03泵轴临界转速的计算
电机转轴的挠度及临界转速计算

b处:f1'= 0.006714438 cm d处:f2'= -0.006606742 cm 5、磁拉力刚度:
转子一:K1= 136812.9233 kg/cm
转子二:K2=
0
kg/cm
6、初始磁拉力:
P1= 1368.129233 kg
P2=
0
kg
7、由磁拉力引起的
挠度:
F0= 1.03954E-12
同步转速:
n=
5781 5000
功率:
P=
300
过载系数:
K=
2.25
2、挠度系数计算:
单位:
cm
cm4
(kg) (kg) (cm) (cm) (cm) (MPa) GS r/min kW
L1=
49
L2=
52.1
L=
126
La=
36
G2=
20
y= 0.388888889
z= 0.285714286
根据y、 z值查图2-119
0 0 0 0
Xi3
91.125 857.375 6331.625 20796.875 34328.125
0 0 0 0 0
Xi3-X(i-1)3
3375 8015.625
7219 18985.75 39170.25 30406.25
0 0 0 0
Kab=
Xi3-X(i-1)3
91.125 766.25 5474.25 14465.25 13531.25
D2无铁心 输入0或 空格
280 2.06E+06
转子二外径: D2=
0
cm
转子一气隙磁密:Bδ1=
临界转速的计算

一、临界转速分析的目的临界转速分析的主要目的在于确定转子支撑系统的临界转速,并按照经验或有关的技术规定,将这些临界转速调整,使其适当的远离机械的工作转速,以得到可靠的设计。
例如设计地面旋转机械时,如果工作转速低于其一阶临界转速Nc1,应使N<0.75Nc1, 如果工作转速高于一阶临界转速,应使 1.4Nck<N<0.7Nck+1,而对于航空涡轮发动机,习惯做法是使其最大工作转速偏离转子一阶临界转速的10~20%。
二、选择临界转速计算方法要较为准确的确定出转子支撑系统的临界转速,必须注意以下两点1.所选择的计算方法的数学模型和边界条件要尽可能的符合系统的实际情况。
2.原始数据的(系统支撑的刚度系数和阻尼系数)准确度,也是影响计算结果准确度的重要因素。
3.适当的考虑计算速度,随着转子支撑系统的日益复杂,临界转速的计算工作量越来越大,因此选择计算方法的效率也是需要考虑的重要因素。
三、常用的计算方法2.Prohl-Myklestad莫克来斯塔德法传递矩阵法基本原理:传递矩阵法的基本原理是,去不同的转速值,从转子支撑系统的一端开始,循环进行各轴段截面状态参数的逐段推算,直到满足另一端的边界条件。
优点:对于多支撑多元盘的转子系统,通过其特征值问题或通过建立运动微分方程的方法求解系统的临界转速和不平衡响应,矩阵的维数随着系统的自由度的增加而增加,计算量往往较大:采用传递矩阵法的优点是矩阵的维数不随系统的自由度的增加而增大,且各阶临界转速计算方法相同,便于程序实现,所需存储单元少,这就使得传递矩阵法成为解决转子动力学问题的一个快速而有效的方法。
缺点:求解高速大型转子的动力学问题时,有可能出现数值不稳定现象。
今年来提出的Riccati 传递矩阵法,保留传递矩阵的所有优点,而且在数值上比较稳定,计算精度高,是一种比较理想的方法,但目前还没有普遍推广。
轴段划分:首先根据支撑系统中刚性支撑(轴承)的个数划分跨度。
临界转速的计算资料

一、临界转速分析的目的临界转速分析的主要目的在于确定转子支撑系统的临界转速,并按照经验或有关的技术规定,将这些临界转速调整,使其适当的远离机械的工作转速,以得到可靠的设计。
例如设计地面旋转机械时,如果工作转速低于其一阶临界转速Nc1,应使N<0.75Nc1, 如果工作转速高于一阶临界转速,应使 1.4Nck<N<0.7Nck+1,而对于航空涡轮发动机,习惯做法是使其最大工作转速偏离转子一阶临界转速的10~20%。
二、选择临界转速计算方法要较为准确的确定出转子支撑系统的临界转速,必须注意以下两点1.所选择的计算方法的数学模型和边界条件要尽可能的符合系统的实际情况。
2.原始数据的(系统支撑的刚度系数和阻尼系数)准确度,也是影响计算结果准确度的重要因素。
3.适当的考虑计算速度,随着转子支撑系统的日益复杂,临界转速的计算工作量越来越大,因此选择计算方法的效率也是需要考虑的重要因素。
三、常用的计算方法2.Prohl-Myklestad莫克来斯塔德法传递矩阵法基本原理:传递矩阵法的基本原理是,去不同的转速值,从转子支撑系统的一端开始,循环进行各轴段截面状态参数的逐段推算,直到满足另一端的边界条件。
优点:对于多支撑多元盘的转子系统,通过其特征值问题或通过建立运动微分方程的方法求解系统的临界转速和不平衡响应,矩阵的维数随着系统的自由度的增加而增加,计算量往往较大:采用传递矩阵法的优点是矩阵的维数不随系统的自由度的增加而增大,且各阶临界转速计算方法相同,便于程序实现,所需存储单元少,这就使得传递矩阵法成为解决转子动力学问题的一个快速而有效的方法。
缺点:求解高速大型转子的动力学问题时,有可能出现数值不稳定现象。
今年来提出的Riccati 传递矩阵法,保留传递矩阵的所有优点,而且在数值上比较稳定,计算精度高,是一种比较理想的方法,但目前还没有普遍推广。
轴段划分:首先根据支撑系统中刚性支撑(轴承)的个数划分跨度。
临界转速的计算修订稿
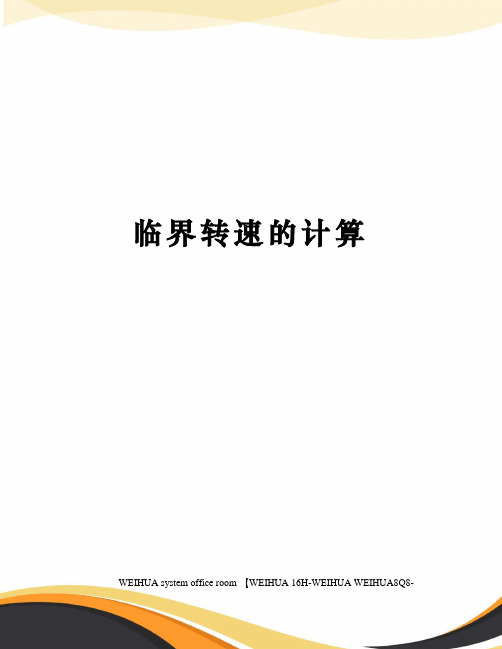
临界转速的计算WEIHUA system office room 【WEIHUA 16H-WEIHUA WEIHUA8Q8-一、临界转速分析的目的临界转速分析的主要目的在于确定转子支撑系统的临界转速,并按照经验或有关的技术规定,将这些临界转速调整,使其适当的远离机械的工作转速,以得到可靠的设计。
例如设计地面旋转机械时,如果工作转速低于其一阶临界转速Nc1,应使N<,如果工作转速高于一阶临界转速,应使<N<+1,而对于航空涡轮发动机,习惯做法是使其最大工作转速偏离转子一阶临界转速的10~20%。
二、选择临界转速计算方法要较为准确的确定出转子支撑系统的临界转速,必须注意以下两点1.所选择的计算方法的数学模型和边界条件要尽可能的符合系统的实际情况。
2.原始数据的(系统支撑的刚度系数和阻尼系数)准确度,也是影响计算结果准确度的重要因素。
3.适当的考虑计算速度,随着转子支撑系统的日益复杂,临界转速的计算工作量越来越大,因此选择计算方法的效率也是需要考虑的重要因素。
三、常用的计算方法应用不多数值积分法(前进法)以数值积分的方法求解支撑系统的运动微分方程,从初始条件开始,以步长很小的时间增量时域积分,逐步推算出轴系的运动唯一能模拟非线性系统的计算方法,在校核其他方法及研究非线性对临界转速的影响方面很有价值计算量较大,必须有足够的积分步数注:斯托多拉法莫克来斯塔德法传递矩阵法基本原理:传递矩阵法的基本原理是,去不同的转速值,从转子支撑系统的一端开始,循环进行各轴段截面状态参数的逐段推算,直到满足另一端的边界条件。
优点:对于多支撑多元盘的转子系统,通过其特征值问题或通过建立运动微分方程的方法求解系统的临界转速和不平衡响应,矩阵的维数随着系统的自由度的增加而增加,计算量往往较大:采用传递矩阵法的优点是矩阵的维数不随系统的自由度的增加而增大,且各阶临界转速计算方法相同,便于程序实现,所需存储单元少,这就使得传递矩阵法成为解决转子动力学问题的一个快速而有效的方法。
轴的临界转速计算公式
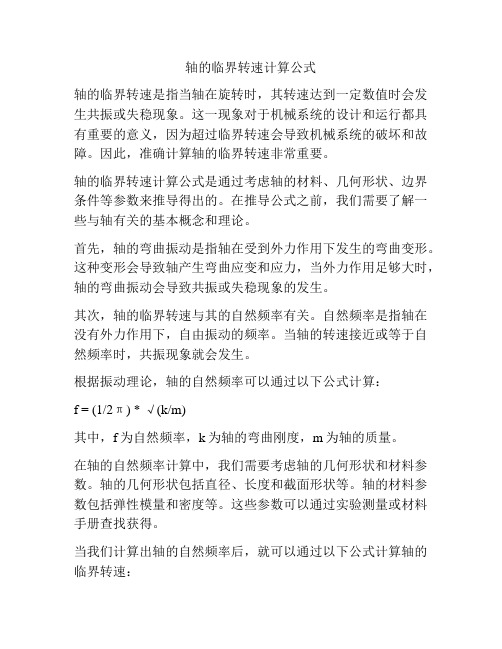
轴的临界转速计算公式轴的临界转速是指当轴在旋转时,其转速达到一定数值时会发生共振或失稳现象。
这一现象对于机械系统的设计和运行都具有重要的意义,因为超过临界转速会导致机械系统的破坏和故障。
因此,准确计算轴的临界转速非常重要。
轴的临界转速计算公式是通过考虑轴的材料、几何形状、边界条件等参数来推导得出的。
在推导公式之前,我们需要了解一些与轴有关的基本概念和理论。
首先,轴的弯曲振动是指轴在受到外力作用下发生的弯曲变形。
这种变形会导致轴产生弯曲应变和应力,当外力作用足够大时,轴的弯曲振动会导致共振或失稳现象的发生。
其次,轴的临界转速与其的自然频率有关。
自然频率是指轴在没有外力作用下,自由振动的频率。
当轴的转速接近或等于自然频率时,共振现象就会发生。
根据振动理论,轴的自然频率可以通过以下公式计算:f = (1/2π) * √(k/m)其中,f为自然频率,k为轴的弯曲刚度,m为轴的质量。
在轴的自然频率计算中,我们需要考虑轴的几何形状和材料参数。
轴的几何形状包括直径、长度和截面形状等。
轴的材料参数包括弹性模量和密度等。
这些参数可以通过实验测量或材料手册查找获得。
当我们计算出轴的自然频率后,就可以通过以下公式计算轴的临界转速:Nc = (f * 60) / p其中,Nc为轴的临界转速,f为自然频率,p为轴的极角。
值得注意的是,以上公式仅适用于简单的轴系统,对于复杂的轴系统,如多段轴或弯曲-扭转耦合系统,需要考虑更多的参数和复杂的计算方法。
最后,为了确保轴的安全运行,我们需要将计算得到的临界转速与实际运行转速进行比较。
如果实际运行转速接近或超过临界转速,就需要采取相应的措施,如增加轴的刚度、改变轴的几何形状或调整轴的支撑方式等,以降低轴的振动和共振风险。
总结起来,轴的临界转速计算公式是根据轴的自然频率和极角等参数推导得出的。
这一公式能够帮助我们了解和预测轴的振动和共振现象,从而采取相应的措施确保轴的安全运行。
然而,需要注意的是,公式适用于简单的轴系统,对于复杂的轴系统需要采用更加细致和复杂的计算方法。
转轴的挠度及临界转速计算

转轴的挠度及临界转速计算程序(一)具有集中载荷的两支点轴承的计算(如图2-118)转轴重量: Q=285(kg) L1=49转子重量: G1=365(kg) L2=52.1铁心有效长度:L fe=46(cm) L=126转子外径: D1=37.2(cm) La=36单边气隙: δ=0.4(cm) G2=20弹性模量: E= 2.06E+06(MPa)y=0.388888889气隙磁密: Bδ=5781GS z=0.285714286同步转速: n=5000r/min根据y、z值查图2-119功率: P=300kWφ=0.5过载系数: K= 2.25b处轴径212、挠度系数计算:单位:cm cm4cm cm3cm3轴a~b段d i J i X i Xi 3Xi3-X(i-1)319321.89906251533753375210490.62522.511390.6258015.625311718.324062526.518609.62572194121017.3633.537595.37518985.755131401.27406342.576765.62539170.256141884.78547.5107171.8830406.257000008000009000001000000∑ K ab=轴c~b段d i J i X i Xi 3Xi3-X(i-1)318200.96 4.591.12591.125 29321.89906259.5857.375766.25 311718.324062518.56331.6255474.25 4131401.27406327.520796.87514465.25 5141884.78532.534328.12513531.25 600000 700000 800000 900000 1000000∑ K cb=3、轴在b点的柔度:αbb= 3.44022E-06cm/kg一、绕度及临界转速计算4、磁拉力刚度:K0=8753.301622kg/cm5、初始单边磁拉力:P0=350.1320649kg6、由G1重量引起的b点绕度:f1=0.001875367cm7、滑环重量G2引起的b点绕度:f2=7.67363E-05cm8、单边磁拉力引起的b点绕度:fδ=0.001883694cm9、轴在b点的总绕度:f=0.003835798cm应小于异步电机同步电机10、转轴临界转速:n kp=6635.556016rpm二、轴的强度计算:1、最大转矩:Mmax=1289.25N.m2、bb点处的弯矩:Mbb=1419.958282N.m3、bb处的交变弯矩应力:σbb=1533266.691N/m24、bb处的剪切应力:τbb=696064.1399N/m2τn=348032.07N/m2脉动循环下的剪切应力:τ∞=870080.1749N/m25、轴在bb处受到的总负荷应力:σ= 2.319281093N/mm2应该小于材料许用[σ]=三、轴承计算:1、转子所受最大径向力:W=715.1320649kg2、a处轴承支承力:Pa=295.7014332kg3、c处轴承支承力:Pc=278.1069141kg4、轴承寿命:Lh=35986600.69小时 应大于10^5式中:ε=3.33f t=1载荷系数F f=1.1温度系数c=39600轴承额定动负荷P i=278.11当量动负荷(二)带外伸端的两支点轴承的计算(如图2-120)一、基本参数:电枢重量(G1包括转轴中部重量的2/3和滑环的重量在内)一、绕度及临界转速计算2、柔度系数计算:3、轴的柔度:α11=7.56093E-07cm/kgα22= 2.42497E-06cm/kgα12=-8.91046E-07cm/kgα21=-8.91046E-07cm/kg4、转子重量所引起的挠度:b处:f1'=0.006714438cmd处:f2'=-0.006606742cm5、磁拉力刚度:转子一:K1=136812.9233kg/cm转子二:K2=0kg/cm6、初始磁拉力:P1=1368.129233kgP2=0kg7、由磁拉力引起的挠度:F0= 1.03954E-12E0=0.896556679b处:f1"=0.001153785cmd处:f2"=-0.001359721cm8、总挠度:同步机b处:f1=0.007868222cm应该<0.008d处:f2=-0.007966462cm应该<09、临界转速:一次:n k=3506.387398rpm应该>975速计算程序(如图2-118)(cm)(cm)(cm)(cm)(kg)曲线cmcm-1[X i3-X(i-1)3]/J i10.4846530916.3375796210.0497816718.6617814727.9533112416.1324766599.61958374[X i3-X(i-1)3]/J i0.4534484472.3804045727.62086401610.32292717.17920081127.956844950.04cm0.032cm55N/mm2小时图2-120)(cm)(cm)(cm)(cm)Mpa[X i3-X(i-1)3]/J i X i2X i2-X(i-1)2[X i2-X(i-1)2]/J i X i-X i-1(X i-X i-1)/J i0.918664587-0.3518347250.3368560430.903685905[X i3-X(i-1)3]/J i X i2X i2-X(i-1)2[X i2-X(i-1)2]/J i X i-X i-1(X i-X i-1)/J i0.056840583204204.490.00397486614.30.00027796311.2813244395459340.80.1133507583.40.00101206-0.5198816461089-8456.29-0.004903061-64.7-3.75139E-0500-10890-330000000000000000000000000异步机cm应该<0.01cm cm应该<0cmrpm满足要求。
临界转速计算公式

临界转速计算公式
临界转速是指转子旋转时达到的最高转速,超过此转速会引起转
子失稳和振动,对运行安全和设备寿命产生威胁。
因此,正确计算临
界转速具有重要意义。
临界转速计算公式是通过分析转子结构和材料特性,综合考虑离
心力和刚度等因素得出的。
一般采用下列公式计算:
n_c = K * sqrt((E*I)/(m*L^3))
其中,n_c为临界转速,K为常数,E为转子材料的弹性模量,I
为转子截面惯性矩,m为转子质量,L为转子长度。
在计算时,需对转子结构和材料特性进行详细分析,确定K值,
计算出转子质量和长度,以及转子截面惯性矩等参数,进行代入计算。
临界转速计算是提高转子转速性能和安全性的重要手段。
对于已
经运行的设备,可以通过计算临界转速来查看其安全性,确定转速上
限并采取相应措施。
对于新设计的设备,临界转速计算则是制定设计
方案的重要依据之一。
此外,对于不同类型的转子,其临界转速计算
方法也有所不同,需根据具体情况确定计算公式和参数。
综上所述,临界转速计算是机械工程师必备的技能之一,对于提
高设备运行性能和延长寿命具有重要意义。
在实际工作中,需结合工
程实际,综合考虑各种因素,确定准确的临界转速,并采取相应措施,保障设备安全和稳定运行。
轴的第一临界转速

轴的第一临界转速作为机械制造行业中的一个重要部件,轴经常会出现各种的问题。
在制造和使用过程中,一些常见的轴问题包括轴断裂、轴弯曲以及轴磨损等等。
而在轴的设计和制造中,临界转速是一个非常重要的因素,需要特别注意。
本文将重点介绍轴的第一临界转速。
一、什么是轴的临界转速?临界转速是指轴转速的某一值,当轴转速达到这个值时,轴身的弯曲振动会变得非常严重,也就是说,轴的波形将表现出明显的波动形状,从而影响了轴的正常工作。
在工程学中,临界转速通常用来描述某个系统的安全运行边界。
二、轴的临界转速的计算方法在设计和制造一个轴时,需要首先计算出轴的临界转速。
一般情况下,轴的临界转速可以按照下面的公式计算得到:Nc=K×√(EI/(ρA))式中,Nc是轴的临界转速,K是一个系数,通常取值为1.2到2.5之间,EI是轴的弯曲刚度,ρ是轴材料的密度,A是轴的截面积。
三、轴的第一临界转速的意义轴的第一临界转速是指轴在没有扭矩作用下的临界转速。
当轴的转速超过第一临界转速时,轴身会出现弯曲振动,这会导致轴的疲劳寿命缩短,从而直接影响轴的可靠性和使用寿命。
因此,在实际制造中,需要尽可能保证轴的第一临界转速低于工作转速。
四、如何提高轴的临界转速为了提高轴的临界转速,可以从以下三个方面进行优化:1、材料的选择。
使用高强度材料可以提高轴的临界转速,例如使用合金钢,可使轴的强度提高20%~30%。
2、减小轴的尺寸。
轴的强度和刚度与其截面积和惯性矩有关,可以通过减小轴的最小截面尺寸来提高轴的临界转速。
3、改变轴的结构。
可以采用镟削、淬火等制造技术来调整轴的结构,提高其临界转速。
总之,轴的第一临界转速是轴制造中非常重要的一个参数。
合理计算和设计各项参数,可以有效提高轴的强度和使用寿命,从而保证轴在工作中的稳定性和可靠性。
- 1、下载文档前请自行甄别文档内容的完整性,平台不提供额外的编辑、内容补充、找答案等附加服务。
- 2、"仅部分预览"的文档,不可在线预览部分如存在完整性等问题,可反馈申请退款(可完整预览的文档不适用该条件!)。
- 3、如文档侵犯您的权益,请联系客服反馈,我们会尽快为您处理(人工客服工作时间:9:00-18:30)。
HGA75-8高压安全注射泵
轴振动和临界转速校核计算
编制
审核
批准
上海凯泉泵业(集团)有限公司
2007年8月
高压安注泵轴振动和临界转速校核计算
1)基本方法:首先求出泵转子在空气中轴的临界转速,然后考虑叶轮密封处对泵轴的临界转速影响,再求出泵轴工作时的第一临界转速。
A.泵轴计算空气中轴的临界转速:
力学模型:以两径向滑动轴承为轴两简支点,简化成等轴径两端外伸轴,以平均Φ64为轴径,超过Φ64的轴重量摊计给各零件的重量中(这样简化计算临界转速偏低而有利安全),轴上各段和圆盘重及重心与支点距离见图。
用分解代换法的邓柯莱公式计算第一临界转速。
a)轴按两支点外悬梁计算临界转速,n ck=299*λh*(E*I n/W/L3)0.5=2466.7 其中:惯性矩I
=82.3,轴重W=55.6 ,轴长L=216.1
n
支承形式系数λh=14.862(按外悬长与L之比查出)
b)外伸端悬重(外悬联轴器和推力轴承盘)后临界转速:
n c左=299*(k/W左)0.5=20656.8;k=3*E*I/(1-μ左)2/L3=24819.2,W左=左悬重=5.2;
n c右=299*(k/W右)0.5=6553.9;k=3*E*I/(1-μ右)2/L3=6005.8 W右=右悬重=23.5;
μ左、μ右分别为左右悬重心至远支点距离与两支点距之比。
c)两支点内多圆盘计算临界转速:
n ci=299*(k i/W i)0.5,k=12*E*I/μi2/(1-μi)2/L3
μi=相应圆盘重心距支点与两支距之比,W i为各相关贺盘(叶
轮、平衡鼓、机封等),分别代入后:
n c1=14482.7 n c2=5815.1 n c3=4598.7
n c4=4796.6 n c5=4535.8 n c6=4380.6
n c7=4312.0 n c8=5937.4 n c9=4412.3
n c10=4592.8 n c11=4886.4 n c12=5336.6
n c13=6148.7 n c14=13435.2
n c1、n c2、n c3分别是从吸入端机封、首级叶轮、次级叶轮。
至吐出端机封等质量和位置产生影响后的临界转速。
d) 泵轴空气中的临界转速:按邓柯莱公式计算得:
1/n c2=1/n CK2+1/n C左2+1/n C右2+1/n C12+1/n C22+。
+1/n142
泵轴空气中第一临界转速:n c=1190.4
以上计算主要参考机械工程手册21篇-机械振动的内容。
B.考虑零件叶轮密封处有水压降时对泵轴的临界转速影响:转子在泵体的水中旋转时,有密封的影响,沿密封环的缝隙压力降产生的力,P P=-k p f p(x)r,
于是:k p=π/4ΔpRλb2a;b=L/δ,a=(1/2λb+1)-2
f p(x)=2/x-2[(1-a x-2)-0.5-1];x=r/δ;Δp沿缝隙的压降,
R、L、δ缝隙密封半径、长度、径向间隙;r密封偏心;λ摩擦系数(取≈0.04)
此力是力求泵轴恢复同心位置,降低轴的挠度,提高第一临界转速。
根据多级泵情况,设P P沿缝隙长度均匀分布,引进分布水动力系数:k(x)= k p/L;得其近似解,通过推导变换后,
有ω=ω0*[1+k*L4/(EJ*π4)]0.5,ω0为泵转子在空气中的临界转速,分别求出k和1/(EJ)后,即可求得泵转子在水中临界转速ω。
k*=∫10k(ξ)y12(ξ)dξ
1/(EJ*)=∫10{1/[EJ(ξ)]}m12(ξ)dξ
就本泵情况,可用下面表达式:
k*=∑n i=1k i[Φ(ξi)-Φ(ξi-1)] =∑n i=1Δk i
1/(EJ*)=∑n i=11/(EJ1)[Φ(ξi)-Φ(ξi-1)]= ∑n i=1Δ1/(EJ1)根据泵的有关尺寸和各密封处的压降分析以及算表求得值列下表中:
在数表中:
叶轮口环、叶轮后轮毂和平衡鼓的径向间隙为0.41mm,平口环结构,缝隙前后压降:设计点平衡鼓前后压差8.0Mpa,叶轮前后压降0.73Mpa。
考虑泵要在大流量运行,在计算中压差为设计点的50%计。
按阶梯轴计1/(EJ*)=EJ=49.54x10-7N/m2。
为此:n ck=n c*[1+k*L3/(EJ*π4)]0.5=4669.5rpm
n ck为泵转子在水中的第一临界转速,高于泵实际转速 1.56倍,符合设任务书中1.25倍要求。
泵转子在水中的第一临界转速的计算方法较多,以上计算方法参考了“泵零件强度计算”(关醒凡、姚兆生编译)有关内容。