滚轮注塑模具设计PPT
注塑模具设计.ppt
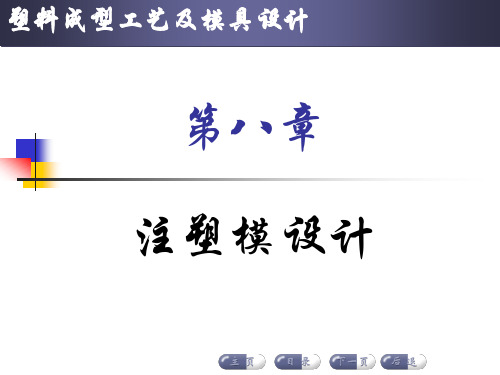
8.2.2 注塑机型号的确定
㈡ 计算校核注塑机成型工艺参数是否满足制品成型的要 求
1.最大注射量的校核计算
(0.8 0.85)V公 V型
(8-1)
式中
V公 -------注塑机公称注射量,cm3
V型 -------每模的塑料体积量,cm3;是所有型腔的 塑料加上浇注系统塑料的体积总和。
8.2.2 注塑机型号的确定
8.3.1 浇注系统设计
1. 主流道:从注塑机喷嘴与模具接触位起,到分流 道为止的这一段流道。作用是负责将塑料熔体输往分流 道。
2.分流道:介于主流道和浇口之间的一段流道,它开 设在分型面上。作用是将主流道送来的塑料分配后,输 往各个浇口。
3.浇口:连接分流道与型腔之间的一段细短通道。 4.冷却穴:一般在主流道的末端设置,以装纳冷却头。
塑料成型工艺及模具设计
第八章 注塑模设计
第8章 注塑模设计
本章基本内容
模具与注塑机的关系 浇注系统的组成及其设计原则 普通浇注系统的设计 无流道浇注系统的设计 注射模的设计程序
第8章 注塑模设计
学习目的与要求
了解注塑机的种类 掌握注塑模的设计程序 掌握浇注系统的组成、作用 掌握浇注系统设计原则。
8.2.2 注塑机型号的确定
2.模具厚度与注塑机模板的闭合厚度
安装模具的厚度(Hm)应在注塑机的 最大模具厚度和最小模具厚度之间,即:
Hmin < Hm < Hmax (8-7) 液压机械式锁模机构的注塑机- 图8-6
8.2.2 注塑机型号的确定
3.模具定位圈与注塑机定位孔,模具主流道端与喷嘴的 配合
3.锁模力的校核
锁模力又称合模力。注塑机的锁模力必须大于模
《注塑模具基础知识》PPT课件
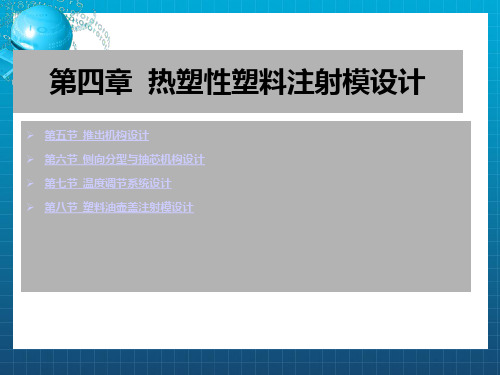
的一种脱模机构。一般有以下几种形式。
• 1.推杆脱模机构
• (1) 机构组成和动作原理
•
推杆脱模是最典型的一次推出机构,它结构简
单,制造容易且维修方便,其机构组成和动作原理如
图4-76所示。它是由推杆1、推杆固定板2、推板导套 3、推板导柱4、推杆垫板5、拉料杆6、复位杆7和限
位钉8等所组成的。推杆、拉料杆、复位杆都装在推 杆固定板2上,然后用螺钉将推杆固定板和推杆垫板
2+L3。
•
拉板脱模机构的优点是省去了推杆及其固定板,可简化模具结构,减小模具高度
,对于开模行程受模具高度影响的注射机,可以增大有效开模行程,增加脱模距。
• 6.多元件组合推出脱模机构
•
对于一些深腔壳体、薄壁制品以及带有局部环状凸起、凸肋或金属嵌件的复杂制
,然后再将塑件从动模上推下,脱螺纹机构也有手动和机动两种方式。
4.5.2 推出力的计算
•
注射成形过程中,型腔内熔融塑料因固化收缩包在型芯上,为使塑件能自动脱落
,在模具开启后就需在塑件上施加一推出力。推出力是确定推出机构结构和尺寸的依
据,其近似计算式为:
•
F=A p(μcosα-sinα) (4-23)
与推板用螺纹联接,见图4-83(a)。应注意,该种结构在合模时,推板与模具底脚之间
应留S=2~3mm的间隙。当导柱足够长时,推杆与推板也可不作联接,见图4-83(b)。对
于有多个圆柱型芯相配的推件板,大多镶上淬火套与型芯相配,便于加工和调换,见
图4-83(a)。图4-83(c)的结构适用于两侧具有推杆的注射机,模具结构可简化,但推板要
• 想一想
•
除了复位杆和弹簧复位之外,还有什么复位方法?
滚轮注射模具设计设计

滚轮注射模具设计摘要本设计是关于塑料制件的模具设计。
综合材料成型的各种工艺方式,本课题设置为注射模具设计。
其中包括注射模的成形零件、工作零件、各种定位机构及导向结构的设计等。
随着塑料的应用领域扩大化,塑料零件的注射模具已成为工厂推崇的产品之一。
产品的寿命及性能也是厂商的重要考虑因素。
模具零件的标准化使用频率越来越高,及标准模具的选用越来越多。
模具标准化程度在一方面体现了社会商品的交换程度。
这也是本次设计重点考察因素之一。
塑料的性能,如此处ABS的应用,在一定程度上反应塑料的适用范围。
本设计的制品是滚轮。
对滚轮结构的合理分析是设计模具的基础。
科学合理的选择有利的分型面及成型方案是本设计应该纳入的核心问题。
此外,设计者的独特设计风格为以后设计提供参考。
设计参考一些前辈们的设计理念以及相关资料的数据。
互联网及书本是本设计重要的参考资料。
老师的指正及学生们的讨论让设计渐渐完善。
模具设计的技术交流是模具设计空间提升的重要方式。
经济全球化离不开技术交流。
关键词:模具,塑料,滚轮,标准化,技术交流Trolley Wheel Plastic Mold DesignABSTRACTThis subject is mainly about mold design, which is used to produce products made in plastic. Compared with many kinds of forming technology, this subject is aimed at injection mold design. This design includes these topics, like forming parts, working parts, all kinds of detent mechanism and positioning structure design, and so on.With the expansion of application domain, injection mold to produce plastic goods has become one of more and more popular products in factories. The age and function of mold is some of important factors. The application of mold standardization appears in factories frequently, and the selection of standard mold is more and more considered. The level of mold standardization implies the frequency about the exchange of social commodities. This topic is also one of significant considerations.The application domain of plastic, like the application of ABS in this subject, responds to the function of plastic in some areas. The goods in this subject are trolley wheel. The reasonable analysis is the base of the mold design. How to select reasonable joint face and forming technology should take into account in the key topic of the design. Besides, the special style of designer can offer some reference in the later design.This design consults many design ideas of predecessors and some data about the subject. Internet and books are important reference material. The design is becoming more perfect under the help of teachers and the discussion between students. The exchange of technology experience is an important way to improve the mold design level. Economic globalism can never realize without the exchange of technology.KEY WORDS: mold,plastic,trolley wheel,standardization,exchange of technology目录前言 (1)第1章前期准备 (3)1.1了解设计任务书 (3)1.1.1接受任务书 (3)1.1.2任务书分析 (3)1.1.3资料准备及时间安排 (4)第2章分析工艺方案的制定依据 (5)2.1制件应用领域 (5)2.1.1滚轮的使用环境 (5)2.2制件工艺性分析 (5)2.2.1材料分析 (5)2.2.2结构分析 (6)第3章核心设计及注射机初选 (8)3.1选择分型面 (8)3.1.1分型面的设计方案 (8)3.1.2分型面的确定 (9)3.2型腔设计 (11)3.2.1型腔的数目 (11)3.2.2型腔的布置 (11)3.3装配草案初定 (11)3.3.1分析设计总结构 (11)3.3.2绘制装配初稿 (12)3.3.3修改草稿定方向 (13)3.4注射机的初选 (14)3.4.1注射机的种类及结构 (14)3.4.2注射机初定 (14)第4章模具结构设计 (16)4.1.1凸模(型芯)设计 (16)4.1.2瓣合凹模(滑块)设计 (16)4.2浇注系统及排溢系统的结构设计 (17)4.2.1流道的设定 (17)4.2.2浇口的设定 (18)4.2.3冷料穴的设定 (19)4.2.4排气槽的设定 (20)4.3温度调节系统的结构设计 (20)4.3.1温度调节对生产率的影响 (20)4.3.2冷却位置的选择 (20)4.3.3冷却水道的布局 (21)4.4脱模机构的设计 (21)4.4.1推出距离计算 (22)4.4.2推出结构的设定 (22)4.5导向和定位的结构设计 (23)4.5.1导柱导套的布局 (23)4.5.2导柱导套的结构设定 (24)4.5.3螺钉和销钉的布局 (25)4.6模具与注射机连接结构设计 (25)4.6.1定位圈的选择 (25)4.6.2动模座板孔径及模具安装方式 (26)第5章绘制装配图及零件图 (27)5.1成形零件的尺寸计算 (27)5.1.1制件尺寸精度分析 (27)5.1.2凸凹模对应尺寸计算 (27)5.2模具标准化 (30)5.2.1模具标准化意义 (30)5.2.2模具的标准化程度选择 (30)5.2.3绘制装配草图 (31)5.3.1推杆强度校核 (32)5.3.2最大注射量校核 (32)5.3.3注射压力校核 (32)5.3.4锁模力校核 (32)5.3.5安装部位的尺寸校核 (33)5.3.6开模行程和顶出结构的校核 (33)5.4装配图修善 (33)5.4.1注射机的最终确定 (33)5.4.2根据数据变动修改装配图 (34)5.4.3完善装配图 (34)5.5零件图绘制 (34)5.5.1零件的分类及部分精度 (35)5.5.2主要零件的加工方法 (35)第6章模具的使用及价格估算 (38)6.1模具价格估算 (38)6.1.1影响价格因素 (38)6.1.2简单估算法 (38)6.1.3详细计算法 (39)6.2模具的使用 (39)6.2.1模具的安装 (39)6.2.2试模及验收 (39)6.2.3管理及维修 (39)结论 (41)谢辞 (43)参考文献 (44)附录 (45)外文资料翻译 (47)前言随着塑料的应用广泛,新材料的不断涌现,掌握一种材料的成型方式是本专业学习者应有的能力。
注塑模设计PPT课件

第3章 常用塑料、制品的注射成型 3.1 常见塑料的注射成型 四、PA6(聚酰胺6或尼龙6) (1)典型应用范围
由于有很好的机械强度和刚度被广泛 用于结构部件。 由于有很好的耐磨损特性,还用于制 造轴承。
•12
第3章 常用塑料、制品的注射成型 3.1 常见塑料的注射成型
四、PA6(聚酰胺6或尼龙6)
•21
第3章 常用塑料、制品的注射成型 3.1 常见塑料的注射成型 六、PVC (聚氯乙烯) (1)典型应用范围
供水管道,家用管道,房屋墙板,商 用机器壳体,电子产品包装,医疗器械, 食品包装等。
(2)注塑工艺及模具条件
干燥处理:通常不需要干燥处理。 熔化温度:185~205℃ 模具温度:20~50℃
聚物。
➢一个是苯乙烯-丙烯腈的 连续相;
➢另一个是聚丁二烯橡胶 分散相。
ABS的特性主要取决 于三种单体的比率以 及两相中的分子结构。 这就可以在产品设计 上具有很大的灵活性。
④ABS材料具有超强的易加工性,外观特性,低蠕 变性和优异的尺寸稳定性以及很高的抗冲击强度。
•4
第3章 常用塑料、制品的注射成型 3.1 常见塑料的注射成型 二、PC(聚碳酸酯) (1)典型应用范围
(2)注塑工艺及模具条件
干燥处理:如果材料是用防水 材料包装供应的,则容器应保持 密闭。如果湿度大于0.2%,建 议在80℃以上的热空气中干燥16 小时。如果材料已经在空气中暴 露超过8小时,建议进行105℃, 8小时以上的真空烘干。 熔化温度:230~280℃,对于 增强品种为250~280℃。 模具温度:80~90℃。
第3章 常用塑料、制品的注射成型 3.1 常见塑料的注射成型
一、ABS(丙烯腈-丁二烯-苯乙烯共聚物)
注塑成型模具设计PPT课件
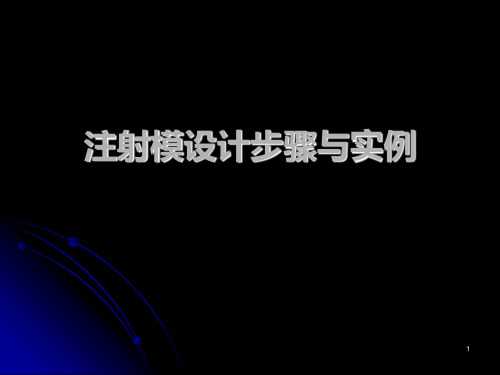
⑵确定型腔的排列方式
拟采用一模两件,考虑浇注系统、模具结构的复杂成程度等因素,拟采用如图 所示的型腔排列方式,其最大优点是便于设置侧向分型抽芯机构。其缺点是熔 料进入型腔后到另一端的料流长度较长,但因本塑件较小,故成型时没有太大 的影响。
图3
9
(3)浇注系统设计
①主流道设计 根据设计手册查得XS-Z-60型注射机喷嘴的有关尺寸为喷嘴 前端孔径d1=φ4mm;喷嘴前端球面半径SR1=12mm。
孔 该塑件有两个13.5×12mm通孔,型芯结构简单,便于安放
侧孔和侧凹 该塑件在宽度方向的一侧有两个4.5×1mm的凸耳 及两个4.1×1.2mm的凹槽,因此,模具设计时必须设置侧向分 型抽芯机构
通过以上分析可见,该塑件结构属于高精度、中等复杂程度。 要严格控制影响塑件精度各个因素,如通过严格控制成型过程 中聚丙烯的收缩率的波动、提高模具成型零件的制造精度等。 塑件结构工艺性较为合理,成型零件采用组合式模具结构,6侧 向凸台和侧孔需用侧向分型抽芯机构成型。
5
脱模斜度 该塑件为开口壳类零件,深度较浅且大圆弧过渡,脱 模容易,故不需考虑脱模斜度。
加强筋 该塑件结构较为复杂,自身结构具有加强筋作用,强度 足够。
圆角 该塑件对圆角没有提出要求,结构工艺性较差,不利于塑 件的成型,建议与用户协调在满足使用要求的前提下在料流转 角处增设圆角;如果不行,模具成型零件应采用组合式结构, 避免应力集中。
另加3~5mm的抽芯安全系数,可取抽芯距S抽=4.9mm。 ②确定斜导柱倾角 斜导柱的倾角是斜抽芯机构的主要技术
参数之一,它与抽拔力以及抽芯距有直接关系,—般取 α=15°~20°,本例中选取α=20°。
尺寸精度 该零件重要尺寸如:12.1mm、12.1 mm、15.1mm、 15mm等精度为3级,次重要尺寸如:13.5 mm、17mm、 10.5mm、14mm等的尺寸精度为4~5级。
滚轮注塑模具设计

目录一、塑件成型工艺设计二、分型面位置及型腔数目的确定三、成型零部件的结构设计四、成型零部件的尺寸计算五、浇注系统设计六、导向机构设计七、推出机构设计八、温度调节及排气系统设计九、结构零部件设计及模架选择十、注射机选择十一、模具零部件材料的选用十二、模具的装配及调试一、塑件成形工艺分析1.1塑件的尺寸和精度分析该塑件的尺寸如下图所示:该塑件无尺寸精度特殊要求,所有尺寸均为自由尺寸,按MT5查取公差。
其主要尺寸公差要求如表所示:1.2 塑件表面质量分析该塑件表面没有提出特殊要求,一般情况下外表面要求光洁,表面粗糙度可以取到0.8aR mμ=。
没有特殊要求时,塑件内部表面粗糙度可取 3.2aR mμ=。
1.3塑件结构工艺性分析(1)壁厚分析:设计合理,壁厚相对均匀。
(2)圆角过渡:要从分型面位置、型芯、型腔结构来分析过渡圆角的设置。
根据本塑件的壁厚,均采用圆角半径R1mm。
(3)脱模斜度:为便于塑件从模腔中取出,塑件的内外壁需要足够的脱塑件标注尺寸塑件尺寸公差(按MT5级精度)塑件标注尺寸塑件尺寸公差(按MT5级精度)外圆尺寸Φ27.5Φ27.5-0.56内孔尺寸Φ4.5Φ4.5+0.56内圆尺寸21.521.5+0.24圆角R1 R1+0.2模斜度。
外形尺寸以大端为基准,斜度往小处取;内形尺寸以小端为基准,斜度往大处取。
型芯脱模斜度为:0.7°,型腔脱模斜度为0.5°1.4 生产实际考虑该塑件的生产类型应该是大批量生产,因此在设计模具时,要提要塑件的生产效率,倾向于采用多型腔、高寿命、自动脱模的模具。
二、分型面位置及型腔数目的确定2.1型腔数目的确定确定型腔数目时应该考虑塑件制品的精度、经济性、成型工艺、保养和维修。
该模具的主要特点是:一模多腔而又结构紧凑,采用的潜伏式浇口在顶出时被切断并自行脱落,省去了浇口工序,因此很适合大批量生产。
2.2确定型腔布局模具采用一模十二腔,布局如下图所示:2.3分型面的选择根据分型面的选择原则,分型面应选择在塑件外形的最大轮廓处,且分型面的选择应有有利于塑件的留模及脱模,而且还要保证塑件的精度要求,满足塑件的外观要求及边缘模具的制造,同时还得考虑模具的排气效果等等。
注塑模具齿轮模具设计及重点.ppt
谷崧塑膠零件模具廠
齒輪模具設計及重點
1.齒輪材質(塑膠)的特性(POM \PC\ PA\)常用的是POM 其次PA其縮水
塑 大眾(16/1000到25/1000不等)孔的收縮率通常是25/1000大於其它部位
膠 的3/1000到5/1000
齒 2.齒輪的精度常用有3.4.5三級.(本公司最高做到3級常見是4.5級)齒的等
谷崧塑膠零件模具廠
齒輪模具設計及重點
圖其 齒 所定 輪 示位 模
极具 其的 重模 要仁 必通 須常 采采 用用 防的 呆是 功圓 能形 如的
CXSON
谷崧塑膠零件模具廠
齒輪模具設計及重點
圖其 齒 所定 輪 示位 模
极具 其的 重模 要仁 必通 須常 采采 用用 防的 呆是 功圓 能形 如的
CXSON
齒輪模具設計及重點
左圖所示是常用 的齒套依圖所示 排氯位置大小﹐
左圖所示是常用 的齒套依圖所示 標注齒套重點寸 法﹐以及定位畫 法
左圖所示是常用 的齒套線割齒形 的參數此參數是 已加縮水(每一項 參數都要加縮水)
CXSON
谷崧塑膠零件模具廠
齒輪模具設計及重點
左圖是齒輪模 的母模仁依圖 所示其注入口 是3點進膠是3 等分是最佳的 設計方式其注 入口的大小通 常在0.7~1.2之 間
塑 膠 齒 輪 的 介 紹
谷崧塑膠零件模具廠
齒輪模具設計及重點
CXSON
塑 膠 齒 輪 的 介 紹
谷崧塑膠零件模具廠
齒輪模具設計及重點
CXSON
塑 膠 齒 輪 的 介 紹
谷崧塑膠零件模具廠
齒輪模具設計及重點
以上是齒輪產品測量單齒齒輪的換算表Z是齒數 H是換算參數,實測值除換算參數等於實際齒外徑
注塑工艺与模具设计PPT课件
模具设计
注塑模具设计思路 本钱设计:模具材料本钱,成型产品本钱,标准件使用本钱等。 模具维护设计:维修配件结构、备用配件、可拆装性配件、复原性能;
模具设计
30%加工
切割加工、热处理、 放电、慢走 丝、氧化性、 组装等
35%销售管 理试模杂费
20%设计费
15%材料费
模具制作费用
破损与修理费用
注塑工艺根底
流动性快
进料点
先冷却, 流动 性慢
模具冷料 井
注塑工艺根底
压力如何影响产品结构及外观 压力会使分子紧靠在一起,收缩性变小,密度变小; 压力缺乏会导致产品不饱模/缩水,会限制注射速度控制系统提供快速射
出的能力; 压力过大会导致产品毛边/批峰/冲胶。
注塑工艺根底
结晶结构 • 模具温度越高,结晶时间越长,结晶体越大,收缩越大,不均匀结晶
〔产品胶料用量〕压力过小,机器喷嘴与模具未对准。可根据实际情 况调试相关参数进行改善。
现场问题
毛边、批峰 • 塑胶熔体流入分模面或镶件合面将产生毛边批峰。 • 熔体的粘度、压力和间隙的宽度决定是否出现毛边。绝大多数胶料来
说,在的间隙一般都不会产生毛边。熔体尽量进入,但立刻凝固,堵 住流动。
现场问题
注塑马 达
注塑成型工艺根底—设备介绍
上段温 度
调整
中段温 度
度调整
下段温 度
度调整
工作台
冷却水循环 器
开模高度 设定钮
慢速关模 设定阀
高压关模 设定阀
射胶时 间
调整
松退时 间
调整
冷却时 间
调整
注塑成型工艺根底—设备介绍
射出速 度调整
背压调 整阀
注塑成型模具设计PPT课件
1
1 注射模设计基本程序
1.了解塑件的技术要求 2.根据塑件形状尺寸,估算塑件体积和重量 3.分析塑件,确定成形方案 4.绘制方案草图 5.设计计算 6.绘制模具设计总装图 7.绘制零件工作图 8,经过全面审核后投产加工
2
2 注射模设计实例
塑料制品如图,大批量生产,试进行塑件的成型工艺和模具设计。
尺寸精度 该零件重要尺寸如:12.1mm、12.1 mm、15.1mm、 15mm等精度为3级,次重要尺寸如:13.5 mm、17mm、 10.5mm、14mm等的尺寸精度为4~5级。
壁厚 壁厚最大处为1.3mm,最小处为0.95mm,壁厚差为 0.35mm,较均匀,有利于零件的成型。
表面质量 该零件的表面除要求没有缺陷、毛刺,内部不得有导 电杂质外,没有特别的表面质量要求,查表可取塑件表面粗糙 度Ra1.6,对应模具成型零件工作部分表面粗糙度为Ra0.4~0.8, 故比较容易实现。
另加3~5mm的抽芯安全系数,可取抽芯距S抽=4.9mm。 ②确定斜导柱倾角 斜导柱的倾角是斜抽芯机构的主要技术
参数之一,它与抽拔力以及抽芯距有直接关系,—般取 α=15°~20°,本例中选取α=20°。
③确定斜导柱的尺寸 斜导柱的直径取决于抽拨力及其倾斜 角度,可按设计资料的有关公式进行计算,本例采用经验估 值,取斜导柱的直径d=14mm。斜导柱的长度根据抽芯距、 固定端模板的厚度、斜销直径及斜角大小确定(参见斜导柱 长度计算公式)。
②下凹模镶块型腔侧壁厚度计算 下凹模镶块型腔为组合式矩形型腔,根据
组合式矩形侧壁厚度计算公式
S强 .
pH1l 2
2H
取p=40MPa(选定值);b=12mm;l=16.95mm;H1=12-1.3=10.7mm; H=H1+h=35.7mm;[σ]=160MPa(底板材料选定为45钢)。代人公式计 算得:S强=3.28mm。
《注塑模具结构动画演示》PPT课件
上一页
下一页
15
滑块脱模_外螺纹
上一页
下一页
16
推板推出
上一页
下一页
17
推杆推出_加强筋
上一页
下一页
18
推杆推出_斜面
上一页
下一页
19
推杆顶出
上一页
下一页
20
推杆推出
上一页
下一页
21
推杆推出
上一页
下一页
22
延迟推出
上一页
下一页
23
圆锥杆顶出
上一页
下一页
24
主流道的顶出形式
上一页
下一页
上一页
下一页
59
推管主型芯固定于动模型芯固定板的形式
上一页
下一页
60
推块脱模机构形式
上一页
下一页
61
推块脱模机构形式
上一页
下一页
62
镶拼式侧隙引气
上一页
下一页
63
镶拼式侧隙引气
上一页
下一页
64
镶拼式侧隙引气
上一页
下一页
65
斜面镶条定位形式 [示意图]
上一页
下一页
66
压缩空气配合推板脱模
注塑模具结构动画演示
(Suitable for teaching courseware and reports)
注塑模具经典结构动画演示
二级推出机构
上一页
下一页
3
可折叠型芯_三维
上一页
下一页
4
可折叠型芯_平面
上一页
下一页
5
侧向分型与抽芯机构_滑块
上一页
下一页
- 1、下载文档前请自行甄别文档内容的完整性,平台不提供额外的编辑、内容补充、找答案等附加服务。
- 2、"仅部分预览"的文档,不可在线预览部分如存在完整性等问题,可反馈申请退款(可完整预览的文档不适用该条件!)。
- 3、如文档侵犯您的权益,请联系客服反馈,我们会尽快为您处理(人工客服工作时间:9:00-18:30)。
模具零部件尺寸的设计
• 根据制品尺寸以及选用注射机型号等确定以下各 零部件的尺寸 1.定模固定板(205mmx245mmx20mm) 2.定模板 (170mmx245mmx30mm) 3.动模板 (170mmx245mmx40mm) 4.推板 (210mmx100mmx15mm) 5.推板固定板 (210mmx100mmx15mm) 材料为40Cr.
• 浇口是连接分流道和型腔之间的一段细短流道 (除直接浇口以外),是塑料注入型腔的入口。 浇口的形状、数量、尺寸和位置对塑件质量影响 很大,是浇注系统的关键部分
• 本设计采用潜伏式浇口。 • 潜伏浇口不影响美观;顶出时自动切断料把;对
于坚韧塑料,适应性差。有利于大批量生产。
成型零部件的设计
• 成型零件的结构设计主要是指构成模具型
XXXX大学本科毕业设计
指导教师:XXX
题目:滚轮注塑模具的设计 学生:0000 学号:000000000 专业:00000000
设计内容
注塑设备的选择 分型面的设计 浇注系统的设计 成型零部件的设计 合模导向机构的设计 定位机构的设计 塑件脱模机构的设计 注塑模温度调节系统的设计 排气系统的设计
模具结构
• 设计模具结构如右图 所示
• 模具为一模十二腔 • 由于制品பைடு நூலகம்构简单,
故采用推杆顶出
浇注系统设计
• 普通浇注系统一般由主流道、分流道、浇口和冷料井等四部分组成
• 主流道设计 • 根据所选注射机,主流道小端尺寸为:
d=注射机喷嘴尺寸+(0.5~1)=4+0.5 取 5mm
主流道球面半径尺寸为: SR=喷嘴球面半径+(2~3) =18+2=20mm 锥孔锥度取2~6度,根据主流道尺寸,确 定主流道衬套尺寸及形式,如右图。 • 主流道衬套由定位环固定在定模座板上 • 主流道衬套的形式有两种:一是主流道衬 套与定位环设计成整体式;二是主流道衬 套与定位环设计成两个零件,然后配合在 固定在定模座板上。
• 查模具设计手册后,本课题选 用XS—ZY-250型注射机,该型
锁模力 1800K 最小厚 200m
N
度
m
螺杆直 50mm 电机功 24KW
径
率
号的注射机的主要技术参数如 注压 147MP 定位圈 100m
下表
直径 m
最大开 500m 合模方 卧式
模行程 m
式
注射行 160m 注射方 螺杆式
程
m
式
设计任务
• 了解塑料模具行业的发展历史、发展现状和未来 的发展的整体趋势
• 复习、回顾在课堂上及课外实践中所学的专业技 术知识,并合理的运用到实际设计中去
• 设计滚轮注塑模具,掌握模具设计的原理和步骤 • 学习模具制造的工艺性,注意模具设计的过程中
应该注意的问题,寻找合理的解决方法 • 完成毕业设计二维图纸及毕业设计论文
• 缺点是可溶于酮类、 醛类及氯化烃中,受 冰乙酸、植物油等侵 蚀会产生应力开裂, 耐候性较差,在紫外
光下易降解。
注射成型设备的选择
• 在制品成型模具设计过程中首 额定注 250cm 最大厚 350m
先计算成型制品所需的注射量, 射量 3
度
m
然后再初步选择成型该制品的 注射机类型及型号
• Mn=M总/0.8=7.609g/0.8=9.511g
模具零部件
• 1.定模板
(170mmx245mmx30mm)
用于固定定模模仁 (型腔镶块)和导套。 应有一定厚度和强度。 一般用40Gr。其上导 套孔与导套一端采用 H7/k6配合,定模与 定模模仁采用H7/m6 配合。
模具零部件
• 4.推板
(210mmx100mmx15mm) 用4个内六角圆柱螺钉与 推板固定板固定,材料为 40Gr.
注塑模温度调节
• 模温对制品结晶度、力学性能、表面质量、内应力和翘曲 变形有很大影响,一般在整个成型周期中模内冷却时间约 占75%,因此提高冷却效率非常关键。该设计的冷却水道 布置如图:
致谢
• 四年的学习生活即将结束。在此,我要感 谢所有曾经教导过我的老师和关心过我的 同学,他们在我成长过程中给予了我很大 的帮助.
分流道的设计
• 分流道的常见断面形状有圆形、梯形、U形、正六边形、 半圆形、矩形等。
本模具中采用的是圆形断面分流道,这种分流道比表面积 最小,故热量散失最少,阻力亦小,浇口可开在六道中心 线上,因而延长了浇口冻结时间。缺点是需要同时在动模 和定模上切削加工,而且要相互吻合,故制造困难,费用 高。
浇口的选择
零件材料及性能分析
• 本课题所要设计模具成型的塑件如图, 选用ABS,热塑性材料,成型工艺性很 好,可以进行注射成型。
• 有优良的力学性能,冲击强度好,绝缘
性好,耐腐蚀,有优良的加工性,热稳
定性好,不易出现降解现象,吸水率高,
密度为1.05~1.18g/cm3,收缩率为
0.4%~0.9%,弹性模量值为2GPa,泊松比 为0.394,吸湿性小于1%,熔融温度 217~237摄氏度,热分解温度大于250摄 氏度。ABS不受水、无机盐、碱及多种 酸的影响。
• 本文能够顺利完成,要特别感谢XXX老师 的悉心指导.
• 最后向所有关心和帮助过我的人表示真心 的感谢.
型
腔的零件,通常有型腔、型芯、凹模、凸 模、镶块、各种成型杆和成型环。
腔
• 型腔是成型塑件外表 面的部件,按其结构 可分为整体式和组合 式两大类
• 因为本设计为一模十 二腔加工且塑件结构 简单尺寸较小,故采 用整体式凹模,如图
型芯
• 凸模也有整体式和组合 式之分,形状简单的主 型芯和模板可作成整体 的;形状比较复杂的, 或形状虽不复杂但从节 省贵重钢材和减少加工 量的角度考虑多采用组 合式,本次设计型芯为 组合式
导向机构的设计
• 导向机构主要有导向 定位和承受注射时产 生的侧压力三个作用
• 本课题对于导向机构 的设计采用了导柱 导向机构。采用四根 对称布置的导柱,安 装在定模板上,导柱 直径为12mm,总长为 55.5mm.
顶出机构的设计
• 脱模推出机构设计原则: • (1)推出机构应尽量设置在动模一侧 • (2)保证塑件在推出时不变形或损坏 • (3)机构简单动作可靠 • (4)良好的塑件外观 • (5)合模时的正确复位