某工厂物料损耗定额标准(doc 3页)
物料损耗控制规范(含表格)
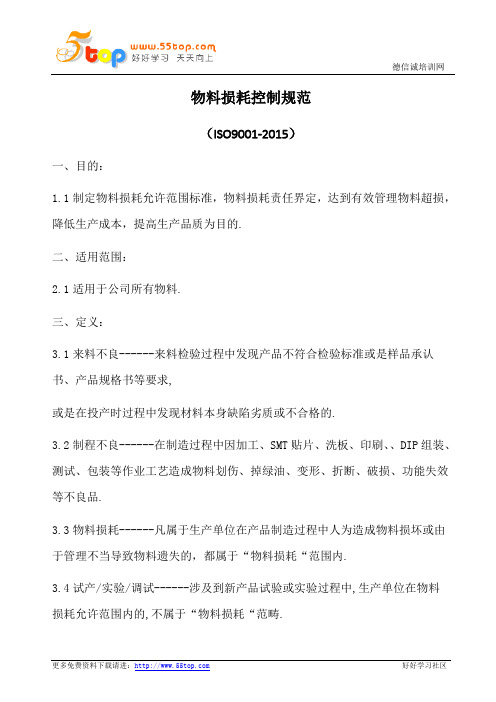
物料损耗控制规范(ISO9001-2015)一、目的:1.1制定物料损耗允许范围标准,物料损耗责任界定,达到有效管理物料超损,降低生产成本,提高生产品质为目的.二、适用范围:2.1适用于公司所有物料.三、定义:3.1来料不良------来料检验过程中发现产品不符合检验标准或是样品承认书、产品规格书等要求,或是在投产时过程中发现材料本身缺陷劣质或不合格的.3.2制程不良------在制造过程中因加工、SMT贴片、洗板、印刷、、DIP组装、测试、包装等作业工艺造成物料划伤、掉绿油、变形、折断、破损、功能失效等不良品.3.3物料损耗------凡属于生产单位在产品制造过程中人为造成物料损坏或由于管理不当导致物料遗失的,都属于“物料损耗“范围内.3.4试产/实验/调试------涉及到新产品试验或实验过程中,生产单位在物料损耗允许范围内的,不属于“物料损耗“范畴.四、职责:4.1生产部:负责在线不良品(含来料、制造)的反馈、及时检查统计并作退库处理.4.2品质部:负责对不良品性质判定及辨别材料所属供应商的评定,提供不良品检验报告.4.3采购部:负责对来料不良品处理意见的评审以及提供物料成本单价. 4.4物料仓:负责不良物料的管理并监督、统计并跟进落实相关部门不良品的处理结果.4.5PMC 计划部:负责编制物料超损标准以及相关超损物料采购申请. 4.6财务部:负责最终决议的执行4.7总监(总经理):负责争议物料、处理方案的最终裁决权. 五、不合格物料的界定:5.1生产来合格物料界定. 5.1.1来料不良退供应商.5.1.1.1兴开泰IQC 检验发现来料是因为供应商本身缺陷或是在运输原因造成外观不良、功能不良且不能达到AQL 接收标准,不良责任属于供方,原则上直接做退货处理.0.250.4抽样数AC RE 抽样数 AC RE 1-8 全数1全数1AQL 标准来料数量(PCS )9-15 全数0 1 全数0 116-25 全数0 1 全数0 126-50 32 0 1 20 0 151-90 50 0 1 20 0 191-150 500 1 32 0 1151-280 500 1 320 1281-500 500 1 320 1501-1200 500 1 32 1 21201-3200 200 1 2 125 1 23201-10000 200 1 2 125 2 310001-36000 315 2 3 200 3 436001-150000 500 3 4 315 5 6150001-500000 800 5 6 500 7 8 ≥500000 1250 7 8 1250 10 115.1.1.2部门电子物料(例如:MOS、IC)IQC按照常规检验合格入库,但部份功能只有在生产或者老化实验时才能发现,如经过分析确认不是由于我司员工、设备、操作方法、环境造成,由此造成的不良由供方赔偿相关损失,包括连带报废物料的损失的浪费工时等.5.1.1.3IQC按国标准GB、T2828抽样方案进行检测,发现不良但又在允收范围内的物料在使用过程中发现的不良不在“物料损耗”范围规定内.5.1.1.4已被IQC判定为不合格但由于生产急需使用而作为特别采用(MRB)处理的物料,在制程过程中出现的不良属“来料不良”范围,必须走(特采流程单),前提是非致命问题,致命问题直接退货处理(退货2个工作日内完成),由最高裁决权裁决,过程中所有的损失需要重新评审,具体操作参考文件(不合格品质控制程序).5.1.1.5来料不良处理流程:流程图完成时间责任单位责任人备注5MIN10MIN 30MIN2H2H4H2个工作日扣款生产部工程部品质部品质部生产部/品质部/仓库品质部/仓库品质部/仓库财务部主管PE工程师现场品检SQE工程师物料员/来料检验/仓库管理员SQE工程师/供方SQE工程师/仓库主管主管发现不良上报结果追踪结果追踪制程不良物料生产不良物料制程工程师确认制程异常处理单IPQC检验核准退料单SQE判定来料不良分析报告不良品入不良仓通知供应商复判仓库打单退供应商A财务最终决议的执行结案B5MIN2H30MIN 1个工作日内 4H 4H 4H品质部品质部 PMC 计划采购部 生产/工程部 财务部 品质部/仓库品检员SQE 工程师 主管 主管 主管/工程师 主管 SQE 工程师/仓库发现不良上报 组织会仪注:其它项目不做时间规定,按正常生产流程走. 5.1.1.5.1所有负责人在拟定的时间要求内没有完成的,且后续没有任何进展,来料不合格物料IQC 检验不合格不合格异常处理 PMC 评审(出货要求急与不急)特采挑选使用 特采上线IQC 标识隔离入库NG (不急或致命缺陷)销售与客户协商SQE 判定来料不良分析报告急单/非致命缺陷PMC 打单物料员领料生产重点检查缺陷包装出货采购来料报价工时,人力评估财务统计成本SQE 通知供应商复判AB则罚款物料总额的2%.事例:物料总额10000RMB,即罚款10000*2%=200RMB.5.1.1.5.2所有负责人在拟定的时间要求内没有完成,且超出时间完成的,即要求说明原因并给予警告,累计三次后,第四次则开始罚款,罚款物料总额的2%.事例:物料总额10000RMB,即罚款10000*2%=200RMB. 5.2制程不良.5.2.1对于PCB 、FPC 、线材、光电开关、包装材料等物料的外观在生产部第一个投入这些物料的工序确认出来的不良归属于来料不良,对于在后面工序发现的不良归属于生产制程不良.5.2.2对于热电偶,温控开关在做功能测试检验工艺确认出物料不良归属于来料不良,对于首件之后或是在后面工序发现的不良归属生产制造不良. 5.2.3在生产过程中因机器、设备抛料、功能不良、返修等不确认因素,造成物料损耗比率在允许的范围内的,不在“物料损耗”范围规定内.1-500PCS 订单 501-1000PCS订单 1001-10000PCS 订单 10001-20000PCS 订单 ≥20001PCS订单 损耗率 损耗率 损耗率 损耗率 损耗率 IC 0.6% 0.3% 0.2% 0.1% 0.05% MOS 0.6% 0.3% 0.2% 0.1% 0.05% 电阻0603 1.0% 0.9% 0.5% 0.3% 0.3% 电阻0402 1.0% 0.9% 0.5% 0.4% 0.4% 电阻0201 1.5% 1.0% 0.8% 0.5% 0.5% 电容0603 1.0% 0.9% 0.5% 0.3% 0.3% 电容0402 1.0% 0.9% 0.5% 0.4% 0.4% 电容0201 1.5% 1.0% 0.8% 0.5% 0.5% 镍片1.3% 1.1%0.9% 0.7% 0.5%订单损耗率 物料名称五金 1.3% 1.1%0.9%0.7%0.5% PTC、NTC 1.1%0.9%0.7%0.5%0.3%极管 1.1%0.6%0.4%0.2%0.3% LED 1.5% 1.4% 1.3% 1.2% 1.0%端子0.8%0.7%0.6%0.5%0.5% PCB0.3%0.2%0.1%0.1%0.05% FPC0.5%0.4%0.3%0.3%0.1%包装材料 1.3% 1.1%0.9%0.7%0.5%其它以整联板领料以实际情况定以实际情况定以实际情况定以实际情况定5.3物料损耗(其它).5.3.1对于在制程中发现的物料不良能确认是供方造成的,其处理方案依次为采购与供应商沟通换货.5.3.2生产部将生产过程中发现的不良物料,生产部对其进行隔离并按原料、作业区分统计不良现象及数量,并填写(不合格品处置表)交由品管部进行检验.5.3.3品管检验员对于生产退料的不良数量、现象以及不合格产生的原因进行再确认,确认无误后交品管部负责人签章审合格后返还至生产部,防止物料缺失.注明:如果生产部对品质部判定标准产生异议时,可寻求部门领导处理.5.4试产/实验/调试.5.4.1针对正常试产、实验的产品(机器设备调试,产品验证,老化实验)等产生的不良品在列表之内的,不属于“物料损耗”范围规定内.1-500PCS 订单501-1000PCS订单1001-10000PCS订单10001-20000PCS订单≥20001PCS订单物料名称订单损耗率损耗率损耗率损耗率损耗率损耗率IC5% 3% 0.3%0.1%0.05% MOS5% 3% 0.3%0.1%0.05%电阻06035% 4% 1.0%0.3%0.3%电阻04025% 4% 1.0%0.4%0.4%电阻02018% 6% 1.2%0.5%0.5%电容06035% 4% 1.0%0.3%0.3%电容04025% 4% 1.0%0.4%0.4%电容02018% 6% 1.2%0.5%0.5%镍片5% 4% 1.0%0.7%0.5%五金5% 4% 1.0%0.7%0.5% PTC、NTC5% 4% 0.8%0.5%0.3%极管5% 4% 0.5%0.2%0.3% LED5% 4% 1.3% 1.2% 1.0%端子5% 4% 0.8%0.5%0.5% PCB1% 0.8% 0.2%0.1%0.05% FPC1% 0.8% 0.3%0.3%0.1%包装材料5% 4% 1.0%0.7%0.5%其它以实际情况定以实际情况定以实际情况定以实际情况定以实际情况定5.5不合格品数据统计.5.5.1物料员填写≤生产超领单≥及≤生产超领处罚明细表≥,≤生产超领处罚明细表≥提交品质部主管核准,品质部评判损耗类型,根据损耗类型到责任单位,责任单位主管按管理规范责追究落实到第一责任人,责任单位经理按管理规范责追究落实到第二责任人,对应责任人及主管/经理签名确认.5.5.2财务部根据≤生产超领处罚明细表≥核算对应损耗金额,损耗金额按照管理规范在绩效考核中体现.六、物料超损统计及费用产生:6.1PMC计划部根据仓管员所发的日报统计生产部每同所有超损物料明细(含物料名称、件数等信息),并在每月23-25日将其统计汇总后,经生产部、采购部、品质部等部门会签经总监、副总监核准后交由财务部,要求会签在1-2个工作日内完成.6.2财务部成本会计根据当月物料超损数量计算超损所产生的费用(直接采购成本)总额,组到生产部门主管、经理确认.6.3生产部主管、经理以物料超补费总额为赔偿标准,责任落实到每一个单位组别和每一名管理与员工承担,具体责任赔偿详见本办法第七节.七、物料超损费用承担与计算方式:7.1费用产生负第一责任:物料使用、损耗直接责任人、助拉、拉长、主管、经理.7.1.1作业制程中人为造成物料损坏或由于管理不当导至物料遗失责任人,赔偿其该工位超损物料的20%,其费用于绩效考核中计扣.7.1.2此生产拉线线长、组长承担超损费用总额的10%.7.1.3此部门主管、经理承担超损费用总额的5%.7.2费用产生负第二责任:以部门拉组为单位.7.2.1物料领用单位,以该部门拉组全体员工(当事人、拉长、助拉、主管除外)为责任对象,赔偿其该部门当月产生超损物料费用总额的65%,统一平均分摊于个人,其费用于绩效考核中计扣:案例说明:7.2.1.1某拉4月份在制造过程中超补物料已经超过允许范围,并产生实际总额查账用100RMB元整.7.2.1.1.1作业制程中人为造成物料损坏或由于管理不当导致物料遗失直接责任人,赔偿其该工位超损物料的20%,计算:100*20%=20RMB元整.7.2.1.1.2该线长、组长承担超损费用总额的10%,计算:线长,100*5%=5RMB 元整组长,100*5%=5RMB元整.7.2.1.1.3该部门主管、经理承担超损费用总额的5%,计算:主管,100*2.5%=2.5RMB元整经理,100*2.5%=2.5RMB元整.7.2.1.1.4该生产线共有10人,责任赔偿比率是65%,计算:100*65%=65RMB 元整,计算到个人则65/10=6.5RMB每人.八、相关支持文件:8.1质量记录控制程序8.2进货检验控制程序8.3不合格品控制程序九、相关表单:生产超领处罚明细表生产超领处罚明细表.xls德信诚培训网电子物料损耗定额标准物料类别损耗率物料类别损耗率电阻0.2% 三极管0.2%电容0.1% 晶振0.02%电位器0.1% 保险丝0.1%数码管0.1% 开关电源0%变压器0.01% 线材0.1% IC 0% 胶A.B 三防漆0.5%LED 0.1% 螺丝、螺母.垫片3% 丝印喷油0.1% 辅料0% 小的结构件.胶件0.1%*说明:①发料时电子部不发备品。
物料消耗定额

物料消耗定额
一、定义:物料消耗定额是指:针对一定条件所规定的生产单位产品或完成单位工作量,合理消耗的物资的标准数量。
(一)物资是物质资料的简称,包括几种不同的含义:
1、包括生产资料在内的全部物质资料;
2、社会总产品;
3、直接参加生产过程的劳动工具和原材料、燃料等生产资料。
我国物资管理工作中讲的“物资”,一般是指除土地、森林、厂房、库房、道路等之外的生产资料。
主要包括:劳动工具、原料、材料、燃料等。
(二)现对定义中三个内容进行解释说明:
1、一定条件:指生产技术水平、经济管理状况等影响物资消耗定额水平的各种因素;
2、单位产品:以实物单位表示的一个产品;
单位工作量:主要是以劳动量指标表示的某项工作量,应是符合国家标准、部颁标准、主管机关规定或合同规定的技术条件的合格产品或工作量。
3、合理消耗物资定额的标准数量:应理解为在最低工艺损耗的情况下,生产单位产品或完成工作量,所需要的足够的物资量。
理论上讲,就是指在充分研究物资消耗规律的基础上,得出的正确反应物资消耗规律的数量。
二、基本结构:He=G0+∑gi
He:生产某产品或完成某工作量的物资消耗定额
G0: 生产某产品或完成某工作量所用物资的有效消耗量
∑gi:生产某产品或完成某工作量所有非有效消耗量之和,包括:(1)工艺损耗:物资在制成产品的加工过程中,由于形状或性能改变而必须产生的加工损耗,受生产技术水平、工人操作水平的影响。
(2)残料:由于材料的规格、尺寸与产品毛坯的尺寸不相适应而产生的边角料,这部分应是在合理下料后,在本企业不能再利用的残料。
三、影响物资消耗的因素:1、人的因素 2、经济条件3、生产技术4、物资质量状况5、自然条件。
车间A物料损耗扣款标准

不以损害公司利益为最低标准。
不以扣款作为公司品质观念的改变、工艺改善作为最终手段。
不以危害公司人性化管理制度作为最终目的。
2、定义:物料种类的10%左右,金额占总金额65%左右的物料即为A 类物料,根据公司的实际情况,其主要包括以下几大类:通讯电子类:IC 、摄像头、显示屏、晶体、内存卡、模块组件、主板、半成品、产成品等其他A 类物料。
DVD 、DVB 类:机芯、IC 、接收头、调谐器、显示屏、硬盘、充电电池、电源适配器、升压组件、半成品、成品等其他A 类物料。
MP3、MP4、GPS 类:IC 、显示屏、晶体、内存卡、显示模块、组件、充电电池、半成品、成品等其他A 类物料。
客户所定其他A 类物料。
3、适用范围:计划部、品质部、财务部、制造中心所有部门、人事部。
4、A 类物料报损流程:5、扣款标准:车间A 类物料若出现损耗,则以“相对损耗率”作为考核办法。
相对损耗率的计算如下: 相对损耗率=当月损耗率—允许损耗率当月损耗率=当月损耗金额*1000/当期领料金额 (注:当月损耗率不能正负相抵) 允许损耗率数据如下表(千分之几):制一部: 0.5 制二部: 1 制三部: 1超过允许损耗率的处罚方法如下:0<相对损耗率≤1: 当月损耗金额=制造60%+公司40%、1<相对损耗率≤4:当月损耗金额=制造65%+公司35%4<相对损耗率≤7: 当月损耗金额=制造70%+公司30%7<相对损耗率≤10:当月损耗金额=制造75%+公司25%10<相对损耗率≤13:当月损耗金额=制造80%+公司20%13<相对损耗率当月损耗金额=制造85%+公司15% 6、注意事项:此扣款标准中的扣款事项以单个A类物料为计量单位。
此扣款标准不与相关部门的规章制度相冲突。
此扣款标准的相关表单可由相关部门自主设定。
生产原材料损耗定额标准及奖罚办法
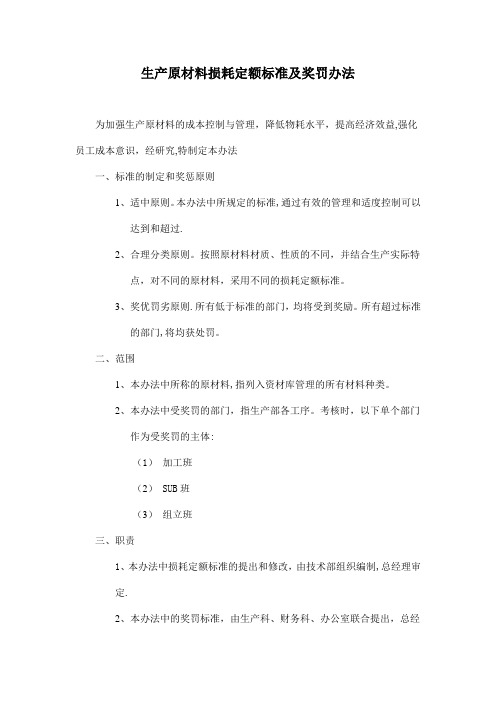
生产原材料损耗定额标准及奖罚办法为加强生产原材料的成本控制与管理,降低物耗水平,提高经济效益,强化员工成本意识,经研究,特制定本办法一、标准的制定和奖惩原则1、适中原则。
本办法中所规定的标准,通过有效的管理和适度控制可以达到和超过.2、合理分类原则。
按照原材料材质、性质的不同,并结合生产实际特点,对不同的原材料,采用不同的损耗定额标准。
3、奖优罚劣原则.所有低于标准的部门,均将受到奖励。
所有超过标准的部门,将均获处罚。
二、范围1、本办法中所称的原材料,指列入资材库管理的所有材料种类。
2、本办法中受奖罚的部门,指生产部各工序。
考核时,以下单个部门作为受奖罚的主体:(1)加工班(2) SUB班(3)组立班三、职责1、本办法中损耗定额标准的提出和修改,由技术部组织编制,总经理审定.2、本办法中的奖罚标准,由生产科、财务科、办公室联合提出,总经理审定。
3、本办法中涉及到的奖罚,由办公室按照实际统计数据,参照标准予以实施.4、考核执行中的相关数据,由以下部门提供:(1)材料单价由财务科提供.(2)月生产标准消耗及实际材料消耗(包括生产实际物料消耗和打端试料消耗),由资材科提供.四、损耗定额标准,如下五、考核及奖罚流程月末考核时,对本部门所耗用物料高于损耗标准的,实际高出的材料按价值由班组承担。
损耗低于标准的,少于标准损耗的材料价值50%作为奖励拨给生产科,生产科将30%发给班组20%留作生产科流动资金。
1、每月末,资材科将生产盈亏数量报办公室,财务科将材料单价报给办公室,办公室计算实际盈亏金额。
加工班盈亏金额=(当月资材结存车间余量—当月车间盘点数量)*材料单价。
SU B、组立班盈亏金额=(资材当月发料总数*损耗标准-当月车间操作不良邀请数量)*材料单价超过或低于标准用量部分的资材,办公室安进口完税价格计算汇总并作为对各生产部门进行罚款和奖励的数据。
2、每月5号前,办公室对各生产部门资材耗用情况整理,对高于或节约的资材价值。
工厂物料损耗定额标准

审核栏(打×为是):
□总经办签名/日期___________ 系统部签名/日期__________
□业务中心签名/日期___________ 资讯部签名/日期__________
技术中心签名/日期___________ 木箱部签名/日期___________
□品质中心签名/日期___________ 喇叭部签名/日期__________
资材中心签名/日期___________ 工程部签名/日期__________
财务中心签名/日期___________ 仓储部签名/日期__________
制造中心签名/日期___________ 策略采购签名/日期__________
编制:审核:批准:
分发部门(打×为是):
()总经办()生产部()工程部
()业务中心()注塑部()人力部
()技术中心()丝印部()机电部
()资材中心()品管部()成品仓
()财务中心()品保部()材料仓
其它部门(请填写在此处):。
物料消耗定额

物料消耗定额
一、定义:物料消耗定额是指:针对一定条件所规定的生产单位产品或完成单位工作量,合理消耗的物资的标准数量。
(一)物资是物质资料的简称,包括几种不同的含义:
1、包括生产资料在内的全部物质资料;
2、社会总产品;
3、直接参加生产过程的劳动工具和原材料、燃料等生产资料。
我国物资管理工作中讲的“物资”,一般是指除土地、森林、厂房、库房、道路等之外的生产资料。
主要包括:劳动工具、原料、材料、燃料等。
(二)现对定义中三个内容进行解释说明:
1、一定条件:指生产技术水平、经济管理状况等影响物资消耗定额水平的各种因素;
2、单位产品:以实物单位表示的一个产品;
单位工作量:主要是以劳动量指标表示的某项工作量,应是符合国家标准、部颁标准、主管机关规定或合同规定的技术条件的合格产品或工作量。
3、合理消耗物资定额的标准数量:应理解为在最低工艺损耗的情况下,生产单位产品或完成工作量,所需要的足够的物资量。
理论上讲,就是指在充分研究物资消耗规律的基础上,得出的正确反应物资消耗规律的数量。
二、基本结构:He=G0+∑gi
He:生产某产品或完成某工作量的物资消耗定额
G0: 生产某产品或完成某工作量所用物资的有效消耗量
∑gi:生产某产品或完成某工作量所有非有效消耗量之和,包括:(1)工艺损耗:物资在制成产品的加工过程中,由于形状或性能改变而必须产生的加工损耗,受生产技术水平、工人操作水平的影响。
(2)残料:由于材料的规格、尺寸与产品毛坯的尺寸不相适应而产生的边角料,这部分应是在合理下料后,在本企业不能再利用的残料。
三、影响物资消耗的因素:1、人的因素 2、经济条件3、生产技术4、物资质量状况5、自然条件。
材料消耗定额的组成与制定方法

(4)理论计算法
❖ 根据施工图纸和其他技术资料,用理论公式计算出 产品的材料净用量,从而制定出材料的消耗定额。
分数量应从摊销量中扣除。
以木模板为例:
❖ (1)现浇砼构件木模板摊销量计算公式如下: ❖ ①一次使用量
一次使用量 = 每m3砼构件的模板接触面积 ×每m2接触面积需模量×(1+制作损耗率)
❖ 含模量=混凝土接触面积/混凝土构件工程量 ❖ 例:现浇钢筋混凝土圈梁设计断面为240×180mm,求其含模
115
例1:
❖ 计算标准砖一砖外墙每m3砌体砖和砂浆的总消耗 量(砖和砂浆损耗率均为1%)
❖ 解:每m3一砖墙中砖净用量 1×2×1
0.24×(0.24+0.01)×(0.053+0.01) = 529.1块 ❖ 砖总消耗量=529.1×(1+1%)=534.29块 ❖ 每m3一砖墙中砂浆净用量 =1 - 529.1×0.24×0.115×0.053 =0.226 m3 ❖ 砂浆总消耗量=0.226×(1+1%)=0.228 m3
材料消耗定额
一、材料消耗定额概述 二、材料消耗定额的组成 三、材料消耗定额的制定方法
一、材料消耗定额概述
❖ 概念:指在正常施工条件下,生产单位合格 产品所必须消耗的建筑材料的数量标准。
❖ 材料分类: ❖ 实体消耗材料 ❖ 措施消耗材料
二、材料消耗定额的组成
原材料净用量
材料消耗净用量 (材料消耗净定额)
。2 020年1 0月25 日星期 日上午5 时59分 59秒05: 59:592 0.10.25
物料消耗定额

物料消耗定额展开全文一、物料消耗定额的内容物料消耗定额是指在一定的生产技术条件下,生产单位产品或完成单位工作量所合理消耗的数量标准。
物料消耗定额是编制物料供应计划和计算物料需要量的依据,是科学组织物料供应的重要基础,物料消耗的构成主要有:1、构成产品的净重的消耗它是指产品自身的重量,是物料消耗最主要部分。
这部分消耗是由产品设计决定的,充分反映了产品设计的水平。
2、工艺性消耗它是指在生产准备和加工过程中,由于改变材料物理或化学性能所产生的物料消耗。
这一部分是工艺技术水平所决定的。
3、非工艺性消耗它是指由于生产过程中不可避免产生废品,运输、保管过程中的合理损耗和其他非工艺技术的原因而引起的损耗。
由于物料消耗构成不同,工业企业物料消耗定额,一般分为工艺消耗定额和物料供应定额两种。
(1)工艺消耗定额,是指在一定条件下,由生产单位产品或完成单位工作量,所用物料的有效消耗量(即产品消耗和合理的工艺消耗两部分构成)。
其是发料和考核物料消耗情况的主要依据。
(2)物料供应计划是由工艺消耗定额和合理的非工艺性损耗确定。
物料供应定额是核算物料需要量,确定物料订货量和采购量的主要依据。
单位产品工艺消耗定额 = 单位产品净重 +各种工艺消耗物料供应定额 =工艺消耗定额 1+材料供应系数材料供应系数 =单位产品非工艺消耗/工艺消耗定额二、制定物料消耗定额的基本方法1、经验估计法经验估计法是根据定额制定人员的经验和掌握的资料来估计制定的。
采用这种方法简便易行,工作量最少,但主观因素较多,科学性和准确性较差一些。
为了提高经验估计法的质量,充分考虑广大员工经过努力可以达到这一因素,一般采用平均概率的方法。
其计算公式:M =(a+4c+b )/6式中:M——加权平均概率求出的物料消耗定额;a——先进的消耗数量,即最少的消耗数量;b——落后的消耗数量,即最多的消耗数量;c——一般的消耗数量。
经验估计法一般适用于单件小批或者在技术资料和统计资料不全的情况下采用。
- 1、下载文档前请自行甄别文档内容的完整性,平台不提供额外的编辑、内容补充、找答案等附加服务。
- 2、"仅部分预览"的文档,不可在线预览部分如存在完整性等问题,可反馈申请退款(可完整预览的文档不适用该条件!)。
- 3、如文档侵犯您的权益,请联系客服反馈,我们会尽快为您处理(人工客服工作时间:9:00-18:30)。
某工厂物料损耗定额标准(doc 3页)
修订履历记录
版本文件编号制/修内容生效日期制/修部门拟订A.0 QMI-097 新制订发行2008-8-13 研发部蒋江明
审核栏(打×为是):
□总经办签名/日期___________ 系统部签名/日期__________
□业务中心签名/日期___________ 资讯部签名/日期__________
技术中心签名/日期___________ 木箱部签名/日期___________
□品质中心签名/日期___________ 喇叭部签名/日期__________
资材中心签名/日期___________ 工程部签名/日期__________
财务中心签名/日期___________ 仓储部签名/日期__________
制造中心签名/日期___________ 策略采购签名/日期__________ 编制:审核:批准:
分发部门(打×为是):
()总经办()生产部()工程部
()业务中心()注塑部()人力部
()技术中心()丝印部()机电部
()资材中心()品管部()成品仓
()财务中心()品保部()材料仓
其它部门(请填写在此处):
1.目的:
建立工厂内物料消耗标准,以作为领/发料依据。
2.适用范围:
工厂内各生产职能部门。
3.名词定议:
无
4.权责:
研发依此标准做BOM表的物料损耗。
5.流程:
略
6.内容:
6.1、PCB板:损耗率0.1%;
6.2、电阻类:损耗率0.4%;
6.3、电容类:损耗率0.2%;
6.4、电位器类:损耗率0.2%;
6.5、数码管类:损耗率0.1%;
6.6、变压器类:损耗率0.1%;
6.7、IC类:损耗率0.1%;
6.8、喇叭:损耗率0.2%;
6.9、二极管类:损耗率0.2%;
6.10、LED类:损耗率0.4%;
6.11、三极管类:损耗率0.2%;
6.12、晶振类:损耗率0.2%;
6.13、保险丝类:损耗率0.1%;
6.14、插座/开关类:损耗率0.3%;
6.15、显示屏类:损耗率0.1%;
6.16、散热器类:损耗率0.2%;
6.17、线材类:损耗率0.1%;
6.18、木箱:损耗率0%;
6.19、包材类:损耗率0.5%;
6.20、EVA类:损耗率0.5%;
6.21、螺丝/螺母:损耗率4%;
6.22、五金铭牌/滴胶铭牌:损耗率0.5%;
6.23、五金件/接线柱/定位扣:损耗率0.5%;
6.24、矽胶片/绝缘豆/LED间隔柱/闭端端子/线扣/束线带:损耗率0.5%;
6.25、网罩组合:损耗率0.2%;
6.26、网布:损耗率2%;
6.27、喇叭硬件:损耗率0.1%;
6.28、喇叭软件:损耗率1%;
6.29、防尘帽:损耗率1%;
6.30、塑胶件:
6.30-1、喷油丝印:功能板/按键/旋钮/网架/回音筒,损耗率0.1%;
6.30-2、喷油丝印:面壳/后壳,损耗率1%;
6.30-3、电子组装:所有塑胶件,损耗率0.1%;
6.30-4、委外加工:塑胶件,损耗率3.5%-4%;
6.31、塑胶原料:损耗率2%;
6.32、所有辅料:损耗率0%;
6.33、说明:
1、发料时电子部不发备品(按实际订单用量发料,考核时,总超领数量减去损耗数量才为
其实际超领数);
2、发料时塑胶原料、喇叭材料发备品(按损耗比率发放);
3、发料时喷油丝印发备品(按损耗率发放);
4、电子部除正常依PMC套料表须料外,结工单时有差料请用工单零星补料;
5、木箱发料直接按BOM发料,不带备品。
7、参考文件:
7.1 《工单管理规范》
8、相关表单:
8.1 生产套料单
8.2物料超领单。