第六章机械可靠性设计方法
机械可靠性设计分析方法

因此如何采用一些较好的近似方法,能比较方便地求得满足工程
精度要求的零件(línɡ jiàn)可靠度的近似解,一直是人们探讨的一
应个力问和题强。度两个概率密度函
数的交叉区,即干涉区阴影
f(s) g(r)
面积的大小(dàxiǎo),反映
g(r) f(s)
了零件或结构可靠度的高低。
该面积越小,可靠度越高,反
解:
面积(miàn jī)A=πr2,则f’(r)=2πr,
f”(r)E=(2Aπ) , 可A 得f
(r
)
1 2
f
(r )D(r)
r2
1 2
(2
即有 1 p f (1 a2 )(1 a1) 1 a1 a2 a1a2
p f a1 a2 a1a2
p f a1a2
a1a2 p f a1 a2 a1a2 1 a1a2 ps 1 a1 a2 a1a2
可见,失效概率数值上不 等于干涉(gānshè)区的阴影 面积。
由于可靠度R(t)总是小于(1-a1a2),所以(1-a1a2)可作为 零件可靠度的上限,成为衡量可靠性的一种(yī zhǒnɡ)指标, 称为零件的非失效保证度。
第十四页,共51页。
例4-2 今有一受拉伸载荷的杆件,已知载荷F(μF, σF )= F(80000, 1200)N, 拉杆直径(zhíjìng)d(μd, σd )=d(40, 0.8)mm,拉杆长 l(μl, σl ) =l(6000, 60)mm,材料的弹性 模量 E(μE, σE) =E(21×104, 3150) Mpa,求在弹性变形 范围内拉杆的伸长δ。
Z
E( X Y
)
E(X ) E(Y )
X Y
Z
2 X
第六章系统可靠性设计
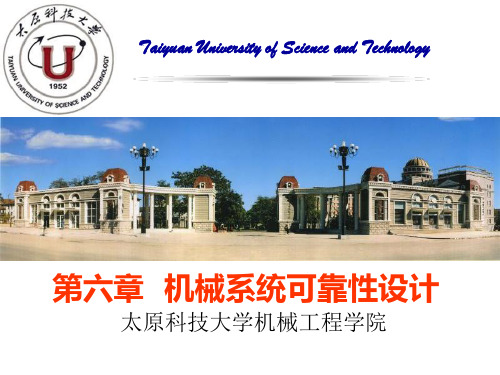
串联系统可靠度计算应用实例:
某带式输送机输送带的接头共有54个, 已知各接头的强度服从指数分布,其失效 率如表所示,试计算该输送带的平均寿命 和工作到1000h的可靠度。
λ ×
接头数
3
5
8
10
12
16
λ×
/h 10 4
0.2
0.15
0.35
0.21
0.18
0.1
解答见书上P65
2)并联系统可靠性模型
s Rdt
0
2
1 1.5 1.5 2
3)混联系统可靠性模型
• 混联系统可靠性模型——是由串联和并联 混合组成的模型。下图为混联系统的可靠 性框图,其数学模型可运用串联和并联两 种基本模型将系统中一些串联及并联部分 简化为等效单元。例如图中ຫໍສະໝຸດ a可按图中b,c,d的次序依次简化.
• 并联系统中系统的可靠度Rs大于任一单元 的可靠度; • 组成系统的单元数越多,系统的可靠度越 高,但系统的造价也越高;
• 机械系统采用并联时,尺寸、重量、价 格都随并联数n成倍地增加。在动力装置、 安全装置、制动装置采用并联时,常取 n=2~3。
若单元可靠度服从指数分布:
Ri e
i t
系统可靠度:
RS (t ) 3R 2 2 R 3 3e 2t 2e 3t
平均无故障工作时间
表决系统可靠度计算实例:
有一架装有3台发动机的飞机,它至少需要 2台发动机正常才能飞行,设飞机发动机的平 均无故障工作时间MTBF=2000h,试估计工作 时间为10h和100h的飞机可靠度。 解:n=3,k=2
系统可靠性设计方法:归纳为两种类型 可靠性预测——按照已知零部件或各单 元的可靠性数据,计算系统的可靠性指标。 可靠性分配——按照已给定的系统可靠 性指标,对组成系统的单元进行可靠性分 配。并在设计方案中比较、优选。
机械设计中的可靠性设计与分析方法
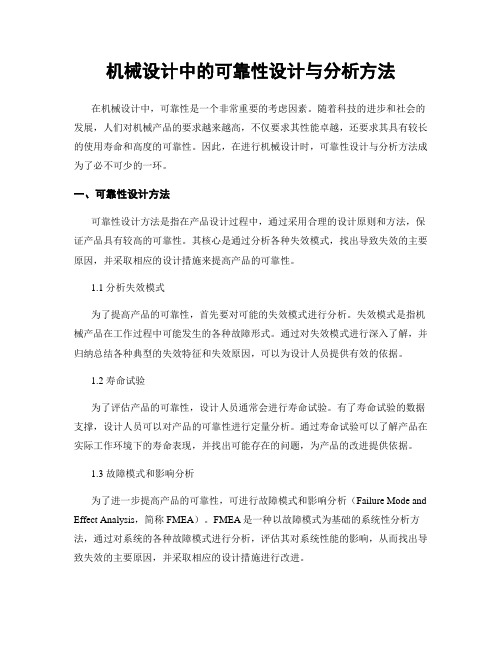
机械设计中的可靠性设计与分析方法在机械设计中,可靠性是一个非常重要的考虑因素。
随着科技的进步和社会的发展,人们对机械产品的要求越来越高,不仅要求其性能卓越,还要求其具有较长的使用寿命和高度的可靠性。
因此,在进行机械设计时,可靠性设计与分析方法成为了必不可少的一环。
一、可靠性设计方法可靠性设计方法是指在产品设计过程中,通过采用合理的设计原则和方法,保证产品具有较高的可靠性。
其核心是通过分析各种失效模式,找出导致失效的主要原因,并采取相应的设计措施来提高产品的可靠性。
1.1 分析失效模式为了提高产品的可靠性,首先要对可能的失效模式进行分析。
失效模式是指机械产品在工作过程中可能发生的各种故障形式。
通过对失效模式进行深入了解,并归纳总结各种典型的失效特征和失效原因,可以为设计人员提供有效的依据。
1.2 寿命试验为了评估产品的可靠性,设计人员通常会进行寿命试验。
有了寿命试验的数据支撑,设计人员可以对产品的可靠性进行定量分析。
通过寿命试验可以了解产品在实际工作环境下的寿命表现,并找出可能存在的问题,为产品的改进提供依据。
1.3 故障模式和影响分析为了进一步提高产品的可靠性,可进行故障模式和影响分析(Failure Mode and Effect Analysis,简称FMEA)。
FMEA是一种以故障模式为基础的系统性分析方法,通过对系统的各种故障模式进行分析,评估其对系统性能的影响,从而找出导致失效的主要原因,并采取相应的设计措施进行改进。
二、可靠性分析方法在机械设计中,可靠性分析方法主要是为了评估设计方案的可靠性,并选择出最佳的设计方案。
2.1 可靠性数学模型可靠性数学模型是一种通过数学方法对产品可靠性进行量化评估的工具。
通过建立合适的可靠性数学模型,可以对产品的失效概率、失效密度、可靠度等进行定量分析,为设计人员提供科学的依据。
2.2 误差拟合法误差拟合法是一种常用的可靠性分析方法。
它通过将实测数据与某一分布函数进行比较,从而找出最佳的分布函数,并利用该分布函数进行概率推断。
第六章-机械可靠性设计原理

S
同样分析方法:
按应力始终小于强度这一条件计算。干涉区内任取
一点δ1,则:
P[(1
d
2
)
(1
d
2
)]
g(1)d
P(S 1)
1 f (S )dS
R P(S ) g( )[ f (S)dS]d
■理论要点:
可靠性设计
• 应力:导致失效的任何因素; 强度:阻止失效发生的任何因素。
• 应力f(s),强度g(δ), 量纲相同,可放在同一坐标系中。
解: 当零件强度标准差为81MPa时
z S 850 380 470 5.1512
2
2 S
422 812 91.2414
R 1(z) 1(5.1512) (5.1512) 0.9999999
当零件强度标准差为120MPa时
可靠性设计
z S 850 380 470 3.6968
2
1
z2
e 2 dz
2
例6-1 已知某零件的工作应力及材料强度均为正态分
布,且应力的均值μS=380MPa,标准差σS=42MPa,材料 强度的均值为850MPa,标准差为81MPa。
可靠性设计
试确定零件的可靠度。另一批零件由于热处理不佳及 环境温度的较大变化,使零件强度的标准差增大至 120MPa。问其可靠度如何?
R
exp
1 2
2s
2 s 2
5
指数
es
正态
N , 2
R 1 exp
1 2
2 s
s2 2
6
指数
es
,
R
1
s
可靠性设计
第三节 机械静强度的可靠性设计
机械可靠性设计6

3.修正名义强度 修正名义强度 考虑尺寸系数、 表面质量系数、 考虑尺寸系数 、 表面质量系数 、 应力集中 系数等对强度的影响。 系数等对强度的影响。 4.确定强度公式中每一修正系数的分布; 确定强度公式中每一修正系数的分布; 确定强度公式中每一修正系数的分布 5.确定强度分布 确定强度分布 如代数法、矩法、蒙特卡罗法。 如代数法、矩法、蒙特卡罗法。
选定可靠度R=0.999 解:⑴ 选定可靠度 ⑵ 计算零件发生强度破坏的概率 F=1-R=1-0.999=0.001 查正态函数表, ⑶ 由F查正态函数表,Z=-3.09,则ZR=3.09 查正态函数表 , ⑷ 强度分布参数
r − N ( 667 , 25 . 3
2
)
⑸ 列出应力表达式
P s= A uA = ,
ZR = ur − us
σ r2 + σ s2
求截面尺寸。 求截面尺寸。
§6.3.2受拉零件的静强度可靠性 6.3.2受拉零件的静强度可靠性 设计
例:要设计一园柱拉杆,所承受的拉力: 要设计一园柱拉杆,所承受的拉力: P ~ N (u p ,σ 2 ) = N (4000012002 )N , p 强度为: 拉杆材料 45 # 钢,强度为: r ~ N (u r , σ r2 ) = N (667,25.32 )mpa 园直径的公差 ± ∆ d = ± 0 .03 u d ,求拉杆的直 径 。
§6.2.2 强度分布参数的近似计算
1.材料的静强度指标 材料的静强度指标 金属材料的抗拉强度和屈服极限能近似或 较好地符合正态分布。 较好地符合正态分布。 2.材料的变异系数 材料的变异系数 金属材料拉伸强度极限:变异系数 金属材料拉伸强度极限:变异系数0.05~0.1 ~ 常用0.05 常用 金属材料屈服极限:变异系数 金属材料屈服极限:变异系数0.05~0.1 ~ 用0.07 常
第六章 机械可靠性设计方法
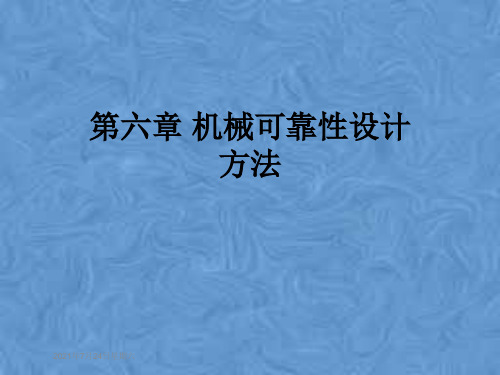
该零件的牢靠度:
R(t ) N R (t ) N
该零件的缺点〔失效〕概率: Q(t ) NQ (t ) N
R(t ) 1 Q(t )
零件寿命-缺点个数散布 直方图
1、缺点散布函数Q〔t〕:该直 方图反映了某类零件在各个寿命 距离时间内缺点发作的牢靠性大 小,即缺点概率的大小。
2、缺点散布函数f〔t〕:曲线f〔t〕反映了缺点概率的频谱, 在牢靠性里称为缺点〔失效〕概率密度函数。
从20世纪70年代起,西方工业兴旺国度片面展开牢靠 性工程实际和运用,牢靠性技术变得越来越重要
从航空、航天、尖端武器和电子等行业,逐渐推行运 用到各个行业
核能、机械、电气、冶金、化工、铁道、船舶、电站 、修建、水利、通讯、医药等
从宇宙飞船到日用产品片面普及
汽车、洗衣机、冰箱、复印机等
NASA将牢靠性工程技术列为登月成功的三大技术成 就之一
工 程 机 械 产 质 量 量 体 系
二、牢靠性出现的缘由
传统的机械零件设计是以计算平安系数为主要内容的,即 零件的平安系数〔n〕=零件的强度〔F〕/零件的应力〔S〕, 且强度及压力均为单值来停止计算,但理想并非如此。
虽然有较高的平安系数,但由于资料强度与应力散布并非 单值的,因此,当处于某种状况时,应力S>资料强度F,这样 零件就能够发作失效。
R(t) 1 Q(t)
R(t ) t f (t )dt
t
Q(t ) 0 f (t )dt
(t ) f (t )
R(t )
f (t) dR(t) dt
R(t) exp( t (t)dt) e0t (t)dt 0
(t )dt
dR(t ) R(t )
从1986年起,机械部曾经发布了六批限期考核机电产 品牢靠性目的的清单,前后共有879种产品曾经停止牢 靠性目的的考核
机械可靠性设计
机械可靠性设计1. 引言机械可靠性设计是在机械工程中至关重要的一个方面。
在设计机械系统时,通过考虑各种可能的故障和失效情况,以及如何预防和减轻这些故障和失效的影响,可以提高机械系统的可靠性和稳定性。
本文将探讨机械可靠性设计的基本原理和方法,并提供一些建议和指导。
2. 机械可靠性概述机械可靠性是指在特定的工作条件下,机械系统能够正常运行的能力。
机械可靠性设计的目标是使机械系统具有较高的可靠性,即在工作中不发生故障或失效的概率较小。
机械可靠性设计通常涉及以下几个方面:•设计阶段的可靠性分析和评估:在设计过程中,通过应用各种可靠性工具和技术,分析和评估机械系统的可靠性。
•可靠性指标的确定:根据系统的工作条件和要求,确定合适的可靠性指标,如失效率、可靠度、平均无故障时间等。
•故障预防和控制:通过合适的设计措施和工程标准,预防和控制机械系统的故障和失效。
•故障排除和修复:在机械系统故障发生时,及时排除故障并进行修复,以最小化系统的停机时间和生产损失。
3. 机械可靠性设计的基本原则在进行机械可靠性设计时,需要遵循以下几个基本原则:3.1 设计的可靠性优先在机械系统的设计过程中,可靠性应该是首要考虑的因素。
在选择和确定各个零部件、结构和材料时,应优先考虑其可靠性和稳定性。
3.2 故障模式和影响分析在设计阶段,应对机械系统进行故障模式和影响分析,了解可能的故障模式和失效的影响,以便采取相应的措施进行预防和修复。
3.3 容错和冗余设计在机械系统设计中,应采用容错和冗余设计,以提高系统的可靠性。
容错设计是指通过设计和选择合适的零部件和系统结构,使系统在部分失效的情况下仍能继续工作;冗余设计是指在系统中增加冗余部件或冗余系统,以提供备用和替代功能。
3.4 可维护性设计在机械系统设计中,应考虑系统的可维护性。
合理的结构设计、易于维修和更换的零部件、合理的维护策略等,可以减少维修时间和维修成本,提高系统的可靠性。
4. 机械可靠性设计的方法和工具4.1 可靠性工具在机械可靠性设计过程中,可以使用各种可靠性工具和技术进行分析和评估。
机械结构可靠性设计
机械结构可靠性设计引言机械结构的可靠性设计是保证机械产品正常运行和可靠性的重要环节。
在机械工程领域,可靠性设计的目标是减少故障和提高机械结构的寿命。
本文将介绍机械结构可靠性设计的基本原理、方法和实践经验。
机械结构可靠性分析方法机械结构可靠性分析是确定机械结构在使用寿命内是否能够满足设计要求的过程。
常用的机械结构可靠性分析方法主要有以下几种:可靠性指标分析法可靠性指标分析法是通过计算机模型和统计分析的方法确定机械结构的可靠性指标。
常用的可靠性指标有可靠度、故障率、平均无故障时间等。
该方法能够通过可靠性指标评估机械结构的可靠性,得出结构的失效概率和使用寿命。
试验法试验法通过对机械结构进行试验,观察和分析试验结果,评估机械结构的可靠性。
该方法能够直接获取机械结构的可靠性信息,但试验耗时、耗费成本较高。
可靠性设计软件的应用借助于可靠性设计软件,可以对机械结构进行可靠性分析和优化设计。
通过输入结构参数、载荷条件等信息,软件可以计算出结构的可靠性指标,并通过优化设计提出改进建议。
机械结构可靠性设计的步骤机械结构可靠性设计的步骤主要包括以下几个方面:确定需求和限制条件首先,需要明确机械结构的使用需求和限制条件。
包括设计要求、载荷条件、工作环境等方面的要求。
获取结构参数根据需求和限制条件,确定机械结构的基本参数。
包括结构的尺寸、材料、连接方式等。
进行可靠性分析根据所选的可靠性分析方法和工具,对机械结构进行可靠性分析。
可以计算出结构的可靠性指标,评估结构的可靠性。
优化设计根据可靠性分析结果,对机械结构进行优化设计。
主要包括结构的减振、增强和改进等方面的设计。
验证和测试对优化设计后的机械结构进行验证和测试,验证其是否满足设计要求和可靠性要求。
完善设计文档根据最终的设计结果,完善机械结构的设计文档,包括设计图纸、计算报告、测试报告等。
实践经验在机械结构可靠性设计的实践中,需要注意以下几个方面:•合理确定可靠性指标:根据实际需求和结构特点,合理选择可靠性指标,以便更好地评估结构的可靠性。
机械可靠性设计
可靠性设计方法论
1
可靠性要求分析
分析并明确机械系统的可靠性要求,以便在设计阶段确定合适的可靠性指标。
2
故障排除与容错设计
开发故障排除策略和容错机制,以最小化故障对系统性能的影响。
3
可靠性优化技术
使用数学建模和模拟分析,优化机械系统的设计,以实现最佳的可靠性性能。
可靠性测试技术与应用
可靠性测试方法
介绍常见的可靠性测试方法, 如可靠性试验和环境试验,以 验证机械系统的可靠性。
振动分析
故障诊断
学习如何使用振动分析技术来 检测机械系统中的故障和异常。
探讨机械系统故障诊断的方法 和工具,以及如何通过准确诊 断来采取械系统的状态监测 技术,以及如何及早预警 并采取措施以防止系统故 障。
机械可靠性设计
欢迎来到机械可靠性设计的世界!通过本次演示,我们将一起探索机械可靠 性设计的重要性以及实践应用。
机械可靠性设计介绍
学习如何通过可靠性设计提高机械系统的性能、可靠性和寿命,从而最大程 度地减少故障和维修成本。
机械系统失效模式分析
了解常见的机械故障模式,并通过失效模式分析(FMEA)来预测并减少系统故障的发生。
定期维护计划
制定有效的定期维护计划, 以确保机械系统的可靠性 和长期稳定运行。
故障分析与根本原因
通过故障分析和根本原因 分析,了解并解决机械系 统故障的根本问题,以防 止再次发生。
案例分析及实践应用
深入研究一些成功的机械可靠性设计案例,并探索如何将所学应用到实际工程项目中。
总结和展望
总结机械可靠性设计的重要性和应用,并展望未来的发展趋势和挑战。
机械设计基础中的机械设计可靠性分析如何提高设计的可靠性和稳定性
机械设计基础中的机械设计可靠性分析如何提高设计的可靠性和稳定性机械设计在各个领域中扮演着重要的角色,而机械设计的可靠性和稳定性是确保产品质量和工作效能的关键因素之一。
本文将探讨机械设计基础中的机械设计可靠性分析方法,以及如何提高设计的可靠性和稳定性。
一、机械设计可靠性分析方法在机械设计过程中,通过可靠性分析来评估设计的可靠性和稳定性是至关重要的。
下面介绍几种常用的机械设计可靠性分析方法。
1.1 故障模式与影响分析(FMEA)故障模式与影响分析(Failure Mode and Effects Analysis,简称FMEA)是一种广泛应用于机械设计中的可靠性分析方法。
它通过识别故障模式、评估故障后果、确定故障频率和严重性,为设计师提供有关如何改进设计的建议。
1.2 可靠性块图(Reliability Block Diagram,简称RBD)可靠性块图是一种通过将系统分解为不同的子系统或组件,并描述它们之间的可靠性连接来进行分析的方法。
通过使用可靠性块图,设计师可以快速评估每个子系统或组件的可靠性,并识别潜在的故障路径。
1.3 可靠性中心程序(Reliability-Centered Maintenance,简称RCM)可靠性中心程序是一种系统方法,用于确定维护策略,以最大程度地提高设备和系统的可靠性和稳定性。
使用RCM可以评估不同的维护任务,并确定适当的维护频率和方法,以确保系统以最佳状态运行。
二、提高设计的可靠性和稳定性的方法除了进行可靠性分析外,还有一些方法可以帮助工程师提高机械设计的可靠性和稳定性。
2.1 材料选择在机械设计中,选择合适的材料是提高设计可靠性和稳定性的重要一环。
设计师需要根据产品的工作环境、承受的载荷和运行温度等因素,选择具有良好强度、韧性和耐磨性等特性的材料。
2.2 加工精度控制在制造过程中,加工精度对设计的可靠性和稳定性有着重要的影响。
设计师需要与制造工程师紧密合作,确保零件的加工精度符合设计要求,避免由于制造误差导致的性能下降和故障发生。
- 1、下载文档前请自行甄别文档内容的完整性,平台不提供额外的编辑、内容补充、找答案等附加服务。
- 2、"仅部分预览"的文档,不可在线预览部分如存在完整性等问题,可反馈申请退款(可完整预览的文档不适用该条件!)。
- 3、如文档侵犯您的权益,请联系客服反馈,我们会尽快为您处理(人工客服工作时间:9:00-18:30)。
现代设计与制造技术
Modern Design Methods And Manufacturer Technology
机械与电子工程学院
机械可靠性设计方法
§1、关于机械可靠性设计的几个问题
一、可靠性研究的必要性
1、产品更新快,采用新技术等未成熟的实验即被采用。 2、整机或系统复杂、零部件数量增多,发生故障的机会增多。 3、工业化国家实行产品责任索赔办法,迫使生产厂家注重可 靠性。 4、产品或系统可靠性的提高可使用户获得较大的经济效益和 社会效益。
机械可靠性设计方法
80年代以来机械可靠性研究在我国开始受到重视,我国有 关可靠性问题的研究。但是可靠性技术在一般工业和企业 中的应用还不广泛,与先进工业国家还存在较大的差距。 – 从1986年起,机械部已经发布了六批限期考核机电产 品可靠性指标的清单,前后共有879种产品已经进行可 靠性指标的考核 – 1990年11月和1995年10月,机械工业部举行了两次新 闻发布会,先后介绍了236和159种带有可靠性指标的 机电产品
概率论与数理统计是可靠性研究的理论基础。 6)可靠性应用技术:包括可靠性设计和预测,可靠性评价与
验证,可靠性标准等。
机械可靠性设计方法
可靠性工程所包含的内容
1)可靠性理论应用到产品的可靠性评价方面,有可靠性 评估与可靠性预测。
2)可靠性理论应用到产品、零件的设计上,有概率工程 设计或可靠性设计。
机械可靠性设计方法
可靠性是一门独立的工程技术学科,它起源于上个世纪五 十年代初。半个世纪以来,可靠性工程经历了50年代的起步阶 段,60年代的发展阶段,70年代的成熟阶段和80年代的更深更 广的发展阶段,以及90年代 以来进入向综合治理化、自动化、 智能化和实用化发展阶段,可靠性工程成为一门提高产品质量 的重要工程技术学科。
机械可靠性设计方法
该零件的可靠度:
R(t) N R (t) N
该零件的故障(失效)概率: Q(t ) NQ (t ) N
R(t) 1 Q(t)
零件寿命-故障个数分布 直方图
1、故障分布函数Q(t):该直
方图反映了某类零件在各个寿命 间隔时间内故障发生的可靠性大 小,即故障概率的大小。
机械可靠性设计方法
虽然有较高的安全系数,但由于材料强度与应力分布并非 单值的,因此,当处于某种情况时,应力S>材料强度F,这样 零件就可能发生失效。
机械可靠性设计方法
传统的安全系数设计法的局限性: 若应力和强度分布的标准差σS和σF保持不变,而以相同的比 例K改变两个分布的平均值μS和μF ,当K>1时, μS和μF右移, 此时安全系数n= μS/μF虽然没变,但是可靠性却提高了。当 K<1时,情况正好相反。
机械可靠性设计方法
可靠性的发展
可靠性的研究开始于20世纪60年代美国的航天计划,起源于军 用电子设备。 – 机械和电子故障是NASA主要关心的问题,其中机械故障引
起的事故多,损失大。如: • 1963年同步通讯卫星SYMCOMⅠ,高压容器断裂,引起 卫星空中坠毁; • 1964年人造卫星Ⅲ号因机械故障而损坏
可靠性工程已从军事装备的可靠性发展到民用产品的可靠 性;从电子产品发展到非电子产品的可靠性;从硬件的可靠性 发展到软件的可靠性;从可靠性工程发展为包括维修工程、测 试工程、保障性工程在内的可信性工程;从重视可靠性统计试 验发展到强调可靠性工程试验,通过环境应力筛选及可靠性强 化试验来暴露产品故障,进而提高产品可靠性。
研究认为,产品故障的发生及其原因是随机事 件,随机性是事物的内在性质,具有不可避免 性。
重新确定了故障原因随机性及其不可避免性的 概念;对一些偶然故障找到了自身的解释;确 定了产品设计、结构、工艺与故障间的关系; 产品的可靠性信息更加完整,对故障本质的认 识更加深入。
形成了可靠性试验方法与数据处理方法;颁布 了有关可靠性标准;建立了预防维修体系和可 靠性管理机构;并使可靠性的教育更加普及。
机械可靠性设计方法
可靠性的数值标准:
可靠度(Reliability)。 失效率或故障率(Failure Rate)。 平均寿命(Main Life)。 有效寿命(Useful Life)。 维修度(Maintainability)。 有效度(Availability)。 重要度(Importance)。 -以上统称“可靠性尺度”
机械可靠性设计方法
§2、可靠性的概念和指标
可靠性:产品在规定条件下和规定时间内完成规定功能的能力。
产品的保险期
保持功能参数在一定界限值内的能力
失效:对不可修复和不予修复的产品,称为失效。
维修:为保持或恢复产品能完成规定功能的能力而采取的技术 管理措施。
维修性(维修度):可以维修的产品在规定条件下使用,在规 定时间内按规定的程序和方法进行维修时,保持或恢复到能完 成规定功能的能力。
1992年3月国防部科工委委托军用标准化中心在北京召开 了“非电产品可靠性工作交流研讨会”
2005年GJB450改版,增加机械可靠性内容
机械可靠性设计方法
可靠性发展历史
阶段),又称为铅笔一纸
阶段
第二阶段(1958—1968 年)
第三阶段(1968年以后)
– 1965年始,NASA开始三项机械可靠性工作 • 用过载试验方法进行可靠性试验验证 • 用随机动载荷验证结构和零件的可靠性 • 在关键机械零件中采用概率设计方法,将可靠度设计到 结构和机械零部件中
机械可靠性设计方法
从20世纪70年代起,西方工业发达国家全面开展可靠性工 程实践和应用,可靠性技术变得越来越重要 – 从航空、航天、尖端武器和电子等行业,逐步推广应 用到各个行业 • 核能、机械、电气、冶金、化工、铁道、船舶、电 站、建筑、水利、通讯、医药等 – 从宇宙飞船到日用产品全面普及 • 汽车、洗衣机、冰箱、复印机等 – NASA将可靠性工程技术列为登月成功的三大技术成就 之一
机械可靠性设计方法
由美国、英国、加拿大、澳大利亚和新西兰五国组成的技 术合作计划(TTCP)委员会编制出一本常用机械设备可 靠性预计手册
日本以民用产品为主,大力推进机械可靠性的应用研究 , 1958年,日本成立了“可靠性研究委员会”,1973年成立 “电子元件可靠性中心” – 日本科技联盟的一个机械工业可靠性分科会将故障模 式、影响(FMEA)等技术成功地引入机械工业的企业 中 – 日本企业界普遍认为:机械产品是通过长期使用经验 的累积,发现故障经过不断设计改进获得的可靠性 – 日本一方面采用成功的经验设计,同时采用可靠性的 概率设计方法的结果以及与实物试验进行比较,总结 经验,收集和积累机械可靠性数据
机械可靠性设计方法
2、故障分布函数f(t):曲线f(t)反映了故障概率的频谱,
在可靠性里称为故障(失效)概率密度函数。
定义为:在时间t附近的单位时间内,失效的产品数dNQ(t)/dt和
产品总数之比。
f (t)
1 N
d dt
NQ (t )
故障(失效)概率密度函数
故障分布函数
1d
d
f (t)
N
3)将可靠性设计与优化理论结合起来,综合各方面的因 素,考虑设计的最佳效果,有可靠性分配与可靠性优化。
4)考虑设备的维修因素之后的可靠性问题,有系统的可 维护性与可利用性的估计。
5)作为以上各分支的基础,有可靠性试验及其数据处理
机械可靠性设计方法
机械可靠性设计方法
机械可靠性设计方法
1)方案论证阶段:确定可靠性指标,对可靠性和成本进行估 算。 2)审批阶段:对可靠度及其增长初步评估、验证试验要求、 评价和选择试制厂家。 3)设计研制阶段:主要进行可靠性预测、分配和故障模式及 综合影响分析,进行具体结构设计。 4)生产及试验阶段:按规范进行寿命试验、故障分析及反馈、 验收试验等。 5)使用阶段:收集现场可靠性数据,为改型提供依据
机械可靠性设计方法
产品质量是产品的一组固有特性满足顾客和其他相关要求的 能力。
产品可靠性是产品性能随时间的保持能力,换言之,要长时 间地保持性能不出故障或出了故障能很快维修是产品很重要 的质量特性。
产品可靠性是产品最重要的质量指标之一,是产品技术性能 和经济性的基本保证,并决定着产品在市场中的竞争能力。
根据日本统计资料介绍,在1971~1981年的10年中,电子 产品可靠性水平提高了1~3个数量级,工程机械产品平均 无故障时间提高了3倍。
机械可靠性设计方法
前苏联对机械可靠性的研究十分重视, 50年代后期,前苏 联开始可靠性研究在其二十年科技规划中,将提高机械产 品可靠性和寿命作为重点任务之一。 – 发布了一系可靠性国家标准,这些标准主要以机械产 品为对象,适于机械制造和仪器仪表制造行业的产品 – 在各类机械设备的产品标准中,还规定了可靠性指标 或相应的试验方案 – 苏联还充分利用丰富的实际经验,研究并提出典型机 械零件的可靠性设计可经验公式,专门出版《机械可 靠性设计手册》 – 苏联还十分重视工艺可靠性和制造过程的严格控制管 理,认为这是保证机械产品可靠性的重要手段
机械可靠性设计方法
美国六七十年代就将可靠性技术引入汽车、发电设备、拖 拉机、发动机等机械产品。 – 80年代,美国罗姆航空研究中心专门作了一次非电子 设备可靠性应用情况的调查分析 – 美国国防部可靠性分析中心(RAC)收集和出版了大 量的非电子零部件的可靠性数据手册 – 以美国亚利桑那大学D.Kececioglu教授为首的可靠性专 家开展机械可靠性设计理论的研究,积极推行概率设 计法,提出开展机械概率设计的十五个步骤
机械可靠性设计方法
可靠性包括两部分内容:可靠性理论基础和可靠性实用技术。
三、可靠性的性质和可靠性预测方法
可靠性性质 可靠性设计时可靠性学科的重要分支,它的重要内容之一是可 靠性预测,其次是可靠性分配。 可靠性预测方法 可靠性预测是一种预测方法,即从所得的失效数据预报一个零 部件或系统实际可能达到的可靠度,预报这些零件或系统在规 定的条件下和在规定的时间内,完成规定功能的概率。