空心球铸造设计报告
有色金属空心球的砂型铸造生产
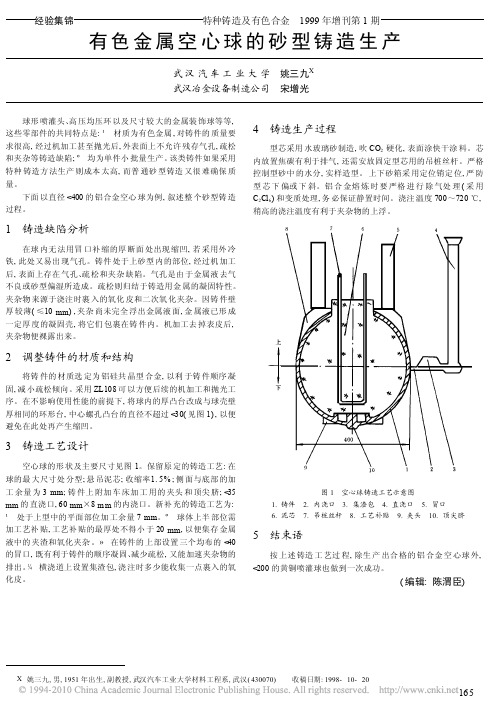
经验集锦特种铸造及有色合金 1999年增刊第1期有色金属空心球的砂型铸造生产武汉汽车工业大学 姚三九X武汉冶金设备制造公司 宋增光 球形喷灌头、高压均压环以及尺寸较大的金属装饰球等等,这些零部件的共同特点是:¹材质为有色金属,对铸件的质量要求很高,经过机加工甚至抛光后,外表面上不允许残存气孔,疏松和夹杂等铸造缺陷;º均为单件小批量生产。
该类铸件如果采用特种铸造方法生产则成本太高,而普通砂型铸造又很难确保质量。
下面以直径<400的铝合金空心球为例,叙述整个砂型铸造过程。
1 铸造缺陷分析在球内无法用冒口补缩的厚断面处出现缩凹,若采用外冷铁,此处又易出现气孔。
铸件处于上砂型内的部位,经过机加工后,表面上存在气孔、疏松和夹杂缺陷。
气孔是由于金属液去气不良或砂型偏湿所造成。
疏松则归结于铸造用金属的凝固特性。
夹杂物来源于浇注时裹入的氧化皮和二次氧化夹杂。
因铸件壁厚较薄(≤10mm),夹杂尚未完全浮出金属液面,金属液已形成一定厚度的凝固壳,将它们包裹在铸件内。
机加工去掉表皮后,夹杂物便裸露出来。
2 调整铸件的材质和结构将铸件的材质选定为铝硅共晶型合金,以利于铸件顺序凝固,减小疏松倾向。
采用ZL108可以方便后续的机加工和抛光工序。
在不影响使用性能的前提下,将球内的厚凸台改成与球壳壁厚相同的环形台,中心螺孔凸台的直径不超过<30(见图1),以便避免在此处再产生缩凹。
3 铸造工艺设计空心球的形状及主要尺寸见图1。
保留原定的铸造工艺:在球的最大尺寸处分型;悬吊泥芯;收缩率1.5%;侧面与底部的加工余量为3mm;铸件上附加车床加工用的夹头和顶尖脐;<35 mm的直浇口,60mm×8m m的内浇口。
新补充的铸造工艺为:¹处于上型中的平面部位加工余量7mm。
º球体上半部位需加工艺补贴,工艺补贴的最厚处不得小于20mm,以便集存金属液中的夹渣和氧化夹杂。
»在铸件的上部设置三个均布的<40的冒口,既有利于铸件的顺序凝固、减少疏松,又能加速夹杂物的排出。
空心球铸造工艺流程

空心球铸造工艺流程英文回答,The process of hollow ball casting involves several key steps to ensure the quality and integrity of the final product.Firstly, the design of the hollow ball mold is crucial in determining the shape and size of the final product. The mold is typically made of metal and is designed to withstand the high temperatures involved in the casting process.Next, the molten metal is prepared by melting the desired metal in a furnace. Once the metal reaches the appropriate temperature, it is poured into the hollow ball mold.As the molten metal cools and solidifies, it takes on the shape of the mold, forming a hollow ball. The cooling process is carefully monitored to prevent any defects or irregularities in the final product.After the metal has fully solidified, the mold is removed, leaving behind the hollow ball. Any excess metalor imperfections are removed through a finishing process, resulting in a smooth and uniform surface.Finally, the hollow balls are inspected for quality and consistency before being packaged and shipped to customers.中文回答,空心球铸造工艺流程包括几个关键步骤,以确保最终产品的质量和完整性。
铸造实验报告书
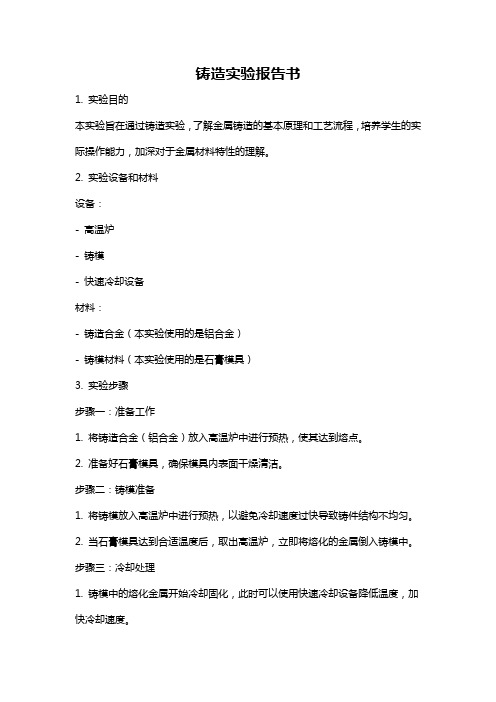
铸造实验报告书1. 实验目的本实验旨在通过铸造实验,了解金属铸造的基本原理和工艺流程,培养学生的实际操作能力,加深对于金属材料特性的理解。
2. 实验设备和材料设备:- 高温炉- 铸模- 快速冷却设备材料:- 铸造合金(本实验使用的是铝合金)- 铸模材料(本实验使用的是石膏模具)3. 实验步骤步骤一:准备工作1. 将铸造合金(铝合金)放入高温炉中进行预热,使其达到熔点。
2. 准备好石膏模具,确保模具内表面干燥清洁。
步骤二:铸模准备1. 将铸模放入高温炉中进行预热,以避免冷却速度过快导致铸件结构不均匀。
2. 当石膏模具达到合适温度后,取出高温炉,立即将熔化的金属倒入铸模中。
步骤三:冷却处理1. 铸模中的熔化金属开始冷却固化,此时可以使用快速冷却设备降低温度,加快冷却速度。
2. 等待足够时间,直到铸件冷却完全固化为止。
4. 实验结果与讨论经过以上实验步骤,我们成功完成了一次铸造实验,并获得了如图所示的铸件。
经过观察,铸件整体形状良好,表面呈现光滑平整的状态。
然而,我们也发现了一些潜在问题,例如:1. 铸件表面出现微小气孔,可能是由于石膏模具的气体释放不彻底导致的。
2. 铸件的某些部位出现缺陷,可能是由于熔化金属的流动性不佳导致的。
针对这些问题,我们可以进一步优化实验流程,改进铸造工艺,以获得更加理想的铸件。
5. 实验结论通过本次铸造实验,我们深入了解了金属铸造的基本原理和工艺流程,通过实际操作也体会到了其中的挑战和困难。
在实验中,我们成功获得了铝合金铸件,对于铸造技术的应用和发展有了更深入的认识。
然而,在铸造过程中也遇到了一些问题和挑战,这也提示我们仍有许多工作需要进一步完善和改进。
我们应该不断学习和探索,提高实际操作技能,以逐步提升铸造工艺的质量。
6. 参考文献暂无以上是本次铸造实验的实验报告书,谢谢阅读!。
手工铸造实验报告总结(3篇)
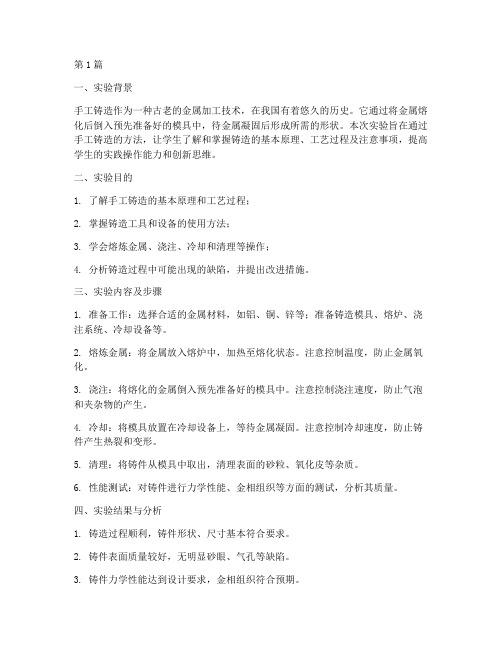
第1篇一、实验背景手工铸造作为一种古老的金属加工技术,在我国有着悠久的历史。
它通过将金属熔化后倒入预先准备好的模具中,待金属凝固后形成所需的形状。
本次实验旨在通过手工铸造的方法,让学生了解和掌握铸造的基本原理、工艺过程及注意事项,提高学生的实践操作能力和创新思维。
二、实验目的1. 了解手工铸造的基本原理和工艺过程;2. 掌握铸造工具和设备的使用方法;3. 学会熔炼金属、浇注、冷却和清理等操作;4. 分析铸造过程中可能出现的缺陷,并提出改进措施。
三、实验内容及步骤1. 准备工作:选择合适的金属材料,如铝、铜、锌等;准备铸造模具、熔炉、浇注系统、冷却设备等。
2. 熔炼金属:将金属放入熔炉中,加热至熔化状态。
注意控制温度,防止金属氧化。
3. 浇注:将熔化的金属倒入预先准备好的模具中。
注意控制浇注速度,防止气泡和夹杂物的产生。
4. 冷却:将模具放置在冷却设备上,等待金属凝固。
注意控制冷却速度,防止铸件产生热裂和变形。
5. 清理:将铸件从模具中取出,清理表面的砂粒、氧化皮等杂质。
6. 性能测试:对铸件进行力学性能、金相组织等方面的测试,分析其质量。
四、实验结果与分析1. 铸造过程顺利,铸件形状、尺寸基本符合要求。
2. 铸件表面质量较好,无明显砂眼、气孔等缺陷。
3. 铸件力学性能达到设计要求,金相组织符合预期。
4. 部分铸件出现轻微的热裂现象,经分析,可能是冷却速度过快或模具设计不合理所致。
五、实验总结1. 手工铸造是一种重要的金属加工方法,具有操作简便、成本低廉等优点。
2. 在实验过程中,要严格遵守操作规程,确保实验安全。
3. 熔炼金属时,要注意控制温度,防止金属氧化。
4. 浇注过程中,要控制浇注速度,避免气泡和夹杂物的产生。
5. 冷却过程中,要控制冷却速度,防止铸件产生热裂和变形。
6. 铸造模具的设计对铸件质量有很大影响,要充分考虑模具的刚度和强度。
7. 通过本次实验,使学生掌握了手工铸造的基本原理和工艺过程,提高了实践操作能力。
铸造设计总结报告范文(3篇)

第1篇一、前言铸造行业作为我国制造业的重要组成部分,具有悠久的历史和丰富的经验。
近年来,随着科技的进步和市场的需求,铸造设计在材料、工艺、设备等方面都取得了显著的成果。
本报告将对我国铸造设计的发展现状、存在的问题及未来发展趋势进行总结和分析。
二、铸造设计发展现状1. 设计理念(1)绿色环保:在铸造设计过程中,注重节能减排,降低能耗,减少废弃物排放,实现可持续发展。
(2)创新驱动:鼓励创新,提高铸造设计的质量和效率,降低生产成本。
(3)以人为本:关注员工身心健康,提高工作环境舒适度,提升员工满意度。
2. 设计技术(1)计算机辅助设计(CAD):利用计算机软件进行铸造设计,提高设计效率和准确性。
(2)计算机辅助工程(CAE):通过模拟分析,优化铸造工艺,提高产品质量。
(3)三维设计:采用三维设计技术,实现铸造件的数字化设计,提高设计精度。
3. 设计软件(1)铸造设计软件:如Pro/ENGINEER、SolidWorks、CATIA等,具有丰富的功能,满足不同铸造设计需求。
(2)铸造工艺模拟软件:如CASTmaster、MAGMA、DEFORM等,用于模拟铸造过程,优化工艺参数。
(3)铸造材料数据库:提供丰富的铸造材料性能数据,为设计提供支持。
三、铸造设计存在的问题1. 设计水平参差不齐:部分企业设计人员缺乏专业知识和经验,导致设计质量不高。
2. 设计周期较长:设计过程中,与生产、工艺等部门沟通不畅,导致设计周期延长。
3. 设计创新不足:在设计过程中,过分依赖传统经验,缺乏创新意识。
4. 设计与生产脱节:设计过程中,对生产设备的性能、工艺参数了解不足,导致设计难以实施。
四、铸造设计未来发展趋势1. 设计与生产深度融合:加强设计、生产、工艺等部门的沟通与协作,提高设计实施效率。
2. 智能化设计:利用人工智能、大数据等技术,实现铸造设计的智能化、自动化。
3. 绿色设计:关注环保,采用绿色材料、绿色工艺,降低能耗,减少废弃物排放。
空心球铸造设计报告

为浇铸的通道。
此方案的优点是能最好的满足无缝无焊接的一个空心
球体,铸成后是一个完整球体。缺点是铸造起来比较困难,
铸完之后内部很可能产生缺陷,且设备构造较复杂,铸造
成本高。该方案实现起来较为困难,故不做更深的研究。
方案二:用熔模铸造。
熔模铸造较难实现,理想的方案是需要两种特殊的材料,一种是内部球模,要求该材料在一个特定的温度t能直接汽化挥发,另一种材料则是要求有良好的抗高温能力的涂料,且有透气性。用于涂在内部的球模上。
具体方案是:用材料一制成内部的球模,将材料二涂在材料一表面作为空心球的内部球模,浇铸时随着浇铸液的逐渐硬化,材料一开始汽化,从材料二表面渗透挥发,由于材料二耐高温,留在球体内部,从而得到一个空心球体。此种方案其实只是一种理想的方案,在浇铸过程中可能出现材料一汽化后,材料二的强度不足被压溃,得不到空心球体,其次两种材料的存在性也未可知。因此此种方案实现起来十分困难,也不做深入探讨。
1、铸造型芯。
如下图一为铸造型芯的造型方案,为防止浇铸液流出,两沙箱之间有止口构造,为保证透气性和散热上沙箱上还要留有气孔,在浇筑过程中,为防止浇不足的现象也可适当给浇铸液加压或者从两个方向同时浇铸。浇铸完成之后铸件如右图二,铸件拼接之后留有凸台是为了能撑住空心球在沙箱内部作为型芯,6个凸台是为了保证其对中性更为良好。
3、浇铸。
砂型和空心球型芯做完之后,将铸铁做成的型芯放在砂型之内,这样就做成了空心球的整个砂型。为保证浇铸质量,在浇铸之前可以将型芯进行一定程度的预热。
4、落砂、清理、检验。即可得到一个空心球,再进行外表面打磨之后即可得到一个光滑的空心球。
此方案是较为理想且可实行的方案,浇铸打磨完之后球外表面是一个整体且光滑,不必采用焊接,制作起来相对简单,成本较低。是较为理想空心球制作方案。
焊接空心钢球的成形工艺设计报告
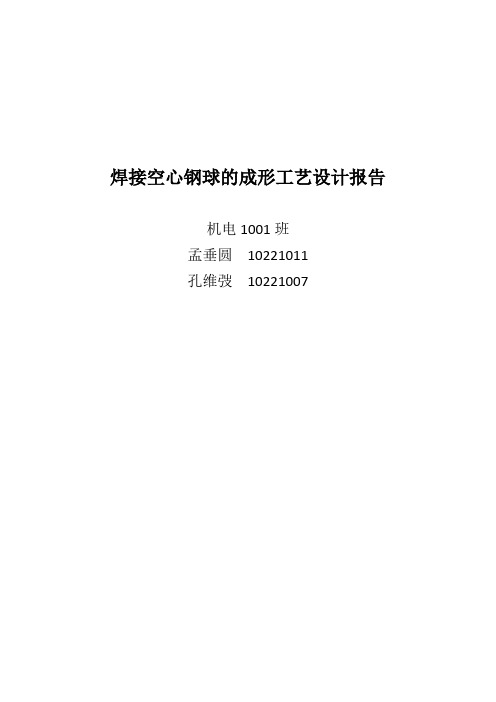
焊接空心钢球的成形工艺设计报告机电1001班孟垂圆10221011孔维弢10221007一、设计题目1、3-5人一组,运用所学焊接成形知识,完成空心钢球的焊接成形工艺设计。
2、钢球材料25#钢,尺寸Ф200mm,壁厚4.5mm3、合作完成专题研究报告并进行PPT汇报二、设计思路分析在之前我们已经做了用铸造的方法来制造空心钢球,一般来说空心钢球较理想的成型方法应该是焊接。
用焊接成型的方法相比铸造可以节省大量的人力物力,制造起来较方便,精度也较高,工艺性也比铸造成型大大提高。
焊接方法从冶金的角度可以分为三大类:一是熔化焊,属于液相焊接;二是压力焊,属于固相焊接;以及最后的钎焊,属于固液焊接。
在这三大类的基础上还可以继续分为手工电弧焊、埋弧自动焊、气体保护焊等等类型。
由于焊接的材料是25号钢,性能优越,需焊接的钢球也不大,考虑经济性和操作方便,所以我们采用手工电弧焊的方案,属于液相的熔化焊。
三、设计方案1、制作球壳为保证焊接球的质量,以及看绿岛焊接条件,两个半球壳均采用热冲压方法成型。
两端要预留焊接的缝隙。
具体参数如下:半球壳外径200mm,内径193mm,预留焊缝。
2、焊接①焊接材料为25#钢,焊接性能优秀。
②焊接采用手工电弧焊,其优点是所用设备、工具简单,操作灵活方便,适用于各种空间位置和各种复杂结构的焊接。
③为保证其良好的工艺性,焊条选用酸性焊条。
查表选用的焊条为:结422铁焊条,因其熔敷效率和熔敷速度均较高;具有较好的导电导热性能,可采用较大的工作电流;焊条脱渣性好,飞溅少,焊缝成型好,可全位置焊接。
④焊接步骤为先将两个半球壳用均匀的焊点连接,然后再将未焊接部分补全。
⑤焊接机构如右图:左端端连接一个转速适当的电机,用两个真空吸盘吸住两半球壳,首先将两个半球壳焊接一个点,再启动电机,再将两半球壳用均匀的焊点连接,然后在开始真正将两半球壳焊接在一起。
3、尺寸检验查表得以下数据:焊接球直径、圆度、壁厚减薄量等尺寸合本规范的规定:外径:±1.5mm圆度:±1.5mm壁厚减薄量:≤0.81mm对口错边量:≤0.45mm焊缝余高:0~1.5mm4、除锈、涂层、表面处理按照设计要求进行除锈和涂装。
铸造工艺设计报告

铸造工艺设计报告一、引言铸造是制造业中一种常见且重要的工艺方法,广泛应用于航空航天、汽车、机械制造等行业。
铸造工艺设计是确保最终产品质量、成本和生产效率的重要环节。
本报告旨在设计一个优化的铸造工艺,以满足客户要求并提高生产效率。
二、设计目标1.提高产品质量:通过选用合适的材料、优化铸造工艺参数和工艺流程,确保产品的物理性能和表面质量符合要求。
2.降低生产成本:通过选用经济合理的铸造材料、优化工艺流程和降低废品率,降低生产成本。
3.提高生产效率:通过合理安排工艺流程、减少工艺环节和优化设备使用,提高生产效率和生产能力。
三、材料选择1.铸造材料的选择应根据产品要求和使用环境来确定。
在本案例中,我们将选择A356.0铝合金作为铸造材料。
2.A356.0铝合金具有良好的液态流动性和加工性能,适用于铸造复杂形状的产品。
此外,它也具有较高的强度和耐腐蚀性能。
四、工艺参数设计1.浇注温度:浇注温度将直接影响到铝合金的凝固过程和产品质量。
通过实验和模拟,确认合适的浇注温度。
2.浇注速度:浇注速度直接影响到产品的密度和表面质量。
通过调整铝液流入的速度,控制浇注过程中的气体夹杂物产生。
3.浇注时间:根据模具设计和产品形状,确定合适的浇注时间,确保铸件充分充型和凝固。
五、工艺流程设计1.模具设计:根据产品形状和尺寸,设计合适的铸造模具。
确保模具能够充分充型,并方便铸造材料的注入和铸件的取出。
2.准备工作:清洁模具表面、预热模具,准备好所需的工具和材料。
3.浇注:控制好浇注温度、速度和时间,确保铝液完全充型并凝固。
4.冷却:待铸件凝固后,对其进行冷却,使其达到足够的强度。
5.修磨和抛光:将铸件修磨光滑,并进行抛光处理,提高表面质量。
6.检验和包装:对铸件进行检验,确保其质量符合要求,并进行包装。
六、优化工艺设计1.利用计算机模拟软件对铸造过程进行仿真,分析工艺参数对铸件质量的影响,进一步优化工艺参数。
2.使用先进的设备和工艺技术,提高生产效率和产品质量。
- 1、下载文档前请自行甄别文档内容的完整性,平台不提供额外的编辑、内容补充、找答案等附加服务。
- 2、"仅部分预览"的文档,不可在线预览部分如存在完整性等问题,可反馈申请退款(可完整预览的文档不适用该条件!)。
- 3、如文档侵犯您的权益,请联系客服反馈,我们会尽快为您处理(人工客服工作时间:9:00-18:30)。
砂型和空心球型芯做完之后,将铸铁做成的型芯放在砂型之内,这样就做成了空心球的整个砂型。为保证浇铸质量,在浇铸之前可以将型芯进行一定程度的预热。
4、落砂、清理、检验。即可得到一个空心球,再进行Leabharlann 表面打磨之后即可得到一个光滑的空心球。
此方案是较为理想且可实行的方案,浇铸打磨完之后球外表面是一个整体且光滑,不必采用焊接,制作起来相对简单,成本较低。是较为理想空心球制作方案。
具体方案是:用材料一制成内部的球模,将材料二涂在材料一表面作为空心球的内部球模,浇铸时随着浇铸液的逐渐硬化,材料一开始汽化,从材料二表面渗透挥发,由于材料二耐高温,留在球体内部,从而得到一个空心球体。此种方案其实只是一种理想的方案,在浇铸过程中可能出现材料一汽化后,材料二的强度不足被压溃,得不到空心球体,其次两种材料的存在性也未可知。因此此种方案实现起来十分困难,也不做深入探讨。
1、铸造型芯。
如下图一为铸造型芯的造型方案,为防止浇铸液流出,两沙箱之间有止口构造,为保证透气性和散热上沙箱上还要留有气孔,在浇筑过程中,为防止浇不足的现象也可适当给浇铸液加压或者从两个方向同时浇铸。浇铸完成之后铸件如右图二,铸件拼接之后留有凸台是为了能撑住空心球在沙箱内部作为型芯,6个凸台是为了保证其对中性更为良好。
方案三:由内到外浇铸。
此种方案是首先用QT500-7制作一个两个壁厚为5mm的空心半球,然后拼接在一起作为一个球模,浇铸时将此球模作为型芯,浇筑完成后就作为空心球的一部分留在空心球内部。此方案的优点是型芯不用取出,可以实现浇铸出一个完整的空心球,缺点是铸件并非是一个整体。此方案具有可行性,下面给出此方案的具体流程:
两个半球壳铸造完成之后,先用机加工在两铸造球壳出加工出止口的结构,然后采用过盈配合的方式将两球壳配合在一起,这样既能防止铁水渗漏到球壳内部,又能保持两球壳的对中性。
2、造砂型。
在浇铸成品之前,必须先制造一个和型芯一样的砂型。因此先做一个和空心球型芯一模一样的木模。如下图:
将此木模作为型芯,在沙箱内做出上图中的砂型。
较大位置安放电机,浇铸时一个旋转轴可以做成空心来作
为浇铸的通道。
此方案的优点是能最好的满足无缝无焊接的一个空心
球体,铸成后是一个完整球体。缺点是铸造起来比较困难,
铸完之后内部很可能产生缺陷,且设备构造较复杂,铸造
成本高。该方案实现起来较为困难,故不做更深的研究。
方案二:用熔模铸造。
熔模铸造较难实现,理想的方案是需要两种特殊的材料,一种是内部球模,要求该材料在一个特定的温度t能直接汽化挥发,另一种材料则是要求有良好的抗高温能力的涂料,且有透气性。用于涂在内部的球模上。
空心球墨铸铁球的铸造成形工艺设计专题报告
一、 设计题目与要求
材料:QT500-7
直径:Ø200 mm
壁厚:15 mm
造型方法:砂型造型
要求:
1可以采取任何工艺措施,但球外表面不允许焊接,可以打磨等。
2设计出铸造工艺方案
3画出铸造工艺图(查阅铸造工艺图的绘制规范)
二、设计分析与思路
空心球不易铸造,最大的难点就在于内部必须要有一个型芯,但如果要铸成一个光滑的球体,且不允许焊接的话,铸成之后内部的型芯就没法取出来。因此要铸成空心球大体上可以分这接个方面的思路:通过离心铸造、由内到外浇铸、熔模铸造。
三、设计方案
方案一:运用离心方法铸造。
要保证能得到一个壁厚为15mm的空心球,离心铸造过程中至少要保证有两个互相垂直的方向在浇铸时有圆周运动。可以仿照陀螺仪的构造,构造两个互相垂直的矩形框,两个矩形框套在一起用。内部的矩形框作旋转,外部的矩形框做与之相垂直的圆周运动,如下图:
图中棕色部分即为铸型位置。两个矩形框之间可以留
四、拓展部分
综合上述几种方案,只有方案三能稍微理想的做出一个空心球,除此我们小组也对另一个方案做了设想。我们知道在太空里金属液能自动收缩成一个完整的球形,由此我们小组做了一个设想,假如在太空中制造,能通过数学计算算出所需金属液色质量以及内部的空气量(考虑热胀冷缩),那么我们可以在太空里铸造,让金属液自己收缩成一个完整球形,然后再金属液内部注入一个气泡,通过一定的离心,让气泡居于金属液中心然后再冷却(太空里没有重力,因此也没有浮力),这样就能得到一个完美的空心球。由于资料的限制,这个只是一个设想,未能提出可行的方案。