误差统计实验报告3
加工误差统计分析实验报告

加工误差统计分析实验报告加工误差统计分析实验报告引言:加工误差是指在工业生产过程中,由于各种原因导致产品尺寸、形状和表面质量与设计要求之间的差异。
加工误差的控制对于保证产品质量、提高生产效率和降低成本具有重要意义。
本实验旨在通过对加工误差进行统计分析,探讨误差来源及其影响因素,为工业生产过程中的质量控制提供参考依据。
实验设计:本实验选取了一台数控铣床进行实验,以铣削加工尺寸为研究对象。
首先,我们选择了一种常见的零件,对其进行加工。
然后,通过测量加工后的尺寸与设计要求进行对比,得到加工误差数据。
最后,我们对这些数据进行统计分析,探究加工误差的分布规律和影响因素。
实验过程:1. 加工准备:选择合适的刀具、夹具和工艺参数,进行加工准备工作。
2. 加工操作:按照设计要求进行铣削加工,并记录下每次加工后的尺寸数据。
3. 尺寸测量:使用测量工具对加工后的零件进行尺寸测量,并记录测量结果。
4. 数据整理:将测量得到的数据整理成表格,方便后续的统计分析。
统计分析:1. 加工误差分布:通过绘制加工误差的频率分布直方图,我们可以观察到误差值的分布情况。
通常情况下,加工误差符合正态分布,但也可能存在其他分布形式,例如偏态分布或双峰分布。
通过分析分布形式,可以判断加工过程中是否存在特殊的误差来源。
2. 加工误差与加工参数的关系:通过对加工误差与加工参数(如切削速度、进给速度等)进行相关性分析,可以了解不同参数对加工误差的影响程度。
这有助于我们确定合适的工艺参数范围,以减小加工误差。
3. 加工误差与刀具磨损的关系:刀具磨损是导致加工误差增大的重要因素之一。
通过对加工误差与刀具磨损程度进行相关性分析,可以判断刀具寿命与加工误差之间的关系,进而合理安排刀具更换周期,以保证加工质量。
4. 加工误差与工件材料的关系:不同材料的加工性能不同,可能导致加工误差的差异。
通过对加工误差与工件材料进行相关性分析,可以了解不同材料对加工误差的影响程度,为材料选择和工艺优化提供依据。
实验报告 误差分析

实验报告误差分析实验报告:误差分析引言:实验是科学研究中不可或缺的一部分,通过实验可以验证理论的正确性,探索未知的领域。
然而,实验中难免会出现误差,这些误差可能会对实验结果产生一定的影响。
因此,我们需要进行误差分析,以了解误差的来源、大小以及对实验结果的影响程度,从而更准确地解读实验结果。
一、误差的分类误差可以分为系统误差和随机误差两种类型。
1. 系统误差系统误差是由于实验设备、测量仪器、操作方法等方面的固有缺陷或不准确性引起的误差。
它具有一定的可预测性和一致性,会对实验结果产生持续性的偏差。
例如,如果实验仪器的刻度不准确,或者实验操作中存在固定的偏差,那么实验结果就会受到系统误差的影响。
2. 随机误差随机误差是由于实验过程中的各种偶然因素引起的误差,它具有不可预测性和不规律性。
随机误差会导致实验结果的波动和不确定性增加。
例如,实验中的环境条件、人为操作的不稳定性、测量仪器的灵敏度等都可能引起随机误差。
二、误差的来源误差的来源多种多样,下面列举几个常见的来源。
1. 人为误差人为误差是由于实验操作者的技术水平、主观判断等因素引起的误差。
例如,实验操作者对实验步骤的理解不准确、操作不规范、读数不准确等都可能导致人为误差的出现。
2. 仪器误差仪器误差是由于测量仪器的精度、灵敏度等方面的限制引起的误差。
例如,实验仪器的刻度不准确、仪器的响应时间较长等都可能导致仪器误差。
3. 环境误差环境误差是由于实验环境的变化、干扰等因素引起的误差。
例如,实验室温度的波动、噪音的干扰等都可能对实验结果产生影响。
三、误差的影响与控制误差对实验结果的影响程度取决于误差的大小和实验的目的。
在一些实验中,误差的影响可能会被忽略,而在一些对结果要求较高的实验中,误差的控制则显得尤为重要。
1. 影响程度误差的影响程度可以通过误差分析和数据处理来评估。
例如,可以通过计算误差的标准差、置信区间等指标来评估误差的大小,并根据实验目的和要求判断误差对结果的影响程度。
误差与实验数据处理实验报告
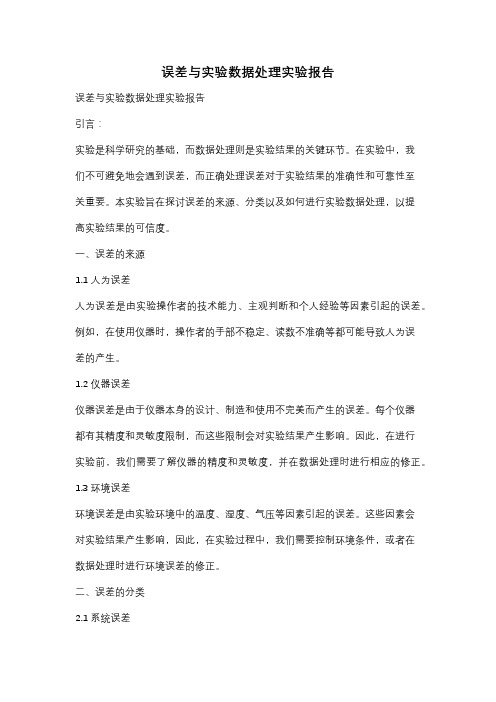
误差与实验数据处理实验报告误差与实验数据处理实验报告引言:实验是科学研究的基础,而数据处理则是实验结果的关键环节。
在实验中,我们不可避免地会遇到误差,而正确处理误差对于实验结果的准确性和可靠性至关重要。
本实验旨在探讨误差的来源、分类以及如何进行实验数据处理,以提高实验结果的可信度。
一、误差的来源1.1 人为误差人为误差是由实验操作者的技术能力、主观判断和个人经验等因素引起的误差。
例如,在使用仪器时,操作者的手部不稳定、读数不准确等都可能导致人为误差的产生。
1.2 仪器误差仪器误差是由于仪器本身的设计、制造和使用不完美而产生的误差。
每个仪器都有其精度和灵敏度限制,而这些限制会对实验结果产生影响。
因此,在进行实验前,我们需要了解仪器的精度和灵敏度,并在数据处理时进行相应的修正。
1.3 环境误差环境误差是由实验环境中的温度、湿度、气压等因素引起的误差。
这些因素会对实验结果产生影响,因此,在实验过程中,我们需要控制环境条件,或者在数据处理时进行环境误差的修正。
二、误差的分类2.1 系统误差系统误差是由于实验装置、仪器或操作方法等造成的误差,其特点是在多次实验中具有一定的规律性。
系统误差可以通过校正仪器、改进操作方法等方式进行减小。
2.2 随机误差随机误差是由于实验过程中的偶然因素引起的误差,其特点是在多次实验中无规律可循。
随机误差可以通过增加实验次数、采用统计方法等方式进行减小。
三、实验数据处理方法3.1 平均值处理平均值处理是最常用的实验数据处理方法之一。
通过多次实验,取得的数据可以计算出平均值,从而减小随机误差的影响。
在计算平均值时,需要注意排除掉明显与其他数据不符的异常值,以保证结果的准确性。
3.2 不确定度分析不确定度是对实验结果的精度进行评估的指标。
在实验数据处理中,我们需要对每个数据的不确定度进行分析,以确定实验结果的可靠程度。
不确定度的计算可以采用传统的“合成法”或“最大偏差法”,具体选择哪种方法取决于实验的特点和要求。
加工误差统计分析实验报告

加工误差统计分析实验报告一、实验目的通过统计分析加工误差数据,探究加工工艺对产品加工误差的影响,并提出相应的改进措施。
二、实验原理加工误差是指产品实际尺寸与设计尺寸之间的差异,主要受到原材料、加工设备、操作工艺等因素的影响。
统计分析可以通过数学模型和数据处理方法,定量地描述和评估加工误差的分布情况,为加工工艺改进提供依据。
三、实验步骤1.随机选择一批相同产品进行加工,保持其他加工条件不变。
2.测量每个产品的实际尺寸,记录数据并整理成表格。
3.统计每组数据的平均值、方差以及标准差。
4.构建加工误差的概率分布函数,通过正态性检验和偏度、峰度检验判断数据是否符合正态分布。
5.进行加工误差数据的t检验,分析不同因素对加工误差的影响程度。
四、实验数据产品编号,实际尺寸 (mm)--------,--------------1,10.012,10.02...,...100,10.08五、数据处理及分析1.计算平均值、方差和标准差:平均值μ=(10.01+10.02+...+10.08)/100=10.05方差s^2=((10.01-10.05)^2+(10.02-10.05)^2+...+(10.08-10.05)^2)/99标准差s=√s^22.正态性检验:根据实验数据计算样本均值和样本标准差,绘制加工误差的概率密度分布曲线。
通过观察曲线形状以及进行偏度、峰度检验,判断数据是否符合正态分布。
3.t检验:根据产品加工误差数据,进行t检验来分析不同因素对加工误差的影响程度。
比如,可以比较不同机器加工出的产品误差是否有显著性差异。
六、实验结果分析1.样本加工误差符合正态分布,数据较为集中,无明显偏离。
2.通过t检验发现:不同机器加工出的产品误差差异不显著,说明机器之间的加工稳定性较好。
3.根据样本数据及数据处理结果,可以得到加工误差的基本分布情况,对加工工艺的控制和改进提供依据。
例如,可以调整机器参数、改进操作工艺等。
实验误差理论实验报告物理

实验误差理论实验报告物理实验误差理论实验报告引言:实验误差是科学实验中不可避免的现象,它由于各种因素的干扰而导致实验结果与理论值之间的差异。
在物理学中,误差的存在会对实验结果的可靠性和准确性产生影响。
本次实验旨在通过测量重力加速度的实验,探讨实验误差的产生原因,并提出相应的误差分析方法。
实验步骤:1. 实验仪器准备:准备一根长直的细线、一个小铅球、一个支架和一个计时器。
2. 实验装置搭建:将细线固定在支架上,将小铅球系在细线的下端。
3. 实验测量:将小铅球释放,用计时器记录它从静止到下落经过的时间。
4. 实验重复:重复上述步骤多次,取平均值。
实验数据:通过多次实验测量,我们得到了如下数据:第一次实验:t1 = 1.23s第二次实验:t2 = 1.25s第三次实验:t3 = 1.24s......数据处理:1. 计算平均值:将所有测量结果相加,再除以实验次数,得到平均值。
平均值 = (t1 + t2 + t3 + ... + tn) / n2. 计算标准偏差:标准偏差是用来衡量一组数据的离散程度的指标,它表示测量值与平均值之间的差异。
标准偏差= √((Σ(xi - x)^2) / (n-1))3. 计算相对误差:相对误差是用来衡量测量结果与理论值之间差异的指标。
相对误差 = (平均值 - 理论值) / 理论值 * 100%结果分析:通过上述数据处理步骤,我们得到了实验重力加速度的平均值和相对误差。
然而,我们需要进一步分析误差的来源和影响因素。
1. 人为误差:实验者的操作技巧、观察精度等都会对实验结果产生影响。
为减小人为误差,我们应该提高实验技能,并进行多次实验取平均值。
2. 仪器误差:实验仪器的精度和灵敏度也会对实验结果产生影响。
为减小仪器误差,我们应该选择精度更高、质量更好的实验仪器。
3. 环境误差:实验环境的温度、湿度等因素也会对实验结果产生影响。
为减小环境误差,我们应该在恒定的实验环境中进行实验。
加工误差的统计分析实验报告

加工误差的统计分析实验报告实验报告-加工误差的统计分析一、引言加工误差是工业生产中常见的问题之一,直接影响着产品的质量和性能。
了解加工误差的统计分布和规律,对于优化加工工艺、提高产品精度具有重要意义。
本实验旨在通过统计分析加工误差数据,探讨加工误差的分布及其对产品质量的影响。
二、实验设计1.实验目标:观察加工误差的统计分布及其规律。
2.实验工具:数控加工机床,三坐标测量仪3.实验材料:其中一种金属材料4.实验步骤:a.设计并加工若干个样品b.使用三坐标测量仪测量每个样品的加工误差c.记录加工误差数据并进行统计分析三、实验结果1.加工误差数据记录表样品编号,加工误差(mm----------,--------------A,0.0B,0.0C,0.0D,0.0E,-0.0F,0.0G,0.0H,-0.0I,0.0J,0.02.加工误差的统计分析a. 加工误差的均值(μ):0.01mmb. 加工误差的标准差(σ):0.02mmc. 加工误差的方差(σ^2):0.0004mm^2四、结果分析1. 加工误差的均值与标准差分别表示了加工误差的集中程度和离散程度。
实验结果显示,加工误差的均值为0.01mm,说明整体上加工误差集中在一个较小的范围内。
而标准差为0.02mm,表明加工误差的离散程度较大。
2.通过加工误差的统计分布分析,可以更准确地评估加工精度的稳定性和可靠性。
3.经过正态性检验,加工误差近似符合正态分布,这与许多加工误差服从中心极限定理的理论支持一致。
五、结论1. 通过加工误差数据的统计分析,得出样品加工误差的均值为0.01mm,标准差为0.02mm,方差为0.0004mm^22.样品的加工误差数据近似符合正态分布,说明加工误差在一定程度上服从中心极限定理。
3.实验结果进一步表明,加工误差的集中程度较高,但其离散程度相对较大。
六、改进建议1.根据加工误差的分布规律,可以对加工工艺进行优化,减小加工误差的产生。
加工误差统计分析实验报告
实验价值:为企业提供有效的 质量控制方法和改进措施
添加 标题
加工误差的定义:加工误差是指零件加 工后实际几何参数(尺寸、形状和位置) 与理想几何参数的偏离程度。
添加 标题
加工误差的分类:根据其产生的原因和 性质,加工误差可分为随机误差、系统 误差和粗大误差三类。
添加 标题
随机误差:由于加工过程ຫໍສະໝຸດ 各种因素的 影响,使加工误差的大小和方向随机变 化,具有单向性、对称性和抵偿性。
加工误差的影响程度:对产 品质量、生产效率、成本等 方面的影响
加工误差产生的原因:机床、 刀具、夹具、测量仪器等因 素导致的误差
加工误差的分类:系统误差、 随机误差、粗大误差等
加工误差的检测方法:直接 测量法、间接测量法、比较
测量法等
提高加工精度:采用更精确的加工设备和工艺,减少误差 加强过程控制:对加工过程进行严格监控,确保每个环节的准确性 引入先进技术:采用先进的误差检测和校正技术,提高加工精度 加强员工培训:提高员工对加工误差的认识和技能水平,减少人为因素造成的误差
,a click to unlimited possibilities
01 实 验 目 的 02 实 验 原 理 03 实 验 步 骤 04 实 验 结 果 05 实 验 结 论 06 参 考 文 献
实验目的:分析加工误差的来 源和影响因素
实验意义:提高加工精度,降 低误差,提高产品质量
实验目标:确定加工误差的分 布规律和变化趋势
采集方法:直接 测量、间接测量、 组合测量
采集工具:测量 仪器、传感器、 计算机等
数据处理:对采 集到的数据进行 预处理、分析、 整理等操作
数据收集:通过实验测量获得数 据
数据处理:对数据进行预处理和 变换
加工误差的统计分析实验报告
实验报告实验名称:加工误差的统计分析一.实验目的通过检测工件尺寸,计算并画出直方图,分析误差性质, 理解影响加工误差的因素。
掌握加工误差统计分析的基本原理和方法。
二.主要实验仪器及材料游标卡尺; 工件N件。
三.实验步骤1.测量各工件上指定尺寸x,并按测量顺序记录如下2.计算尺寸分散范围R:由于随机误差和变值系统误差的存在,零件加工尺寸的实际值各不相同,这种现象称为尺寸分散。
样本尺寸的最大值Xmax与最小值Xmin之差,称为分散范围。
R= Xmax-Xmin=3.分组并计算组距△x:将样本尺寸按大小顺序排列,分成k组,则组距为:△x =R/k。
分组数k一般取为7.4. 绘制分布曲线(直方图):以工件尺寸为横坐标, 以各组中实际尺寸出现的频数作纵坐标, 即可作出等宽直方图。
再连接直方图中每一直方宽度的中点(组中值)得到一条折线,即实际分布曲线。
5. 根据分布图分析a.实际分布曲线是否接近正态分布b.实际尺寸平均值与理论尺寸平均值是否相等c.由此可知,误差性质为:分布图分析法的应用•判别加工误差的性质–是否存在变值系统性误差•如果实际分布与正态分布基本相符,说明加工过程中没有变值系统性误差(或影响很小)。
–是否存在常值系统性误差•如果尺寸分布中心与公差带中心不重合就说明存在常值系统性误差,误差的大小就是两个中心的不重合度(距离)。
下面是赠送的励志散文欣赏,不需要的朋友下载后可以编辑删除!!上面才是您需要的正文。
十年前,她怀揣着美梦来到这个陌生的城市。
十年后,她的梦想实现了一半,却依然无法融入这个城市。
作为十年后异乡的陌生人,她将何去何从?笔记本的字迹已经模糊的看不清了,我还是会去翻来覆去的看,依然沉溺在当年那些羁绊的年华。
曾经的我们是那么的无理取闹,那么的放荡不羁,那么的无法无天,那么轻易的就可以抛却所有去为了某些事情而孤注一掷。
而后来,时光荏苒,我们各自离开,然后散落天涯。
如今,年年念念,我们只能靠回忆去弥补那一程一路走来落下的再也拾不起的青春之歌。
随机误差的统计分布实验报告
随机误差的统计分布实验报告随机误差的统计分布实验报告引言:在科学研究和实验中,我们经常会遇到各种误差。
其中,随机误差是不可避免的,它是由于实验条件的不完美、测量仪器的误差以及实验者的技术水平等因素引起的。
为了更好地理解随机误差的特性和分布规律,我们进行了一系列的实验。
实验目的:本次实验的主要目的是通过对一组数据的收集和分析,探究随机误差的统计分布规律,并验证中心极限定理的适用性。
实验步骤:1. 实验器材准备:我们准备了一台精密天平,用于测量实验中所需的物品的质量。
2. 实验样本选择:我们随机选择了50个物品作为实验样本,这些物品的质量在一定范围内波动。
3. 实验数据收集:我们使用天平测量了每个样本的质量,并记录下来。
4. 数据处理与分析:在收集完实验数据后,我们进行了一系列的数据处理和分析,以探究随机误差的统计分布规律。
实验结果:通过对实验数据的分析,我们得到了以下结果:1. 随机误差的分布呈现正态分布的趋势:我们将实验数据绘制成直方图,发现其呈现出典型的钟形曲线,符合正态分布的特征。
这表明随机误差在一定程度上服从正态分布。
2. 中心极限定理的适用性:我们对实验数据进行了多次抽样,并计算了每次抽样的均值。
结果显示,随着抽样次数的增加,抽样均值的分布逐渐接近正态分布。
这验证了中心极限定理的适用性,即当样本容量足够大时,样本均值的分布趋近于正态分布。
3. 随机误差的大小与分布:通过对实验数据的统计分析,我们发现随机误差的大小与分布与所测量的物理量有关。
在某些情况下,随机误差的大小与物理量的大小成正比,而在其他情况下,则呈现出不同的关系。
这表明随机误差的大小和分布是一个复杂的问题,需要进一步研究和探索。
结论:通过本次实验,我们得出了以下结论:1. 随机误差在一定程度上服从正态分布。
2. 中心极限定理适用于随机误差的分布,当样本容量足够大时,样本均值的分布趋近于正态分布。
3. 随机误差的大小和分布与所测量的物理量有关,需要进行更深入的研究和探索。
加工误差的统计分析实验报告
加工误差的统计分析实验报告
《加工误差的统计分析实验报告》
在工业生产中,加工误差是一个常见的问题,它会直接影响产品的质量和性能。
为了解决这一问题,我们进行了一项加工误差的统计分析实验,以期找到有效
的控制和改善方法。
实验过程中,我们选择了一批相同规格的零件进行加工,并对加工过程中的误
差进行了详细记录和分析。
首先,我们对零件的尺寸进行了测量,并得到了一
系列的数据。
然后,我们使用统计学方法对这些数据进行了处理和分析,得出
了一些有价值的结论。
通过实验,我们发现加工误差的分布呈现出一定的规律性,大部分误差集中在
一个较小的范围内,但也存在一些异常值。
此外,我们还发现了一些可能导致
加工误差的原因,比如加工设备的精度、操作人员的技术水平等。
基于实验结果,我们提出了一些改善措施。
首先,我们建议对加工设备进行定
期检修和维护,以保证其加工精度。
其次,我们还提出了加强操作人员培训和
技术指导的建议,以提高其加工技术水平。
最后,我们还计划对加工工艺进行
优化,以减小加工误差的发生概率。
总的来说,通过这次实验,我们对加工误差有了更深入的了解,并提出了一些
有效的改善措施。
我们相信,通过这些措施的实施,我们能够有效地控制和减
小加工误差,提高产品的质量和性能。
希望我们的实验报告能够对其他相关领
域的研究和实践提供一定的借鉴和参考。
- 1、下载文档前请自行甄别文档内容的完整性,平台不提供额外的编辑、内容补充、找答案等附加服务。
- 2、"仅部分预览"的文档,不可在线预览部分如存在完整性等问题,可反馈申请退款(可完整预览的文档不适用该条件!)。
- 3、如文档侵犯您的权益,请联系客服反馈,我们会尽快为您处理(人工客服工作时间:9:00-18:30)。
机械制造技术基础实验指导书同济大学机械工程学院二00九年十一月实验一 加工误差统计分析一、实验目的1、学会用点图法研究被加工零件尺寸的变化规律和控制被加工零件尺寸2、在已调整好的机床上加工一批零件,鉴定该机床的工艺能力。
3、掌握绘制R x -点图的方法,能根据R x -点图分析工艺过程的稳定性,计算工序能力系数等。
二、实验使用的设备和工具1、机床:斯来福临精密数控平面磨床K-P36 Compact2、量具:螺旋测微仪、千分仪三、实验内容在数控磨床上加工一批零件,依次测量出其高度尺寸,然后绘制被加工零件尺寸的R x -图,分析被加工零件尺寸的变化规律,从中找出误差的性质和原因,并计算机床的工艺能力系数、确定机床的工艺能力等级。
四、实验原理和方法在磨床上用磨削45HRC59~62工件一批,做出R x -控制图。
应用数理统计方法对加工误差(或其他质量指标)进行分析,是进行过程控制的一种有效方法,也是实施全面质量管理的一个重要方面。
其基本原理是利用加工误差的统计特性,对测量数据进行处理,作出R x -点图,据此对加工误差的性质、工序能力及工艺稳定性等进行识别和判断,进而对加工误差作出综合分析。
详见教材相关章节。
1、 R x -图绘制:1)确定样组容量,对样本进行分组样组容量一般取m=2~10件,通常取4或5。
按样组容量和加工时间顺序,将样本划分成若干个样组。
2)计算各样组的平均值和极差对于第i 个样组,其平均值和极差计算公式为:11ni i j m j x x ==∑,a x i ni i i 式中 i x ——第i 个样组的平均值;i R ——第i 个样组的极差;x ij ——第i 个样组第j 个零件的测量值; x imax ——第i 个样组数据的最大值; x imin ——第i 个样组数据的最小值 3)计算R x -图控制限R x -图的控制限为:11U 2L 2x = x =mm k ik i x x x A R x A R=⎧=⎪⎪⎪+⎨⎪-⎪⎪⎩∑中线上控制线上控制线11U 1L 2R = R =m m k ik i R R D R D R=⎧=⎪⎪⎪⎨⎪⎪⎪⎩∑中线上控制线上控制线 式中A 2、D 1、D 2——常数,可由表1.2查得; K m --样组个数。
表3.2 d 、n a 、A2、D1、D2值N (件) d n aA 2 D 1 D 2 4 0.880 0.486 0.73 2.28 0 5 0.864 0.430 0.58 2.11 0 6 0.8480.3950.482.004) 绘制R x -图以样组序号为横坐标,分别以各样组的平均值x 和极差R 为纵坐标,画出R x - 图,并在图上标出中心线和上、下控制限。
2、直方图和分布曲线绘制 1)初选分组数K一般应根据样本容量来选择,参见表3.1.表1.1 分组数K 的选定n 25~40 40~60 60~100 100 100~160 160~250 k6 781011122)确定组距找出样本数据的最大值Ximax 和最小值Ximin ,并按下式计算组距:m a x m i n'11x x R d k k -==--选取与计算的d'值相近的且为测量值尾数整倍数的数值为组距 。
3)确定分组数1R k d =+4)确定组界各组组界为:m i n(1)2dx i d +-± (j=1,2,……,k ) 5)统计各组频数n i (即落在各组组界范围内的样件个数) 6)画直方图以样本数据值为横坐标,标出各组组界;以各组频数 为纵坐标,画出直方图。
7)计算总体平均值与标准差平均值得计算公式为:11ni ni x x ==∑式中 x i -第i 个样件的测量值; n-样本容量。
标准差的计算公式为:nx xni i∑=-=12)(σ8)画分布曲线若研究的质量指标是尺寸误差,且工艺过程稳定,则误差分布曲线接近正态分布曲线;若研究的质量指标是形位误差或其他,则应根据实际情况确定其分布曲线。
画出分布曲线,注意使分布曲线与直方图协调一致。
9)画公差带在横轴下方画出公差带,以便与分布曲线相比较。
3、工序能力系数计算标准差的计算公式为:nx xni i∑=-=12)(σ式中 x i -第i 个样件的测量值; n -样本容量。
工序能力系数C p 按下式计算:6p T C σ=4、判别工艺过程稳定性可按表3.3所列标准进行判别。
注意,同时满足表中左列3个条件,工艺过程稳定;表中右列条件之一不满足,即表示工艺过程不稳定。
表3.3 正常波动与异常波动标志正 常 波 动异 常 波 动1、没有点子超出控制线2、大部分点子在平均线上下波动,小部分在控制线附近3、点子没有明显的规律性1、有点子超出控制线2、点子密集在平均线上下附近3、点子密集在控制线附近4、连续7点以上出现在平均线一侧5、连续11点中有10点以上出现在平均线一侧6、连续14点中有12点以上出现在平均线一侧7、连续17点中有14点以上出现在平均线一侧8、连续20点中有16点以上出现在平均线一侧9、点子有上升或下降的倾向10、点了有周期性的波动四、实验步骤1、在已调整好的平面磨床K-P36加工50 个高度11.307 ±0.06的方形工件。
2、在加工过程中用千分尺依次测量各个零件的,以5个零件为一组记录于报告内的原始数据记录表(见附表)上。
3、计算出每组零件尺寸平均值x和极差R,再依次记录在实验报告内的原始数据记录表上。
4、计算x和R的平均值x和R。
5、计算Rx-图控制线。
6、绘制Rx-控制图。
7、分析Rx-图的点子是否为正常波动,以判断工艺是否稳定8、绘制分布图。
9、计算全部零件尺寸的均方根偏差σ,计算工艺能力系数,确定工序能力等级。
五、分析判断实验结果1、通过对实际分布图及Rx-控制图分析、判断影响该批零件加工精度的主要误差因素。
2、推断该工序的工艺能力,确定工艺等级。
3、判断工艺是否稳定。
4、试提出解决上述工艺问题的措施。
六、思考题1、分布图主要说明什么问题?在什么情况下分布曲线接近于正态曲线?在什么情况下分布曲线与正态曲线偏离较远?2、R x -图主要说明什么问题?分布图与R x -图关系如何?3、分析产生加工误差的主要因素有哪些?其中哪些是常值系统误差?哪些是变值系统误差?哪些是随机误差?如何从分布图及R x -图中加以判断?4、分析工艺过程稳定性(或不稳定性)的原因?附表:测量值记录表样本组编号 尺寸(mm)小样本 均值x小样本 极差R1 2 3 4 5 1 11.294 11.293 11.299 11.293 11.288 11.293 0.011 2 11.286 11.289 11.290 11.285 11.281 11.286 0.009 3 11.307 11.293 11.298 11.292 11.287 11.295 0.02 4 11.295 11.287 11.293 11.267 11.261 11.281 0.034 5 11.289 11.288 11.290 11.281 11.279 11.285 0.011 6 11.290 11.291 11.289 11.289 11.285 11.289 0.006 7 11.284 11.288 11.290 11.286 11.282 11.286 0.008 8 11.290 11.287 11.286 11.282 11.281 11.285 0.009 9 11.293 11.292 11.294 11.286 11.286 11.290 0.008 1011.29111.28811.29011.286 11.28511.2880.006x11.288 R0.0122x-图控制线计算Rx-图的控制线为:R4) 绘制Rx-图为了作图精确起见,借助matlab工具作图,将作图程序附于最后。
据点子正常波动和异常波动判断方法,可以发现x图中没有1个数据点超出控制线,而且所有点在平均线上下无规律波动,R图中也没有1个点超出控制线,大多分布在中线与下控制线之间,说明了工艺是稳定的。
绘制分布图1)初选分组数K样本容量为50,故根据表3.1初步选取分组数为72)确定组距组距为:3)确定分组数组数12345678频数110102710014)确定组界各组组界为:m i n(1)2dx i d +-± (j=1,2,……,k ) 则各组组界如下表5)统计各组频数n i (即落在各组组界范围内的样件个数)6)画直方图,分布曲线,及公差带以样本数据值为横坐标,标出各组组界;以各组频数为纵坐标,画出直方图,并描出分布曲线,在横坐标下方加上公差带便于与分布曲线进行比较。
组数12345678组界上限11.264511.271511.278511.285511.292511.299511.306511.3135组界下限11.257511.264511.271511.278511.285511.292511.299511.30657)计算总体平均值与标准差 平均值得计算公式为:501150i i x x ==∑ 式中 x i -第i 个样件的测量值;标准差的计算公式为:231() 6.9910n i i x x n σ-=-==⨯∑3、工序能力系数计算 工序能力系数按下式计算 :实验结果分析判断:1. 影响该批零件加工精度的主要误差因素是磨床的系统误差。
此外还有加工零件前,没有将磨床冲洗干净,导致磨床表面有残余的磨削,加工零件放于其上,导致了加工误差。
2. 该工序的工艺等级为特级,工艺能力过高,不一定经济。
3. 该工艺稳定。
4. 在加工零件之前,用冲洗液将磨床表面冲洗干净,保证不再残留磨削后在进行加工。
思考题:1. 分布图重要说明了零件加工误差的主要误差的性质,是来源于系统性误差还是随机性误差,若引起系统性误差的因素不变,引起随机误差的多种因素的作用都微小且在数量级上大致相等时,加工所得的尺寸将按正态分布曲线分布,当随机性误差中混入了系统性误差时或加工工艺未达到热平衡前,分布图与正态曲线偏离较远。
x-图主要用于判定工艺稳定性以及用于工序质量控制,它的波动说2.Rx-图明了工件平均值的变化趋势和随机误差的分散程度。
分布图与Rx-图能够反映随机受系统性误差影响相同,只影响曲线位置,但是R误差的分散程度,而且计算方便,能及时提供主动控制的资料。
3.产生加工误差的主要因素有原理误差,机床误差,调整误差,热变形引起的误差,内应力变形引起的误差,工艺系统受力变形引起的误差。
原理误差,机床,刀具,夹具,量具的制造误差,调整误差,工艺系统的静力变形,机床,夹具和量具的磨损值在一定时间内是常值系统误差。