机械制造中的加工方法及设备
机械制造生产方法
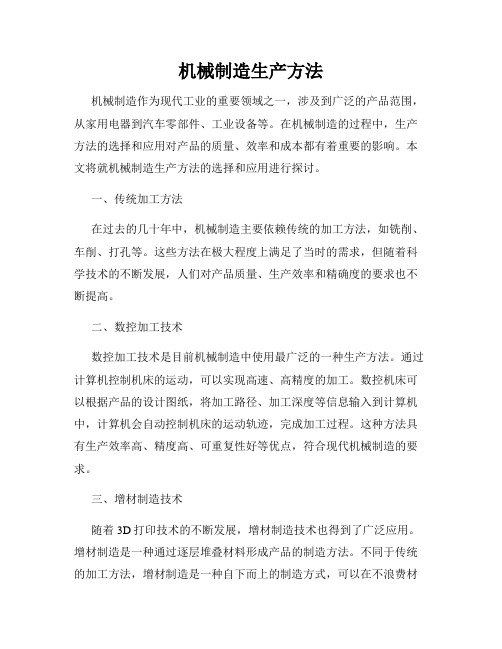
机械制造生产方法机械制造作为现代工业的重要领域之一,涉及到广泛的产品范围,从家用电器到汽车零部件、工业设备等。
在机械制造的过程中,生产方法的选择和应用对产品的质量、效率和成本都有着重要的影响。
本文将就机械制造生产方法的选择和应用进行探讨。
一、传统加工方法在过去的几十年中,机械制造主要依赖传统的加工方法,如铣削、车削、打孔等。
这些方法在极大程度上满足了当时的需求,但随着科学技术的不断发展,人们对产品质量、生产效率和精确度的要求也不断提高。
二、数控加工技术数控加工技术是目前机械制造中使用最广泛的一种生产方法。
通过计算机控制机床的运动,可以实现高速、高精度的加工。
数控机床可以根据产品的设计图纸,将加工路径、加工深度等信息输入到计算机中,计算机会自动控制机床的运动轨迹,完成加工过程。
这种方法具有生产效率高、精度高、可重复性好等优点,符合现代机械制造的要求。
三、增材制造技术随着3D打印技术的不断发展,增材制造技术也得到了广泛应用。
增材制造是一种通过逐层堆叠材料形成产品的制造方法。
不同于传统的加工方法,增材制造是一种自下而上的制造方式,可以在不浪费材料的情况下完成复杂形状的制造。
增材制造技术可以应用于机械零部件的快速制造、定制化生产等领域,具有很大的潜力。
四、智能制造技术智能制造技术是指通过信息技术与先进制造技术相结合,实现生产过程的智能化和自动化。
在机械制造中,智能制造技术可以应用于产品的设计、加工过程的监控与控制、设备的维护与优化等方面。
智能制造技术的应用可以提高生产效率、降低生产成本,并且可以根据市场需求快速响应,为企业创造更大的竞争优势。
综上所述,机械制造生产方法的选择和应用对于产品的质量和效率有着重要的影响。
传统加工方法、数控加工技术、增材制造技术和智能制造技术是当前机械制造中常用的方法。
随着科技的发展,我们可以预见,未来机械制造的生产方法将继续不断创新和发展,为人们创造更好的机械产品。
机械制造技术基础总结

机械制造技术基础总结机械制造技术基础第一章重点车削加工:工件旋转作主运动,车刀作进给运动的切削加工方法称为车削加工。
铣削加工:铣刀旋转作主运动,工件作进给运动的切削加工方法称为铣削加工。
刨削加工:刀具的往复直线运动为主切削运动,工作台带动工件作间歇的进给运动的切削加工方法称为刨削加工。
钻削加工:钻削是用钻头、铰刀或锪刀等工具在材料上加工孔的工艺过程。
刀具(钻头)是旋转运动为主切削运动,刀具(钻头)的轴向运动是进给运动。
镗削加工:镗削是用镗刀对已经钻出、铸出的孔作进一步加工,通常镗刀旋转做主运动,工件或镗刀直行作进给运动。
磨削加工:用砂轮或涂覆模具以较高的线速度对工件表面进行加工的方法成为磨削加工,主运动是砂轮的旋转。
成形法:成形法是用与被切削齿轮的齿槽线截面形状相符的成型刀具切出齿形的方法,所使用的机床一般为普通机床,刀具为普通铣刀,需要两个简单的成形运动:道具的旋转运动(主切削运动)和直线移动(进给运动)。
展成法:展成法是利用齿轮刀具与被切齿轮保持啮合运动的关系而切出齿形的方法,常用机床有滚齿机、插齿机等,常用加工法有滚齿法、插齿法、磨齿法、剃齿法等。
内传动链:有准确传动比的连接一个执行机构和另一个执行机构之间的传动链。
展成传动链和差动传动链为内联系传动链。
课本P26外传动链:是动力源与执行机构之间或两个执行机构之间没有准确传动比要求的传动链。
速度传动链和轴向进给传动链为外联系传送链。
课本P26表面成型运动:表面成形运动是指在切削加工中刀具与工件的相对运动,可分解为主运动和进给运动。
(来自百度)滚齿原理?滚齿属于展成法加工,用齿轮滚刀在滚齿机上加工齿轮的轮齿,它是按一对螺旋齿轮相啮合的原理进行加工的。
滚齿时的运动主要有:(1)主运动。
主运动是指滚刀的高速旋转。
(2)分齿运动(展成运动)。
分齿运动是指滚刀与被切齿轮之间强制的按速度比保持一对螺旋齿轮啮合关系的运动。
(3)垂直进给运动。
为了在齿轮的全齿宽上切出齿形,齿轮滚刀需要沿工件的轴向作进给运动。
机械加工设备工艺及一般知识

机械加工设备工艺及一般知识一、机械加工设备1、定义机械加工设备是指用切削的方法将金属毛坯加工成机器零件的机器,它是制造机器的机器。
所以又称为“工作母机”或“工具机”,习惯上简称为机床。
机床工业肩负着为国民经济各部门提供现代化装备的任务。
一个国家机床工业的技术水平,在很大程度上标志着这个国家的工业生产能力和科学技术水平。
显然,机床在国民经济建设中起着重大的作用。
2、机床的分类A、按加工性质和所用刀具分为12大类:车床、钻床、镗床、磨床、齿轮加工机床、螺纹加工机床、刨插床、铣床、拉床、特种加工机床、锯床及其他机床。
B、同类机床的分类I.按通用性程度可分为:1)普通机床:可用于加工多种零件的不同工序,加工范围较广,通用性较大。
但结构较复杂,这种机床主要适用于单件小批生产。
如:卧式车床、万能升降台铣床。
2)专门化机床:它的工艺范围较狭窄。
只能用于加工某一类或几类零件的某一道(或几道)特定工序。
如:曲轴车床、凸轮轴车床。
3)专用机床:它的工艺范围最窄。
只能用于某一种零件的某一道特定工序,试用于大批量生产。
如:专用镗床、专用磨床。
I.按工作精度分为:普通精度机床、精密机床和高精度机床。
II.按自动化程度分为:手动、机动、半自动和自动的机床。
III.按重量、尺寸划分:仪表机床、中型机床、大型机床(重量大于10吨)、重型机床(重量大于30吨)和超重型机床(重量大于100吨)。
3、机床型号的编织方法机床的型号是每种机床的一个代号。
用以简明地表示机床的类型、通用和结构特性,以及主要参数。
机床的类别用汉语拼音大写字母表示。
普通机床类别代号车床CT6140主参数(最大车削直径400mm4、机床的传动联系在切削加工过程中,装在机床上的工件和刀具按一定的规律作相对运动,通过刀具的刀刃对毛坯的切削作用,把毛坯上多余的金属切掉,从而得到所要求的表面形状。
每个运动都有三个基本部分:1)、执行件执行运动的部件。
如主轴、刀架;其任务是:带工件或刀具完成旋转或直线运动,并保持准确的运动轨迹。
机械制造流程指南

机械制造流程指南第1章机械加工基础 (4)1.1 加工方法概述 (4)1.2 常用机械加工工艺 (4)1.2.1 车削加工 (4)1.2.2 铣削加工 (4)1.2.3 钻削加工 (4)1.2.4 镗削加工 (4)1.2.5 磨削加工 (4)1.2.6 压力加工 (5)1.3 机械加工精度与表面质量 (5)1.3.1 机械加工精度 (5)1.3.2 表面质量 (5)第2章金属材料与热处理 (5)2.1 常用金属材料 (5)2.1.1 碳钢 (5)2.1.2 合金钢 (5)2.1.3 工具钢 (6)2.1.4 有色金属 (6)2.2 钢的热处理工艺 (6)2.2.1 退火 (6)2.2.2 正火 (6)2.2.3 淬火 (6)2.2.4 回火 (6)2.3 金属材料的功能检测 (6)2.3.1 物理功能检测 (6)2.3.2 力学功能检测 (7)2.3.3 耐腐蚀功能检测 (7)2.3.4 工艺功能检测 (7)第3章零件设计与工艺分析 (7)3.1 零件结构设计 (7)3.1.1 设计原则 (7)3.1.2 设计方法 (7)3.2 零件加工工艺性分析 (7)3.2.1 分析内容 (8)3.2.2 分析方法 (8)3.3 零件加工工艺方案制定 (8)3.3.1 制定原则 (8)3.3.2 制定方法 (8)第4章铣削加工 (8)4.1 铣削加工概述 (9)4.2 铣床与铣刀 (9)4.2.1 铣床 (9)4.2.2 铣刀 (9)4.3 铣削加工工艺参数选择 (9)4.3.1 切削速度 (9)4.3.2 进给量 (9)4.3.3 切削深度 (9)4.4 铣削加工常见问题及解决方法 (9)4.4.1 刀具磨损 (9)4.4.2 表面质量不佳 (10)4.4.3 加工精度不足 (10)4.4.4 生产效率低下 (10)第5章车削加工 (10)5.1 车削加工概述 (10)5.2 车床与车刀 (10)5.2.1 车床 (10)5.2.2 车刀 (10)5.3 车削加工工艺参数选择 (10)5.3.1 切削速度 (10)5.3.2 进给量 (10)5.3.3 切削深度 (11)5.4 车削加工常见问题及解决方法 (11)5.4.1 表面粗糙度问题 (11)5.4.2 尺寸精度问题 (11)5.4.3 螺纹加工问题 (11)5.4.4 切削振动问题 (11)第6章钻削与镗削加工 (11)6.1 钻削加工 (11)6.2 钻床与钻头 (11)6.2.1 钻床 (11)6.2.2 钻头 (12)6.3 镗削加工 (12)6.4 镗床与镗刀 (12)6.4.1 镗床 (12)6.4.2 镗刀 (12)第7章磨削加工 (13)7.1 磨削加工概述 (13)7.2 磨床与磨具 (13)7.2.1 磨床 (13)7.2.2 磨具 (13)7.3 磨削加工工艺参数选择 (13)7.3.1 磨削速度 (13)7.3.2 磨削深度 (13)7.3.3 磨削宽度 (13)7.3.4 磨削液 (14)7.4 精密与超精密磨削技术 (14)7.4.1 精密磨削 (14)7.4.2 超精密磨削 (14)第8章特种加工技术 (14)8.1 电火花加工 (14)8.1.1 电火花加工原理 (14)8.1.2 电火花加工设备与工艺参数 (14)8.1.3 电火花加工的应用 (14)8.2 激光加工 (14)8.2.1 激光加工原理 (15)8.2.2 激光加工设备与工艺参数 (15)8.2.3 激光加工的应用 (15)8.3 超声波加工 (15)8.3.1 超声波加工原理 (15)8.3.2 超声波加工设备与工艺参数 (15)8.3.3 超声波加工的应用 (15)8.4 电子束与离子束加工 (15)8.4.1 电子束加工原理 (15)8.4.2 离子束加工原理 (16)8.4.3 电子束与离子束加工设备与工艺参数 (16)8.4.4 电子束与离子束加工的应用 (16)第9章装配与调试 (16)9.1 机械装配基本原理 (16)9.1.1 装配的基本要求 (16)9.1.2 装配前的准备工作 (16)9.2 装配工艺流程 (16)9.2.1 装配顺序 (16)9.2.2 装配方法 (17)9.2.3 装配过程中的注意事项 (17)9.3 装配精度检测 (17)9.3.1 尺寸精度检测 (17)9.3.2 形位精度检测 (17)9.3.3 运动精度检测 (17)9.4 机械设备的调试与运行 (17)9.4.1 空载调试 (18)9.4.2 负载调试 (18)9.4.3 运行测试 (18)第10章质量控制与生产管理 (18)10.1 质量控制体系 (18)10.1.1 质量控制体系的基本构成 (18)10.1.2 质量控制体系的运行机制 (18)10.1.3 质量控制体系的实施要领 (18)10.2 加工质量分析与控制 (18)10.2.1 加工质量分析的方法 (18)10.2.2 常见加工缺陷及其产生原因 (18)10.2.3 加工质量控制措施 (18)10.3 生产调度与设备管理 (18)10.3.1 生产调度的基本原则 (19)10.3.2 设备管理的方法与措施 (19)10.3.3 设备维护与故障排除 (19)10.4 现场管理与安全生产 (19)10.4.1 现场管理的基本要求与方法 (19)10.4.2 安全生产的目标与措施 (19)10.4.3 安全的预防与处理 (19)第1章机械加工基础1.1 加工方法概述机械加工是指利用机械力对工件进行切削、磨削、压力加工等,以达到一定的几何形状、尺寸精度和表面质量的过程。
机械制造工艺方法

机械制造工艺方法一、概述机械制造工艺方法是制造业中一种重要的技术手段,它涉及到从原材料的加工到成品制造的整个过程。
机械制造工艺方法的合理应用对于提高生产效率、降低成本、保证产品质量以及提升企业的竞争力具有重要意义。
本文将重点介绍机械制造工艺方法中的主要工艺方法以及现代机械制造工艺的发展趋势。
二、主要工艺方法1.铸造工艺铸造工艺是一种将液态金属浇注到铸型中,待其冷却凝固后得到一定形状和性能的零件或毛坯的工艺方法。
铸造工艺广泛应用于各种机械零件的生产,尤其是一些形状复杂、难以加工的零件。
根据铸造材料的不同,铸造工艺可分为铸铁、铸钢、铜、铝等不同的铸造方法。
2.锻造工艺锻造工艺是一种通过施加外力使金属坯料变形,从而得到所需形状和性能的零件的工艺方法。
锻造工艺可以改善金属的力学性能和物理性能,提高其抗疲劳、耐磨损等性能。
根据变形温度的不同,锻造工艺可分为热锻、冷锻和温锻三种类型。
3.焊接工艺焊接工艺是一种通过熔融金属或其焊接材料,将两个或多个金属材料连接在一起的工艺方法。
焊接工艺广泛应用于桥梁、船舶、管道等大型结构的制造中。
焊接工艺有许多种,如电弧焊、气体保护焊、激光焊等。
4.切削加工工艺切削加工工艺是一种通过刀具对工件进行切削加工,从而得到一定形状和尺寸的零件的工艺方法。
切削加工是机械制造中应用最广泛的一种加工方法,它可以加工各种形状和尺寸的零件,如轴、齿轮、凸轮等。
根据切削运动的形式不同,切削加工可分为铣削、车削、钻削等多种类型。
5.特种加工工艺特种加工工艺是一种利用光、电、热等物理能量来进行材料加工的工艺方法,也被称为非传统加工方法。
与传统的切削加工方法相比,特种加工工艺可以加工硬度高、韧性好、耐高温的材料,而且加工过程中不会产生切削力,可以避免工件的变形。
常见的特种加工工艺有激光加工、电火花加工、离子束加工等。
三、现代机械制造工艺的发展趋势随着科技的不断发展,现代机械制造工艺正朝着智能化、精密化、绿色化等方向发展。
机械工程中的精密制造技术

机械工程中的精密制造技术机械工程是一门广泛的工程学科,涵盖了从设计和制造到维护和改进的各个方面。
而精密制造技术则是机械工程中一个非常重要的领域。
它主要指通过先进的生产工艺和高精度的机器设备,制造具有高度精度和良好可靠性的机械零件和装置的技术。
在各种机械工程领域中,高精度的机器零件和装置是非常重要的,它们对机械性能和使用寿命的稳定性有着至关重要的影响。
因此,精密制造技术也被广泛应用于各种行业和领域。
本篇文章将介绍机械工程中的精密制造技术,包括所涉及的工艺和设备、应用领域以及发展趋势等方面。
一、精密制造技术的工艺和设备精密制造技术的实现需要先进的生产工艺和高精度的机器设备,其中最重要的工艺和设备包括:数控加工技术、磨削技术、电火花加工技术、车削技术等。
1. 数控加工技术数控加工技术是目前最为先进的加工工艺之一,它主要利用计算机控制系统来控制和驱动加工机床进行高度精度的切削加工。
数控加工技术与传统的手工或机械切削加工相比,具有更高的精度、更快的加工速度和更好的加工质量。
目前数控加工技术已经广泛应用于各种领域中的零件制造、模具制造、精密模型加工等方面。
2. 磨削技术磨削技术是一种通过摩擦磨擦和切削等方式,对工件表面进行高精度的加工。
磨削技术广泛应用于各种领域中的零件制造和模具制造等方面。
目前最常用的磨削技术包括平面磨、球面磨、外圆磨、内圆磨、立式磨、锯片磨等。
3. 电火花加工技术电火花加工技术是一种利用电脉冲能量在工件上形成微小的放电火花,从而实现高精度的切削加工。
它可以对各种金属材料进行加工,并且具有极高的加工精度、加工速度和表面质量。
由于其精度高、工艺简单等优点,电火花加工技术目前已经广泛应用于模具制造、精密机械零件加工等领域。
4. 车削技术车削技术是一种通过旋转刀具对工件进行切削加工的技术。
它广泛应用于各种机械制造领域中,如轴类零件、齿轮、螺纹等的制造。
车削技术可以通过不同的切削方法和刀具设计来实现高精度的加工,如单刃车削、多刃车削、铰削、镗削等。
机械制造工艺与设备

机械制造工艺与设备摘要:机械制造工艺与设备是现代工业领域中至关重要的一部分。
本文旨在探讨机械制造工艺及其所需设备的关键方面。
通过深入研究机械制造的各个方面,我们可以更好地理解和应用这些技术,从而提高生产效率,降低成本,并实现更高的产品质量。
本文将涵盖各种制造工艺,如加工、焊接、装配等,以及所需的机械设备,如机床、焊接机器人、自动化装配线等。
最后,我们还将探讨未来机械制造工艺和设备的发展趋势,以便读者更好地了解这个领域的前景。
关键词:机械制造、工艺、设备、生产效率引言机械制造工艺与设备在现代工业中扮演着至关重要的角色。
随着科技的不断进步,制造业也在不断发展和演变,机械制造工艺和设备的创新成为了实现高效生产和高质量产品的关键。
本文将深入探讨机械制造工艺和所需设备的关键方面,以帮助读者更好地理解和应用这些技术。
首先,我们将关注机械制造工艺。
制造工艺是制造产品的过程,包括原材料的加工、零件的制造和组装。
加工工艺涵盖了各种方法,如铣削、车削、钻削等,这些方法可以将原材料加工成所需的形状和尺寸。
此外,焊接和粘接工艺用于将零件连接在一起,形成完整的产品。
装配工艺则涉及将各个零件组装在一起,确保产品的功能完整性和性能。
机械制造工艺的选择取决于产品的要求和设计。
为了实现不同的机械制造工艺,需要各种机械设备的支持。
机床是其中一个关键的设备,用于进行加工工艺,如铣削、车削和钻削。
机床的精度和稳定性对最终产品的质量至关重要。
此外,焊接机器人在焊接工艺中发挥着重要作用,它们能够提高焊接速度和质量,同时降低劳动力成本。
自动化装配线也是现代制造业中的常见设备,它们可以实现高效的零件组装,从而提高生产效率。
随着科技的不断进步,机械制造工艺和设备也在不断演进。
数字化制造技术、人工智能和物联网的应用正在改变制造业的格局。
数字化制造技术可以实现更高级别的自动化和智能化,从而提高生产的灵活性和适应性。
人工智能可以用于预测性维护,减少设备故障和停机时间。
机械制造中的机械零部件加工与装配

机械制造中的机械零部件加工与装配机械制造是现代工业生产的基石之一,而机械零部件则是构成机械设备的重要组成部分。
机械零部件的加工与装配是机械制造过程中不可或缺的环节,它直接影响着机械设备的性能和质量。
本文将从机械零部件加工和装配两个方面进行论述。
一、机械零部件加工机械零部件加工是指将原材料转变为具有特定形状、尺寸和功能的零件的过程。
在机械零部件加工中,常用的加工方法包括铣削、车削、钻孔、磨削等。
铣削是通过旋转刀具将工件上的材料去除,从而形成特定形状的零件。
铣削适用于平面、曲面和开槽等加工需求。
而车削则是通过旋转工件,并沿着切削区域对其进行切削,来实现零件的加工目的。
钻孔是通过切削工具在工件上形成孔洞的过程,常用于安装螺栓、销子等连接零件。
磨削是利用磨料颗粒在工件表面进行切削,来获得高精度和光洁度的零件。
在机械零部件加工过程中,同时还需要注意工艺参数的选择,例如切削速度、进给速度和切削深度等,以确保零件的加工质量和加工效率。
二、机械零部件装配机械零部件装配是指将多个加工好的零件按照一定的工序和方法组合在一起,形成完整的机械设备的过程。
机械零部件的装配过程中,需要注意以下几个方面。
首先,需要进行零件的配对和匹配。
确保零件之间的相互匹配性,以避免在装配过程中出现配合不良、间隙过大或过小等问题。
其次,要进行合理的零件组合顺序和装配顺序的确定。
根据零件之间的相互关系,将相对独立的零件先组装在一起,逐步完成整个机械装配过程。
同时,还需要注意装配过程中的各种安装要求,例如对螺栓的拧紧力矩、轴承的润滑等。
此外,机械零部件的装配过程中,也需要注意装配的规范性和准确性。
确保各个零部件的位置准确,以及安装质量达到要求。
在装配过程中,还需要进行相关的检测和测试,以验证装配的正确性和可靠性。
总结机械零部件的加工与装配是机械制造过程中重要的环节。
通过合理选择加工工艺和工艺参数,可以获得高质量的机械零部件;通过合理组织和安排装配过程,可以保证机械设备的装配质量和装配效率。
- 1、下载文档前请自行甄别文档内容的完整性,平台不提供额外的编辑、内容补充、找答案等附加服务。
- 2、"仅部分预览"的文档,不可在线预览部分如存在完整性等问题,可反馈申请退款(可完整预览的文档不适用该条件!)。
- 3、如文档侵犯您的权益,请联系客服反馈,我们会尽快为您处理(人工客服工作时间:9:00-18:30)。
(二)提高生产效率的途径
1、采用高速切削 通过提高切削速度来提高生产效率,同时可以降低加工表 面的粗糙度。 2、采用强力切削 通过增大切削面积( ap×f )来提高生产效率。在刀尖处 磨出一段κr′=0长度为1.2~1.5f的修光刃,在f提高几倍甚至 几十倍的条件下进行切削,Ra=5~2.5μm. 比高速切削的生产效率更高。要求车床加工系统必须具有 足够的刚性及功率。 3、采用多刀加工 通过减少刀架行程长度提高生产效率。
三 外圆表面的磨削加工
(一)加工方法 1、工件有中心支承的外圆磨削
(1)纵向进给磨削
(2)横向进给磨削(切入磨削)
2 工件无支承点的外圆磨削(无心磨削)
3 快 速 点 磨
快速点磨与传统磨削相比,砂轮与工件接触面积小,磨削速度高,磨削过 程中磨削力小,磨削热少,加工质量好,生产效率高,砂轮寿命长。
第三章 机械制造中的加工方法及设备
第一节 概述
一 机械制造中的加工方法 1、材料去除加工(Δm<0) 在被加工对象上去除掉一部分材料的加工方法。 材料利用率低,加工精度相对较高、表面质量相对较 好,适应性强。分为切削加工(车铣刨磨)和特种加 工(电火花,电子束等)。 2 、材料成形加工(Δm=0) 在较高的温度(或压力)下,使材料在模具中成 形的方法,例如铸造、锻造、挤压、粉末冶金等。 3、材料累积加工(Δm>0) 利用微体积材料逐渐叠加的方式使零件成形。例 如电镀、化学镀等原子沉积和热喷涂、静电喷涂等微 粒沉积加工以及快速原型制造等。
刀片夹固应满足夹紧可靠,装卸方便,定位精确等要求。
(四)机床分类
1、卧式机床 2、立式机床 3、转塔机床 4、仿行机床 5、专门化机床
二 外圆表面的车拉加工 车拉加工是将传统的车削和拉削加工结合在一起的一种 组合式的加工方法。
车拉用于外圆表面加工时,加工精度较高,可省去精车, 粗磨工序。 车拉加工时,工件高速旋转,刀具同时也做慢速旋转。 根据刀齿切入进给方式不同,车拉刀分为螺旋形和圆柱 形车拉刀。
常用的钻孔刀具:麻花钻,中心钻,深孔钻等。
了解麻花钻的结构。标准麻花钻结构,麻花钻的切削部分,标准麻花钻的几何角度 钻孔加工特点:由于构造上的限制,钻头的弯曲刚度和扭转刚度都较低,定心性不好, 钻孔加工精度较低,表面粗糙度也较大;钻孔的金属切削率大,切削效率高。主要用于加 工质量不高的孔,例如螺栓孔,螺纹底孔,油孔等。对于加工精度和表面质量要求较高的 孔,则应在后续加工中通过扩孔,铰孔,镗孔,磨孔或拉孔来达到。
镗孔加工精度为IT9~IT7,表面粗糙度3.2~0.8µm。
大批量的生产中,为提高镗孔效率,可以使用镗模。
四 珩磨孔(光整加工)
1.珩磨原理及珩磨头 珩磨是利用磨条(油石)的珩磨头对孔进行光整加工的方法。
与镗孔相比,铰孔生产率高,容易保证孔的精度;但铰孔不能校 正孔轴线的位置误差,孔的位置精度应由前面的工序保证。
铰孔尺寸精度一般为IT9~IT7,表面粗糙度3.2~0.8µ m。对于中等 尺寸、精度要求较高的孔,钻—扩—铰工艺是生产中常用的典型加 工方案。
三 镗孔
镗孔是在预制孔上用切削刀具使之扩大的一种加工方法。既可在镗床进行,也可以在车 床上进行。 1.镗孔方式(三种) ⑴工件旋转图3-37 ⑵刀具旋转图3-38 ⑶刀具既旋转又进给图3-39 2.金刚镗 背吃刀量和进给量小,切削速度高。加工精度很高,表面粗糙度很低。
(三)外圆磨削时的工艺特点及应用范围
1 工艺特点 ⑴磨粒硬度高,能加工一般金属刀具不能加工的工件表面,例如 带有不均匀铸、锻硬皮的工件表面、淬硬表面等。 ⑵磨削加工能切除极薄极细的切屑,修正误差能力强,加工精度 高,加工表面粗糙度小 ⑶由于磨粒切除金属材料是用负前角切削,磨削速度极高,因此 磨削区瞬时温度极高。 ⑷由于大负前角磨粒在切除金属的过程中消耗的摩擦功大,再加 上磨屑细薄,切除单位体积的金属所消耗的能量要比车削大。 2 用途 适用于精加工,可用于加工淬火钢,工具钢以及硬质合金等硬度 很高的材料。也可用砂轮磨削带有不均匀铸、锻硬皮的工件。 不适宜加工塑性较大的有色金属材料,容易堵塞砂轮,使其失去切 削作用。 磨削广泛用于单件小批量生产,也广泛用于大批量生产。
2.扩孔 扩孔是用扩孔钻对已经钻出,铸出或锻出的孔作进一步的加工, 以扩大孔径并提高孔的加工质量(扩孔) 。扩孔钻与麻花钻相似, 但刀齿数较多,没有横刃,结构如图3-33。 与钻孔比较,扩孔具有下列特点: ⑴扩孔钻齿数多(3-8个齿),导向性好,切削比较稳定。 ⑵扩孔钻没有横刃,切削条件好 ⑶加工余量较小,容屑槽可以做的浅些,钻芯可以做的粗些,刀体 强度和刚性好。 扩孔加工精度一 工孔径D<100mm。在钻直径较大的孔时( D≥30mm ),常用小 钻头预钻孔,然后再用相应尺寸的扩孔钻扩孔,可以提高孔的加工 质量和生产效率。 扩孔除了加工圆柱孔外,还可以用各种特殊形状的扩孔钻(锪钻) 来加工各种沉头座孔和锪平面。图3-34 锪钻
(三)车刀的种类和用途
按 用 途 分 类
车刀结构上分为整体车刀,焊接车刀和机械夹固式车刀。
1、整体车刀 只有高速钢车刀才做成整体车刀,截面为 正方形或矩形,耗用刀具材料较多,一般只用切槽,切 断。
2、焊接车刀 将硬质合金刀片焊接在普通碳素钢刀体上。优点是结 构简单、紧凑、刚性好、使用灵活、制造方便,缺点是 焊接时产生的应力会降低硬质合金刀片的使用性能,甚 至会产生裂纹。 3、机械夹固式车刀 简称机夹车刀。分为机夹重磨车刀和机夹可转为车刀。
(四)外圆表面光整加工
光整加工是精加工之后,从工件表面上不切除或切除极薄金属层,用以提高加工表面的 尺寸和形状精度,降低表面粗糙度的加工方法。主要方法有研磨,超精加工,滚压,抛光 等 1.研磨
研磨是在研具与工件之间加入研磨剂对工件表面进行光整加工的方法。
研具材料比工件材料软,部分磨粒能嵌入研具的表层,对工件表面进行微量切削。最常 用的研具材料是硬度为120—160HBW的铸铁。也可以用铜,巴式合金等。 研磨剂由磨料,研磨液和表面活性物质等混合组成。磨料主要起切削作用,应有较高硬 度(刚玉,碳化硅,碳化硼等)。研磨液主要起冷却润滑作用,常用的有煤油,汽油等。 表面活性物质附着在工件表面,使其生成一层极薄的软化膜,易于切除(油酸,硬质酸 等)。 研磨分手工研磨和机械研磨。 研磨设备简单,成本低,加工质量容易保证,可加工钢,铸铁,硬质合金,陶瓷等多种 材料,适应性强。加工条件控制得当,可获得很高的尺寸精度,很小的表面粗糙度和较高 的形状精度。
二 零件表面成形原理及机床基本知识
(一)零件表面的形成方法及所需运动
1、零件表面可以看作一条线(母线)沿另一条线(导线) 运动的轨迹。 母线和导线统称为形成表面的发生线(成形线)。
常见的零件表面按其形状可分为四类:
⑴旋转表面 ⑵纵向表面 ⑶螺旋表面 ⑷复杂曲面
2、零件表面的形成方法及所需的成形运动 要研究零件表面的形成方法,应该首先研究表面发生 线的形成方法。
(三)机床的分类
(四)金属切削机床型号的编制
1、通用机床 2、专用机床
第二节 外圆表面加工(车削、车拉、磨削)
一 车削 (一)加工方法 1、粗车 外圆加工最经济有效的方法。主要目的是高效地从毛坯上切除 多余的金属,提高生产率是其主要任务。ap,f↑,使得Q↑, 要使得T ↑,ν c↓。κr应该大,以减小Fp,防止工件变形和振动;选取较小的 γo,αo,λs<0,以增强车刀切削部分强度。粗车的加工精度可以达 到IT12~IT11,粗糙度Ra50~12.5μm。 2、精车 主要任务是保证工件的加工精度和表面质量。ap,f ↓,νc ↑,选 取较大的γo,αo,λs>0,以提高加工表面的质量。精车可以作为 较高精度外圆的最终加工或作为精细加工的预加工。精车的加工精 度可以达到IT8~IT6,粗糙度RaRa1.6~0.8μm。 3、细车 ap,f取值极小, νc 较大。一般用CBN,金刚石超硬刀具,机床 也必须主轴能做高速回转并具有很高刚度的高精度或精密机床。加 工精度IT8~IT6,粗糙度Ra1.25~0.02μm。
2、金属切削机床的传动 机床为了获得所需运动,需要通过传动机构把执行机 构和动力源,或者把两个不同的执行机构联接起来,构成 机床的传动联系。 构成机床传动联系的一系列传动件称为传动链。 ⑴外联系传动链 动力源和运动执行机构之间的传动联系。作用:使执 行机构按预定的速度运动,并传递一定的动力。传动比的 变化只影响执行机构的运动速度,不影响发生线的性质。 ⑵内联系传动链 执行机构之间的传动联系。作用:将两个或两个以上 的单独运动组成复合的成形运动。要求各执行件之间的相 对运动有严格的要求。需要有严格的传动比。
(二)外圆磨削时的尺寸控制 磨削时砂轮具有自锐作用。当磨粒的锋刃磨钝之后,作 用在磨粒上的力增大,使磨粒被压碎,形成新的锋刃,或 者整颗磨粒脱落露出新的磨粒锋刃来工作。砂轮的自锐作 用可以使磨粒始终保持锋利状态,但同时会使砂轮的径向 磨损速度加剧,使磨削外圆一般不能用预先确定的径向进 给量的方法来保证工件的直径尺寸。为保证外圆磨削的尺 寸精度,需要根据工件在磨削过程中的实际尺寸变化来控 制砂轮的径向进给量。在大批大量生产中,通常采用在磨 削过程中对工件进行主动测量的方法来控制工件尺寸。
表面发生线的形成方法一般有以下四种:
⑴轨迹法
⑵成形法
⑶相切法 ⑷展成法
(二)机床的基本结构和传动
1、金属切削机床的基本结构 ⑴动力源 电动机,为机床执行机构的运动提供动力。 ⑵运动执行机构 机床执行运动的机构,如主轴、刀架和工作台等,带动刀具或工 件旋转或移动 ⑶传动机构 将动力源的运动和动力传给运动执行机构,或将运动由一个执行 机构传递到另一个执行机构,以保持两个运动之间的准确传动关系。 传动机构可以改变运动方向、运动速度及运动形式。 ⑷控制系统和伺服系统 对机床进行控制,实现各运动之间的准确 协调。 ⑸支撑系统 床身,立柱及相关机械联接在内的支撑结构。 ⑹其他 冷却装置,润滑系统,排屑装置,自动测量装置等。