磨削过程模型的建立及其计算机仿真
MATLAB与VB接口编程实现磨削温度场的仿真

第28卷 第11期2006年11月武 汉 理 工 大 学 学 报JOURNA L OF WUHAN UNIVERSIT Y OF TECHN OLOG Y Vol.28 No.11 Nov.2006MA T LAB 与VB 接口编程实现磨削温度场的仿真汪心立,张建华,任升峰,段彩云,董春杰(山东大学机械工程学院,济南250061)摘 要: 将MA TLAB 的强大数学运算功能和图形绘制功能与VB 在用户界面开发方面的优势结合起来,通过混合编程实现了磨削温度场的仿真研究。
在仿真系统的前端界面输入计算温度场的命令语句或者是直接输入磨削用量后经过调用MA TLAB 软件计算可以得到相应条件下的温度场模型,同时该仿真系统除了应用温度场仿真外还可扩充到其他物理量如磨削力,表面粗糙度等的仿真研究。
关键词: 磨削; 温度场; MA TLAB ; VB ; 计算机仿真中图分类号: TP 391.9文献标志码: A 文章编号:167124431(2006)1120111203Simulation of G rinding T emperature Field B ased on the Applicationof MAT LAB and VBW A N G Xi n 2li ,ZHA N G Jian 2hua ,R EN S heng 2f eng ,DUA N Cai 2yun ,DON G Chun 2jie(School of Mechanical Engineering ,Shandong University ,Jinan 250061,China )Abstract : This paper introduced the research of simulation in grinding temperature field based on the hybrid programming between MA TLAB and VB.The simulation integrates their advantages ,which were powerful mathematic calculation capacity and graphic capacity of MA TLAB ,and VB ’s friendly visual interface.When inputting programmed command of temperature pattern or grinding parameters directly ,the temperature distribution could be gained through calculating by MA TLAB ,and be 2sides ,it could also be applied to other physical quantity simulation ,for example grinding force ,surface roughness and so on.K ey w ords : grinding ; temperature fields ; MA TLAB ; VB ; computer simulation 收稿日期:2006205220.基金项目:国家自然科学基金(50275087).作者简介:汪心立(19802),男,硕士.E 2mail :wangxinli @在磨削温度场的仿真研究中,应用数学模型和计算机仿真技术能够得出比较准确的温度分布图,可以分析磨削用量对温度场的影响,进而发现磨削温度场的变化规律,通过优化磨削用量,使温度场的温度变化趋向于合理[1],最终能够达到在磨削过程中减少磨削烧伤发生的效果。
磨削强化过程的温度场计算机动态仿真与实验验证
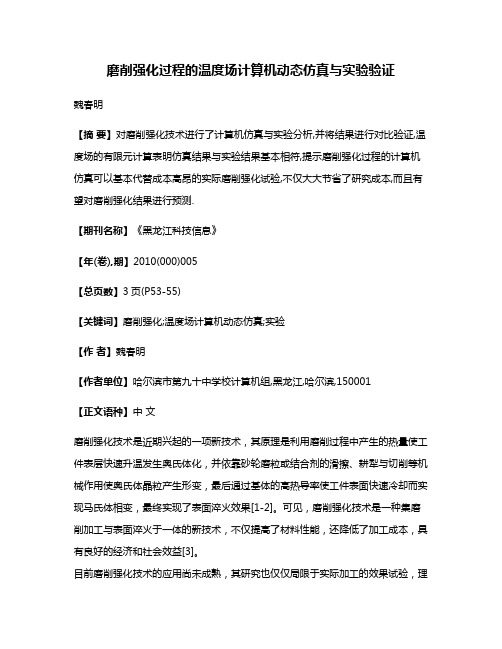
磨削强化过程的温度场计算机动态仿真与实验验证魏春明【摘要】对磨削强化技术进行了计算机仿真与实验分析,并将结果进行对比验证,温度场的有限元计算表明仿真结果与实验结果基本相符,提示磨削强化过程的计算机仿真可以基本代替成本高昂的实际磨削强化试验,不仅大大节省了研究成本,而且有望对磨削强化结果进行预测.【期刊名称】《黑龙江科技信息》【年(卷),期】2010(000)005【总页数】3页(P53-55)【关键词】磨削强化;温度场计算机动态仿真;实验【作者】魏春明【作者单位】哈尔滨市第九十中学校计算机组,黑龙江,哈尔滨,150001【正文语种】中文磨削强化技术是近期兴起的一项新技术,其原理是利用磨削过程中产生的热量使工件表层快速升温发生奥氏体化,并依靠砂轮磨粒或结合剂的滑擦、耕犁与切削等机械作用使奥氏体晶粒产生形变,最后通过基体的高热导率使工件表面快速冷却而实现马氏体相变,最终实现了表面淬火效果[1-2]。
可见,磨削强化技术是一种集磨削加工与表面淬火于一体的新技术,不仅提高了材料性能,还降低了加工成本,具有良好的经济和社会效益[3]。
目前磨削强化技术的应用尚未成熟,其研究也仅仅局限于实际加工的效果试验,理论研究较少,因此磨削强化的试验研究成本较高,而且具有很高的盲目性。
现针对这一缺点,提出并进行了磨削强化过程的计算机动态仿真,从而为试验过程中温度场的研究、强化效果的预测、各项加工参数的合理选择,以及强化过程的理论研究等内容提供了基础。
磨削强化过程中,砂轮与工件表面间的接触面即为热源。
由于砂轮与工件之间存在进给运动,因此该热源可视为沿着工件表面匀速移动;为了使工件表面产生良好的强化效果,该温度场还应当使工件与其接触时,表面迅速升温至Ac3以上并奥氏体化,并在其离开时迅速冷却,以产生足够的马氏体。
因此应当将移动热源和瞬态温度场结合,进行强化过程中工件表面的热分析。
根据传热学理论,三维瞬态温度场中的固体导热微分方程为[4-5]:式中 T——物体的瞬态温度(℃);t——过程进行的时间(s);λ——材料的导热系数;qm——热流密度;ρ——材料密度;cp——材料的定压比热(J/kg·℃)。
matlab的平磨工件表面三维模型仿真方法

文章标题:深入探讨matlab的平磨工件表面三维模型仿真方法一、引言在制造业中,表面质量对工件的性能和外观至关重要。
平磨是一种常见的表面加工方法,对工件表面质量的影响非常大。
为了更好地理解和控制平磨工件表面的三维模型,使用matlab进行仿真已成为一种有效的方法。
本文将深入探讨matlab的平磨工件表面三维模型仿真方法。
二、matlab在平磨工件表面三维模型仿真中的应用1. 数据采集与处理在进行平磨工件表面三维模型仿真时,首先需要对工件表面进行数据采集。
这涉及到使用各种传感器来获取工件表面的高度数据。
matlab提供了丰富的数据处理工具,可以对采集到的数据进行滤波、插值等预处理,以准备好用于仿真的数据。
2. 三维模型建立基于采集到的工件表面高度数据,利用matlab可以方便地建立工件的三维模型。
通过对数据进行表面重建算法的运用,可以得到工件表面的三维模型,并进行可视化展示。
3. 条件设置与仿真在建立工件的三维模型后,可以在matlab中设定不同的加工条件,如磨削速度、磨削压力等,对工件表面进行仿真。
matlab提供了多种仿真方法,如有限元法、离散元法等,可以有效地模拟平磨过程对工件表面的影响。
4. 结果分析与优化通过matlab进行仿真后,可以对仿真结果进行分析,并根据需要进行优化。
可以通过对仿真结果进行曲面拟合,找出工件表面的几何特征,对表面质量进行评价,并提出相应的优化建议。
三、个人观点和理解matlab作为一款强大的科学计算软件,在平磨工件表面三维模型仿真中具有广泛的应用前景。
通过matlab的仿真方法,不仅可以更好地理解平磨工件表面的变化规律,还能为工程实践提供科学依据。
对我来说,深入学习和掌握matlab在平磨工件表面三维模型仿真中的方法,将有助于我在相关领域的研究和实践中取得更优异的成果。
四、总结与回顾通过本文的讨论,我们对matlab在平磨工件表面三维模型仿真中的方法有了更深入的了解。
磨边机的磨削过程的数学模型的研究
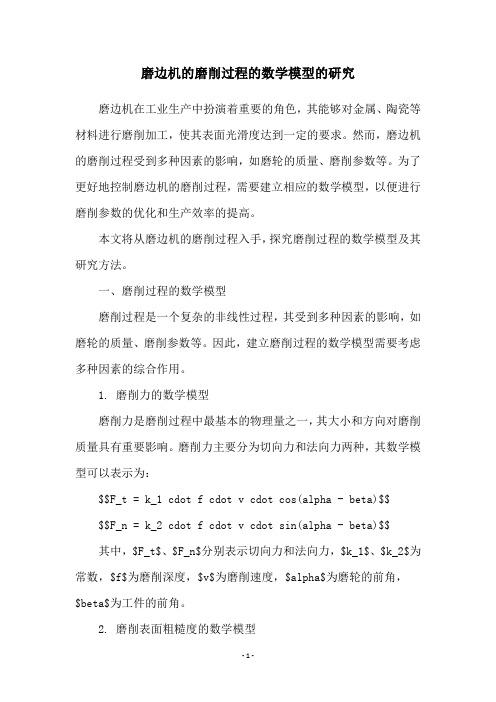
磨边机的磨削过程的数学模型的研究磨边机在工业生产中扮演着重要的角色,其能够对金属、陶瓷等材料进行磨削加工,使其表面光滑度达到一定的要求。
然而,磨边机的磨削过程受到多种因素的影响,如磨轮的质量、磨削参数等。
为了更好地控制磨边机的磨削过程,需要建立相应的数学模型,以便进行磨削参数的优化和生产效率的提高。
本文将从磨边机的磨削过程入手,探究磨削过程的数学模型及其研究方法。
一、磨削过程的数学模型磨削过程是一个复杂的非线性过程,其受到多种因素的影响,如磨轮的质量、磨削参数等。
因此,建立磨削过程的数学模型需要考虑多种因素的综合作用。
1. 磨削力的数学模型磨削力是磨削过程中最基本的物理量之一,其大小和方向对磨削质量具有重要影响。
磨削力主要分为切向力和法向力两种,其数学模型可以表示为:$$F_t = k_1 cdot f cdot v cdot cos(alpha - beta)$$$$F_n = k_2 cdot f cdot v cdot sin(alpha - beta)$$ 其中,$F_t$、$F_n$分别表示切向力和法向力,$k_1$、$k_2$为常数,$f$为磨削深度,$v$为磨削速度,$alpha$为磨轮的前角,$beta$为工件的前角。
2. 磨削表面粗糙度的数学模型磨削表面粗糙度是衡量磨削质量的重要指标之一,其数学模型可以表示为:$$R_a = frac{1}{2pi} int_0^{2pi} h(x) cdot cos(x) dx$$ 其中,$R_a$为磨削表面粗糙度,$h(x)$为表面高度函数。
3. 磨削温度的数学模型磨削过程中会产生大量的热量,磨削温度对磨削质量具有重要影响。
磨削温度的数学模型可以表示为:$$T = T_0 + k_3 cdot f cdot v cdot ln(frac{t}{t_0})$$ 其中,$T$为磨削温度,$T_0$为初始温度,$k_3$为常数,$t$为磨削时间,$t_0$为初始时间。
磨削加工运动学及有限元建模与仿真

磨削加工运动学及有限元建模与仿真韩振鲁 李长河(青岛理工大学 山东青岛 266033)摘 要 介绍了建立磨削加工运动学模型的基本方法,讨论了对砂轮表面形貌的模拟,多种运动几何模型的比较以及应用运动学经验模型解析公式。
详细介绍了有限元分析的基础,在磨削加工中利用有限元分析的理论,所开发的有限元仿真自主软件,能够自动产生完全的模拟仿真过程。
研究表明,建模仿真对于研究磨削过程是非常适合的方法。
有限元仿真方法可以让使用者对于加工过程有更好的理解,并可以帮助分析复杂的试验结果。
经过计算机程序中的误差处理后,加工工件就能达到较高的精度,同时降低了制造成本。
关键词运动学模型 表面形貌 模拟仿真 有限元分析1 运动学模型自从建立第一个磨削过程的运动模型,迄今已有45年了。
尽管从那时到现在所有的方法都用来开发建模,包含对砂轮、工件和磨削运动学的描述,但是各种模型间仍具有显著的差异。
20世纪60年代和20世纪70年代早期的磨削运动学模型奠定了二维磨削理论的基础,在1980年后,当计算机运算速度大大提高后,人们建立了更加复杂的模型,这些方法中最典型的是对磨削过程采用三维立体的观点,主要是基于工件表面和砂轮表面的在几何学上的互相渗透的经验运动模型。
该模型中,磨削过程的输出参数可以通过解析和经验公式计算出来。
1.1 砂轮表面形貌的模拟在讨论磨削加工的所有模型中,对砂轮表面形貌的模拟是必不可少的一部分。
现在有两种方法来对砂轮表面形貌进行定量描述:一是直接对砂轮表面进行扫描,二是运用统计学的方法对砂轮表面进行分析来合成砂轮表面形貌。
Inasaki在他的磨削过程模拟中,提出了一个直接得到砂轮表面形貌的方法。
他得到了绕砂轮一周的表面形貌数据,并将这些数据储存在微机以供日后模拟使用。
通过已扫描的表面来分析砂轮的特性进而导出砂轮的表面形貌的一般数据信息。
利用这些统计的砂轮表面形貌数据,例如磨粒大小的平均值和分布、磨粒分布的方向以及磨粒突出表面的高度等等,综合这些参数就有可能得到比较合理的砂轮表面形貌数据。
仿真技术及其在磨削加工中的应用

模型可以分为物理模型和数学模型 。物理模型又 称为实体模型 ,它是实际系统在尺寸上缩小或放大后 的相似体 。数学模型是用数学方程来描述实际系统的 结构和性能的模型[1] 。数学模型建模包括经验公式 法 、基本定律法和非线性隐式法三大类 。
输入磨削类型 、工件属性 、磨削砂轮规格和加工参数 ,
来预报各磨削特性 ,如力 、功率 、挠度 、温度 、比能 、粗糙
度和椭圆度等 。校准过程中 ,系统首先比较在初磨阶
段的最初过渡期间测量和预报的功率来估计系统刚度 。
表 1 用 GRINDSIM 优化仿真的磨削时间比较
粗磨
精磨
光磨
I
进给率 mmΠsp 时间 s
随后用初磨阶段稳定期间内的平均功率来校准初始砂 轮磨损的平面模型 。在优化阶段 ,一般的优化目标是 最小化周期时间 。
表一是运用 GRINDSIM 优化仿真的一个时间比 较 。I 是普通的磨削加工参数 ,加工一个零件共需要 31. 9 秒 。在同样的加工条件下 ,用软件以最小化周期 时间为目标进行优化仿真 ,II 服从无烧伤约束 ,加工时 间减小到了 23. 1 秒 ,此时磨削弧区达到了烧伤极限 。 III 是允许在粗磨阶段烧伤 ,在随后的精磨阶段去除烧 伤的热损伤材料 ,可以进一步减少磨削时间到 15. 5 秒 ,而且用此软件的热模型还可以计算出粗磨时的热 损伤深度[16] 。
“仿真”一词的确切含义目前仍有争议 ,简单地说 , 仿真是建立相应物理系统的数学模型在计算机上解算 的过程[14] 。由于数字计算机执行的对象只能是离散 (数字) 形式的 ,所以仿真技术的最大特征是在模型中 使用时间离散值 。这样 ,仿真对象的任何时刻的运行 状态都可以用仿真软件来清楚地描述[7] 。 2. 5 建模与仿真的关系
表面磨削力的建模和实验研究

在这里, C 是砂轮单位面积上有效的研磨刀刃的数量, r 是切屑宽度与切屑厚度 的比率,de 是砂轮的等效直径。 将式(9)代入等式(8) ,得到磨削应变速率为
实验数据 (刘, 1991) 表明, 剪切流应力与剪切应变率近似成正比, 也就是说, 动态的特定切屑形成能 ud 与剪切应变率对数近似成正比,即:
组参数试验三次,然后取平均值,见表 3) ,7 个未知参数(见表 4)通过求解线 性方程组确定。 将表 4 中的实验常数代入等式(27) ,可以得到磨削力的计算公式
这里
是剪切流动应力,
剪应变,
是剪切应变率,T 是变形温度。
当于剪切应力 ,剪切应变率 增加,剪切流 的材料的应力将增加。当 变形温度上升时,材料的剪切流动应力会减少。动态具体切屑形成能 ud 和剪切 流动应力的变化是成正比, 这是剪切应变效应,剪切应变率效应和热软化的效应
综合作用的结果。 2.1.2。剪应变效应 在两维的切割情况下,剪切带的剪切应变(Shinji 等人,1985)是
图 2 高精度平面磨削机床 MGK7120×6. 式中,W 是法向负荷,A0 是接触面积, 性能确定的系数。 表 1 测力计性能参数 测量范围 灵敏度 线性度 固定频率 工作温度范围 Fx , Fy : ±5 kN, Fz :−5/+10 kN Fx , Fy :10 mV/N, Fz : 5 mV/N ±1% Fx , Fy : 2 KHz, Fz : 3.5 KHz 0–60℃ 和 通过接触界面的物理和机械
在研究成果的基础上,结合马尔金的磨削理论(马尔金,2002 年)和著名的金 属材料切削变形理论(刘,1991;真嗣等人,1985) ,一个新的易于使用的表面磨 削力数学模型被提出,改进的模型考虑到了磨削 参数和金属材料的切割动态力学表现之间的关系, 还有磨削参数对工件与砂轮之 间的摩擦系数的影响,磨削力模型中与砂轮和工件有关的常量是由实验得到的。 比较这个新的磨削力数学模型计算结果和实验结果,模型的有效性得到了证明。 2。磨削力数学模型 磨削力可以分为两部分,切削变形力和滑动力,切割变形力可以分离成切屑形 成力和耕作力。在磨削力的计算模型中忽略耕作力因为它是远小于切屑变形力 (马尔金,2002 年) ,因此磨削力可以分为两个部分:切屑形成力和滑动力。 Fn = Fn,ch + Fn,sl Ft = Ft,ch + Ft,sl (1)
摩擦磨损试验机的虚拟设计与仿真分析

东北大学硕士学位论文目录目录独创性声明…………………………………………………………………I摘要……………………………………………………………………..IIAbstract………………………………………………………………………………………………………………..III第1章绪论……………………………………………………………..11.1课题研究的背景和意义…………………………………………………………………..11.2国内外研究现状及发展动态……………………………………………………………..21.3虚拟设计技术简介…………………………………………………………………………41.4课题研究的思路及主要内容……………………………………………………………..5第2章摩擦磨损试验机的总体设计……………………………………72.1试验机的功能及技术参数………………………………………………………………..72.2试验机的设计依据………………………………………………………………………..72.3试验机的系统组成…………………………………………………………………………92.3.1动力传动系统…………………………………………………………………….102.3.2加载系统…………………………………………………………………………..112.3.3感应加热系统…………………………………………………………………….112.3.4润滑系统………………………………………………………………………….122.4试验机的机械系统建模…………………………………………………………………122.4.1零部件三维实体模型的建立…………………………………………………….122.4.2机械系统虚拟装配模型的建立………………………………………………….1312.4.3机械系统装配模型干涉检验…………………………………………………….15.2.5本章小结…………………………………………………………………………………16第3章试验机关键零部件的有限元分析………………………………173.1轴承座和传动轴的结构静力分析………………………………………………………173.1.1轴承座的静力分析……………………………………………………………….173.1.2传动轴的静力分析……………………………………………………………….20f东北大学硕士学位论文目录5.3有限元分析模型的建立…………………………………………………………………625.3.1感应加热一维模型的建立……………………………………………………….625.3.2边晃条件、分析单元与网格划分……………………………………………….635.3.3电磁场与温度场相互耦合的实现……………………………………………….655.4感应加热实际工况模拟与分析…………………………………………………………665.4.1工况模拟工艺参数与材料特性参数…………………………………………….665。
- 1、下载文档前请自行甄别文档内容的完整性,平台不提供额外的编辑、内容补充、找答案等附加服务。
- 2、"仅部分预览"的文档,不可在线预览部分如存在完整性等问题,可反馈申请退款(可完整预览的文档不适用该条件!)。
- 3、如文档侵犯您的权益,请联系客服反馈,我们会尽快为您处理(人工客服工作时间:9:00-18:30)。
将磨削初始条件及模型参数输入到磨削仿真 程序中, 运行仿真程序即可得出磨削过程的仿真曲 线。本文列举了几个主要仿真曲线, 图 4 是总进给 量和磨削切深仿真曲线; 图 5 是磨削力和光磨阶段 工件表面粗糙度的仿真与试验对比曲线。
其试验是在 M MB1320 半自动外圆磨床上进 行 的, 工 件 材 料 选 用 淬 火 45 钢, 所 用 砂 轮 是 GB70RAP 400×32×203。具体仿真输入参数如 下: v 2 = 33m / s, v1 = 0. 25m/ s, vf = 0. 015m m/ s, dwi = 59m m, dwf = 58. 85mm , ds = 200mm , km =
C
v
0. 1
53 -
v2
0. 765- / 2
( 15)
对于滚珠轴承 = 0. 25, 则
max( z =
0) =
C
v
0. 1
28v
0. 2
25
0. 64
( 16)
可 见, 对于横向进给磨削, 磨削深度是影响磨削热
源表面最高温度的重要因素。
1. 5 工件表面粗糙度模型的建立 根据影响工件表面粗糙度的一些主要因素, 引
·3·
( a) 磨削深度—时间关系曲线
中国机械工程第 13 卷第 1 期 2002 年 1 月上半月
29 7~3 02 [ 2] Suto T , Sata T . Simulatio n o f Gr inding pro cess
Based on W heel Surfa ce Char acteristic. Bull. Ja pan So c. P rce. Eng g. , 1981: 15, 27~34 [ 3] Steffens K , K onig W. Closed lo op simulation of g r inding . A nn. CIRP , 1983, 32( 1) : 255~259 [ 4] Chen X un, W Br ian Ro we . A naly sis and Simulation o f T he Gr inding Pr ocess. Int . J. M T M , 1996, 36 ( 8) : 871~906 [ 5] [ 日] 臼井英治著, 高希正译. 切削磨削加工学. 北京: 机械工业出版社, 1982: 89~90
有关的系数; b 为磨削宽度; 为有效磨粒间隔; 为经验常
·1·
数, 一般取 0. 2 ~ 0. 5; v1 为工件速度; v 2 为砂轮速度; dw 为 工件直径; ds 为砂轮直径; 为工件每转磨削深度。
1. 2 磨削深度模型的建立
由式( 1) 可见, 外圆横磨过程中, 是影响磨削
力 的主要因素, 它是依赖于时间连续变化的, 这正 是能够对磨削过程进行实时描述的关键。当磨削进
将式( 1) 代入式( 13) 并设
de =
dwd s d w + ds
则
max ( x , z ) =
[
3. 1Rw J
a(
2a )
0.
47d
/2e
w 0. 235
-
2
]
v0.531
v2
0. 765-
/2
ex p[ -
0.
69
d
e
( 0. 185
2 a)
-
0.
63v
1
0.63
- z 0. 185 ]
对于粗磨阶段, 解式( 6) 可得 t 时刻实际总进
给量
r( t) = 1 vf ( t -
+ e- t)
( 7)
·2·
中国机械工程第 13 卷第 1 期 2002 年 1 月上半月
实际进给磨削深度为
( t)
=
r ′( t) nw
=
vf nw
(
1
-
e
t)
( 8)
经过时间 t 1 进入光磨阶段后, x ′= vf = 0。此
时可得光磨阶段总的进给量和磨削深度为
r( t) = 1 v f ( t1 +
e - ( t- t1) )
( 9)
( t) =
1 nw
vf
(
e-
(
t-
t1 )
-
e-
t)
( 10)
当 磨削深度被计算出来之后, 将式( 8) 和式
( 10) 代入式( 1) , 即可建立依赖于时间变化的磨削
力的模型。进而可以对磨削功率、工件平均温升、磨
又由
s′=
dw dsG
r
′
=
Fn ke
=
kc ke
=
k cr ′ k enw
( 5)
式中, G 为磨削比; nw 为工件转速。
将式( 5) 代入式( 4) 并令
1+
dw dsG
=
,
kc k e nw
=
则式( 4) 变为
″+ r ′= x ′
( 6)
x ′= vf 式中, vf 为砂轮架横向控制进给率, 粗磨时 vf 为常量, 光磨 时为零。
王龙山 教授
在磨削过程中, 对整个磨削过程进行依赖于时 间变化的计算机仿真需要集成众多的磨削模型。磨 削行为计算机仿真的主要文献有 利用蒙特卡洛 法对磨削过程仿真, 但其精确性不高[ 1] ; 建立在 砂轮表面特性的磨削过程仿真, 但是磨粒的尺寸没 有包括到仿真模型中去[ 2] ; 磨削闭合回路仿真, 但是仿真的结果过分地依赖 于对砂轮表面的测 量[ 3] ; 磨削过程的分析和仿真, 增加了对砂轮修 整形貌的仿真, 但将磨粒都近似看成球形, 这势必 影响模型的精确性[ 4] 。所有这些仿真都缺乏对时间 的依赖性, 不能真正反映磨削过程的变化, 这不仅 有碍于对磨削机理的理解, 而且也不利于模型的实 际应用。因此, 建立一系列能够对磨削过程进行在 线描述的实时模型, 正是对磨削过程进行动态仿真 的关键。
在所有的磨削参数当中, 磨削深度是影响磨削 过程的主要因素, 故本文首先建立了随时间变化的 磨削深度的数学模型, 在此基础之上进一步建立了 依赖于时间变化的磨削力、工件平均温升、磨削接 触区热源表面的最高温度及工件表面粗糙度的数 学模型。通过向仿真程序中输入磨削仿真参数, 运 行磨削模型的仿真程序, 利用计算机生成离散的数 据, 从而使磨削深度、磨削力、工件平均温升、磨削 接触区热源表面的最高温度及工件表面粗糙度可 以被计算和估计, 并最终通过计算机绘制出磨削过 程的仿真曲线, 所得的仿真结果与预想的和试验的 结果具有良好的一致性, 证明了所建模型的正确 性。
1000kg/ m m, k a= 500kg / mm , kw = 300kg / mm , k = 165kg/ mm, = 60°, G = 18. 1, = 0. 5, =
图 3 磨削过程仿真流程图 图中, r( ) 为描述工件形状的函数; t 为总的磨削时间; t1、t 2 分别为粗磨时间和光磨时间; N 为设定的磨 削过 程仿真总的采样 点数; N 1、N 2 分别为 粗磨和光磨阶 段 的采样点数; i 为采样计数器; ti 为第 i 个采样点所对应 的时间; r ( ti) 、 ( ti) 、F t( ti) 、FN ( ti) 、w ( ti) 、max( ti) 及 R a ( ti ) 分别为磨削进给 量、磨削深度、切向力、法向力、工 件平均温度、接触区最高温 度及工件表面粗糙度 的数 学模型。
入稳定阶段后, 式( 1) 中的
kb 4 t an
-2(
v v
1 2
)
1-
(
dw + d dw ds
s)
-
/2
基本接近于常量, 令其为 kc。又当 较小时, 1 - / 2
≈ 1, 则有
F n ≈ kc
( 2)
设磨削系统的等效刚度系数为 ke( 见图 2) ,
则
1 ke
=
1 km
+
1 kw
+
1 ka
收稿日期: 2000—03—07 基金项目: 教育部高温结构陶瓷及工程陶瓷加工技术重点实验 室基金资助项目( T D97—06)
另外, 由于本文中所建的磨削模型具有良好的 时间依赖性, 所以, 本文还为磨削过程的预测、控制 及优化提供了必要条件, 也为虚拟制造和虚拟磨削 创造了先决条件。
1 磨削过程模型的建立
( 14)
其中3. 1Rw J
a(
2a )
0.
d 47 / e
2-
0.
235w
-
2
可认为是与砂轮
和工件有关的一个常数, 设其为 C, 而且磨削接触
区最高温度发生在磨削接触面上, 即 z = 0处, 则磨
削接触区最高温度的数学模型为
磨削过程模型的建立及其计算机仿真——王龙山 李国发
max( z =
0) =
本文的所有磨削模型都是针对外圆横向进给 磨削而建立的, 只要稍作改动即可应用于其它外圆 磨削过程。 1. 1 磨削力模型的建立
磨削力的计算在实际工作中是很重要的, 它不 仅是机床设计和工艺改进的主要依据, 而且是磨削 稳定性及磨削烧伤的重要影响因素。
首先, 将磨粒简化为具有一定顶角的圆锥( 见 图 1) 作为磨粒的基本模型[ 5] 。之后, 采用单位磨削