轮胎耐久性及轮胎高速性能转鼓试验机校准规范
轻型载重轮胎高速
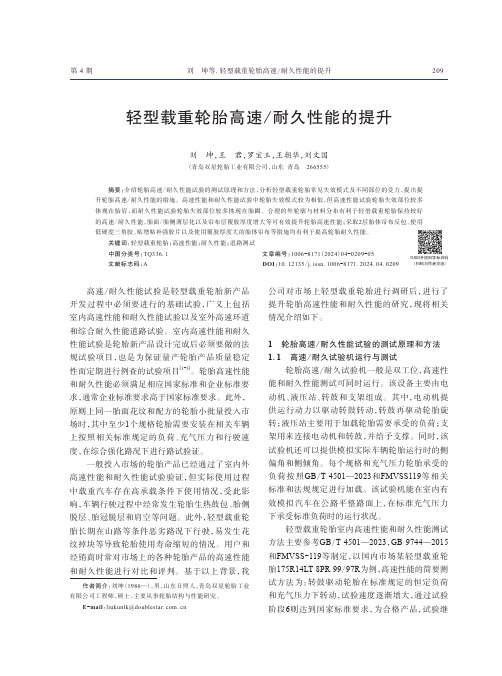
第 4 期刘 坤等.轻型载重轮胎高速/耐久性能的提升209轻型载重轮胎高速/耐久性能的提升刘 坤,王 君,罗宝玉,王朝华,刘文国(青岛双星轮胎工业有限公司,山东青岛266555)摘要:介绍轮胎高速/耐久性能试验的测试原理和方法,分析轻型载重轮胎常见失效模式及不同部位的受力,提出提升轮胎高速/耐久性能的措施。
高速性能和耐久性能试验中轮胎失效模式较为相似,但高速性能试验轮胎失效部位较多体现在胎肩,而耐久性能试验轮胎失效部位较多体现在胎圈。
合理的外轮廓与材料分布有利于轻型载重轮胎保持较好的高速/耐久性能,胎面/胎侧薄层化以及帘布层覆胶厚度增大等可有效提升轮胎高速性能;采取2层胎体帘布反包、使用低硬度三角胶、贴增粘补强胶片以及使用覆胶厚度大的胎体帘布等措施均有利于提高轮胎耐久性能。
关键词:轻型载重轮胎;高速性能;耐久性能;道路测试中图分类号:TQ336.1 文章编号:1006-8171(2024)04-0209-05文献标志码:A DOI:10.12135/j.issn.1006-8171.2024.04.0209高速/耐久性能试验是轻型载重轮胎新产品开发过程中必须要进行的基础试验,广义上包括室内高速性能和耐久性能试验以及室外高速环道和综合耐久性能道路试验。
室内高速性能和耐久性能试验是轮胎新产品设计完成后必须要做的法规试验项目,也是为保证量产轮胎产品质量稳定性而定期进行例查的试验项目[1-5]。
轮胎高速性能和耐久性能必须满足相应国家标准和企业标准要求,通常企业标准要求高于国家标准要求。
此外,原则上同一胎面花纹和配方的轮胎小批量投入市场时,其中至少1个规格轮胎需要安装在相关车辆上按照相关标准规定的负荷、充气压力和行驶速度,在综合强化路况下进行路试验证。
一般投入市场的轮胎产品已经通过了室内外高速性能和耐久性能试验验证,但实际使用过程中载重汽车存在高承载条件下使用情况,受此影响,车辆行驶过程中经常发生轮胎生热鼓包、胎侧脱层、胎冠脱层和肩空等问题。
轮胎性能测试方法概况
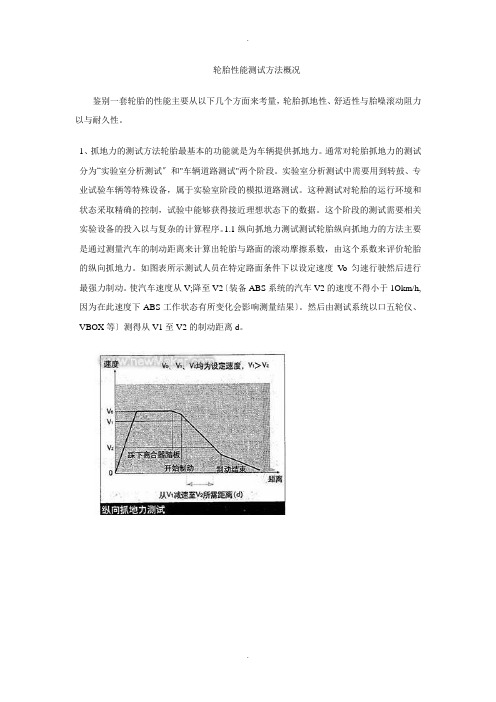
轮胎性能测试方法概况鉴别一套轮胎的性能主要从以下几个方面来考量,轮胎抓地性、舒适性与胎噪滚动阻力以与耐久性。
1、抓地力的测试方法轮胎最基本的功能就是为车辆提供抓地力。
通常对轮胎抓地力的测试分为“实验室分析测试〞和"车辆道路测试"两个阶段。
实验室分析测试中需要用到转鼓、专业试验车辆等特殊设备,属于实验室阶段的模拟道路测试。
这种测试对轮胎的运行环境和状态采取精确的控制,试验中能够获得接近理想状态下的数据。
这个阶段的测试需要相关实验设备的投入以与复杂的计算程序。
1.1纵向抓地力测试测试轮胎纵向抓地力的方法主要是通过测量汽车的制动距离来计算出轮胎与路面的滚动摩擦系数,由这个系数来评价轮胎的纵向抓地力。
如图表所示测试人员在特定路面条件下以设定速度V o匀速行驶然后进行最强力制动。
使汽车速度从V;降至V2〔装备ABS系统的汽车V2的速度不得小于1Okm/h,因为在此速度下ABS工作状态有所变化会影响测量结果〕。
然后由测试系统以口五轮仪、VBOX等〕测得从V1至V2的制动距离d。
V1和V2是测试过程中已经确定的定量d则通过仪器测得接下来就可以通过公式来计算以林值的大小则可用来衡量纵向抓地力。
简言之,d作为整个计算过程中的唯一变量,是改变μ值直接也是唯一的数据。
所以如果媒体或者一般测试机构在做轮胎比较测试的时候只需测得V,至V2的制动距离d就可以直接进行比较和评价了。
1.2横向抓地力测试产测试横向抓地力有三种模式:湿滑圆形场地测试积水弯道测试以与综合场地道路测试。
①·湿滑圆形场地测试首牛在附着1~2mm水深的圆形湿滑场地测试需要以一定的圆形半径在横向抓地力的极限状态下行驶数圈。
也就是在车辆即将出现侧滑的情况下绕圈行驶。
测量车辆绕行一周的时间,同时将行驶半径进行计算可以得出轮胎的极限横向加速度。
媒体或一般测试机构通过汽车在极限状态下的绕圈时间,就能对几套轮胎的横向抓地力进行评估。
·②积水弯道测试积水弯道测试则是在圆形场地中设置一道20m圆弧长7mm水深的积水带。
汽车轮毂试验的三个标准和分析过程

汽车轮毂试验的三个标准和分析过程一有关汽车轮毂的三个试验标准根据国内和国际标准化组织(ISO) 的规定,汽车轮毂必须满足三个典型试验的要求。
有关的国内标准与ISO 的标准是一致的,国外不同国家的标准可能不完全一样,但是基本方面还是一致的,只是具体载荷大小有所差别。
在国内,这三个试验对应的标准分别是:1. 车轮动态弯曲疲劳和径向疲劳试验方法- QCT221其中包含了动态弯曲和径向载荷两个疲劳试验标准。
2. 车轮冲击试验方法- GBT15704其中包含了轮毂冲击试验的标准。
下面简单介绍这三个试验标准。
标准1:汽车轻合金车轮的性能要求和试验方法QC/T221—1997前言本标准是根据1995 年标准制修订计划安排组织制定的。
本标准在制订过程中,参照采用了美国SFI、日本JASO 等有关标准。
本标准由机械工业部汽车工业司提出。
本标准由全国汽车标准化技术委员会归口。
本标准由广东南海中南铝合金轮毂有限公司负责起草、立中车轮制造有限公司参加起草。
本标准主要起草人:雷铭君。
1 范围本标准规定了汽车轻合金车轮的动态弯曲疲劳性能、动态径向疲劳性能要求及试验方法。
本标准适用于全部或部分轻合金制造的汽车车轮。
2 试验项目2.1 动态弯曲疲劳试验;2.2 动态径向疲劳试验。
3 试验样品弯曲疲劳和径向疲劳试验用的车轮应是未经试验或未使用过的新成品车轮,每个车轮只能做一次试验。
4 动态弯曲疲劳试验4.1 试验设备试验台应有一个旋转装置,车轮可在一固定不变的弯矩作用下旋转,或是车轮静止不动,而承受一个旋转弯曲力矩作用(见图1)4.2 试验程序4.2.1 准备工作根据车轮在车辆上安装的实际情况,按规定的扭矩最低值的115%,将车轮紧固在试验装置的支承面上,螺母不允许加润滑剂。
调整车轮位置后,将轮辋的轮缘夹紧到试验夹具上。
试验的连接件和车轮的配合面应去除多余的堆聚物、灰尘或杂质。
车轮的螺栓和螺母在试验过程中可再次紧固。
加载系统应保持规定的载荷,误差不超过±2.5%。
载重汽车轮胎测试标准、测试项目和测试要求
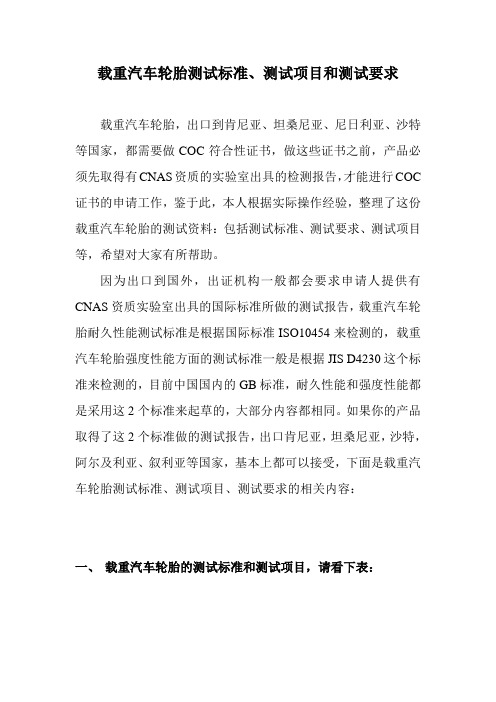
载重汽车轮胎测试标准、测试项目和测试要求载重汽车轮胎,出口到肯尼亚、坦桑尼亚、尼日利亚、沙特等国家,都需要做COC符合性证书,做这些证书之前,产品必须先取得有CNAS资质的实验室出具的检测报告,才能进行COC 证书的申请工作,鉴于此,本人根据实际操作经验,整理了这份载重汽车轮胎的测试资料:包括测试标准、测试要求、测试项目等,希望对大家有所帮助。
因为出口到国外,出证机构一般都会要求申请人提供有CNAS资质实验室出具的国际标准所做的测试报告,载重汽车轮胎耐久性能测试标准是根据国际标准ISO10454来检测的,载重汽车轮胎强度性能方面的测试标准一般是根据JIS D4230这个标准来检测的,目前中国国内的GB标准,耐久性能和强度性能都是采用这2个标准来起草的,大部分内容都相同。
如果你的产品取得了这2个标准做的测试报告,出口肯尼亚,坦桑尼亚,沙特,阿尔及利亚、叙利亚等国家,基本上都可以接受,下面是载重汽车轮胎测试标准、测试项目、测试要求的相关内容:一、载重汽车轮胎的测试标准和测试项目,请看下表:序号 测试项目 测试标准 备注1 耐久性 ISO104542 强度性能JIS D4230二、 标准要求:1、耐久性要求将轮胎安装在规定的测量轮辋上,充以其最大额定负荷相应气压,轮胎轮辋组合体在38度±3度温度下,至少停放3h ,然后试验转鼓以匀加速启动到初始试验速度的时间应在5min 以内,各速度等级轮胎的耐久性试验条件应符合下表的规定:载重汽车轮胎耐久性试验条件轮胎速度符号试验转鼓速度r /(km/h ) 轮胎最大额定负荷的百分比/2/3子午线轮胎 斜交轮胎持续时间7h (第一阶段) 16h (第二阶段) 24h (第三阶段)a) 单胎最大额定负荷≤1500kgF 35 3565 85 100 G 40 40 J 50 50 K 55 55 L 60 55 70 90 105 M 80 65 7575115N 90 - P 100 - Q 及其以上 120- b) 单胎最大额定负荷≥1500kgF 35 35 65 85 100G 45 35 J 50 40 K 55 50 L 65 - M 70 -2、强度性能测试要求将试验轮胎安装在规定的测量轮辋上,充入最大负荷对应的气压,实验室温度应保持在18-36度范围内,试验轮胎和轮辋组合体应在实验室温度下至少停放3h,然后将停放后的试验轮胎气压重新调整到规定值,再将试验轮胎和轮辋组合体安装到试验机上,沿轮胎胎面中心线取大致间隔相等的5个点进行试验,压头垂直于胎面,并压在靠近胎面圆周中心线的花纹块上,避免压入花纹沟中,压入轮胎的速度为50mm/min±2.5mm/min,测量每个点的轮胎破坏前瞬时的压力和压入深度(行程),或压头触及轮辋瞬时的压力或行程,再转入下一个点实验前校正气压。
全钢子午线轮胎胎圈耐久性能试验方法有限元验证
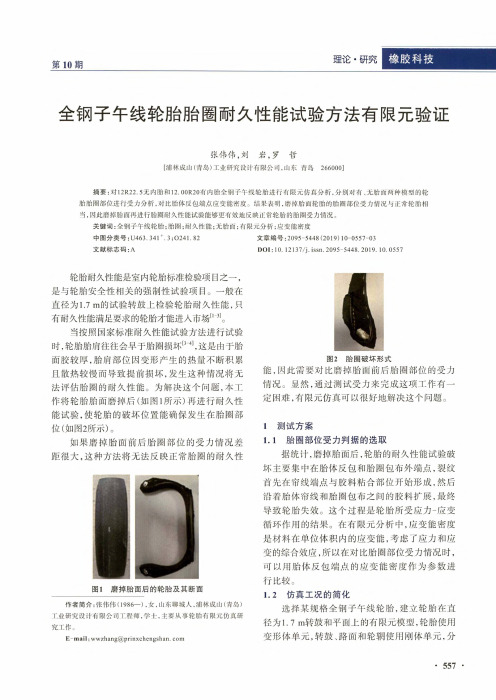
理论•研究第10期全钢子午线轮胎胎圈耐久性能试验方法有限元验证张伟伟,刘岩,罗哲[浦林成山(青岛)工业研究设计有限公司,山东青岛266000]摘要:对12R22.5无内胎和12.00R20有内胎全钢子午线轮胎进行有限元仿真分析,分别对有、无胎面两种模型的轮胎胎圈部位进行受力分析,对比胎体反包端点应变能密度。
结果表明,磨掉胎面轮胎的胎圈部位受力情况与正常轮胎相当,因此磨掉胎面再进行胎圈耐久性能试验能够更有效地反映正常轮胎的胎圈受力情况。
关键词:全钢子午线轮胎;胎圈;耐久性能;无胎面;有限元分析;应变能密度中图分类号:U463.341+.3;O241.82文章编号:2095-5448(2019)10-0557-03文献标志码:A DOI:10.12137/j.issn.2095-5448.2019.10.0557轮胎耐久性能是室内轮胎标准检验项目之一,是与轮胎安全性相关的强制性试验项目。
一般在直径为1.7m的试验转鼓上检验轮胎耐久性能,只有耐久性能满足要求的轮胎才能进入市场“叫当按照国家标准耐久性能试验方法进行试验时,轮胎胎肩往往会早于胎圈损坏这是由于胎面胶较厚,胎肩部位因变形产生的热量不断积累且散热较慢而导致提前损坏,发生这种情况将无法评估胎圈的耐久性能。
为解决这个问题,本工作将轮胎胎面磨掉后(如图1所示)再进行耐久性能试验,使轮胎的破坏位置能确保发生在胎圈部位(如图2所示)。
如果磨掉胎面前后胎圈部位的受力情况差距很大,这种方法将无法反映正常胎圈的耐久性图1磨掉胎面后的轮胎及其断面作者简介:张伟伟(1986-),女,山东聊城人.浦林成山(青岛)工业研究设计有限公司工程师.学士.主要从事轮胎有限元仿真研究工作。
E-mail:wwzhang@图2胎圈破坏形式能,因此需要对比磨掉胎面前后胎圈部位的受力情况。
显然,通过测试受力来完成这项工作有一定困难,有限元仿真可以很好地解决这个问题。
1测试方案1.1胎圈部位受力判据的选取据统计,磨掉胎面后,轮胎的耐久性能试验破坏主要集中在胎体反包和胎圈包布外端点,裂纹首先在帘线端点与胶料粘合部位开始形成,然后沿着胎体帘线和胎圈包布之间的胶料扩展,最终导致轮胎失效。
GBT13204-2002 摩托车轮胎高速性能试验方法 转鼓法
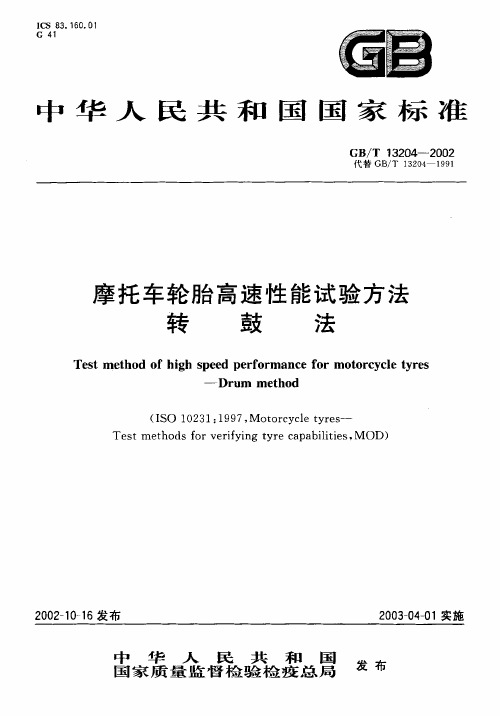
422 将轮胎与轮辆组合体压在试 验转鼓 的外表 面上 。 ..
423 将试验负荷施加于试验轴上 , 表 2 . . 见 , 表 2 高速试验负荷
试 验 负 荷
速度级别代号
轮辆 直径 代号 7 5及其 以上 , 负荷 指 数6 5及其 以上 的加强型轮胎 7%最大负荷 能力 5
士 15% 0 .
其速度 能力应满足试验方 法的要求 , 精度为满刻度 的士3 %e 32 充气压力表 : . 最大刻度 至少为 40 a精度为 士1 k a 0 k , P 0 , P
3 3 试 验 轮 姻 : 合 GB/ 28 . 符 T 9 3规 宁 的 标 准 较 姻 。 试 验方法
G T 30 - 2 0 B/ 12 4 0 2
摩托车轮胎高速性能试验方法
转 鼓 法
范围
本标准规 定了在转鼓试 验机上进行摩托 车轮胎高速性能试验 的方法。 本标准适用 于速度级别代 号 M 级及 以上或 最高速度 能力 10 / 3 k h及以上 的摩托车充 气轮胎, m 不 适 用于最高速度 能力低于 10 h的摩托 车充气 轮胎 。 3k m/
- / 12 4 1 9 GB T 3 0 - 9 1 本标 准委 托 全 国摩 托 车 自行 车 轮 胎 轮 辆 标 准 化 分 技 术 委 员会 负 责 解 释 。
转鼓法 》 。
GB T 3 0 - 2 0 / 124 02
引
言
G / 124已经 实施近 十年, 0 BT 3 它在我 国摩 托车轮胎 高速性 能试验 中起 到重要 的作用。
2 规范 性引用文件
下列文件 中的条款通过本标 准的引用而成为本 标准 的条 款 。凡是 注 日期 的引用 文件 , 其随后所有 的修 改单( 不包括勘误 的内容) 或修订 版均不适用 于本标准 , 然而, 鼓励根据 本标准达成协议 的各方研究 是 否可使用这些 文件 的最新版本 。凡 是不注 日期 的引用文件 , 新版本适用于本标 准。 其最
载重子午胎室内性能试验方法

载重子午胎耐久性能试验方法--------转鼓法转鼓试验就是用转鼓作为活动的模拟路面,将试验轮胎以规定的负荷压在转鼓上,做连续匀速行驶试验。
整个试验按行驶时间分几个阶段,并按阶段逐步增加负荷。
试验条件及步骤:1.将轮胎安装在标准轮辋上,充以其最大额定负荷相应的气压(当规定单胎和双胎两种使用条件时,以单胎最大额定负荷所对应的气压为准)。
2.轮胎轮辋组合体在38℃±3℃的温度下至少停放3H。
3.转鼓以匀加速由启动到规定速度的时间应在5min以内。
4.将准备好的轮胎轮辋组合体安装在试验轴上,使之垂直转鼓外表面加压,并按下表规定条件进行试验。
5.试验过程中不得中断,不得重新调整气压,不得人为地冷却轮胎,并保持各阶段相应的试验负荷不变。
6.完成试验后,要立即停机,测量轮胎气压和主要尺寸,待自然冷却后,卸下轮胎进行外观检查。
7.各速度等级轮胎的耐久性试验条件应符合下表所示:载重子午胎强度试验方法试验条件及步骤:1.将外观正常的轮胎充入双胎最大负荷对应的气压后安装在标准轮辋上。
2.在试验室温度下至少停放3小时,试验室温度为18-36℃,之后将停放后的轮胎气压重新调整到双胎最大负荷对应的气压。
3.将准备好的轮胎固定在试验机上,沿轮胎胎面中心线取大致间隔相等的5个点(轮辋名义直径≤10英寸的轮胎取大致间隔3个点)进行试验。
4.压头垂直于胎面,并压在靠近胎面圆周中心线的花纹块上,避免压入花纹沟中。
5.测量每个点轮胎破坏前瞬时的压力和压入深度(行程),或压头触及轮辋的瞬时压力和行程。
6.如果压头触及轮辋,轮胎没压穿,且没达到最小破坏能值,则此点视为达到最小破坏能。
7.用公式计算各点的破坏能:W=(F×P)/2000W-破坏能;JF-作用力;NP-行程;mm8.计算出各点的破坏能的算术平均值,作为该轮胎的破坏能。
载重汽车轮胎最小破坏能轮胎强度试验机所用压头直径阵mm载重子午胎高速性能试验方法该试验就是在规定的轮辋充气内压和负荷下,按逐级递增行驶速度的方法进行行驶试验,直至轮胎损坏或达到规定速度,以测定轮胎的临界速度,损坏速度,行驶时间和里程等。
轮胎、轮辋及气门嘴标准精选(最新)

轮胎、轮辋及气门嘴标准精选(最新)轮胎、轮辋及气门嘴标准精选(最新)G518《GB518-2007摩托车轮胎》G519《GB/T519-2003充气轮胎物理性能试验方法》G521《GB/T521-2012轮胎外缘尺寸测量方法》G1190《GB/T1190-2009工程机械轮胎技术要求》G1192《GB/T1192-2008农业轮胎技术条件》G1702《GB/T1702-2008力车轮胎》G1703《GB/T1703-2008力车内胎》G1796.1《GB1796.1-2008轮胎气门嘴第1部分:压紧式内胎气门嘴》G1796.2《GB1796.2-2008轮胎气门嘴第2部分:胶座气门嘴》G1796.3《GB1796.3-2008轮胎气门嘴第3部分:卡扣式气门嘴》G1796.6《GB1796.6-2008轮胎气门嘴第6部分:气门芯》G2933《GB/T2933-2009充气轮胎用车轮和轮辋的术语、规格代号和标志》G2977《GB/T2977-2008载重汽车轮胎规格、尺寸、气压与负荷》G2978《GB/T2978-2014轿车轮胎规格、尺寸、气压与负荷》G2979《GB/T2979-2008农业轮胎规格、尺寸、气压与负荷》G2980《GB/T2980-2009工程机械轮胎规格、尺寸、气压与负荷》G2981《GB/T2981-2014工业车辆充气轮胎技术条件》G2982《GB/T2982-2014工业车辆充气轮胎规格、尺寸、气压与负荷》G2983《GB/T2983-2008摩托车轮胎系列》G3487《GB/T3487-2005汽车轮辋规格系列》G3900《GB/T3900-2012轮胎气门嘴系列》G4501《GB/T4501-2008载重汽车轮胎性能室内试验方法》G4502《GB/T4502-2009轿车轮胎性能室内试验方法》G6326《GB/T6326-2005轮胎术语及其定义》G6327《GB/T6327-1996载重汽车轮胎强度试验方法》G7036.1《GB7036.1-2009充气轮胎内胎:汽车轮胎内胎》G7036.2《GB7036.2-2007充气轮胎内胎:摩托车轮胎内胎》G7037《GB7037-2007载重汽车翻新轮胎》G7377《GB/T7377-2008力车轮胎系列》G9102《GB/T9102-2003锦纶6轮胎浸胶帘子布》G9743《GB9743-2015轿车轮胎》G9744《GB9744-2015载重汽车轮胎》G9745《GB9745-2009航空轮胎》G9746《GB/T9746-2013航空轮胎系列》G9747《GB/T9747-2008航空轮胎试验方法》G9749《GB/T9749-2008力车轮胎性能试验方法》G9764《GB9764-2009轮胎气门嘴芯腔》G9765《GB9765-2009轮胎气门嘴螺纹》G9766.1《GB/T9766.1-2008轮胎气门嘴试验方法第1部分:压紧式内胎气门嘴试验方法》G9766.2《GB/T9766.2-2008轮胎气门嘴试验方法第2部分:胶座气门嘴试验方法》G9766.3《GB/T9766.3-2008轮胎气门嘴试验方法第3部分:卡扣式气门嘴试验方法》G9766.4《GB/T9766.4-2009轮胎气门嘴试验方法第4部分:压紧式无内胎气门嘴试验方法》G9766.5《GB/T9766.5-2009轮胎气门嘴试验方法第5部分:大芯腔气门嘴试验方法》G9766.6《GB/T9766.6-2008轮胎气门嘴试验方法第6部分:气门芯试验方法》G9766.7《GB/T9766.7-2009轮胎气门嘴试验方法第7部分:零部件试验方法》G9767《GB/T9767-2002轮胎气门芯试验方法》G9768《GB/T9768-2008轮胎使用与保养规程》G9769《GB/T9769-2005轮辋轮廓检测》G10823《GB/T10823-2009充气轮胎轮辋实心轮胎规格、尺寸与负荷》G10824《GB/T10824-2008充气轮胎轮辋实心轮胎技术规范》G11181《GB/T11181-2003子午线轮胎用钢帘线》G12836.2《GB12836.2-2003无内胎气门嘴第2部分:压紧式气门嘴》G12837《GB12837-1999大芯腔轮胎气门嘴》G12839《GB/T12839-2012轮胎气门嘴术语及其定义》G12939《GB/T12939-2002工业车辆轮辋规格系列》G13202《GB/T13202-2007摩托车轮辋系列》G13203《GB/T13203-2014摩托车轮胎性能试验方法》G13204《GB/T13204-2002摩托车轮胎高速性能试验方法转鼓法》G13652《GB/T13652-2004航空轮胎表面质量》G14450《GB/T14450-2004胎圈用钢丝》G14646《GB14646-2007轿车翻新轮胎》G14687《GB/T14687-1993工业车轮》G14688《GB/T14688-1993工业脚轮》G14828《GB/T14828-2003农业轮胎牵引性能试验方法》G15323《GB15323-2009航空轮胎内胎》G15324《GB/T15324-2004航空轮胎内胎物理性能试验方法》G16622《GB/T16622-2009压配式实心轮胎规格、尺寸与负荷》G16623《GB/T16623-2008压配式实心轮胎技术规范》G18505《GB/T18505-2013汽车轮胎动平衡试验方法》G18506《GB/T18506-2013汽车轮胎均匀性试验方法》G18861《GB/T18861-2012汽车轮胎和摩托车轮胎滚动阻力试验方法多点试验》G19047《GB19047-2003增强型载重汽车轮胎》G19388《GB/T19388-2003轿车轮胎滚动周长试验方法》G19389《GB/T19389-2003载重汽车轮胎滚动周长试验方法》G19390《GB/T19390-2003轮胎用聚酯浸胶帘子布》G21285《GB/T21285-2007轮胎气门嘴及其零部件的标识方法》G21286《GB/T21286-2007充气轮胎修补》G22036《GB/T22036-2008轮胎惯性滑行通过噪声测试方法》G22037《GB/T22037-2008航空有内胎轮胎胎圈密合压力试验方法电测法》G22038《GB/T22038-2008汽车轮胎静态接地压力分布试验方法》G22039《GB/T22039-2008航空轮胎激光数字无损检测方法》G22391《GB/T22391-2008实心轮胎耐久性试验方法转鼓法》G23657《GB/T23657-2009力车轮辋系列》G23663《GB/T23663-2009汽车轮胎纵向和横向刚性试验方法》G23664《GB/T23664-2009汽车轮胎无损检验方法X射线法》G24799《GB/T24799-2009轮胎用特种内胎》G26276《GB/T26276-2010工程机械子午线轮胎无损检验方法X 射线法》G26277《GB/T26277-2010轮胎电阻测量方法》G26278《GB/T26278-2010轮胎规格替换指南》G26732《GB/T26732-2011轮胎翻新工艺》G29040《GB/T29040-2012汽车轮胎滚动阻力试验方法单点试验和测量结果的相关性》G29042《GB/T29042-2012汽车轮胎滚动阻力限值》G30193《GB/T30193-2013工程机械轮胎耐久性试验方法》G30195《GB/T30195-2013汽车轮胎耐撞击性能试验方法》G30196《GB/T30196-2013自体支撑型缺气保用轮胎》G30197《GB/T30197-2013工程机械轮胎作业能力测试方法转鼓法》G30198《GB/T30198-2013汽车轮胎不圆度试验方法》JT752《JT/T752-2009横向力摩擦系数系统专用测试轮胎》GJ107A《GJB107A-1995航空轮胎设计要求》GJ108A《GJB108A-1998航空轮胎试验方法静负荷、动态模拟和导静电性能试验》GJ1261A《GJB1261A-2004军用越野汽车轮胎通用规范》HG2177《HG/T2177-1998轮胎外观质量》HG2195《HG/T2195-2001航空轮胎使用与保养》HG3979《HG/T3979-2007工程机械翻新轮胎》JJF1194《JJF1194-2008轮胎强度及脱圈试验机校准规范》JJF1195《JJF1195-2008轮胎耐久性及轮胎高速性能转鼓试验机校准规范》JJF1413《JJF1413-2013轮胎压力表型式评价大纲》。
- 1、下载文档前请自行甄别文档内容的完整性,平台不提供额外的编辑、内容补充、找答案等附加服务。
- 2、"仅部分预览"的文档,不可在线预览部分如存在完整性等问题,可反馈申请退款(可完整预览的文档不适用该条件!)。
- 3、如文档侵犯您的权益,请联系客服反馈,我们会尽快为您处理(人工客服工作时间:9:00-18:30)。
中华人民共和国国家计量技术规范JJF 1 195--2008轮胎耐久性及轮胎高速性能转鼓试验机校准规范Calibration Specification of Drum Tester forTyre Endurance and High Speed Test2008—03—24发布2008—06—24实施国家质量监督检验检疫总局发布轮胎耐久性及轮胎高速性能转鼓试验机校准规范Calibration Specification of Drum Testerfor Tyre Endurance and High SpeedTest本规范经国家质量监督检验检疫总局2008年3月24日批准,并自2008年6月24日起施行。
归口单位:全国法制计量管理计量技术委员会起草单位:北京橡胶工业研究设计院汕头市浩大轮胎测试装备有限公司本规范由全国法制计量管理计量技术委员会负责解释JJF1195--2008本规范主要起草人:王克先(北京橡胶工业研究设计院) 高健(北京橡胶工业研究设计院) 李抱清(北京橡胶工业研究设计院) 陈迅(汕头市浩大轮胎测试装备有限公司)参加起草人:周勇力(北京橡胶工业研究设计院) 闫抒昀(北京橡胶工业研究设计院) 刘心慧(北京橡胶工业研究设计院)JJF1195--2008目录1 范围1 2引用文献1 3概述1 4计量特性l 4.1转鼓l 4.2试验负荷1 4.3试验速度1 4,4加速时间1 5校准条件2 5.1环境条件2 5.2标准器及辅助件2 6校准项目和校准方法2 6.1转鼓2 6.2试验负荷示值误差2 6.3试验速度3 7校准结果表述4 8复校时间间隔4附录B测量不确定度的评定 6 附录A校准证书格式5JJF1195--2008轮胎耐久性及轮胎高速性能转鼓试验机校准规范1范围本规范适用于轿车轮胎、载重汽车轮胎和摩托车轮胎的耐久性转鼓试验机和高速性能转鼓试验机(以下简称试验机)的校准。
2引用文献本规范引用了下列文献GB/T6326--2005轮胎术语及其定义JJF1001—1998通用计量术语及定义JJF1059—1999测量不确定度评定与表示使用本规范时应注意使用上述引用文献的现行有效版本。
3概述试验机是专用于进行轮胎耐久性或高速性能试验的设备。
试验机由主机(机架、转鼓)、加载和负荷控制系统、驱动和速度控制系统等组成。
转鼓的钢制表面作为模拟路面,转鼓由电动机驱动,其转速可以调整。
耐久性试验和高速性能试验所不同的是高速试验机要求速度更高,所以当试验机的参数能满足轮胎进行耐久性和高速性能试验的规定条件时,耐久和高速试验可使用同一试验机。
4计量特性4.1转鼓4.1.1转鼓直径:(1700--4-17)mm。
4.1.2转鼓径向跳动不大于0.25mm。
4.2试验负荷4.2.1测量范围:(O.5~60)kN。
4.2.2分度值:0.001kN。
4.2,3示值最大允许误差;±1.5%。
4.3试验速度4.3.1测量范围:(30~320)km/h。
4.3.2分度值:0.1km/h。
4.3.3示值最大允许误差:±1.0%。
4.3.4波动度在15min内不超过1.0%。
4.4加速时间a)耐久性试验机。
转鼓以匀加速启动至达到80km/h的时闯不大于5min。
1JJF1195--2008b)高速性能试验机。
转鼓启动加速至80km/h的时间不大于5min。
其他试验阶段速度每增加40km/h,,其稳定的时间应小于1 min。
注:由于校准不判定合格与否,故上述各项要求仅供参考。
5校准条件5.1环境条件a)温度:(20~40)℃;b)相对湿度:≤85%;c)工作电源:电压的波动范围应不超出额定电压的±10%。
5.2标准器及辅助件5.2.1标准器a)标准测力仪两台。
测量范围分别为:(0.5~10)kN和(2~60)kN;准确度等级:0.3级;b)转速表。
测量范围:(1~1000)r/min;准确度等级:0.2级;c)钢直尺一支。
测量范围:500mm;分度值:1mm;d)钢卷尺一个。
测量范围:10m;准确度等级:Ⅱ级;e)百分表一个。
测量范围:(o~10)mm;准确度等级:1级;f)秒表一个。
分度值:0.1S。
5.2.2辅助件a)测力仪支架及力传感器支座;b)用于进行加速时间测试的新轮胎一套。
6校准项目和校准方法6.1转鼓6.1.1转鼓直径转鼓直径用钢卷尺分别测量转鼓鼓面的中部及两边距边缘50mm处的周长,取平均值。
按公式(1)计算其直径。
D一生(1)丁亡式中:D——转鼓直径(D的计算值取整数),mm;L——三次测得转鼓周长的平均值,mm;7【——圆周率,取Ⅱ一3.14。
6.1.2转鼓径向跳动用百分表测量转鼓鼓面中间及距两边边缘50mm三处的径向跳动,取最大值为校准结果。
6.2试验负荷示值误差将标准测力仪装于轮胎支承轴和校准用支座之间,调整其位置,使其中心线在转鼓轴与轮胎支承轴中心的连线重合。
2nF1195--2008缓慢加载,在测量范围内取大致均匀分布的5点进行测试。
当标准测力仪达到所取测量值时,读取试验机相应示值。
重复测量3次。
按公式(2)计算负荷示值误差。
qf一—F1i--。
一Fo,×100%F叭一式中:吼——第i测量点,负荷相对误差;F。
——第i测量点,试验机3次示值的算术平均值,kN;F。
——第i测量点,标准测力仪示值,kN。
6.3试验速度6.3.1速度用转速表测量转鼓速度。
耐久性试验机取30km/h,60km/h,100km/h3个测量点。
高速性能试验机取80km/h,160km/h,240km/h,320km/h4个测量点。
当试验机转速示值为规定值时,记录转速表测量的转速值。
每测量点重复测量3次,按公式(3)计算速度示值误差。
氏。
一(瓦百瓦梳一1)×1叩%(3)式中:&——第i测量点,速度示值误差%,对耐久性试验机i一1,2,3,对高速性能试验机i一1,2,3,4;Vi——第i测量点,试验机速度示值,km/h;7c——圆周率,取7c一3.14。
D——转鼓直径,m;ff。
——第i测量点转速表测得3次转速值的平均值,r/rain。
6.3.2速度波动度启动转鼓加速至80km/h,速度稳定后,观察速度示值变化,每5min记录一次,记录3次,按公式(4)计算其速度波动度。
b一—Vmax--—Vmin×100%(4)‰式中:6——速度波动度;。
——试验机3次记录示值中的最大值,km/h;口——试验机3次记录示值中的最小值,km/h;矾——试验机设定速度,km/h。
6.3.3加速时间 a)将轮胎安装在轮胎支承轴上,按试验要求加载;b)耐久性试验机。
用秒表测量转鼓从启动至达到80km/h的时间,重复测量3次,取算术平均值作为测量结果;c)高速性能试验机。
用秒表测量转鼓从启动至达到80km/h的时间,重复测量3次,取算术平均值作为测量结果;转速从100km/h始,按40km/h为一挡逐步增速至220km/h,记录每挡达到速度稳定时间作为阶段加速时间测量结果。
3JJF1195--20087校准结果表述校准结果在校准证书或校准报告上反映。
校准证书或报告应包括以下内容a)名称,“校准证书”或“校准报告”;b)证书或报告的编号,每页及总页数;c)送校单位,地址;d)试验机名称,规格型号及编号;e)校准地点;f)校准日期;g)校准环境条件;h)校准所依据的技术规范;i)校准所用测量标准器的溯源性及其有效性说明;j)校准机构;k)校准结果数据及其测量不确定度说明;1)校准证书或报告的报告人,审核签发人的签名;m)证书或报告的有效期;n)未经校准机构书面批准,不得部分复制证书或报告的声明等其他说明。
8复校时间间隔复校时间间隔由用户自定,建议为1年。
4JJF1195--2008附录A校准证书格式A.1校准证书应包括第7条所列要求的信息。
A.2校准证书背面格式如表A.1。
表A.1校准证书背面格式校准结果室温——℃转鼓直径(mm)径向跳动(ram)18工位28工位校准点示值示值相对误差%校准点-示值示值相对误差%负荷(kN)校准点示值速度相对误差%速度波动度%速度(km/h)加速范围(km/h)时间(min)加速时间备注53jF 1195--2008附录B测量不确定度的评定B .1负荷校准测量不确定度评定B .1.1建立数学模型,列不确定度式以标准测力仪为基础,试验机显示对应的示值,计算其相对误差,校准结果的数学模型为:8一!学×100%式中:卜试验机示值相对误差,%;F 。
——试验机示值,kN ;F ——标准测力仪示值,kN 。
由不确定度传播律:“2(占)一c}ד2(F1)+f;ד2(F)其中㈨一著一去心一薯一一乒Fl不确定度式为:烈a)一(去)2 Xu2(F1)+(-甜斌(F)B .t .2不确定度来源 a)试验机示值的误差产生的不确定度“。
b)试验机测量重复性产生的不确定度“。
c)标准测力仪产生的不确定度“。
B .1.3不确定度分量的评估 a)试验机示值误差产生的标准不确定度“,试验机的负荷示值分辨力为0.001 kN ,以等概率分布(矩形分布)落在宽度为0.001 kN /2—0.000 5 kN的区间内。
其标准不确定度为“,(F1)一0.000 5 kN /,/3=0.000.、kN ,自由度Ⅵ一+。
b)试验机测量重复性产生的标准不确定度“。
加载负荷为50 kN ,重复测量9次,其值为:50.051,50.082,50.075,50.043,50.060,50.091,50.070,50.078,50.092 kN ,Fi 一50.071 kN ,测量实验标准差^J ——百二T 一I i ;1浮kN 一0.017,kN/∑(F,:一F ,)2s(F1)三次平均测量结果重复性标准不确定度为“:(F1)一s(F 。
)/√可一o .017 1/。
/3 kN自由度v :一8。
c)标准测力仪的标准不确定度“。
6JJF1195--2008标准测力仪准确度等级为0.3级,其极限误差为±0.3%,对50kN可能有±0.15kN误差。
按均匀分布,其标准不确定度为:“(F)一0.15/√手kN一0.087kN估计其标准不确定度80%可靠,故自由度为:一丢×[帮]一一丢×[罕]~一12表B.1输出量的标准不确定度分量一览表序输入量的标准不确定度评定自由度输出量的标准不确定度分量号来源符号数值符号数值符号灵敏系数c,c。
『X“(z)1试验机示值误差“l(F1)0.000 3 kN+oo“11/F一0.02kN“0.01%2 试验机测量重复性“2(F1)0.01kN8 “21/F一0.02kN“0.02%3标准测力仪误差"3(F)0.087kN12“3F./F2—0.02kN一‘0.17%B.1.4合成标准不确定度的评定由于标准不确定度分量互不相关,故“。