铝合金铸件缺陷胶粘修复工艺规范(修补工艺)
铸造常见缺陷的修补技术PPT课件
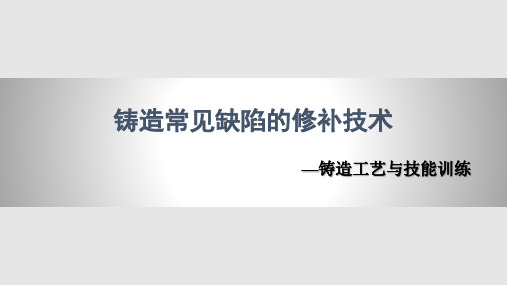
2)焊补时 ① 焊条直径可按待焊处壁厚进行选用。 ② 根据焊条直径、焊条类型、待焊铸件的壁厚等选择适当的电流。 ③ 用非石墨型焊条冷焊时,通常采取“小电流、短路、断续、分散焊” 。 ④ 用特制铸铁芯焊条冷焊时一般采取“大电流、连续、集中式操作”。 ⑤ 焊补厚壁件时可用多层堆焊的方法。 ⑥ 当焊件的材质较差、且焊缝强度高时,可用栽丝法。 ⑦ 当焊补有裂纹倾向缺陷时,可采用热态锤击法
3)焊补时注意事项 ① 难焊的铸件应在室内进行,以防风吹,最好将铸 件放置在炉旁,有助于提高整个铸件的温度。 ② 焊前若将需焊铸件局部或整体预热至100~200℃时, 则更能改善焊补区的加工性能。
(2)电弧半热焊补 电弧半热焊补常用钢芯石墨化型铸铁焊条。 常用于焊补非加工面上的各类缺陷。 1)焊补前 ① 缺陷的清理和加工与电弧冷焊基本相同。 ② 待焊的缺陷部分通常加热到400℃左右。 2)焊补时 ① 半热焊用的电流比冷焊用的电流要稍大。 ② 半热焊通常采取“连续堆焊” 的方法。 ③ 电弧通常采用长弧,但不宜太长,以免药皮中大量石墨化元素烧损;也 不宜太短,否则药皮不能充分熔化。
其修补方法是在缺陷处钻孔、精铰,采用过盈配合压入与铸件同质材料加 工的塞子,然后(分直流与交流)、软电缆、焊钳、焊条、地线夹、 面罩、清理工具等。 2. 操作步骤 (1)正确选择焊补设备、辅具、焊条及个人防护用具。 (2)根据焊条直径、焊条类型、待焊铸件的壁厚等选择 适当的电流。 (3)对焊补铸件缺陷周围进行必要的处理。
三、浸渍填补
浸渍填补是解决铸件渗漏问题的新技术,是将胶状的浸渗剂渗入铸件的 孔隙中使其硬化,与铸件孔隙内壁连成一体,达到堵漏的目的。
1. 浸渗剂 目前常用的浸渗剂有水玻璃型、合成树脂型和厌氧型三种。 2. 渗补工艺 渗补工艺因铸件结构、生产类型、浸渗剂种类、铸件缺陷位置及状态的 不同而不同。
铸件缺陷的检查与修补

铸件缺陷的检查与修补摘要本文首先阐述了铸件常见缺陷,其次,就铸件缺陷的检查与修补进行了深入的探讨,具有一定的参考价值。
关键词铸件缺陷;检查;修补0 引言铸造工艺与其他工艺相比,是—项比较复杂的工艺。
在全部铸造生产中,影响铸件质量的因素很多,很容易产生各种类型的铸造缺陷。
铸件虽然产生缺陷。
但不的—律视为废品。
应根据铸件的具体情况来进行具体的分析,某些有铸造缺陷的铸件经过修补后还可以使用。
1 铸件常见缺陷铸件缺陷有:冷隔、浇不足、气孔、粘砂、夹砂、砂眼、胀砂等。
1)冷隔和浇不足液态金属充型能力不足,或充型条件较差,在型腔被填满之前,金属液便停止流动,将使铸件产生浇不足或冷隔缺陷。
浇不足时,会使铸件不能获得完整的形状;冷隔时,铸件虽可获得完整的外形,但因存有未完全融合的接缝,铸件的力学性能严重受损。
防止浇不足和冷隔:提高浇注温度与浇注速度。
2)气孔气体在金属液结壳之前未及时逸出,在铸件内生成的孔洞类缺陷。
气孔的内壁光滑,明亮或带有轻微的氧化色。
铸件中产生气孔后,将会减小其有效承载面积,且在气孔周围会引起应力集中而降低铸件的抗冲击性和抗疲劳性。
气孔还会降低铸件的致密性,致使某些要求承受水压试验的铸件报废。
另外,气孔对铸件的耐腐蚀性和耐热性也有不良的影响。
防止气孔的产生:降低金属液中的含气量,增大砂型的透气性,以及在型腔的最高处增设出气冒口等。
3)粘砂铸件表面上粘附有一层难以清除的砂粒称为粘砂。
粘砂既影响铸件外观,又增加铸件清理和切削加工的工作量,甚至会影响机器的寿命。
例如铸齿表面有粘砂时容易损坏,泵或发动机等机器零件中若有粘砂,则将影响燃料油、气体、润滑油和冷却水等流体的流动,并会玷污和磨损整个机器。
防止粘砂:在型砂中加入煤粉,以及在铸型表面涂刷防粘砂涂料等。
4)夹砂在铸件表面形成的沟槽和疤痕缺陷,在用湿型铸造厚大平板类铸件时极易产生。
铸件中产生夹砂的部位大多是与砂型上表面相接触的地方,型腔上表面受金属液辐射热的作用,容易拱起和翘曲,当翘起的砂层受金属液流不断冲刷时可能断裂破碎,留在原处或被带入其它部位。
5.3.3-1 WP-5铸铝合金件的焊接修理工艺

§5.3.1 WP-5铸铝合金件的焊接在项目五中,学习§5.1、5.2、5.3、之后,需要补充讲解阻铝合金的焊接技术,因为这三节中使用到这个技术。
铸铝合金ZL101、ZL102、zL103易于气焊焊接;ZL201焊接性良好;ZL104、ZL105焊接性尚好。
由于铸铝中一般都含有大量杂质,其中不仅有铝、铁、锰、锌、铜、硅等元素的氧化物,还有浇铸过程中熔解于合金中德气体,如氢(含0.15%~4.5%)、一氧化碳、二氧化碳等,因此,铸造铝合金焊接比较困难。
铸造铝合金目前主要采取气焊、电弧焊或氩弧焊。
此处主要介绍阻铝合金的气焊方法,并简要说明电弧焊的要领;至于氩弧焊铸造铝合金则工艺与焊接变形铝合金相同。
放在以后专门介绍。
一、铸造铝合金的气焊1、焊接材料焊接铸铝时采用低熔点的LT1焊丝,或与工件成分相同的铸造焊条(φ3~8mm),不易采用纯铝或LF21焊丝。
焊药采用粉401,使用前,用干净水在不锈钢或瓷杯里调成糊状,用毛刷均匀地涂抹在焊丝表面,厚度0.5~1.0mm;然后用火焰枪烤干。
烤干时温度不超过150℃,以免焊药脱落。
糊状焊药保存时间不得超过9小时,最好随调随用。
2、焊前准备(1)用手錾錾切工件地补焊部位,直至露出金属光泽为止;用打光毛刺,再酒精清洗干净;(2)后壁工件焊接前开制V型焊接槽,以保证焊透;(3)薄壁焊件焊前配制垫板,防止焊接过程熔化金属由焊缝背面或两旁流出;(4)预热温度250~350℃,预热后立即焊接;3、铸铝焊接操作要领(1)气焊阻铝合金件时,氧炔焰应调节为中性焰或碳化焰,焰心距工件表面6~10mm;(2)焊接采用右焊法或左焊法,焊枪运动速度在不扩大焊池面积地情况下,愈慢愈好;但也不要太慢。
(3)焊接过程中,要用焊丝或焊条深入熔池内搅动,以充分发挥焊药地作用,促使熔池内氧化物地去除。
这时焊丝(或焊条)要处于红热状态,如果焊丝过冷就会使得熔融金属粘附其上;若焊丝过热则会容易融入焊缝,导致焊缝表面粗糙。
【新提醒】适合新手的铝合金焊接及铝合金缺陷修复方法

【新提醒】适合新手的铝合金焊接及铝合金缺陷修复方法前言:铝合金的焊接无论工用,还是民用都不可缺少。
在熔焊方式上最常用铝合金焊接方法会用TIG不熔化钨极氩弧焊(比如采用交流氩弧焊机用WE55焊丝焊接),及少量的MIG熔化性钨极氩弧焊,还有很少见的SMAW直流手弧电焊(直流电焊机用WE555铝条焊接)。
而在钎焊方式上最多的是传统的用焊粉配合铝硅焊丝气焊,因为其工作熔点高(比如采用MAGNA55配合MAGNA55-F,550℃-600℃),所以对于操作者的手法要求是比较高的。
不管什么方法都有其可取之处,也是萝卜青菜各有所爱,但是上述所讲焊接方式多少都是需要懂得一定的焊接技术或者需要配备昂贵的焊接设备。
如果说对于新手遇到铝合金焊接或者铝合金修复的时候怎么办?花几个月的时间去学氩弧焊?去购买氩弧焊机?NO!其实铝合金焊接及修复对新手来说都已经不是个难题了,需要如下装备你就是铝合金焊接及铝合金修复专家需要懂得的技术:加热的技术(会开煤气或者会烧气焊,高级一点的会用感应加热或者电控加热)需要的装备和材料:煤气罐或者丙烷或者氧乙炔;小号喷枪或者钎焊枪;简易打磨工具(锯条,纱布,不锈钢刷);WE53焊丝可以解决的铝合金焊接领域:大件铝的连接,搭接,角接,补大洞(可以替换氩弧焊,具体案例威欧丁焊接会做一个示范给对焊接确实感兴趣的朋友们的),小件铝及精密铝的磨损修复,气孔修复,裂纹修复,面与面的全面叠焊,还有解决我们平时很难见到的一些铝件缺陷(欢迎各位同仁有这方面的缺陷或者铝焊接难题可以反馈给我们)简易焊接方法:1)打磨,清洁(需要受力比较大的结构件需要开坡口)2)加热母材至400度左右,可以选用一切的加热热源。
3)用WE53搽拭母材表面,同时用枪的火焰末梢燎燎WE53并保持目材的400度温度就可以了4)在搽拭母材的过程中,WE53会像水一样流动到母材成型。
(代表性的操作案例可以见:威欧丁特种焊接-WE53铝焊视频教学-铝焊接可以这么简单!)强度测试:在焊接之前可以随便找个铝件进行试焊,然后做破坏性试验,强度可以达到215Mpa 高于一般的母材的强度。
2911-001铸铁件缺陷的修补工艺守则

铸铁件缺陷修补规定编号:H2911-001代替:郴州华安电机制造有限公司2005年7月铸铁件缺陷的修补工艺守则H2911-0011.范围本规定适用于本公司电机产品所有铸件中。
a).超过Q/NF1410《铸件质量分等规定》的铸造缺陷的焊补。
b).粗加工后加工面上发现的铸造缺陷的焊补。
c).精加工后加工面上发现的缺陷的修补。
2.引用标准Q/NF1410《铸件质量分等规定》GB3836.13第5.3.1.2(隔爆面修补规定)3.判定铸件缺陷的职权划分3.1铸件毛坯的表面缺陷由铸件生产厂根据Q/NF1410《铸件质量分等规定》和铸造缺陷的焊补价值确定,但交货时铸件表面质量必须满足相关要求。
3.2粗加工后加工面上发现的铸造缺陷由成品车间检查员在缺陷部位涂白漆作为标记,对生锈后不易观察的缺陷,如疏松、裂纹等,应使用白漆写上疏松、裂纹等字样,同时开据不合格品单,并会同铸件生产厂(生产供应科代表或负责联系,下同)按本规定和铸造缺陷的焊补价值确定是否料废。
在未被确认是否料废之前,成品车间应按待处理品处理,确保铸件不受其它损伤,否则由此造成的损失由成品车间负责。
3.3精加工后加工面上发现的铸造缺陷由成品车间检查员按本规定和GB3836.13第5.3.1.2中隔爆面允许修补的范围确定。
4.缺陷修补的工序划分4.1精加工后加工面上的缺陷由成品车间修补。
4.2铸件毛坯及粗加工后加工面上的缺陷由铸件生产厂焊补。
4.3隔爆零件水压试验时发现的非加工面上的气孔和砂眼由铸件生产厂负责焊补和打磨,并应保证精加工面不变形。
4.4铸件外表面在电机装配后存在的影响表观质量的缺陷由喷包工序打腻子修补并磨平,超出Q/NF1410规定的毛坯缺陷由铸件生产厂负责修补和打磨。
4.5铸件从铸件库运出至电机入库因磕碰造成的散热片断裂等外观缺陷由成品车间焊补并打磨。
铸铁件缺陷的修补工艺守则H2911-0015.铸造缺陷修补的分类规定5.1铸件毛坯缺陷和粗加工后发现的缺陷。
铝合金压铸产品缺陷及处理

铝合金压铸产品铸造缺陷产生原因及处理办法1、表面铸造缺陷1.1 拉伤(1)特征:(2)产生原因:(3)处理方法:1.2 气泡(1)特征:(2)产生原因(3)处理方法1.3 裂纹(1)特征:(2)产生原因:(3)处理方法:1.4 变形(1)特征:(2)产生原因:(3)处理办法:1.5 流痕、花纹(1)特征:(2)产生原因:(3)处理方法:1.6 冷隔(1)特征(2)产生原因:(3)处理方法:1.7 变色、斑点(1)特征:(2)产生原因:(3)处理方法:1.8 网状毛翅(1)特征:(2)产生原因:(3)处理方法:1.9 表面凹陷(1)特征:(2)产生原因:(3)处理方法:1.10 欠铸(1)特征:(2)产生原因:(3)处理方法:1.11 毛刺飞边(1)特征:(2)产生原因:(3)处理方法:2、压铸件内部缺陷2.1 气孔(1)特征及检查方法:(2)产生原因:(3)处理方法:2.2 缩孔、缩松(1)特征及检查方法:(2)产生原因:(3)处理方法:2.3 夹杂(1)特征及检查方法:(2)产生原因:(3)处理方法:2.4 脆性(1)特征及检查方法:(2)产生原因:(3)处理方法:2.5 渗漏(1)特征及检查方法:(2)产生原因:(3)处理方法:2.6 非金属硬点(1)特征及检查方法:(2)产生原因:(3)处理方法:2.7 金属硬点(1)特征及检查方法:(2)产生原因:(3)处理方法:3、缺陷产生的影响因素3.1 压铸件常见缺陷及影响因素,见表13.2 解决缺陷的思路由于每一种缺陷的产生原因来自多个不同的影响因素,因此在实际生产中要解决问题,面对众多原因到底是先调机?或是先修模具?建议按难易程度,先简后复杂去处理,其次序:(1)清理分型面、清理型腔、清理顶杆;改变涂料、改善喷涂工艺;增大锁模力;增加浇注金属量;这些是靠简单操作即可实施的措施。
(2)调整工艺参数、压射力、压射速度、充型时间、开模时间、浇注温度、模具温度等。
铝合金的铸造缺陷及其解决方案

铝合金的铸造缺陷及其解决方案关键信息项:1、铝合金铸造缺陷的类型名称:____________________________描述:____________________________2、造成铸造缺陷的原因因素:____________________________详细解释:____________________________3、解决方案的具体措施方法:____________________________实施步骤:____________________________4、预防铸造缺陷的策略策略:____________________________执行要点:____________________________11 铝合金铸造缺陷的类型111 气孔气孔是铝合金铸造中常见的缺陷之一。
气孔通常呈圆形或椭圆形,其尺寸大小不一。
112 缩孔和缩松缩孔是由于铸件在凝固过程中,金属液补缩不足而形成的较大孔洞。
缩松则是分散的细小缩孔。
113 夹渣夹渣指在铸件内部或表面存在的非金属夹杂物。
114 裂纹裂纹分为热裂纹和冷裂纹。
热裂纹在凝固末期高温下形成,冷裂纹则在较低温度下产生。
12 造成铸造缺陷的原因121 熔炼工艺不当熔炼过程中,如果温度控制不合理、熔炼时间过长或过短、搅拌不均匀等,都可能导致合金成分不均匀,气体和夹杂物含量增加。
122 浇注系统设计不合理浇注系统的结构和尺寸如果设计不当,可能导致金属液的流动不畅,产生卷气、冲砂等问题,从而形成气孔、夹渣等缺陷。
123 模具问题模具的温度不均匀、模具的排气不畅、模具的表面粗糙度不合适等,都可能影响铸件的质量,导致缺陷的产生。
124 铸造工艺参数不合理包括浇注温度、浇注速度、冷却速度等参数,如果选择不当,会直接影响铸件的凝固过程,从而引发各种缺陷。
13 解决方案的具体措施131 优化熔炼工艺严格控制熔炼温度和时间,采用合适的搅拌方式,确保合金成分均匀,减少气体和夹杂物的含量。
铝合金缺陷修复新工艺

铝合金缺陷修复新工艺:1、概述批量生产的低压薄壁容器,零件大部分采用ZL115压差铸造毛坯。
虽然铸件经过X光探伤检测,但是由于结构特征的限制和铸造缺陷的大小与分布的敏感方向不同,有些缺陷在X光片上不能明显呈现出来,常常在机械加工之后发现,有些直径微小的穿透性气孔只能在压力试验之后发现。
这严重影响到产品质量和生产进度,甚至造成巨大经济损失。
一些常规焊补方法均不能很好地满足技术要求。
为了验证该项新工艺对解决铸铝零件机加后所出现的密封性和外观缺陷修复的有效性,寻找出一种铸铝件缺陷修复新途径,我们进行了大量工艺试验和必要的检测,并形成一套正确的铸铝件缺陷修复工艺规程。
2、金属表面修补机的缺陷修复机理由于铝及其合金的化学活泼性很强,表面极易形成氧化膜,且多属于难熔性质(如Al2O3的熔点约为2050℃,MgO的熔点约为2500℃)加之铝及其合金导热性强,焊接时容易造成不熔合现象。
由于氧化膜比重同铝的比重极其接近,所以也容易成为焊缝金属的夹杂物。
同时铝及其合金的线胀系数大,导热性又强,焊接时容易产生翘曲变形。
这是铝及其合金焊接时颇感困难的问题。
目前熔化焊中最常用的氩弧焊是靠“阴极雾化”作用,将氧化膜破碎,在氩气的保护下,使氧化膜不能重新产生。
但是在焊接热处理强化处理后的铝合金时,近缝区存在强度大大削弱的现象,也不可避免的会产生翘曲变形。
金属表面修补机主要用于修复铸造缺陷,它有逆变式高频+脉冲电源、可使焊丝高速旋转的焊枪和控制部分组成。
其修复缺陷的机理为:利用高频+脉冲电压将气体击穿形成等离子气,从而产生温度可达6000℃以上的电火花,电火花将可熔性旋转电极(即焊丝)瞬间(10-5—10-6秒)和与其接触的母材同时熔化,依靠瞬间高温和旋转焊丝与母材的机械摩檫及旋转电场力的综合作用,使氧化膜破碎,在氩气的保护下,使氧化膜不能重新产生,从而完成焊丝与母材的冶金结合。
由于电火花作用时间短,与焊丝直接接触的母材局部熔化,铝的导热性很好,瞬间将输入的热量扩散并散失到空气中,基体几乎不产生温升,从而基体不会变形,精密铸铝件机械加工后进行缺陷的修复,而不会影响尺寸精度。
- 1、下载文档前请自行甄别文档内容的完整性,平台不提供额外的编辑、内容补充、找答案等附加服务。
- 2、"仅部分预览"的文档,不可在线预览部分如存在完整性等问题,可反馈申请退款(可完整预览的文档不适用该条件!)。
- 3、如文档侵犯您的权益,请联系客服反馈,我们会尽快为您处理(人工客服工作时间:9:00-18:30)。
铝合金铸件缺陷胶粘修复工艺规范
文件编号:W29-AL-41-08-001
小组成员:皮振江秦红林丛培军马思宁赵莹高殿阁王彦飞张乃辉
编制:王彦飞初稿日期:2008年5月15日更改日期:
1、概念
胶粘修复工艺就是采用特殊的胶粘剂对存在缺陷或者破损的机械零件进行挽救修复的一种工艺方法,它属于机械零件再制造技术的范畴。
胶粘修复工艺在铝合金铸件的缺陷修复方面的应用已经有了多年历史,早已成为了一种成熟的缺陷修复技术。
本铝合金铸件缺陷胶粘修复工艺将以复杂典型的铝合金气缸盖(如EA888气缸盖)的缺陷胶粘修复为范例进行说明。
2、适用范围
胶粘修复工艺使用的前提是绝对不修复零件上承受巨大工作载荷的以及工作环境非常恶劣、苛刻的区域上的缺陷,如铝合金气缸盖的燃烧室区域内的缺陷,而且必须保证经过修复后的缺陷部位不影响气缸盖的正常使用,不影响功能。
一般来说,气缸盖的毛坯面和加工面上直径大小不超过3mm,深度不超过2mm,可见基底的气孔、缩松、砂眼等孔洞类缺陷都可以考虑采用胶粘工艺方法修复;而对直径大于3mm的缺陷,可以考虑使用焊补的方法修复。
但是,胶粘修复工艺在气缸盖上的使用必须通过客户的质量或产品研发部门的批准认可。
图示1、气缸盖燃烧室部位缺陷不允许修复
3、工艺流程
3.1缺陷形式和部位确定
由质保部检查员对可以采用胶粘工艺进行修复的有缺陷的气缸盖进行判定分离,并在缺陷部位用彩笔明确标识,放在专门的工位器具上,待指定的专业人员进行挽救修复。
图示2、缺陷部位用蓝色彩笔明确标出
3.2缺陷部位表面预处理
对缺陷部位先采用打磨、钻孔或抛光等方法清理掉缺陷部位处的氧化皮、氧化渣等可能会影响胶粘强度的杂质,然后用压缩空气吹干净,就可准备涂胶。
特别要注意的是,因为油污对胶粘效果的影响非常大,所以操作过程中必须避免缺陷部位粘有油污。
如果缺陷部位的厚度在5mm和8mm之间,则预处理深度不能超过3mm;如果缺陷部位厚度大于8mm,则预处理深度最大可以达到4mm。
因此对有油污的表面,可以辅助用丙酮擦洗处理,然后再用干净的水冲洗干净,最后用热风机进行辅助吹干。
注意:在进、排气面上气道口周围钻孔时,一旦钻孔导致孔洞和气道贯通,则不得对铸件进行修复,而应直接按废品处理。
电钻,φ2mm钻
头,钻孔深度不能
超过3mm。
图示3、对直径小于φ2mm的渣孔用φ2mm的钻头扩孔
3.3配胶
胶水采用北京奥宇可鑫表面技术有限公司的AK01-5铸铝缺陷修补胶,它由A胶和B胶两种组分构成,A胶为黑灰色,B胶为白色,使用之前需要将两种组分按照一定的比例充分搅拌混合后才可使用(A组分和B组分的体积比为2:1)。
配胶工作可在缺陷部位表面预处理工作完成之后进行,配完的混合胶应在40分钟内用完。
(为避免胶的浪费,应根据胶补件数和胶补速度决定胶的混合量)
图例4、A胶B胶
图示5:配胶
3.4涂胶
将配好的胶粘剂采用特制的工具涂抹到预处理完毕的缺陷部位,要求涂层相对均匀致密。
向缺陷内部填充胶粘剂时应使胶粘剂和铸件充分接触,同时用填充工具不断挤压胶粘剂,使胶粘剂填满缺陷内部,避免铸件内部出现气泡缺陷。
图示6:涂胶
3.5清理
在胶粘过程中,难免会在非胶粘表面弄上胶液,或者因涂胶量大、胶合时挤出过多的胶,这些胶固化后不仅影响外观而且修正困难,所以应当在胶液固化之前清理干净,必要时可以在受影响区域内进行喷涂处理,以保证铸件的表面质量。
3.6固化
固化又成为硬化或变定,是获得良好胶粘性能的关键过程,只有完全固化,强度才会最大。
对通过胶粘修复的铸件要达到最好的固化效果,通常在室温(20℃-30℃)下放置30分钟可以基本固化,10小时侯可达到最高强度。
冬天施工如果温度太低,会延长固化时间,因此可用钨灯、烘箱等方法加热固化,30℃-60℃加温3-5小时后,再缓慢降至室温,并且至少在常温下放置24小时待修复部位完全固化后才可进入下道工序。
3.7修正胶后表面处理
对胶合后固化后的缺陷修复部位采用打磨、抛光、喷涂等方法进行表面处理,确保铸件的外形尺寸符合产品要求,表面平整、光滑有光泽。
3.10做修复标识
为了使经过修复的产品具有可追溯性,必须在产品的固定部位做永久性的固定的标识,如打钢号字头,用记号笔写标记等。
图示7: EA888缸盖胶粘修复标识示例
胶粘代码J ,钢号字头印记。
J
3.11检验和记录
质量检查人员对修复后的铸件进行检查,合格的铸件按要求进行准确详细的记录后方可流入下道工序。
表: EA888气缸盖缺陷修复记录
序号 铸造日期 模号
浇注者 代号
铸件顺 序号
修复部位修复方法
修复者 代号
修复日期
合格与否
4、注意事项
4.1对胶粘修复人员的要求
胶粘修复人员必须经过技术开发部严格的培训后方可上岗。
4.2对胶粘修复材料的要求
胶粘剂必须是专用的铝合金缺陷修补膏,而且经过了客户质量或产品研发部门的认可。
4.3对胶粘修复环境的要求
胶粘修复的环境必须保持清洁干燥。
4.4对胶粘修复方法的要求
必须严格按照技术开发部制定的工艺规范进行严格的操作。
4.5对胶粘修复铸件检验人员的要求
胶粘修复铸件检验人员必须经过质量或技术发展部门严格的培训后方可上岗。
5、参考文件
[1] 奥宇可鑫新编使用胶接与粘涂技术 高应岑 编著 [2] 德国大众汽车集团 VW 50096 标准 [3] 德国大众汽车集团 PV 6257 标准。