的浪费
制
移动
40%
造
所谓的附加值指的是通过加工或组装提 高产品的价值,其余的都是非附加值,就 浪费。
活
附加价值动作
15%
TOYOTA汽车公司
动
非效率的 ‘工作’ 40%
11 /72
定义 95%以上是浪费
规范 标准 专业 高效
-11/70-
八大浪费讲义教材
1.成型件:不良报废消除 2.消除因成型件不良拆卸卡环/电源按键/铭牌等人力成本 3.卡环/电源按键/铭牌报废率为0
21
© by ETC of Changhong 2010-02
二.制造过多(过早)浪费
12.5% 14297
10
of Changhong 2010-02
2012
2013
365000
385000
243000
255000
2.1%
4.9%
70070
73437
8.3%
4.8%
20440
22715 11.1% Copyright © 34618 by ETC
17.5%
32446
浪费的本质
从人均能源看浪费问题:
课程大纲
1. 前言 2. 浪费的本质
3. 八大浪费 4. 案例分享
5. 结束语
3
Copyright © by ETC of Changhong 2010-02
前言
工厂减少“八大浪费”活动的目的
?
改善现场、减少库存、降低成本、提升效率、减少产品制造过程周期时间等等
制造管理革新
4
Copyright © by ETC of Changhong 2010-02
1995
1996 1997
131176
135192 135909
97857
99366 97039
6.3%
1.5% -2.3%
22956
25281 27725
7.5%
10.1% 9.7%
2361
2433 2446
1.3%
3.1% 0.5%
8002
8112 8698
IE之八大浪费培训资料
库存水平
不良品
故障
点点停 缺勤
能力不 平衡
调整时 间长
计划有误
品质不一致
3.2 库存的浪费
3.改善在库过多的方法
1)分类管理法---根据生产计划及交货期分批购入原材料﹐保 证最低库存量﹔通用性生产物料考虑实时生产或实时送货 的方式﹐降低库存。
2)JIT库存管理
3)控制在库金额。
4)定期盘点。(日,周,月盘制度)
四. 如何发现浪费
1.发现浪费的重点: 1)三现原则:到现场 、看现物、掌握现状。
任何企图在座在办公室里解决现场问题都是徒劳的 。
四. 如何发现浪费
2) 5 Why: 对每个浪费的动作反复问为什么(Why)? 找出根本原因。
3)根据三现和5-Why改善展开方法 Step-1 根据三现原则
一现:到现场 二现:看现物(问题) 三现:掌握现状 Step-2 对作业反复提出为什么(why) 找出问题发生的根本原因。 Step-3 怎么改善?(How) 不让问题重复发生,找出能改善的好方法。 Step-4 改善(Improve) 要确认是否容易,方便,安全,稳定的进行作业。
由于这些活动潜在于工作的动作中而不易被表面化,所 以就要掌握IE知识进行分析。
五. IE如何消除浪费
现代工业工程提供了解决方法:
*工作研究(Work study) *设施设计(Facility design) *物流分析 *生产计划与控制(Production planning and control) *工作评价与人事考核 *质量控制(Quality control) *经济技术分析、成本控制 *价值工程(Value engineering) *人机工程
2. 浪费的产生:
企业八大浪费培训ppt课件(精)
企业八大浪费培训ppt 课件
汇报人: 2023-12-30
目录
• 浪费现象概述 • 生产过剩浪费 • 库存浪费 • 运输浪费 • 加工浪费 • 动作浪费 • 等待浪费 • 管理浪费
浪费现象概述
01
浪费定义与分类
浪费定义
指任何不增加产品价值却增加成 本的活动或过程。
浪费分类
生产过剩、库存、不合格品、动 作、加工、等待、搬运和运输。
提高设备利用率方法
合理安排设备使用时间
根据生产计划和实际需求,合理安排设 备使用时间,避免设备空闲和过度使用
。
采用先进的生产技术和工艺
引进先进的生产技术和工艺,提高设 备运行速度和加工精度,减少生产过
程中的浪费。
加强设备维护和保养
定期对设备进行维护和保养,确保设 备处于良好状态,提高设备运行效率 。
减少等待时间措施
优化生产计划
合理安排生产计划,避免生 产流程中的瓶颈环节,确保
生产顺畅进行。
1
提高设备可靠性
加强设备维护和保养,减少 设备故障率,提高设备运行
稳定性。
加强物料管理
优化物料采购和库存管理, 确保物料及时供应,减少等 待时间。
提高员工技能
加强员工培训,提高员工操 作技能和生产效率,减少人 为因素造成的等待时间。
过多搬运
生产过程中存在过多的搬 运环节,增加了运输成本 和时间成本。
无效运输
运输过程中存在无效或重 复的运输,如空驶、对流 运输等。
运输不当
运输方式、工具选择不当 ,导致运输效率低下或货 物损坏。
减少运输浪费措施
简化生产流程
通过优化生产布局和工艺流程,减少 不必要的搬运环节。
提高运输效率
汇报人: 2023-12-30
目录
• 浪费现象概述 • 生产过剩浪费 • 库存浪费 • 运输浪费 • 加工浪费 • 动作浪费 • 等待浪费 • 管理浪费
浪费现象概述
01
浪费定义与分类
浪费定义
指任何不增加产品价值却增加成 本的活动或过程。
浪费分类
生产过剩、库存、不合格品、动 作、加工、等待、搬运和运输。
提高设备利用率方法
合理安排设备使用时间
根据生产计划和实际需求,合理安排设 备使用时间,避免设备空闲和过度使用
。
采用先进的生产技术和工艺
引进先进的生产技术和工艺,提高设 备运行速度和加工精度,减少生产过
程中的浪费。
加强设备维护和保养
定期对设备进行维护和保养,确保设 备处于良好状态,提高设备运行效率 。
减少等待时间措施
优化生产计划
合理安排生产计划,避免生 产流程中的瓶颈环节,确保
生产顺畅进行。
1
提高设备可靠性
加强设备维护和保养,减少 设备故障率,提高设备运行
稳定性。
加强物料管理
优化物料采购和库存管理, 确保物料及时供应,减少等 待时间。
提高员工技能
加强员工培训,提高员工操 作技能和生产效率,减少人 为因素造成的等待时间。
过多搬运
生产过程中存在过多的搬 运环节,增加了运输成本 和时间成本。
无效运输
运输过程中存在无效或重 复的运输,如空驶、对流 运输等。
运输不当
运输方式、工具选择不当 ,导致运输效率低下或货 物损坏。
减少运输浪费措施
简化生产流程
通过优化生产布局和工艺流程,减少 不必要的搬运环节。
提高运输效率
- 1、下载文档前请自行甄别文档内容的完整性,平台不提供额外的编辑、内容补充、找答案等附加服务。
- 2、"仅部分预览"的文档,不可在线预览部分如存在完整性等问题,可反馈申请退款(可完整预览的文档不适用该条件!)。
- 3、如文档侵犯您的权益,请联系客服反馈,我们会尽快为您处理(人工客服工作时间:9:00-18:30)。
路漫漫其修远兮,
八大浪费---过量生产
5. 例子:
1.
当前状态:10名操作员
100件
但是我只要100件
2.
当前状态:10名操作员
3.
当前状态:8名操作员
120件
顾客
100件
路漫漫其修远兮,
八大浪费---过量生产
在所有的Muda中,过量生产是最严重的Muda,它 带给人们一个安心的错觉,掩盖了各种问题,以及隐藏 了由于等待所带来的浪费,失去了持续改善的机会. 要把过量生产当做犯罪看待. 过量生产起源于下列无效的观念及政策:
指凡是不能直接创造出价值的一切活动,均视为浪费 强调。
对JIT来讲,凡是超出增加产品价值所绝对必须的 最少量的物料,设备,人力,场地,时间的部分都是浪费 这里有两层意思:
不增加价值的活动,是浪费 增加价值,但是所用的资源
超过了“绝对最少”的界 限,也是浪费
不创造商品价值 创造商品价值
路漫漫其修远兮,
Modified by Name here
Change of summary Initial Release
路漫漫其修远兮,
大纲
➢ 浪费的定义 ➢ 八大浪费总括 ➢ 各个浪费:定义,产生原因,危害,解决方法 ➢ 消除八大浪费的七个手法 ➢ 总结 ➢ 现场互动
路漫漫其修远兮,
浪费的定义
浪费的定义:
3.产生的危害
过量的原材料 额外的库存 过度占用空间,设备,人力 搬运,堆积的浪费,管理工时的浪费 产品的贬值
路漫漫其的消除
避免过量计划: 计算机信息集成控制;准确掌控不良率;制定宽放标准和
计划校正机制;缩短交付周期(CT,批量);
避免前工序过量投入: 生产线平衡; 一个流作业; 作业要求;
供应﹑管理方面考虑,采用最为合适的形状.
路漫漫其修远兮,
八大浪费---搬运浪费
搬运手段合理化
1. 搬运作业遵循原则: 机械化原则;自动化原则;标准化原则;均衡原则;及时原则; 直线原则;安全第一原则.
2. 搬运方法: 传送带; 定量搬运和定时搬运; 搬运工具的合理化.
3. 现场布置
路漫漫其修远兮,
因此应尽量减少或消除搬运。
路漫漫其修远兮,
八大浪费---搬运浪费
3.改善方向: 合理化布局
合理化布局设计的要点: 1. 辅助生产线的终点,应尽量接近供给对象的主生产线工序; 2. 充分探讨供应各工序零部件的方法; 3. 研究空卡板﹑包装箱﹑夹具的返回方法; 4. 沿生产线设置大小适当的零部件暂放场所; 5. 不要忘记在生产线中设置检查工序和修理工序; 6. 确保设备的保养与修理所需空间; 7. 生产线的形状受到产品和场地的制约,可从安装﹑零部件
Verified
: Name here
Approver
: Name here
Document No. : Corp-HR-T&D-TM-PXXX
Version/Status : 1.0/Approved
Location
: E-office/DMS
Change History
Version 1.0
Date 20th Mar 2010
八大浪费培训教材
路漫漫其修远兮,
2020年4月4日星期六
基本原则
▪ 准时参加 ▪ 手机静音或关机 ▪ 仔细聆听–他人说话时,尊重他人 ▪ 全心全力参与 ▪ 共同目标–有一个更深刻的理解 ▪ 培训结束时参加测试
路漫漫其修远兮,
Document Properties
Creator
:
Function
:
路漫漫其修远兮,
八大浪费---过量生产
1. 没有考虑到下一个制程或下一条生产线的正确生产速度, 而只尽其所能,在本制程生产过多的产品.
2. 让作业员有成长伸缩的充分空间. 3. 让每一制程或生产线有提高自己的生产力的利益. 4. 因为有不合格品而想提高直通率(OAY: 直通率指从物料加
工到组装成品一次性成功合格品的比率). 5. 因为有多余的产能,所以允许机器生产多于所需之量. 6. 因为引进了昂贵的机器设备—为折旧费的分摊,而提高稼
运输
原 料 运输 加 工
原料
存放
装配
检包 验装
库存
成品
增值活动 非增值活动
路漫漫其修远兮,
浪费定义---八大浪费
搬运
过量生产
库存
过度加工
不良修正
路漫漫其修远兮,
动作
等待
管理浪费
八大浪费---搬运浪费
1.定义:
流程中因两点间距离远,而造成的搬运,走动 括人和机器.
等浪费,包
2.浪费产生的原因:
取放产生的浪费 空间产生的浪费 工厂布局不合理产生的浪费 线路设计不合理产生的浪费 搬运设备不合理产生的浪费 搬运作业是不产生任何附加价值的活动,
路漫漫其修远兮,
八大浪费---库存浪费
4.改善库存多的方法:
分类管理法----根据生产计划及交货期分批 购入原材料,保证最低库存量;通用性生产 物料考虑即时生产或即时送货的方式,降低 库存.
JIT库存管理----广告牌管理 控制在库金额 定期盘点 库存警示方法
路漫漫其修远兮,
八大浪费---过度加工
浪费的定义
浪费的3种形态: 1.勉 强:超过能力界限的超负荷状态;(会导致设
备故障,品质低下,人员不安全) 2.不充分利用:有能力,但未给予充足的工作量的未 饱和状态;(人员工作量不饱和,设备稼动率低) 3.不均衡:有时超负荷,有时又不饱和的状态;
路漫漫其修远兮,
浪费的定义
一般工厂增值与非增值活动的划分:
八大浪费---过量生产
1.定义:
生产了过多的,超出客户或下游工序需求的数量
哈, 我把所 有的订单都 做完了
我们还得弄一个大点 的仓库!
我们马上就完工 了
路漫漫其修远兮,
结果呢?
八大浪费---过量生产
2.原因可能是…
过量计划:信息不准;计划错误;计划失当;信息传递不 畅;制程反应速度慢 前工序过量投入:工时不平衡;广告牌信息错误;不是 一个流;工作纪律差
动率,生产过多的产品. ……
路漫漫其修远兮,
八大浪费---库存浪费
1.定义:
制造业的工厂, 原材料﹑零部件﹑半成品﹑成品等 超过必须要的数量
2.浪费发生的原因:
原材料过量采购 空闲时多制造的产品 提前制造的产品 半成品,在制品过多
路漫漫其修远兮,
八大浪费---库存浪费
3.产生的危害:
占用了大量的资金 增加了管理费用 面临过时的市场风险 有质量变更的风险
八大浪费---过量生产
5. 例子:
1.
当前状态:10名操作员
100件
但是我只要100件
2.
当前状态:10名操作员
3.
当前状态:8名操作员
120件
顾客
100件
路漫漫其修远兮,
八大浪费---过量生产
在所有的Muda中,过量生产是最严重的Muda,它 带给人们一个安心的错觉,掩盖了各种问题,以及隐藏 了由于等待所带来的浪费,失去了持续改善的机会. 要把过量生产当做犯罪看待. 过量生产起源于下列无效的观念及政策:
指凡是不能直接创造出价值的一切活动,均视为浪费 强调。
对JIT来讲,凡是超出增加产品价值所绝对必须的 最少量的物料,设备,人力,场地,时间的部分都是浪费 这里有两层意思:
不增加价值的活动,是浪费 增加价值,但是所用的资源
超过了“绝对最少”的界 限,也是浪费
不创造商品价值 创造商品价值
路漫漫其修远兮,
Modified by Name here
Change of summary Initial Release
路漫漫其修远兮,
大纲
➢ 浪费的定义 ➢ 八大浪费总括 ➢ 各个浪费:定义,产生原因,危害,解决方法 ➢ 消除八大浪费的七个手法 ➢ 总结 ➢ 现场互动
路漫漫其修远兮,
浪费的定义
浪费的定义:
3.产生的危害
过量的原材料 额外的库存 过度占用空间,设备,人力 搬运,堆积的浪费,管理工时的浪费 产品的贬值
路漫漫其的消除
避免过量计划: 计算机信息集成控制;准确掌控不良率;制定宽放标准和
计划校正机制;缩短交付周期(CT,批量);
避免前工序过量投入: 生产线平衡; 一个流作业; 作业要求;
供应﹑管理方面考虑,采用最为合适的形状.
路漫漫其修远兮,
八大浪费---搬运浪费
搬运手段合理化
1. 搬运作业遵循原则: 机械化原则;自动化原则;标准化原则;均衡原则;及时原则; 直线原则;安全第一原则.
2. 搬运方法: 传送带; 定量搬运和定时搬运; 搬运工具的合理化.
3. 现场布置
路漫漫其修远兮,
因此应尽量减少或消除搬运。
路漫漫其修远兮,
八大浪费---搬运浪费
3.改善方向: 合理化布局
合理化布局设计的要点: 1. 辅助生产线的终点,应尽量接近供给对象的主生产线工序; 2. 充分探讨供应各工序零部件的方法; 3. 研究空卡板﹑包装箱﹑夹具的返回方法; 4. 沿生产线设置大小适当的零部件暂放场所; 5. 不要忘记在生产线中设置检查工序和修理工序; 6. 确保设备的保养与修理所需空间; 7. 生产线的形状受到产品和场地的制约,可从安装﹑零部件
Verified
: Name here
Approver
: Name here
Document No. : Corp-HR-T&D-TM-PXXX
Version/Status : 1.0/Approved
Location
: E-office/DMS
Change History
Version 1.0
Date 20th Mar 2010
八大浪费培训教材
路漫漫其修远兮,
2020年4月4日星期六
基本原则
▪ 准时参加 ▪ 手机静音或关机 ▪ 仔细聆听–他人说话时,尊重他人 ▪ 全心全力参与 ▪ 共同目标–有一个更深刻的理解 ▪ 培训结束时参加测试
路漫漫其修远兮,
Document Properties
Creator
:
Function
:
路漫漫其修远兮,
八大浪费---过量生产
1. 没有考虑到下一个制程或下一条生产线的正确生产速度, 而只尽其所能,在本制程生产过多的产品.
2. 让作业员有成长伸缩的充分空间. 3. 让每一制程或生产线有提高自己的生产力的利益. 4. 因为有不合格品而想提高直通率(OAY: 直通率指从物料加
工到组装成品一次性成功合格品的比率). 5. 因为有多余的产能,所以允许机器生产多于所需之量. 6. 因为引进了昂贵的机器设备—为折旧费的分摊,而提高稼
运输
原 料 运输 加 工
原料
存放
装配
检包 验装
库存
成品
增值活动 非增值活动
路漫漫其修远兮,
浪费定义---八大浪费
搬运
过量生产
库存
过度加工
不良修正
路漫漫其修远兮,
动作
等待
管理浪费
八大浪费---搬运浪费
1.定义:
流程中因两点间距离远,而造成的搬运,走动 括人和机器.
等浪费,包
2.浪费产生的原因:
取放产生的浪费 空间产生的浪费 工厂布局不合理产生的浪费 线路设计不合理产生的浪费 搬运设备不合理产生的浪费 搬运作业是不产生任何附加价值的活动,
路漫漫其修远兮,
八大浪费---库存浪费
4.改善库存多的方法:
分类管理法----根据生产计划及交货期分批 购入原材料,保证最低库存量;通用性生产 物料考虑即时生产或即时送货的方式,降低 库存.
JIT库存管理----广告牌管理 控制在库金额 定期盘点 库存警示方法
路漫漫其修远兮,
八大浪费---过度加工
浪费的定义
浪费的3种形态: 1.勉 强:超过能力界限的超负荷状态;(会导致设
备故障,品质低下,人员不安全) 2.不充分利用:有能力,但未给予充足的工作量的未 饱和状态;(人员工作量不饱和,设备稼动率低) 3.不均衡:有时超负荷,有时又不饱和的状态;
路漫漫其修远兮,
浪费的定义
一般工厂增值与非增值活动的划分:
八大浪费---过量生产
1.定义:
生产了过多的,超出客户或下游工序需求的数量
哈, 我把所 有的订单都 做完了
我们还得弄一个大点 的仓库!
我们马上就完工 了
路漫漫其修远兮,
结果呢?
八大浪费---过量生产
2.原因可能是…
过量计划:信息不准;计划错误;计划失当;信息传递不 畅;制程反应速度慢 前工序过量投入:工时不平衡;广告牌信息错误;不是 一个流;工作纪律差
动率,生产过多的产品. ……
路漫漫其修远兮,
八大浪费---库存浪费
1.定义:
制造业的工厂, 原材料﹑零部件﹑半成品﹑成品等 超过必须要的数量
2.浪费发生的原因:
原材料过量采购 空闲时多制造的产品 提前制造的产品 半成品,在制品过多
路漫漫其修远兮,
八大浪费---库存浪费
3.产生的危害:
占用了大量的资金 增加了管理费用 面临过时的市场风险 有质量变更的风险