材料疲劳特性参数定义
材料力学性能-疲劳

第九讲:材料在交变载荷下的力学行为(下)
2016-04-22
温故而知新:
交变载荷及其重要参数; 交变载荷下的材料力学行为:疲劳及疲劳损伤; 金属疲劳破坏的特点:
阶段分明、低应力、不可预测
S-N曲线; 疲劳缺口敏感度; 疲劳裂纹扩展速率,Paris方程,Forman方程。
本讲重点(第9讲):材料在交变载荷下的力学行为
经验表明,若把总应变幅 ∆ε 分解为弹性应变幅 ∆εe 和塑性应变幅 ∆εp 时,二者 与循环次数的关系都可以近似用直线表示。
仿照静拉伸时的真应力-真应变表达式,循环应力-
应变中的塑性部分表达式可以写为:
σ
ห้องสมุดไป่ตู้
p
=
K ′
∆ε p 2
n′
K ′:循环应变的强度系数
n′ :循环加载下的形变硬化指数,一般0.1~0.2。
∆ε e
2
=
σ ′f
E
(2N f
)b
由此,Manson-Coffin提出塑性应变幅∆εp/2和疲劳寿命2Nf的 关系:即Manson-Coffin方程 :
循环软化:应变幅恒定条件下, 变形抗力随周次的增加而不断减小 、应变逐渐增加的现象。危险!
经验表明:
Manson等人根据大量试验结果,归纳出预测材料发生循环硬化或软化的判据 (一次拉伸σb/σ0.2):当σb/σ0.2 >1.4时,材料发生硬化;当σb/σ0.2 <1.2时,材料发生 软化;比值介于1.2~1.4之间时,难以判断;
低周疲劳和高周疲劳:
低周疲劳特点: 交变载荷大; 塑性变形; 寿命短,只有几千次。
高周疲劳特点: 交变载荷小,频率高; 弹性变形; 寿命长; 蠕变为主。
金属材料的力学性能-疲劳强度

金属材料的力学性能-疲劳强度疲劳强度:机械零件,如轴、齿轮、轴承、叶片、弹簧等,在工作过程中各点的应力随时间作周期性的变化,这种随时间作周期性变化的应力称为交变应力(也称循环应力)。
在交变应力的作用下,虽然零件所承受的应力低于材料的屈服点,但经过较长时间的工作后产生裂纹或突然发生完全断裂的现象称为金属的疲劳。
疲劳强度是指金属材料在无限多次交变载荷作用下而不破坏的最大应力称为疲劳强度或疲劳极限。
实际上,金属材料并不可能作无限多次交变载荷试验。
一般试验时规定,钢在经受107次、非铁(有色)金属材料经受108次交变载荷作用时不产生断裂时的最大应力称为疲劳强度。
疲劳破坏是机械零件失效的主要原因之一。
据统计,在机械零件失效中大约有80%以上属于疲劳破坏,而且疲劳破坏前没有明显的变形,所以疲劳破坏经常造成重大事故,所以对于轴、齿轮、轴承、叶片、弹簧等承受交变载荷的零件要选择疲劳强度较好的材料来制造。
材料的疲劳性能

图5-11
2020/5/4
● 三、 过载持久值及过载损伤界 ●研究意义: ●过去人们一直认为,承受交变载荷作用的机件
按-1确定许用应力是安全的,但是没有考虑特
殊情况。实际上,机件在服役过程中不可避免 地要受到偶然的过载荷作用,如汽车的急刹车、 突然启动等。还有些机件不要求无限寿命,而 是在高于疲劳极限的应力水平下进行有限寿命 的服役。在这些情况下,仅依据材料的疲劳极 限是不能全面准确评定材料的抗疲劳性能的, 所以我们要了解过载持久值和过载损伤界。
2020/5/4
规则周期变动应力(循环应力) 无规则随机变动应力
变动应力如图5-1 所示。
生产中机件正常工作 时,其变动应力多为循 环应力,实验室也容易 模拟,所以研究较多。
应力大小变化
应力大小、方向无规则变化
应力大小、方向都变化
2020/5/4
图5-1 变动应力示意图
σ
r=0 r=–1
r=–∞
1 1
2
2
8
3
3 5 7 9
4
46
5
6
10 12 14
11 13
水平下进行,如图5-8所示。
图5-8 升降法测定疲劳极限示意图
原则是:凡前一个试样达不到规定的循环周次就断裂(用
表示),则后一个试样就在低一级应力水平下进行试验;若
前一个试样在规定循环周次下仍然未断(用 表示),则后一个
试样就在高一级应力水平下进行,如此得到13个以上的有效
●本章主要介绍:
● 金制 属。 疲介 劳绍 的估 基算 本裂 概纹 念形 和成 一寿 般命 规的 律方 。法 疲。 劳 失 效 的 过 程 和 机
2020/5/4
第一节疲劳破坏的一般规律
机械设计课件03第三章

计算安全系数及疲劳强度条件为:
a. AOJ区域内:smin为负值; b. GIC区域内:按静强度计算;
Sca
ss s lim s s S s s max s a s m
c. OJGI区域内:疲劳极限
s max 2s 1 ( Ks s )s min Sca S s max ( Ks s )(2s a s min )
r
s min s max
-1<r<1(r≠0)
非对称循环应力
r = -1 对称循环应力
r =0 脉动循环应力
r =1 静应力
§3-1 材料的疲劳特性
二、 s -N疲劳曲线(r一定)
AB段:静应力强度 ,N≤ 103 BC段:低周疲劳(应变疲劳), 103 ≤ N≤ 104 ,N , σmax CD段:有限寿命疲劳,N> 104
ks 1 1
各系数查取见附表
§3-2 机械零件的疲劳强度计算
二、单向稳定变应力时的疲劳强度计算 强度计算式: S s lim s max S ca
计算步骤:
机械零件的疲劳强度计算2
s
s max
求得危险截面的 smax及s
min
据此计算出sm及sa
标出M(sm ,sa )(或N) 根据应力变化规律找到对应的 极限应力值 由强度计算式求出sca
式中ρ1和ρ2 分别为两零件初始接触线处的曲率半径, 其中 正号用于外接触,负号用于内接触。 注意:接触变应力是一个脉动循环变应力
思考题:3-9 3-13 作 业: 3-18 3-20 3-21
四、双向稳定变应力时的疲劳强度计算
当零件上同时作用有同相位的稳定对称循环变应力sa 和ta时, 由实验得出的极限应力关系式为:
§3-1 材料的疲劳特性.
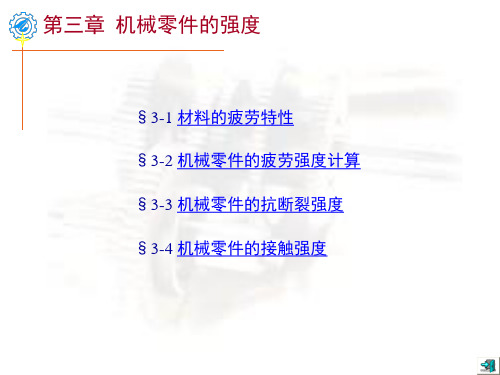
通过对大量结构断裂事故分析表明,结构内部裂纹和缺陷的存在是 导致低应力断裂的内在原因。
对于高强度材料,一方面是它的强度高(即许用应力高),另一方 面则是它抵抗裂纹扩展的能力要随着强度的增高而下降。因此,用传统 的强度理论计算高强度材料结构的强度问题,就存在一定的危险性。 断裂力学——是研究带有裂纹或带有尖缺口的结构或构件的强度和 变形规律的学科。准确的说,上述裂纹是指宏观裂纹,即用肉眼或低倍 显微镜能看得见的裂纹。工程中常认为裂纹尺寸大于0.1mm,就称为宏 观裂纹。断裂力学建立了构件的裂纹尺寸、工作应力以及材料抵抗裂纹 扩展能力三者之间的定量关系。
z r s
m s rN N s rm N 0 C
s rN s r (N N D )
有限寿命区间内循环次数N与疲劳极限srN的关系为:
s rN s
m N0 r Nr
K Ns r
式中, sr、N0及m的值由材料试验确定。KN寿命系数.
三、等寿命疲劳曲线(极限应力线图)
材料的疲劳特性
不同应力比时材料的疲劳极限也不相同,可用极限应力线图表示。
第三章 机械零件的强度
§3-1 材料的疲劳特性
§3-2 机械零件的疲劳强度计算 §3-3 机械零件的抗断裂强度 §3-4 机械零件的接触强度
材料的疲劳特性
二、 s-N疲劳曲线 疲劳极限:应力循环特性r一定时,应力经 过N次循环而材料不发生疲劳破坏的最大应 力。 r一定时,极限应力与应力循环次数的关系 曲线称为疲劳曲线。
二、 材料的疲劳曲线
材料的疲劳特性
材料的疲劳特性
疲劳曲线
机械零件的疲劳大多发生在s-N曲线的 CD段,可用下式描述:
m s rN N C ( NC N ND ) D点以后的疲劳曲线呈一水平线,代表着 无限寿命区其方程为:
如何在工程力学中评估结构的疲劳性能?
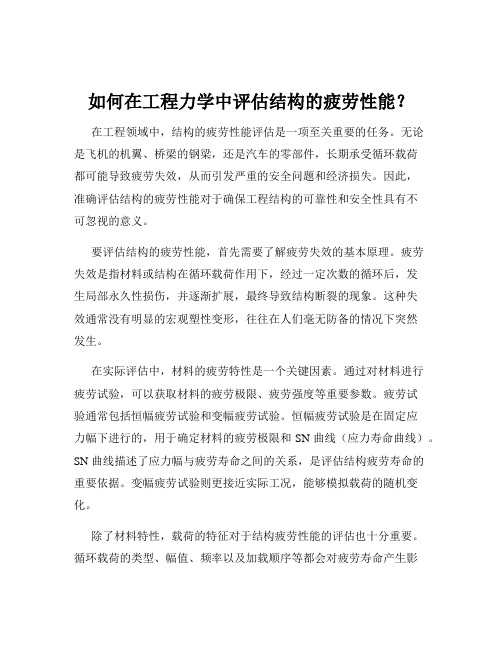
如何在工程力学中评估结构的疲劳性能?在工程领域中,结构的疲劳性能评估是一项至关重要的任务。
无论是飞机的机翼、桥梁的钢梁,还是汽车的零部件,长期承受循环载荷都可能导致疲劳失效,从而引发严重的安全问题和经济损失。
因此,准确评估结构的疲劳性能对于确保工程结构的可靠性和安全性具有不可忽视的意义。
要评估结构的疲劳性能,首先需要了解疲劳失效的基本原理。
疲劳失效是指材料或结构在循环载荷作用下,经过一定次数的循环后,发生局部永久性损伤,并逐渐扩展,最终导致结构断裂的现象。
这种失效通常没有明显的宏观塑性变形,往往在人们毫无防备的情况下突然发生。
在实际评估中,材料的疲劳特性是一个关键因素。
通过对材料进行疲劳试验,可以获取材料的疲劳极限、疲劳强度等重要参数。
疲劳试验通常包括恒幅疲劳试验和变幅疲劳试验。
恒幅疲劳试验是在固定应力幅下进行的,用于确定材料的疲劳极限和 SN 曲线(应力寿命曲线)。
SN 曲线描述了应力幅与疲劳寿命之间的关系,是评估结构疲劳寿命的重要依据。
变幅疲劳试验则更接近实际工况,能够模拟载荷的随机变化。
除了材料特性,载荷的特征对于结构疲劳性能的评估也十分重要。
循环载荷的类型、幅值、频率以及加载顺序等都会对疲劳寿命产生影响。
例如,高幅值、低频率的载荷往往会加速疲劳损伤的积累,而复杂的加载顺序可能导致疲劳寿命的预测变得更加困难。
结构的几何形状和尺寸同样不能忽视。
存在应力集中的部位,如孔洞、缺口、倒角等,容易引发疲劳裂纹的萌生和扩展。
因此,在设计阶段就需要对结构的几何形状进行优化,尽量减少应力集中的现象。
同时,结构的尺寸也会影响疲劳性能,较大尺寸的结构可能存在更多的内部缺陷,从而降低疲劳强度。
对于复杂的工程结构,有限元分析(FEA)是一种常用的评估方法。
通过建立结构的有限元模型,可以计算出结构在不同载荷条件下的应力分布和应变情况。
结合材料的疲劳特性,可以预测结构的疲劳寿命和可能的失效部位。
然而,有限元分析的准确性取决于模型的精度、材料参数的准确性以及所采用的疲劳寿命预测模型。
疲劳分析1
ANSYS帮助中疲劳一章的翻译(1)(资料来源:半导体仿真论坛—)第13章疲劳13.1 疲劳的定义疲劳是结构在承受低于其极限载荷的力的反复作用下发生破裂的现象。
例如,一根钢条或许可以承受只有300KN的静态拉力的作用,但在200KN的力的反复作用下,就很可能发生破坏。
引起疲劳失效的主要因素包括:·经历的载荷周期数;·单周期内应力的变化幅度;·单周期内的平均应力;·局部应力集中的存在。
当计算在预计的生命周期中某个部分的耗用状况时,一个正式的疲劳评估要涉及以上任何一个因素。
13.1.1 ANSYS程序的任务ANSYS 疲劳计算是以ASME锅炉与压力容器规范的第3部分(和第8部分第二章)为依据,采用了简化了的弹塑性假设和Miner累积疲劳准则。
除了基于ASME规范的疲劳计算外,用户也可以自己定义宏指令,或者用合适的第三方程序与ANSYS分析结果相接。
(更多信息请参考ANSYS APDL程序指南)ANSYS有以下疲劳计算能力:·用户可以对现有的应力结果进行后处理来确定任何实体单元和壳单元的疲劳耗用因数(对线单元模型疲劳分析用户也可以手工输入应力)。
·用户可以在预先选定的位置上确定一定数目的事件以及这些事件中的载荷,然后保存这些位置上的应力。
·用户可以为每个位置定义应力集中系数和给每个事件定义比例因数。
13.1.2 基本术语位置在模型上所要保存疲劳应力的节点。
用户通常可以选取结构上易于发生疲劳破坏的的点的位置。
事件是在某个特定的应力循环中出现在不同的时刻的一系列应力状态。
更多信息请参考本章后面的获取精确耗用系数指南。
载荷一个应力状态,是事件的一部分。
交变应力强度是任何两个载荷间的应力状态的差的测量值,程序不因平均应力的影响而调整交变应力强度。
13.2 疲劳计算的步骤疲劳计算是应力计算结束后在通用后处理器POST1中进行的。
通常包括以下五个主要步骤:1. 进入通用后处理POST1,恢复数据库;2. 设定尺寸(位置﹑事件和载荷的数目),定义疲劳材料特性,确定应力位置,定义应力集中因数。
机械结构的疲劳特性分析与优化
机械结构的疲劳特性分析与优化引言:机械结构在实际应用中,经常会受到长期使用和循环加载的影响,从而导致疲劳破坏。
为了确保机械结构的可靠性和寿命,研究其疲劳特性并进行优化设计非常重要。
本文将从疲劳的基本概念入手,探讨机械结构的疲劳分析方法,并介绍一些常见的疲劳优化技术。
第一部分:疲劳的基本概念与机制1.1 疲劳定义和分类疲劳是指物体在连续循环加载下发生的失效现象,主要分为低周疲劳和高周疲劳两种。
低周疲劳发生在加载次数较少的情况下,而高周疲劳则发生在加载次数较多的情况下。
1.2 疲劳破坏的机制疲劳破坏的机制主要包括裂纹的形成与扩展。
在循环加载下,结构内部会出现微小缺陷,随着加载次数的增加,缺陷处会出现应力集中,导致裂纹的形成。
随后,裂纹会在加载过程中不断扩展,最终导致结构破坏。
第二部分:机械结构的疲劳分析方法2.1 应力分析方法应力分析是疲劳分析的基础,可以通过有限元分析等方法获取结构在不同工况下的应力分布。
应力分析可以帮助确定结构的疲劳寿命和受力集中区域。
2.2 疲劳损伤累积理论主要包括极限应力法、应力幅与寿命曲线法、振幅频率公式法等。
这些方法可以根据实测应力历程和材料疲劳性能曲线,对结构的疲劳寿命作出较为准确的预测。
第三部分:机械结构的疲劳优化技术3.1 结构强度优化针对结构的疲劳薄弱区域或高应力区域,可以通过结构形状的调整或增加材料的强度来提高结构的疲劳寿命。
3.2 材料优化选用合适的材料对于提高机械结构的疲劳寿命至关重要。
常见的方法包括采用高疲劳强度和高韧性材料、进行表面改性等。
3.3 负载控制优化对于受到循环加载的结构,合理的负载控制可以降低结构的疲劳损伤。
例如,合理设计加载路径、降低加载频率等。
3.4 疲劳寿命预测模型优化通过建立可靠的疲劳寿命预测模型,可以更准确地预测机械结构的疲劳性能。
优化预测模型的方法包括增加样本数量、优化参数选择等。
结论:机械结构的疲劳特性分析与优化是确保机械结构可靠性和寿命的重要手段。
§3-1 材料的疲劳特性 §3-2 机械零件的疲劳强度计算
§3-2 机械零件的疲劳强度计算
OM与AG的交点M'的应力值即为计算时的所用的极限应力。
s ae 。 联解OM及AG两直线的方程式,可求出点M‘的坐标值 s me σa 列出OM与AG的直线方程, A M' G σ ' ae 解方程组即可。 N'
s s me s 1 K s s ae s a s ae s m s me
σmax
σmin
σ
T σa σm
sm
s max s min
2
sa
s max s min
2 s min r
r ─应力比(循环特性)
s max
o
t
描述规律性的交变应力可有5个参数,但其中只有两个参数是独立的。
σ o
σ
σ
最不利
r = -1 对称循环应力 smax=σ-1
r =+1
t o
r=0 脉动循环应力 smax=σ0
s max s min
2
A
M'
M
G
N' C σm
σa
O
N
sa c' --是一条过原点和M点 sm 的直线。
σm
σ'me
掌握图解法,尺子量。公式不必记忆
☻工作点M:位于AOG区域,零件疲劳损坏,疲劳强度条件是: s 'max s 'ae s 'me s 1 Sca S s max sa sm Ks s a s s m ☻工作点N:位于GOC区域,零件屈服失效,静强度条件为: s ' s 'me sS Sca ae S sa sm sa sm
钛合金疲劳极限
钛合金疲劳极限【原创版】目录1.钛合金概述2.疲劳极限的定义3.钛合金的疲劳极限特性4.影响钛合金疲劳极限的因素5.提高钛合金疲劳极限的方法正文【1.钛合金概述】钛合金是一种以钛为基础,加入其他元素(如铝、钒、钛等)制成的高性能合金材料。
因其具有优良的抗腐蚀性、高温强度和低密度等特点,被广泛应用于航空航天、化工、医疗等领域。
然而,钛合金在循环加载条件下容易出现疲劳损伤,因此研究其疲劳极限具有重要意义。
【2.疲劳极限的定义】疲劳极限是指材料在循环加载过程中,能够承受的最大应力幅值。
当应力幅值超过疲劳极限时,材料将发生疲劳损伤,最终导致断裂。
【3.钛合金的疲劳极限特性】钛合金的疲劳极限一般较低,且受到许多因素的影响,如材料成分、热处理工艺、加工方式等。
此外,钛合金在循环加载过程中容易出现蠕变损伤,从而降低其疲劳极限。
【4.影响钛合金疲劳极限的因素】(1)材料成分:钛合金中的铝、钒等元素对疲劳极限产生显著影响。
适当增加铝含量可提高疲劳极限,但过量的铝会导致晶粒粗化,降低疲劳极限;钒的加入可提高疲劳极限,但过量的钒会导致强度下降。
(2)热处理工艺:热处理工艺对钛合金的疲劳极限具有重要影响。
适当的热处理可以改善晶粒细化、析出相的形成和分布,从而提高疲劳极限。
(3)加工方式:钛合金的加工方式(如锻造、轧制、拉丝等)对其疲劳极限产生显著影响。
合理的加工方式可以改善材料组织形态,提高疲劳极限。
【5.提高钛合金疲劳极限的方法】(1)优化材料成分:合理控制铝、钒等元素的含量,以提高疲劳极限。
(2)采用适当的热处理工艺:通过调整热处理温度、保温时间等参数,优化组织形态,提高疲劳极限。
(3)选择合适的加工方式:根据实际需求选择合适的加工方式,以改善材料组织形态,提高疲劳极限。
(4)表面处理:通过表面处理技术(如喷涂、渗氮等)改善钛合金表面的疲劳性能,提高疲劳极限。