联合脱硫脱硝技术
烟气同时脱硫脱硝技术探讨

热 ; ) 附剂来源广泛 , 4吸 不存在 中毒问题 ; ) 5 工艺简单 ,
aa m n )联合脱硫脱 硝技术 ,是将 S , b t et e O 氧化 为S O 后制
程 中,活性炭会与 二氧化硫发生反应 ,在吸附 、冉生 、
除需要用 氨还 原N x ,不消耗任何其 他化学 品 ,也不 0外
循环使 用 中损耗 大 ;7)吸 附脱硫存 在脱 硫容量低 、脱 产生废水 、废物等二 次污染物 ,同时还能 回收硫酸 ,并
硫速率慢 、再生频 繁等缺点 ,导致 吸附设 备庞大 ,阻碍 可利用余热提高锅炉效率 。 了其工业化推广应用 。
本 、德 国 、美 国得到工业应用 ,活性炭脱 硫脱 硝的早期 研究 以两段法工艺为主 ,主要由吸附 、解析和硫 回收三 部分组成。烟气 进人含有 活性炭 的移 动床吸收塔 ,吸收
1 固相吸收/ 再生烟气脱 硫脱硝工艺
同时脱硫脱硝典型 的工艺有干法 ( 固相吸收和再 塔 由两部分组成 ,活性炭在垂直 吸收塔 内因重力作用从 如
新 回到吸收器 中循环使用 ;回收的二氧化硫 可进一步处 现 了该技术 的工业化 ,运行数据表明 :二氧化硫的去除
理得到硫或硫酸等副产物 ;氮氧化物通过 喷射氨或再循 率在9 %~9 . 0 9 %,氮 氧化物 的去除率在5 %~8 %【 9 0 0 2 ] 。 环至锅炉分解为氮气和水 。该工 艺常用 的吸收剂是活性 活性炭吸收工 艺的将 点表现 为: ) 有很高 的脱硫 1具 炭 、氧化铜 、分子筛 、硅胶等 ,所用 的吸收设备的床层 效率 和低 温 (O  ̄ 2 0C 条件下较 高的脱硝效率; ) I0C~ 0  ̄ ) 2
烟气同时脱硫脱硝的六种方法

烟气同时脱硫脱硝的六种方法脱硫脱硝的六种方法:1)活性炭法该工艺主体设备是一个类似于超吸附塔的活性炭流化床吸附器,在吸附器内,烟气中的SO2被氧化成SO3并溶于水中,产生稀硫酸气溶胶,随后由活性炭吸附。
向吸附塔内注入氨,氨与NOx在活性炭催化还原作用下生成N2,吸附有SO2的活性炭可进入脱附器中加热再生。
2)SNOx(WSA-SNOx)法WSA-SNOx法是湿式洗涤并脱除NOx技术。
在该工艺中烟气首先经过SCR反应器,NOx在催化剂作用下被氨气还原为N2,随后烟气进入改质器中,SO2在此被固相催化剂氧化为SO3,SO3经过烟气再热器GGH后进入WSA冷凝器被水吸收转化为硫酸。
采用SNOx技术,SO2和NOx的脱除率可达95%。
SNOx技术除消耗氨气外,不消耗其他的化学品,不产生其他湿法脱硫产生的废水、废弃物等二次污染,不产生石灰石脱硫产生的CO2,不足之处是能耗较大,投资费用较高,而且浓硫酸的储存及运输较困难。
3)NOxSO法在电除尘器(EP)下游设置流化床吸收塔(FB),用硫酸钠浸渍过的γ-Al2O3圆球作为吸收剂,吸收剂吸收NOx、SO2后,在高温下用还原性气体(CO、CH4等)进行还原,生成H2S和N2。
4)高能粒子射线法高能粒子射线法包括电子束(EBA)工艺和等离子体工艺,原理是利用高能粒子(离子)将烟气中的部分分子电离,形成活性自由基和自由电子等,氧化烟气中的NOx。
这种技术不仅能去除烟气中的NOx 和SO2,还能同时去除重金属等物质。
典型工艺过程依次包括:游离基的产生,脱硫脱硝反应,硫酸铵、硝酸铵的产生。
主要有电子束照射技术和脉冲电晕等离子体技术。
电子束照射技术脱硝率可达到75%以上,不产生废水和废渣。
脉冲电晕等离子体技术可同时脱硫、脱硝和除尘,但是耗能较大,目前对其反应机理还缺乏全面的认识。
5)湿式FGD加金属螯合物法仲兆平等发明了喷射鼓泡法用烟气脱硫脱硝吸收液,包括石灰或石灰石浆液、占石灰或石灰石浆液0.05%~0.5%(质量分数)的水溶性有机酸和占石灰或石灰石浆液0.03%~0.3%(质量分数)的铁系或铜系金属螯合物。
活性炭联合脱硫脱硝技术探讨
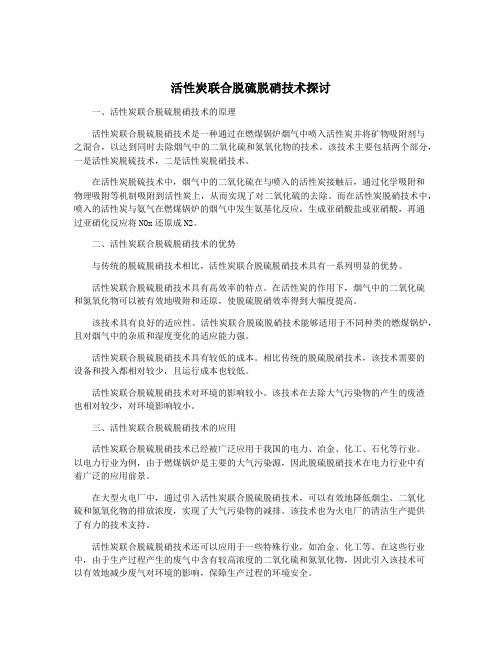
活性炭联合脱硫脱硝技术探讨一、活性炭联合脱硫脱硝技术的原理活性炭联合脱硫脱硝技术是一种通过在燃煤锅炉烟气中喷入活性炭并将矿物吸附剂与之混合,以达到同时去除烟气中的二氧化硫和氮氧化物的技术。
该技术主要包括两个部分,一是活性炭脱硫技术,二是活性炭脱硝技术。
在活性炭脱硫技术中,烟气中的二氧化硫在与喷入的活性炭接触后,通过化学吸附和物理吸附等机制吸附到活性炭上,从而实现了对二氧化硫的去除。
而在活性炭脱硝技术中,喷入的活性炭与氨气在燃煤锅炉的烟气中发生氨基化反应,生成亚硝酸盐或亚硝酸,再通过亚硝化反应将NOx还原成N2。
二、活性炭联合脱硫脱硝技术的优势与传统的脱硫脱硝技术相比,活性炭联合脱硫脱硝技术具有一系列明显的优势。
活性炭联合脱硫脱硝技术具有高效率的特点。
在活性炭的作用下,烟气中的二氧化硫和氮氧化物可以被有效地吸附和还原,使脱硫脱硝效率得到大幅度提高。
该技术具有良好的适应性。
活性炭联合脱硫脱硝技术能够适用于不同种类的燃煤锅炉,且对烟气中的杂质和湿度变化的适应能力强。
活性炭联合脱硫脱硝技术具有较低的成本。
相比传统的脱硫脱硝技术,该技术需要的设备和投入都相对较少,且运行成本也较低。
活性炭联合脱硫脱硝技术对环境的影响较小。
该技术在去除大气污染物的产生的废渣也相对较少,对环境影响较小。
三、活性炭联合脱硫脱硝技术的应用活性炭联合脱硫脱硝技术已经被广泛应用于我国的电力、冶金、化工、石化等行业。
以电力行业为例,由于燃煤锅炉是主要的大气污染源,因此脱硫脱硝技术在电力行业中有着广泛的应用前景。
在大型火电厂中,通过引入活性炭联合脱硫脱硝技术,可以有效地降低烟尘、二氧化硫和氮氧化物的排放浓度,实现了大气污染物的减排。
该技术也为火电厂的清洁生产提供了有力的技术支持。
活性炭联合脱硫脱硝技术还可以应用于一些特殊行业,如冶金、化工等。
在这些行业中,由于生产过程产生的废气中含有较高浓度的二氧化硫和氮氧化物,因此引入该技术可以有效地减少废气对环境的影响,保障生产过程的环境安全。
催化裂化烟气同时脱硫、脱硝新技术

催化裂化烟气同时脱硫、脱硝新技术随着工业的发展,烟气污染对环境和人类健康造成了严重的影响。
而其中硫氧化物和氮氧化物是主要的污染物之一。
因此,研究开发一种能够同时高效脱除烟气中的硫氧化物和氮氧化物的催化裂化新技术显得尤为重要。
催化裂化烟气同时脱硫、脱硝技术是一种基于催化作用的先进技术,能够在高温条件下实现烟气中硫氧化物和氮氧化物的去除,有效减少其对环境的影响。
该技术综合应用了催化剂、吸附剂等多种材料,通过化学反应达到同时脱硫、脱硝的目的。
首先,催化剂在催化裂化过程中起到了重要的作用。
催化剂可以降低反应温度和活化能,提高反应速率和选择性,从而促进硫氧化物和氮氧化物的催化转化。
催化剂的选择和设计对于技术的效率和稳定性具有关键影响。
目前常用的催化剂包括贵金属类、过渡金属氧化物类等,其性能和稳定性经过多次研究得到不断改善。
其次,吸附剂在催化裂化烟气处理中也起到了重要作用。
吸附剂可以吸附烟气中的硫氧化物和氮氧化物,使其从气相转化为固相,从而实现脱硫、脱硝的效果。
常用的吸附剂有活性炭、分子筛等,其物理性能和吸附能力的改进对于技术的性能和经济效益具有重要意义。
通过将催化剂和吸附剂结合使用,催化裂化烟气同时脱硫、脱硝技术能够较好地解决烟气污染问题。
催化裂化烟气处理工艺中,烟气经过预处理后,进入催化裂化装置,通过催化剂的作用,使硫氧化物和氮氧化物发生催化反应转化为无害物质。
然后,烟气经过吸附剂的处理,吸附剂将烟气中的硫氧化物和氮氧化物吸附下来,使其被固定在吸附剂上,达到脱硫、脱硝的效果。
最后,经过处理后的烟气排放出去时,其硫氧化物和氮氧化物含量大幅降低,对环境的影响也得到了有效的控制。
总的来说,催化裂化烟气同时脱硫、脱硝新技术是一种高效、环保的烟气处理技术。
通过合理选择和设计催化剂和吸附剂,可以实现烟气中硫氧化物和氮氧化物的高效去除,减少对环境的影响。
随着技术的不断进步和优化,催化裂化烟气处理技术将会在工业生产中得到广泛应用,为改善环境质量和保护人类健康做出贡献。
尿素湿法联合脱硫脱硝技术研究

尿素湿法联合脱硫脱硝技术研究摘要:主要研究尿素湿法联合脱硫脱硝技术,对尿毒脱硫、脱硝以及联合反应原理进行了认真研究,并通过实际运行,对该项技术在烟气脱硫脱硝中的应用效果进行了详细讨论,认为该项技术的反应产物能够用于化肥生产,有着一定的经济效益,有着较好的脱硫脱硝效果,并且运行成本更低。
关键词:尿素湿法;脱硫脱硝煤仍然是我国主要的能源形式,火力发电在我国电力供应中占有绝对的优势,大量的煤炭燃烧产生了严重的环境污染,废气中的硫氧化合物和氮氧化合物是酸雨和光化学烟雾的罪魁祸首,而进行煤炭脱硫脱硝是降低煤炭燃烧污染最有效的措施,尿素湿法联合脱硫脱硝技术作为一种优秀的脱硫脱硝技术能够将回收的硫酸铵制作为化肥,是一种十分优秀的、变废为宝的技术,有着广阔的应用前景。
一、反应原理分析热力学过程都具有明显的方向性,能够自发进行的热力过程反向过程不能自发进行,热力学第二定律就对能量转换和传递过程的方向性有着非常清晰的描述。
(一)尿素脱硫机理尿素湿法烟气脱硫化学反应链如下:图1-1 脱硫化学反应链具体反应过程有三个阶段:1.尿素吸收液物理吸收烟气中的SO2、O2烟气中SO2 含量一般在0.05-0.3%,氧气含量在2-4%,烟气总压在1 大气压左右,水溶液和烟气达到气液相平衡时溶液中SO2 和O2 的浓度很低。
低温下的吸收液对SO2 溶液的吸收脱除作用主要依靠物理作用,化学作用不明显,SO2 会不断在吸收液中富集,液相浓度不断上升,但是在SO2 气相浓度变化不大的情况下,物理吸收能力不会下降。
2.尿素水解尿素水解为氨基甲酸铵。
尿素溶液呈弱碱性,溶液中会发生水解:错误!未找到引用源。
(1-1)生成氨基甲酸铵,这是一个放热反应,常温下的水解反应很慢,溶液中氨基甲酸铵组分很少,但是溶液温度上升,在70℃以上时水解反应加快。
温度一定情况下尿素水解速度可以通过公式计算出来:错误!未找到引用源。
(1-2)式中:v-尿素水解速度(g·L-1·s-1);K-尿素水解速度常数,不同温度下水解速度变化范围很大,溶液温度对尿素水解速度常数影响十分明显。
活性焦联合脱硫脱硝技术及其在我国的适用性分析

分 为 2大类 ,即同时脱硫 脱 硝 (iut eu O/ Sm lnos : a S
大学( 北京) 化学与环境 工程学院 20 0 8级在读硕士研究 生,研 究
方 向 洁 净 煤 技术 。
( .中国矿业 大学 ( 1 北京 )化 学与环境 工程学 院 ,北 京 10 8 ; 0 0 3 2 .煤炭科 学研究 总院 北 京煤化 工研究 分院 ,北 京 10 1 ) 0 0 3 摘 要 :介 绍 了国 内外脱硫 脱硝 工艺技 术的发 展情 况 ;重点分 析 了活 性 焦联合 脱 硫脱 硝技
关键词 :烟 气 ;活 性焦 ;脱硫 ;脱 硝 ;适用 性
中图分类 号 :X 0 . 7 13
文 献标 识码 :A
文章 编号 :10 —3 7 2 1 ) 30 3 - 0 58 9 (0 0 0 -0 4 4 0 中使 用 最 多 的 是 石 灰 石/ 灰一石 膏 湿 法 工 艺 。 石
和 2. J O 2 6 Mtl 。S ,和 N 是 大 气 的 主 要 污 染 J O 物 ,它 们 产 生 酸 雨 、形 成 光 化 学 烟 雾 、破 坏 臭
这是 目前脱 硫效 率 最 高 的 烟 气脱 硫 ( G 技术 , F D) 在钙 硫摩尔 比值 为 11~25时 ,脱 硫 效 率 可达 . . 9 % ~ 。我 国对 此工艺 主要 是在 引进 国外技 术 的 8 基础上 进行 消化吸 收 ,但 在一些 关键 设备 的制造
煤
炭
加
工
与
综
合
利
用
No 3, 2 0 . 01
烟气脱硫脱硝 技术方案

1、化学反应原理任意浓度的硫酸、硝酸,都能够跟烟气当中细颗粒物的酸、碱性氧化物产生化学反应,生成某酸盐和水,也能够跟其它酸的盐类发生复分解反应、氧化还原反应,生成新酸和新盐,通过应用高精尖微分捕获微分净化处理技术产生的巨大量水膜,极大程度的提高烟气与循环工质接触、混合效率,缩短工艺流程,在将具有连续性气、固、液多项流连续进行三次微分捕获的同时,连续进行三次全面的综合性高精度微分净化处理。
2、串联叠加法工作原理现有技术装备以及烟气治理工艺流程的效率都是比较偏低,例如脱硫效率一般都在98%左右甚至更低,那么,如果将三个这样工作原理的吸收塔原型进行串联叠加性应用,脱硫效率一定会更高,例如99.9999%以上。
工艺流程工作原理传统技术整治大气环境污染,例如脱硫都是采用一种循环工质,那么,如果依次采用三种化学性质截然不同的循环工质,例如稀酸溶液、水溶液和稀碱溶液进行净化处理,当然可以十分明显的提高脱除效率,达到极其接近于百分百无毒害性彻底整治目标.1、整治大气环境污染,除尘、脱硫、脱氮、脱汞,进行烟气治理,当然最好是一体化一步到位,当然首选脱除效率最高,效价比最高,安全投运率最高,脱除污染因子最全面,运行操作最直观可靠,运行费用最低的,高效除尘、脱硫、脱氮、脱汞一体化高精尖技术装备。
2、高效除尘、脱硫、脱氮、脱汞一体化高精尖技术装备,采用最先进湿式捕获大化学处理技术非选择性催化还原法,拥有原创性、核心性、完全自主知识产权,完全国产化,发明专利名称《一种高效除尘、脱硫、脱氮一体化装置》,发明专利号。
3、吸收塔的使用寿命大于30年,保修三年,耐酸、耐碱、耐摩擦工质循环泵,以及其它标准件的保修期,按其相应行业标准执行.4、30年以内,极少、甚至可以说不会有跑、冒、滴、漏、渗、堵现象的发生。
5、将补充水引进到3#稀碱池入口,根据实际燃煤含硫量和烟气含硝量调整好钠碱量以及相应补充水即可正常运行。
6、工艺流程:三个工质循环系统的循环工质,分别经过三台循环泵进行加压、喷淋。
科技成果——工业烟气钢渣法联合脱硫脱硝技术

科技成果——工业烟气钢渣法联合脱硫脱硝技术
技术开发单位
郑州中科新兴产业技术研究院、中国科学院过程工程研究所
适用范围
主要适用于钢铁、焦炭、水泥、玻璃等非电行业。
成果简介
该技术在钢渣法脱硫的基础上,开发了烟气臭氧氧化钢渣联合脱硫脱硝与尾渣资源化技术。
突破了强化吸收助剂开发、联合脱硫脱硝高效吸收塔设计、脱硫脱硝废水中硝酸盐分离提取与尾渣建材化/生态化利用等关键技术。
技术效果
该技术已开展千方级中试技术验证,结果表明,SO2脱除率>95%,NOx脱除率>70%,烟气污染物出口浓度满足国标特殊区域排放要求。
该技术实现了烟气中SO2和NOx在一塔中的同步脱除和钢渣的规模化协同处置,具有臭氧用量小、投资与运行成本低、无废水废渣排放、副产品效益高等优势,形成了以废治废、高效利用的循环经济型废气治理新模式。
应用情况
在小试试验基础上,中国科学院过程工程研究所与宁波太极环保设备有限公司(以下简称太极环保)合作,于太极环保厂区内建立了3000m3/h烟气钢渣法联合脱硫脱硝中试装置。
经过一个月的稳定运行,试验结果表明,整套装置运行良好,SO2脱除率达99%左右,NOx
脱除率达70%左右,出口烟气污染物浓度满足国标要求。
地址:宁波市慈溪市北三环西路。
市场前景
该技术进一步可以推广至玻璃、水泥、工业锅炉、垃圾焚烧炉、陶瓷窑炉、石化催化裂化烟气、化工烟气等行业,支撑这些行业对脱硫脱硝技术的迫切需求,整个市场容量保守估计超过2000亿元。
- 1、下载文档前请自行甄别文档内容的完整性,平台不提供额外的编辑、内容补充、找答案等附加服务。
- 2、"仅部分预览"的文档,不可在线预览部分如存在完整性等问题,可反馈申请退款(可完整预览的文档不适用该条件!)。
- 3、如文档侵犯您的权益,请联系客服反馈,我们会尽快为您处理(人工客服工作时间:9:00-18:30)。
联合脱硫脱硝技术1 概述随着我国经济的快速发展,排放的也不断增长。
由煤炭燃烧所释放的占总排放量的85%,占总排放量的60%,二者所引起的酸雨量占总酸雨量的82%。
据有关研究指出,我国每年排放造成的经济失约亿万元,现在每年我国和酸雨污染造成的经济损失约5000亿元。
自上世纪70年代开始,发达国家在多年烟气so2排放控制技术研究的基础上,开始工业烟气中和同时脱除的研究。
目前,脱硫脱硝一体化技术多处于研究阶段,都没有得到大规模的工业应用。
开发技术简单,运行成本低,具有良好运行性能的脱硫脱硝一体化技术将是未来烟气综合治理技术的发展方向。
2 方式一、传统脱硫脱硝当今国内外广泛使用的脱硫脱硝一体化技术主要是湿式烟气脱硫和选择性催化还原或选择性非催化还原技术脱硝组合。
湿式烟气脱硫常用的是采用石灰或石灰石的钙法,脱硫效率大于90%,其缺点是工程庞大,初投资和运行费用高,且容易形成二次污染。
选择性催化还原脱硝反应温度为250~450℃时,脱硝率可达70%~90%。
该技术成熟可靠,目前在全球范围尤其是发达国家应用广泛,但该工艺设备投资大,需预热处理烟气,催化剂昂贵且使用寿命短,同时存在氨泄漏、设备易腐蚀等问题。
选择性非催化还原温度区域为870~1200℃,脱硝率小于50%。
缺点是工艺设备投资大,需预热处理烟气,设备易腐蚀等问题。
二、干法脱硫脱硝干法烟气脱硫脱硝一体化技术包括四个方面:固相吸收/再生法、气/固催化同时脱硫脱硝技术、吸收剂喷射法以及高能电子活化氧化法。
3 相关技术固体吸附再生法主要有碳质材料吸附法、吸附法。
1.碳质材料吸附法根据吸附材料的不同又可分为活性炭吸附法和活性焦吸附法两种,其脱硫脱硝原理基本相同。
活性炭吸附法整个脱硫脱硝工艺流程分两部分:吸附塔和再生塔。
而活性焦吸附法只有一个吸附塔,塔分两层,上层脱硝,下层脱硫,活性焦在塔内上下移动,烟气横向流过塔。
该方法的主要优点有:①具有很高的脱硫率(98%)和低温(100~200℃)条件下较高的脱硝率(80%);②处理后的烟气排放前不需加热;③不使用水,没有二次污染;④吸附剂来源广泛,不存在中毒问题,只需补充消耗掉的部分;⑤能去除湿法难去除的so2;⑥能去除废气中的hf、hcl、砷、汞等污染物,是深度处理技术;⑦具有除尘功能,出口排尘浓度小于10mg/m3;⑧可以回收副产品,如:高纯硫磺、浓硫酸、化学肥料等;⑨建设费用低,运转费用经济,占地面积小。
新的活性炭纤维脱硫脱硝技术。
该技术是将活性炭制成直径20μm左右的纤维状,极大地增大了吸附面积,提高了吸附和催化能力。
经过发展,现在该技术脱硫脱硝率可达90%。
近年来有人将活性炭吸附和微波技术结合起来,提出了微波诱导催化还原脱硫脱硝技术。
该技术用活性炭作为氮氧化物载体,利用微波能诱导可实现脱硫脱硝率达到90%以上。
该法的吸附剂是以r-氧化铝为载体,用碱或碱成分盐的溶液喷涂载体,然后将浸泡过的吸附剂加热、干燥,去除残余水分而制成。
吸附剂吸附饱和后可以再生,再生过程是将吸附饱和的吸附剂送入加热器,在温度600℃左右加热使得nox被释放,然后将nox循环送回锅炉的燃烧器中。
在燃烧器中nox的浓度达到一个稳定状态,且形成一个化学平衡。
这样就不会再生成nox而只能是n2,从而抑制nox生成。
在再生器中加入还原气体,就会产生高浓度的so2、h2s混合气体,利用克劳斯法可以进行硫磺的回收。
cuo吸附脱硫脱硝工艺法采用吸附剂进行脱硫脱硝,整个反应分两步:1)在吸附器中:在300℃~450℃的温度范围内,吸附剂与二氧化硫反应,生成cuso4;由于cuo和生成的cuso4对nh3还原氮氧化物有很高的催化活性,结合scr法进行脱硝。
2)在再生器中:吸附剂吸收饱和后生成的cuso4被送到再生器中再生,再生过程一般用h2或ch4对cuso4进行还原,再生出的二氧化硫可通过claus装置进行回收制酸;还原得到的金属铜或cu2s在吸附剂处理器中用烟气或空气氧化成cuo,生成的cuo又重新用于吸收还原过程。
该工艺能达到90%以上的二氧化硫脱除率和75%~80%的氮氧化物脱除率。
吸附法反应温度要求高,需加热装置,并且吸附剂的制各成本较高。
近年来随着研究的进展,出现了将活性焦/炭(ac)与cuo结合的方法。
二者结合后可制各出活性温度适宜的催化吸收剂,克服了ac使用温度偏低和cuo/al2o3活性温度偏高的缺点。
采用一步法干式洗涤,可脱除烟气中99%以上的硫氧化物,并可选择性地或同时除去99%的氮氧化物,排放尾气完全符合环境标准。
由于它采用无机化合物作吸收剂,而不是传统工艺中的氨,因此其副产物是可回收的硝酸盐和硫酸盐,而不是需要堆埋的污染环境的石膏副产物。
该工艺适用于以天然气或煤为燃料的发电厂,目前仍在实验阶段,未见诸工业应用。
[2]气固催化脱硫脱硝技术此类工艺使用催化剂降低反应活化能,促进二氧化硫和氮氧化物的脱除,比起传统的工艺,具有更高的氮氧化物脱除效率。
选择性催化还原法scr去除nox。
此工艺可脱除95%的so2、90%的nox和几乎所有的颗粒物。
该工艺除了将烟气中的so2转化为so3后制成硫酸,以及用scr除去nox外,还能将co及未燃烧的烃类物质氧化为co2和水。
此工艺脱硫脱硝效率较高,没有二次污染,技术简单,投资及运行费用较低,适用于老厂的改造。
是一种新型的高温烟气净化工艺,该工艺能同时去除二氧化硫、氮氧化物和烟尘,并且都是在一个高温的集尘室中集中处理。
由于将三种污染物的脱除集中在一个设备上,从而降低了成本并减少了占地面积。
其缺点是由于要求的烟气温度为300℃~500℃,就需要采用特殊的耐高温陶瓷纤维编织的过滤袋,因而增加了成本。
烟气清洁工艺已发展到中试阶段,燃煤锅炉烟气中的so2和nox的脱除效率能达到99%以上。
该工艺是在单独的还原步骤中同时将so2催化还原为h2s,nox还原为n2,剩余的氧还原为水;从氢化反应器的排气中回收h2s;从h2s富集气体中生产元素硫。
循环流化床技术在最近几年得到了快速发展,不仅技术成熟可靠,而且投资运行费用也大为降低,为了开发更经济、高效、可靠的联合脱硫脱硝方法,人们将循环流化床引入烟气同时脱硫脱硝技术中。
烟气循环流化床联合脱硫脱硝技术是用消石灰作为脱硫的吸收剂脱除二氧化硫,产物主要是caso4和10%的caso3;脱硝反应使用氨作为还原剂进行选择催化还原反应,催化剂是具有活性的细粉末化合物feso4·7h2o,不需要支撑载体,运行温度在385℃。
吸收剂喷射技术将碱或尿素等干粉喷入炉膛、烟道或喷雾干式洗涤塔内,在一定条件下能同时脱除二氧化硫和氮氧化物。
脱硝率主要取决于烟气中的二氧化硫和氮氧化物的比、反应温度、吸收剂的粒度和停留时间等。
不过当系统中二氧化硫浓度低时,氮氧化物的脱除效率也低。
因此,该工艺适用于高硫煤烟气处理。
炉膛石灰(石)/尿素喷射同时脱硫脱硝工艺将炉膛喷钙和选择非催化还原结合起来,实现同时脱除烟气中的二氧化硫和氮氧化物。
喷射浆液由尿素溶液和各种钙基吸收剂组成,总含固量为30%,ph值为5~9,与干ca(oh)2吸收剂喷射方法相比,浆液喷射增强了so2的脱除,这可能是由于吸收剂磨得更细、更具活性。
整体干式so2/nox排放控制工艺采用下置式燃烧器,这些燃烧器通过在缺氧环境下喷入部分煤和空气来抑制氮氧化物的生成。
过剩空气的引入是为了完成燃烧过程,以及进一步除去氮氧化物。
低氮氧化物燃烧器预计可减少50%的氮氧化物排放,而且在通入过剩空气后可减少70%以上的nox排放。
无论是整体联用干式so2/nox排放控制系统,还是单个技术,都可应用于电厂或工业锅炉上,主要适用于较老的中小型机组。
电子活化氧化法目前主要有电子束照射法和脉冲电晕等离子体法。
1.电子束照射法利用阴极发射并经电场加速形成高能电子束,这些电子束辐照烟气时产生自由基,再和sox 和nox反应生成硫酸和硝酸,在通入氨气(nh3)的情况下,产生(nh4)2so4和nh4no3氨盐等副产品。
脱硫率90%以上,脱硝率80%以上。
但耗电量大(约占厂用电的2%),运行费用高。
2.脉冲电晕等离子体法该方法由于具有设备简单、操作简便,显著的脱硫脱硝和除尘效果以及副产物可作为肥料回收利用等优点而成为国际上脱硫脱硝的研究前沿。
脉冲电晕等离子体技术和电子束法均属于等离子体法.脉冲电晕与传统的液相(氢氧化钙或碳酸氢铵)吸收技术相结合,提高了烟气二氧化硫和氮氧化物的脱除效率,实现脱硫、脱硝的一体化。
脉冲电晕放电脱硫脱硝有着突出的优点,在节能方面有很大的潜力,对电站锅炉的安全运行也没有影响。
湿法脱硫脱硝湿法烟气同时脱硫脱硝工艺通常在气/液段将no氧化成no2,或者通过加入添加剂来提高no的溶解度。
湿式同时脱硫脱硝的方法目前大多处于研究阶段,包括氧化法和湿式络合法。
(一)氧化法氯酸氧化工艺是采用湿式洗涤系统,在一套设备中同时脱除烟气中的二氧化硫和氮氧化物。
工艺采用氧化吸收塔和碱式吸收塔两段工艺,在脱除二氧化硫和氮氧化物的同时脱除有毒微量金属元素,如as、be、cd、cr、pb、hg和se。
isabelle等研究了在酸性条件下利用双氧水将nox和so2氧化成硝酸和硫酸的工艺。
黄磷氧化法是将no氧化为no2,与液态的碱性吸收浆液反应生成硫酸盐和硝酸盐,对二氧化硫和氮氧化物的去除率达到95%以上,但黄磷具有易燃性、不稳定性和一定的毒性,需用预处理的方法解决这些问题。
(二)湿式络合吸收工艺湿式络合吸收工艺一般采用铁或钴作催化剂。
在水溶液中加入能络合no的络合剂后,使之结合成络合物。
与络合剂结合的no可与溶液中的so32-/hso3-发生反应,形成一系列n-s 化合物,并使络合剂再生。
该工艺需通过从吸收液中去除连二硫酸盐、硫酸盐和n-s化合物以及三价铁螯合物还原成亚铁螯合物而使吸收液再生。
湿式络合吸收法工艺可以同时脱硫脱硝,但目前仍处于试验阶段。
影响其工业应用的主要障碍是,反应过程中螯合物的损失和金属螯合物再生困难、利用率低,因而存在运行费用高等问题。
脱硫脱硝一体化工艺已经成为各国控制烟气污染的研发热点,目前大多数脱硫脱硝一体化工艺仅停留在研究阶段,尽管已经有少量示范工程应用,但由于运行费用较高制约了其大规模推广应用。
开发适合我国国情,投资少、运行费用低、效率高、副产品资源化的脱硫脱硝一体化技术成为未来发展的重点。