机械手臂外文翻译
机械手臂外文文献翻译、中英文翻译、外文翻译

外文出处:《Manufacturing Engineering and Technology—Machining》附件1:外文原文ManipulatorRobot developed in recent decades as high-tech automated production equipment. I ndustrial robot is an important branch of industrial robots. It features can be program med to perform tasks in a variety of expectations, in both structure and performance a dvantages of their own people and machines, in particular, reflects the people's intellig ence and adaptability. The accuracy of robot operations and a variety of environments the ability to complete the work in the field of national economy and there are broad p rospects for development. With the development of industrial automation, there has be en CNC machining center, it is in reducing labor intensity, while greatly improved lab or productivity. However, the upper and lower common in CNC machining processes material, usually still use manual or traditional relay-controlled semi-automatic device . The former time-consuming and labor intensive, inefficient; the latter due to design c omplexity, require more relays, wiring complexity, vulnerability to body vibration inte rference, while the existence of poor reliability, fault more maintenance problems and other issues. Programmable Logic Controller PLC-controlled robot control system for materials up and down movement is simple, circuit design is reasonable, with a stron g anti-jamming capability, ensuring the system's reliability, reduced maintenance rate, and improve work efficiency. Robot technology related to mechanics, mechanics, elec trical hydraulic technology, automatic control technology, sensor technology and com puter technology and other fields of science, is a cross-disciplinary integrated technol ogy.First, an overview of industrial manipulatorRobot is a kind of positioning control can be automated and can be re-programmed to change in multi-functional machine, which has multiple degrees of freedom can be used to carry an object in order to complete the work in different environments. Low wages in China, plastic products industry, although still a labor-intensive, mechanical hand use has become increasingly popular. Electronics and automotive industries thatEurope and the United States multinational companies very early in their factories in China, the introduction of automated production. But now the changes are those found in industrial-intensive South China, East China's coastal areas, local plastic processin g plants have also emerged in mechanical watches began to become increasingly inter ested in, because they have to face a high turnover rate of workers, as well as for the workers to pay work-related injuries fee challenges.With the rapid development of China's industrial production, especially the reform and opening up after the rapid increase in the degree of automation to achieve the wor kpiece handling, steering, transmission or operation of brazing, spray gun, wrenches a nd other tools for processing and assembly operations since, which has more and mor e attracted our attention. Robot is to imitate the manual part of the action, according to a given program, track and requirements for automatic capture, handling or operation of the automatic mechanical devices.In real life, you will find this a problem. In the machine shop, the processing of part s loading time is not annoying, and labor productivity is not high, the cost of producti on major, and sometimes man-made incidents will occur, resulting in processing were injured. Think about what could replace it with the processing time of a tour as long a s there are a few people, and can operate 24 hours saturated human right? The answer is yes, but the robot can come to replace it.Production of mechanical hand can increase the automation level of production and labor productivity; can reduce labor intensity, ensuring product quality, to achieve saf e production; particularly in the high-temperature, high pressure, low temperature, lo w pressure, dust, explosive, toxic and radioactive gases such as poor environment can replace the normal working people. Here I would like to think of designing a robot to be used in actual production.Why would a robot designed to provide a pneumatic power: pneumatic robot refers to the compressed air as power source-driven robot. With pressure-driven and other en ergy-driven comparison have the following advantages: 1. Air inexhaustible, used late r discharged into the atmosphere, does not require recycling and disposal, do not pollu te the environment. (Concept of environmental protection) 2. Air stick is small, the pipeline pressure loss is small (typically less than asphalt gas path pressure drop of one-thousandth), to facilitate long-distance transport. 3. Compressed air of the working pre ssure is low (usually 4 to 8 kg / per square centimeter), and therefore moving the mate rial components and manufacturing accuracy requirements can be lowered. 4. With th e hydraulic transmission, compared to its faster action and reaction, which is one of th e advantages pneumatic outstanding. 5. The air cleaner media, it will not degenerate, n ot easy to plug the pipeline. But there are also places where it fly in the ointment: 1. A s the compressibility of air, resulting in poor aerodynamic stability of the work, resulti ng in the implementing agencies as the precision of the velocity and not easily control led. 2. As the use of low atmospheric pressure, the output power can not be too large; i n order to increase the output power is bound to the structure of the entire pneumatic s ystem size increased.With pneumatic drive and compare with other energy sources drive has the followin g advantages:Air inexhaustible, used later discharged into the atmosphere, without recycling and disposal, do not pollute the environment. Accidental or a small amount of leakage wo uld not be a serious impact on production. Viscosity of air is small, the pipeline pressu re loss also is very small, easy long-distance transport.The lower working pressure of compressed air, pneumatic components and therefor e the material and manufacturing accuracy requirements can be lowered. In general, re ciprocating thrust in 1 to 2 tons pneumatic economy is better.Compared with the hydraulic transmission, and its faster action and reaction, which is one of the outstanding merits of pneumatic.Clean air medium, it will not degenerate, not easy to plug the pipeline. It can be saf ely used in flammable, explosive and the dust big occasions. Also easy to realize auto matic overload protection.Second, the composition, mechanical handRobot in the form of a variety of forms, some relatively simple, some more complic ated, but the basic form is the same as the composition of the , Usually by the implem enting agencies, transmission systems, control systems and auxiliary devices composed.1.Implementing agenciesManipulator executing agency by the hands, wrists, arms, pillars. Hands are crawlin g institutions, is used to clamp and release the workpiece, and similar to human finger s, to complete the staffing of similar actions. Wrist and fingers and the arm connecting the components can be up and down, left, and rotary movement. A simple mechanical hand can not wrist. Pillars used to support the arm can also be made mobile as needed .2. TransmissionThe actuator to be achieved by the transmission system. Sub-transmission system c ommonly used manipulator mechanical transmission, hydraulic transmission, pneuma tic and electric power transmission and other drive several forms.3. Control SystemManipulator control system's main role is to control the robot according to certain p rocedures, direction, position, speed of action, a simple mechanical hand is generally not set up a dedicated control system, using only trip switches, relays, control valves a nd circuits can be achieved dynamic drive system control, so that implementing agenc ies according to the requirements of action. Action will have to use complex program mable robot controller, the micro-computer control.Three, mechanical hand classification and characteristicsRobots are generally divided into three categories: the first is the general machinery does not require manual hand. It is an independent not affiliated with a particular host device. It can be programmed according to the needs of the task to complete the oper ation of the provisions. It is characterized with ordinary mechanical performance, also has general machinery, memory, intelligence ternary machinery. The second category is the need to manually do it, called the operation of aircraft. It originated in the atom, military industry, first through the operation of machines to complete a particular job, and later developed to operate using radio signals to carry out detecting machines suc h as the Moon. Used in industrial manipulator also fall into this category. The third cat egory is dedicated manipulator, the main subsidiary of the automatic machines or automatic lines, to solve the machine up and down the workpiece material and delivery. T his mechanical hand in foreign countries known as the "Mechanical Hand", which is t he host of services, from the host-driven; exception of a few outside the working proc edures are generally fixed, and therefore special.Main features:First, mechanical hand (the upper and lower material robot, assembly robot, handlin g robot, stacking robot, help robot, vacuum handling machines, vacuum suction crane, labor-saving spreader, pneumatic balancer, etc.).Second, cantilever cranes (cantilever crane, electric chain hoist crane, air balance th e hanging, etc.)Third, rail-type transport system (hanging rail, light rail, single girder cranes, doubl e-beam crane)Four, industrial machinery, application of handManipulator in the mechanization and automation of the production process develo ped a new type of device. In recent years, as electronic technology, especially comput er extensive use of robot development and production of high-tech fields has become a rapidly developed a new technology, which further promoted the development of ro bot, allowing robot to better achieved with the combination of mechanization and auto mation.Although the robot is not as flexible as staff, but it has to the continuous duplication of work and labor, I do not know fatigue, not afraid of danger, the power snatch weig ht characteristics when compared with manual large, therefore, mechanical hand has b een of great importance to many sectors, and increasingly has been applied widely, for example:(1) Machining the workpiece loading and unloading, especially in the automatic lat he, combination machine tool use is more common.(2) In the assembly operations are widely used in the electronics industry, it can be used to assemble printed circuit boards, in the machinery industry It can be used to ass emble parts and components.(3) The working conditions may be poor, monotonous, repetitive easy to sub-fatigue working environment to replace human labor.(4) May be in dangerous situations, such as military goods handling, dangerous go ods and hazardous materials removal and so on..(5) Universe and ocean development.(6), military engineering and biomedical research and testing.Help mechanical hands: also known as the balancer, balance suspended, labor-saving spreader, manual Transfer machine is a kind of weightlessness of manual load system, a novel, time-saving technology for material handling operations booster equipment, belonging to kinds of non-standard design of series products. Customer application ne eds, creating customized cases. Manual operation of a simulation of the automatic ma chinery, it can be a fixed program draws ﹑ handling objects or perform household to ols to accomplish certain specific actions. Application of robot can replace the people engaged in monotonous ﹑ repetitive or heavy manual labor, the mechanization and a utomation of production, instead of people in hazardous environments manual operati on, improving working conditions and ensure personal safety. The late 20th century, 4 0, the United States atomic energy experiments, the first use of radioactive material ha ndling robot, human robot in a safe room to manipulate various operations and experi mentation. 50 years later, manipulator and gradually extended to industrial production sector, for the temperatures, polluted areas, and loading and unloading to take place t he work piece material, but also as an auxiliary device in automatic machine tools, ma chine tools, automatic production lines and processing center applications, the comple tion of the upper and lower material, or From the library take place knife knife and so on according to fixed procedures for the replacement operation. Robot body mainly b y the hand and sports institutions. Agencies with the use of hands and operation of obj ects of different occasions, often there are clamping ﹑ support and adsorption type of care. Movement organs are generally hydraulic pneumatic ﹑﹑ electrical device dri vers. Manipulator can be achieved independently retractable ﹑ rotation and lifting m ovements, generally 2 to 3 degrees of freedom. Robots are widely used in metallurgic al industry, machinery manufacture, light industry and atomic energy sectors.Can mimic some of the staff and arm motor function, a fixd procedure for the capture, handling objects or operating tools, automatic operation device. It can replace hum an labor in order to achieve the production of heavy mechanization and automation th at can operate in hazardous environments to protect the personal safety, which is wide ly used in machinery manufacturing, metallurgy, electronics, light industry and nuclea r power sectors. Mechanical hand tools or other equipment commonly used for additio nal devices, such as the automatic machines or automatic production line handling an d transmission of the workpiece, the replacement of cutting tools in machining centers , etc. generally do not have a separate control device. Some operating devices require direct manipulation by humans; such as the atomic energy sector performs household hazardous materials used in the master-slave manipulator is also often referred to as m echanical hand.Manipulator mainly by hand and sports institutions. Task of hand is holding the wor kpiece (or tool) components, according to grasping objects by shape, size, weight, mat erial and operational requirements of a variety of structural forms, such as clamp type, type and adsorption-based care such as holding. Sports organizations, so that the com pletion of a variety of hand rotation (swing), mobile or compound movements to achie ve the required action, to change the location of objects by grasping and posture. Robot is the automated production of a kind used in the process of crawling and mo ving piece features automatic device, which is mechanized and automated production process developed a new type of device. In recent years, as electronic technology, esp ecially computer extensive use of robot development and production of high-tech fiel ds has become a rapidly developed a new technology, which further promoted the dev elopment of robot, allowing robot to better achieved with the combination of mechani zation and automation. Robot can replace humans completed the risk of duplication of boring work, to reduce human labor intensity and improve labor productivity. Manipu lator has been applied more and more widely, in the machinery industry, it can be use d for parts assembly, work piece handling, loading and unloading, particularly in the a utomation of CNC machine tools, modular machine tools more commonly used. At pr esent, the robot has developed into a FMS flexible manufacturing systems and flexibl e manufacturing cell in an important component of the FMC. The machine tool equipment and machinery in hand together constitute a flexible manufacturing system or a f lexible manufacturing cell, it was adapted to small and medium volume production, y ou can save a huge amount of the work piece conveyor device, compact, and adaptabl e. When the work piece changes, flexible production system is very easy to change wi ll help enterprises to continuously update the marketable variety, improve product qua lity, and better adapt to market competition. At present, China's industrial robot techno logy and its engineering application level and comparable to foreign countries there is a certain distance, application and industrialization of the size of the low level of robo t research and development of a direct impact on raising the level of automation in Ch ina, from the economy, technical considerations are very necessary. Therefore, the stu dy of mechanical hand design is very meaningful.附件1:外文资料翻译译文机械手机械手是近几十年发展起来的一种高科技自动化生产设备。
毕业设计机械手外文翻译

外文翻译译文题目 一种与移动机械臂的部分零件所受载荷相协译文题目调的运动结构(2)原稿题目A kinematically compatible framework for cooperative payload transport by nonholonomic mobile manipulators(2)原稿出处 Auton Robot (2006) 21:227–242 原稿出处A kinematically compatible framework for cooperative payload transport by nonholonomic mobile manipulators (2) M. Abou-Samah 1 , C. P. Tang 2 , R. M. Bhatt 2 and V. Krovi 2(1) MSC Software Corporation, Ann Arbor, MI 48105, USA (2) Mechanical (2) Mechanical and and Aerospace Engineering, State University of of New New York at at Buffalo, Buffalo, Buffalo, NY 14260, USA Received: 5 August 2005 Revised: 25 May 2006 Accepted: 30 May 2006 Published online: 5 September 2006 Abstract In this paper, we examine the development of a kinematically compatible control framework for a modular system of wheeled mobile manipulators that can team up to cooperatively transport a common payload. Each individually autonomous mobile manipulator consists of a differentially-driven Wheeled Mobile Robot (WMR) with a mounted two degree-of-freedom (d.o.f) revolute-jointed, planar and passive manipulator arm. The composite wheeled vehicle, formed by placing a payload at the end-effectors of two (or more) such mobile manipulators, has the capability to accommodate, detect and correct both instantaneous and finite relative configuration errors.The kinematically-compatible motion-planning/control framework developed here is intended to facilitate maintenance of all kinematic (holonomic and nonholonomic) constraints within such systems. Given an arbitrary end-effector trajectory, each individual mobile-manipulator's bi-level hierarchical controller first generates a kinematically- feasible desired trajectory for the WMR base, which is then tracked by a suitable lower-level posture stabilizing controller. Two variants of system-level cooperative control schemes schemes——leader-follower and decentralized control control——are then created based on the individual mobile-manipulator control scheme. Both methods are evaluated within an implementation framework that emphasizes both virtual prototyping (VP) and hardware-in-the-loop (HIL) experimentation. Simulation and experimental results of an example of a two-module system are used to highlight the capabilities of a real-time local sensor-based controller for accommodation, detection and corection of relative formation errors. Keywords Composite system-Hardware-in-the-loop-Mobile manipulator- Physical cooperation-Redundancy resolution-Virtual prototypingKinematic collaborationof two mobilemanipulators We now examine two variants of system-level cooperative control schemes schemes——leader-follower and decentralized control control——that can be created based on the individual mobile-manipulator control scheme.Leader-follower approach The first method of modeling such a system considers the midpoint of the mobile base (MP B) of the mobile-manipulator B to be rigidly attached to the end-effector of mobile manipulator A, as depicted in Fig. 4. Figure 4(b) depictshow the end-effector frame {E } of MP A is rigidly attached to the frame at MP B (separated by a constant rotation angle β).(15)Fig. 4 Schematic diagrams of the leader-follower scheme: (a) the 3-link mobile manipulator under analysis, and (b) the two-module composite system MP B now takes on the role of the leader and can be controlled to follow any trajectory trajectory that that is feasible feasible for for a WMR. Hence, given a trajectory trajectory of of the leader MP B , and the preferred manipulator configuration of, Eq. (5) can be rewritten as:(16)and correspondingly Eqs. (6)and correspondingly Eqs. (6)––(8) as:(17)Thus, the trajectory of the virtual (reference) robot for the follower MP A, and the derived velocities can now bedetermined. determined. This This This forms forms forms the the the leader-follower leader-follower leader-follower scheme scheme scheme used used used for for for the the the control control control of of of the the collaborative system carrying a common payload.Decentralized approachThe second second approach approach approach considers considers considers the the frame attached attached to to a point of interest interest on on the common payload as the end-effector frame of both the flanking mobile manipulator systems, as depicted in Fig. 5. Thus, a desired trajectory specified for this payload frame can then provide the desired reference trajectories for the two mobile platforms using the similar framework developedin the previous section by takingand , where . Thispermits Eq. (5) to be rewritten as: (18)Fig. 5 Decentralized control scheme implementation permits the (a) composite system; to be treated as (b) two independent 2-link mobile manipulators and correspondingly Eq. (6)and correspondingly Eq. (6)––(8) as:(19)Each two-link mobile manipulator now controls its configuration with reference to this common end-effector frame mounted on the payload. However, thelocations locations of of of the the the attachments attachments attachments of of of the the the physical physical physical manipulators manipulators manipulators with respect with respect with respect to to to the the payload reference frame must be known apriori.Implementation frameworkWe examine the design and development of a two-stage implementation framework, shown in Fig. 6, that emphasizes both virtual prototyping (VP) based refinement and hardware-in-the-loop (HIL) experimentation.Fig. 6 Paradigm for rapid development and testing of the control scheme on on virtual and physical virtual and physical prototypes Virtual prototyping based refinementIn the first stage, we employ virtual prototyping (VP) tools to rapidly create, evaluate and refine parametric models of the overall system and test various algorithms algorithms in in in simulation simulation simulation within within within a a a virtual virtual virtual environment. environment. environment. 3D 3D 3D solid solid solid models models models of of of the the mobile platforms and the manipulators of interest are created in a CAD package,4 and exported with their corresponding geometric and material properties into a dynamic simulation environment.5 Figure 7(a) shows an example of the application of such framework for simulating the motion of a mobile platformcontrolled controlled by an by an by an algorithm algorithm algorithm implemented implemented implemented in Simulink.in Simulink.6 However, However, it is important it is importantto note that the utility of such virtual testing is limited by: (a) the ability to correctly model and simulate the various phenomena within the virtual environment; (b) the fidelity of the available simulation tools; and (c) ultimately, ultimately, the the the ability ability ability of of of the the the designer designer designer to to to correctly correctly correctly model model model the the the desired desired desired system system and suitably interpret the results.Fig. 7 A single WMR base undergoing testing within the (a) virtual prototyping framework; and (b) hardware-in-the-loop (HIL) testing framework Hardware-in-the-loop experimentationWe employ a hardware-in-the-loop (HIL) methodology for rapid experimental verification of the real-time controllers on the electromechanical mobile manipulator prototypes. Each individual WMR is constructed using two powered wheels and two unactuated casters. Conventional disc-type rear wheels, powered by gear-motors, are chosen because of robust physical construction and ease of operation in the presence of terrain irregularities. Passive ball casters are preferred over wheel casters to simplify the constraints on maneuverability introduced by the casters. The mounted manipulator arm has two passive revolute joints with axes of rotation parallel to each other and perpendicular to the base of the mobile platform. The first joint is placed appropriately at the geometric center on top frame of the platform. The location of the second joint can be adjusted to any position along the slotted first link. The second link itself is reduced to a flat plate supported by the second joint. Each joint is instrumented instrumented with with optical encoder that can measure the joint rotations. The completely assembled two-link mobile manipulator is shown in Fig. 1(c). The second mobile manipulator (see left module of Fig. 1(b) and (d)) employs the same same overall overall overall design design design but but possesses possesses a a motor motor at at the the base base base joint joint joint of of of the the mounted two-link arm. The motor may be used to control the joint two-link arm. The motor may be used to control the joint motion along a motion along a predetermined trajectory (which can include braking/holding the joint at a predetermined predetermined position). position). position). When When When the the the motor motor motor is is is switched switched switched off off off the the the joint joint joint now now now reverts reverts to a passive joint (with much greater damping). The motor is included for permitting future force-redistribution studies. In this paper, however, the motor is used solely to lock the joint prevent self-motions self-motions of of the articulated linkage for certain pathological cases (Bhatt et al., 2005; Tang and Krovi, 2004). PWM-output motor driver cards are used to drive the gearmotors; and encoder cards monitor the encoders instrumenting the various articulated arms. This embedded controller controller communicates communicates communicates with with a designated designated host host computer using TCP/IP for program download and data logging. The host computer withMATLAB/Simulink/Real Time Workshop 8 provides a convenient graphical userinterface environment for system-level software development using a block-diagrammatic language. The compiled executable is downloaded over the network and executes in real-time on the embedded controller while accessing locally installed hardware components.In particular, the ability to selectively test components/systems at various levels (e.g. individual motors, individual WMRs or entire systems) without wearing out components during design iterations was very useful. Figure 7(b) illustrates the implementation of such a system on one of the WMRs. Numerous calibration, simulation and experimental studies carried out with this framework, at the individual-level and system-level, are reported in Abou-Samah (2001).Experimental resultsFor the subsequent experiments,99we prescribe the initial configuration configuration of of the two-module composite system, as shown in Fig. 8. Specifically, we position thetwo two WMRs such WMRs such WMRs such that MP that MP that MP A is A is A is located located located at a relative position of at a relative position of ,and with a relative orientation difference of with respect to MP B.For fixed link-lengths this inherently specifies the values of the various configuration angles as shown in Table 1.Table 1 Parameters for the initial configuration of the two-module composite wheeled system (see Fig. 8 for details) Link lengths of the articulationL 1 0.28 0.28 m m m (11 (11 (11 in) in)L 2 0.28 0.28 m m m (11 (11 (11 in) in) Relative angles of the configuration of thearticulationL 3 0.28 0.28 m m m (11 (11 (11 in) in)φ 1 333333.98°.98°.98°φ 2 280.07°280.07°φ 3 337.36°337.36° Offset between the wheeled mobile basesφ 4 128.59°128.59°δ 0.00°0.00°0.00 m (0 in)0.61 0.61 m m m (24 (24 (24 in) in)Fig. 8 Initial configuration of the two-module composite wheeled system Leader-follower approachA straight line trajectory at a velocity of 0.0254 m/s is prescribed for the leader, MP B. Given a desired configuration of the manipulator arm, the algorithm algorithm described in described in described in Section 4.1 Section 4.1 Section 4.1 is used is used is used to to to obtain a desired obtain a desired obtain a desired trajectory for trajectory for MP A. A large disruption is intentionally introduced by causing one of the wheels of MP A to run over a bump, to evaluate the effectiveness of wheels of MP A to run over a bump, to evaluate the effectiveness of the the disturbance accommodation, detection and compensation.The results are examined in two case scenarios examined in two case scenarios –– Case A: MP A employs odometric estimation for localization as seen in Fig. 9, and Case B: MP A employs sensed articulations for localization as seen in Fig. as seen in Fig. 1010. In each of these figures, (a) presents the overall -trajectory of {M } of MPA with respect to the end-effector frame {E } (that is rigidly attached to the {M } of MPB) while (b), (c) and (d) present the relative orientation difference, X -difference and Y -difference as functions of time. Further in both sets of figures, the ‘Desired’ (––(–– line) is the desired trajectory typically computed offline; and ‘Actual’ (–o – line) is the actual trajectory followed by the system, as determined by post-processing the measurements of the instrumented articulations.However, in Fig. However, in Fig. 99, the (, the (––x – line) represents the odometric estimate while in Fig. in Fig. 1010 it stands for the articulation based estimate (which therefore coincides with the ‘Actual’ (–coincides with the ‘Actual’ (–o o – line) trajectory).Fig. 9 Case A: Odometric Estimation of Frame M, used in the control of MP A following MPB in a leader-follower approach, is unable to detect non-systematic errors such as wheel-slip. (a) XY trajectory of Frame M; (b) Orientation versus Time; (c) X position of Frame M versus Time; and (d) Y position of Frame M versus Time Fig. 10 Case B: Articulation based Estimation of Frame M, used for control of MPA with respect to MP B in a leader-follower approach is able to detect and correct non-systematic errors such as wheel-slip. slip. (a) (a) XY trajectory of Frame M; (b) Orientation versus Time; (c) X position of Frame M versus time; and (d) Y position of Frame M versus time In Case A, the introduction of the disruption causes a drift in the relative configuration of the system which remains undetected by the odometric estimation. Further, as seen in Fig. 9, this drift has a tendency to grow if left uncorrected. However, as seen in Fig. 10, the system can use the articulation-based articulation-based estimation estimation estimation (Case (Case (Case B) B) B) to to not only only detect detect detect disturbances disturbances disturbances to to to the the relative configuration but also to successfully restore the original system configuration.Decentralized control approachIn this decentralized control scenario, a straight line trajectory with a velocity of 0.0254 m/s is presented for the payload frame. As in the leader-follower scenario, a large disruption is introduced by causing one of the wheels of MP A to run over a bump. The algorithm is tested using two further case scenarios scenarios——Case Case C:C: Both mobile mobile platforms platforms platforms employ employ odometric odometric estimation estimation estimation for for localization as shown in Fig. as shown in Fig. 1111, and Case D: Both mobile platforms employsensed articulations for localization as shown in Fig. as shown in Fig. 1212.Fig. 11 Case C: Odometric estimation of frames M of MP A and MP B, used in the control of MP A with respect to MP B in the decentralized approach, is again unable to detect non-systematic errors such as wheel-slip. (a) XY trajectory of frame M of MP A; (b) XY trajectory of frame M of MP B; (c) Relative orientation, between MP A and MP B, versus time; (d) X distance, between MP A and MP B, versus time; and (e) Y distance, between MP A and MP B, versus time. (f) Sequential photographs of the corresponding composite system motion (as time progresses from left to right along each row)Fig. 12 Case D: Articulation based estimation of frames M of MP A and MP B, used for the control of MP A and MP B with respect to a payload-fixed frame is able to detect and correct non-systematic errors such as wheel-slip. (a) XY trajectory of frame M of MP A; (b) XY trajectory of frame M of MP B; (c) Relative orientation, between MP A and MP B, versus time; (d) X distance, between MP A and MP B, versus time; and (e) Y distance, between MP A and MP B, versus time. (f) Sequential photographs of the corresponding composite system motion (as time progresses from left to right along each row) In In each each each of of of these these these figures, figures, figures, subplots subplots subplots (a) (a) (a) and and and (b) (b) (b) presents presents presents the the the overall overalltrajectories trajectories of of frames frames {{M } of MP A and MP B respectively respectively with with with respect respect respect to to their initial poses. Subplots (c), (d) and (e) present the relative orientation difference, X -difference and Y -difference of frames {M } of MP A and MP B respectively as functions of time. Further in both sets of figures, the ‘Desired’ ‘Desired’ (––(––(–– line) is the desired trajectory trajectory typically typically computed offline; and ‘Actual’ (–and ‘Actual’ (–o o – line) is the actual trajectory followed by the system, as determined by post-processing the measurements of the instrumented articulations. articulations. However, However, However, in in in Fig. Fig. Fig. 1111, the (–x – line) line) represents represents represents the the odometric estimate while in Fig. estimate while in Fig. 1212 it stands for the articulation based estimate.In Case C, both mobile platforms use the odometric estimation for localization —hence hence as as as expected, expected, expected, Fig. Fig. Fig. 1111 reflects reflects the the the fact fact fact that that that the the the system system system is is unable unable to to to detect detect detect or or or correct correct correct for for for changes changes changes in in in the the the relative relative relative system system system configuration. configuration. However the data obtained from the articulations accurately captures theexistence of errors between the frames of reference of MP B and MP A. Thus, using the articulation-based articulation-based estimation estimation of relative configuration for control as in Case D allows the detection of disturbances and successful restoration of the original system configuration configuration as as shown in Fig. 12. Note, however, however, while while the relative system configuration is maintained, errors relative to a global reference frame cannot be detected if both WMRs undergo identical simultaneous disturbances . Detection of such absolute errors would require an external reference and is beyond the scope of the existing framework.ConclusionIn this paper, we examined the design, development and validation of a kinematically compatible framework for cooperative transport of a common payload payload by by by a a team team of of nonholonomic nonholonomic mobile mobile mobile manipulators. manipulators. manipulators. Each Each Each individual individual individual mobile mobile manipulator module consists of a differentially driven wheeled WMR retrofitted with with a a a passive passive passive two two two revolute revolute revolute jointed jointed jointed planar planar planar manipulator manipulator manipulator arm. arm. arm. A composite A composite A composite multi multi degree-of-freedom degree-of-freedom vehicle vehicle system could then be modularly created by attaching a common payload on the end-effector of two or more such modules.The composite composite system system allowed payload trajectory tracking errors, arising from subsystem controller errors or environmental disturbances, to be readily accommodated within the compliance offered by the articulated linkage. The individual mobile manipulators compensated by modifying their WMR bases’ motion plans to ensure prioritized satisfaction of the nonholonomic constraints. constraints. The The stabilizing controllers of the WMR bases could then track the recomputed “desired motion plans” to help restore the system system-configuration. -configuration. This scheme not only explicitly ensured maintenance of the kinematic compatibility constraints within the system but is also well suited for an online sensor-based motion planning implementation.This This algorithm was algorithm was algorithm was then then then adapted to adapted to adapted to create two create two create two control schemes for control schemes for the overall composite system — the leader follower approach and the decentralized approach. We evaluated both approaches within an implementation framework that emphasized both, virtual prototyping and hardware-in-the-loop using the case-study of a two module composite system. Experimental results verified the ability of the composite system with sensed articulations to not only accommodate instantaneous disturbances due to terrain irregularities but also to to detect detect detect and and and correct correct correct drift drift drift in in in the the the relative relative relative system system system configuration. configuration. configuration. The The The overall overall framework readily facilitates generalization to treat larger systems with many more mobile manipulator modules.Appendix AThe kinematic constraint equations shown in Eq. (3) may be written in the general form as:(20)Then the velocity constraint equation can be written as:(21)The general solution to this differential equation is:(22)By appropriate selection of the initial conditions within the experimentalsetup, one can create the condition , i.e., exactly satisfying the constraint at the initial time, which then permits the constraint constraint to be to be to be satisfied satisfied satisfied for all for all for all time. However, time. However, time. However, one could also one could also one could also enhance this enhance this process by adding another term to the right-hand-side of Eq. (21) as:(23)where Φ is a positive-definite positive-definite constant constant matrix. This results in a first order stable system:(24)whose solution for any arbitrary initial configuration is:(25)In such systems, there is no longer a requirement to enforcesince the solution exponentially stabilizes to regardless of the initial conditions. This feature could potentially be easily added to transform Eq. (5) to further improve overall performance, but was not required. ReferencesAbou-Samah, M. 2001. A kinematically compatible framework for collaboration of multiple non-holonomic wheeled mobile robots. M. Eng. Thesis, McGill University, Montreal, Canada. Abou-Samah, Abou-Samah, M. M. M. and and and Krovi, Krovi, Krovi, V. V. V. 2002. 2002. 2002. Optimal Optimal Optimal configuration configuration configuration selection selection selection for for for a a a cooperating cooperating cooperating system system system of of mobile manipulators. In P roceedings Proceedings of the 2002 ASME Design Engineering Technical Conferences , DETC2002/MECH-34358, Montreal, QC, Canada. Adams,J.,Bajcsy, R.,Kosecka,J., R.,Kosecka,J., Kumar, Kumar, Kumar, V., V., V., Mandelbaum, Mandelbaum, Mandelbaum, R., R., R., Mintz, Mintz, Mintz, M., M., M., Paul, Paul, Paul, R., R., R., Wang, Wang, Wang, C.-C., C.-C., Yamamoto, Yamamoto, Y Y ., and and Yun, Yun, Yun, X. X. X. 1996. 1996. 1996. Cooperative Cooperative Cooperative material material material handling handling handling by by by human human human and and and robotic robotic robotic agents: agents: Module development and system synthesis. Expert Systems with Applications, 11(2):89, 11(2):89, 11(2):89––97. Bhatt, R.M., Tang, C.P ., Abou-Samah, M., and Krovi, V. 2005. A screw-theoretic analysis framework for for payload payload payload manipulation manipulation manipulation by by by mobile mobile mobile manipulator manipulator manipulator collectives. collectives. collectives. In In Proceedings of the 2005 ASME International Mechanical Engineering Congress & Exposition, IMECE2005-81525, Orlando, Florida, USA. Borenstein, J., Everett, B., and Feng, L. 1996. Navigating Mobile Robots: Systems and Techniques. A. K. Peters, Ltd., Wellesley, MA. Brockett, R.W. 1981. Control theory and singular riemannian geometry. In P .J. Hilton and G.S. Young (eds), New Directions in Applied Mathematics, Springer-Verlag, New York, pp. 11–27. Campion, Campion, G., G., G., Bastin, Bastin, Bastin, G., G., G., and and and D'Andrea-Novel, D'Andrea-Novel, D'Andrea-Novel, B. B. B. 1996. 1996. 1996. Structural Structural Structural properties properties properties and and and classification classification classification of of kinematic kinematic and and and dynamic dynamic dynamic models models models of of of wheeled wheeled wheeled mobile mobile mobile robots. robots. IEEE Transactions on Robotics and Automation , 12(1):47–62. Canudas de Witt, C., Siciliano, B., and Bastin, G. 1996. Theory of Robot Control. Springer-Verlag, Berlin. Desai, Desai, J. J. J. and and and Kumar, Kumar, Kumar, V. V. V. 1999. 1999. 1999. Motion Motion Motion planning planning planning for for for cooperating cooperating cooperating mobile mobile mobile manipulators. manipulators. Journal of Robotic Systems , 16(10):557–579. Donald, B.R., Jennings, J., and Rus, D. 1997. Information invariants for distributed manipulation. TheInternational Journal of Robotics Research, 16(5):673–702. Honzik, B. 2000. Simulation of the kinematically redundant mobile manipulator. In Proceedings of the 8th MATLAB Conference 2000, Prague, Czech Republic, pp. 91, Prague, Czech Republic, pp. 91–95. Humberstone, C.K. and Smith, K.B. 2000. Object transport using multiple mobile robots with non-compliant endeffectors. In D istributed Distributed Autonomous Robotics Systems 4, Springer-Verlag, Tokyo, 4, Springer-Verlag, Tokyo, Tokyo, pp. 417–426. Juberts, M. 2001. Intelligent control of mobility systems, Needs. ISD Division, Manufacturing Engineering Laboratory, National Institute of Standards and Technology. Khatib, Khatib, O., O., O., Yokoi, Yokoi, K., K., Chang, Chang, Chang, K., K., K., Ruspini, Ruspini, Ruspini, D., D., D., Holmberg, Holmberg, Holmberg, R., R., R., and and and Casal, Casal, Casal, A. A. A. 1996. 1996. 1996. Vehicle/arm Vehicle/arm coordination and multiple mobile manipulator decentralized cooperation. In Proceedings of the 1996IEEE/RSJ International Conference on Intelligent Robots and Systems, Osaka, Japan, pp. 546–553. Kosuge, K., Osumi, T., Sato, M., Chiba, K., and Takeo, K. 1998. Transportation of a single object by two decentralized-controlled nonholonomic mobile robots. In 1998 IEEE International Conference on Robotics and Automation, Leuven, Belgium, pp. 2989–2994. Kube, C.R. and Zhang, H. 1997. Task modelling in collective robotics. Autonomous Robots , Kluwer Academic Publishers, 4(1):53–72. Latombe, J.-C. 1991. R obot Robot Motion Planning. Kluwer Academic Publishers, Boston, MA. Li, Z. and Canny, J.F. 1993. Nonholonomic Motion Planning. Kluwer Academic Publishers, Boston, MA. Murray, R.M. and Sastry, S.S. 1993. Nonholonomic motion planning: Steering using sinusoids. IEEE Transactions on Automatic Control, 38(5):700–716. Nakamura, Y . 1991. A dvanced Advanced Robotics: Redundancy and Optimization. Addison-Wesley Publishing Company, Inc., California. Samson, Samson, C. C. C. and and and Ait-Abderrahim, Ait-Abderrahim, Ait-Abderrahim, K. K. K. 1991a. 1991a. 1991a. Feedback Feedback Feedback control control control of of of a a a nonholonomic nonholonomic nonholonomic wheeled wheeled wheeled cart cart cart in in cartesian space. space. In In Proceedings of the 1991 IEEE International Conference on Robotics and Automation , Sacramento CA, pp. 1136–1141. Samson, C. and Ait-Abderrahim, K. 1991b. Feedback stabilization of a nonholonomic wheeled mobile robot. robot. In In Proceedings of the 1991 IEEE/RSJ International Workshop on Intelligent Robots andSystems , Osaka, Japan, pp. 1242–1247. Schenker, P .S., Huntsberger, T.L., Pirjanian, P ., Trebi-Ollennu, A., Das, H., Joshi, S., Aghazarian, H., Ganino, A.J., Kennedy, B.A., and Garrett, M.S. 2000. Robot work crews for planetary outposts: Close cooperation and coordination of multiple mobile robots. In Procedings of SPIE Symposium on Sensor Fusion and Decentralized Control in Robotic Systems III , Boston, MA. Seraji, Seraji, H. H. H. 1998. 1998. 1998. A A A unified unified unified approach approach approach to to to motion motion motion control control control of of of mobile mobile mobile manipulators. manipulators. The International Journal of Robotics Research, 17(2):107, 17(2):107–118. Spletzer, J., Das, A.K., Fierro, C.J., Kumar, V., and Ostrowski, J.P. 2001. Cooperative localization and control for multi-robot manipulation. In Procedings of the 2001 IEEE/RSJ International Conference on Intelligent Robots and Systems, Maui, Hawaii, USA, pp. 631–636. Stilwell, Stilwell, D.J. D.J. D.J. and and and Bay, Bay, Bay, J.S. J.S. J.S. 1993. 1993. 1993. Towards Towards Towards the the the development development development of of of a a a material material material transport transport transport system system system using using swarms of ant-like robots. In Procedings of the 1993 IEEE/RSJ International Conference on Intelligent Robots and Systems, Atlanta, GA, pp. 766, Atlanta, GA, pp. 766–771. Tang, C.P . 2004. Manipulability-based analysis of cooperative payload transport by robot collectives. M.S. Thesis, University at Buffalo, Buffalo, NY . Tang, C.P . and Krovi, V. 2004. Manipulability-based configuration evaluation of cooperative payload transport by by mobile mobile robot collectives. In Proceedings of the 2004 ASME Design Engineering Technical Conferences and Computers and Information in Engineering Conference , DETC2004-57476, Salt Lake City, UT, USA. Tanner, H.G., Kyriakopoulos, K.J., and Krikelis, N.I. 1998. Modeling of multiple mobile manipulators handling a common deformable object. Journal of Robotic Systems, 15(11):599, 15(11):599, 15(11):599––623. Wang, Z.-D., Nakano, E., and Matsukawa, T. 1994. Cooperating multiple behavior-based robots for object manipulation. In 1994 1994 IEEE/RSJ International Conference on Intelligent Robots and Systems . Whitney, Whitney, D.E. D.E. D.E. 1969. 1969. 1969. Resolved Resolved Resolved motion motion motion rate rate rate control control control of of of manipulators manipulators manipulators and and and human human human prostheses. prostheses. IEEE Transactions on Man-Machine Systems, MMS-10;47, MMS-10;47–53. Yamamoto, Y. 1994. Control and coordination of locomotion and manipulation of a wheeled mobile manipulator. Ph.D. Thesis, University of Pennsylvania, Philadelphia, PA. Yamamoto, Y . and Yun, X. 1994. Coordinating locomotion and manipulation of a mobile manipulator. IEEE Transactions on Automatic Control, 39(6):1326–1332. Footnotes 1.R indicates revolute joint. RRR indicates serial linkages connected by three revolute joints. 2.We denote “desired ” quantities using superscript d in the rest of the paper. 3.Reference robot variables are denoted using superscript r and actual robot variables without any superscript for the rest of the paper. 4.SolidWorks TM was the CAD package used for this work. 5.MSC Visual Nastran TM was the dynamic simulation environment used for this work. 。
机械手臂外文翻译
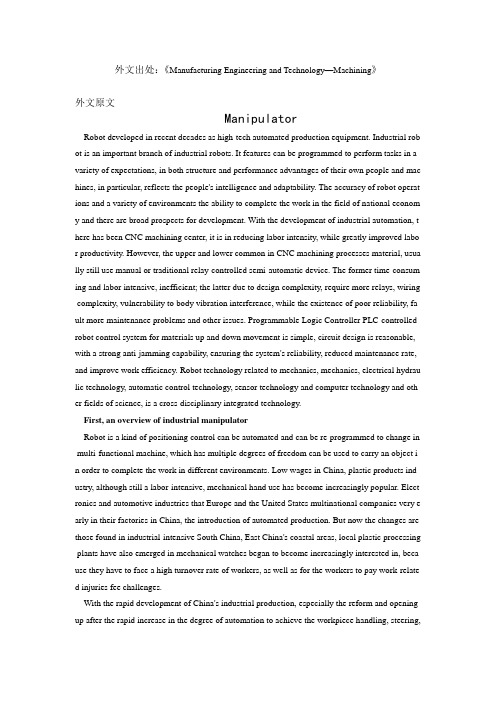
外文出处:《Manufacturing Engineering and Technology—Machining》外文原文ManipulatorRobot developed in recent decades as high-tech automated production equipment. Industrial rob ot is an important branch of industrial robots. It features can be programmed to perform tasks in a variety of expectations, in both structure and performance advantages of their own people and mac hines, in particular, reflects the people's intelligence and adaptability. The accuracy of robot operat ions and a variety of environments the ability to complete the work in the field of national econom y and there are broad prospects for development. With the development of industrial automation, t here has been CNC machining center, it is in reducing labor intensity, while greatly improved labo r productivity. However, the upper and lower common in CNC machining processes material, usua lly still use manual or traditional relay-controlled semi-automatic device. The former time-consum ing and labor intensive, inefficient; the latter due to design complexity, require more relays, wiring complexity, vulnerability to body vibration interference, while the existence of poor reliability, fa ult more maintenance problems and other issues. Programmable Logic Controller PLC-controlled robot control system for materials up and down movement is simple, circuit design is reasonable, with a strong anti-jamming capability, ensuring the system's reliability, reduced maintenance rate, and improve work efficiency. Robot technology related to mechanics, mechanics, electrical hydrau lic technology, automatic control technology, sensor technology and computer technology and oth er fields of science, is a cross-disciplinary integrated technology.First, an overview of industrial manipulatorRobot is a kind of positioning control can be automated and can be re-programmed to change in multi-functional machine, which has multiple degrees of freedom can be used to carry an object i n order to complete the work in different environments. Low wages in China, plastic products ind ustry, although still a labor-intensive, mechanical hand use has become increasingly popular. Elect ronics and automotive industries that Europe and the United States multinational companies very e arly in their factories in China, the introduction of automated production. But now the changes are those found in industrial-intensive South China, East China's coastal areas, local plastic processing plants have also emerged in mechanical watches began to become increasingly interested in, beca use they have to face a high turnover rate of workers, as well as for the workers to pay work-relate d injuries fee challenges.With the rapid development of China's industrial production, especially the reform and opening up after the rapid increase in the degree of automation to achieve the workpiece handling, steering,transmission or operation of brazing, spray gun, wrenches and other tools for processing and asse mbly operations since, which has more and more attracted our attention. Robot is to imitate the ma nual part of the action, according to a given program, track and requirements for automatic capture , handling or operation of the automatic mechanical devices.In real life, you will find this a problem. In the machine shop, the processing of parts loading ti me is not annoying, and labor productivity is not high, the cost of production major, and sometime s man-made incidents will occur, resulting in processing were injured. Think about what could rep lace it with the processing time of a tour as long as there are a few people, and can operate 24 hour s saturated human right? The answer is yes, but the robot can come to replace it.Production of mechanical hand can increase the automation level of production and labor produ ctivity; can reduce labor intensity, ensuring product quality, to achieve safe production; particularl y in the high-temperature, high pressure, low temperature, low pressure, dust, explosive, toxic and radioactive gases such as poor environment can replace the normal working people. Here I would l ike to think of designing a robot to be used in actual production.Why would a robot designed to provide a pneumatic power: pneumatic robot refers to the comp ressed air as power source-driven robot. With pressure-driven and other energy-driven comparison have the following advantages: 1. Air inexhaustible, used later discharged into the atmosphere, do es not require recycling and disposal, do not pollute the environment. (Concept of environmental p rotection) 2. Air stick is small, the pipeline pressure loss is small (typically less than asphalt gas pa th pressure drop of one-thousandth), to facilitate long-distance transport. 3. Compressed air of the working pressure is low (usually 4 to 8 kg / per square centimeter), and therefore moving the mate rial components and manufacturing accuracy requirements can be lowered. 4. With the hydraulic t ransmission, compared to its faster action and reaction, which is one of the advantages pneumatic outstanding. 5. The air cleaner media, it will not degenerate, not easy to plug the pipeline. But ther e are also places where it fly in the ointment: 1. As the compressibility of air, resulting in poor aer odynamic stability of the work, resulting in the implementing agencies as the precision of the velo city and not easily controlled. 2. As the use of low atmospheric pressure, the output power can not be too large; in order to increase the output power is bound to the structure of the entire pneumatic system size increased.With pneumatic drive and compare with other energy sources drive has the following advantage s:Air inexhaustible, used later discharged into the atmosphere, without recycling and disposal, do not pollute the environment. Accidental or a small amount of leakage would not be a serious impa ct on production. Viscosity of air is small, the pipeline pressure loss also is very small, easy long-distance transport.The lower working pressure of compressed air, pneumatic components and therefore the materi al and manufacturing accuracy requirements can be lowered. In general, reciprocating thrust in 1 t o 2 tons pneumatic economy is better.Compared with the hydraulic transmission, and its faster action and reaction, which is one of th e outstanding merits of pneumatic.Clean air medium, it will not degenerate, not easy to plug the pipeline. It can be safely used in fl ammable, explosive and the dust big occasions. Also easy to realize automatic overload protection. Second, the composition, mechanical handRobot in the form of a variety of forms, some relatively simple, some more complicated, but the basic form is the same as the composition of the , Usually by the implementing agencies, transmis sion systems, control systems and auxiliary devices composed.1.Implementing agenciesManipulator executing agency by the hands, wrists, arms, pillars. Hands are crawling institution s, is used to clamp and release the workpiece, and similar to human fingers, to complete the staffin g of similar actions. Wrist and fingers and the arm connecting the components can be up and down , left, and rotary movement. A simple mechanical hand can not wrist. Pillars used to support the ar m can also be made mobile as needed.2. TransmissionThe actuator to be achieved by the transmission system. Sub-transmission system commonly us ed manipulator mechanical transmission, hydraulic transmission, pneumatic and electric power tra nsmission and other drive several forms.3. Control SystemManipulator control system's main role is to control the robot according to certain procedures, d irection, position, speed of action, a simple mechanical hand is generally not set up a dedicated co ntrol system, using only trip switches, relays, control valves and circuits can be achieved dynamic drive system control, so that implementing agencies according to the requirements of action. Actio n will have to use complex programmable robot controller, the micro-computer control.Three, mechanical hand classification and characteristicsRobots are generally divided into three categories: the first is the general machinery does not re quire manual hand. It is an independent not affiliated with a particular host device. It can be progra mmed according to the needs of the task to complete the operation of the provisions. It is character ized with ordinary mechanical performance, also has general machinery, memory, intelligence tern ary machinery. The second category is the need to manually do it, called the operation of aircraft. It originated in the atom, military industry, first through the operation of machines to complete a pa rticular job, and later developed to operate using radio signals to carry out detecting machines suc h as the Moon. Used in industrial manipulator also fall into this category. The third category is ded icated manipulator, the main subsidiary of the automatic machines or automatic lines, to solve the machine up and down the workpiece material and delivery. This mechanical hand in foreign count ries known as the "Mechanical Hand", which is the host of services, from the host-driven; excepti on of a few outside the working procedures are generally fixed, and therefore special.Main features:First, mechanical hand (the upper and lower material robot, assembly robot, handling robot, stac king robot, help robot, vacuum handling machines, vacuum suction crane, labor-saving spreader, p neumatic balancer, etc.).Second, cantilever cranes (cantilever crane, electric chain hoist crane, air balance the hanging, e tc.)Third, rail-type transport system (hanging rail, light rail, single girder cranes, double-beam cran e)Four, industrial machinery, application of handManipulator in the mechanization and automation of the production process developed a new ty pe of device. In recent years, as electronic technology, especially computer extensive use of robot development and production of high-tech fields has become a rapidly developed a new technology , which further promoted the development of robot, allowing robot to better achieved with the com bination of mechanization and automation.Although the robot is not as flexible as staff, but it has to the continuous duplication of work an d labor, I do not know fatigue, not afraid of danger, the power snatch weight characteristics when compared with manual large, therefore, mechanical hand has been of great importance to many se ctors, and increasingly has been applied widely, for example:(1) Machining the workpiece loading and unloading, especially in the automatic lathe, combinat ion machine tool use is more common.(2) In the assembly operations are widely used in the electronics industry, it can be used to asse mble printed circuit boards, in the machinery industry It can be used to assemble parts and compo nents.(3) The working conditions may be poor, monotonous, repetitive easy to sub-fatigue working e nvironment to replace human labor.(4) May be in dangerous situations, such as military goods handling, dangerous goods and haza rdous materials removal and so on..(5) Universe and ocean development.(6), military engineering and biomedical research and testing.Help mechanical hands: also known as the balancer, balance suspended, labor-saving spreader, ma nual Transfer machine is a kind of weightlessness of manual load system, a novel, time-saving tec hnology for material handling operations booster equipment, belonging to kinds of non-standard d esign of series products. Customer application needs, creating customized cases. Manual operation of a simulation of the automatic machinery, it can be a fixed program draws ﹑ handling objects o r perform household tools to accomplish certain specific actions. Application of robot can replace t he people engaged in monotonous ﹑ repetitive or heavy manual labor, the mechanization and aut omation of production, instead of people in hazardous environments manual operation, improving working conditions and ensure personal safety. The late 20th century, 40, the United States atomic energy experiments, the first use of radioactive material handling robot, human robot in a safe roo m to manipulate various operations and experimentation. 50 years later, manipulator and gradually extended to industrial production sector, for the temperatures, polluted areas, and loading and unl oading to take place the work piece material, but also as an auxiliary device in automatic machine tools, machine tools, automatic production lines and processing center applications, the completio n of the upper and lower material, or From the library take place knife knife and so on according t o fixed procedures for the replacement operation. Robot body mainly by the hand and sports instit utions. Agencies with the use of hands and operation of objects of different occasions, often there are clamping ﹑ support and adsorption type of care. Movement organs are generally hydraulic pn eumatic ﹑﹑ electrical device drivers. Manipulator can be achieved independently retractable ﹑rotation and lifting movements, generally 2 to 3 degrees of freedom. Robots are widely used in me tallurgical industry, machinery manufacture, light industry and atomic energy sectors.Can mimic some of the staff and arm motor function, a fixd procedure for the capture, handling objects or operating tools, automatic operation device. It can replace human labor in order to achie ve the production of heavy mechanization and automation that can operate in hazardous environm ents to protect the personal safety, which is widely used in machinery manufacturing, metallurgy, e lectronics, light industry and nuclear power sectors. Mechanical hand tools or other equipment co mmonly used for additional devices, such as the automatic machines or automatic production line handling and transmission of the workpiece, the replacement of cutting tools in machining centers, etc. generally do not have a separate control device. Some operating devices require direct manip ulation by humans; such as the atomic energy sector performs household hazardous materials used in the master-slave manipulator is also often referred to as mechanical hand.Manipulator mainly by hand and sports institutions. Task of hand is holding the workpiece (or tool) components, according to grasping objects by shape, size, weight, material and operational re quirements of a variety of structural forms, such as clamp type, type and adsorption-based care suc h as holding. Sports organizations, so that the completion of a variety of hand rotation (swing), mo bile or compound movements to achieve the required action, to change the location of objects by g rasping and posture.Robot is the automated production of a kind used in the process of crawling and moving piece f eatures automatic device, which is mechanized and automated production process developed a ne w type of device. In recent years, as electronic technology, especially computer extensive use of ro bot development and production of high-tech fields has become a rapidly developed a new technol ogy, which further promoted the development of robot, allowing robot to better achieved with the combination of mechanization and automation. Robot can replace humans completed the risk of d uplication of boring work, to reduce human labor intensity and improve labor productivity. Manip ulator has been applied more and more widely, in the machinery industry, it can be used for parts a ssembly, work piece handling, loading and unloading, particularly in the automation of CNC mach ine tools, modular machine tools more commonly used. At present, the robot has developed into a FMS flexible manufacturing systems and flexible manufacturing cell in an important component o f the FMC. The machine tool equipment and machinery in hand together constitute a flexible man ufacturing system or a flexible manufacturing cell, it was adapted to small and medium volume pr oduction, you can save a huge amount of the work piece conveyor device, compact, and adaptable. When the work piece changes, flexible production system is very easy to change will help enterpr ises to continuously update the marketable variety, improve product quality, and better adapt to ma rket competition. At present, China's industrial robot technology and its engineering application le vel and comparable to foreign countries there is a certain distance, application and industrializatio n of the size of the low level of robot research and development of a direct impact on raising the le vel of automation in China, from the economy, technical considerations are very necessary. Theref ore, the study of mechanical hand design is very meaningful.外文资料翻译译文机械手机械手是近几十年发展起来的一种高科技自动化生产设备。
机械【经典外文翻译】-手臂可调式捆包打结器(译文+英文)-毕业论文

1Bale twine knotter with adjustable wiperBackground of the inventionThis invention relates to twine knotters for hay or straw baling machines and more particularly to an improved wiper arm for such knotters.In one conventional baler, the twine knotter includes a rotatably mounted billhook for forming a loop of twine thereabout. On one side of the billhook is a wiper arm which has a pair of finers defining a fork for receiving and guiding twine used to tie a bale. On one side of the billhook is a knife riveted to the fork for cutting the twine after a loop in the twine has been formed around the billhook. A wiper is formed integrally with the fork of the arm and strips or wipers the loop of twine form around the billhook as the severed end of the twine is held in the billhook jaw.Proper adjustment of the wiper arm relative to the billhook is critical to the operation of the nkotter as the wiper must strip or wipe the twine loop from the billhook to complete the formation of the knot. Wiper arm adjustment is performed initially at the point of manufacture and periodically thereafter when servicing the baler. It is accomplished by modeling or bending the arm in three areas with a special tool. By modeling, the wiper is centered with respect to the heel of the billhook and adjusted so theat it just clears the billhook jaw. For this reason, it is desirable that the wiper arm be relatively rigid and unyielding so that proper adjustment can be maintained and yet be sufficiently bendable to permit initial adjustmen. Also, in recent years , stronger twines are being used on such balers to tie bales of higher density. Such changes subject the wiper arm to higher forces during operation thus making it more difficult to maintain the arm in proper adjustmen, while at the same time, making the arm flexible enough to permit initial adjustment.Accordingly, it is an object of this invention to provide a knotter with an improved wiper arm having a strong and rigid construction to maintain an accurate adjustmen.Another object of this invention is to provide a knotter with a wiper arm which has a wiper which is easily and accurately adjustable with respect to the billhook of the knotter.SUMMARY OF THE INVENTIONThese and other objects of the invention are accomplished by knotter comprising a rotatably mounted billhook for forming a loop of twine thereabout and a wiper arm with an improved adjustably mounted wiper for sliding a twine loop form the billhook while the twine end is retained in a jaw of the billhook to complete the formation of a weine knot. In one embodiment, the wiper has slots formed teerein and is adjustably mounted on the arm and relative to the billhook by screws inserted through the slots and thereadably mounted in the arm. In a second embodiment, the wiper has first and second portions joined together at a right angle and is asjustably mounted relative to the arm and to the billhook of the knotter by the insertion and removal of shims between the second portion of the wiper and the arm.2Brief description of the drawingsFIG. 1 is a fragmentary perpective view of a twine knotter in accordance with a preferred embodiment of this invention.FIG. 2 is an esploded view of a wiper arm of the kontter shown in FIG.1FIG. 3 is a view of the knotter of FIG.1 taken along line 3—3.FIG. 4 is a fragmentary perspective view of a knotter wiper arm in accordance with a second embodiment of this invention.FIG. 5--9 are fragmentary perspective views pf a knotter of FIG.1 showing progressive stages of knot tying.Description of the preferred embodimentsFIGS.1—3 show in fragmentary form a knotter 1 in accordance with the preferrde embodiment of this invention. Knotters of this general type are well knowen in the art and are widely used commercially, such as in the John Deere 466 Series balers sole by John Deere Company, a corporation of Delaware. Such balers are used for the baling of hay or straw into a rectangular parallelpiped shaped bale.Knotter 1 comprises a billhook 13 including (1) a center shaft 3on which billhook 13 is rotatably mounted in a knotter frame 5 and (2) a jaw 14 around which a loop of twine is formed as rotated and for retaining the twine end during knot formation. On one said of billhook 13 a twine disk 15 and a twine holder 16 are provided for holding a segment of twine 19. On the opposite side and below billhook 13, a wiper arm 17 is provided.Wiper arm 17 (FIGS.1,2) includes a twine guiding fork 20 preferably of cast iron,a knife blade 24 bolted to fork 20 cutting the twine and a wiper 21 for removing a loop of twine 19 from billhook 13.Fork 20 consists of a pair of fingers 22,23 between which twine 19 is received and guided and a vertex 25 at which fingers 22,23 are joined. One side of certex 25 has a boss 25 with a pair of threaded apertures 29,31 and th which wiper 21 is adjustably mounted. Fork 20 may be formed either by casting or forging and therefore is a strong, rigid component.Wiper 21, preferably of case hardened steel, is platelike and has a pair of slots 33, 35 corresponding in spacing to the threaded apertures 29,31 of boss 25. The profile of wiper 21 is conventional and has an arcuate recess or ledge 37. Wiper 21 is detachably mounted to fork 20 by a pair of screws 39,41 which pass through slots 33,35 and threadably engage apertues 29,31 so that fork 20 and wiper 21 are held tightly toghter. Wiper 21 is asjustable relative to fork 20 by moving wiper 21 back and forth in a plane parallel to the major planes of wiper 21 and in a direction parallel to the direction of elongation of slots 33,35 when screws 39,41 are loosened. Referring now to FIG. 3, wiper 21 is positioned closely to billhook 13 which ledge or recess 37 centered in relation to an outer surface or heel 43 of jaw 14. The maximum recommended clearance between a first portion 43 of jaw 14 and ledge 37 is 2.4.mm.. at the closest distance which jaw portion 45 approaches during rotation of billhook 13 during the formation of a twine knot.In contrast to the conventional integral wiper arm described in the Background of the Invention which requires modeling or bending of the wiper arm at positions corresponding to positions A,B and C shown in FIG. 2 in order to adjust the wiper with respect to the billhook for proper stripping of a twine loop from the billhook, the present embodiment of the invention achieves alignment simply and easily by adjustment of wiper 21 by loosening of screws 39,41 and sliding platelike wiper 21 back and forth. This permits fork 20 and wiper 21 to be deformable in use.In accordance with the features of a second embodiment of this invention, FIG. 4 shows a vertex 51 of a wiper arm 53 identical to wiper arm 17 except for the portion shown and descrobed in FIG.4. shows a vertex 51 of a wiper arm 53 identical to wiper arm 17 except for the portion shown and described in FIG. 4. Wper arm 53 portion shown and described in FIG. 4. Wper arm 53includes awiper 55 having first and second portions 57, 59 joined together at a right angle.Wiper 55 is adjustably mounted to a major surface 61 of vertex 51 by an attachment means 63,here shown as a pair of bolts(only one of which—bolt 65—is visble in FIG.4)inserted through aperture 67, 69 in wiper 55 and vertex 51, respectively. Adjustment pof the height of a ledge 71 of wiper 55 above surface 61 is accomplished by the insertion and removal of shim means 73 inserted on bolt 65 between surface 61 and second portion 59 of wiper 55. Shim means 73 is here shown as a plurality of washers.The functionng of knotter 1 for tying twine around a bale of hay is conventional and will be described herein only briefly. Particular reference is made to FIG.1 and FIGS.5—9 which show the progressive stages of knot formation.FIG.1 shows the condition when a needle 75 (showm in FIG.5) is threaded with twine 10 stored in a twine box (not shown) and from a prior cycle, one end of twine 19 is held in twine disk 15 by twine holder 16. Twine 19 is threaded through fork 20 between fingers 22,23 and ocer the top of bale 77. As bale 77 is formed and moves against twine 19,twine 19 is extended across the outer surface of bale 77 by pulling more twine from the twine box. As shown in FIG.5,when bale 77 reaches a predetermined length, a measuring wheel(not shown) activates kontter 1; and needle 75(with the help of a tucker finger, not shown) brings a second steand of twine 19 from below and around the trailing end of bale 77, through fork 20, across billhook 13 and into twine disk 15. In FIG.6, disk 15 is then turned (counterclockwise) sufficiently to permit twine holder 16 to secure both strands of twine 19 n disk 15 and billhook 13 starts to revolve. The turning of billhook 13(FIG.7) causes a loop 78 of twine 19 to be formde around the exteriof surface of billhook 13, and jaw 14 is opened to receive twine 19. wiper arm 17(FIG.7) is moved, thereby advancing knife 24 against twine 19 to cue twine 19 helld in disk 15 for the formation of the next knot in the next knotter cycle. Jaw 14 (FIG.8) is closed and holds the ends of twine 19 tighely. Further movement of wiper arm 17 causes wiper 21 to push or wipe the twine loop 78 from billhook 13 as jaw 14 holds the two cut1手臂可调式捆包打结器发明背景这项捆绳打结器的发明和割草机有关,更特别的是为打结机器改良了手臂装置。
机械手外文翻译(英)
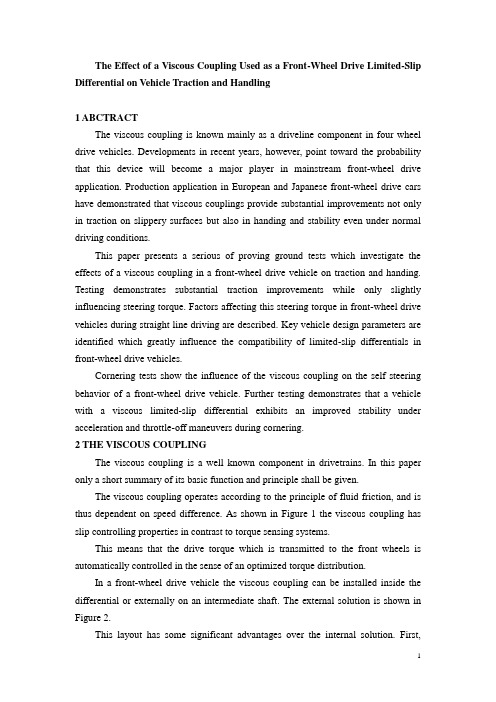
The Effect of a Viscous Coupling Used as a Front-Wheel Drive Limited-Slip Differential on Vehicle Traction and Handling1 ABCTRACTThe viscous coupling is known mainly as a driveline component in four wheel drive vehicles. Developments in recent years, however, point toward the probability that this device will become a major player in mainstream front-wheel drive application. Production application in European and Japanese front-wheel drive cars have demonstrated that viscous couplings provide substantial improvements not only in traction on slippery surfaces but also in handing and stability even under normal driving conditions.This paper presents a serious of proving ground tests which investigate the effects of a viscous coupling in a front-wheel drive vehicle on traction and handing. Testing demonstrates substantial traction improvements while only slightly influencing steering torque. Factors affecting this steering torque in front-wheel drive vehicles during straight line driving are described. Key vehicle design parameters are identified which greatly influence the compatibility of limited-slip differentials in front-wheel drive vehicles.Cornering tests show the influence of the viscous coupling on the self steering behavior of a front-wheel drive vehicle. Further testing demonstrates that a vehicle with a viscous limited-slip differential exhibits an improved stability under acceleration and throttle-off maneuvers during cornering.2 THE VISCOUS COUPLINGThe viscous coupling is a well known component in drivetrains. In this paper only a short summary of its basic function and principle shall be given.The viscous coupling operates according to the principle of fluid friction, and is thus dependent on speed difference. As shown in Figure 1 the viscous coupling has slip controlling properties in contrast to torque sensing systems.This means that the drive torque which is transmitted to the front wheels is automatically controlled in the sense of an optimized torque distribution.In a front-wheel drive vehicle the viscous coupling can be installed inside the differential or externally on an intermediate shaft. The external solution is shown in Figure 2.This layout has some significant advantages over the internal solution. First,there is usually enough space available in the area of the intermediate shaft to provide the required viscous characteristic. This is in contrast to the limited space left in today’s front-axle differentials. Further, only minimal modification to the differential carrier and transmission case is required. In-house production of differentials is thus only slightly affected. Introduction as an option can be made easily especially when the shaft and the viscous unit is supplied as a complete unit. Finally, the intermediate shaft makes it possible to provide for sideshafts of equal length with transversely installed engines which is important to reduce torque steer (shown later in section 4).This special design also gives a good possibility for significant weight and cost reductions of the viscous unit. GKN Viscodrive is developing a low weight and cost viscous coupling. By using only two standardized outer diameters, standardized plates, plastic hubs and extruded material for the housing which can easily be cut to different lengths, it is possible to utilize a wide range of viscous characteristics. An example of this development is shown in Figure 3.3 TRACTION EFFECTSAs a torque balancing device, an open differential provides equal tractive effort to both driving wheels. It allows each wheel to rotate at different speeds during cornering without torsional wind-up. These characteristics, however, can be disadvantageous when adhesion variations between the left and right sides of the road surface (split-μ) limits the torque transmitted for both wheels to that which can be supported by the low-μwheel.With a viscous limited-slip differential, it is possible to utilize the higher adhesion potential of the wheel on the high-μsurface. This is schematically shown in Figure 4.When for example, the maximum transmittable torque for one wheel is exceeded on a split-μsurface or during cornering with high lateral acceleration, a speed difference between the two driving wheels occurs. The resulting self-locking torque in the viscous coupling resists any further increase in speed difference and transmits the appropriate torque to the wheel with the better traction potential.It can be seen in Figure 4 that the difference in the tractive forces results in a yawing moment which tries to turn the vehicle in to the low-μside, To keep the vehicle in a straight line the driver has to compensate this with opposite steering input. Though the fluid-friction principle of the viscous coupling and the resulting softtransition from open to locking action, this is easily possible, The appropriate results obtained from vehicle tests are shown in Figure 5.Reported are the average steering-wheel torque Ts and the average corrective opposite steering input required to maintain a straight course during acceleration on a split-μtrack with an open and a viscous differential. The differences between the values with the open differential and those with the viscous coupling are relatively large in comparison to each other. However, they are small in absolute terms. Subjectively, the steering influence is nearly unnoticeable. The torque steer is also influenced by several kinematic parameters which will be explained in the next section of this paper.4 FACTORS AFFECTING STEERING TORQUEAs shown in Figure 6 the tractive forces lead to an increase in the toe-in response per wheel. For differing tractive forces, Which appear when accelerating on split-μwith limited-slip differentials, the toe-in response changes per wheel are also different.Unfortunately, this effect leads to an undesirable turn-in response to the low-μside, i.e. the same yaw direction as caused by the difference in the tractive forces.Reduced toe-in elasticity is thus an essential requirement for the successful front-axle application of a viscous limited-slip differential as well as any other type of limited-slip differential.Generally the following equations apply to the driving forces on a wheelμV T F F =With =T F Tractive Force=V F Vertical Wheel Load=μUtilized Adhesion CoefficientThese driving forces result in steering torque at each wheel via the wheel disturbance level arm “e ” and a steering torque difference between the wheels given by the equation:△e T =()lo H hi H F F e ---∙∙δcosWhere △=e T Steering Torque Differencee=Wheel Disturbance Level Arm=δKing Pin Anglehi=high-μside subscriptlo=low-μside subscriptIn the case of front-wheel drive vehicles with open differentials, △Ts is almost unnoticeable, since the torque bias (lo H hi T F F --/) is no more than 1.35.For applications with limited-slip differentials, however, the influence is significant. Thus the wheel disturbance lever arm e should be as small as possible. Differing wheel loads also lead to an increase in △Te so the difference should also be as small as possible.When torque is transmitted by an articulated CV-Joint, on the drive side (subscript 1) and the driven side (subscript 2),differing secondary moments are produced that must have a reaction in a vertical plane relative to the plane of articulation. The magnitude and direction of the secondary moments (M) are calculated as follows (see Figure 8):Drive side M1 =v v T T ββηtan /)2/tan(2-∙Driven side M2 =v v T T ββηtan /)2/tan(2+∙With T2 =dyn T r F ∙ηT =()system Jo T f int ,,2βWhere v β∧=Vertical Articulation Angleβ∧=Resulting Articulation Angled y n r ∧=Dynamic Wheel RadiusηT ∧=Average Torque LossThe component δcos 2∙M acts around the king-pin axis (see figure 7) as a steering torque per wheel and as a steering torque difference between the wheels as follows: ])tan /2/tan ()sin /2/tan [(cos 22li w hi w T T T T T ----+±=∆νηννηνβββββδ where ∧=∆βT Steering Torque DifferenceW ∧=Wheel side subscriptIt is therefore apparent that not only differing driving torque but also differingarticulations caused by various driveshaft lengths are also a factor. Referring to the moment-polygon in Figure 7, the rotational direction of M2 or βT respectively change, depending on the position of the wheel-center to the gearbox output.For the normal position of the halfshaft shown in Figure 7(wheel-center below the gearbox output joint) the secondary moments work in the same rotational direction as the driving forces. For a modified suspension layout (wheel-center above gearbox output joint, i.e. v βnegative) the secondary moments counteract the moments caused by the driving forces. Thus for good compatibility of the front axle with a limited-slip differential, the design requires: 1) vertical bending angles which are centered around 0=v βor negative (0<v β) with same values of v βon both left and right sides; and 2) sideshafts of equal length.The influence of the secondary moments on the steering is not only limited to the direct reactions described above. Indirect reactions from the connection shaft between the wheel-side and the gearbox-side joint can also arise, as shown below:Figure 9: Indirect Reactions Generated by Halfshaft Articulation in the Vertical PlaneFor transmission of torque without loss and vd vw ββ= both of the secondary moments acting on the connection shaft compensate each other. In reality (with torque loss), however, a secondary moment difference appears:△W D DW M M M 12-=With -+=ηT T T W D 22The secondary moment difference is: =D W M ()VW W VW W VD VD W T T D T w T T ββββηηηtan /2/tan sin /tan 22/2+-++For reasons of simplification it apply that V VW VD βββ==and ηηηT T T W D == to give △()V V V D W T M βββηtan /1sin /12/tan ++∙=△DW M requires opposing reaction forces on both joints where L M F D W D W /∆=. Due to the joint disturbance lever arm f, a further steering torque also acts around the king-pin axis:L f M T D W f /cos δ∙∙∆=()lo lo D W hi hi D W f L M L M f T //cos ---∙∙=∆Where ∧=f T Steering Torque per Wheel∧=∆f T Steering Torque Difference∧=f Joint Disturbance Lever∧=L Connection shaft (halfshaft) LengthFor small values of f, which should be ideally zero, f T ∆ is of minor influence.5.EFFECT ON CORNERINGViscous couplings also provide a self-locking torque when cornering, due to speed differences between the driving wheels. During steady state cornering, as shown in figure 10, the slower inside wheel tends to be additionally driven through the viscous coupling by the outside wheel.Figure 10: Tractive forces for a front-wheel drive vehicle during steady state corneringThe difference between the Tractive forces Dfr and Dfl results in a yaw moment MCOG , which has to be compensated by a higher lateral force, and hence a larger slip angle af at the front axle. Thus the influence of a viscous coupling in a front-wheel drive vehicle on self-steering tends towards an understeering characteristic. This behavior is totally consistent with the handling bias of modern vehicles which all under steer during steady state cornering maneuvers. Appropriate test results are shown in figure 11.Figure 11: comparison between vehicles fitted with an open differential and viscous coupling during steady state cornering.The asymmetric distribution of the tractive forces during cornering as shown in figure 10 improves also the straight-line running. Every deviation from the straight-line position causes the wheels to roll on slightly different radii. The difference between the driving forces and the resulting yaw moment tries to restore the vehicle to straight-line running again (see figure 10).Although these directional deviations result in only small differences in wheel travel radii, the rotational differences especially at high speeds are large enough for a viscous coupling front differential to bring improvements in straight-line running.High powered front-wheel drive vehicles fitted with open differentials often spintheir inside wheels when accelerating out of tight corners in low gear. In vehicles fitted with limited-slip viscous differentials, this spinning is limited and the torque generated by the speed difference between the wheels provides additional tractive effort for the outside driving wheel. this is shown in figure 12Figure 12: tractive forces for a front-wheel drive vehicle with viscous limited-slip differential during acceleration in a bendThe acceleration capacity is thus improved, particularly when turning or accelerating out of a T-junction maneuver ( i.e. accelerating from a stopped position at a “T” intersection-right or left turn ).Figures 13 and 14 show the results of acceleration tests during steady state cornering with an open differential and with viscous limited-slip differential .Figure 13: acceleration characteristics for a front-wheel drive vehicle with an open differential on wet asphalt at a radius of 40m (fixed steering wheel angle throughout test).Figure 14: Acceleration Characteristics for a Front-Wheel Drive Vehicle with Viscous Coupling on Wet Asphalt at a Radius of 40m (Fixed steering wheel angle throughout test)The vehicle with an open differential achieves an average acceleration of 2.0 2/sm while them(limited by/s vehicle with the viscous coupling reaches an average of 2.3 2engine-power). In these tests, the maximum speed difference, caused by spinning of the inside driven wheel was reduced from 240 rpm with open differential to 100 rpm with the viscous coupling.During acceleration in a bend, front-wheel drive vehicles in general tend to understeer more than when running at a steady speed. The reason for this is the reduction of the potential to transmit lateral forces at the front-tires due to weight transfer to the rear wheels and increased longitudinal forces at the driving wheels. In an open loop control-circle-test this can be seen in the drop of the yawing speed (yaw rate) after starting to accelerate (Time 0 in Figure 13 and 14). It can also be taken from Figure 13 and Figure 14 that the yaw rate of the vehicle with the open differential falls-off more rapidly than for the vehicle with the viscous coupling starting to accelerate. Approximately 2 seconds after starting to accelerate, however, the yaw rate fall-off gradient of the viscous-coupled vehicle increases more than at thevehicle with open differential.The vehicle with the limited slip front differential thus has a more stable initial reaction under accelerating during cornering than the vehicle with the open differential, reducing its understeer. This is due to the higher slip at the inside driving wheel causing an increase in driving force through the viscous coupling to the outside wheel, which is illustrated in Figure 12. the imbalance in the front wheel tractive forces results in a yaw momentM acting in direction of the turn, countering theCSDundersteer.When the adhesion limits of the driving wheels are exceed, the vehicle with the viscous coupling understeers more noticeably than the vehicle with the open differential (here, 2 seconds after starting to accelerate). On very low friction surfaces, such as snow or ice, stronger understeer is to be expected when accelerating in a curve with a limited slip differential because the driving wheels-connected through the viscous coupling-can be made to spin more easily (power-under-steering). This characteristic can, however, be easily controlied by the driver or by an automatic throttle modulating traction control system. Under these conditions a much easier to control than a rear-wheel drive car. Which can exhibit power-oversteering when accelerating during cornering. All things, considered, the advantage through the stabilized acceleration behavior of a viscous coupling equipped vehicle during acceleration the small disadvantage on slippery surfaces.Throttle-off reactions during cornering, caused by releasing the accelerator suddenly, usually result in a front-wheel drive vehicle turning into the turn (throttle-off oversteering ). High-powered modeles which can reach high lateral accelerations show the heaviest reactions. This throttle-off reaction has several causes such as kinematic influence, or as the vehicle attempting to travel on a smaller cornering radius with reducing speed. The essential reason, however, is the dynamic weight transfer from the rear to the front axle, which results in reduced slip-angles on the front and increased slip-angles on the rear wheels. Because the rear wheels are not transmitting driving torque, the influence on the rear axle in this case is greater than that of the front axle. The driving forces on the front wheels before throttle-off (see Figure 10) become over running or braking forces afterwards, which is illustrated for the viscous equipped vehicle in Figure 15.Figure 15:Baraking Forces for a Front-Wheel Drive Vehicle with ViscousLimited-Slip Differential Immediately after a Throttle-off Maneuver While CorneringAs the inner wheel continued to turn more slowly than the outer wheel, the viscous coupling provides the outer wheel with the larger braking force f B . The force difference between the front-wheels applied around the center of gravity of the vehicle causes a yaw moment G C M 0 that counteracts the normal turn-in reaction.When cornering behavior during a throttle-off maneuver is compared for vehicles with open differentials and viscous couplings, as shown in Figure 16 and 17, the speed difference between the two driving wheels is reduced with a viscous differential.Figure 16: Throttle-off Characteristics for a Front-Wheel Drive Vehicle with an open Differential on Wet Asphalt at a Radius of 40m (Open Loop)Figure 17:Throttle-off Characteristics for a Front-Wheel Drive Vehicle with Viscous Coupling on Wet Asphalt at a Radius of 40m (Open Loop)The yawing speed (yaw rate), and the relative yawing angle (in addition to the yaw angle which the vehicle would have maintained in case of continued steady state cornering) show a pronounced increase after throttle-off (Time=0 seconds in Figure 14 and 15) with the open differential. Both the sudden increase of the yaw rate after throttle-off and also the increase of the relative yaw angle are significantly reduced in the vehicle equipped with a viscous limited-slip differential.A normal driver os a front-wheel drive vehicle is usually only accustomed to neutral and understeering vehicle handing behavior, the driver can then be surprised by sudden and forceful oversteering reaction after an abrupt release of the throttle, for example in a bend with decreasing radius. This vehicle reaction is further worsened if the driver over-corrects for the situation. Accidents where cars leave the road to the inner side of the curve is proof of this occurrence. Hence the viscous coupling improves the throttle-off behavior while remaining controllable, predictable, and safer for an average driver.6. EFFECT ON BRAKINGThe viscous coupling in a front-wheel drive vehicle without ABS (anti-lock braking system) has only a very small influence on the braking behavior on split-μ surfaces. Hence the front-wheels are connected partially via the front-wheel on the low-μ side is slightly higher than in an vehicle with an open differential. On the other side ,the brake pressure to lock the front-wheel on the high-μ side is slightlylower. These differences can be measured in an instrumented test vehicle but are hardly noticeable in a subjective assessment. The locking sequence of front and rear axle is not influenced by the viscous coupling.Most ABS offered today have individual control of each front wheel. Electronic ABS in front-wheel drive vehicles must allow for the considerable differences in effective wheel inertia between braking with the clutch engaged and disengaged.Partial coupling of the front wheels through the viscous unit does not therefore compromise the action of the ABS - a fact that has been confirmed by numerous tests and by several independent car manufacturers. The one theoretical exception to this occurs on a split-μ—surface if a yaw moment build-up delay or Yaw Moment Reduction(YMR) is included in the ABS control unit. Figure 18 shows typical brake pressure sequences, with and without YMR.figure 18: brake pressure build-up characteristics for the front brakes of a vehicle braking on split-μwith ABS.In vehicles with low yaw inertia and a short wheelbase, the yaw moment build-up can be delayed to allow an average driver enough reaction time by slowing the brake pressure build-up over the ABS for the high-μwheel. The wheel on the surface with the higher friction coefficient is therefore, particularly at the beginning of braking, under-braked and runs with less slip. The low-μwheel, in contrast, can at the same time have a very high slip, which results in a speed difference across the viscous differential. The resulting self-locking torque then appears as an extra braking force at the high-μwheel which counteracts the YMR.Although this might be considered as a negative effect and can easily be corrected when setting the YMR algorithm for a vehicle with a front viscous coupling, vehicle tests have proved that the influence is so slight that no special development of new ABS/YMR algorithms are actually needed. Some typical averaged test results are summarized in Figure 19.figure 19 : results form ABS braking tests with YMR on split-μ(V o=50 mph, 3rd Gear, closed loop ) in figure 19 on the left a comparison of the maximum speed difference which occurred in the first ABS control cycle during braking is shown. It is obvious that the viscous coupling is reducing this speed difference. As the viscous coupling counteracts the YMR, the required steering wheel angle to keep the vehicle in straight direction in the first second of braking increased from 39°to 51°(figure 19,middle). Since most vehicle and ABS manufacturers consider 90°to be the critical limit, this can be tolerated. Finally, as the self-locking torque produced by the viscous coupling causes an increase in high-µ. Wheel braking force, a slightly higher vehicle deceleration was maintained(figure 19,right).7 SUMMARYin conclusion,it can be established that the application of a viscous coupling in a front-axle differential. It also positively influences the complete vehicle handling and stability , with only slight, but acceptable influence on torques-steer.To reduce unwanted torque-steer effects a basic set of design rules have been established:●Toe-in response due to longitudinal load change must be as small as possible .●Distance between king-pin axis and wheel center has to be as small as possible.●Vertical bending angle-rang should be centered around zero(or negative).●vertical bending angles should be the same for both sides.●Sideshafts should be of equal length.Of minor influence on torque-steer is the joint disturbance lever arm which should be ideally zero for other reasons anyway. Braking with and without ABS is only negligibly influenced by the viscous coupling. Traction is significantly improved by the viscous limited slip differential in a front-wheel drive vehicle.The self-steering behavior of a front-wheel drive vehicle is slightly influenced by a viscous limited slip differential in the direction of understeer. The improved reactions to throttle-off and acceleration during cornering make a vehicle with viscous coupling in the front-axle considerably more stable, more predictable and therefore safer.11。
机械手外文翻译
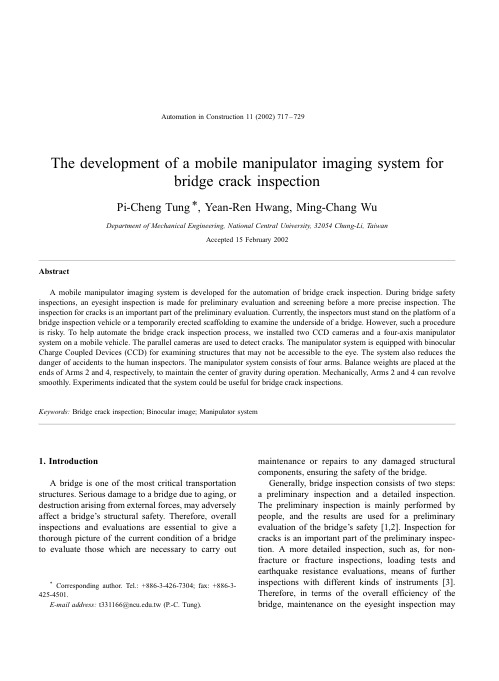
The development of a mobile manipulator imaging system forbridge crack inspectionPi-Cheng Tung*,Yean-Ren Hwang,Ming-Chang WuDepartment of Mechanical Engineering,National Central University,32054Chung-Li,TaiwanAccepted15February2002AbstractA mobile manipulator imaging system is developed for the automation of bridge crack inspection.During bridge safety inspections,an eyesight inspection is made for preliminary evaluation and screening before a more precise inspection.The inspection for cracks is an important part of the preliminary evaluation.Currently,the inspectors must stand on the platform of a bridge inspection vehicle or a temporarily erected scaffolding to examine the underside of a bridge.However,such a procedure is risky.To help automate the bridge crack inspection process,we installed two CCD cameras and a four-axis manipulator system on a mobile vehicle.The parallel cameras are used to detect cracks.The manipulator system is equipped with binocular Charge Coupled Devices(CCD)for examining structures that may not be accessible to the eye.The system also reduces the danger of accidents to the human inspectors.The manipulator system consists of four arms.Balance weights are placed at the ends of Arms2and4,respectively,to maintain the center of gravity during operation.Mechanically,Arms2and4can revolve smoothly.Experiments indicated that the system could be useful for bridge crack inspections.Keywords:Bridge crack inspection;Binocular image;Manipulator system1.IntroductionA bridge is one of the most critical transportation structures.Serious damage to a bridge due to aging,or destruction arising from external forces,may adversely affect a bridge’s structural safety.Therefore,overall inspections and evaluations are essential to give a thorough picture of the current condition of a bridge to evaluate those which are necessary to carry out maintenance or repairs to any damaged structural components,ensuring the safety of the bridge.Generally,bridge inspection consists of two steps: a preliminary inspection and a detailed inspection. The preliminary inspection is mainly performed by people,and the results are used for a preliminary evaluation of the bridge’s safety[1,2].Inspection for cracks is an important part of the preliminary inspec-tion.A more detailed inspection,such as,for non-fracture or fracture inspections,loading tests and earthquake resistance evaluations,means of further inspections with different kinds of instruments[3]. Therefore,in terms of the overall efficiency of the bridge,maintenance on the eyesight inspection may*Corresponding author.Tel.:+886-3-426-7304;fax:+886-3-425-4501.E-mail address:t331166@.tw(P.-C.Tung).Automation in Construction11(2002)717–729discover damage to a bridge’s structure earlier,ena-bling the problem and the extent of the damage to be roughly estimated in advance.The information obtained from an eyesight inspection can then be used as a preliminary evaluation basis for screening before further inspection with instruments is made.There are some major advantages to the eyesight inspection of a bridge,i.e.it is easy to do,it saves time and costs,and it is efficient.Currently,the inspectors must stand on the platform of a bridge inspection vehicle or on a temporarily erected scaffolding to exa-mine the structure underside of the bridge and the portions above the water surface that cannot be seen directly by the eye.Fig.1shows the inspectors stan-ding on the platform of a bridge inspection vehicle. Fig.2shows the inspectors standing on a temporary scaffolding[4,5].As there are so many bridges,how to heighten inspection efficiency,while at the same time protecting the safety of the inspectors becomes an important issue.A robot system for the underwater inspection of bridge piers has already been investi-gated[6].Inspection by means of the above-mentioned ins-pection vehicle or temporary scaffolding may lead to accidents involving the inspectors.To eliminate such a danger,we developed a manipulator system,equip-ped with binocular Charge Coupled Devices(CCD) cameras.Two CCD cameras are installed on atwo-Fig.1.Inspectors standing on the platform of a bridge inspection vehicle.P.-C.Tung et al./Automation in Construction11(2002)717–729718axis rotational frame laid on the front end of Arm 4of the manipulator system.Binocular stereo images are simultaneously captured by CCD cameras and transmitted to the computer through a transmission cable.The CCD images,which contain physical noise,need to be processed before crack positions can be determined.Traditional pattern matching algorithms [7–10]require a large memory and a long computa-tion time.Furthermore,these methods are also sensi-tive to image noise.To solve these problems,we propose a new algorithm that can integrate the gray-ness variation along the horizontal axis and thus reduce the processingtime.Fig.2.Inspectors standing on a temporary scaffolding.P .-C.Tung et al./Automation in Construction 11(2002)717–729719Fig.3.The coordination system of the parallel binocular CCDcameras.Fig.4.Images from the(a)left and(b)rightcameras.Fig.5.The(a)left and(b)right images after the Sobel operation.P.-C.Tung et al./Automation in Construction11(2002)717–729 720The remainder of the paper is organized as follows: in Section2,we discuss the new binocular CCD images comparison algorithm,and then obtain the crack’s position.The experimental results are dis-cussed in Section3and a conclusion is given in Section4.2.Crack inspection via binocular CCD camera imagesWe used two parallel CCD cameras,to determine the distance between the object and the cameras.Fig. 3shows the geometric relationship of anobject Fig.6.Total gray value summation along the x-direction for the(a)left and(b)right images.P.-C.Tung et al./Automation in Construction11(2002)717–729721appearing before the two cameras.A coordinate system is defined at the center of the first CCD camera with its Z-axis along the normal direction of the CCD chips and the X-and Y-axes along the image’s x and y-axes.The following formula can be derived[10]:Z¼kÀk Bx2Àx1;ð1Þwhere k is the lens’focus length,Z represents the distance between the object and the planes of the camera,B represents the distance between the two CCD camera centers,x1,y1are the image coordinates of the first camera and x2,y2are the image coordinates of the second ing Eq.(1),one can find Z,as long as the difference between x1and x2is available. Once Z is found,X and Y can be obtained by the following equations[10].X¼x1kðkÀZÞð2ÞY¼y1kðkÀZÞ:ð3ÞSince the two camera images have a horizontal shift,the value of(x1Àx2)can be found by comparing any disparities between the two CCD images.Pre-vious comparison algorithms for finding the corre-spondence between two images have focused on matching region segments[7]and/or points,and lines [7–10].Due to differences between any two cameras, there may exist variations between images,such as brightness or image noises.A direct comparison of two images using the region matching methods[7] does not usually provide good results for determining these disparities.Although the comparison of signifi-cant image features(such as lines,circles,etc.[7–10]) may provide good results,this also requires a long computation time.Since our CCD cameras are ins-talled in parallel on a two-axis rotational frame laid on the front end of Arm4of the manipulator system,the images captured by the cameras will have a horizontal dislocation in the images’X-direction,as shown in Fig.4.Therefore,we developed a new algorithm to compare the total‘‘projection gray values’’along the image’s horizontal lines.2.1.Projection algorithmThe algorithm has five steps.Step1:Grab the left and right images,i.e.and I l(x,y)and I r(x,y).Illustrated in Fig.4.Fig.7.Total summation difference between the two images along the x-direction.P.-C.Tung et al./Automation in Construction11(2002)717–729722Step2:For the left and right images(denoted by I l(x,y)and I r(x,y),respectively),we find their corre-sponding images(denoted by I w l(x,y)and I w r(x,y), respectively)after the Sobel operation.The images after the Sobel operation are shown in Fig.5.Step3:Project the gray values of I w l(x,y)and I w r (x,y)onto a line parallel to the image’s x-axis.These values are plotted in Fig.6.P lðjÞ¼X mi¼1I w lðj;iÞ;j¼1;2;3...nP rðjÞ¼X mi¼1I w rðj;iÞ;j¼1;2;3...n;where m and n represent the height and the width of the image,respectively.Step4:Define a function J(k)asJðkÞ¼X nj¼1A P lðjþkÞÀP rðjÞA;k¼1;2;3...n:The result is shown in Fig.7.The value of k,which minimizes J,represents the disparity,or the value (x1Àx2),for the two images.Step5:Utilize Eqs.(1)–(3)to calculate the coor-dinates Z,X and Y.2.2.Parameter adjustmentWe designed a series of experiments using different lens focus lengths and variable distances to verify the projection algorithm results.Fig.8shows the exper-imental results when the lens focus length was set to 500mm.The upper(and the lower)curve represents the actual Z value(and the estimated Z value)versus the disparity of the two images.Due to errors in the estimation of Z,the errors in the estimates of X and Y became too large to be used for the manipulator system.Possible reasons include:(i)B,k measure-ment errors,(ii)the non-parallel effect of CCD chips. It is difficult to adjust CCD chips,because they are installed inside the cameras.Even if we could ensure that the cameras are exactly parallel to each other,the normal vector of the CCD chips may not be parallel. Hence,we must add two adjusting parameters to the estimation formula(Eq.(1)).Z¼kÀk Bx2Àx1Âm2þm1;ð4Þwhere m1and m2are the compensation parameters. Parameter m1can be considered as the focus length k adjustment,while m2can be considered as the Bad-Fig.8.Distance estimation for the binocular CCD cameras.Table1Maximum and mean errors after calibrationExperiment Lens focusdistance(mm)Object movementrange(cm)B(mm)k(mm)m1m2Maximumerror(cm)Averageerror(cm)Ex.1Various70–21013325À192.8 1.49 3.25 1.76 Ex.2700mm70–21013325À26.90 1.16000.6840.278 Ex.3Infinite70–21013325À38.90 1.14 1.820.65 Ex.41050mm70–21013325À22.62 1.1600 1.1550.502 Ex.5500mm60–404426.310.079 1.0490.350.168 Ex.62000mm60–404425.317.200.9830.4380.178P.-C.Tung et al./Automation in Construction11(2002)717–729723justment.By minimizing the least square errors of all differences between the actual and the estimated Z values,one can obtain optimal m 1and m 2values.Table 1lists the results for different focus lengths andthe maximum and average errors after calibration.Fig.9shows that,after calibration,the errors between the actual and estimated Z values have been reduced dramatically.As listed in Table 1,the maximum error is 3.5mm and the mean error is 1.68mm when the focus is 500mm,and the working range is 40–60cm.The corresponding errors for the estimated X and Y are less than 1mm.3.Experimental setup and resultsThe manipulator system discussed in this article has four arms.Arm 1is fixed on a revolving platform mounted on the vehicle.Arms 1,2,3and 4,as well as the revolving platform are placed on the vehicle as shown in Fig.10.The four arms are arranged as follows.Arm 1is placed vertically on the platform.Arm 2is laid vertically to Arm 1.On the vertical end of Arm 2,Arm 3is fixed to a 1.8-m long C-shaped steel beam and two other 1.8-m C-shaped steel beams equipped with slides.Through the action of aslidingFig.9.The resultant curves aftercalibration.Fig.10.The manipulator system.P .-C.Tung et al./Automation in Construction 11(2002)717–729724block,Arm 3can move vertically in the direction of the Z axis.The dynamic source for the sliding comes from the lifting device mounted on Arm 2.Arm 4,which is connected perpendicular to the bottom of the Arm 3extension,can revolve around the Arm 3axis.As Arm 4can be extended up to 4m,it is divided into two sections in order to facilitate storage;each section can revolve.The CCD cameras are fastened to the front end of Arm 4,and the images are transmitted via BNC cable to the screen of the control computer.The manipulator system may either revolve or move linearly.Arm 4,driven by a servomotor and a velocity reducer,enables a planar revolution facilitatesthe observation of bridge cracks.An oil-pressure motor and gears drives the revolving platform.Arm 3can move up and down linearly.Table 2Size and function of the manipulator system Number of arm SizeWeight (kg)FunctionArm 1H-shape steel beam:250Â250Â1500mm151.8This is the main support beam of the system;it supports the entire load of the whole structure and can move up and down,which permits Arm 3to move over the bridge railing and then down to facilitate detection.Arm 2H-shaped steel beam:250Â250Â3400mm 169.7Pushes Arms 3and 4over the bridge railing by a revolving movement and supports the load.Balance weight is laid on the arm’s rear end 300Arm 3C-shape steel beam:200Â75Â1800mm 22.976.15Pushes Arm 4below the underside of the bridge surface by a lifting up and down First section:sliding block and sliding rail 200Â10Â1800mm expansion movement.Second section:sliding block and sliding rail 200Â10Â1800mm 76.15Total weight of Arm3175.2Arm 4Section 1,aluminum extrusion:60Â60Â2500mm 7Pushes the CCD camera to the underside of the bridge surface by a revolving action.Section 1,sleeve:90Â80Â250mm3Section 1,balance weight:10Section 2,aluminum extrusion:80Â80Â2500mm 13.5Section 2,front sleeve:100Â100Â250mm 1.5Section 2,balance weight:84Section 2,rear sleeve:110Â100Â250mm 2.9Front ad rear shafts: 2.9Total weight:124.8Total weight of Arms 1,2,3,4and balance weights922Fig.11.Image transmission system.P .-C.Tung et al./Automation in Construction 11(2002)717–729725The dimensions of the manipulator system are as follows:Arm 1—1.7m high,Arm 2—3.4m long,Arm 3—5m long,and Arm 4—4m long.Balance weights are placed at the ends of Arms 2and 4,respectively,to maintain the center of gravity during operation.Thus,Arms 2and 4can rotate smoothly.ToFig.12.The bridge to be inspected and themanipulator.Fig.13.Arm 2is approximately perpendicular to the bridge.P .-C.Tung et al./Automation in Construction 11(2002)717–729726allow these arms to revolve smoothly,thrust bearings are used.Arm 4is made of A6N01S-T5,an integrally formed aluminum intrusion.This type integral forma-tion is used as much as possible during processing in order to reduce the stress concentration.The total weight of the system,including the balance weights,is around 922kg;for further details about the size and function,please refer to Table 2.The image transmission system is comprised of three parts shown in Fig.11,including a camera system,an image capturing system and a computer.A SONY XC-75camera is used,which has agene-Fig.14.Arm 4makes both horizontal and circularmovements.Fig.15.Crack ‘‘a’’measured by the CCD camera’s right eye.P .-C.Tung et al./Automation in Construction 11(2002)717–729727ral resolution 640Â480,or at best 769Â494.The image capturing system uses a Matrix Meteor-II Standard image capture card,which can catch a video signal at up to 60frames/s with a resolution of 640Â480.The system is operated by a multi-media computer.The video signal of the image captured by the CCD camera is transmitted through the system via a BNC cable,which sends it to a personal computer,where it is then displayed on a screen after being processed by the computer’s processing unit.For practical applications,the manipulator system is transported to the desired inspected bridge.Fig.12shows a bridge to be inspected and the manipulator system.Arm 1is fixed on a platform that revolves on the base plate,powered by a 7000-W electric gener-ator.After rotating the revolving platform toward the inspection area,Arm 2will be approximately perpen-dicular to the bridge railing,as shown in Fig.13.Through the action of the sliding block,Arm 3can move vertically in the direction of the Z -axis.Arm 4,which is connected perpendicular to the bottom of the Arm 3extension,can now revolve around the Arm 3axis.Arm 4is driven by a servomotor and a velocity reducer to produce a planar revolution,which facili-tates the bridge cracks observation.Fig.14shows that Arm 4can make both horizontal and circular move-ments that enable it to be extended to the underside of the bridge to observe cracks with the binocular CCD cameras.The images for the same crack ‘‘a’’capturedfrom the right and left cameras are shown in Figs.15and 16,respectively.One can find the horizontal image difference,that is x 2Àx 1,for the crack ‘‘a’’is 119pixels.By applying Eq.(4)derived in Section 2,one finds that the estimated distance from the crack ‘‘a’’to the camera is 1.93m.Also,the crack length is estimated as 8cm by applying Eqs.(2)and (3).This shows that the high degree of accuracy of the system during on-site observations.4.ConclusionWe developed a manipulator system using binoc-ular CCD cameras,which can offer another option to the current manual bridge crack inspection process.This system uses two cameras operated in parallel to detect cracks.A new algorithm is also proposed that will process the binocular images and calculate the crack pared with the current method of inspection,by an inspector standing on the platform of an inspection vehicle or on a temporary scaffolding,the manipulator system decreases the danger of acci-dents.Currently,the use of CCDs with the manipu-lator system is not intended as a human substitute for all inspection works,but may only involve a portion of work,since the human who is put in the same spot as the CCD cameras will take more intensive advant-age of human stereovision capabilities,recognition of color-shades,and ability to perform interactivetestsFig.16.Crack ‘‘a’’measured by the CCD camera’s left eye.P .-C.Tung et al./Automation in Construction 11(2002)717–729728such as scratching of the surface and other tactile investigations.References[1]Federal Highway Administration(FHWA),Bridge Inspec-tion’s Training Manual,July1991.[2]Bridge Maintenance Training Manual,US Federal HighwayAdministration,FHWA-HI-94-034,Prepared by Wilbur Smith Associates,1992.[3]B.Bakht,L.G.Jaeger,Bridge testing—a surprise every time,Journal of Structural Engineering,ASCE116(5)(May1990) 1370–1383.[4]Product Catalog,Paxton-Mitchell Snooper R Underbridge In-spection Machines,26Broadway—26th Floor New York,NY 10004USA.[5]Shibata Tsutomu,Shibata Atsushi,Summary Report of Re-search and Study on Robot Systems for Maintenance of High-ways and Bridges,Robot,no.118,Sep.1997,JARA Tokyo, Japan,pp.41–51.[6]J.E.De Vault,Robot system underwater inspection of bridgepiers,IEEE Instrumentation and Measurement Magazine3(3) (Sept.2000)32–37.[7]G.Medioni,R.Nevatia,Segment-based stereo matching,Computer Vision,Graphics and Image Processing,vol.31, (1985)2–18.[8]K.Kawasue,T.Ishimatsu,3-D measurement of moving papersby circular image shifting,IEEE Transactions on Industrial Electronics(1997)703–706.[9]N.Ayache,B.Faverjon,Efficient registration of stereo imagesby matching graph descriptions of edge segments,Internation-al Journal of Computer Vision(1987)107–131.[10]K.S.Fu,R.C.Gonzalez,S.G.Lee,Robotics Control,Sensing,Vision,and Intelligence,McGraw-Hill,New York,1987.P.-C.Tung et al./Automation in Construction11(2002)717–729729。
机械手的专用英语
机械手的专用英语English:A mechanical arm, also known as a robotic arm or industrial robot arm, is a programmable mechanical device with multiple degrees of freedom, designed to manipulate objects or perform tasks in place of a human arm. These devices are commonly used in manufacturing, assembly, and packaging processes to increase efficiency and precision. The mechanical arm typically consists of multiple joints and segments, allowing it to mimic the movement and flexibility of a human arm. It may be equipped with various end effectors, such as grippers, suction cups, or welding tools, to perform a wide range of tasks. The control system of a mechanical arm can be programmed to execute specific movements or sequences, making it versatile and adaptable to different production needs.中文翻译:机械手,也称为机器人手臂或工业机械手臂,是一种可编程的机械设备,具有多个自由度,旨在操作物体或执行任务,以取代人类手臂。
机械手英文专业词汇
机械手英文专业词汇Abnormal emergency stop 急停异常Adjuster handle 可调位紧定手柄Agent 代理商Air pressure detector 气压检知组Air pressure pneumatic pressure 气压Alarm Light警报灯Arch 拱Arm type手臂型式Arm up and low cylinder 上下气缸Arthrosis bearing oriented pin 关节轴承定位销Arthrosis bearing 关节轴承Assistant arm 副手臂Auto cycle pause time 自动循环暂停时间Auto-loader 上料机Avoid 避免Axis 轴Balance of machinery 机械平衡Base part 基座部Bumper 缓冲器Buzzer 蜂鸣器Caution light 警示灯Chain 链条Chip 切削Chip 芯片Circinal nut 圆螺母Clamp cylinder 夹具气缸Claw revolving cylinder 爪旋气缸Clip 夹住、切断Clockwise 顺时针Colon unit 双头组合Concavity 凹面Connector 接头Control panel 控制屏Cooper joint 逆止阀Counter clockwise 反时针方向Cross head link pin 小锁轴Cylinder 气缸Cylinder for forward and back 前后气缸Damage 损坏Detach 分离Drag chain 引拔拖链Drawbench closing board 引拔封板Drawbench cylinder 引拔气缸Drawbench fixed base 引拔固定座Drawbench ginder 引拔梁Drawbench guide arm 引拔导杆Drawbench 拔管机Driling 打眼Drowing 延伸Ejector valve 顶针阀Ejector 顶出、脱模Electomagnetic valve cover 电磁阀盖板Electomagnetic valve 电磁阀Electormagnetic valve base 电磁阀固定架Electric control 电控部Electronic control department 电控部Emergency stop 紧急制动器Error 错误Extend伸展External 外部的Extremity 极端Extrude mould delayed 顶针延时Fabricate 制作Fallback hold down plate 后退挡块Falling proof cylinder 防落气缸Fan 风扇Feedback 反馈Filter 滤波器Fixed tie 感应开关固定带Fixture 夹具Function 功能Generator 发生器Govern junction 调速接头Handle 把手Induction switch 感应开关Injection mould 喷射铸造法Key 键L type joint L型接头Lock tightly 锁紧Locknut 防松螺母Lubrication 润滑Machine nameplate 铭牌Machine rotating 机身回旋Machine rotator right 机身旋正Machine specification 规格Machine 机器Magnetic spring switch 磁簧开关Main arm 主手臂Main link pin 大锁轴Mechanical 驱动用汽轮机Motor 电动机Mould 模具Near-link switch 近接开关Nut 螺帽Open mould time delayed 开模延时Operator 作业员Pad 垫片Peg 定位把Plastic injection moulding machine 注塑机Pneumatic parts list 气动零件清单Pneumatic pressure 气压Power supply device 电源供应器Power supply filter 电源滤波器Power switch 电源开关Power 功率Punched hole 冲孔Punching machine 冲床Quick coupling 快速接头Radiation 辐射Reject 不良品Relay board 中继板Relay 继电器Reset 复位Revolving ball bearing 拱旋转轴承Revolving shaft 旋转轴Rigid 硬质Robot 机械手Rotate 旋转Safety gate 安全门Screw speed 螺杆转速Screw 螺钉Screwer 螺纹刀Sensitivity 灵敏度Servo motor伺服电机Signal lamp 信号灯Signal terminal 信号端子排Signal 信号Silencer 堵头Skate 滑轨Slot 槽Spring 弹簧Standard parts 标准件Stationary ring 吊环Straight joint 铜直立接头Strap 皮带Thimble 可顶针Mid-plate mould 中板模Rotate-out control 旋出电磁阀Stroke 行程Swing cylinder axletree 摆动缸轴承Swing cylinder rewlving shaft 摆动气缸旋转轴Swing cylinder 摆动气缸Swing cylinder 摆动气缸Switch-on 用开关Terminal cover 电磁阀孔封盖Thead processing 螺纹加工Tie rod nut 调模丝母To stretch 拉伸Track 磁道Tube管Vacumm checking 真空检测Vacuum generator 真空发生器Valve 阀门Vernier 游标Vertical joint 直立接头Water-proof junction 防水夹紧接头Wearable piece 耐磨片Workable 工作台机身部零件表旋转轴Revolving shaft 拱旋转轴承Revolving ball bearing 拱 Arch止动垫圈Prevent locomotor gasket圆螺母Circinal nut 旋出角度调整架Revolving angle adjust frame 防松螺母Locknut 垫片Pad 防松夹紧接头Waterproof clamp tie-in 连接器插头Plug M5圆把手M6 Handle定位柱Peg 滤波器Filter电源固定板Power fix board 电源供应器Power 耐磨片Wearable piece 拱旋转轴Arch revolving shaft 棘轮扳手Ratch wheel spanner 无油轴承Oil free shaft 基座Base 内六角圆柱头螺钉Inner hexangular columniform bolt 关节轴承定位销Arthrosis bearing oriented pin 关节轴承Arthrosis bearing 调速接头Govern junction 感应开关Induction switch 感应开关固定带Fixed tie 摆动气缸Swing cylinder 防松螺母Locknut 摆动缸轴承Swing cylinder axletree摆动气缸旋转轴Swing cylinder revolving shaft 惰轮lazy-wheel 横行惰轮座Transverse lazy-wheel seat 近接开关Sensitive switch 横行拖链Transverse chain 横行皮带调整夹板Transverse belt adjust clip 减速机Speed-down machineFlange基座部引拔固定座Drawbench base 滚珠轴承Ball beaing 旋转轴Recolving shaft 轴承挡块Bearing hold down plate 旋转角度调整架Revolving angle adjust frame 摆动气缸旋转轴Swing cylinder revolving shaft 风扇Fan 摆动气缸固定座Swing cylinder fixed base M20软管固定座M20 tube fixed base 引拔做固定块Drawbench base fixed block 基座Base 软管接头Tube junction引拔部吊环Stationary rings后退档块Fallback hold down plate缓冲器Bumper调速接头Govern junction前后气缸Fore and after cylinder引拔封板Drawbench closing board 引拔梁Drawbench ginder引拔导杆Drawbench guide arm引拔拖链Drag chain 引拔拖链板Drag chain board 引拔气缸Drawbench cylind 引拔固定座Drawbench fixed base可调位紧定手柄Adjuster handle前后气缸固定架Fore and after cylinder fixed frame保险杠Bumper护住固定架Protective-tube fixed frame横行皮带压板ransverse belt adjust strip 炮管罩盖Cover 1 of the barrel横行滑板Transverse slide board 上/下机座Up/down seat 横行拖链Transverse chain 横行拖链板Transverse chain board手臂部线形轴承Axletree 手臂梁Arm girder 防落气缸架Safe cylinder frame 下降挡板Down block 下固定板Down fixed frame气缸杆活动套Cylinder board 护管固定架Protective-tube fixed frame 上下气缸Up and down cylinder 信号端子排Signal junction 主手臂下固定板Main arm Low fixing board 下固定板Low fixing board 皮带belt 皮带夹板2 Flight fixed board 2 皮带固定座Belt clamp plate 皮带轮止动圈Oil free shaft 线轨挡块Falling hold down plate 皮带轮Belt wheel 齿轮座Gear base 皮带夹板Belt wheels side board 线性轴承Linearity shafe气阀部电磁阀盖板Electromagnetic valve cover 护管接头Protective value junction 电磁阀孔封盖Terminal cover 气压检知组Air pressure detector 电磁阀Electromagnetic valve L-型接头L-type junction 气阀箱连接座Air valve connecting base 调速阀Speed-adjusting valve 调压阀Pressure-adjust valve 气阀罩盖Motor cover 负压表Series pressure meter电控部滤波器Filter 电控箱固定板Electric control fix board 电源供应器Power 风扇Fan报警器Indicator ligh 电控箱支座上Electric control nog 1 电源开关Switch 电控箱盖Cover电控箱支座下Electric control nog 2 中继板Circuit board 电控箱罩壳(左)Electric cabinet encloser(left)电控箱Electric control 防水夹紧接头Preventing water clamp junction 中继板Circuit board 电源供应器Power 电控箱盖side boardof control box 伺服放大器Servo magnifier夹具部夹具片Fixture piece 夹具片连杆Fixture side board 夹具侧板定位柱Fixture side board oriented pillar 夹具片定位销Fixture piece oriented pin 夹具气缸垫片Fixture cylinder gasket 连杆定位销C onnecting pole oriented pin 端盖Cover 夹具固定块Fixture fixed block 夹具调节块Adjusting board of grip 短滑块Short sliding board侧姿组侧姿连接板上up board for side-pose link 侧姿连接板下under board for side-pose link侧姿封板side-pose cover 端子排Terminal group 转接头固定板Fix board of turning joint侧姿气缸Side-pose rotation cylinder 调速接头Speed-adjust joint 感应开关snesor侧姿固定架Side-pose part fix 侧姿旋转板side-pose rotating board 侧姿连杆轴side-pose link axis 耳环Earring 连杆Link pole 侧姿旋转轴side-pose rotating axis。
机械臂的外文文献以及翻译演示教学
精品文档附件1:外文资料翻译译文机械手机械手是近几十年发展起来的一种高科技自动化生产设备。
工业机械手是工业机器人的一个重要分支。
它的特点是可通过编程来完成各种预期的作业任务,在构造和性能上兼有人和机器各自的优点,尤其体现了人的智能和适应性。
机械手作业的准确性和各种环境中完成作业的能力,在国民经济各领域有着广阔的发展前景。
随着工业自动化的发展, 出现了数控加工中心,它在减轻工人的劳动强度的同时, 大大提高了劳动生产率。
但数控加工中常见的上下料工序, 通常仍采用人工操作或传统继电器控制的半自动化装置。
前者费时费工、效率低; 后者因设计复杂, 需较多继电器,接线繁杂, 易受车体振动干扰,而存在可靠性差、故障多、维修困难等问题。
可编程序控制器PLC控制的上下料机械手控制系统动作简便、线路设计合理、具有较强的抗干扰能力, 保证了系统运行的可靠性,降低了维修率, 提高了工作效率。
机械手技术涉及到力学、机械学、电气液压技术、自动控制技术、传感器技术和计算机技术等科学领域,是一门跨学科综合技术。
一、工业机械手的概述机械手是一种能自动化定位控制并可重新编程序以变动的多功能机器,它有多个自由度,可用来搬运物体以完成在各个不同环境中工作。
在工资水平较低的中国,塑料制品行业尽管仍属于劳动力密集型,机械手的使用已经越来越普及。
那些电子和汽车业的欧美跨国公司很早就在它们设在中国的工厂中引进了自动化生产。
但现在的变化是那些分布在工业密集的华南、华东沿海地区的中国本土塑料加工厂也开始对机械手表现出越来越浓厚的兴趣,因为他们要面对工人流失率高,以及为工人交工伤费带来的挑战。
随着我国工业生产的飞跃发展,特别是改革开发以后,自动化程度的迅速提高,实现工件的装卸、转向、输送或操作钎焊、喷枪、扳手等工具进行加工、装配等作业自化,已愈来愈引起我们重视。
机械手是模仿着人手的部分动作,按给定的程序、轨迹和要求实现自动抓取、搬运或操作的自动机械装置。
关于现代工业机械手外文文献翻译@中英文翻译@外文翻译
附录About Modenr Industrial Manipulayor Robot is a type of mechantronics equipment which synthesizes the last research achievement of engine and precision engine, micro-electronics and computer, automation control and drive, sensor and message dispose and artificial intelligence and so on. With the development of economic and the demand for automation control, robot technology is developed quickly and all types of the robots products are come into being. The practicality use of robot not only solves the problems which are difficult to operate for human being, but also advances the industrial automation program. Modern industrial robots are true marvels of engineering. A robot the size of a person can easily carry a load over one hundred pounds and move it very quickly with a repeatability of 0.006inches. Furthermore these robots can do that 24hours a day for years on end with no failures whatsoever. Though they are reprogrammable, in many applications they are programmed once and then repeat that exact same task for years.At present, the research and development of robot involves several kinds of technology and the robot system configuration is so complex that the cost at large is high which to a certain extent limit the robot abroad use. To development economic practicality and high reliability robot system will be value to robot social application and economy development. With he rapid progress with the control economy and expanding of the modern cities, the let of sewage is increasing quickly; with the development of modern technology and the enhancement of consciousness about environment reserve, more and more people realizedthe importance and urgent of sewage disposal. Active bacteria method is an effective technique for sewage disposal. The abundance requirement for lacunaris plastic makes it is a consequent for plastic producing with automation and high productivity. Therefore, it is very necessary to design a manipulator that can automatically fulfill the plastic holding. With the analysis of the problems in the design of the plasticholding manipulator and synthesizing the robot research and development condition in recent years, a economic scheme is concluded on the basis of the analysis of mechanical configuration, transform system, drive device and control system and guided by the idea of the characteristic and complex of mechanical configuration, electronic, software and hardware. In this article, the mechanical configuration combines the character of direction coordinate which can improve the stability and operation flexibility of the system. The main function of the transmission mechanism is to transmit power to implement department and complete the necessary movement. In this transmission structure, the screw transmission mechanism transmits the rotary motion into linear motion. Worm gear can give vary transmission ratio. Both of the transmission mechanisms have a characteristic of compact structure. The design of drive system often is limited by the environment condition and the factor of cost and technical lever. The step motor can receive digital signal directly and has the ability to response outer environment immediately and has no accumulation error, which often is used in driving system. In this driving system, open-loop control system is composed of stepping motor, which can satisfy the demand not only for control precision but also for the target of economic and practicality. On this basis, the analysis of stepping motor in power calculating and style selecting is also given. The analysis of kinematics anddynamics for object holding manipulator is given in completing the design of mechanical structure and drive system.Current industrial approaches to robot arm control treat each joint of the robot arm as a simple joint servomechanism. The servomechanism approach models the varying dynamics of a manipulator inadequately because it neglects the motion and configuration of the whole arm mechanism. These changes in the parameters of the controlled system sometimes are significant enough to render conventional feedback control strategies ineffective. The result is reduced servo response speed and damping, limiting the precision and speed of the end-effecter and making it appropriate only for limited-precision tasks. Manipulators controlled in this manner move at slow speeds with unnecessary vibrations. Any significant performance gain in this and other areas of robot arm control require the consideration of more efficient dynamic models, sophisticated control approaches, and the use of dedicated computer architectures and parallel processing techniques.In the industrial production and other fields, people often endangered by such factors as high temperature, corrode, poisonous gas and so forth at work, which have increased labor intensity and even jeopardized the life sometimes. The corresponding problems are solved since the robot arm comes out. The arms can catch, put and carry objects, and its movements are flexible and diversified. It applies to medium and small-scale automated production in which production varieties can be switched. And it is widely used on soft automatic line. The robot arms are generally made by withstand high temperatures, resist corrosion of materials to adapt to the harsh environment. So they reduced the labor intensity of the workers significantly and raised work efficiency. The robot arm is an importantcomponent of industrial robot, and it can be called industrial robots on many occasions. Industrial robot is set machinery, electronics, control, computers, sensors, artificial intelligence and other advanced technologies in the integration of multidisciplinary important modern manufacturing equipment. Widely using industrial robots, not only can improve product quality and production, but also is of great significance for physical security protection, improvement of the environment for labor, reducing labor intensity, improvement of labor productivity, raw material consumption savings and lowering production costs.There are such mechanical components as ball footbridge, slides, air control mechanical hand and so on in the design. A programmable controller, a programming device, stepping motors, stepping motors drives, direct current motors, sensors, switch power supply, an electromagnetism valve and control desk are used in electrical connection.Robot is the automated production of a kind used in the process of crawling and movin g piece features automatic device, which is mechanized and automated production process d eveloped a new type of device. In recent years, as electronic technology, especially compute r extensive use of robot development and production of hightech fields has become a rapidl y developed a new technology, which further promoted the development of robot, allowing robot to better achieved with the combination of mechanization and automation. Robot can replace humans completed the risk of duplication of boring work, to reduce human labor int ensity and improve labor productivity. Manipulator has been applied more and more widely, in the machinery industry, it can be used for parts assembly, work piece handling, loading a nd unloading, particularly in the automation of CNC machine tools, modular machine toolsmore commonly used. At present, the robot has developed into a FMS flexible manufacturin g systems and flexible manufacturing cell in an important component of the FMC. The mac hine tool equipment and machinery in hand together constitute a flexible manufacturing syst em or a flexible manufacturing cell, it was adapted to small and medium volume production , you can save a huge amount of the work piece conveyor device, compact, and adaptable. When the work piece changes, flexible production system is very easy to change will help e nterprises to continuously update the marketable variety, improve product quality, and better adapt to market competition. At present, China's industrial robot technology and its enginee ring application level and comparable to foreign countries there is a certain distance, applica tion and industrialization of the size of the low level of robot research and development of a direct impact on raising the level of automation in China, from the economy, technical cons iderations are very necessary. Therefore, the study of mechanical hand design is very meani ngful.关于现代工业机械手机器人是典型的机电一体化装置,它综合运用了机械与精密机械、微电子与计算机、自动控制与驱动、传感器与信息处理以及人工智能等多学科的最新研究成果,随着经济技术的开展和各行各业对自动化程度要求的提高,机器人技术得到了迅速开展,出现了各种各样的机器人产品。
- 1、下载文档前请自行甄别文档内容的完整性,平台不提供额外的编辑、内容补充、找答案等附加服务。
- 2、"仅部分预览"的文档,不可在线预览部分如存在完整性等问题,可反馈申请退款(可完整预览的文档不适用该条件!)。
- 3、如文档侵犯您的权益,请联系客服反馈,我们会尽快为您处理(人工客服工作时间:9:00-18:30)。
外文出处:《Manufacturing Engineering and Technology—Maching》附件1:外文原文ManipulatorFirst, an overview of industrial manipulatorWith the rapid development of China's industrial production, especially the reform and openingup after the rapid increase in the degree of automation to achieve the workpiece handling, steering,transmission or operation of brazing, spray gun, wrenches and other tools for processing and assembly operations since, which has more and more attracted our attention. Robot is to imitate the manual part of the action, according to a given program, track and requirements for automatic capture, handling or operation of the automatic mechanical devices.Production of mechanical hand can increase the automation level of production and labor productivity; can reduce labor intensity, ensuring product quality, to achieve safe production; particularly in the high-temperature, high pressure, low temperature, low pressure, dust, explosive, toxic andradioactive gases such as poor environment can replace the normal working people. Here I would like to think of designing a robot to be used in actual production.Why would a robot designed to provide a pneumatic power:1." Air inexhaustible, used later discharged into the atmosphere, does not require recycling and disposal, do not pollute the environment. (Concept of environmental protection)2." Air stick is small, the pipeline pressure loss is small (typically less than asphalt gas path pressure drop of one-thousandth), to facilitate long-distance transport.5." The air cleaner media, it will not degenerate, not easy to plug the pipeline. But there are also places where it fly in the ointment:2." As the use of low atmospheric pressure, the output power can notbe too large; in order to increase the output power is bound to the structure of the entire pneumaticsystem size increased.Air inexhaustible, used later discharged into the atmosphere, without recycling and disposal, donot pollute the environment. Accidental or a small amount of leakage would not be a serious impact on production. Viscosity of air is small, the pipeline pressure loss also is very small, easy long-distance transport.Compared with the hydraulic transmission, and its faster action and reaction, which is one of the outstanding merits of pneumatic.1.Implementing agencies2. Transmission3. Control SystemRobots are generally divided into three categories:Main features:First, mechanical hand (the upper and lower material robot, assembly robot, handling robot, stacking robot, help robot, vacuum handling machines, vacuum suction crane, labor-saving spreader, pneumatic balancer, etc.).Second, cantilever cranes (cantilever crane, electric chain hoist crane, air balance the hanging, etc.)Third, rail-type transport system (hanging rail, light rail, single girder cranes, double-beam crane)Four, industrial machinery, application of hand(3) The working conditions may be poor, monotonous, repetive easy to sub-fatigue working environment to replace human labor.(4) May be in dangerous situations, such as military goods handling, dangerous goods and hazardous materials removal and so on..(5) Universe and ocean development.(6), military engineering and biomedical research and testing.Help mechanical hands:附件1:外文资料翻译译文机械手机械手是近几十年发展起来的一种高科技自动化生产设备。
工业机械手是工业机器人的一个重要分支。
它的特点是可通过编程来完成各种预期的作业任务,在构造和性能上兼有人和机器各自的优点,尤其体现了人的智能和适应性。
机械手作业的准确性和各种环境中完成作业的能力,在国民经济各领域有着广阔的发展前景。
随着工业自动化的发展,出现了数控加工中心,它在减轻工人的劳动强度的同时,大大提高了劳动生产率。
但数控加工中常见的上下料工序,通常仍采用人工操作或传统继电器控制的半自动化装置。
前者费时费工、效率低;后者因设计复杂,需较多继电器,接线繁杂,易受车体振动干扰,而存在可靠性差、故障多、维修困难等问题。
可编程序控制器PLC控制的上下料机械手控制系统动作简便、线路设计合理、具有较强的抗干扰能力,保证了系统运行的可靠性,降低了维修率,提高了工作效率。
机械手技术涉及到力学、机械学、电气液压技术、自动控制技术、传感器技术和计算机技术等科学领域,是一门跨学科综合技术。
1.工业机械手的概述机械手是一种能自动化定位控制并可重新编程序以变动的多功能机器,它有多个自由度,可用来搬运物体以完成在各个不同环境中工作。
在工资水平较低的中国,塑料制品行业尽管仍属于劳动力密集型,机械手的使用已经越来越普及。
那些电子和汽车业的欧美跨国公司很早就在它们设在中国的工厂中引进了自动化生产。
但现在的变化是那些分布在工业密集的华南、华东沿海地区的中国本土塑料加工厂也开始对机械手表现出越来越浓厚的兴趣,因为他们要面对工人流失率高,以及为工人交工伤费带来的挑战。
随着我国工业生产的飞跃发展,特别是改革开发以后,自动化程度的迅速提高,实现工件的装卸、转向、输送或操作钎焊、喷枪、扳手等工具进行加工、装配等作业自化,已愈来愈引起我们重视。
机械手是模仿着人手的部分动作,按给定的程序、轨迹和要求实现自动抓取、搬运或操作的自动机械装置。
在现实生活中,你是否会发现这样一个问题。
在机械工厂里,加工零件装料的时候是不是很烦的,劳动生产率不高,生产成本大,有时候还会发生一些人为事故,导致加工者受伤。
想想看用什么可以来代替呢,加工的时候只要有几个人巡视一下,且可以二十四个小时饱和运作,人行吗?回答是肯定的,但是机械手可以来代替它。
生产中应用机械手可以提高生产的自动化水平和劳动生产率;可以减轻劳动强度、保证产品质量、实现安全生产;尤其是在高温、高压、低温、低压、粉尘、易爆、有毒气体和放射性等恶劣的环境中能够代替人进行正常的工作。
想到这里我就很想设计一个机械手,来用于生产实际中。
为什么选着设计机械手用气动来提供动力:气动机械手是指以压缩空气为动力源驱动的机械手。
用气压驱动与其他能源驱动比较有以下优点:1.空气取之不竭,用过之后排入大气,不需要回收和处理,不污染环境。